Conveyor Roller Material Rollers in Various Sizes
Material rollers are pivotal components in the realm of conveyor systems, playing a crucial role in the seamless operation of myriad industrial applications. These rollers, by facilitating the smooth and efficient movement of materials, significantly enhance the productivity and operational efficiency of industries ranging from manufacturing to logistics and beyond. The significance of material rollers extends beyond merely propelling goods along a line; they are instrumental in optimizing the workflow, minimizing manual handling, and thereby elevating workplace safety standards. Conveyor systems, augmented with the right material rollers, become more than just a means of transport—they transform into essential tools for operational excellence. Their critical role in ensuring the swift, safe, and efficient movement of goods underscores the importance of selecting the right type of rollers, tailored to the specific needs of the operation at hand. This introduction delves into how material rollers become the backbone of industrial operations, underscoring their indispensability in enhancing efficiency and safeguarding the well-being of the workforce.
Types of Material Rollers
Material rollers come in various types, each designed to meet specific needs in different industries and applications. Here is a detailed description of the primary types of material rollers:
Gravity Rollers
- Definition: Gravity rollers rely on the force of gravity to move materials. They are unpowered and used in simple, manual systems.
- Applications: Commonly used in warehousing, packaging, and assembly lines where products need to move from one point to another without powered assistance.
- Features: Simple design, low cost, easy to install and maintain. They are typically used for lightweight items and in environments where powered rollers are not necessary.
Powered Rollers
- Definition: Powered rollers use motors to drive the rollers and move materials along the conveyor system.
- Applications: Widely used in more complex and demanding environments such as manufacturing plants, distribution centers, and airports for baggage handling.
- Features: Can handle heavier loads and provide precise control over the speed and direction of material movement. They can be integrated with sensors and control systems for automation.
Idler Rollers
- Definition: Idler rollers support the conveyor belt and the material being transported without being powered to move the belt.
- Applications: Used in conveyor systems to provide additional support and maintain tension in the belt. Common in mining, aggregate handling, and bulk material transportation.
- Features: Robust construction to handle heavy loads, low maintenance requirements. They help in reducing friction and wear on the belt, extending its lifespan.
Conveyor Rollers
- Definition: Conveyor rollers are the most common type, forming the rolling surface of conveyor belts and systems.
- Applications: Found in a variety of industries, including manufacturing, packaging, and logistics. They facilitate the continuous movement of materials along the conveyor belt.
- Features: Available in various materials, sizes, and configurations to suit different applications. They can be gravity-driven or powered, depending on the system requirements.
Custom Rollers
- Definition: Custom rollers are specifically designed to meet unique requirements that standard rollers cannot fulfill.
- Applications: Used in specialized applications where standard rollers are inadequate, such as in custom machinery, specialized manufacturing processes, or unique material handling needs.
- Features: Tailored to specific dimensions, materials, and performance characteristics. They can be engineered to handle extreme conditions, specific load capacities, and particular environmental factors.
Each type of material roller serves a distinct purpose, and the choice depends on factors such as the type of material being handled, the weight and size of the materials, the environment in which they will be used, and the specific requirements of the application. Understanding these types and their applications helps in selecting the right roller for optimizing efficiency and productivity in material handling systems.

Materials Used for Rollers
The choice of material for rollers is crucial in determining their performance, durability, and suitability for various applications. Here is a detailed description of the primary materials used for rollers:
Steel Rollers
- Description: Made from high-strength steel, these rollers are known for their durability and load-bearing capacity.
- Applications: Ideal for heavy-duty applications such as mining, metal processing, and large-scale manufacturing. They are also used in environments with high impact and abrasive materials.
- Features: Exceptional strength and durability, resistance to wear and deformation, suitable for harsh environments. They can be coated or treated to enhance corrosion resistance.
Aluminum Rollers
- Description: Lighter than steel, aluminum rollers are made from aluminum alloys that provide a good balance of strength and weight.
- Applications: Commonly used in food processing, packaging, and light manufacturing where weight savings are beneficial and corrosion resistance is needed.
- Features: Lightweight, good corrosion resistance, easy to handle and install, lower load capacity compared to steel. They are suitable for environments where hygiene and non-magnetic properties are important.
Plastic Rollers
- Description: Made from various types of plastic such as polyethylene, polypropylene, and nylon, these rollers are suitable for a range of light to medium-duty applications.
