Mild Steel Roller Durability and Cost-Effectiveness
Mild steel rollers are integral components in the machinery of numerous industries, serving a pivotal role in the seamless operation of conveyor systems, manufacturing processes, and material handling tasks. The choice of mild steel as a material for these rollers is no coincidence; its versatility and durability make it an ideal candidate for withstanding the rigorous demands of daily industrial use. Mild steel, known for its excellent weldability and formability, offers a balance of strength and flexibility that is crucial for rollers that must endure heavy loads, abrasive conditions, and variable temperatures. This adaptability ensures that mild steel roller can be customized to meet the specific requirements of different applications, from agriculture and construction to mining and beyond, making them a cornerstone in the efficiency and productivity of modern industry.
What Is Mild Steel Roller
Known for their efficient performance and corrosion resistance, mild steel rollers excel in weldability and formability.Mild steel rollers, by virtue of their composition, stand out as the backbone of numerous mechanical systems, playing a pivotal role in the seamless operation of conveyor systems, automated assembly lines, and various material handling setups. The choice of mild steel for these rollers is deliberate, leveraging the material’s inherent qualities to meet the rigorous demands of industrial environments. With a carbon content typically ranging between 0.05% and 0.25%, mild steel combines the structural integrity necessary to withstand operational stresses with the pliability required for precision manufacturing and shaping.
This unique blend of attributes makes mild steel rollers exceptionally versatile, enabling their use in a diverse array of applications—from the gentle handling of delicate materials in the food and beverage industry to the robust demands of heavy machinery in construction and mining operations. The adaptability of mild steel allows for the production of rollers in various sizes and specifications, tailored to the specific needs of different machinery and conveying systems. Furthermore, the surface of these rollers can be treated or coated to enhance their resistance to wear, corrosion, and other environmental factors, thereby extending their operational lifespan and ensuring consistent performance under varying conditions.
Moreover, the economic efficiency of mild steel as a raw material contributes to the cost-effectiveness of producing mild steel rollers, offering a budget-friendly solution without compromising quality or functionality. This affordability, coupled with the material’s durability, makes mild steel rollers a preferred choice for businesses looking to optimize their operational efficiency while maintaining strict control over costs. In essence, the integration of mild steel rollers into mechanical systems exemplifies a harmonious balance between performance, versatility, and economic viability, underscoring their indispensable role in the industrial sector.
Comparison of Mild Steel Rollers with Other Types of Steel Rollers
When comparing mild steel rollers to rollers made from other types of steel, such as hot rolled steel, several key differences emerge:
- Carbon Content: Mild steel rollers contain a lower carbon content compared to hot rolled steel, making them softer and more pliable, which is ideal for applications requiring flexibility and durability.
- Surface Finish: Mild steel often has a smoother finish than hot rolled steel, which can have a rougher surface due to the scaling that occurs during the cooling process.
- Weldability: The lower carbon content of mild steel rollers enhances their weldability, allowing for easier modifications or repairs compared to hot rolled steel rollers.
- Strength and Hardness: Hot rolled steel rollers typically offer higher strength and hardness due to their manufacturing process. However, mild steel rollers provide sufficient strength for many applications, with the added benefit of increased flexibility.
- Cost-Effectiveness: Mild steel is generally more cost-effective than hot rolled steel, making mild steel rollers a more economical choice for many projects without compromising on performance.
- Durability: While both materials are durable, the ductility of mild steel allows rollers made from this material to absorb impact better, reducing the risk of cracking under heavy loads.
- Corrosion Resistance: Mild steel rollers, like all mild steel products, are susceptible to corrosion if not properly treated or coated, whereas hot rolled steel can sometimes offer slightly better resistance due to its denser surface.
- Application Suitability: Mild steel rollers are preferred in applications where flexibility, weldability, and cost are critical, while hot rolled steel rollers are chosen for projects requiring higher strength and resistance to wear and tear.
Mild steel rollers stand out for their unique combination of durability, affordability, and versatility, making them a preferred choice in industries ranging from manufacturing to logistics and beyond. Their comparison with hot rolled steel rollers highlights the importance of selecting the appropriate material based on specific application requirements to ensure optimal performance and longevity.

Types of Mild Steel Roller
Mild steel rollers are commonly used in various industrial applications, including conveyor systems. Here are some types of mild steel rollers:
Plain Steel Rollers:
- Description: Basic cylindrical rollers made entirely of mild steel.
- Applications: Suitable for general-purpose use in conveyor systems where smooth transportation of materials is required.
