Metric Conveyor Rollers: A Comprehensive Introduction
Conveyor systems are integral to the manufacturing and distribution sectors, facilitating the efficient movement of goods across facilities. Central to these systems are the rollers that support and drive conveyor belts. Among these, metric conveyor rollers are particularly vital due to their standardization and adaptability in various industrial applications globally. These rollers are designed to meet specific metric measurements, which ensures consistency and interchangeability across different machinery and setups. The widespread use of metric conveyor rollers is attributed to their ability to enhance operational efficiency and reduce downtime in production lines. Industries ranging from automotive to food processing rely heavily on these robust and precise components to maintain smooth operational flows and meet stringent production demands.
The Basics of Metric Conveyor Rollers
Metric conveyor rollers are essential components in automated conveyor systems, defined by their adherence to the metric system of measurements. These rollers typically feature diameters and lengths measured in millimeters, offering precision that is crucial for seamless integration into various industrial setups. The design and sizing of metric conveyor rollers follow a standardized approach, which facilitates compatibility and replacement across different equipment and countries that utilize the metric system.
One of the primary distinctions between metric conveyor rollers and their imperial counterparts lies in the measurement system used. The metric system uses units such as millimeters and centimeters, which are universally accepted in scientific and industrial applications worldwide, ensuring a broader applicability and ease of use. In contrast, the imperial system utilizes inches and feet, which can lead to conversion errors and inconsistencies when used in industries that standardize on the metric system.
The table below highlights some key differences and conversion factors between these two systems in conveyor applications:
This distinction is crucial as it impacts the interoperability of conveyor components across different countries and industries. By adopting metric conveyor rollers, companies can ensure a more universal fit and easier procurement of replacement parts, enhancing maintenance efficiency and reducing operational disruptions.
Types of Metric Conveyor Rollers
Metric conveyor rollers are available in various types, each designed to fulfill specific industrial requirements and handling characteristics. These rollers are constructed from different materials such as steel, aluminum, resin, and rubber, which affect their durability, weight, and suitability for different environments and tasks. Below, we explore four primary examples of metric conveyor rollers that highlight the range of options available for different industrial applications.
Industrial Conveyor Rollers
Industrial conveyor rollers are the backbone of many production lines, designed to handle a wide range of materials and weights. These rollers are typically made from robust materials like steel or aluminum for strength and durability, resin for corrosion resistance, or rubber for added grip and noise reduction. The choice of material often depends on the specific needs of the conveyor system, such as food processing which requires non-toxic and easy-to-clean surfaces, or heavy industry where strength and durability are paramount.
Specialty Rollers
- Grooved Conveyor Rollers: These metric conveyor rollers are designed with grooves that can aid in the alignment and driving of belts, particularly useful in sorting operations. The grooves help maintain the belt’s position and can also be used to facilitate the movement of items across the belt’s surface, enhancing the sorting process.
- Heavy Duty Conveyor Rollers: Built to handle higher loads and harsh conditions, these rollers are constructed from materials such as hardened steel or reinforced plastics. Heavy duty metric conveyor rollers are essential in industries like mining and construction where rollers must withstand rigorous use and substantial weight.
- 4 Inch Diameter Conveyor Rollers: These metric conveyor rollers are sized specifically with a diameter of approximately 100 mm (4 inches), making them versatile for medium-scale transport tasks. They are popular in both light and heavy industries due to their optimal size, providing a good balance between performance and durability.
- Omni Conveyor Rollers: Omni rollers, or omnidirectional rollers, allow movement in multiple directions, providing versatility in conveyor design. These metric conveyor rollers can transfer loads smoothly between different conveyor lines without the need for additional pushers or transfer stations.
- Belt Conveyor Drive Roller: This type of roller is crucial for driving the conveyor belt, imparting the motion necessary for moving the belt along the conveyor system. These drive rollers are often rubber-coated to increase friction between the roller and the belt, ensuring efficient transfer of force.
Each type of metric conveyor roller has unique attributes tailored to specific industrial needs, contributing to the efficiency and effectiveness of conveyor systems across various sectors.
Choosing the Right Metric Conveyor Rollers
Selecting the appropriate metric conveyor rollers is critical to ensuring efficiency, safety, and longevity of your conveyor system. When choosing metric conveyor rollers, several factors must be considered to match the needs of your specific application. Understanding these factors can greatly influence the performance and operational efficiency of your conveyor system.
Factors to Consider
- Load Capacity: The weight that the metric conveyor rollers will need to support is one of the most crucial considerations. Rollers must be capable of handling the maximum load without deforming or failing. Steel rollers might be preferred in heavy-load environments, whereas aluminum or plastic rollers could be suitable for lighter applications.