- Applications: Used in industries like food and beverage, pharmaceuticals, and chemical processing where corrosion resistance and lightweight are important.
- Features: Lightweight, corrosion-resistant, non-conductive, quiet operation, and easy to clean. They are not suitable for high-temperature or heavy-load applications.
Rubber-Coated Rollers
- Description: These rollers have a core made of steel or aluminum that is coated with a layer of rubber or similar elastomeric material.
- Applications: Used in applications where traction and gentle handling of materials are required, such as printing, textiles, and packaging.
- Features: Excellent grip and traction, cushioning effect, reduced noise and vibration, resistance to slipping. The rubber coating can be formulated for specific properties such as resistance to chemicals or high temperatures.
Composite Material Rollers
- Description: Made from advanced composite materials, these rollers combine the benefits of multiple materials to achieve desired properties.
- Applications: Suitable for specialized applications that require a combination of high strength, low weight, and resistance to specific environmental conditions, such as aerospace, automotive, and high-tech manufacturing.
- Features: High strength-to-weight ratio, customizable properties, excellent corrosion and wear resistance, and long service life. They can be designed to meet specific performance criteria for unique applications.
The choice of roller material depends on the specific requirements of the application, including load capacity, environmental conditions, and desired performance characteristics. Steel rollers offer unmatched strength for heavy-duty applications, while aluminum rollers provide a lightweight and corrosion-resistant option. Plastic rollers are ideal for environments requiring chemical resistance and cleanliness, and rubber-coated rollers are perfect for applications needing additional traction and gentle handling. Composite material rollers offer customizable solutions for advanced and specialized needs. Understanding these material properties helps in selecting the appropriate rollers to optimize efficiency, durability, and performance in material handling systems.

Applications of Material Rollers
Material rollers are critical components in various industries, facilitating efficient material handling and processing. Here is a detailed description of their applications in different sectors:
Assembly Lines
- Description: Material rollers are extensively used in assembly lines to transport parts and assemblies through various stages of production.
- Applications: Automotive manufacturing, electronics assembly, appliance production.
- Features: They enable smooth, continuous movement of components, improve workflow efficiency, and reduce manual handling. Rollers can be powered or gravity-driven depending on the assembly line requirements.
Packaging Industries
- Description: In the packaging industry, rollers help in moving products through different packaging stages, from filling and sealing to labeling and palletizing.
- Applications: Food packaging, pharmaceuticals, consumer goods.
- Features: Rollers ensure precise and efficient movement of products, enhancing packaging speed and accuracy. They can be designed to handle delicate items gently to prevent damage.
Warehousing and Distribution
- Description: Material rollers are crucial in warehousing and distribution centers for moving goods throughout the facility, from receiving to storage and shipping.
- Applications: E-commerce fulfillment centers, retail distribution, logistics hubs.
- Features: They support efficient sorting, handling, and transportation of goods, reducing labor costs and increasing throughput. Rollers can be integrated with automated systems for enhanced productivity.
Food and Beverage Industry
- Description: In the food and beverage sector, rollers are used for conveying raw materials, processed foods, and packaged products.
- Applications: Food processing plants, beverage bottling facilities, dairy production.
- Features: Rollers in this industry must meet strict hygiene standards, be easy to clean, and resist corrosion. Plastic and stainless steel rollers are commonly used to meet these requirements.
Mining and Heavy Industry
- Description: The mining and heavy industry sectors use material rollers to transport bulk materials, such as ore, coal, and aggregates, within the processing facilities.
- Applications: Mining operations, quarries, steel mills.
- Features: Rollers in these applications are designed to withstand heavy loads, abrasive materials, and harsh operating conditions. Steel and rubber-coated rollers are often used for their durability and impact resistance.
Material rollers are indispensable in various industrial applications, each requiring specific features to optimize performance. In assembly lines, they enhance production efficiency; in packaging industries, they ensure precise and rapid movement of goods. Warehousing and distribution centers rely on rollers for streamlined handling and sorting, while the food and beverage industry needs rollers that meet hygiene and safety standards. Mining and heavy industries demand robust rollers that can endure extreme conditions and heavy loads. By understanding the unique requirements of each application, the appropriate type and material of rollers can be selected to maximize operational efficiency and reliability.

