Optimizing Systems with Material Handling Rollers
Conveyor rollers are fundamental components in the efficient operation of material handling systems across various industries. Known for their versatility, material handling rollers facilitate the smooth and efficient transportation of goods, reducing manual labor and enhancing workflow. These rollers support a multitude of applications, from simple warehouse item sorting to complex assembly lines in manufacturing. The importance of material handling rollers extends beyond mere functionality; they also play a crucial role in minimizing downtime and improving overall industrial productivity. As we delve deeper, we’ll explore how these essential components contribute significantly to the optimization of operations in diverse industrial environments.
What are Material Handling Rollers
Material handling rollers, commonly known as conveyor rollers, are cylindrical components that facilitate the movement of materials along conveyor systems. These rollers are pivotal in ensuring that goods are transported smoothly across various stages of processing and distribution without the need for extensive human labor. The functionality of material handling rollers is not limited to just moving goods; they also play a significant role in controlling the speed and direction of the materials being handled.
To illustrate the versatility and utility of material handling rollers, consider these five examples:
- Warehouse Distribution: In a warehouse, material handling rollers are used to move products from storage areas to loading docks. They are essential for swift sorting, packing, and shipping processes.
- Food Processing Plants: In these facilities, material handling rollers ensure hygienic and efficient transport of food products through different stages of processing, from cleaning to packaging.
- Pharmaceutical Manufacturing: Conveyor rollers in the pharmaceutical industry are designed to handle sensitive materials with precision and care, ensuring that products move seamlessly through production lines under controlled conditions.
- Automotive Assembly Lines: Material handling rollers are integral to the automotive industry, where they are used to move parts and assemblies through various stages of vehicle construction, from chassis assembly to final inspection and testing.
- Airport Baggage Handling: These rollers are crucial in the efficient movement of luggage between check-in, security, and aircraft loading areas, significantly enhancing the overall speed and efficiency of airport operations.
Through these examples, it becomes clear that material handling rollers are indispensable in numerous industrial and commercial settings, driving efficiency and productivity across diverse applications.
Types of Material Handling Rollers
Material handling rollers come in various designs and specifications, each tailored to meet specific industrial needs and applications. These rollers are categorized based on size, load capacity, material, and the unique features they possess. Understanding the different types of material handling rollers is crucial for selecting the right one for your conveyor system. Here’s a detailed exploration of five key types:
- Mini Conveyor Rollers: These small-diameter rollers are designed for lightweight applications and tight spaces. Mini rollers are ideal for moving small items and are commonly found in industries like electronics manufacturing and postal services.
- Heavy-Duty Industrial Rollers: Built to withstand large loads and harsh conditions, heavy-duty rollers are used in industries such as mining, construction, and heavy manufacturing. Their robust construction ensures longevity and reliability under extreme conditions.
- 4″ Conveyor Rollers: These medium-sized rollers provide a balance between the small mini rollers and larger heavy-duty types. They are versatile and commonly used in food processing, pharmaceuticals, and packaging industries where moderate load capacity is required.
- Conveyor Rollers with Brackets: These are designed for easy installation and adjustment. Rollers with brackets are used when conveyor paths need to be quickly altered or when additional support is necessary. They are crucial for modular conveyor systems.
- Plastic Conveyor Rollers: Made from durable plastics like polyurethane, these rollers are used in environments where corrosion resistance and noise reduction are priorities. Plastic rollers are lighter than metal ones and are used in food production, chemical processing, and other clean or quiet environments.
In addition to these types, specialized material handling rollers like those fitted with sensors for speed and load monitoring are increasingly being integrated into advanced automated systems. This diversity in roller types ensures that there is a suitable roller for every material handling need, enhancing efficiency and safety across various industries.
Conveyor Roller Materials and Specifications for Material Handling Rollers
The efficiency and functionality of material handling rollers largely depend on their materials and specifications. These factors are carefully chosen based on the application’s specific requirements, such as load capacity, environmental conditions, and operation speed. Here we delve into the common materials used for material handling rollers and discuss key specifications like diameter, length, and capacity.
Materials Used in Material Handling Rollers:
- Steel Rollers: Highly durable and capable of carrying heavy loads, steel rollers are commonly used in industries such as mining and heavy manufacturing. Their strength makes them suitable for high-impact environments.
- Aluminum Rollers: Lighter than steel, aluminum rollers are used where weight is a concern, such as in packaging or assembly lines. They offer good corrosion resistance and are easier to handle during installation.