- Speed Requirements: The speed at which the conveyor will operate also affects the choice of rollers. High-speed operations require rollers designed to minimize friction and heat buildup, which could otherwise lead to premature wear or failure.
- Environmental Conditions: The operating environment is critical when selecting metric conveyor rollers. For instance, operations in corrosive environments such as chemical processing plants might require rollers made from materials like stainless steel or coated with corrosion-resistant finishes. Similarly, operations in very dusty or wet conditions will need sealed roller bearings to prevent contamination and ensure smooth operation.
- Temperature Extremes: Rollers must be chosen considering the temperature ranges they will be exposed to. Some materials and lubricants perform poorly in extreme temperatures, which could affect roller functionality and longevity. For example, extreme cold can cause materials to become brittle, while extreme heat can lead to material expansion and increased wear.
Consultation with Manufacturers for Custom Needs
In addition to standard metrics, many operations have unique requirements that standard metric conveyor rollers may not meet. In such cases, consultation with manufacturers is essential. Manufacturers can provide valuable guidance on custom solutions that can handle specific loads, speeds, or environmental challenges. They can also advise on the best materials and engineering designs suited to your specific conditions. This collaborative approach ensures that the rollers are perfectly tailored to your system’s needs, enhancing performance and preventing costly downtime due to incompatibility or roller failure.
Choosing the right metric conveyor rollers involves a comprehensive evaluation of your system’s requirements and a thorough discussion with knowledgeable manufacturers. By taking these steps, you can ensure that your conveyor system operates smoothly, efficiently, and reliably under all conditions.
Manufacturers of Metric Conveyor Rollers
Selecting a reputable manufacturer is essential when sourcing metric conveyor rollers to ensure high-quality, reliability, and suitability for specific industrial applications.
- Omni Metalcraft Corp. – Omni is a prominent name in the conveyor system industry, renowned for its comprehensive range of rollers. They offer a variety of metric conveyor rollers designed to meet diverse industrial demands. Known for their robust construction and versatility, Omni’s rollers are made from materials like high-grade steel and durable polymers, ensuring long-term durability and performance in various operational conditions.
- Interroll Group – Based in Switzerland, Interroll is recognized for its precision-engineered conveyor components. Their products are a staple in many industries due to their high compatibility and performance standards. Interroll’s offerings include a wide array of rollers that cater to different environmental conditions and load capacities, using cutting-edge technology in their manufacturing processes.
- Rulmeca Group – Operating globally, Rulmeca is known for high-quality conveyor rollers that are extensively used in heavy-duty industrial applications. Their rollers are designed to handle significant loads and are made using premium materials like reinforced steel and engineered plastics, ensuring enhanced functionality across diverse settings.
These manufacturers adhere to stringent international standards, providing a broad spectrum of both standard and customized roller solutions. Their use of advanced manufacturing technologies and high-quality materials such as steel, aluminum, and synthetic composites maximizes the durability and functionality of their rollers, making them suitable for a wide range of industrial applications.
Obtaining Metric Conveyor Rollers
Procuring the right metric conveyor rollers involves making informed decisions about whether to purchase new or used rollers and knowing where to source them effectively. Understanding the pros and cons of each option and identifying the most reliable purchasing channels are crucial steps.
New vs. Used Rollers
Pros and Cons
Pros of New Rollers:
- Reliability: New metric conveyor rollers come with the assurance of optimal performance and minimal risk of failure.
- Warranty: They often include manufacturer warranties, providing protection against defects.
- Latest Technology: New rollers are more likely to incorporate the latest design improvements and materials technology.
Cons of New Rollers:
- Cost: They are typically more expensive than used rollers, representing a higher initial investment.
Pros of Used Rollers:
- Cost-Effective: Used rollers are usually available at a lower price point, making them attractive for budget-conscious operations.
- Eco-Friendly: Purchasing used rollers can be seen as an environmentally friendly option as it extends the lifecycle of existing products.
Cons of Used Rollers:
- Wear and Tear: They may come with unknown histories and potential wear that could lead to early failure.
- No Warranty: Used rollers typically do not carry warranties, which could increase the risk in case of defects.
What to Look for When Buying Used Rollers
- Physical Condition: Check for visible signs of wear such as cracks, rust, and deformation. These can indicate how well the roller has been maintained and the environment it was used in.
- Bearing Operation: Ensure that the bearings operate smoothly without excessive noise or vibration, which could indicate internal wear.
