Critical Considerations In Mining Conveyor Design
In the heart of the mining industry, conveyor systems stand as the lifeline, facilitating the seamless flow of raw minerals from the depths of mines to the surface. The critical role of these systems cannot be overstated, as they significantly enhance operational efficiency, safety, and productivity. This underscores the paramount importance of mining conveyor design, a complex process that demands a meticulous approach to ensure the conveyance mechanisms are not only efficient but also safe and reliable. As the global demand for raw minerals escalates, driven by advancements in technology and the growing needs of various industries, the pressure on mining operations to deliver is immense. In this context, mining conveyor design emerges as a fundamental aspect, bridging the gap between demand and supply. It is through well-thought-out conveyor designs that the mining industry can meet the increasing demand for raw minerals, ensuring that operations are both sustainable and profitable. The essence of mining conveyor design lies in its ability to optimize the extraction and transportation processes, making it a cornerstone of modern mining operations.
What is Mining Conveyor Systems in Mining Conveyor Design
The foundation of effective mining operations lies in the intricate mining conveyor design, which facilitates the movement of materials across various segments of a mining site. This section delves into the core conveyor systems utilized in mining, highlighting their diversity and specialized applications.
Belt Conveyors in Mining Conveyor Design
Belt conveyors are pivotal in mining conveyor design, offering versatility for transporting a wide array of materials.
Incline Belt Conveyors: Designed to move materials uphill, overcoming elevation challenges in mines.
Decline Belt Conveyors: Utilized for transporting materials downhill from higher points within a mine.
Curved Belt Conveyors System: Engineered to navigate curves and corners, optimizing the layout of mining operations.
Long-distance Belt Conveyors: Facilitate the transport of materials over vast distances, connecting different parts of mining operations.
Pipe Conveyors: Enclose materials in a pipe-like belt, minimizing spillage and environmental impact.
Slider Bed Conveyors: Employ a smooth surface under the belt, reducing friction and wear, ideal for fine or small materials.
Roller Conveyors in Mining Conveyor Design
Roller conveyors are integral to mining conveyor design, supporting materials as they move along the system:
- Gravity Roller Conveyors: Use gravity to move materials, ideal for downward or level transportation.
- Powered Roller Conveyors: Incorporate motors to move materials, suitable for heavy loads and uphill transport.
- Flexible Roller Conveyors: Offer adjustable paths, accommodating varying layouts and spaces.
- Accumulating Roller Conveyors: Allow materials to accumulate without pressure, reducing damage to sensitive loads.
- Impact Roller Conveyors: Equipped with shock-absorbing rollers, minimizing damage from heavy or abrasive materials.
- Trough Roller Conveyors: Feature a trough-shaped design, securing materials in place during transport.
Chain Conveyors in Mining Conveyor Design
Chain conveyors stand out in mining conveyor design for their strength and durability.
- Drag Chain Conveyors: Drag materials through a trough, ideal for heavy or abrasive materials.
- Tubular Drag Chain Conveyors: Enclose materials in a tube, protecting them and the environment.
- Bucket Chain Conveyors: Employ buckets to lift materials vertically, suitable for deep mining operations.
- Scraper Chain Conveyors: Use a chain to scrape materials along the floor of the conveyor, efficient for fine or sticky materials.
- Apron Chain Conveyors: Feature metal plates or aprons, robust for transporting large boulders or ores.
- Heavy-duty Chain Conveyors: Designed for the most demanding loads, ensuring reliability in harsh mining conditions.
Specialized Systems in Mining Conveyor Design
Mining conveyor design also incorporates specialized systems tailored to specific operational needs. Three examples of each include:
- Shuttle Conveyors: Move back and forth along a track, offering flexible loading points.
- Overland Conveyors: Span across long distances, connecting different mining sites or processing facilities.
- Material Stacker Conveyors: Stack materials in piles or bins, optimizing storage and handling.
