Leading Mine Conveyor Belt Systems Manufacturers
Mine conveyor belt systems play a crucial role in modern mining operations, significantly enhancing both efficiency and safety. These systems are essential for the swift and secure transportation of materials within mining sites. The evolution of mine conveyor belt systems has seen significant technological advancements, making them indispensable in handling bulk materials over long distances and challenging terrains. From their early days to the sophisticated systems used today, mine conveyor belt systems have continuously improved, contributing to increased productivity and reduced operational risks. This article delves into various aspects of these systems, highlighting their importance, advancements, and the diverse types used in the mining industry.
Leading Manufacturers of Mine Conveyor Belt Systems
Overview of Top Global Manufacturers
The mine conveyor belt systems industry is dominated by several leading manufacturers who have set the standards in quality, innovation, and reliability. Notable names include ContiTech, Fenner Dunlop, and Bridgestone. These companies have extensive experience and a global footprint, making them pivotal in advancing the technology and applications of mine conveyor belt systems. ContiTech, a division of Continental AG, is renowned for its high-performance conveyor belts designed for mining environments. Fenner Dunlop, with over 150 years of experience, specializes in durable and efficient conveyor belts, particularly suited for challenging mining conditions. Bridgestone, another industry leader, offers a wide range of conveyor belts that cater to various mining needs, emphasizing both durability and efficiency.
Key Innovations and Technologies Introduced by These Manufacturers
Leading manufacturers of mine conveyor belt systems have continuously pushed the envelope in terms of innovation and technology. ContiTech, for example, has developed a range of heat-resistant and flame-retardant conveyor belts that are essential for safe mining operations. Their MegaPipe conveyor belt is an example of innovation, capable of handling large volumes of materials while minimizing dust and spillage. Fenner Dunlop has introduced the UsFlex series, known for its superior impact and tear resistance, making it ideal for heavy-duty mining operations. Additionally, their ECO series focuses on environmentally friendly materials and manufacturing processes, reflecting the industry’s shift towards sustainability.
Bridgestone has made significant advancements with their Super Low Loss (SLL) conveyor belts, which reduce power consumption by up to 25%. This innovation not only lowers operational costs but also contributes to reducing the environmental impact of mining activities. Their steel cord belts, designed for high-stress applications, feature enhanced durability and strength, ensuring they can withstand the rigorous demands of mining environments.
Case Studies Highlighting Successful Implementations of Mine Conveyor Belt Systems
Real-world applications of these innovative mine conveyor belt systems demonstrate their effectiveness and reliability. For instance, ContiTech’s MegaPipe conveyor belt was successfully implemented in a large copper mine in Chile. The system significantly reduced material spillage and dust, improving both the environmental footprint and operational efficiency. Similarly, Fenner Dunlop’s UsFlex series was deployed in a coal mine in Australia, where it endured harsh conditions and heavy loads, demonstrating exceptional durability and performance over several years.
Bridgestone’s Super Low Loss conveyor belts were installed in a gold mine in South Africa, where the reduction in energy consumption translated to substantial cost savings and a lower carbon footprint. These case studies not only highlight the capabilities of mine conveyor belt systems but also underscore the importance of selecting the right system for specific mining conditions and requirements.
Criteria for Selecting a Reliable Conveyor Belt Manufacturer
Choosing a reliable manufacturer for mine conveyor belt systems involves several critical criteria. First, consider the manufacturer’s track record and reputation within the industry. Companies like ContiTech, Fenner Dunlop, and Bridgestone have established themselves as leaders through consistent quality and innovation. It’s essential to evaluate their range of products and whether they meet the specific needs of your mining operations, such as resistance to heat, fire, and abrasion.
Another crucial factor is the manufacturer’s commitment to research and development. Leading manufacturers invest significantly in developing new technologies and improving existing ones, ensuring they stay ahead of industry trends and challenges. Additionally, consider the level of customer support and after-sales service provided. Reliable manufacturers offer comprehensive support, including installation, maintenance, and troubleshooting services.
Finally, assess the manufacturer’s sustainability practices. In today’s environmentally conscious market, it’s important to choose a manufacturer that prioritizes eco-friendly materials and processes. Fenner Dunlop’s ECO series is a prime example of how manufacturers are integrating sustainability into their product lines.
By considering these factors, mining operations can ensure they select a manufacturer that not only provides high-quality mine conveyor belt systems but also aligns with their operational goals and values.