The Essence of Heavy Duty Conveyor Material Rollers
Heavy duty conveyor rollers are a specialized category of material rollers designed to withstand extreme conditions and handle heavy loads with unparalleled efficiency. Characterized by their robust construction, these rollers are typically made from materials such as reinforced steel, high-impact plastics, or coated with durable rubber to resist wear, corrosion, and impact. Examples include stainless steel rollers for corrosive environments, polyurethane-coated rollers for gentle handling of delicate materials, impact rollers placed at conveyor feeding points to absorb shock, high-load capacity steel rollers for heavy industrial applications, and thermoplastic rollers known for their quiet operation and corrosion resistance.
The applications that necessitate the use of heavy duty material rollers are diverse and demanding. Industries such as mining, quarrying, and bulk material handling rely on these durable components to transport heavy and abrasive materials over long distances. Similarly, the manufacturing sector, especially in the automotive and heavy machinery segments, utilizes heavy duty rollers to move large parts and assemblies. Warehousing and distribution centers also benefit from these rollers, where the rapid movement of heavy goods is a daily requirement.
Opting for heavy duty rollers brings a plethora of benefits in terms of durability and reliability. For instance, they significantly reduce the maintenance downtime, as their robust construction can handle the wear and tear of continuous operation without frequent replacements. These rollers also improve safety by ensuring the conveyor system operates smoothly under heavy load conditions, reducing the risk of malfunctions that could lead to accidents. Furthermore, heavy duty rollers enhance operational efficiency by allowing for the swift movement of heavy materials, thereby increasing throughput. Their durability ensures long-term cost savings, as the initial investment in high-quality rollers pays off over time with reduced need for repairs and replacements. Lastly, the reliability of these rollers supports uninterrupted operations, critical for meeting production deadlines and maintaining supply chain continuity.
A Guide to Replacement Conveyor Material Rollers
The timely replacement of conveyor rollers is pivotal in maintaining the efficiency and longevity of conveyor systems. Material rollers, integral to these systems, must be periodically assessed and replaced to prevent downtime, ensure safety, and uphold productivity. For instance, in sectors like mining and quarrying, worn-out rollers can lead to conveyor belt misalignment, causing material spillage and operational delays. In manufacturing, damaged rollers can result in the uneven movement of parts, affecting product quality. Distribution centers reliant on speedy sorting and transportation of goods cannot afford the delays caused by malfunctioning rollers. In the food and beverage industry, compromised rollers can lead to hygiene concerns and product contamination. Similarly, in the recycling sector, broken or inefficient rollers can obstruct the continuous flow of materials, impacting the sorting and processing efficiency.
Identifying the signs that indicate the need for roller replacement is crucial. Common indicators include visible wear and tear, such as cracks and chips on the roller surface, which can impair movement and damage conveyor belts. Unusual noises, such as grinding or squeaking, often signal internal bearing failure. Roller rotation issues, where rollers are stuck or turn with difficulty, can cause conveyor belt slippage or misalignment. Inconsistent movement of materials, manifesting as jerks or stalls, indicates uneven roller surface or diameter differences due to wear. Lastly, increased energy consumption can be a subtle sign of deteriorating roller efficiency, as more power is required to move the conveyor belt over damaged or seized rollers.
Choosing the right replacement rollers involves several key considerations. Weight capacity is paramount; selecting rollers that can adequately support the weight of conveyed materials without deformation or failure is essential. The choice of materials for the rollers, such as steel, plastic, or rubber-coated, should be based on the nature of the materials being conveyed and the operational environment. For example, steel rollers are suited for heavy-duty applications and harsh conditions, while plastic rollers might be preferred for lighter loads and cleaner environments. The operational environment also influences the choice; in corrosive or humid conditions, corrosion-resistant materials like stainless steel or coated rollers are ideal. Additionally, the diameter and length of the rollers must match the existing conveyor framework to ensure compatibility and smooth operation.
Gravity Material Rollers Conveyor: A Closer Look
Gravity roller conveyors utilize the natural force of gravity to move goods along the conveyor path without the need for an external power source. This system comprises a series of material rollers set at a slight decline or leveraged by manual force, allowing items to glide over them with minimal friction. The simplicity of this design offers significant benefits, including reduced energy costs, since it eliminates the need for motors or electrical power. It also boasts low maintenance requirements, as there are fewer moving parts that can wear out or break down. Furthermore, gravity conveyors provide a safe and quiet operation, making them suitable for many work environments.