- Polyurethane Rollers: Known for their quiet operation and non-marking properties, polyurethane rollers are ideal for indoor environments where noise reduction is crucial, such as in distribution centers and warehouses.
- Rubber-Coated Rollers: These rollers provide excellent grip and noise reduction. Rubber-coated rollers are typically used in applications requiring gentle handling of delicate materials to prevent damage during transport.
- Composite Material Rollers: Made from a blend of plastics and reinforced fibers, composite rollers are designed for environments where corrosion and chemical resistance are necessary, such as in chemical processing plants.
Specifications of Material Handling Rollers:
- Roller Diameter: This specification is critical as it determines the type of materials that can be transported. Smaller diameters are typically used for lightweight materials, while larger diameters are reserved for heavier items.
- Roller Length: The length of the roller must be suitable for the width of the materials being handled. Adequate coverage ensures stable and efficient transport of goods across the conveyor system.
- Load Capacity: Each roller is rated for a specific load capacity, which must not be exceeded to maintain safety and longevity. The choice of material often impacts the load capacity, with steel being suitable for high-load applications.
- Operating Conditions: Rollers are also specified by their suitability for different environments, such as high temperatures, corrosive substances, or outdoor conditions.
These materials and specifications is essential when selecting material handling rollers, as the right choice can significantly enhance system efficiency and reduce maintenance needs.
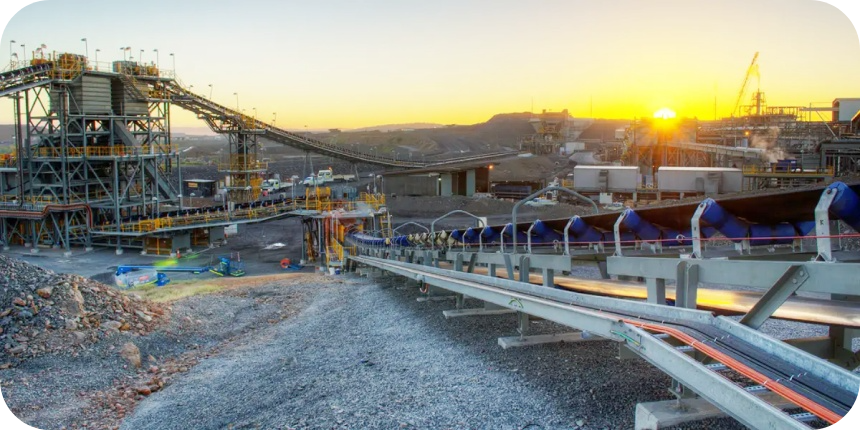
Price Considerations for Material Handling Rollers
When investing in material handling rollers, understanding the factors that influence their price is crucial for budget planning and operational efficiency. Various elements contribute to the cost, and recognizing these can help in making informed purchasing decisions. Here, we’ll explore the key factors that affect the price of material handling rollers and provide tips for selecting cost-effective solutions without sacrificing quality.
Factors Influencing the Price of Material Handling Rollers:
- Material Used: The type of material (steel, aluminum, polyurethane, etc.) significantly affects the cost. Steel rollers are generally more expensive due to their durability and load capacity, whereas aluminum rollers might be less costly but offer less strength.
- Manufacturing Process: Rollers that require more complex manufacturing processes, such as those with precise engineering tolerances or specialized coatings, typically cost more.
- Size and Specifications: Larger and custom-sized rollers that require additional material and labor to produce will naturally be pricier than standard sizes.
- Quantity Ordered: Bulk orders often reduce the unit price due to economies of scale. Smaller orders may carry a higher price tag per unit due to the fixed costs associated with production setups.
- Supplier and Shipping Costs: The choice of supplier and the location from which the rollers are shipped can also impact costs. International shipping and handling fees can add significantly to the overall expense.
Tips for Choosing Cost-Effective Material Handling Rollers:
- Assess Your Specific Needs: Understand the exact requirements of your conveyor system to avoid over-specifying or under-specifying, both of which can lead to unnecessary expenses.
- Compare Suppliers: Don’t settle for the first quote you receive. Compare offers from multiple suppliers to find the best balance between price and quality.
- Consider Total Cost of Ownership: Look beyond the initial purchase price. Consider factors like maintenance costs, durability, and operational efficiency which can save money in the long run.
- Opt for Standard Sizes When Possible: Custom specifications can drive up costs considerably. If standard sizes can meet your needs, they often represent a more cost-effective choice.
- Leverage Bulk Purchases: If possible, plan your needs in advance and purchase in bulk. This approach usually secures a lower price per unit and reduces shipping costs over time.