Diverse Types of Mine Conveyor Belt Systems
Overview of Different Conveyor Belt Types and Their Applications in Mining
Mine conveyor belt systems are essential for the efficient and safe transportation of materials within mining operations. These systems have evolved to meet the demands of different mining environments and material handling requirements. The selection of the right type of conveyor belt is crucial for optimizing performance, ensuring safety, and reducing operational costs. Various types of conveyor belts are designed for specific applications, each with unique features and benefits.
Detailed Descriptions and Use-Cases for Each Type
To provide a clear understanding of the diverse types of mine conveyor belt systems and their specific applications, the following table outlines key types, their features, and use-cases:
Criteria for Selecting the Right Type of Conveyor Belt for Specific Mining Operations
Selecting the appropriate mine conveyor belt system requires careful consideration of several factors. The first step is to assess the specific material handling requirements, such as the type of material, its abrasiveness, temperature, and potential exposure to oils or chemicals. It’s also important to consider the operational environment, including whether the belt will be used above or underground, and the distance and inclination of the transport path.
Additionally, evaluating the belt’s durability, tensile strength, and resistance to environmental factors is crucial. Manufacturers like ContiTech, Fenner Dunlop, and Bridgestone provide detailed specifications and case studies that can help in making informed decisions. Ensuring compliance with safety standards, especially for flame-resistant and heat-resistant belts, is essential for maintaining a safe working environment.
By understanding the unique requirements of each mining operation and the capabilities of different mine conveyor belt systems, operators can optimize their material handling processes, enhance efficiency, and reduce operational costs.
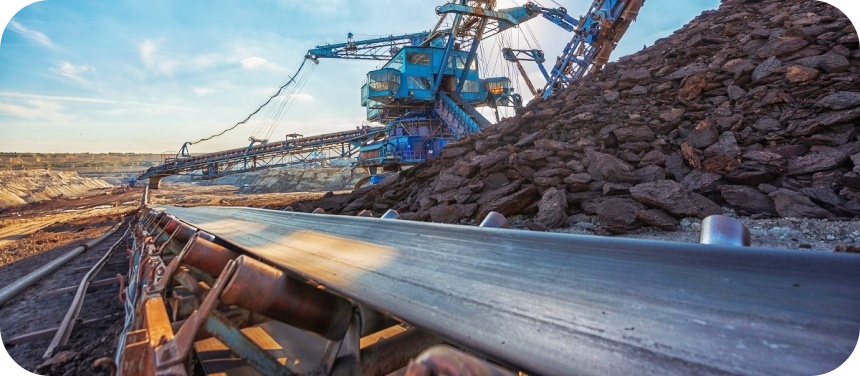
Comprehensive Resources on Mine Conveyor Belt Systems
Importance of Detailed Documentation and Guides in PDF Format
In the mining industry, having access to comprehensive and detailed documentation is crucial for the efficient and safe operation of mine conveyor belt systems. PDFs serve as an invaluable resource for operators, technicians, and engineers, providing a centralized and easily accessible repository of information. These documents are essential for ensuring that mine conveyor belt systems operate smoothly, minimizing downtime and maximizing productivity.
Detailed PDFs cover various aspects of mine conveyor belt systems, including installation procedures, maintenance schedules, and safety protocols. This information helps in standardizing operations, ensuring that all personnel are well-informed and capable of handling the equipment correctly. For example, ContiTech provides extensive PDF guides that detail the installation and maintenance of their conveyor belts, ensuring that customers can set up and maintain their systems with confidence.
Overview of Essential Topics Covered in Mining Conveyor Belt System PDFs
Mine conveyor belt systems PDFs typically cover a wide range of topics that are essential for the effective management and operation of these systems. Key topics include:
- Installation Guides: Detailed instructions on how to properly install mine conveyor belt systems, including specifications on tensioning, alignment, and splicing.
- Maintenance Manuals: Comprehensive guides on regular maintenance practices to ensure the longevity and reliability of the conveyor belt systems. These manuals often include schedules for routine inspections and parts replacements.
- Safety Protocols: Critical information on safety procedures and standards that must be adhered to during the operation and maintenance of mine conveyor belt systems. This includes emergency procedures, risk assessments, and compliance with industry regulations.
- Operational Best Practices: Recommendations for optimizing the performance and efficiency of mine conveyor belt systems, including tips on load management, belt speed, and environmental considerations.