Ideal applications for gravity roller conveyors include material handling tasks that involve lightweight to medium-weight products. These conveyors are especially favored in pick-and-pack operations, assembly lines, and loading docks. They are also commonly used in distribution centers and warehouses for sorting packages and in manufacturing settings for moving parts between different stages of production processes. The simplicity and efficiency of gravity conveyors make them an excellent choice for sectors looking to optimize operational workflow without substantial investments.
Comparing gravity roller conveyors with powered conveyor systems highlights several key differences and preferences based on specific operational needs.
This comparison shows that gravity conveyors are preferred when operational simplicity, cost-efficiency, and quiet, safe environments are prioritized. In contrast, powered conveyor systems offer greater versatility and control, especially for handling heavier loads over longer distances with variable speeds.
Industrial Conveyor Material Rollers
Industrial conveyor rollers are crucial components in the manufacturing, distribution, and logistics sectors, serving as the backbone of material handling systems. These material rollers facilitate the movement of goods through production lines, warehouses, and distribution centers, ensuring efficiency and speed in operations. Their versatility allows for customization according to specific industry needs, from the food sector to heavy machinery manufacturing.
The materials used in the construction of conveyor rollers are selected based on the application’s specific requirements, including the weight of the items being transported, the environment (e.g., presence of chemicals, temperature extremes), and the desired durability and friction characteristics. Here are five examples showcasing the diversity of material rollers and their applications:
- Steel Rollers: Known for their strength and durability, steel rollers are commonly used in heavy manufacturing, mining, and quarrying. They are capable of handling heavy loads and are resistant to impact, making them suitable for harsh industrial environments.
- Plastic Rollers: Lightweight and corrosion-resistant, plastic rollers are ideal for light to medium-duty applications. They are often found in food processing and pharmaceutical industries, where hygiene and cleanliness are paramount. Plastic rollers also offer a quiet operation, which is beneficial in environments where noise reduction is desired.
- Rubber-Coated Rollers: These rollers provide additional grip and reduce slippage, making them perfect for moving irregularly shaped items or materials that require gentle handling. Industries like paper printing and packaging frequently utilize rubber-coated rollers to prevent damage to delicate products.
- Stainless Steel Rollers: Specifically designed for use in corrosive environments or where strict hygiene standards are enforced, stainless steel rollers are prevalent in chemical processing, food production, and pharmaceutical industries. Their resistance to corrosion and easy cleaning properties make them indispensable in these settings.
- High-Temperature Rollers: Fabricated from materials capable of withstanding extreme temperatures, these rollers are employed in applications like heat treating, metalworking, and ceramics manufacturing. They ensure the reliable transportation of materials through processes involving high heat, without degradation.
These examples highlight the adaptability of material rollers to various industrial needs, underscoring their essential role in optimizing the flow of materials across different stages of production, warehousing, and distribution. The choice of roller material directly impacts the efficiency, safety, and cost-effectiveness of conveyor systems, making it crucial to select the most appropriate type based on the specific operational demands.
Material Rollers Price Considerations
When it comes to acquiring material rollers for conveyor systems, understanding the factors that influence their price is crucial for making informed purchasing decisions. The cost of conveyor rollers is significantly affected by the material from which they are made, their size and type, and the quantity ordered.
Material: The choice of material has a direct impact on price. Steel rollers, for example, are typically more expensive than plastic rollers due to their durability and capacity to handle heavier loads. Stainless steel and specialized coatings for corrosion resistance or high-temperature applications further increase the cost.
Size: Larger rollers require more material to manufacture and are consequently more expensive. The diameter and length of the rollers must be tailored to the specific requirements of the conveyor system, affecting the overall price.
Type: The complexity of the roller design influences its cost. Simple gravity rollers are generally less expensive than motorized or specialty rollers designed for specific functions, such as accumulating or sorting materials.
Quantity: Ordering in bulk often results in a lower cost per unit due to economies of scale. Suppliers may offer discounts for large orders, making it a cost-effective option for larger projects or for companies looking to stockpile spares for future maintenance.
Balancing cost with quality and longevity in roller selection involves considering the long-term operational costs rather than just the initial purchase price. Investing in higher-quality, more durable rollers can lead to reduced maintenance and replacement costs over time, offering better value for money. For critical applications, opting for rollers that offer the best performance and longevity may be more economical in the long run, even if the upfront cost is higher.
