The Essential Guide to Mini Gravity Roller Conveyor
In the realm of material handling and logistics, the efficiency and smooth operation of conveyor systems are paramount. Among these systems, the mini gravity roller conveyor stands out for its simplicity and effectiveness in moving goods. This type of conveyor utilizes the force of gravity to propel items forward, making it an energy-efficient solution for businesses. The focus on mini gravity roller conveyor, along with its essential components like conveyor rollers, small diameter conveyor rollers, and small diameter rollers, highlights the importance of compact and versatile conveyor solutions in today’s fast-paced industrial environments. These conveyors are specifically designed to handle small packages and items, providing a seamless and cost-effective method for sorting, distributing, and transporting goods across various sectors. Their introduction has revolutionized the way small items are handled, offering both flexibility and reliability in operations.
The Basics of Mini Gravity Roller Conveyor
Mini gravity roller conveyors are an essential component of modern material handling, designed to transport goods using the natural force of gravity. Unlike traditional conveyor systems, these mini conveyors are specifically engineered for efficiency, flexibility, and cost-effectiveness in handling small packages. Here’s how they stand apart:
- Size and Scalability: Mini gravity roller conveyors are compact and can be easily integrated into existing spaces or systems, making them ideal for facilities with limited space.
- Energy Efficiency: These conveyors utilize gravity, eliminating the need for electrical power to move items, which reduces energy consumption and operational costs.
- Simplicity of Design: With fewer moving parts than motorized conveyors, mini gravity roller conveyors are simpler in design, leading to lower maintenance requirements and downtime.
- Cost-Effectiveness: The initial investment and ongoing operational costs are significantly lower for mini gravity roller conveyors compared to their powered counterparts.
- Flexibility in Application: They can be used in a variety of settings, from packaging lines to distribution centers, offering versatility in material handling.
- Ease of Installation: Mini gravity roller conveyors can be quickly and easily installed, reconfigured, or expanded, allowing for scalability as business needs change.
- Improved Safety: With no power source and fewer mechanical components, these conveyors pose a lower risk of accidents or injuries, enhancing workplace safety.
- Quiet Operation: The absence of motors and electrical components means mini gravity roller conveyors operate quietly, contributing to a more pleasant work environment.
The role of small diameter rollers in mini gravity roller conveyors cannot be overstated. These rollers are pivotal in providing several advantages for handling small packages:
- Enhanced Product Handling: Small diameter rollers ensure smoother transitions and handling of small or lightweight items, minimizing product damage.
- Increased Flexibility: They allow for tighter turns and closer roller spacing, accommodating a wider range of product sizes and shapes.
- Lower Resistance: Small diameter rollers reduce the friction between the conveyor and the product, facilitating easier movement of goods.
- Improved Precision: The closer spacing of small rollers offers better control and positioning of items on the conveyor, crucial for assembly or sorting tasks.
- Modularity: Systems equipped with small diameter rollers can be easily modified or extended, providing businesses with the flexibility to adapt to changing operational needs.
- Cost Savings: The efficiency and reduced maintenance of conveyors with small diameter rollers contribute to lower operational costs over time.
- Space Optimization: Their compact size allows for more efficient use of available space, a critical factor in crowded or limited work areas.
- Ease of Maintenance: Simple design and accessibility make it easier to perform maintenance or replace individual rollers, reducing downtime.
- Versatility: Small diameter rollers are suitable for a variety of materials and surfaces, enhancing the conveyor’s utility across different industries.
Mini gravity roller conveyors, with their small diameter rollers, represent a pivotal innovation in the field of material handling, offering a multitude of benefits for businesses looking to improve efficiency and reduce costs in the transportation of small packages.
Key Features of Mini Gravity Roller Conveyor
Mini gravity roller conveyors are a cornerstone in the efficient movement of goods within various industrial settings. Their design and functionality offer a multitude of benefits, making them a preferred choice for businesses looking to optimize their operations. Here are some key features that distinguish these conveyors:
- Durability and Material Options: Mini gravity roller conveyors are built to last, with construction materials including high-grade steel and lightweight aluminum. These materials ensure the conveyors can withstand the rigors of daily use while providing the flexibility to choose the right material based on environmental conditions and the nature of goods being transported. Steel offers robustness for heavier loads, whereas aluminum provides a lighter option for easier mobility and resistance to corrosion.