Each of these conveyor systems plays a crucial role in the mining conveyor design, ensuring materials are transported efficiently, safely, and reliably across mining operations. Their selection and implementation depend on the specific requirements of the mining site, including the type of material, distance of transport, and environmental considerations.
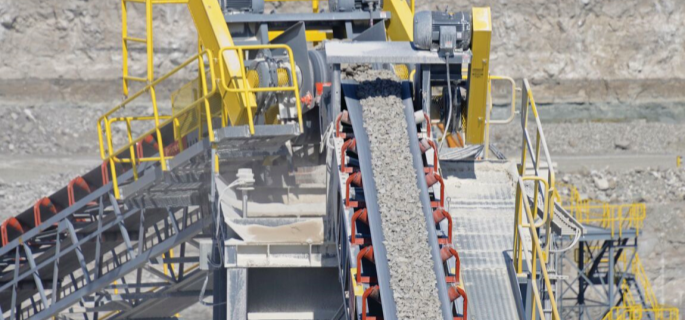
Key Components of Mining Conveyor Design
A successful mining conveyor design hinges on the integration and optimization of several key components. Each plays a vital role in ensuring the conveyor’s efficiency, reliability, and safety. This section provides a detailed exploration of these components within the context of mining conveyor design.
Idlers in Mining Conveyor Design
Idlers are crucial for supporting the conveyor belt and the material being transported. They reduce the conveyor belt’s wear and energy consumed by the conveyor.
- Impact Idlers: Positioned at loading points to absorb the shock of falling materials.
- Carry Idlers: Support the belt and material weight on the carrying side.
- Return Idlers: Support the belt on the return side.
- Guide Idlers: Prevent the belt from straying off its intended path.
- Spiral Idlers: Reduce the buildup of material on the belt.
- Troughing Idlers: Shape the belt into a trough for carrying more material.
Pulleys in Mining Conveyor Design
Pulleys drive the belt and can change its direction. They are essential for the belt’s proper tensioning and alignment.
- Drive Pulleys: Provide the driving force to the belt.
- Tail Pulleys: Located at the tail end, they help in belt tensioning.
- Head Pulleys: Positioned at the discharge point, they can also be drive pulleys.
- Snub Pulleys: Increase the angle of wrap on the drive pulley, enhancing traction.
- Take-up Pulleys: Adjust the belt’s tension to prevent slippage.
- Bend Pulleys: Change the belt’s direction.
Drive Units in Mining Conveyor Design
Drive units are the powerhouses of conveyor systems, providing the necessary force to move the belt and its load.
- Electric Motors: The most common drive unit, offering high efficiency and reliability.
- Hydraulic Motors: Used in applications requiring variable speed control.
- Gearboxes: Reduce the motor’s speed to the desired conveyor speed.
- ABB Conveyors: Feature advanced drive technology for optimal performance.
- Variable Frequency Drives (VFDs): Allow for speed control, improving energy efficiency.
- Fluid Couplings: Provide soft start capabilities, protecting the conveyor belt from sudden stresses.
Trunk Conveyors in Mining Conveyor Design
Trunk conveyors are the main arteries of the conveyor system, transporting materials over long distances.
- Overland Trunk Conveyors: Connect different parts of a mining operation across vast distances.
- Underground Trunk Conveyors: Transport material from deep within the mine to the surface.
- Inclined Trunk Conveyors: Move materials up steep inclines.
- Declined Trunk Conveyors: Safely transport materials down slopes.
- Curved Trunk Conveyors: Navigate around obstacles and terrain.
- High-speed Trunk Conveyors: Designed for rapid material transport.
The integration and proper functioning of these components are fundamental to the mining conveyor design. Idlers and pulleys ensure the belt’s stability and longevity, drive units provide the necessary power, and trunk conveyors facilitate the efficient transport of materials. Together, they form a cohesive system that maximizes the efficiency, reliability, and safety of the mining conveyor operation.
Types of Mining Conveyor Belts in Mining Conveyor Design
The selection of the appropriate conveyor belt is a critical decision in mining conveyor design, directly impacting the system’s efficiency, durability, and safety. This section explores the various types of conveyor belts used in mining and the considerations involved in selecting the right type of belt for specific mining operations.