- Advantages: Durable, cost-effective, and easy to manufacture.
Grooved Rollers:
- Description: These rollers feature grooves along their surface. The grooves can vary in shape and size depending on the application.
- Applications: Used in applications where precise tracking and guiding of materials are essential, such as in handling round objects like pipes or cables.
- Advantages: Improved material alignment and reduced slippage.
Rubber Coated Rollers:
- Description: Mild steel rollers with a rubber coating to provide a cushioned surface.
- Applications: Ideal for handling delicate or fragile materials where reducing damage is crucial.
- Advantages: Enhanced grip, reduced noise, and minimized wear on both the roller and the conveyed material.
- Description: These rollers are designed to absorb and withstand heavy impacts.
- Applications: Commonly used at loading points of conveyor systems where materials are dropped from a height.
- Advantages: Robust construction, shock absorption, and longer lifespan under harsh conditions.
Spiral Rollers:
- Description: Rollers with a spiral pattern on their surface, which can be made from metal or rubber.
- Applications: Used in applications where self-cleaning is important, such as in handling bulk materials that can stick to the roller surface.
- Advantages: Prevents material buildup, self-cleaning properties, and improved material flow.
Tapered Rollers:
- Description: Rollers that taper towards the ends, creating a conical shape.
- Applications: Utilized in conveyor curves to maintain the alignment and smooth transition of materials.
- Advantages: Improved material guidance around curves, reduced wear, and smoother transitions.
Motorized Rollers:
- Description: Rollers with built-in motors that drive the conveyor belt or materials.
- Applications: Used in automated conveyor systems where precise control of speed and direction is needed.
- Advantages: Increased efficiency, reduced need for external drive systems, and precise control over conveyor operations.
Friction Driven Rollers:
- Description: These rollers operate by friction, moving the conveyor belt without the need for external motors.
- Applications: Common in gravity conveyors and applications where minimal power consumption is desired.
- Advantages: Simple design, low maintenance, and energy efficiency.
Conveyor Drum Rollers:
- Description: Large diameter rollers, typically used at the ends of conveyor belts.
- Applications: Serve as drive or tensioning rollers in conveyor systems, providing the necessary force to move the belt.
- Advantages: High load-bearing capacity, efficient belt movement, and effective tensioning.
Each type of mild steel roller is engineered to meet specific operational requirements, ensuring optimal performance and longevity in various industrial applications.

Mild Steel Roller Specification
Mild steel rollers come with various specifications tailored to meet different industrial needs. Here are some key specifications that are typically considered for mild steel rollers:
1. Material Specifications:
- Material: Mild steel (commonly grades like AISI 1018, AISI 1045)
- Surface Treatment: Galvanized, painted, or powder-coated to prevent corrosion
2. Dimensional Specifications:
- Diameter: Ranges from 20 mm to 500 mm or more, depending on application
- Length: Can be customized, typically ranges from 100 mm to 3000 mm
- Wall Thickness: Varies based on load requirements, commonly 2 mm to 10 mm
3. Mechanical Specifications:
- Load Capacity: Can range from a few kilograms to several tons per roller
- Bearing Type: Ball bearings, roller bearings, or bush bearings
- Shaft Diameter: Usually ranges from 10 mm to 60 mm
4. Tolerance Specifications:
- Dimensional Tolerance: Generally within ±0.5 mm for length and diameter
- Roundness Tolerance: Typically within 0.05 mm to 0.1 mm
- Concentricity: Usually within 0.05 mm to 0.1 mm
5. Surface Finish Specifications:
- Surface Roughness: Typically Ra 1.6 µm to Ra 3.2 µm
- Coating Thickness: For painted or galvanized rollers, typically 20 µm to 100 µm
6. Environmental and Operational Specifications:
- Temperature Range: Operating temperature from -20°C to +120°C
- Environmental Resistance: Corrosion-resistant coatings for outdoor or corrosive environments
7. Special Features:
- Grooved Rollers: Groove dimensions and patterns (V-groove, U-groove, etc.)
- Rubber Coated Rollers: Rubber hardness (Shore A), thickness of the coating
- Impact Rollers: Reinforced structure, shock absorption characteristics
- Spiral Rollers: Spiral pitch and depth
- Tapered Rollers: Taper angle and length
- Motorized Rollers: Motor specifications (voltage, power, speed)
- Friction Driven Rollers: Friction coefficient and surface material
- Conveyor Drum Rollers: Drum diameter, width, and drive mechanism
8. Compliance and Standards:
- Industry Standards: Conformance to standards such as ISO, DIN, ASTM
- Quality Certifications: ISO 9001, CE marking, etc.