- Roller Specifications: The heart of mini gravity roller conveyors lies in their rollers, which are available in small diameters to accommodate a wide range of products. These rollers come with various weight capacities, catering to different operational needs. The incorporation of spring-loaded axles facilitates easy installation and replacement, enhancing the conveyor’s overall efficiency and reducing maintenance time.
- Frame Specifications: The versatility of mini gravity roller conveyors is partly due to their frame designs, which allow rollers to be set above or below the frame. This flexibility ensures that the conveyor can be adapted to different applications, whether it requires a flat surface for smooth transitions or elevated rollers for easier manual access to goods.
- Modularity: These conveyors are designed to be modular, meaning they can be easily extended, shortened, or integrated with existing conveyor systems. This modularity allows for quick adjustments to the layout or length of the conveyor line, accommodating changes in production needs or facility layouts without significant downtime.
- Ease of Installation: The design of mini gravity roller conveyors simplifies installation, enabling quick setup and integration into existing operations. This ease of installation reduces the need for specialized tools or extensive technical expertise, allowing businesses to get their conveyor systems up and running in less time.
- Low Maintenance: Thanks to their simple design and the use of durable materials, mini gravity roller conveyors require minimal maintenance. The need for lubrication is reduced, and the ease of replacing rollers or adjusting the frame contributes to lower maintenance costs and less operational downtime.
- Energy Efficiency: Operating without the need for power, mini gravity roller conveyors utilize the natural force of gravity to move products. This not only reduces energy consumption but also minimizes the environmental impact of the conveyor system, making it a sustainable choice for eco-conscious businesses.
- Cost-Effectiveness: The initial investment and ongoing operational costs of mini gravity roller conveyors are significantly lower compared to powered conveyor systems. Their durability, low maintenance requirements, and energy efficiency contribute to a lower total cost of ownership, offering an economical solution for material handling needs.
Mini gravity roller conveyors, with their array of key features, provide a reliable, efficient, and cost-effective solution for transporting goods. Their durability, flexibility, and ease of use make them an invaluable asset in streamlining operations and enhancing productivity in various industrial environments.
Discover our premium conveyor rollers. Inquire for more information!
Applications and Benefits of Mini Gravity Roller Conveyor
Mini gravity roller conveyors are versatile systems that play a crucial role in the efficient movement of goods across various sectors. Their design allows for a wide range of applications, while the benefits they offer make them an attractive option for many businesses looking to improve their material handling processes.
Applications of Mini Gravity Roller Conveyor
The table below outlines some of the key applications of mini gravity roller conveyors across different industries:
Benefits of Mini Ggravity Roller Conveyor
The integration of mini gravity roller conveyors into material handling systems brings about significant operational advantages:
- Versatility in Material Handling: Mini gravity roller conveyors can be used across various industries, including manufacturing, distribution, and retail, showcasing their flexibility in handling different types of goods.
- Economical and Energy Efficient: These conveyors do not require electricity to operate, making them an energy-efficient solution. Their low initial cost and minimal maintenance requirements further contribute to their cost-effectiveness.
- Customization and Integration: Mini gravity roller conveyors can be easily customized and integrated into existing material handling setups, allowing businesses to tailor the system to their specific needs for enhanced efficiency.
- Ease of Installation and Reconfiguration: The simple design of mini gravity roller conveyors allows for quick installation and easy reconfiguration, adapting to changing business needs without significant downtime.
- Improved Workplace Safety: By reducing the need for manual handling of goods, these conveyors help minimize the risk of injuries, contributing to a safer work environment.
- Low Maintenance Requirements: The durable design and quality materials used in mini gravity roller conveyors result in lower maintenance needs, reducing long-term operational costs.
- Quiet Operation: Unlike powered conveyors, mini gravity roller conveyors operate quietly, contributing to a more pleasant and less disruptive work environment.
- Enhanced Productivity: By streamlining the movement of goods, mini gravity roller conveyors can significantly increase productivity, ensuring that products are moved quickly and efficiently through the production line or warehouse.