- Compatibility: Verify that the specifications match your conveyor system’s requirements. Incompatibility can lead to inefficient operation or damage.
- Vendor Reputation: Purchase from reputable suppliers who are known for quality and reliability in their used equipment.
Finding Metric Conveyor Rollers for Sale
Tips for Sourcing Rollers
- Assess Needs Thoroughly: Understand the specific requirements of your conveyor system including load, speed, and environmental conditions to choose the appropriate type of rollers.
- Compare Suppliers: Evaluate different suppliers to find the best balance between price, quality, and service.
- Check References: Ask for customer references from suppliers to verify the quality and reliability of their rollers.
- Consider Custom Solutions: If standard rollers do not meet your needs, consider asking manufacturers for custom-designed metric conveyor rollers that specifically match your specifications.
Online Marketplaces and Direct Manufacturer Purchases
Metric conveyor rollers can be sourced from a variety of channels. Online marketplaces offer a broad selection of both new and used rollers, providing the convenience of easy comparison and purchase. Direct purchases from manufacturers, on the other hand, allow for a more personalized interaction and the possibility of custom specifications. Both methods have their merits, and the choice will depend on the specific needs and circumstances of the purchaser.
Finding the right metric conveyor rollers involves careful consideration of the type of roller needed, the condition of used rollers, and the sourcing method that best suits the operational requirements and budget constraints.
Installation and Maintenance of Metric Conveyor Rollers
Ensuring the proper installation and regular maintenance of metric conveyor rollers is essential for maximizing their efficiency and extending their lifespan. This section provides fundamental guidance on installing these rollers and offers maintenance tips to achieve optimal performance and longevity.
Basic Guidance on Installing Metric Conveyor Rollers
The correct installation of metric conveyor rollers is crucial for the smooth operation of conveyor systems. Here are the basic steps:
- Preparation: Before installation, ensure that the conveyor frame is clean and level. Check for any debris or obstructions that could interfere with the rollers.
- Alignment: Accurately align the rollers within the conveyor frame to ensure that they are parallel to each other and perpendicular to the direction of the conveyor belt. Misalignment can cause excessive wear and tear.
- Secure Fastening: Use appropriate fasteners to securely mount the rollers in place. This prevents them from loosening over time due to vibrations or load movement.
- Testing: After installation, run the conveyor system at low speed to check for proper roller function and smooth belt movement. Make adjustments as necessary to correct any issues.
Maintenance Tips for Longevity and Optimal Performance
Regular maintenance of metric conveyor rollers is vital to prevent breakdowns and ensure efficient operation.
- Regular Cleaning: Keep the rollers and the surrounding area free of dirt, debris, and other contaminants that can build up and cause damage or inefficiency. This is particularly important in environments with high dust levels or particulate matter.
- Lubrication: Properly lubricate bearings and any other moving parts according to the manufacturer’s recommendations. Over-lubrication can attract dirt and under-lubrication can cause premature wear.
- Inspection: Conduct regular inspections to check for signs of wear such as cracks, corrosion, or misalignment. Early detection of these issues can prevent more significant problems down the line.
- Replacement of Worn Parts: Timely replace any rollers that show significant wear or damage. Delaying replacement can lead to further damage to the conveyor system and potentially costly repairs.
By following these installation and maintenance practices, the longevity and performance of metric conveyor rollers can be significantly enhanced, ensuring that the conveyor system operates reliably and efficiently. This not only helps in reducing downtime but also in maintaining productivity and safety in industrial operations.
Custom Solutions and Innovation in Metric Conveyor Rollers
In the realm of metric conveyor rollers, custom solutions and technological advancements play a pivotal role in catering to specific industrial needs and enhancing overall system performance. Customization allows for tailored designs that fit unique operational requirements, while innovations in technology lead to improvements in efficiency, durability, and functionality.
Examples of Custom Roller Solutions for Unique Applications
- Temperature-Resistant Rollers: For industries like metal processing or glass manufacturing, where high temperatures are prevalent, custom metric conveyor rollers are designed using materials that can withstand extreme heat without degrading.
- Anti-Static Rollers: In environments where static electricity can pose a hazard, such as in the electronics manufacturing industry, rollers are customized with anti-static properties to prevent static charges that could damage sensitive components.
- Food-Grade Rollers: For the food and beverage industry, rollers are customized to comply with hygiene standards and regulations. These rollers are made from materials that are easy to clean and resistant to corrosion by food acids and wash-down procedures.