Applications of Mild Steel Roller
Mild steel rollers are pivotal components across a broad spectrum of industries, where their robustness, versatility, and cost-effectiveness enable the smooth execution of numerous processes. The adaptability of mild steel rollers to various operational demands makes them indispensable in sectors as diverse as agriculture, mining, construction, and manufacturing, among others.
Industries Utilizing Mild Steel Rollers
The versatility of mild steel rollers is showcased through their application in numerous industries, each with its unique set of challenges and requirements. These rollers are not just components; they are the backbone of efficient material handling and processing across various sectors:
- Agriculture: In the agricultural sector, mild steel rollers are integral to machinery like tractors, harvesters, and conveyors used for processing and transporting grain and other produce. Their durability ensures reliable operation in the challenging outdoor conditions typical of farming.
- Mining: The mining industry relies on mild steel rollers for the heavy-duty conveyors that transport ore and other materials from the mine face to processing facilities. Their strength and load-bearing capacity are crucial in these demanding applications.
- Construction: In construction, mild steel rollers are found in equipment ranging from asphalt paving machines to portable conveyors used for moving materials across job sites. Their robustness allows for consistent performance under the weight of heavy building materials.
- Manufacturing: Manufacturing facilities use mild steel rollers in assembly lines and packaging conveyors, where they facilitate the efficient movement of products through various stages of production and preparation for shipment.
- Logistics and Warehousing: For logistics and warehousing, mild steel rollers form the backbone of sorting systems, loading docks, and storage solutions, helping to streamline the handling of goods.
- Food Processing: Even in the food processing industry, mild steel rollers are employed in conveyor systems designed for the gentle handling of food products, ensuring they move smoothly through the production line without damage.
- Recycling Plants: Recycling operations depend on mild steel rollers for the conveyors that sort and transport recyclable materials, where their durability withstands the abrasive nature of recycled waste.
Discover our range of conveyor rollers. Inquire for information!
Specific Machinery and Processes Utilizing Mild Steel Rollers
The application of mild steel roller extends to specific machinery and processes, underscoring their adaptability and essential role in industrial operations:
- Conveyor Belts: In virtually all the industries mentioned, conveyor belts equipped with mild steel rollers are fundamental for the transportation of raw materials, components, and finished products.
- Roller Tables: In manufacturing and metalworking, roller tables facilitate the movement of heavy items across the shop floor, with mild steel rollers providing the necessary support and ease of movement.
- Agricultural Machinery: Machines such as balers and feed conveyors utilize mild steel rollers for their reliability and strength in the harsh conditions of agricultural work.
- Mining Equipment: Conveyors used in mining for moving extracted materials over long distances rely on mild steel rollers for their high load-bearing capacity and resistance to wear.
- Packaging Lines: In packaging lines, mild steel rollers ensure the smooth transition of products into packaging stations, where precision and reliability are key to maintaining efficiency.
- Material Handling Systems: For material handling in warehouses and distribution centers, mild steel rollers are essential components of both automated and manual conveyor systems, optimizing the flow of goods.
The widespread application of mild steel roller across these diverse industries underscores their importance in the global economy. Their ability to meet the demands of different environments and processes while maintaining high performance and cost-efficiency is unparalleled, making them a cornerstone of industrial operations worldwide.

How to Choose the Best Mild Steel Roller
Selecting the best mild steel roller for your specific application involves a careful consideration of various factors that can significantly impact the performance, durability, and overall efficiency of your machinery or conveyor system. The right choice ensures not only the smooth operation of your equipment but also contributes to its longevity and reduces the need for frequent maintenance or replacements. Below, we explore the critical factors and the importance of certain characteristics such as roller diameter, material coating, and load-bearing capacity, which are essential in making an informed decision when choosing mild steel rollers.
Factors to Consider When Selecting Mild Steel Rollers
- Application Requirements: Understand the specific needs of your application, including the type of materials being handled and the environment in which the rollers will operate.
- Load Capacity: Evaluate the maximum load the mild steel rollers will need to support. Choosing a roller with an appropriate load-bearing capacity is crucial to prevent deformation or failure.
- Speed Requirements: Consider the operational speed of your conveyor or machinery. The mild steel roller must be capable of handling the required speed without compromising on performance or safety.
- Environmental Conditions: Assess the working environment, including exposure to chemicals, moisture, and temperature extremes. This will help determine the need for specific coatings or treatments to enhance corrosion resistance.
