Innovations in Mini Steel Roller: Enhancing Industrial Processes
Mini steel rollers are pivotal components in the machinery and equipment used across a broad spectrum of industries, from manufacturing and logistics to construction and beyond. These compact yet robust rollers are designed to facilitate the movement and handling of materials with efficiency and precision. The availability of mini steel roller for sale has revolutionized the way small-scale operations are conducted, offering solutions that are both cost-effective and space-saving. Their application in heavy-duty tasks is particularly noteworthy, as they are capable of withstanding high loads and rigorous use while maintaining their functionality and integrity. This versatility makes mini steel rollers an indispensable tool in the industrial world, underscoring their significance in enhancing operational efficiency and productivity in various settings.
What Is Mini Steel Roller
Mini steel rollers, integral components in the mechanics of modern machinery, offer a unique blend of durability and precision in a compact form. To fully grasp the essence and utility of mini steel roller, it’s essential to delve into their definition and key characteristics. These components are more than just small-scale versions of their larger counterparts; they are engineered with precision to fulfill specific roles in various industrial environments. Mini steel rollers are defined by their compact design, which does not compromise on strength or functionality. This unique combination of features makes them indispensable in scenarios where space is at a premium but efficiency and reliability cannot be sacrificed. Here, we explore nine pivotal attributes that define mini steel rollers and underscore their importance in industrial applications:
- Compact Size: Mini steel rollers are distinguished by their small size, making them ideal for applications where space is limited.
- High Durability: Constructed from steel, these rollers are built to withstand heavy loads and resist wear and tear, ensuring longevity.
- Precision Movement: They facilitate precise movement and control of materials, crucial for delicate and detailed operations.
- Versatility: Mini steel rollers are used in a variety of settings, from conveyor systems to machinery components.
- Load Capacity: Despite their small size, they can support significant weight, making them suitable for heavy-duty tasks.
- Corrosion Resistance: Many mini steel rollers are treated or manufactured with materials that resist corrosion, enhancing their durability in harsh environments.
- Easy Maintenance: Their design allows for easy maintenance and replacement, minimizing downtime in industrial operations.
- Cost-Effective: They offer an economical solution for upgrading or constructing machinery without compromising on quality.
- Customization: Mini steel roller can be customized in terms of size, material, and surface treatment to meet specific application requirements.
The distinction between mini steel roller and standard steel rollers
To further understand the role and efficiency of mini steel roller, it’s essential to compare them with standard steel rollers. The table below outlines the key distinctions:
Understanding the characteristics and distinctions of mini steel roller compared to standard steel rollers is crucial for selecting the right component for your machinery. Mini steel rollers offer a specialized solution where precision, durability, and space efficiency are paramount, making them a versatile choice for a wide range of industrial applications.
Types of Mini Steel Roller
The versatility of mini steel roller is evident in the variety of types available, each designed to meet specific industrial needs. From heavy-duty operations to applications requiring corrosion resistance, the selection of the right mini steel roller can significantly impact the efficiency and longevity of machinery. Here, we explore three primary types of mini steel roller, highlighting their features, benefits, and industrial applications.
Heavy Duty Mini Steel Rollers
Heavy-duty mini steel rollers are the backbone of many industrial operations, designed to endure the toughest conditions without compromising on performance. Their construction and design are focused on reliability and durability, essential for the demanding environments in which they operate.
Features and Benefits:
- Enhanced Durability: Utilizing high-grade steel and sometimes incorporating additional hardening processes to ensure they can withstand extreme conditions.
- Increased Load Capacity: Specifically engineered to handle substantial weights, these rollers are pivotal in sectors like mining, heavy manufacturing, and construction.
- Precision Engineering: Crafted with meticulous attention to detail, ensuring that they deliver precise movement and alignment critical in automated systems and precision machinery.
- Robust Design: Features such as reinforced cores and thicker walls make them resistant to bending and deformation.
- Versatile Applications: While designed for heavy loads, their precise engineering also makes them suitable for applications requiring detailed accuracy.