To achieve this balance, it’s advisable to conduct a thorough analysis of the operational environment and the specific requirements of the conveyor system. Consider factors such as the expected load, the type of materials being conveyed, and the conditions under which the system operates (e.g., exposure to chemicals, temperature extremes). This analysis can help identify the most suitable type of material rollers that will provide the best return on investment through durability, reduced downtime, and efficient operation.

Sizing Matters: From 4 Inch to 1 Inch Diameter Conveyor Material Rollers
The size of material rollers, particularly their diameter, plays a critical role in the design and functionality of conveyor systems. The diameter of a roller affects the conveyor’s ability to handle different types of loads, its speed, and its durability. Larger rollers can support heavier loads and reduce the overall wear on the system by offering a larger surface area and reducing the rotation needed to move the conveyor belt. Conversely, smaller rollers are suited for lighter loads and can be used to create compact conveyor designs, beneficial in environments where space is limited.
4 Inch Diameter Conveyor Rollers
Four-inch diameter material rollers are typically utilized in heavy-duty applications where the conveyor system must support substantial loads. These larger rollers are common in industries such as mining, bulk material handling, and heavy manufacturing. For example, a mining operation transporting large volumes of ore over long distances would benefit from 4-inch rollers, as their size and strength can easily support the weight of the ore, reducing the strain on the conveyor belt and motor. Additionally, these rollers provide a smoother operation for heavy loads, minimizing the risk of jams or disruptions in the flow of materials.
1 Inch Diameter Conveyor Rollers
On the other hand, 1-inch diameter material rollers are designed for lighter applications and situations where conveyor systems need to navigate tight spaces. These rollers are often found in electronics manufacturing, pharmaceuticals, and food processing industries. For instance, in a pharmaceutical packaging line, 1-inch rollers can be used to transport small boxes of medicine through various stages of packaging and inspection. The smaller diameter allows for tighter curves and more flexibility in conveyor layout, essential in cleanroom environments where space is meticulously organized.
The selection between 4 inch and 1 inch diameter conveyor rollers ultimately depends on the specific requirements of the application, including the weight of the materials being conveyed, the available space for the conveyor system, and the desired speed of operation. In heavy-duty settings where durability and load capacity are paramount, 4-inch rollers provide the necessary support and longevity. In contrast, for applications requiring high precision, flexibility, and efficiency in limited spaces, 1-inch rollers offer an ideal solution. Understanding the significance of roller size enables engineers and designers to tailor conveyor systems that are optimally configured for their intended use, ensuring efficient, reliable, and cost-effective material handling solutions.
Installation and Maintenance: Conveyor Material Rollers with Bracket
The proper installation and regular maintenance of material rollers and their brackets are crucial for the optimal performance and longevity of conveyor systems. Ensuring that these components are correctly set up and routinely checked can significantly impact the efficiency and reliability of the material handling process.
Importance of Proper Installation and Maintenance
Correct installation ensures that material rollers are aligned, level, and securely fitted to prevent operational issues such as belt misalignment, uneven wear on rollers, and unnecessary stress on the conveyor structure. It’s vital that each roller is installed with precision to maintain a smooth and efficient conveyor operation. Regular maintenance, including inspection, cleaning, and lubrication (where applicable), prevents the premature wear of rollers and brackets, reduces the likelihood of system downtime, and extends the lifespan of the conveyor system. Maintenance routines should include checking for signs of wear or damage, ensuring rollers rotate freely without excessive noise, and verifying the integrity of the mounting brackets.
Benefits of Using Rollers with Brackets for Ease of Installation and Stability
Rollers fitted with brackets offer significant advantages in terms of installation and stability. These brackets facilitate a straightforward and quick installation process, allowing for easy alignment and adjustment. The design of roller brackets ensures that rollers are securely mounted, providing a stable and uniform support across the conveyor system. This stability is crucial for maintaining consistent contact between the conveyor belt and rollers, which is essential for the smooth transportation of materials.
The use of brackets also allows for easier maintenance and replacement. Rollers can be quickly removed and replaced without the need for extensive disassembly, minimizing downtime and maintaining productivity. Additionally, the enhanced stability provided by brackets reduces vibrations and wear, leading to a quieter operation and longer service life for both the rollers and the conveyor belt.