- Roller Diameter: The diameter of the mild steel roller plays a pivotal role in determining its suitability for your application, affecting load distribution and the smoothness of operation.
- Shaft Attachment: The method of attaching the roller to the shaft (e.g., fixed, floating, or threaded) should align with your system’s design requirements for optimal performance.
- Maintenance and Accessibility: Opt for rollers that are easy to maintain and replace, considering the accessibility of the system for routine inspections and servicing.
- Cost-Effectiveness: While not compromising on quality, consider the overall cost-effectiveness of the roller, including initial purchase price, maintenance costs, and potential downtime.
Importance of Roller Diameter, Material Coating, and Load-Bearing Capacity
- Roller Diameter: The diameter of a mild steel roller is integral to its functionality. Larger diameters generally distribute loads more evenly and can handle higher speeds, but the right size should be determined based on the specific application and space constraints.
- Material Coating: Coatings on mild steel rollers can significantly enhance their resistance to wear, corrosion, and abrasion. Options such as galvanization, powder coating, or rubber lining can extend the life of the rollers and are particularly important in harsh or corrosive environments.
- Load-Bearing Capacity: The ability of a mild steel roller to support the intended load without deformation or failure is fundamental. Underestimating the load-bearing capacity can lead to premature wear, roller damage, and potential operational hazards.
- Surface Texture and Treatment: The surface texture, achieved through specific coatings or treatments, can influence the traction and movement of materials across the roller. This is especially relevant in applications where slippage could be a concern.
- Compatibility with Conveyor Belts: Ensure that the mild steel rollers are compatible with the type of conveyor belt used, to prevent damage to both the rollers and the belt.
- Durability Under Load: Continuous operation under load can stress the rollers. Selecting a roller designed for durability under your specific operational conditions is essential.
- Impact Resistance: In applications where the rollers are subject to impact, choose mild steel rollers designed to absorb and withstand such forces, ensuring continuous, reliable operation.
By carefully considering these factors and the importance of roller diameter, material coating, and load-bearing capacity, you can select the best mild steel rollers for your application, optimizing your system’s performance and reliability.

Mild Steel Gravity Rollers
Mild steel gravity rollers are a type of conveyor roller used primarily in gravity conveyor systems. They are constructed from mild steel, making them strong and durable for handling a variety of loads. Here are some key features and benefits of mild steel gravity rollers:
Features
- Material: Made from mild steel, which provides excellent strength and durability.
- Surface Finish: Typically have a smooth or galvanized finish to prevent rust and corrosion.
- Diameter and Length: Available in various diameters and lengths to suit different conveyor systems.
- Bearing Type: Usually equipped with high-quality bearings to ensure smooth and efficient rotation.
- Load Capacity: Capable of handling medium to heavy loads, depending on the roller’s specifications.
Benefits
- Cost-Effective: Mild steel is generally more affordable than stainless steel, making these rollers a cost-effective choice.
- Durability: Strong and able to withstand significant wear and tear, ideal for industrial environments.
- Versatility: Suitable for a wide range of applications, including packaging, assembly lines, and warehouse logistics.
- Ease of Maintenance: Simple design allows for easy maintenance and replacement when necessary.
- Customizable: Can be manufactured to meet specific requirements, such as size, load capacity, and surface finish.
Applications
- Material Handling: Used in gravity conveyors for moving products in warehouses and distribution centers.
- Assembly Lines: Facilitates the movement of products between workstations.
- Packaging: Ideal for transporting packages and products in packaging operations.
- Logistics: Used in logistics and distribution for efficient movement of goods.
If you have specific requirements or need more detailed information about mild steel gravity rollers, please let me know!
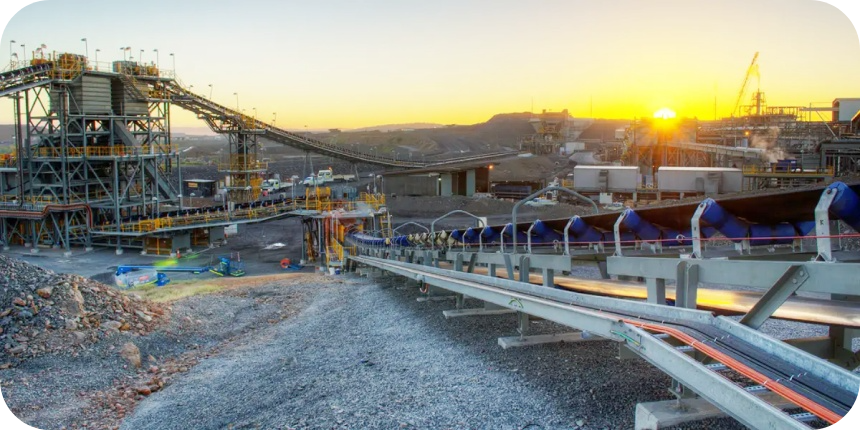
HS Code for Mild Steel Roller
The global trade of goods requires a standardized method for classifying products to streamline customs, tariffs, and shipping procedures. This is where the Harmonized System (HS) code comes into play, serving as a universally recognized classification system for international trade. Each HS code is a unique identifier for a product, detailing its nature, material, and intended use, thereby facilitating smoother transactions across borders.