Multi-ply Belts in Mining Conveyor Design
Multi-ply conveyor belts are composed of several layers of fabric and rubber, making them versatile and durable.
- General-purpose Multi-ply Belts: Suitable for a wide range of materials under standard conditions.
- Abrasion-resistant Multi-ply Belts: Designed for transporting sharp and abrasive materials.
- Oil-resistant Multi-ply Belts: Used in environments where oil and grease are present.
- Fire-resistant Multi-ply Belts: Essential in mines where fire hazards exist.
- Heat-resistant Multi-ply Belts: Capable of withstanding high temperatures from hot materials.
- Cold-resistant Multi-ply Belts: Engineered to perform in low-temperature conditions.
Straight-warp Belts in Mining Conveyor Design
Straight-warp conveyor belts are built to withstand severe impact and tearing, making them ideal for heavy-duty applications.
- Heavy-load Straight-warp Belts: For transporting large volumes of heavy materials.
- Impact-resistant Straight-warp Belts: Designed to resist damage from large, heavy, or sharp objects.
- Tear-resistant Straight-warp Belts: Prevents propagation of tears, ensuring longevity.
- High-tensile Straight-warp Belts: Offers superior strength for long-distance conveying.
- Energy-efficient Straight-warp Belts: Reduces energy consumption by minimizing belt drag.
- Low-maintenance Straight-warp Belts: Requires less frequent repairs and replacements.
Steel-cord Belts in Mining Conveyor Design
Steel-cord conveyor belts are reinforced with steel cables, providing high strength and low elongation for long-distance applications.
- Long-distance Steel-cord Belts: Ideal for cross-country and overland transportation.
- High-strength Steel-cord Belts: Supports heavy loads without significant stretching.
- Vertical Steel-cord Belts: Used in steep incline or decline conveyance.
- Fire-resistant Steel-cord Belts: Incorporates fire-retardant properties for safety.
- Rip-resistant Steel-cord Belts: Features a rip detection system for early warning.
- Flexible Steel-cord Belts: Despite their strength, they are flexible enough for curved paths.
Heat-resistant Belts in Mining Conveyor Design
Heat-resistant conveyor belts are designed to withstand high temperatures from materials like sinter, coke, and cement.
- Moderate-heat Resistant Belts: For temperatures up to 200°C.
- High-heat Resistant Belts: Can handle materials with temperatures up to 400°C.
- Extreme-heat Resistant Belts: Designed for the most severe heat conditions, exceeding 400°C.
- Low-shrinkage Heat-resistant Belts: Minimizes dimensional changes at high temperatures.
- Chemical-resistant Heat Belts: Offers resistance to chemicals in addition to heat.
- Energy-saving Heat-resistant Belts: Reduces heat loss, improving energy efficiency.
The selection process for mining conveyor belts in mining conveyor design involves a thorough analysis of material characteristics, such as abrasiveness, temperature, and weight, as well as operational requirements like length of conveyance, environmental conditions, and load capacity. Understanding these factors ensures the chosen conveyor belt enhances the mining operation’s efficiency, safety, and productivity.
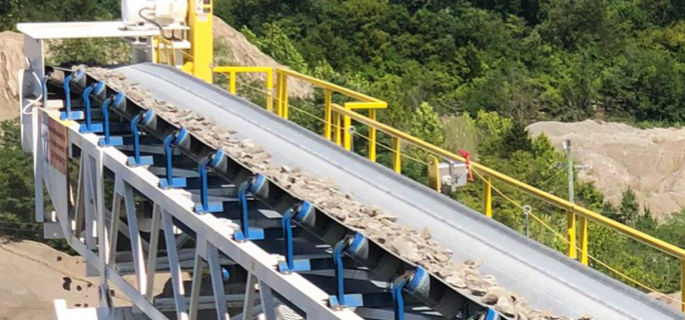
Safety and Reliability in Mining Conveyor Design
Ensuring safety and reliability is paramount in mining conveyor design. This section delves into the essential safety features and strategies that enhance the reliability of mining conveyors, underlining their importance in maintaining operational integrity and protecting personnel.
