Rise and Decline: Maximum Angle of Belt Conveyor
In the realm of material handling and industrial operations, the maximum angle of belt conveyor stands as a critical factor in designing efficient conveyor systems. This concept is pivotal in determining how effectively a conveyor can transport materials, especially in challenging conditions where space and material characteristics vary. Understanding the maximum angle of belt conveyor is essential across various industries, from mining to packaging, as it directly influences the conveyor’s capacity, safety, and overall performance. This introduction delves into the significance of conveyor belt angle, exploring its impact on the design and operational efficiency of conveyor systems. By comprehensively grasping this concept, engineers and operators can optimize conveyor functionality, ensuring seamless material handling in diverse industrial environments.
The Concept of Maximum Angle of Belt Conveyor
What is the Maximum Angle of Belt Conveyor
The maximum angle of belt conveyor is a critical factor in the design and operation of material handling systems. This angle determines the steepest incline at which a conveyor can operate while effectively transporting materials.
Definition and Importance
- Definition: The maximum angle of a belt conveyor, often referred to as the incline limit, is the highest angle at which the conveyor can function without the risk of material sliding back down the belt.
- Significance: This angle is crucial for ensuring the conveyor’s efficiency and safety. It affects the conveyor’s design, the choice of conveyor belt material, and the overall system’s capacity to handle different types of loads.
Impact on Material Transport
- Material Retention: The maximum angle directly influences how well materials stay on the belt during transportation. Beyond this angle, materials may start to roll or slide back, leading to inefficiencies and potential hazards.
- Conveyor Design Considerations: Conveyor systems must be designed with the maximum angle in mind to ensure that materials are transported smoothly and securely. This includes considering the type of material, belt texture, and conveyor speed.
Factors Affecting the Maximum Angle
- Material Characteristics: The type of material being conveyed (e.g., granularity, moisture content) significantly impacts the maximum angle. For instance, dry, granular materials can be transported at steeper angles than wet or sticky substances.
- Belt Design: Features such as cleats, sidewalls, and the overall belt texture play a vital role in determining the maximum angle. These features provide additional grip and support to prevent material slippage.
The maximum angle of belt conveyor is a fundamental aspect that dictates the efficiency and safety of the material handling process. Understanding and correctly implementing this angle is essential for the optimal design and operation of conveyor systems.
Maximum Angle of Belt Conveyor Formula
Calculating the Optimal Incline for Belt Conveyors
The maximum angle of belt conveyor is a critical value that determines the efficiency and feasibility of the conveyor system. This section introduces the formula used to calculate this angle and explains its application in real-world conveyor design scenarios.
Introduction to the Calculation Formula
- Troughed belt conveyors handle lower than to 18° inclines; steep incline conveyors manage up to 90° with plain belts limited to 20°.
- Formula Structure: While the specific formula can vary based on conveyor design and material type, a common form is:
Maximum Angle = arctan(Coefficient of Friction)
. This formula calculates the angle in radians or degrees, providing a theoretical maximum incline based on frictional forces.
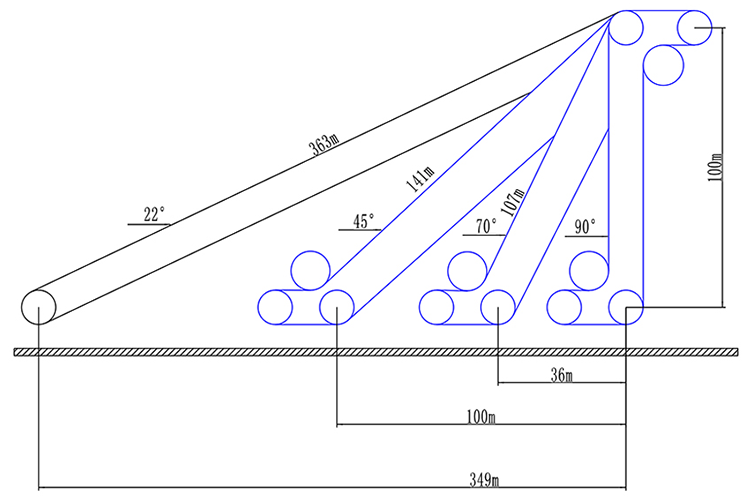
Derivation and Application
- Frictional Considerations: The coefficient of friction between the material and the conveyor belt is a key variable. It depends on both the material’s properties (like texture and moisture content) and the belt’s surface characteristics.