- High-Load Capacity Rollers: Heavy industries like mining or quarrying require rollers that can carry oversized and heavy loads. Custom heavy-duty rollers are engineered with reinforced materials and bearings to support the increased weight without failure.
Technological Advancements and Their Impact on Roller Design and Function
- Smart Rollers: Integration of IoT (Internet of Things) sensors in metric conveyor rollers allows for real-time monitoring of performance and maintenance needs. These smart rollers can track wear levels, load capacities, and operational efficiency, enabling predictive maintenance and minimizing downtime.
- Composite Materials: The use of advanced composite materials in roller construction enhances the strength-to-weight ratio, providing lighter rollers that do not compromise on durability or load-bearing capacity. This innovation not only reduces the energy required to move the rollers but also extends their lifespan.
- Precision Machining Techniques: Modern machining technologies have improved the precision with which metric conveyor rollers are made. This results in rollers with very tight tolerances that operate more smoothly and reduce the risk of misalignment, thus lowering wear and tear.
- Eco-friendly Designs: Recent innovations include the development of rollers designed to reduce environmental impact. These include manufacturing processes that use less energy and materials that are recyclable. Eco-friendly designs help companies reduce their carbon footprint while maintaining efficiency and compliance with environmental regulations.
Through these custom solutions and technological innovations, metric conveyor rollers are continuously evolving to meet the diverse and changing needs of industries worldwide. These advancements not only cater to specific functional requirements but also push the boundaries of what conveyor systems can achieve, thereby setting new standards in material handling efficiency and reliability.
FAQs About Metric Conveyor Rollers
A conveyor roller is a critical component used in conveyor systems, which are prevalent in numerous industrial sectors like manufacturing, distribution, and packaging. These rollers are cylindrical devices that are mounted within conveyor tracks. Their primary function is to guide and support conveyor belts or facilitate the movement of materials along a desired path without significant friction. Conveyor rollers can vary widely in size, material, and design based on their specific application. They play a vital role in the smooth and efficient transportation of goods within a facility, making them indispensable in settings where rapid movement of products is necessary.
Conveyor rollers come in various types to suit different environmental conditions and operational needs. The most common types include:
Gravity Rollers: These rollers operate without external power, using the force of gravity to move items. They are ideal for light to medium loads and are commonly used in picking and assembly operations.
Motorized Rollers: These are powered rollers that can control the movement and speed of the conveyor belt and are suitable for handling heavy loads.
Impact Rollers: Positioned at points where objects are loaded onto the conveyor, these rollers are designed to absorb the shock and impact.
Guide Rollers: Used to ensure that the conveyor belts do not shift sideways.
Grooved Rollers: These have grooves that are designed to match with belts or other rolling components. They are often used in belt-driven conveyors.
Each type of roller is designed to meet specific industrial requirements and to handle materials more efficiently based on their characteristics.
Conveyor rollers are measured by their diameter and length to ensure they fit the specific requirements of the conveyor system they will be integrated into. The diameter of the roller is critical as it influences the speed at which materials can be moved and the type of materials that can be transported. The length of the roller must be compatible with the width of the conveyor belt to provide adequate support. Measurements are typically taken in millimeters or inches, depending on the standard used in the location or industry. Proper measurement is crucial for maintaining the efficiency and longevity of the conveyor system.
The size of conveyor rollers can vary significantly depending on the application. Sizes commonly range from as small as a few inches in diameter and length to large rollers measuring several feet. The choice of size is influenced by several factors, including the load weight, the type of materials being transported, the speed of the conveyor, and the overall size of the conveyor system. For instance, heavier loads and higher speeds typically require larger and more robust rollers to handle the increased demand. In contrast, lighter and slower applications can utilize smaller rollers. Standard sizes are available, but many manufacturers also offer custom-sized rollers to meet specific operational requirements.
Last Updated on April 23, 2024 by Jordan Smith
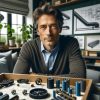
Jordan Smith, a seasoned professional with over 20 years of experience in the conveyor system industry. Jordan’s expertise lies in providing comprehensive solutions for conveyor rollers, belts, and accessories, catering to a wide range of industrial needs. From initial design and configuration to installation and meticulous troubleshooting, Jordan is adept at handling all aspects of conveyor system management. Whether you’re looking to upgrade your production line with efficient conveyor belts, require custom conveyor rollers for specific operations, or need expert advice on selecting the right conveyor accessories for your facility, Jordan is your reliable consultant. For any inquiries or assistance with conveyor system optimization, Jordan is available to share his wealth of knowledge and experience. Feel free to reach out at any time for professional guidance on all matters related to conveyor rollers, belts, and accessories.