By taking these factors and tips into account, you can make more economical decisions when purchasing material handling rollers, ensuring you receive the best value for your investment without compromising on the necessary quality and performance of your conveyor system.
Heavy Duty Conveyor Rollers for Material Handling Rollers
Heavy duty conveyor rollers are designed to handle the most demanding tasks in material handling environments. These robust rollers are engineered to support high loads and withstand harsh conditions, making them essential for industries that require reliability and durability. Here, we delve into the characteristics of heavy-duty industrial rollers and the benefits they provide in various application scenarios.
Characteristics of Heavy Duty Conveyor Rollers:
Heavy-duty conveyor rollers are typically constructed from high-grade steel or other durable materials that can endure the stress of heavy loads and abrasive conditions. They may also feature special coatings or treatments to resist corrosion, wear, and other environmental factors that could degrade their performance over time. The design of these rollers often includes larger diameters and thicker walls to increase their strength and load-bearing capacity.
Application Scenarios for Heavy Duty Material Handling Rollers:
- Mining and Quarrying: In the mining industry, material handling rollers must withstand abrasive dust, heavy loads, and vibrations. Heavy-duty rollers are used on conveyor belts that transport ores, crushed stone, and other heavy materials from the extraction point to processing locations.
- Manufacturing and Assembly: For manufacturing plants, especially those producing heavy machinery or steel products, heavy-duty rollers ensure that materials move smoothly through production lines without disruption, contributing to efficiency and safety.
- Port and Cargo Facilities: Ports and cargo handling facilities utilize heavy-duty conveyor rollers to move large containers and bulk goods. These environments demand rollers that can handle extreme loads and operate reliably in outdoor conditions, including exposure to seawater and weather changes.
- Agriculture and Bulk Handling: In agriculture, conveyor systems equipped with heavy-duty rollers are used for moving large quantities of grains or other bulk products. These rollers must be robust enough to handle significant weights over extended periods during peak harvest times.
- Recycling Facilities: Conveyors in recycling facilities face challenging conditions, including exposure to various materials of varying weights and sizes. Heavy-duty rollers help ensure that these materials are transported efficiently, reducing downtime and maintenance needs.
Benefits of Using Heavy Duty Material Handling Rollers:
- Durability: Designed to last under tough conditions, heavy-duty rollers reduce the frequency and cost of replacements.
- Increased Load Capacity: They enable the transportation of heavier materials without the risk of breakdowns, enhancing operational capabilities.
- Reduced Maintenance: Stronger materials and construction mean less wear and tear, leading to lower maintenance costs and less downtime.
- Versatility: Suitable for a wide range of industrial applications, heavy-duty rollers can be customized to meet specific environmental and operational requirements.
- Enhanced Safety: By reliably handling heavy loads, these rollers contribute to safer working conditions by preventing accidents associated with equipment failure.
Heavy-duty conveyor rollers are pivotal components in sectors where material handling involves extreme conditions and heavy loads. Their robust construction not only ensures operational efficiency but also plays a crucial role in maintaining safety and reducing operational costs.
Selecting the Right Conveyor Roller for Material Handling Rollers
Choosing the right conveyor roller is crucial for the efficiency and longevity of material handling systems. Different applications and environments require specific types of rollers to ensure optimal performance and durability. Here, we provide detailed advice on how to select the appropriate material handling rollers, focusing on factors such as load capacity, environmental conditions, and conveyor length.
Advice on Choosing the Right Type of Conveyor Roller:
- Warehouse Distribution: For general warehouse operations involving varied products and packaging, medium-duty steel or plastic rollers are usually sufficient. These rollers should accommodate moderate load capacities and offer flexibility in terms of speed and handling.
- Food Processing: In environments where sanitation and corrosion resistance are critical, stainless steel or plastic rollers are preferable. These materials can withstand frequent washdowns and resist the corrosive effects of cleaning chemicals.
- Heavy Manufacturing: For heavy manufacturing, such as automotive or metal fabrication, choose heavy-duty steel rollers. These rollers can handle high load capacities and withstand the abrasive conditions often present in such environments.
- Chemical Industries: In industries dealing with chemicals or high-corrosion environments, rollers made from materials like polyurethane or specially coated metals are ideal to prevent corrosion and damage from harsh substances.
- Outdoor Applications: For outdoor applications such as in the construction or mining sectors, choose rollers designed with materials and bearings that can withstand weather conditions and potential contaminants like dust and mud.