- Real-World Application: In practical scenarios, this formula helps designers and engineers determine the feasibility of transporting certain materials at specific inclines. It guides the selection of belt materials and the design of conveyor systems to ensure efficient and safe operation.
Limitations and Considerations
- Safety Margins: In practice, engineers often apply safety margins to the calculated maximum angle to account for variations in material properties and operational conditions.
- Material Behavior: The formula assumes uniform material behavior, which might not always be the case in real-world conditions where materials can behave unpredictably.
The maximum angle of belt conveyor formula is a fundamental tool in the design and operation of conveyor systems. It provides a theoretical basis for determining the steepest incline at which a conveyor can operate effectively, guiding decisions in conveyor design and material handling strategies.
Boost efficiency with our high-performance belt conveyors. Contact us now!
Using a Maximum Angle of Belt Conveyor Calculator
Navigating Online Tools for Conveyor Angle Determination
Online calculators for determining the maximum angle of a belt conveyor are valuable tools in the planning and design phase of conveyor systems. This section guides how to use these calculators effectively and illustrates their application in various scenarios.
Guide to Using Online Calculators
- Input Requirements: Typically, these calculators require inputs such as the type of material being conveyed, the material’s bulk density, the conveyor belt’s width, and the desired throughput. Some calculators might also ask for the coefficient of friction between the material and the belt.
- Process of Calculation: After entering the necessary data, the calculator processes the information to provide the maximum angle at which the conveyor can operate without material slippage. This angle is crucial for designing an efficient and safe conveyor system.
Examples of Application Scenarios
- Scenario 1: For a mining operation transporting dry, granular material, the calculator can help determine the steepest incline at which the material can be moved efficiently.
- Scenario 2: In an agricultural setting, where lighter materials like grains are conveyed, the calculator can assist in optimizing the conveyor design for maximum productivity.
Benefits of Using Calculators
- Time Efficiency: These calculators save time by quickly providing essential data needed for conveyor design.
- Accuracy: They offer a more accurate way to estimate the maximum angle, reducing the risk of design errors and operational inefficiencies.
Considerations When Using Calculators
- Validation of Results: It’s advisable to validate the calculator’s results with manual calculations or consult with conveyor system experts, especially for complex or large-scale projects.
- Understanding Limitations: Online calculators provide estimates based on standard conditions and may not account for specific operational nuances. It’s important to consider these limitations in the planning process.
Using a maximum angle of belt conveyor calculator is an efficient and effective way to estimate the optimal incline for conveyor systems. These tools play a crucial role in the preliminary stages of conveyor design, helping to ensure that the final system is both efficient and safe for its intended application.
Maximum Angle of Belt Conveyor: Calculating the Optimal Incline
Understanding the maximum angle of belt conveyor is crucial for designing an efficient material handling system. The angle calculation is a process that determines the steepest incline at which a conveyor belt can operate effectively without material rollback. This calculation is not just a theoretical exercise; it has practical implications in various industries where conveyors are essential.
The first step in calculating the maximum angle of a belt conveyor is to consider the type of material being transported. Different materials have varying properties like bulk density, particle size, and moisture content, all of which influence the material’s behavior on the conveyor. For instance, dry, fine particles may require a shallower angle compared to larger, more cohesive materials.
The design of the conveyor belt itself is another critical factor. Features such as the belt’s width, texture, and the presence of cleats or ribs can significantly affect the maximum angle. A smooth belt may not be able to transport materials at the same angle as a belt with a rough surface or cleats designed to prevent slippage.
Conveyor speed is also a vital consideration. Faster belt speeds can cause materials to slide back more easily, especially at steeper angles. Therefore, the speed must be adjusted according to the angle to ensure efficient material movement.
Other factors that need to be taken into account include the conveyor’s overall length, the height of the incline, and environmental conditions like humidity and temperature, which can affect material properties.
After considering these factors, calculations can be made using specific formulas or by employing conveyor angle calculators available online. These tools often require inputting the conveyor’s dimensions and the material characteristics to provide an estimated maximum angle for operation.
It is essential to remember that these calculations provide a starting point. Real-world testing and adjustments are often necessary to fine-tune the conveyor setup for optimal performance.