Mini gravity roller conveyors offer a range of applications and benefits that make them a valuable asset in any material handling system. Their versatility, cost-effectiveness, and ease of integration provide businesses with a practical solution for improving their operations, enhancing efficiency, and reducing costs.
How to Choose the Right Mini Gravity Roller Conveyor
Selecting the appropriate mini gravity roller conveyor for your operational needs involves careful consideration of various factors. These conveyors are pivotal in optimizing efficiency and productivity in material handling. Below, we delve into the essential considerations for selection and the availability of custom solutions to ensure you make the most informed decision.
Considerations for Selection
When it comes to choosing the right mini gravity roller conveyor, several key factors must be taken into account to ensure the conveyor meets your specific requirements:
- Load Capacity: Assess the weight of the items the conveyor will need to handle. Ensuring the mini gravity roller conveyor can support the weight of your products is crucial to prevent damage to the conveyor and ensure safety in operations.
- Roller Material: The material of the rollers (steel, aluminum, or plastic) should be selected based on the environment in which the conveyor will be used and the type of products it will carry. For instance, steel rollers are ideal for heavy-duty applications, while aluminum or plastic rollers might be preferred for lighter loads or specific environmental conditions.
- Frame Design: The design of the frame affects the conveyor’s strength and durability. Consider the frame material and construction to ensure it meets the demands of your operational environment.
- Roller Diameter and Spacing: Small diameter rollers are better suited for smaller items, but the specific size and spacing will depend on the dimensions of the products being transported. Closer spacing can support smaller items more effectively.
- Conveyor Length and Width: The size of the conveyor should match the space available in your facility and the size of the items being transported. It’s important to measure the area where the conveyor will be installed to ensure a proper fit.
- Flexibility and Modularity: Consider whether your operation requires a conveyor that can be easily reconfigured or expanded in the future. Modular mini gravity roller conveyors offer the flexibility to adjust to changing business needs.
- Environmental Conditions: If the conveyor will be used in a harsh environment (e.g., high humidity, exposure to chemicals), select materials and designs that can withstand these conditions without corroding or degrading.
- Cost: While it’s important to find a cost-effective solution, consider the total cost of ownership, including maintenance, durability, and efficiency, rather than just the initial purchase price.
Custom Solutions
Custom configurations for mini gravity roller conveyors are not just about adapting to physical dimensions; they also involve tailoring the system to meet specific operational challenges and efficiency goals. Here are additional aspects where custom solutions can significantly benefit your operations:
- Integration with Other Systems: Custom solutions can ensure seamless integration with existing conveyor systems, automated sorting systems, or warehouse management software, enhancing overall operational coherence and efficiency.
- Specialized Roller Surfaces: For operations that require the handling of very delicate or slippery items, rollers can be coated with materials that increase grip or reduce the chance of damage to the items being transported.
- Adjustable Speed Capabilities: While traditional mini gravity roller conveyors rely on gravity, custom solutions can include adjustable inclines or added mechanisms like brake rollers to control the speed of the conveyed items, ensuring smooth and safe handling, especially in areas where manual interaction is frequent.
- Enhanced Load Distribution: Custom configurations can be designed to improve load distribution across the conveyor, preventing overloading on certain sections and ensuring uniform wear and tear. This is particularly important for irregularly shaped items or varying load sizes.
- Environment-specific Adaptations: For operations in extreme environments, such as cold storage, cleanrooms, or outdoor settings, conveyors can be customized with materials and lubricants suited to these conditions, ensuring reliability and longevity of the system.
By considering these additional custom solution aspects, businesses can further optimize their mini gravity roller conveyor systems to meet specific operational needs, improve efficiency, and reduce costs. Tailoring the system extends beyond mere physical adjustments, encompassing a holistic approach to operational improvement and integration within the broader logistical framework. This level of customization ensures that the conveyor system is not only a perfect fit for the current operational setup but also adaptable to future changes and challenges.
Selecting the right mini gravity roller conveyor involves careful consideration of your specific needs and operational conditions. By focusing on these key considerations and exploring custom solutions, you can ensure that your conveyor system optimally supports your material handling processes.