- Long Service Life: The combination of material quality, design, and construction techniques extends their operational lifespan, reducing the need for frequent replacements.
Stainless Steel Roller
Stainless steel rollers are the epitome of resilience and hygiene, making them a preferred choice in environments where cleanliness and resistance to corrosion are non-negotiable.
Advantages:
- Corrosion Resistance: Their resistance to rust and corrosion is unparalleled, thanks to the stainless steel construction, making them ideal for chemical processing plants, outdoor applications, and marine environments.
- Hygienic: The non-porous surface of stainless steel makes these rollers easy to sanitize, preventing bacterial growth and contamination.
- Versatility: Their durability and resistance to various environmental factors make them suitable for a wide array of applications, from food processing to pharmaceutical manufacturing.
- Aesthetic Appeal: Stainless steel has a clean, professional look that is maintained over time, even in harsh conditions.
- Temperature Resistance: Capable of withstanding high temperatures, these rollers are also used in heat-intensive processes.
- Eco-Friendly: Stainless steel is recyclable, making these rollers a more sustainable option for environmentally conscious operations.
Steel Roller Machines
The integration of mini steel rollers into machinery represents a significant advancement in industrial technology, enhancing efficiency and precision across various sectors.
Overview:
- Conveyor Systems: Their role in conveyor systems is critical, enabling the smooth transport of goods with minimal friction and wear, which is essential in logistics and distribution centers.
- Printing and Packaging Equipment: These rollers ensure the precise feeding of materials and alignment necessary for high-quality printing and packaging, where even minor deviations can lead to significant quality issues.
- Textile Machinery: In textile production, the rollers’ precision and smooth operation facilitate the handling of delicate fabrics, preventing damage and ensuring high-quality output.
- Automated Assembly Lines: They play a crucial role in the automation of assembly lines, where precision and reliability speed up production and reduce errors.
- Material Handling: Beyond conveyors, these rollers are used in various material handling equipment, enhancing efficiency and safety in moving heavy loads.
- Specialized Industrial Applications: From aerospace component manufacturing to electronic assembly, these rollers adapt to the specific needs of highly specialized industries, proving their versatility and indispensability.
Coated Mini Steel Roller
Coated mini steel rollers are designed with a protective layer to enhance their functionality and durability in specific environments. This coating, which can be made from materials such as rubber, polyurethane, or Teflon, adds a layer of protection against abrasion, chemicals, and impact, making these rollers versatile in their application.
Features and Benefits:
- Abrasion Resistance: The coating provides a protective barrier, reducing wear and tear from abrasive materials, thus extending the roller’s lifespan.
- Chemical Resistance: Certain coatings offer resistance to chemicals, making these rollers suitable for use in chemical processing plants or environments where chemical exposure is common.
- Noise Reduction: The soft nature of some coatings, like rubber, can significantly reduce operational noise, contributing to a more pleasant working environment.
- Improved Traction: Coatings can offer better material grip, preventing slippage and improving the accuracy of material handling.
- Customizability: The type of coating can be tailored to meet the specific needs of the application, whether it’s for temperature resistance, non-marking properties, or electrical conductivity.
- Impact Protection: Coated rollers can absorb shocks and impacts better than uncoated ones, protecting both the roller and the materials being handled.
High-Temperature Mini Steel Roller
High-temperature mini steel rollers are specifically engineered to operate in environments where temperatures can compromise the integrity and performance of standard rollers. These rollers are constructed from materials that can withstand extreme heat, such as high-grade stainless steel or alloys designed for high-temperature applications.
Features and Benefits:
- Heat Resistance: Capable of operating in environments with temperatures that would degrade standard rollers, maintaining integrity and performance.
- Durability in Extreme Conditions: Designed to resist warping, melting, or other forms of degradation that can occur at high temperatures.
- Low Thermal Expansion: Materials used in these rollers have low thermal expansion rates, ensuring dimensional stability even in fluctuating temperatures.
- Resistance to Thermal Shock: Able to withstand rapid temperature changes without cracking or failing, essential for processes involving sudden heating or cooling.