Calculating the maximum angle of belt conveyor involves a detailed analysis of material properties, conveyor design, and operational parameters. This process is vital to ensure that the conveyor operates efficiently, safely, and effectively in transporting materials.
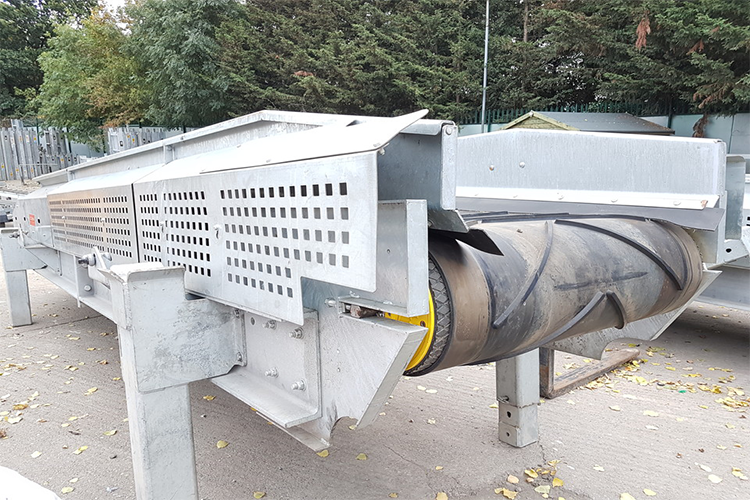
Maximum Angle of Belt Conveyor: Understanding the Inclination Formula
The maximum angle of belt conveyor about inclination is a pivotal factor in conveyor design, dictating the steepest angle at which the conveyor can operate efficiently and safely. This section delves into the formula used to calculate this critical angle and examines the variables that influence it.
Exploring the Inclination Formula
- Fundamental Formula: The core formula for determining the maximum angle of inclination is
Maximum Incline Angle = arctan(Coefficient of Friction)
. This formula calculates the angle in degrees, providing the theoretical maximum incline based on the frictional forces between the conveyor belt and the material being transported. - Coefficient of Friction: Central to this formula is the coefficient of friction, which varies depending on the material type and the conveyor belt’s surface. This coefficient is a measure of how easily the material can slide over the belt surface.
Variables Impacting Conveyor Performance
- Conveyor Belt Material Properties: The nature of the material (e.g., granularity, moisture content, and bulk density) significantly affects the coefficient of friction. For instance, wet or sticky materials may have a higher coefficient, allowing for a steeper incline.
- Belt Texture and Design: The design of the conveyor belt, including its texture, cleats, and overall composition, plays a crucial role. Belts with rough textures or fitted with cleats can transport materials at steeper angles by increasing the effective coefficient of friction.
- Environmental Factors: External conditions like humidity, temperature, and exposure to elements can alter the material’s behavior on the belt, impacting the maximum angle of inclination.
Minimum and Maximum Slope Angle on a Conveyor
The minimum and maximum slope angles for a conveyor depend largely on the type of material being transported, the design of the conveyor belt, and the overall configuration of the system. Here’s a general guideline:
Minimum Slope Angle: The minimum slope is often close to horizontal, especially if the goal is to prevent the backslide of materials. For materials that are non-adhesive and free-flowing, a gentle slope may suffice, typically around 0 to 5 degrees.
Maximum Slope Angle:
- Non-slippery, dry, and cohesive materials: These can be transported on steeper inclines. The maximum angle can range from 18 to 30 degrees, with some specially designed belts capable of handling up to 45 degrees or more under ideal conditions.
- Wet or sticky materials: These require a shallower slope to prevent the material from sticking to the belt or sliding back down. Typical maximum slopes for these materials might range from 10 to 20 degrees.
- Loose materials such as grains or coal: These might slide back if the angle is too steep, generally limiting maximum slopes to around 15 to 25 degrees.
Special conveyor belts with high grip surfaces or cleats can handle steeper angles. These are often used in applications requiring the vertical transport of bulk materials, such as in mining or agricultural industries.
The slope angle of a conveyor can significantly vary based on the type of product being moved, the design of the conveyor, and the specific characteristics of the belt. Here’s how each of these factors influences the choice of slope angle:
Type of Product:
- Texture and Cohesiveness: Smooth, non-cohesive materials like certain minerals or grains may require shallower angles to prevent slippage. In contrast, cohesive or sticky materials may adhere to the belt better, allowing for steeper slopes.
