Tech Guide: Mining Conveyor Belt Metal Detector Features
Mining operations are complex environments where safety and efficiency are paramount. The introduction of a mining conveyor belt metal detector has significantly enhanced these aspects by providing a reliable means of detecting harmful metals embedded in the conveyed material. These sophisticated devices are crucial in identifying and removing metallic contaminants that could otherwise cause damage to processing equipment, leading to costly downtime and potential hazards. By ensuring that only clean material progresses through the production line, these metal detectors play a pivotal role in maintaining the integrity of mining operations, safeguarding equipment, and protecting the workforce. Their ability to detect both ferrous and non-ferrous metals makes them an indispensable tool in the mining industry, optimizing the extraction and processing phases for better productivity and safety.
The Importance of Mining Conveyor Belt Metal Detectors
Mining conveyor belt metal detectors are indispensable tools in the mining industry, serving multiple crucial roles that significantly contribute to the protection of machinery and the reduction of operational downtime. These devices are not only pivotal in ensuring the purity and quality of the mined materials but also play a vital part in safeguarding the mechanical components of the mining infrastructure. Below, we delve into eight critical roles played by these metal detectors and explore six common metals detected along with the potential risks they pose to the mining operations.
Critical Roles of Mining Conveyor Belt Metal Detectors
- Prevention of Equipment Damage: Metal detectors identify and remove metallic contaminants that can cause significant damage to crushers, grinders, and other processing equipment. By detecting these metals early, the detectors prevent costly repairs and replacements.
- Ensuring Product Quality: By removing metal contaminants, these detectors ensure that the final product meets quality standards, which is crucial for customer satisfaction and regulatory compliance.
- Avoiding Downtime: Detecting metal contaminants early helps in avoiding unexpected machinery breakdowns, which can lead to extensive downtime and lost production.
- Safety Enhancement: Metal detectors reduce the risk of sparks or explosions that can occur if metal pieces come into contact with machinery, thereby enhancing workplace safety.
- Cost Reduction: By preventing equipment damage and downtime, mining conveyor belt metal detectors help in significantly reducing operational costs.
- Improving Efficiency: These detectors allow for a smoother operation flow by minimizing disruptions caused by metal contamination, thus improving overall efficiency.
- Enhancing Mining Processes: The use of these detectors can help in refining the mining process by providing data on the type and amount of metal contaminants found, which can be used for process optimization.
- Regulatory Compliance: In some cases, the removal of metal contaminants is a regulatory requirement, and metal detectors ensure compliance with these regulations.
Common Metals Detected and Their Risks
- Iron: The most common contaminant, which can cause severe damage to processing equipment and degrade the quality of the mined product.
- Copper: Often found in electrical components and machinery. Copper can cause equipment malfunctions and represents a significant financial loss if not detected.
- Aluminum: Lightweight and common in mining operations, aluminum can cause processing issues and machinery damage.
- Stainless Steel: Particularly challenging to detect due to its non-magnetic properties, stainless steel poses a risk of damage to crushing and milling equipment.
- Gold: While valuable, unintended gold pieces can lead to inaccuracies in processing and valuation if not properly accounted for.
- Lead: Its heavy weight and softness can lead to machinery damage, and due to health risks, it is crucial to detect and manage lead contamination.
Mining conveyor belt metal detectors are essential for the successful operation of mining ventures, providing a multitude of benefits that protect equipment, ensure product quality, enhance safety, and ultimately save costs. Their ability to detect a wide range of metals and mitigate the associated risks underscores their importance in the mining industry.
What is the Operation of Mining Conveyor Belt Metal Detectors
Mining conveyor belt metal detectors play a crucial role in the mining industry, ensuring the safety and efficiency of the processing line by detecting and removing metallic contaminants from the materials being transported. This guide delves into the operational mechanism and adaptability of these sophisticated devices, highlighting how they maintain the integrity of the product and the machinery.