The integration of material rollers with brackets into conveyor systems not only simplifies the installation process but also contributes to the overall stability and efficiency of material handling operations. Proper installation, combined with regular maintenance, ensures that conveyor systems remain reliable and effective, supporting uninterrupted operations and extending the lifespan of the material handling infrastructure.
FAQs About Material Rollers
Conveyor rollers are crafted from a variety of materials, each chosen for its unique properties to suit specific operational needs. The most common materials include steel, stainless steel, plastic, and rubber-coated rollers. Steel rollers are favored for their strength and durability, making them ideal for heavy-duty applications where high load-bearing capacity is a necessity. Stainless steel rollers offer added resistance to corrosion and are preferred in environments where cleanliness and exposure to chemicals are concerns, such as in the food processing and pharmaceutical industries. Plastic rollers provide a lightweight and corrosion-resistant alternative, suitable for conveying lighter loads in cleaner environments; they are often used in electronic and food packaging industries due to their non-marking properties. Lastly, rubber-coated rollers are used where additional grip is needed to move materials smoothly, particularly useful in the paper printing and packaging sectors. The choice of material directly impacts the roller’s performance, lifespan, and suitability for specific tasks, making it essential to select the right material based on the application’s demands.
The rollers on a conveyor, known as conveyor rollers, are cylindrical components that facilitate the movement of materials along the conveyor belt. They are mounted along the length of the conveyor frame and can be either powered, driving the belt and materials forward, or unpowered, where they simply support and guide the belt under the force of gravity or manual push. Conveyor rollers play a crucial role in the efficient operation of the conveyor system, enabling the smooth and continuous flow of goods. They are designed to withstand the load of the materials being transported, reduce friction, and minimize wear on the conveyor belt. The selection of appropriate rollers, considering their diameter, material, and bearing type, is vital for optimizing conveyor performance and durability.
Roller conveyors utilize rollers made from materials such as steel, stainless steel, plastic, aluminum, and rubber coatings. Each material offers distinct advantages and is chosen based on the conveyor’s application, environmental conditions, and the nature of the materials being handled. Steel rollers are common in heavy-duty applications for their high strength and durability. Stainless steel rollers are preferred in corrosive environments or in industries requiring strict hygiene standards. Plastic rollers are selected for lighter applications or where corrosion resistance is a priority. Aluminum rollers offer a lightweight yet sturdy alternative, often used in portable conveyor systems. Rubber-coated rollers provide additional traction and noise reduction, beneficial in delicate handling situations. The diversity in roller materials allows for custom configurations of roller conveyors to meet the specific needs of various industries and applications.
Conveyor rollers come in several types, each designed to fulfill specific functions within a conveyor system. The primary types include gravity rollers, drive rollers, impact rollers, and return rollers. Gravity rollers operate without external power, relying on gravity or manual force to move items; they are cost-effective and suitable for simple, lightweight conveying tasks. Drive rollers are motorized and propel the conveyor belt, essential for automated systems where precise control over movement and speed is required. Impact rollers are placed at points where material is loaded onto the conveyor, designed to absorb shock and protect the belt and system from damage. Return rollers support the underside of the belt as it loops back to the start. Other specialized types include grooved rollers for belt-driven conveyors, tapered rollers for curves and corners, and plastic rollers for lightweight or clean applications. Each type serves a unique purpose, contributing to the conveyor system’s overall efficiency and effectiveness.
Last Updated on August 6, 2024 by Jordan Smith
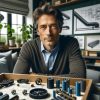
Jordan Smith, a seasoned professional with over 20 years of experience in the conveyor system industry. Jordan’s expertise lies in providing comprehensive solutions for conveyor rollers, belts, and accessories, catering to a wide range of industrial needs. From initial design and configuration to installation and meticulous troubleshooting, Jordan is adept at handling all aspects of conveyor system management. Whether you’re looking to upgrade your production line with efficient conveyor belts, require custom conveyor rollers for specific operations, or need expert advice on selecting the right conveyor accessories for your facility, Jordan is your reliable consultant. For any inquiries or assistance with conveyor system optimization, Jordan is available to share his wealth of knowledge and experience. Feel free to reach out at any time for professional guidance on all matters related to conveyor rollers, belts, and accessories.