Examples of Useful PDF Resources
Several companies provide detailed PDFs that serve as invaluable resources for those operating mine conveyor belt systems. Some notable examples include:
- Fenner Dunlop’s Installation and Maintenance Guides: These guides offer step-by-step instructions on installing and maintaining conveyor belts, ensuring that systems are set up correctly and maintained to the highest standards. Fenner Dunlop’s PDFs include diagrams and detailed explanations, making them user-friendly for both experienced technicians and newcomers.
- Bridgestone’s Conveyor Belt Design Manual: This comprehensive manual covers the design aspects of conveyor belts, including materials selection, load calculations, and design criteria. It provides a thorough understanding of how to design effective mine conveyor belt systems tailored to specific mining conditions.
- ContiTech’s Safety Protocols: ContiTech provides extensive safety documentation, outlining the necessary precautions and procedures to ensure safe operation. Their PDFs include guidelines on handling hazardous materials, emergency response plans, and compliance with international safety standards.
Benefits of Having Access to Extensive Documentation for Operational Efficiency and Troubleshooting
Having access to extensive documentation in the form of PDFs offers numerous benefits for the operation of mine conveyor belt systems.
- Operational Efficiency: Detailed documentation ensures that all aspects of the conveyor belt systems are understood and properly managed. This leads to more efficient operations, as personnel can refer to the PDFs for guidance on best practices, troubleshooting tips, and optimization strategies.
- Reduced Downtime: Maintenance manuals and troubleshooting guides help in identifying and addressing issues promptly, reducing downtime and maintaining continuous operation. For instance, regular reference to Fenner Dunlop’s maintenance guides can help identify wear and tear early, allowing for timely interventions.
- Enhanced Safety: Safety protocols and procedures detailed in PDFs ensure that all personnel are aware of and adhere to safety standards, reducing the risk of accidents and injuries. ContiTech’s safety documentation is particularly valuable in ensuring that safety is prioritized in all operations.
- Consistency in Operations: PDFs provide a standardized approach to operating and maintaining mine conveyor belt systems, ensuring consistency across different sites and teams. This is crucial for large mining operations with multiple sites, where standardized procedures help maintain uniformity and quality.
By integrating these comprehensive PDF resources into their operational workflows, mining companies can significantly enhance the efficiency, safety, and reliability of their mine conveyor belt systems.
Maintaining Mine Conveyor Belt Systems for Optimal Performance
Importance of Regular Maintenance and Its Impact on System Longevity
Regular maintenance is crucial for the optimal performance and longevity of mine conveyor belt systems. These systems are subjected to harsh conditions, including heavy loads, abrasive materials, and extreme weather, which can lead to wear and tear. Consistent maintenance ensures that the conveyor belts remain in good condition, reducing the likelihood of unexpected breakdowns and costly repairs.
The impact of regular maintenance on the longevity of mine conveyor belt systems cannot be overstated. For example, a study by ContiTech found that well-maintained conveyor belts could extend their operational life by up to 30%. This not only enhances productivity by minimizing downtime but also saves significant costs in the long term. Regular inspections and maintenance routines help in identifying potential issues early, allowing for timely interventions that prevent minor problems from escalating into major failures.
Key Maintenance Practices for Mine Conveyor Belt Systems
Effective maintenance of mine conveyor belt systems involves several key practices, each aimed at ensuring the system’s reliability and efficiency.
- Routine Inspections: Regular inspections are essential for identifying wear and damage. Inspectors should check for signs of belt wear, misalignment, and damage to the conveyor structure. For instance, Fenner Dunlop recommends weekly inspections to ensure all components are functioning correctly.
- Belt Cleaning: Keeping the conveyor belt clean is vital for preventing material buildup, which can lead to misalignment and increased wear. Automated belt cleaning systems, like those provided by Bridgestone, can significantly reduce manual cleaning efforts and improve system efficiency.
- Lubrication: Proper lubrication of moving parts, such as bearings and rollers, reduces friction and wear. This practice is essential for maintaining smooth operation and prolonging the life of the conveyor components.
- Tensioning and Alignment: Ensuring the belt is properly tensioned and aligned prevents excessive wear and reduces the risk of belt slippage or breakage. ContiTech provides detailed guidelines on how to correctly tension and align conveyor belts to optimize performance.
Advanced Monitoring and Diagnostic Tools for Predictive Maintenance
The use of advanced monitoring and diagnostic tools is revolutionizing the maintenance of mine conveyor belt systems. These tools enable predictive maintenance, allowing operators to address issues before they lead to system failures.