Operational Mechanism
At the heart of a mining conveyor belt metal detector is its ability to detect metal contaminants through the generation and monitoring of a magnetic field. The detector creates a continuous magnetic field across the conveyor belt. When a piece of metal passes through this magnetic field, it causes a disturbance or fluctuation. This fluctuation is detected by the system’s sensitive electronic sensors.
The process begins with a transmitter coil generating a high-frequency magnetic field. As the conveyor belt moves, materials pass through this magnetic field. Non-metallic materials do not affect the field, but metallic objects induce a secondary magnetic field, distinct from the one generated by the transmitter. The detector’s receiver coils are finely tuned to pick up these secondary magnetic fields, triggering the detection process. Upon detection, the system can signal an alarm, stop the conveyor belt, or activate a mechanism to remove the metallic contaminant.
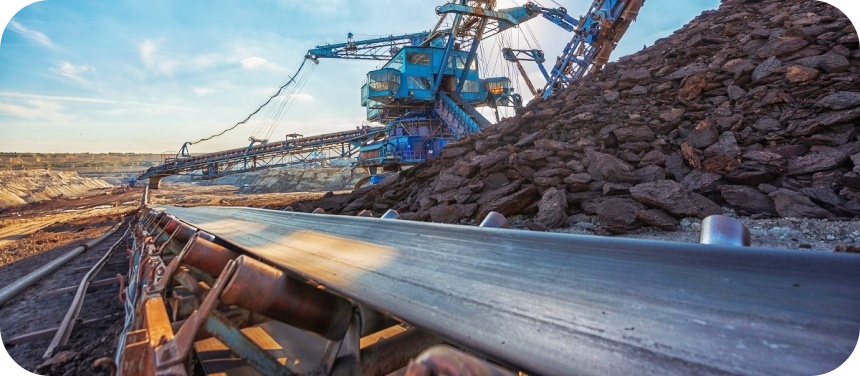
Adaptability to Mining Environments and Materials
Mining conveyor belt metal detectors are designed with adaptability in mind, capable of functioning in the diverse and challenging environments characteristic of the mining industry. These detectors can adjust their sensitivity and detection algorithms based on the type of material being transported, be it coal, minerals, or precious metals. This flexibility is crucial for minimizing false positives, which can occur due to the mineral content in the ore itself.
Moreover, these detectors are built to withstand the harsh conditions of mining operations, including dust, moisture, and extreme temperatures. Their design often includes rugged construction and materials suited for these environments. Additionally, the technology behind mining conveyor belt metal detectors is continuously evolving, incorporating advancements such as digital signal processing and artificial intelligence to enhance their detection capabilities and reliability. This ensures that they can effectively identify a wide range of metal contaminants, from large pieces of scrap metal to fine particles that might otherwise go undetected.
Mining conveyor belt metal detectors are indispensable tools in the mining industry, offering a blend of sensitivity, adaptability, and durability. By detecting metallic contaminants with high precision and adapting to various materials and environmental conditions, they help protect machinery, ensure product quality, and maintain operational efficiency.
Types of Mining Conveyor Belt Metal Detectors and Their Applications
Mining conveyor belt metal detectors are essential tools in the mining industry, designed to enhance safety, efficiency, and the overall productivity of mining operations. These detectors come in various models, each with specific applications and features that make them suitable for different mining environments. This section provides insights into four distinct models, including the well-regarded Eriez 1200 Series and GTEK GJT series, and delves into eight key features that are critical when selecting a mining conveyor belt metal detector.
Various Models and Their Applications
Key Features to Consider
- Sensitivity: The ability to detect varying sizes and types of metal, including both ferrous and non-ferrous materials. High sensitivity ensures that even the smallest contaminants are identified.
- Customization: Detectors that offer customizable settings and features allow for tailored solutions to meet specific operational needs, enhancing their effectiveness in different mining applications.