Key Considerations When Selecting Material Handling Rollers:
- Load Capacity: It is essential to select rollers that can support the weight and type of goods being transported. Underestimating load capacity can lead to roller failure and conveyor system downtime.
- Environment: The operating environment significantly influences the choice of roller material. For corrosive environments, materials like stainless steel or coated rollers are necessary. For high-temperature areas, heat-resistant materials should be used.
- Conveyor Length: Longer conveyor systems may require rollers with higher load-bearing capacities to prevent sagging and ensure smooth operation over greater distances.
- Speed Requirements: The speed at which the conveyor will operate also affects the type of roller needed. High-speed applications may require rollers with precision bearings to reduce friction and wear.
- Maintenance and Durability: Consider the ease of maintenance and the expected lifespan of the rollers. Investing in higher-quality rollers might be more cost-effective over time due to lower maintenance costs and fewer replacements.
By carefully considering these factors and choosing the right type of material handling rollers, businesses can ensure that their conveyor systems operate efficiently, safely, and cost-effectively in their specific industrial contexts.
Conveyor Roller Replacement and Maintenance for Material Handling Rollers
Effective maintenance and timely replacement of conveyor rollers are critical to ensuring the longevity and efficiency of material handling systems. Understanding when and how to replace material handling rollers, along with implementing a regular maintenance schedule, can significantly extend the life of the rollers and reduce system downtime. Below are detailed guidelines on these aspects.
Guidelines on When and How to Replace Material Handling Rollers:
- Wear and Tear: Regular inspections should be conducted to check for signs of wear, such as cracks, deformation, or excessive noise during operation. Rollers showing these symptoms should be replaced promptly to avoid system failure.
- Performance Issues: If rollers are no longer rotating smoothly or if the conveyor belt starts slipping or misaligning frequently, these may be signs that the rollers need to be replaced due to worn-out bearings or misshapen roller tubes.
- After a Set Period: Depending on the operational load and environment, establish a routine schedule for replacing rollers (e.g., every 2-3 years) as a preventative measure, even if visible wear isn’t immediately apparent.
- Replacement Process: To replace a roller, first ensure that the conveyor system is safely turned off and locked out. Remove the damaged roller, usually by detaching the brackets or holders. Install the new roller and ensure it is securely fastened and aligned with the conveyor belt.
Importance of Regular Maintenance to Extend the Life of Material Handling Rollers:
- Lubrication: Regular lubrication of bearings can prevent friction and wear, extending the life of the rollers. Use the appropriate grade of lubricant as specified by the roller manufacturer.
- Cleaning: Rollers should be kept free from dust, debris, and residues that can build up and impair their function. A regular cleaning schedule should be adhered to, especially in dirty or gritty environments.
- Inspection: Conduct systematic inspections of all rollers to identify potential issues early. This includes checking for proper alignment, rotation, and any signs of wear or damage.
- Load Management: Ensuring that the conveyor system is not overloaded is vital in maintaining the health of the rollers. Consistent overloading can accelerate wear and lead to premature failure.
- Record Keeping: Maintain a log of all maintenance activities, replacements, and observations from inspections. This historical data can help predict future needs and optimize maintenance planning.
By adhering to these guidelines for replacement and maintenance, the operational reliability of material handling rollers can be greatly enhanced. This proactive approach not only saves costs in the long run but also ensures that the conveyor system operates at peak efficiency, supporting the overall productivity of the facility.
Innovations in Conveyor Roller Technology for Material Handling Rollers
The future of conveyor technology is rapidly evolving, with significant innovations in material handling rollers that promise to transform industry practices. These advancements focus on enhancing efficiency, reducing environmental impact, and improving overall system reliability. Below, we explore some of the key trends in the design and materials of material handling rollers and discuss their potential impacts on industry practices.
Key Innovations and Trends in Material Handling Rollers:
- Smart Rollers: Integration of sensors and IoT technology in rollers allows for real-time monitoring of system performance. These smart rollers can track load conditions, speed, and wear, enabling predictive maintenance and reducing downtime.
- High-Performance Materials: The development of new composite materials and advanced polymers that are lighter, more durable, and corrosion-resistant is making rollers more efficient and sustainable. These materials also allow for quieter operation, which is beneficial in noise-sensitive environments.
- Energy-Efficient Designs: Rollers are being designed to minimize energy consumption by reducing friction and improving load handling. Some innovative designs include the use of magnetic levitation instead of traditional bearings to reduce contact and thus wear and energy use.
- Modular and Scalable Systems: The trend towards modular conveyor systems with interchangeable parts, including rollers, facilitates easier maintenance and system upgrades, adapting to changing operational needs without complete system overhauls.