Explanation of the Harmonized System (HS) Code for International Trade
The Harmonized System (HS) Code is a globally standardized system of names and numbers to classify traded products. Developed and maintained by the World Customs Organization (WCO), it serves as the foundation for customs tariffs and international trade statistics in over 200 countries, representing about 98% of world trade. The system is designed to facilitate the international transport of goods by simplifying the identification and classification of commodities.
The HS Code system is structured into 21 sections, which are further divided into 99 chapters. Each chapter is broken down into headings and subheadings, representing a hierarchy that categorizes goods in increasing levels of specificity. This hierarchical structure allows for the precise classification of a wide range of commodities, from raw materials to finished products, including mild steel rollers.
Each HS code consists of six digits: the first two represent the chapter the goods are classified under, the next two digits identify the heading within that chapter, and the final two digits indicate the subheading. This six-digit code is universally recognized, ensuring consistency in the classification of goods across international borders. However, countries can extend the code to eight or ten digits for further classification, allowing for more detailed tracking and analysis of trade data.
The significance of the HS Code system in international trade cannot be overstated. It streamlines the process of exporting and importing by providing a common language for customs authorities, traders, and transporters. By accurately classifying goods, the HS Code system helps in determining applicable tariffs, identifying trade restrictions or requirements, and ensuring compliance with international trade regulations. Moreover, the system plays a crucial role in trade negotiations, economic research, and the monitoring of controlled goods, including environmental and endangered species protections.
For businesses engaged in international trade, understanding the HS Code system is essential. Proper classification of products like mild steel rollers not only ensures compliance with global trade laws but also optimizes tariff rates, potentially leading to significant cost savings. Additionally, the HS Code system aids in market analysis and strategic planning by providing insights into global trade flows and trends.
Specific HS Code for Mild Steel Rollers and Its Significance
The specific HS code for mild steel roller plays a crucial role in the international trade of these industrial components. While the exact HS code can vary depending on the specific type of roller and its application, mild steel rollers generally fall under a category that includes various types of rollers used in machinery and mechanical appliances. For example, rollers for conveyor belts might be classified under a different code than rollers designed for rolling mills, despite both being manufactured from mild steel.
Identifying the correct HS code for mild steel roller is essential for several reasons:
- Customs and Tariffs: The HS code determines the rate of duty and taxes applicable to the product, affecting the overall cost of importing or exporting mild steel rollers.
- Compliance: Using the correct HS code ensures compliance with international trade regulations, helping to avoid delays, fines, or other penalties at customs.
- Trade Statistics: HS codes are used to compile accurate trade statistics, which are vital for economic analysis and policy-making.
- Market Research: Businesses use HS codes to conduct market research, identifying potential markets, and understanding competition and demand for mild steel rollers.
- Product Classification: The HS code provides a clear description of the product, facilitating easier identification and classification during the trade process.
For businesses involved in the manufacturing, export, or import of mild steel rollers, understanding and utilizing the correct HS code is a critical aspect of navigating the complexities of international trade. It ensures that products move efficiently across borders, complying with all regulatory requirements while optimizing costs related to duties and taxes.
Mild Steel vs. Hot Rolled Steel for Rollers
When selecting materials for manufacturing rollers, two popular choices are mild steel and hot rolled steel. Each material offers distinct advantages and disadvantages, depending on the specific application requirements. This detailed comparison aims to shed light on the differences between mild steel rollers and hot rolled steel rollers, helping you make an informed decision for your needs.
Pros and Cons of Mild Steel Roller
Pros:
- Cost-Effectiveness: Mild steel rollers are more affordable, making them suitable for projects with tight budgets.
- Weldability: They can be easily welded without the need for pre-heating, simplifying the manufacturing process.
- Surface Finish: Offers a smoother finish, which is beneficial for applications requiring a high-quality surface.
- Dimensional Accuracy: Provides higher dimensional accuracy, crucial for precision applications.