- Integration Capabilities: The ease with which a detector can be integrated into existing conveyor systems and workflows is crucial for maintaining operational efficiency and minimizing installation time.
- Durability: Given the harsh conditions often found in mining environments, detectors must be built to withstand dust, moisture, vibration, and temperature extremes.
- User-Friendliness: Devices should have intuitive controls and interfaces to ensure they can be easily operated and adjusted by personnel, reducing training requirements and enhancing usability.
- Detection of Various Metal Types: The ability to detect a wide range of metal types, including both ferrous and non-ferrous metals, is essential for comprehensive protection.
- Adjustable Sensitivity: The feature to adjust sensitivity based on the specific requirements of the mining operation or the nature of the materials being processed can greatly reduce false positives and improve detection accuracy.
- Maintenance and Support: Easy maintenance and accessible support from manufacturers ensure that any issues can be quickly resolved, reducing downtime and maintaining high levels of operational efficiency.
When selecting a mining conveyor belt metal detector, it’s important to consider a range of models and evaluate them based on key features such as sensitivity, customization options, and integration capabilities. By carefully assessing these aspects, mining operations can choose a detector that not only meets their specific needs but also enhances safety, efficiency, and productivity. Manufacturers like Eriez and GTEK offer a variety of models, such as the Eriez 1200 Series and GTEK GJT Series, that cater to the diverse requirements of the mining industry, ensuring there is a suitable option for every application.
Choosing the Best Mining Conveyor Belt Metal Detector for Mining Applications
Selecting the most appropriate mining conveyor belt metal detector is pivotal for ensuring operational efficiency, safety, and compliance with industry standards in mining applications. With numerous models available from reputable manufacturers like Eriez and GTEK, it’s essential to consider several factors to find the detector that best suits your specific needs. Here, we outline ten critical factors to guide your selection process and briefly mention the significance of choosing reputable manufacturers.
Factors to Consider
- Sensitivity: The detector’s ability to identify various types of metal contaminants, including both ferrous and non-ferrous metals. High sensitivity is crucial for detecting small or finely dispersed metal particles.
- Size and Type of Metal to be Detected: Consider the size and type of metal contaminants common in your operation. This determines the required sensitivity and detection capabilities.
- Conveyor Belt Size: The size and configuration of your conveyor system affect the size and type of metal detector needed. Ensure the detector is compatible with your conveyor belt’s width and speed.
- Material Characteristics: The nature of the material being processed (e.g., mineral content, moisture level) can affect the detector’s performance. Select a detector capable of handling the specific characteristics of your materials.
- Customization Options: Look for detectors that offer customization options, allowing you to tailor the device’s settings and features to your specific needs.
- Integration Capabilities: The ability to integrate the metal detector with existing mining and material handling infrastructure is crucial for seamless operation.
- Environmental Conditions: The mining environment (e.g., dust, moisture, temperature) can impact the detector’s functionality. Choose a detector designed to withstand the conditions of your operation.
- Reliability and Durability: Opt for a detector known for its reliability and durability, ensuring it can withstand the rigors of mining operations without frequent breakdowns.
- Ease of Installation and Maintenance: Consider how easy it is to install and maintain the detector. Minimal downtime for installation and maintenance is essential to maintain operational efficiency.
- Cost: While cost should not be the sole factor in your decision, consider the total cost of ownership, including purchase price, installation, maintenance, and potential downtime.
Reputable Manufacturers: Eriez and GTEK
When selecting a mining conveyor belt metal detector, choosing a model from a reputable manufacturer is vital. Both Eriez and GTEK are renowned for their range of products designed specifically for mining applications. These manufacturers offer detectors that excel in sensitivity, durability, and integration capabilities, ensuring that you can find a model that meets the unique demands of your mining operation.
Eriez and GTEK provide comprehensive support and customization options, allowing you to optimize the detector for your specific application. Their commitment to quality and innovation means you can rely on their products to enhance safety, efficiency, and compliance in your mining operations.