- Enhanced Surface Treatments: New coatings and surface treatments are being developed to enhance the functionality of rollers. These include anti-static coatings to prevent dust accumulation, and hygienic coatings for use in food processing and pharmaceuticals, which prevent contamination.
Potential Impacts of These Innovations on Industry Practices:
- Increased Efficiency: Smart and energy-efficient rollers can significantly reduce energy costs and improve the speed and accuracy of material handling operations.
- Enhanced Durability and Lower Maintenance Costs: The use of high-performance materials and advanced surface treatments means rollers last longer and require less frequent replacement or maintenance.
- Flexibility and Scalability: Modular systems allow businesses to adapt their conveyor setups quickly and cost-effectively to meet changing production demands or technological advancements.
- Improved Safety and Environmental Impact: New technologies that reduce roller noise and energy consumption contribute to safer and more environmentally friendly workplaces.
- Data-Driven Operations: The integration of sensors and IoT technology into material handling rollers enables better data collection, which can be used to optimize operations, improve safety, and anticipate maintenance needs before failures occur.
As these innovations continue to develop, material handling rollers are set to become even more integral to industrial automation, helping companies to increase productivity, reduce costs, and achieve greater operational flexibility. These advancements are not just improving individual components but are reshaping entire supply chains and production methodologies.
Speak with our team about custom conveyor roller options.
FAQs About Material Handling Rollers
Material handling rollers are crafted from a variety of materials, each selected for specific properties that enhance performance under different operating conditions. The most common materials include steel, known for its strength and durability, making it ideal for heavy-duty applications such as in mining or construction. Aluminum rollers offer a lightweight alternative, suitable for lighter loads and requiring less energy to operate, which is often chosen for applications like packaging or assembly lines. Plastic rollers, including those made from polyurethane or nylon, are used where corrosion resistance or quieter operation is needed, such as in food processing or pharmaceutical environments. Additionally, rubber-coated rollers are preferred in scenarios requiring gentle handling of fragile materials to prevent damage during transportation.
The rollers on a conveyor are cylindrical components that facilitate the movement of materials along the conveyor belt. They are mounted within the conveyor frame and may vary in size, material, and design based on the application. Rollers function by rotating on their axes, which allows the conveyor belt to glide over them smoothly. This helps in the efficient transfer of goods from one point to another within a facility. They are fundamental in minimizing manual handling, reducing labor costs, and increasing workplace safety and productivity. Conveyor rollers are integral to the operation of both powered and gravity-driven conveyor systems and are designed to support the weight of the items being transported without significant friction.
Conveyor rollers come in several types, each designed to meet specific industrial needs. Gravity rollers, which use the force of gravity to move materials, are commonly used in manual sorting operations. Motorized or drive rollers are powered by motors, making them suitable for automated handling systems. Other types include grooved rollers, which are used with belts to increase traction, and impact rollers, placed at conveyor feeding points to absorb the shock of loading material. Tapered rollers are used in curves, helping maintain the alignment of packages as they move through bends. Each type of roller is crucial for ensuring that the conveyor system functions efficiently and meets the operational demands of different environments.
Conveyor rollers can vary widely in size, which is typically dictated by the application and the load they are required to carry. The diameter of the rollers commonly ranges from as small as 20 mm for light-duty applications to over 200 mm for heavy industrial uses. The length of the rollers also varies, usually tailored to match the width of the conveyor belt or the items being transported. Smaller rollers are used where fine control and low-profile materials are involved, while larger rollers are better suited for moving bulky or heavy goods. Selecting the right size is crucial as it affects the roller’s ability to distribute the load, reduce friction, and maintain the efficiency and longevity of the conveyor system.
Last Updated on July 29, 2024 by Jordan Smith
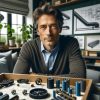
Jordan Smith, a seasoned professional with over 20 years of experience in the conveyor system industry. Jordan’s expertise lies in providing comprehensive solutions for conveyor rollers, belts, and accessories, catering to a wide range of industrial needs. From initial design and configuration to installation and meticulous troubleshooting, Jordan is adept at handling all aspects of conveyor system management. Whether you’re looking to upgrade your production line with efficient conveyor belts, require custom conveyor rollers for specific operations, or need expert advice on selecting the right conveyor accessories for your facility, Jordan is your reliable consultant. For any inquiries or assistance with conveyor system optimization, Jordan is available to share his wealth of knowledge and experience. Feel free to reach out at any time for professional guidance on all matters related to conveyor rollers, belts, and accessories.