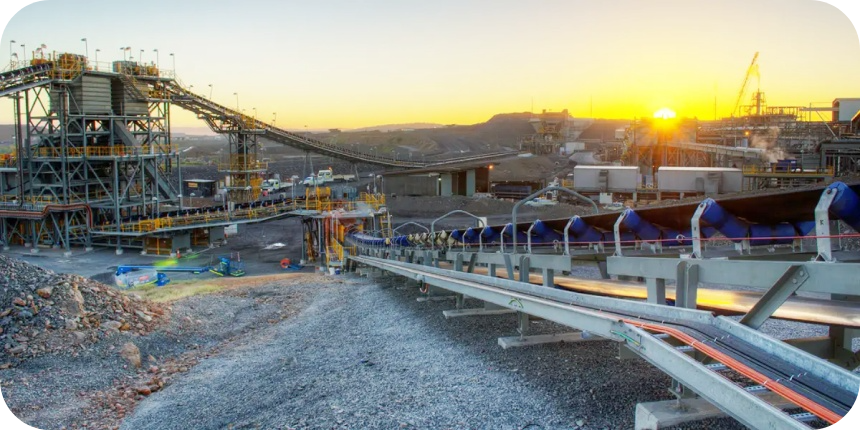
Installation and Maintenance of Mini Gravity Roller Conveyor
Ensuring the optimal performance and longevity of your mini gravity roller conveyor system involves careful attention during both the installation and maintenance phases. Proper setup and regular upkeep can significantly enhance the efficiency and durability of these essential components of material handling systems.
Setting Up Your Conveyor System
Here are eight fundamental tips for installing mini gravity roller conveyors:
- Understand the Layout: Before installation, thoroughly plan the layout of the conveyor system. Consider the flow of materials, available space, and integration with other systems.
- Check the Floor Level: Ensure the installation surface is level. An uneven floor can lead to inefficient operation and excessive wear on the conveyor.
- Assemble with Care: Follow the manufacturer’s instructions closely during assembly. Incorrect assembly can lead to operational issues or safety hazards.
- Adjust Roller Spacing: Based on the size of the items being transported, adjust the spacing of the rollers to prevent items from slipping between them.
- Securely Fasten All Components: Ensure all parts of the conveyor are securely fastened and check for any loose components to prevent accidents or malfunctions.
- Test Before Use: Once installed, run tests with your actual products to ensure the conveyor operates smoothly and efficiently under load.
- Train Your Staff: Proper training on the operation and safety protocols of the mini gravity roller conveyor is essential for all staff members who will interact with the system.
- Consider Ergonomics: Install the conveyor at a height that is comfortable for operators, reducing strain and improving productivity.
Maintenance Tips
Maintaining your mini gravity roller conveyor is crucial for its longevity and reliability. Here are nine maintenance tips:
- Regular Inspections: Conduct regular inspections to identify any potential issues early, such as misaligned rollers or loose components.
- Clean Rollers Regularly: Keep the rollers clean to prevent build-up of debris that can hinder the conveyor’s performance.
- Lubricate Bearings: If the conveyor’s design allows for lubrication, ensure bearings are lubricated properly to reduce friction and wear.
- Check for Wear and Tear: Regularly inspect rollers and frames for signs of wear or damage and replace parts as necessary.
- Maintain Proper Alignment: Ensure the conveyor remains properly aligned. Misalignment can cause uneven wear and operational inefficiencies.
- Tighten Fasteners: Periodically check and tighten any bolts and fasteners to prevent loosening due to vibration.
- Monitor Load Capacities: Avoid overloading the conveyor, as excessive weight can strain the system and lead to premature wear.
- Implement a Maintenance Schedule: Establish a regular maintenance schedule based on the manufacturer’s recommendations and stick to it.
- Keep Spare Parts on Hand: Having spare rollers, bearings, and other critical parts on hand can minimize downtime when replacements are necessary.
By adhering to these installation and maintenance guidelines, you can ensure that your mini gravity roller conveyor operates at peak efficiency, providing reliable service for many years. Regular upkeep not only extends the life of the conveyor but also maintains its safety and effectiveness in your material handling operations.