- Minimal Maintenance: The robust nature of these rollers in high-temperature environments reduces the need for frequent maintenance or replacement.
- Application Specificity: Ideal for use in industries such as metal processing, glass manufacturing, and baking, where high temperatures are a regular aspect of the manufacturing process.
By understanding the nuanced differences and specific advantages of each type of mini steel roller, industries can make informed decisions, ensuring that their machinery and processes are optimized for the highest levels of efficiency and productivity.
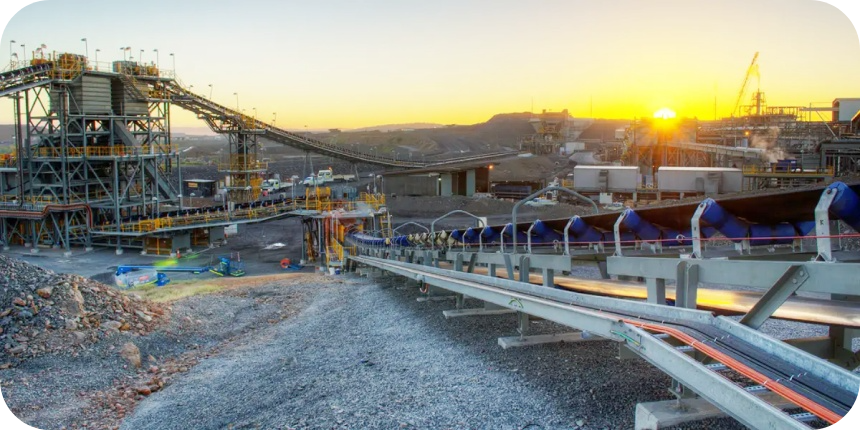
Applications of Mini Steel Roller
The mini steel roller, a cornerstone of modern industrial design, embodies versatility and efficiency. Its compact size belies its strength and durability, making it an indispensable component in a myriad of applications. From the intricate workings of high-tech machinery to the robust demands of heavy industry, mini steel rollers facilitate smooth operations, enhance productivity, and ensure precision across various sectors. Below, we delve into six key applications, highlighting their integral roles and the unique benefits they bring to each field.
Industrial Applications
Mini steel rollers are pivotal in the industrial sector, where their robustness and precision drive the efficiency of numerous systems.
- Conveyor Systems: They are the backbone of conveyor systems, ensuring the seamless transport of goods.
- Assembly Lines: These rollers streamline operations in assembly lines, enhancing productivity and precision.
- Packaging Machinery: In packaging machinery, they contribute to the accurate and efficient packaging of products.
- Sorting Systems: Utilized in sorting systems, they enable the rapid and accurate sorting of items.
- Material Handling: They are crucial in material handling equipment, offering durability and reliability.
- Load Distribution: Mini steel rollers ensure even load distribution, protecting both the machinery and the products.
Steel Roller Wheels and Bearings
In wheels and bearings, mini steel rollers are essential for mobility and efficiency, supporting loads and reducing friction.
- Enhanced Mobility: They facilitate smooth movement in various applications, from vehicles to machinery.
- Load Support: These rollers are designed to support significant loads, ensuring stability and durability.
- Precision Movement: Their use in precision applications highlights their importance in ensuring accurate operations.
- Durability: Mini steel rollers are known for their durability, even under constant use.
- Reduced Friction: They play a key role in minimizing friction, leading to smoother operations and energy savings.
- Versatile Use: Their versatility is evident in their use across a wide range of equipment and furniture.
Steel Roller Scale
In measurement and scale systems, the precision and reliability of mini steel roller are paramount, ensuring accurate operations.
- Measurement Accuracy: They are integral to maintaining measurement accuracy in precision instruments.
- Smooth Operation: The smooth operation of these rollers is crucial for the calibration of devices.
- Reliability: Their reliability is essential in applications where precision cannot be compromised.
- Minimal Maintenance: These rollers require minimal maintenance, ensuring consistent performance.