Choosing the best mining conveyor belt metal detector involves careful consideration of various factors, including sensitivity, conveyor belt size, material characteristics, and environmental conditions. By focusing on these key aspects and opting for detectors from reputable manufacturers like Eriez and GTEK, you can ensure the safety, efficiency, and productivity of your mining operations.
Installation and Calibration of Mining Conveyor Belt Metal Detectors for Optimal Performance
The installation and calibration of mining conveyor belt metal detectors are critical processes that directly impact their effectiveness and reliability. Proper installation ensures that the detector is perfectly aligned with the conveyor system, while accurate calibration allows it to identify metallic contaminants with high precision. Below we explore the importance of these processes and offer practical tips for integrating metal detectors with existing conveyor systems.
Importance of Proper Installation and Calibration
- Maximizes Sensitivity: Correct installation and calibration ensure the detector operates at its highest sensitivity, enabling it to detect the smallest metal contaminants.
- Prevents False Alarms: Accurate calibration reduces the likelihood of false alarms, which can cause unnecessary downtime and disrupt mining operations.
- Ensures Reliability: Properly installed and calibrated detectors deliver consistent performance, reducing the need for frequent adjustments and maintenance.
- Improves Efficiency: By detecting and removing metallic contaminants efficiently, these detectors help maintain the flow of materials on the conveyor belt, thereby improving overall operational efficiency.
- Protects Equipment: Detecting and removing metal contaminants before they can cause damage to downstream equipment saves on repair costs and extends equipment life.
- Enhances Safety: By preventing metal contaminants from reaching processing equipment, these detectors help to minimize the risk of equipment failure and potential safety hazards.
- Ensures Compliance: Many mining operations are subject to regulatory standards that require the detection and removal of metal contaminants, making proper installation and calibration essential for compliance.
- Optimizes Performance: Regular calibration ensures the detector continues to perform optimally over time, even as conditions on the mining site change.
Tips for Integrating Metal Detectors with Existing Conveyor Systems
- Consult with Experts: Engage with the metal detector manufacturer or a professional installer for guidance on the best practices for installation and integration.
- Consider Conveyor Design: Ensure the metal detector is compatible with the design and dimensions of your existing conveyor system.
- Plan for Adequate Space: Make sure there is enough space around the conveyor for the installation and for future maintenance activities.
- Ensure Proper Alignment: The detector should be perfectly aligned with the conveyor belt to avoid false readings and ensure accurate detection.
- Follow Manufacturer’s Instructions: Adhere strictly to the manufacturer’s installation and calibration instructions to ensure optimal performance.
- Test with Different Materials: During calibration, test the detector with various materials and metal contaminants to ensure it is accurately tuned for your specific application.
- Train Operators: Ensure that operators are trained on how to use and maintain the detector, including how to perform routine calibrations.
- Schedule Regular Maintenance: Establish a regular maintenance schedule to check the detector’s performance and recalibrate as necessary, ensuring consistent operation.
By emphasizing the importance of proper installation and calibration and following these integration tips, mining operations can significantly enhance the performance and reliability of their mining conveyor belt metal detectors. This not only improves the efficiency and safety of mining operations but also ensures compliance with industry regulations and standards.
Maintenance and Troubleshooting of Mining Conveyor Belt Metal Detectors
To ensure the longevity and reliability of mining conveyor belt metal detectors, regular maintenance and prompt troubleshooting are essential. Proper care not only extends the lifespan of these devices but also ensures they operate at optimal efficiency, safeguarding your mining operations against potential downtime and equipment damage. Here, we provide nine basic maintenance tips and outline six common issues along with troubleshooting steps, with references to resources like the Eriez 1230 Metal Detector Manual for specific guidance.
Basic Maintenance Tips
- Regular Inspections: Conduct routine inspections to check for wear and tear, especially on components most exposed to the harsh mining environment.