- Corrosion Resistance: With proper coatings, mild steel rollers can exhibit good corrosion resistance.
- Weight: Generally lighter than hot rolled steel, reducing the overall weight of the machinery.
- Flexibility: More flexible, allowing for easier shaping and customization.
- Environmental Impact: Easier to recycle, making them a more environmentally friendly option.
Cons:
- Durability: Less durable compared to hot rolled steel, potentially leading to more frequent replacements.
- Strength: Lower tensile strength, making them unsuitable for high-stress applications.
- Work Hardening: Exhibits a lower work hardening rate, which can be a disadvantage in applications requiring hardening.
- Temperature Resistance: Lower resistance to high temperatures.
- Maintenance: May require more maintenance to prevent corrosion if not properly coated.
- Wear Resistance: Less wear resistance, which could lead to faster degradation in certain environments.
- Impact Resistance: Lower impact resistance, making them less ideal for heavy-duty applications.
- Limited Applications: Not suitable for applications where high strength and durability are critical.
Pros and Cons of Hot Rolled Steel Roller
Pros:
- Durability: Offers superior durability, making it suitable for heavy-duty applications.
- Strength: Higher tensile strength to withstand higher stress and load.
- Work Hardening: Benefits from a higher work hardening rate, useful for increasing resistance in wear-heavy environments.
- Temperature Resistance: Better suited for applications involving high temperatures.
- Impact Resistance: Higher impact resistance, ideal for industrial applications.
- Longevity: Generally lasts longer than mild steel rollers, reducing the need for frequent replacements.
- Heavy-Duty Applications: Perfectly suited for applications requiring high strength and durability.
- Reduced Maintenance: Requires less maintenance due to its inherent strength and durability.
Cons:
- Cost: More expensive, which can increase the overall project costs.
- Weldability: Requires pre-heating before welding, complicating the manufacturing process.
- Surface Finish: Rougher surface finish, which may not be ideal for all applications.
- Dimensional Accuracy: Lower dimensional accuracy due to potential cooling shrinkage.
- Weight: Heavier, which could increase the weight of the machinery or structure.
- Corrosion Resistance: Without proper treatment, it is less resistant to corrosion.
- Flexibility: Less flexible, making it harder to shape and customize.
- Environmental Impact: The manufacturing process is more energy-intensive, potentially leading to a higher environmental footprint.
The choice between a mild steel roller and a hot rolled steel roller depends on the specific requirements of your application, including budget constraints, durability needs, and environmental considerations. Mild steel rollers offer a cost-effective solution with good weldability and surface finish, while hot rolled steel rollers provide superior strength and durability for heavy-duty applications.
Mild Steel Roller Price Considerations
When embarking on projects that require the use of steel rollers, one of the key considerations is the cost. The price of steel rollers can vary widely based on a range of factors. Understanding these factors is essential for budgeting accurately and ensuring that your project costs remain manageable. This is especially true when considering mild steel rollers, which are popular for their cost-effectiveness and versatility in various applications. Below, we explore the factors that influence the price of steel rollers and offer strategic tips for obtaining the best value when purchasing mild steel roller.
Factors Influencing Steel Roller Prices
Before diving into the specifics, it’s important to recognize that the price of steel rollers is not arbitrary. It is influenced by a complex interplay of material costs, manufacturing processes, and market dynamics. Here are the key factors that determine how much you’ll pay for steel rollers:
- Material: The choice of material, particularly when comparing mild steel with alternatives like hot rolled steel, significantly impacts cost. Mild steel is often more affordable, affecting the overall price of the roller.
- Size: The physical dimensions of the roller directly influence its price. Larger rollers require more material and more complex manufacturing processes, leading to higher costs.
- Manufacturing Process: The steps involved in producing the roller, including any specialized machining or finishing, can add considerable expense.
- Customization: Custom-made rollers, tailored to specific dimensions or with unique features, will invariably cost more than standard models due to the extra labor and customization work involved.
- Quantity: Ordering in bulk can significantly reduce the unit price of each roller, thanks to economies of scale.
- Market Demand: The current demand for steel and steel products can fluctuate, affecting prices. High demand can drive prices up, while lower demand can make them more affordable.
- Supplier: Prices can also vary between suppliers based on their manufacturing capabilities, quality standards, and the additional services they offer.
- Coatings and Treatments: Opting for rollers with special coatings or treatments for enhanced performance or durability can increase the price.