- Condition Monitoring Systems: Systems like Fenner Dunlop’s EagleEye® provide real-time monitoring of conveyor belt conditions. These systems use sensors to detect anomalies such as belt slippage, excessive wear, and misalignment, alerting operators to potential problems before they become critical.
- Thermal Imaging: Thermal imaging cameras can identify overheating components, such as bearings and motors, which may indicate impending failure. Regular thermal scans help in early detection of issues, enabling preemptive maintenance actions.
- Ultrasonic Testing: This technology is used to detect internal damage within the conveyor belt, such as tears and delaminations. Ultrasonic testing provides a non-invasive method to assess the health of the belt and ensure it is free from hidden defects.
Common Maintenance Challenges and Solutions
Despite the best maintenance practices, operators of mine conveyor belt systems often face several common challenges. Addressing these challenges effectively is crucial for maintaining optimal performance.
- Material Buildup: One of the most common issues is material buildup on the belt and conveyor components. This can lead to misalignment and increased wear. Implementing effective belt cleaning systems and regular maintenance routines can mitigate this problem.
- Component Wear: High abrasion and heavy loads can cause rapid wear of conveyor components. Using high-quality, abrasion-resistant materials, like those in ContiTech’s Decter belts, can reduce wear and extend the life of the components.
- Environmental Conditions: Extreme weather conditions, such as high temperatures and humidity, can affect the performance of mine conveyor belt systems. Heat-resistant and moisture-resistant belts, like those provided by Fenner Dunlop, are essential for maintaining performance in harsh environments.
- Misalignment: Conveyor belt misalignment is a common issue that can lead to significant wear and tear. Regular inspections and adjustments, as well as the use of advanced alignment tools, can help maintain proper belt alignment.
By implementing these key maintenance practices, utilizing advanced monitoring tools, and addressing common challenges, operators can ensure that their mine conveyor belt systems operate at peak efficiency, reducing downtime and extending the lifespan of the equipment.
Acquiring Mine Conveyor Belt Systems: Buying Guide
Factors to Consider When Purchasing a Mine Conveyor Belt System
When acquiring mine conveyor belt systems, several crucial factors must be considered to ensure the selection of a system that meets operational needs and provides long-term value. Key considerations include:
- Material Handling Requirements: The type of materials being transported, their abrasiveness, and the distance they need to be moved are essential factors. For example, heavy ores require robust systems like steel cord conveyor belts, while lighter materials might only need standard rubber belts.
- Environmental Conditions: The operating environment, including temperature extremes, humidity, and exposure to chemicals or oils, influences the type of conveyor belt needed. Fenner Dunlop’s HeatMaster series is designed for high-temperature environments, while their Oil-Resistant belts are suited for greasy conditions.
- Durability and Lifespan: Investing in durable mine conveyor belt systems is crucial for minimizing downtime and maintenance costs. Systems from manufacturers like ContiTech and Bridgestone are known for their longevity and resilience in harsh mining conditions.
- Regulatory Compliance: Ensuring that the conveyor belt systems comply with local and international safety and environmental regulations is vital. This includes adherence to fire resistance standards for underground belts and other specific industry requirements.
Overview of Different Purchasing Options (New vs. Used Systems)
When purchasing mine conveyor belt systems, operators can choose between new and used systems. Each option has its benefits and considerations.
How to Evaluate Vendors and Suppliers for Quality and Reliability
Selecting a reliable vendor or supplier is crucial for acquiring high-quality mine conveyor belt systems. Here are steps to evaluate potential vendors:
- Reputation and Track Record: Research the vendor’s reputation in the industry. Long-established companies like Fenner Dunlop and ContiTech are known for their reliability and quality products. Customer reviews and case studies can provide insights into their performance.
- Product Range and Customization: Ensure the vendor offers a wide range of conveyor belts that can be tailored to specific needs. Customization options are important for addressing unique mining challenges.
- After-Sales Support: Reliable vendors provide comprehensive after-sales support, including installation assistance, maintenance services, and troubleshooting. For example, Fenner Dunlop offers extensive support and training for their products, ensuring optimal performance and longevity.
- Certifications and Compliance: Verify that the vendor’s products comply with relevant industry standards and certifications. This includes fire resistance, durability, and environmental compliance.
Cost-Benefit Analysis of Investing in High-Quality Conveyor Belt Systems
Investing in high-quality mine conveyor belt systems can lead to significant long-term benefits, despite the higher initial cost. Here’s a cost-benefit analysis:
- Initial Investment: High-quality conveyor belts from top manufacturers may have a higher upfront cost. For instance, a new steel cord belt from Bridgestone might cost more than a standard rubber belt.