- Cleanliness: Keep the detector and its surroundings clean. Dust and debris can affect the sensitivity and functionality of the device.
- Calibration Checks: Perform regular calibration checks to ensure the detector operates at its optimal sensitivity and accuracy.
- Software Updates: If your detector uses software, ensure it is always updated to the latest version to benefit from improved features and bug fixes.
- Connection Integrity: Regularly check all electrical connections and wiring for signs of damage or corrosion and repair or replace as necessary.
- Component Replacement: Replace worn-out or damaged parts immediately to prevent further damage and ensure continuous operation.
- Professional Audits: Schedule annual audits by professional service technicians to ensure your system is functioning correctly and to conduct any necessary repairs.
- Operator Training: Ensure operators are well-trained in both the operation and basic maintenance procedures to identify and resolve minor issues quickly.
- Documentation: Keep a detailed log of all maintenance activities, inspections, and repairs for future reference and compliance purposes.
Common Issues and Troubleshooting Steps
- False Alarms: If the detector is signaling metal when none is present, recalibrate the sensitivity settings, and ensure the conveyor is not introducing electrical noise or vibrations.
- Inconsistent Detection: Check for environmental factors that could affect detection, like temperature changes or nearby equipment. Adjust the phase setting as necessary.
- System Not Powering Up: Ensure power supply is correctly connected and circuit breakers are intact. Check for blown fuses or tripped circuits.
- Weak Detection Signal: Inspect the coils for damage and ensure they are properly connected. Test the detector with samples of metal to determine if sensitivity needs adjustment.
- Unresponsive Controls: If digital controls are unresponsive, reset the system, and check for any needed software updates. If physical controls are unresponsive, inspect for mechanical damage or electrical issues.
Following these maintenance tips and troubleshooting steps can significantly reduce downtime and improve the performance and reliability of your mining conveyor belt metal detectors. For specific issues or more complex problems, consulting the manufacturer’s manuals, such as the Eriez 1230 Metal Detector Manual, or contacting professional service technicians is recommended to ensure your equipment continues to operate efficiently and effectively.
Cost Considerations for Mining Conveyor Belt Metal Detectors
When investing in mining conveyor belt metal detectors, understanding the associated costs is crucial for budgeting and ensuring you receive value for your investment. The price range of these detectors can vary significantly based on several factors, including sensitivity, customization options, brand reputation, and additional features. Here, we discuss the factors that influence the cost of metal detectors and provide advice on balancing budget constraints with the need for quality and reliability.
Factors Influencing Cost
- Sensitivity and Detection Capabilities: High-sensitivity detectors capable of identifying both ferrous and non-ferrous metals, including small or finely dispersed particles, tend to be more expensive.
- Customization Options: Detectors that offer customizable features, such as adjustable sensitivity, frequencies, and rejection systems, may cost more due to their flexibility and advanced technology.
- Brand and Manufacturer Reputation: Well-known brands with a proven track record of reliability and excellent after-sales service often price their equipment higher to reflect their market position and product quality.
- Integration and Installation Requirements: The complexity of integrating the detector with existing conveyor systems can influence the cost, especially if custom modifications or additional components are necessary.
- Environmental and Operational Durability: Detectors designed to withstand harsh mining environments, including dust, moisture, and extreme temperatures, may incorporate more durable materials and advanced engineering, impacting the price.
- Additional Features: Features such as wireless connectivity, data logging, and advanced diagnostics can add to the cost of metal detectors but offer greater control and insight into the detection process.
- Maintenance and Support Services: Ongoing maintenance and support services, including software updates and professional audits, can also factor into the overall cost of ownership.
- Regulatory Compliance: Detectors that meet specific industry standards or regulatory requirements might come at a premium due to the additional testing and certification involved.
Balancing Budget Constraints with Quality and Reliability Needs
- Assess Your Specific Needs: Identify the key features and capabilities essential for your operation to avoid paying for unnecessary extras.