- Customizable: They can be tailored to meet specific requirements of measurement devices.
- High Precision: Mini steel rollers enable high-precision operations, critical in many industrial applications.
Robotics and Automation
In robotics and automation, mini steel roller stands out for their ability to facilitate controlled, precise movements in compact spaces.
- Robotic Movement: They are key to the smooth and controlled movement in robotic systems.
- Load Handling: Designed to handle dynamic loads typical in automated processes.
- Compact Design: Their compact design is ideal for the confined spaces in robotics.
- High Performance: Mini steel rollers deliver the high performance required for efficient automation.
- Durability in Repetitive Use: They withstand repetitive movements, a common requirement in robotics.
- Customization for Specific Tasks: Their adaptability allows for customization to specific automated tasks.
Aerospace and Aviation
In the aerospace and aviation industries, mini steel rollers are valued for their precision engineering and load-bearing capacity, essential for the assembly and maintenance of aircraft.
- Aircraft Assembly: They play a crucial role in the precise assembly of aircraft components.
- Maintenance Platforms: Integral to the construction of stable and precise maintenance platforms.
- Load-Bearing Capacity: Their ability to handle heavy components is vital in aerospace manufacturing.
- High-Quality Standards: Mini steel roller meets the stringent quality standards of the aerospace industry.
- Resistance to Environmental Factors: They offer resistance to temperature fluctuations and corrosion.
- Precision Engineering: Essential for the safe and efficient operation of aviation equipment.
Medical Equipment
In the medical sector, the smooth operation, durability, and hygiene offered by mini steel roller enhance the functionality and safety of medical devices and equipment.
- Hospital Beds: They ensure the smooth operation of hospital beds, improving patient comfort.
- Surgical Instruments: Key to the mobility of surgical instruments, enhancing operational efficiency.
- Imaging Equipment: Critical for the precise operation of imaging equipment, aiding in accurate diagnostics.
- Laboratory Devices: Utilized in laboratory devices for the precise handling of sensitive materials.
- Patient Handling Equipment: They improve the safety and ease of use of patient handling equipment.
- Durability and Hygiene: Their durability and ease of cleaning are crucial in medical environments.
Through these applications, the mini steel roller demonstrates its critical role in advancing technology, enhancing efficiency, and ensuring precision across a wide range of industries.
How to Choose the Right Mini Steel Roller
Selecting the appropriate mini steel roller for your application is a critical decision that impacts the efficiency, longevity, and overall performance of your machinery. With the vast array of options available, understanding the specific requirements of your application and how different factors influence the suitability of a mini steel roller is essential. This section outlines the key considerations and underscores the importance of load capacity, material, and surface treatment in determining the optimal roller for your needs.
Fill Out the Form for mini steel Conveyor Roller Customization Options.
Factors to Consider When Selecting a Mini Steel Roller
The selection process involves several critical considerations, each playing a pivotal role in ensuring the chosen mini steel roller meets the demands of your application:
- Load Capacity: The foremost consideration is the roller’s ability to support the weight and stress of your operation without compromising performance or integrity.
- Material: Different materials offer varying degrees of strength, durability, and resistance to environmental factors, making the choice of material a significant determinant of the roller’s applicability and lifespan.
- Surface Treatment: Surface treatments can enhance a roller’s resistance to wear, corrosion, and other environmental challenges, extending its useful life and maintaining its efficiency.
- Operating Environment: Factors such as temperature, humidity, and exposure to chemicals or abrasive materials dictate the need for specific roller materials and treatments.
- Size and Dimensions: Proper sizing is crucial for compatibility with existing systems and for achieving desired performance levels.
- Bearing Type: The type of bearing affects the roller’s load capacity, speed capability, and maintenance requirements.
- Speed Requirements: High-speed applications may necessitate rollers designed to minimize friction and heat buildup.
- Customization Needs: Custom features may be necessary for unique applications, requiring a manufacturer that can accommodate specific design requests.
- Maintenance Requirements: A roller’s material and surface treatment can affect its maintenance needs. Durable materials and protective surface treatments can reduce the frequency and complexity of maintenance tasks.