Tips for Getting the Best Value When Purchasing Mild Steel Rollers
Purchasing mild steel rollers requires a strategic approach to ensure you’re getting the best value for your money. Here are some tips to guide you in making cost-effective decisions without compromising on quality:
- Bulk Purchases: Consider the long-term needs of your project and opt for bulk purchases where possible to benefit from lower prices.
- Compare Suppliers: Take the time to research and compare different suppliers. Look at their prices, product quality, and customer reviews to ensure you’re choosing the best option.
- Standard Sizes: Whenever feasible, use rollers of standard sizes and specifications. Custom sizes can significantly increase costs.
- Negotiate: Don’t hesitate to negotiate prices with suppliers, especially for large orders. There’s often room for negotiation that can lead to better deals.
- Quality over Price: It’s tempting to go for the cheapest option, but investing in higher-quality rollers can save money in the long run by reducing the need for replacements and maintenance.
- Total Cost of Ownership: Consider not just the purchase price, but also the longevity, maintenance needs, and operational efficiency of the rollers over their lifetime.
- Plan Ahead: Avoid rush orders by planning your needs well in advance. This can save on expedited shipping costs and give you a stronger negotiating position.
- Deals and Discounts: Keep an eye out for promotional deals, discounts, or clearance sales, which can offer significant savings, especially if your requirements are flexible.
By understanding the factors that influence the cost of mild steel roller and following these tips, you can make a more informed purchasing decision. This approach not only ensures that you get the best value for your investment but also contributes to the overall success and efficiency of your project.
Need high-quality conveyor rollers? Contact us for more details today!
Mild Steel Rollers for Sale
Finding mild steel rollers for sale that meet your specific project requirements involves knowing where to look and understanding the importance of quality and warranty considerations. Mild steel rollers are a fundamental component in various industrial, construction, and manufacturing applications due to their durability, versatility, and cost-effectiveness. Below, we provide comprehensive advice on where to find mild steel roller and highlight crucial factors to consider regarding quality and warranty to ensure you make a well-informed purchase.
Where to Find Mild Steel Rollers for Sale
- Manufacturers: Directly purchasing from manufacturers is one of the best ways to ensure you’re getting high-quality mild steel roller. Manufacturers can offer customized solutions tailored to your specifications.
- Industrial Supply Distributors: These distributors typically have a wide range of mild steel rollers in stock, catering to different industrial needs. They can be a great source for quick purchases.
- Online Marketplaces: Platforms like Alibaba, Amazon Business, and eBay offer a vast selection of mild steel roller from various sellers, including both new and used options.
- Specialty Stores: Look for stores that specialize in industrial components. These stores often have knowledgeable staff who can help you find the right mild steel roller for your application.
- Trade Shows and Expos: Attending industry-specific trade shows can connect you with manufacturers and distributors of mild steel rollers, offering the opportunity to see the products in person and negotiate deals.
- Local Industrial Auctions: Auctions can be a source for finding high-quality mild steel roller at reduced prices. Keep an eye on local auction listings for industrial equipment.
- Referrals: Ask for recommendations from industry peers or forums. Often, the best deals and suppliers come from the shared experiences of others in your field.
- Direct Sales Websites: Many manufacturers and distributors have their own websites where you can purchase mild steel rollers directly, often with options for customization.
Importance of Quality and Warranty Considerations
When purchasing mild steel rollers, paying attention to quality and warranty is crucial for ensuring the longevity and efficiency of your investment.
- Material Quality: Ensure the mild steel used in the rollers is of high quality, as this directly impacts their durability and performance.
- Manufacturing Standards: Look for rollers manufactured according to recognized industrial standards, ensuring they can withstand the demands of your applications.
- Warranty Coverage: A comprehensive warranty can protect your purchase against defects and failures, providing peace of mind and potentially saving on future repair costs.
- Brand Reputation: Consider buying from reputable brands known for their commitment to quality and customer service. A good reputation often indicates reliability and satisfaction.
- Certifications: Check for any relevant certifications that affirm the rollers meet specific safety and quality standards.
- After-Sales Support: Ensure the supplier offers excellent after-sales support, including access to spare parts and technical assistance, to address any issues that may arise during use.
By carefully selecting where to purchase your mild steel roller and prioritizing quality and warranty considerations, you can significantly enhance the success of your projects. High-quality mild steel roller not only performs better but also offers greater longevity, reducing the need for frequent replacements and thereby lowering long-term costs.