FAQs about Mini Gravity Roller Conveyor
Gravity roller conveyors are essential components in the material handling industry, designed to facilitate the movement of goods across a defined area with minimal effort. Utilizing the force of gravity, these conveyors efficiently transport items across flat or slightly inclined surfaces. They are predominantly used for moving products in warehouses, distribution centers, manufacturing plants, and packaging facilities. The simplicity of their design allows for the easy transportation of a wide variety of items, ranging from small boxes to large pallets, making them a versatile solution for many sectors.
The primary use of gravity roller conveyors is to streamline the process of moving goods, whether it’s for sorting, assembly, inspection, or packaging. They significantly reduce the need for manual handling, thereby minimizing labor costs and enhancing workplace safety. Additionally, gravity roller conveyors can be integrated into larger conveyor systems, serving as a cost-effective method for transporting products over short to medium distances within a facility.
Gravity conveyor rollers come in a variety of sizes to accommodate different loads and operational requirements. The diameter of these rollers can range from as small as 3/4 inch to over 3 inches, with the most common sizes being 1.9 inches and 2.5 inches. The length of the rollers also varies, designed to match the width of the conveyor and the size of the products being transported. This can range from a few inches to several feet, ensuring that there is a roller size available to meet the specific needs of any material handling application.
The choice of roller size is critical, as it affects the conveyor’s ability to transport items smoothly and efficiently. Smaller diameter rollers are typically used for lighter loads and smaller items, providing closer spacing that supports the underside of the transported goods more uniformly. Larger rollers, on the other hand, are suited for heavier loads, offering greater durability and the ability to handle more weight without deformation.
Conveyor rollers are categorized based on their design, functionality, and the materials used in their construction. The main types include:
Gravity Rollers: Operate without external power, using the force of gravity to move items. Ideal for lightweight to medium-weight products.
Powered Rollers: Equipped with motors, these rollers move items along the conveyor belt at a consistent speed, suitable for heavier loads and automated systems.
Grooved Rollers: Designed with grooves that can accommodate belts or o-rings, allowing for the transportation of lighter items at slight inclines.
Plastic Rollers: Made from durable plastic materials, these rollers are lightweight, corrosion-resistant, and suitable for a variety of applications, including food processing.
Stainless Steel Rollers: Known for their durability and resistance to corrosion, making them ideal for harsh environments or where cleanliness is a priority.
Impact Rollers: Positioned at conveyor loading zones to absorb the impact of heavy items, protecting the belt and system from damage.
Each type of roller offers unique advantages and is selected based on the specific requirements of the application, including the weight of the items being transported, the environment in which the conveyor will operate, and the desired speed of movement.
The gravity roller conveyor is the type that operates on the principle of gravity. It does not require electrical power or manual effort to move items along its path. Instead, it relies on the natural force of gravity and the slight inclination of the conveyor to facilitate the movement of goods. This makes gravity roller conveyors an energy-efficient and cost-effective solution for transporting items across short to medium distances within a facility.
Gravity roller conveyors are widely used in various industries for tasks such as sorting, assembling, transporting, and accumulating products. They are particularly favored for their simplicity, reliability, and low maintenance requirements. By providing a smooth and controlled method of moving goods, gravity roller conveyors help improve operational efficiency, reduce manual labor, and enhance workplace safety.
Last Updated on June 26, 2024 by Jordan Smith
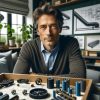
Jordan Smith, a seasoned professional with over 20 years of experience in the conveyor system industry. Jordan’s expertise lies in providing comprehensive solutions for conveyor rollers, belts, and accessories, catering to a wide range of industrial needs. From initial design and configuration to installation and meticulous troubleshooting, Jordan is adept at handling all aspects of conveyor system management. Whether you’re looking to upgrade your production line with efficient conveyor belts, require custom conveyor rollers for specific operations, or need expert advice on selecting the right conveyor accessories for your facility, Jordan is your reliable consultant. For any inquiries or assistance with conveyor system optimization, Jordan is available to share his wealth of knowledge and experience. Feel free to reach out at any time for professional guidance on all matters related to conveyor rollers, belts, and accessories.