- Operational Efficiency: High-quality systems are designed to optimize efficiency and reduce operational costs. Bridgestone’s SLL belts, for example, can reduce energy consumption by up to 25%, leading to substantial savings over time.
- Maintenance and Downtime: Durable and reliable conveyor belts require less frequent maintenance and experience fewer breakdowns. This reduces downtime and maintenance costs, ensuring continuous operation and productivity. ContiTech’s Flexsteel belts, known for their durability, often result in lower long-term maintenance expenses.
- Longevity: Investing in high-quality belts ensures a longer operational lifespan. While the initial cost is higher, the extended lifespan and reduced need for replacements can result in significant cost savings.
- Safety and Compliance: High-quality conveyor belts that meet safety and environmental standards help avoid fines and compliance issues. This not only protects workers but also enhances the company’s reputation and operational stability.
Choosing the right mine conveyor belt systems involves careful consideration of various factors, a thorough evaluation of vendors, and a cost-benefit analysis to ensure long-term efficiency and reliability. By investing in high-quality systems, mining operations can achieve optimal performance, safety, and cost savings.
Special Considerations for Mine Conveyor Belt Systems in Underground Mining
Unique Challenges and Requirements for Underground Mining Conveyor Belts
Underground mining presents unique challenges that significantly impact the design and operation of mine conveyor belt systems. These environments are characterized by confined spaces, high humidity, and potential exposure to flammable gases, all of which necessitate robust and specialized conveyor belt solutions.
One primary challenge is the limited space available for installing and operating conveyor belts. Mine conveyor belt systems in underground settings must be designed to fit within narrow tunnels and shafts without compromising efficiency or safety. This often involves using belts with smaller widths and employing innovative installation techniques to maximize space utilization.
Another critical requirement is the ability to withstand harsh environmental conditions. For instance, the belts must be resistant to moisture and abrasion, as they often encounter wet and abrasive materials. Fenner Dunlop’s MineFlex belts are specifically designed for such conditions, offering high resistance to wear and tear while maintaining flexibility and strength.
The potential presence of flammable gases and dust in underground mines necessitates the use of flame-resistant conveyor belts. These belts must meet stringent safety standards to prevent ignition and propagation of fire. The FireMaster series by Fenner Dunlop is an example of such a belt, featuring self-extinguishing properties and compliance with international safety regulations.
Safety Features and Regulatory Compliance for Underground Conveyor Belts
Safety is paramount in underground mining, and mine conveyor belt systems must incorporate specific features to ensure the protection of workers and equipment. Flame resistance is a crucial safety feature, as underground mines are particularly susceptible to fire hazards. Conveyor belts used in these environments must comply with regulations such as MSHA (Mine Safety and Health Administration) standards in the United States or similar international standards.
In addition to flame resistance, mine conveyor belt systems must include anti-static properties to reduce the risk of sparks that could ignite flammable gases. These belts are treated with special compounds to dissipate static electricity, enhancing safety in explosive environments.
Regular inspection and maintenance protocols are also vital for maintaining the safety and reliability of underground conveyor belts. ContiTech offers comprehensive maintenance manuals and inspection guidelines that help operators adhere to safety standards and ensure the longevity of their belts.
Technologies Enhancing the Performance of Conveyor Belts in Underground Settings
Advancements in technology have significantly enhanced the performance and reliability of mine conveyor belt systems in underground mining. One such technology is the development of sensor-based monitoring systems that provide real-time data on belt conditions. These systems, like Fenner Dunlop’s EagleEye®, use sensors to detect wear, misalignment, and other potential issues, allowing for proactive maintenance and reducing downtime.
Automated tensioning systems are another technological advancement that improves the performance of underground conveyor belts. These systems ensure that the belts remain at optimal tension, preventing slippage and reducing wear. ContiTech’s AutoTension system, for instance, continuously monitors and adjusts belt tension, enhancing efficiency and extending the belt’s lifespan.
Material science advancements have led to the development of more durable and flexible belt materials. High-strength synthetic materials and reinforced steel cords are now commonly used in underground mining conveyor belts, providing superior durability and resistance to harsh conditions. Bridgestone’s steel cord belts, for example, are designed to handle heavy loads and extreme conditions, making them ideal for underground mining operations.