FAQs about Mild Steel Roller
The best steel for rollers depends on the specific application and requirements such as load capacity, environment, and desired lifespan. Mild steel and hot rolled steel are two of the most commonly used materials for rollers due to their strength, durability, and cost-effectiveness. Mild steel rollers are preferred for applications requiring a smooth surface finish, weldability, and where corrosion resistance can be enhanced through coatings. They are cost-effective and offer sufficient strength for many industrial applications. Hot rolled steel rollers, on the other hand, are chosen for their superior strength and durability, making them suitable for heavy-duty applications. They can withstand higher loads and are less prone to wear and tear but come with a rougher surface finish. Ultimately, the selection should be based on a balance between performance requirements and budget constraints, considering factors such as load capacity, environmental conditions, and whether the application demands resistance to abrasion or corrosion.
Steel rollers are utilized in a wide range of industrial, manufacturing, and material handling applications due to their durability, strength, and versatility. They are commonly found in conveyor systems, facilitating the movement of goods across warehouses, production lines, and distribution centers. Steel rollers are essential components in the agriculture, mining, construction, and manufacturing sectors, used in machinery such as roller conveyors, roller mills, and roller presses. Their ability to handle heavy loads and withstand harsh environments makes them ideal for applications requiring high durability and reliability. Additionally, steel rollers are used in applications ranging from the movement of raw materials to the final stages of product packaging and distribution, showcasing their adaptability across various industries.
Rollers can be made from a variety of materials, each selected based on the specific needs of the application, including load requirements, environmental conditions, and cost considerations. Common materials include steel (mild steel and hot rolled steel), aluminum, plastic, rubber, and stainless steel. Mild steel is widely used for its versatility and cost-effectiveness, suitable for a broad range of applications. Hot rolled steel offers increased strength and durability for heavy-duty applications. Aluminum rollers provide a lightweight alternative with good corrosion resistance. Plastic and rubber rollers are chosen for their ability to provide cushioning and reduce noise, suitable for delicate or uneven surfaces. Stainless steel rollers are preferred in environments where corrosion resistance and hygiene are critical, such as in food processing or pharmaceutical industries. The choice of material is crucial in ensuring the roller meets the operational demands and longevity required for the application.
Gravity rollers are typically made from materials such as mild steel, galvanized steel, aluminum, or plastic. The choice of material largely depends on the application’s specific requirements, including weight capacity, environmental conditions, and cost. Mild steel and galvanized steel gravity rollers are common due to their strength and durability, with galvanization offering additional corrosion resistance. Aluminum gravity rollers are a lightweight option, preferred in applications where ease of handling and resistance to corrosion are important. Plastic gravity rollers are used in situations requiring low noise, gentle handling of materials, or where corrosion resistance is a priority. Each material offers distinct advantages, and the selection should consider the balance between performance needs and budgetary constraints to ensure efficient and reliable operation in the intended application environment.
Hot rolled mild steel typically falls into the category of low carbon steel, with grades such as ASTM A36 being the most common. ASTM A36 is widely used due to its good balance of strength and ductility. It is easily weldable and machinable, making it suitable for a wide range of structural and industrial applications. Other common grades include S235JR, S275JR, and S355JR, which are used in the construction of bridges, buildings, and other large structures. These grades provide the necessary mechanical properties and are readily available, making them popular choices for hot rolled mild steel products.
Cold rolled steel and mild steel are not the same, though they can be related. Mild steel refers to a type of low carbon steel, typically containing 0.05% to 0.25% carbon, known for its malleability and ductility. Cold rolling is a process that involves rolling the steel at room temperature, which increases its strength and surface finish. Therefore, cold rolled steel can be made from mild steel, but the term “cold rolled” refers to the processing method, not the material itself. Cold rolled steel generally has a smoother finish and tighter tolerances compared to hot rolled steel, making it suitable for applications requiring precise dimensions and surface quality.
Last Updated on July 30, 2024 by Jordan Smith
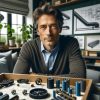
Jordan Smith, a seasoned professional with over 20 years of experience in the conveyor system industry. Jordan’s expertise lies in providing comprehensive solutions for conveyor rollers, belts, and accessories, catering to a wide range of industrial needs. From initial design and configuration to installation and meticulous troubleshooting, Jordan is adept at handling all aspects of conveyor system management. Whether you’re looking to upgrade your production line with efficient conveyor belts, require custom conveyor rollers for specific operations, or need expert advice on selecting the right conveyor accessories for your facility, Jordan is your reliable consultant. For any inquiries or assistance with conveyor system optimization, Jordan is available to share his wealth of knowledge and experience. Feel free to reach out at any time for professional guidance on all matters related to conveyor rollers, belts, and accessories.