- Size and Weight: Heavier and larger particles can be transported on steeper slopes because their weight helps prevent rollback.
- Moisture Content: Wet materials might necessitate a shallower slope to prevent slippage or sticking to the belt.
Type of Conveyor:
- Standard Belt Conveyors: These typically handle moderate slopes, generally not exceeding 20 degrees, depending on the belt and product characteristics.
- Inclined or Declined Conveyors: These are specifically designed for steeper slopes and can include features like cleated belts or side walls to increase the angle at which materials can be transported without sliding back.
- Pocket Belts or Closed Belt Conveyors: These can handle very steep inclines, even up to vertical, as materials are contained in pockets or within a fully enclosed belt.
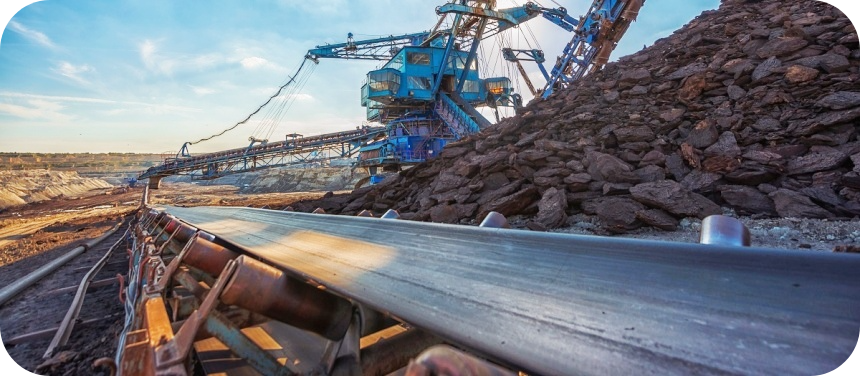
Belt Type:
- Smooth Belts: Generally used for conveying on a horizontal or low incline as they can easily slip under steeper conditions.
- Textured or Cleated Belts: Designed for steeper inclines, these belts have raised sections or cleats that help hold the material in place as it ascends or descends.
- Material and Build Quality: High-quality, durable belts designed for specific environmental conditions (like heat, cold, or abrasiveness) can operate at different angles effectively.
By carefully considering these factors, conveyor systems can be optimized for specific materials and conditions, ensuring efficient and reliable material handling.
Practical Application of the Formula
- Design and Safety Considerations: When designing a conveyor system, this formula helps in determining the safest and most efficient angle for material transport. It guides decisions on belt selection and system layout.
- Customization for Specific Needs: The formula can be adjusted for specific operational requirements, considering the unique characteristics of the material and the operational environment.
- Limitations and Safety Margins: While the formula provides a theoretical maximum, practical application often involves incorporating safety margins. These margins account for potential variations in material properties and ensure the longevity and safety of the conveyor system.
The maximum angle of inclination formula is an essential tool in the design and operation of belt conveyors. Understanding and accurately applying this formula ensures that conveyor systems are optimized for both performance and safety, tailored to the specific needs of the material being transported.
Maximum Angle of Belt Conveyor: Conveyor Slope and Material Behavior
The conveyor slope angle is a critical aspect that directly correlates with the maximum angle of belt conveyor. This angle not only influences the conveyor’s design but also affects its operational efficiency. Understanding the relationship between the slope angle and the maximum angle of inclination is essential for ensuring that the conveyor operates effectively and safely under various conditions.
The analysis of the conveyor slope angle involves evaluating how different materials behave when transported at various inclines. Each type of material has unique properties that affect its movement on the conveyor. For instance, materials with a high degree of cohesiveness or larger particle sizes may be less likely to slide back at steeper angles, allowing for a higher maximum angle of inclination. In contrast, fine, granular materials or those with a lower coefficient of friction may require a shallower slope to prevent slippage and maintain control over the material flow.
The maximum angle of belt conveyor is also influenced by the material’s bulk density and moisture content. Heavier and wetter materials might necessitate a lower slope angle to ensure that the conveyor can transport them effectively without overloading the system or causing spillage.
Additionally, the shape of the material plays a significant role in determining the suitable conveyor slope angle. Irregularly shaped or spherical materials may behave unpredictably at certain angles, potentially leading to operational challenges. Understanding these material characteristics is crucial for selecting the right conveyor design and slope angle.