Safety Features in Mining Conveyor Design
Safety features are integral to mining conveyor design, aimed at minimizing risks and ensuring a secure working environment. Six specific examples of each category include:
Guarding
- Belt Guards: Prevent access to moving belts and pulleys.
- Tail Pulley Guards: Shield the tail pulley to prevent accidental contact.
- Pinch Point Guards: Cover potential pinch points where injuries could occur.
- Skirtboard Guards: Enclose skirtboards at loading zones to prevent material spillage.
- Conveyor Crossover Guards: Provide safe passages over conveyors for personnel.
- Electrical Guards: Protect electrical components to prevent electrical hazards.
Emergency Shut-offs
- Pull Cord Switches: Allow for the conveyor to be stopped immediately from any point along its length.
- Emergency Stop Buttons: Strategically placed for quick access in case of an emergency.
- Belt Misalignment Switches: Automatically stop the conveyor if the belt becomes misaligned.
- Under-speed Sensors: Detect if the conveyor belt slows down unexpectedly, triggering a shutdown.
- Zero Speed Switches: Ensure the conveyor stops if the belt stops moving.
- Safety Interlocks: Prevent the conveyor from starting under unsafe conditions.
Fugitive Dust Control
- Dust Suppression Systems: Apply water or chemicals to reduce dust emissions.
- Enclosed Conveyors: Minimize dust by fully enclosing the conveyor belt.
- Dust Collection Systems: Vacuum airborne dust from critical areas.
- Skirting Systems: Seal the edges of the belt to prevent dust escape.
- Wind Guards: Reduce the wind’s ability to disperse dust from the conveyor.
- Water Sprinklers: Strategically placed to dampen materials and reduce dust.
Strategies for Enhancing Reliability in Mining Conveyor Design
Reliability in mining conveyor design ensures continuous operation and reduces unexpected downtime. Six specific examples of each strategy include:
Build Quality
- High-grade Materials: Use of abrasion-resistant and durable materials for longer life.
- Robust Design: Engineering conveyors to withstand harsh mining conditions.
- Precision Manufacturing: Ensuring components are made to exact specifications for optimal performance.
- Quality Control Checks: Rigorous testing of components before installation.
- Corrosion Protection: Application of coatings and treatments to resist rust and corrosion.
- Wear Monitoring: Incorporating sensors to monitor wear and tear on critical components.
Maintenance Practices
- Regular Inspections: Scheduled checks to identify and rectify potential issues early.
- Preventative Maintenance: Routine maintenance tasks to prevent failures.
- Predictive Maintenance: Using data analytics to predict and prevent breakdowns.
- Training Programs: Educating maintenance staff on best practices and safety protocols.
- Spare Parts Inventory: Keeping critical spare parts on hand for quick replacements.
- Maintenance Records: Documenting maintenance activities for ongoing analysis and improvement.
Automation
- Automated Monitoring Systems: For real-time tracking of conveyor performance and health.
- Remote Control Operations: Allowing for the safe operation of conveyors from a distance.
- Intelligent Systems: Utilizing AI and machine learning for predictive analytics.
- Automated Alignment: Systems to automatically correct belt misalignment.
- Load Management: Software to optimize load distribution and conveyor speed.
- Safety Systems Integration: Incorporating safety features into the conveyor’s control system for immediate response to hazards.
Redundancy
- Dual Drive Systems: Providing a backup in case one drive unit fails.
- Backup Power Supplies: Ensuring operations can continue during power outages.
- Redundant Safety Features: Multiple layers of safety features to ensure protection.
- Alternative Material Routes: Designing the system to reroute materials if one conveyor fails.
- Modular Components: Allowing for quick replacement and repair.