- Consider Total Cost of Ownership: Factor in not just the purchase price, but also installation costs, maintenance expenses, and potential savings from reduced downtime and equipment damage.
- Evaluate Return on Investment: High-quality detectors may have a higher upfront cost but can offer significant long-term savings by preventing costly breakdowns and ensuring continuous operation.
- Research and Compare: Take the time to research different models and brands, comparing their features, reliability reviews, and prices to find the best value for your needs.
- Seek Professional Advice: Consulting with industry experts or the detector manufacturers can provide insights into the most cost-effective solutions for your specific circumstances.
- Negotiate Package Deals: If purchasing multiple units or requiring additional services, negotiate package deals with suppliers for better pricing.
- Explore Financing Options: Some manufacturers or suppliers may offer financing options that can help spread the cost over time, making it easier to manage budget constraints.
- Plan for the Future: Invest in a metal detector that can adapt to future needs, possibly through upgrades or modular components, to avoid the need for a complete replacement as your operation evolves.
By carefully considering these cost factors and balancing them with the need for a reliable and effective mining conveyor belt metal detector, mining operations can make informed decisions that ensure operational efficiency, safety, and regulatory compliance, while also managing budgetary constraints.
Where to Buy Mining Conveyor Belt Metal Detectors
Purchasing a mining conveyor belt metal detector is a significant investment, and finding the right supplier is crucial to ensure you get a reliable product that meets your operational needs. Whether you’re looking for new or used options, there are several avenues to explore. Here, we provide six suggestions for finding these detectors for sale and ten tips on evaluating sellers and products to ensure you make a wise investment.
Suggestions for Finding Detectors
- Manufacturer Websites: Directly purchasing from manufacturers like Eriez or GTEK ensures you get genuine products with full warranties and support services.
- Industrial Supply Companies: Companies specializing in mining or industrial equipment often offer a range of metal detectors and can provide expert advice on choosing the right model.
- Online Marketplaces: Websites like Alibaba, eBay, and Amazon can be sources for new and used detectors, often at competitive prices.
- Trade Shows and Expos: Mining and industrial trade shows are great places to see the latest technology in action, compare different models, and negotiate deals directly with suppliers.
- Refurbished Equipment Suppliers: Some suppliers specialize in refurbished or used equipment, offering high-quality detectors at lower prices.
- Industry Forums and Networks: Recommendations from industry peers in forums or networks can lead you to reputable suppliers and alert you to available second-hand equipment.
Tips on Evaluating Sellers and Products
- Verify Seller Reputation: Look for reviews, testimonials, and feedback from previous customers to gauge the reliability and customer service of the seller.
- Assess Product Quality: Ensure the metal detector meets industry standards and comes with the necessary certifications for mining use.
- Inquire About Warranties: A comprehensive warranty can provide peace of mind and protect your investment against early failures or defects.
- Check for Support and Services: Reliable post-sale support, including training, maintenance, and repair services, is crucial for the long-term operation of the equipment.
- Compare Prices: While price shouldn’t be the only factor, comparing costs from various suppliers can help you find the best deal.
- Understand the Return Policy: Knowing the return policy is essential, especially if you’re purchasing without a prior in-person inspection.
- Inspect Used Equipment: If buying used, request detailed photos, operation history, and maintenance records to assess the condition of the equipment.
- Ask for Demonstrations: Whenever possible, see the metal detector in action to verify its performance and ease of use.
- Consider Compatibility: Make sure the detector can be easily integrated with your existing conveyor system and operations.
- Plan for Future Needs: Evaluate whether the detector can be upgraded or expanded to meet future operational requirements, ensuring longevity and adaptability.
By following these suggestions and tips, you can navigate the market for mining conveyor belt metal detectors more effectively, ensuring you find a quality product that suits your needs and budget. Whether you opt for a new or used detector, taking the time to research and evaluate your options will lead to a more informed and beneficial investment.