- Operational Noise: Surface treatments can also impact the operational noise level. Smoother finishes can lead to quieter operation, which is beneficial in noise-sensitive environments.
- Cost-Effectiveness: While higher-quality materials and advanced surface treatments may increase initial costs, they can offer greater cost-effectiveness over time through reduced maintenance needs and longer operational life.
By carefully evaluating these factors, you can make an informed decision that ensures the selected mini steel roller not only meets but exceeds your application’s requirements. This strategic approach to selection is crucial for optimizing the performance of your machinery and extending its service life.
Maintenance and Care for Mini Steel Roller
Proper maintenance and care are crucial for maximizing the lifespan and ensuring the optimal performance of mini steel roller. Regular and appropriate upkeep not only extends the operational life of these components but also maintains their efficiency and reliability in various applications. Here, we provide comprehensive insights into maintaining mini steel rollers, including tips and practices for cleaning and lubrication.
Tips on Maintaining Mini Steel Rollers
- Regular Inspections: Conduct periodic inspections to identify wear, damage, or any signs of fatigue. Early detection of issues can prevent costly repairs or replacements.
- Proper Alignment: Ensure that mini steel rollers are correctly aligned in their tracks or frames to prevent uneven wear and tear.
- Avoid Overloading: Adhere to the specified load capacities to prevent deformation or failure of the rollers.
- Environmental Protection: Protect rollers from harsh environmental conditions by implementing shields or covers if they are exposed to corrosive substances, extreme temperatures, or abrasive materials.
- Timely Replacement of Worn Parts: Replace any worn or damaged parts promptly to maintain the integrity and performance of the roller system.
- Use of Compatible Parts: When replacements are necessary, use parts that are compatible with the original specifications to ensure proper fit and function.
- Keep Tracks Clean: Regularly clean the tracks or surfaces on which mini steel rollers operate to prevent debris accumulation that can cause damage or hinder movement.
- Scheduled Maintenance: Establish a routine maintenance schedule based on the manufacturer’s recommendations and operational demands.
Cleaning and Lubrication Practices for Different Types of Mini Steel Rollers
Maintaining mini steel rollers involves regular cleaning and appropriate lubrication to ensure their longevity and optimal performance. Different types of rollers may require specific maintenance practices based on their material, application, and environmental exposure.
- Routine Cleaning: Regularly remove dirt, dust, and debris from the roller surface using a soft brush or cloth to prevent buildup that can impair functionality.
- Lubrication: Apply appropriate lubricants to bearings and moving parts to reduce friction and wear. The type of lubricant may vary based on the roller material and operational environment.
- Use of Specific Cleaners: For rollers used in sensitive environments, such as food processing or pharmaceuticals, use cleaners that are safe and approved for such settings.
- Lubrication Frequency: The frequency of lubrication should be based on the manufacturer’s guidelines and the intensity of the roller’s use. High-demand applications may require more frequent lubrication.
- Corrosion Prevention: For mini steel rollers exposed to moisture or corrosive substances, apply corrosion inhibitors or use stainless steel rollers with inherent corrosion resistance.
- Cleaning Agents: Avoid using harsh chemicals or abrasive tools for cleaning, as these can damage the roller surface or protective coatings.
- Special Considerations for Coated Rollers: For rollers with surface treatments or coatings, ensure that cleaning and lubrication practices do not degrade the coating. Use compatible products that preserve the integrity of the surface treatment.
By adhering to these maintenance and care tips, you can ensure that your mini steel rollers continue to operate efficiently and effectively, contributing to the smooth operation of your machinery and systems. Regular upkeep not only extends the service life of these components but also helps maintain their performance at optimal levels.
Where to Buy Mini Steel Roller
In the quest for high-quality mini steel rollers, selecting the right supplier or manufacturer is as crucial as the components themselves. The ideal supplier not only offers a product that meets or exceeds your specifications but also enhances your purchasing experience through exceptional service and support. This section provides a structured approach to identifying reputable suppliers and underscores the importance of quality, customer service, and after-sales support in making an informed choice.