- Fail-safe Controls: Systems designed to default to a safe condition in the event of a failure.
Incorporating these safety features and reliability strategies into mining conveyor design not only safeguards the workforce but also ensures that mining operations can proceed smoothly and efficiently, minimizing downtime and maximizing productivity.
Mining Conveyor Design Excel
Using Excel for Conveyor Design
In the realm of mining conveyor design, Excel is an invaluable tool for engineers and designers. It allows for detailed and customizable calculations, facilitating the design process of complex conveyor systems. Excel’s flexibility and computational power make it ideal for managing the various parameters and variables involved in conveyor design, enabling precise and efficient planning.
Benefits of Using Excel for Conveyor System Calculations
Using Excel for mining conveyor design offers several key benefits:
- Flexibility: Excel can handle a wide range of calculations and can be tailored to fit specific project requirements. It allows for the creation of custom formulas and the integration of multiple data sets.
- Visualization: Excel provides various charting and graphing tools to visualize data, making it easier to interpret and present design calculations.
- Efficiency: Automating calculations through Excel reduces the risk of human error and speeds up the design process. Complex scenarios can be modeled quickly, allowing for rapid iteration and optimization.
- Accessibility: Excel is widely used and easily accessible, ensuring that project stakeholders can view and understand the design calculations.
- Documentation: Excel workbooks can serve as detailed records of the design process, providing a comprehensive log of all calculations and assumptions made during the project.
Key Parameters and Formulas Used in Excel for Designing Conveyors
Designing a mining conveyor system in Excel involves several critical parameters and formulas. Key parameters include:
- Belt Tension: Calculated using the formula ( T = F \times (L + H) ), where ( T ) is the belt tension, ( F ) is the force required to move the load, ( L ) is the length of the conveyor, and ( H ) is the height difference between the start and end points.
- Motor Power: Determined by the formula ( P = (T \times V) / (33000 \times \eta) ), where ( P ) is the power required, ( T ) is the belt tension, ( V ) is the belt speed, and ( \eta ) is the efficiency of the system.
- Belt Speed: Calculated as ( V = D \times \pi \times N ), where ( V ) is the belt speed, ( D ) is the diameter of the drive pulley, and ( N ) is the rotational speed of the drive pulley.
- Load Carrying Capacity: Determined using the formula ( Q = V \times A \times \rho ), where ( Q ) is the load capacity, ( V ) is the belt speed, ( A ) is the cross-sectional area of the load, and ( \rho ) is the density of the material being transported.
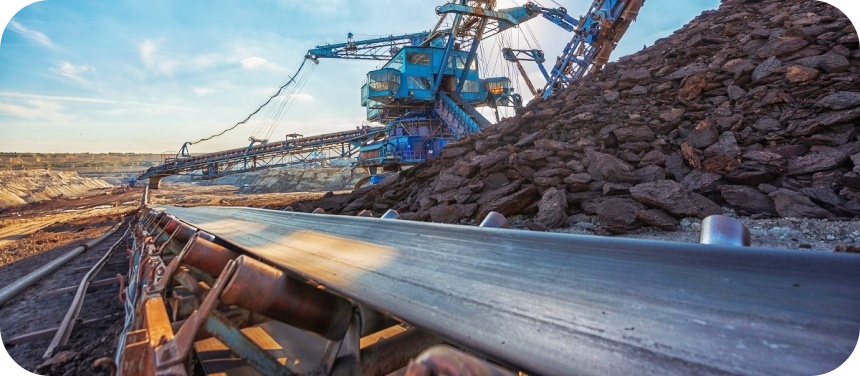
Step-by-Step Guide to Creating an Excel Model for Conveyor Design
Creating an Excel model for mining conveyor design involves the following steps:
Set Up the Spreadsheet:
- Create a new workbook and label sheets for different sections such as “Inputs”, “Calculations”, and “Outputs”.
- In the “Inputs” sheet, define all the parameters needed for the calculations, such as conveyor length, height difference, material density, belt speed, and efficiency.