It’s important to note that the maximum angle of belt conveyor is not a fixed value but varies depending on these material characteristics. Therefore, a thorough assessment of the material to be conveyed is necessary to determine the optimal slope angle for a specific application.
The conveyor slope angle is a vital factor in conveyor design, directly impacting the maximum angle of inclination. Careful consideration of the material properties and behavior at various angles is essential for designing an efficient and effective conveyor system. This understanding ensures that the conveyor not only meets the operational requirements but also maintains safety and reliability throughout its service life.
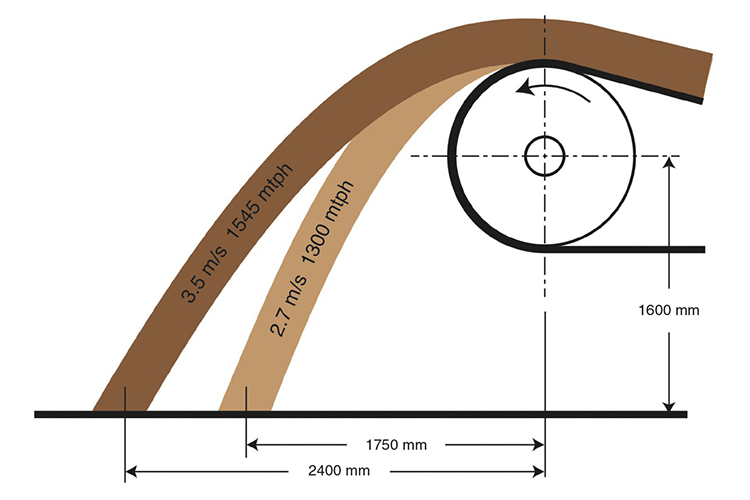
Maximum Angle of Belt Conveyor: Gravity Conveyor Slope Calculation
Understanding the impact of gravity on the slope of a conveyor belt is crucial for designing an efficient gravity conveyor system. This section explores how gravity influences the slope calculation of a belt conveyor and outlines methods to determine the optimal slope for gravity conveyors, ensuring efficient material flow.
Impact of Gravity on Conveyor Slope
- Role of Gravity: In gravity conveyors, gravity is the driving force that moves the material along the conveyor belt. The slope of the conveyor must be steep enough to allow gravity to overcome the friction between the material and the conveyor belt, enabling smooth movement.
- Balancing Slope and Speed: The slope must be carefully calculated to balance the gravitational force and the desired speed of material movement. Too steep a slope can cause materials to move too quickly, leading to potential spillage or damage, while too shallow a slope may not provide enough force for movement.
Calculating the Optimal Slope for Gravity Conveyors
- Basic Slope Calculation: The basic formula for calculating the slope of a gravity conveyor is
Slope (in degrees) = arctan(Height / Length)
. This formula gives a starting point for determining the conveyor’s angle. - Considering Material Characteristics: The characteristics of the material being conveyed, such as weight, size, and shape, play a significant role in slope calculation. Heavier and larger materials may require a steeper slope compared to lighter materials.
- Friction Factor: The friction factor between the material and the conveyor belt surface must be considered. Materials with higher friction coefficients may require a steeper slope to ensure movement.
- Safety and Efficiency Considerations: The optimal slope must ensure safety and efficiency. It should prevent excessive speed that could lead to material loss or safety hazards, while also ensuring that materials do not stall on the conveyor.
Practical Application in Conveyor Design
- Testing and Adjustments: Practical testing is often necessary to fine-tune the slope based on real-world conditions. Adjustments may be required to achieve the desired material flow rate and to accommodate specific operational requirements.
- Use of Slope Calculators: Online calculators and engineering tools can assist in the initial estimation of the conveyor slope. These tools take into account various factors to provide a more accurate calculation.
- Expert Consultation: Consulting with conveyor system experts can provide valuable insights, especially for complex or large-scale gravity conveyor systems.
Calculating the slope of a gravity conveyor is a critical aspect of conveyor design in terms of the maximum angle of belt conveyor, directly influenced by gravity and material characteristics. A well-calculated slope ensures efficient material flow, operational safety, and overall system effectiveness, making it a key consideration in the design and operation of gravity conveyor systems.
You May Also Want to Learn: What’s the Difference of Incline Conveyors Vs. Steep Incline Conveyors?