Need more information on our conveyor belts? Send us your inquiry.
FAQs about Mining Conveyor Belt Metal Detector
Metal detectors on conveyor belts are designed to identify and signal the presence of metal in materials being transported on the belt. The system typically consists of a metal detector loop that surrounds the conveyor belt. This loop generates an electromagnetic field. When a piece of metal passes through this field, it disturbs the field’s frequency. The metal detector’s control system, which continuously monitors the electromagnetic field, detects this disturbance.
A metal detector calibrated for a conveyor belt application can differentiate between the normal conditions of the belt’s operation and the presence of metal contaminants. Sophisticated electronics are used to cancel out the effect of the belt and only signal when metal is detected. This enables the system to alert operators or automatically reject the contaminated product from the line, ensuring that metal does not contaminate the final product or damage downstream equipment.
Most conveyor belts will not be detected by metal detectors if they are made from non-metallic materials, which is often the case in various industries, including mining. However, metal detectors are finely tuned to ignore the presence of the belt itself during operation, even if the belt has metal components like reinforcing steel strands, provided the metal detector is properly calibrated.
When installing a new conveyor belt or using a metal detector for the first time with an existing belt, the system may need recalibration to account for any metallic properties of the belt. This is to ensure that the belt does not trigger false positives, which can disrupt the mining process.
The majority of metal detectors are capable of detecting a wide range of metals, including both ferrous (iron-based) and non-ferrous metals. However, certain metals such as stainless steel, particularly those with a high grade and low magnetic permeability, can sometimes be difficult to detect. This is because these metals have poor electrical conductivity and do not create a strong interaction with the electromagnetic field generated by the metal detector.
Additionally, metals that are non-magnetic and highly conductive, such as gold, platinum, and certain alloys, may be harder to detect, especially in small quantities. Advanced metal detectors with high sensitivity and specific calibration can often detect these types of metals more effectively.
In mining, metal detectors are used primarily for two purposes: to protect machinery and to ensure the quality of the mined material. They detect and remove any metallic impurities that could potentially cause damage to crushers, grinders, and other equipment downstream. This helps to avoid costly repairs and downtime, maintaining operational efficiency.
Metal detectors in mining also play a crucial role in quality control by ensuring that the extracted materials are free of unwanted metallic contamination before being processed or shipped to customers. This is particularly important for commodities like coal, where metal contaminants can significantly reduce the quality of the product.
Mining conveyor belts can be purchased from specialized industrial suppliers that cater to the mining industry, manufacturers of bulk material handling equipment, and conveyor system suppliers. These belts are often available for purchase directly from the manufacturer’s websites, industrial supply catalogs, or through mining equipment distributors.
For specific needs or custom solutions, you may need to work directly with a company that specializes in the design and manufacturing of conveyor belts for mining applications. Companies such as Fenner Dunlop, ContiTech, and Bridgestone provide custom conveyor solutions and are well-regarded in the industry. Additionally, online marketplaces like Alibaba and trade shows focused on mining technology are excellent places to find a wide array of options and to make connections with suppliers and manufacturers.
Last Updated on August 1, 2024 by Jordan Smith
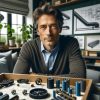
Jordan Smith, a seasoned professional with over 20 years of experience in the conveyor system industry. Jordan’s expertise lies in providing comprehensive solutions for conveyor rollers, belts, and accessories, catering to a wide range of industrial needs. From initial design and configuration to installation and meticulous troubleshooting, Jordan is adept at handling all aspects of conveyor system management. Whether you’re looking to upgrade your production line with efficient conveyor belts, require custom conveyor rollers for specific operations, or need expert advice on selecting the right conveyor accessories for your facility, Jordan is your reliable consultant. For any inquiries or assistance with conveyor system optimization, Jordan is available to share his wealth of knowledge and experience. Feel free to reach out at any time for professional guidance on all matters related to conveyor rollers, belts, and accessories.