Guidance on Finding Reliable Suppliers and Manufacturers of Mini Steel Rollers
Identifying a trustworthy supplier for mini steel roller involves several key considerations. These steps are designed to ensure that you partner with a supplier capable of meeting your needs effectively and efficiently.
- Research and Reputation: Start with thorough research. Look for suppliers with a solid reputation in the market, evidenced by positive reviews and testimonials from satisfied customers.
- Comprehensive Product Catalog: A wide product range indicates the supplier’s capability to cater to diverse needs, making it easier to find rollers that match your specific requirements.
- Customization Services: Suppliers offering customization options can be invaluable, especially if your application demands unique specifications not met by standard products.
- Technical and Customer Support: Evaluate the level of technical and customer support provided. Reliable suppliers are ready to assist with product selection, installation guidance, and troubleshooting.
- Quality Certifications: Certifications such as ISO standards serve as a benchmark for quality and reliability, indicating the supplier’s adherence to industry best practices.
- Efficient Fulfillment: Assess the supplier’s ability to deliver orders within acceptable lead times. Prompt service is essential to avoid operational delays.
- Global Operations: A supplier with a global footprint can offer more flexible logistics and support, especially if you operate in multiple markets.
Key Considerations in Supplier Selection
When selecting a supplier for mini steel roller, the emphasis on quality, customer service, and after-sales support cannot be overstated. These elements are fundamental to a satisfactory purchasing experience and the long-term success of your operations. Beyond ensuring product reliability and operational efficiency, they foster a supportive relationship between you and your supplier.
- Quality Products: The cornerstone of any supplier relationship is the quality of the products provided. High-quality mini steel rollers ensure durability, reliability, and consistent performance, which are crucial for maintaining operational efficiency and minimizing downtime.
- Exceptional Customer Service: Outstanding customer service is indicative of a supplier’s commitment to their clients. It ensures that any inquiries, concerns, or issues are addressed promptly and effectively, facilitating a smooth and hassle-free purchasing process.
- Robust After-Sales Support: Effective after-sales support, including accessible warranties, maintenance advice, and readily available replacement parts, underscores the supplier’s confidence in their products and their commitment to customer satisfaction. It’s essential for the long-term reliability and performance of your mini steel roller.
- Partnership Approach: A supplier that prioritizes quality and service acts as a partner in your success, offering added value that can significantly enhance your operations. This relationship is built on trust and mutual respect, leading to better outcomes for your projects.
- Investment in Innovation: Suppliers who emphasize quality and customer service are often at the forefront of industry innovation. Their commitment to excellence means they are continuously improving their products and services, which can provide you with access to the latest technologies and solutions.
- Risk Mitigation: Engaging with suppliers who offer reliable after-sales support and value customer service helps mitigate operational risks. Knowing that you can count on prompt assistance and support in case of issues provides peace of mind and operational stability.
Selecting the right supplier for mini steel roller is about more than just the product itself; it’s about forming a partnership that will contribute to the success of your operations. By prioritizing quality, customer service, and after-sales support, you can ensure that this partnership will be beneficial both now and in the future..
Last Updated on July 24, 2024 by Jordan Smith
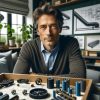
Jordan Smith, a seasoned professional with over 20 years of experience in the conveyor system industry. Jordan’s expertise lies in providing comprehensive solutions for conveyor rollers, belts, and accessories, catering to a wide range of industrial needs. From initial design and configuration to installation and meticulous troubleshooting, Jordan is adept at handling all aspects of conveyor system management. Whether you’re looking to upgrade your production line with efficient conveyor belts, require custom conveyor rollers for specific operations, or need expert advice on selecting the right conveyor accessories for your facility, Jordan is your reliable consultant. For any inquiries or assistance with conveyor system optimization, Jordan is available to share his wealth of knowledge and experience. Feel free to reach out at any time for professional guidance on all matters related to conveyor rollers, belts, and accessories.