Incline conveyors and steep incline conveyors serve similar purposes but are designed for different degrees of slope and types of material handling. Understanding their differences is essential when selecting the right conveyor system for specific applications. Here’s a breakdown of the key differences:
Incline Conveyors
- Slope Angle: Typically, incline conveyors have a slope angle ranging from about 15 to 30 degrees. They are designed to handle moderate inclines where the material can be transported upward without significant risk of sliding back down.
- Belt Type: Incline conveyors usually employ traditional conveyor belts made of rubber or PVC with a flat or slightly textured surface, sometimes outfitted with cleats to prevent slippage.
- Applications: These conveyors are suited for a wide range of applications in warehouses, packaging industries, or any environment where materials need to be moved from one elevation to another at a moderate slope.
- Material Handling: Ideal for handling packed goods or materials that are relatively stable on the belt, such as boxed items, bags, or stable aggregates.
Steep Incline Conveyors
- Slope Angle: Steep incline conveyors can handle much sharper angles, typically from about 30 to 90 degrees. These conveyors are specifically designed to transport materials vertically or at a high incline.
- Belt Type: These conveyors often use specialized belts with significant texturing, cleats, or even sidewalls to hold materials in place as they move vertically. The belts are engineered to prevent material rollback.
- Applications: Steep incline conveyors are commonly found in mining, agricultural processing, or where space is limited and materials need to be conveyed over very steep ascents.
- Material Handling: They are especially useful for bulk materials like grains, sand, gravel, or any other loose material that needs to be moved upwards without spillage.
The primary difference lies in the angle of incline and the specialized designs to accommodate those angles. While both types of conveyors elevate materials, steep incline conveyors are equipped to handle much steeper slopes and more challenging material handling scenarios, thanks to their enhanced design features like cleated and sidewalled belts. This makes steep incline conveyors suitable for industries where vertical or near-vertical material transport is necessary, maximizing space efficiency and handling capabilities.
Reduce downtime with our superior belt conveyors. Contact our experts now!
FAQs about Maximum Angle of Belt Conveyor
The angle of incline for a belt conveyor, often referred to as the maximum incline angle, is the steepest angle at which the conveyor can operate and effectively move materials without them sliding back. This angle varies depending on the material being conveyed and the design of the conveyor. For standard belt conveyors, the maximum incline angle typically ranges from 15 to 25 degrees. However, with specialized designs and materials, such as cleated or ribbed belts, the angle can be significantly steeper.
The degree of a belt conveyor usually refers to its incline angle. This is the angle at which the conveyor is set relative to the horizontal plane. The specific degree varies based on the conveyor design and the type of material being transported. Standard conveyors typically have a degree of incline up to 25 degrees, while specialized high angle conveyors can operate at inclines of 30 degrees or more.
A high angle belt conveyor is a type of conveyor system designed to transport materials at steep inclines or even vertically. These conveyors are capable of handling inclines greater than the typical maximum of 20-25 degrees seen in standard belt conveyors. High angle conveyors often use additional features like sidewalls and cleated belts to securely transport materials at inclines of up to 90 degrees in some cases. They are particularly useful in applications where space is limited or where materials need to be lifted from deep pits or mines.
The maximum angle for a screw conveyor, also known as an auger conveyor, is typically around 45 degrees. Beyond this angle, the efficiency of the conveyor in moving materials decreases significantly. The exact maximum angle can vary depending on factors like the design of the screw and the properties of the material being conveyed. Screw conveyors are often used for handling bulk materials in industries such as agriculture, mining, and manufacturing.
Last Updated on June 6, 2024 by Jordan Smith
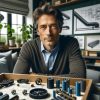
Jordan Smith, a seasoned professional with over 20 years of experience in the conveyor system industry. Jordan’s expertise lies in providing comprehensive solutions for conveyor rollers, belts, and accessories, catering to a wide range of industrial needs. From initial design and configuration to installation and meticulous troubleshooting, Jordan is adept at handling all aspects of conveyor system management. Whether you’re looking to upgrade your production line with efficient conveyor belts, require custom conveyor rollers for specific operations, or need expert advice on selecting the right conveyor accessories for your facility, Jordan is your reliable consultant. For any inquiries or assistance with conveyor system optimization, Jordan is available to share his wealth of knowledge and experience. Feel free to reach out at any time for professional guidance on all matters related to conveyor rollers, belts, and accessories.