Case Studies of Underground Mining Operations Using Conveyor Belt Systems
Real-world examples highlight the effectiveness and reliability of advanced mine conveyor belt systems in underground mining operations. One notable case is the use of Fenner Dunlop’s FireMaster conveyor belts in a coal mine in Queensland, Australia. These belts provided exceptional flame resistance and durability, significantly enhancing safety and operational efficiency in the mine.
Another example is the implementation of ContiTech’s AutoTension system in a copper mine in Chile. The automated tensioning system reduced maintenance requirements and improved the overall performance of the conveyor belt system, leading to increased productivity and reduced operational costs.
In South Africa, a platinum mine employed Bridgestone’s steel cord conveyor belts to transport ore from deep underground shafts to the surface. The belts’ high strength and resistance to wear ensured reliable operation in a demanding environment, demonstrating the importance of selecting the right belt for specific mining conditions.
These case studies underscore the critical role of advanced mine conveyor belt systems in enhancing safety, efficiency, and reliability in underground mining operations. By addressing the unique challenges of these environments and leveraging the latest technologies, mining companies can optimize their material handling processes and achieve greater operational success.
Need custom conveyor belts? Contact us for tailored solutions!
FAQs about Mine Conveyor Belt Systems
In mining operations, heavy-duty conveyor belts are essential for transporting materials efficiently and safely. The most commonly used type is the steel cord conveyor belt. These belts are designed to handle heavy loads and long distances, making them ideal for the mining industry. Steel cord belts consist of a rubber cover and steel cords that provide high tensile strength and resistance to impact, tearing, and abrasion. Additionally, they offer excellent flexibility and can be used in both underground and surface mining applications. These belts are particularly suited for transporting bulk materials such as coal, ore, and aggregates. They ensure reliable operation even in harsh environments, contributing to the efficiency and productivity of mining operations.
The most commonly used belt in mines is the steel cord conveyor belt. Steel cord belts are favored for their durability, strength, and ability to handle high-stress conditions. These belts feature steel cords embedded within the rubber, providing superior tensile strength and resistance to stretching and tearing. This construction allows them to transport large volumes of materials over long distances, which is a common requirement in mining operations. Steel cord belts are also highly resistant to fire and heat, which enhances safety in underground mining environments. Their robust design ensures minimal downtime and maintenance, making them a cost-effective choice for mining companies looking to optimize their material handling processes.
Mining operations utilize several types of conveyor belts, each designed to meet specific requirements. The primary types include steel cord belts, textile belts, and solid woven belts. Steel cord belts, known for their strength and durability, are ideal for long-distance and heavy-load applications. Textile belts, made from synthetic fibers, offer flexibility and are suitable for shorter distances and lighter loads. They are often used in conjunction with steel cord belts in various stages of the mining process. Solid woven belts are another option, providing excellent resistance to impact, cutting, and abrasion. These belts are commonly used in underground mining due to their fire-resistant properties. Each type of belt plays a crucial role in ensuring efficient material transport and handling within the mining industry, contributing to overall productivity and safety.
The most common conveyor belt system in mining is the steel cord conveyor belt system. This system is widely used due to its ability to handle large volumes of materials over extended distances with high efficiency. Steel cord conveyor belts are known for their exceptional strength, flexibility, and durability, making them suitable for the demanding conditions of mining operations. These systems typically include a series of belts, pulleys, and motors that work together to transport materials from the mining site to processing areas or storage facilities. The steel cords within the belts provide the necessary tensile strength to withstand the heavy loads and high-speed operation required in mining. Additionally, these systems are designed to minimize downtime and maintenance costs, enhancing overall operational efficiency. The robust construction and reliable performance of steel cord conveyor belt systems make them the preferred choice for many mining companies worldwide.
Last Updated on August 9, 2024 by Jordan Smith
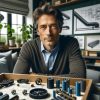
Jordan Smith, a seasoned professional with over 20 years of experience in the conveyor system industry. Jordan’s expertise lies in providing comprehensive solutions for conveyor rollers, belts, and accessories, catering to a wide range of industrial needs. From initial design and configuration to installation and meticulous troubleshooting, Jordan is adept at handling all aspects of conveyor system management. Whether you’re looking to upgrade your production line with efficient conveyor belts, require custom conveyor rollers for specific operations, or need expert advice on selecting the right conveyor accessories for your facility, Jordan is your reliable consultant. For any inquiries or assistance with conveyor system optimization, Jordan is available to share his wealth of knowledge and experience. Feel free to reach out at any time for professional guidance on all matters related to conveyor rollers, belts, and accessories.