Input Data:
- Enter the known values for each parameter in the “Inputs” sheet. Use descriptive labels and units for clarity.
Define Formulas:
- In the “Calculations” sheet, use the input data to define the necessary formulas. Reference the input cells to ensure that changes in input values automatically update the calculations.
- Calculate belt tension, motor power, belt speed, and load carrying capacity using the formulas provided above.
Analyze Results:
- Use the “Outputs” sheet to summarize the key results. Create charts and graphs to visualize the data and highlight important findings.
- Perform sensitivity analysis by varying key parameters and observing the impact on the system’s performance.
Validate and Optimize:
- Cross-check the results with industry standards and guidelines to ensure accuracy.
- Optimize the design by adjusting parameters to achieve the desired balance between efficiency, capacity, and cost.
Sample Templates and Resources for Download
To assist in mining conveyor design using Excel, several sample templates and resources are available for download:
Conveyor Design Template:
- A comprehensive template that includes input sections, predefined formulas, and output visualizations. This template can be customized to fit specific project requirements.
Belt Tension Calculation Sheet:
- A focused template for calculating belt tension, incorporating all necessary parameters and formulas.
Motor Power Calculation Workbook:
- A detailed workbook for determining the required motor power, including efficiency considerations and power factor calculations.
Load Carrying Capacity Model:
- A template that helps in calculating and visualizing the load carrying capacity of different conveyor designs.
These resources can streamline the mining conveyor design process, making it easier to create accurate and efficient conveyor systems tailored to specific project needs. By leveraging the power of Excel, engineers can enhance their design capabilities and deliver optimized solutions for complex mining operations.
Designing a Heavy-Duty Conveyor System for Mining Sites
Designing a heavy-duty conveyor system for mining sites requires meticulous planning and attention to detail to ensure efficiency, durability, and safety. Here are the key considerations and steps involved in the process.
1. Understanding Material Characteristics
Bulk Density:
- Measure the bulk density of the material to determine the conveyor’s load capacity and belt tension requirements.
Particle Size and Shape:
- Consider the size and shape of the material to choose the appropriate belt type and surface texture to prevent slippage and ensure smooth transport.
Moisture Content:
- High moisture content can affect material flow and increase the risk of belt slippage. Select belts and components that can handle wet conditions.
Abrasiveness:
- Materials with high abrasiveness can wear down belts and components quickly. Use wear-resistant materials and coatings to extend the lifespan of the conveyor.
2. Conveyor Layout and Route Planning
Travel Distance:
- Calculate the total travel distance to determine the conveyor length. This includes horizontal distances and any vertical lifts required.
Elevation Changes:
- Plan for changes in elevation. Steep inclines may require special belt types and additional power to move the material uphill.
Space Constraints:
- Consider the available space on-site. Compact designs may be necessary for confined spaces, while overland conveyors might be used for long-distance transport.
3. Structural Design and Support
Load Capacity:
- Design the conveyor structure to support the maximum expected load. This includes considering peak loads and ensuring all components can handle the weight.
Support Structures:
- Use sturdy materials for support structures, such as steel or reinforced concrete, to ensure stability and durability.
Foundation and Anchoring:
- Ensure proper foundation and anchoring of the conveyor to prevent movement and maintain alignment, especially in dynamic mining environments.
4. Conveyor Components and Specifications
Belt Type and Specifications:
- Choose the appropriate belt type based on material characteristics, load capacity, and environmental conditions. Options include rubber, steel cord, and fabric belts.
Pulleys and Idlers:
- Select high-quality pulleys and idlers that can withstand the operational demands. Ensure they are properly aligned and maintained to prevent belt wear and misalignment.
Drive Systems:
- Use powerful drive systems capable of handling the conveyor load and ensuring smooth operation. Consider variable frequency drives (VFDs) for better control and efficiency.
Belt Tensioners and Take-Up Units:
- Implement tensioners and take-up units to maintain proper belt tension and compensate for stretch and wear over time.
5. Safety Features
Guarding:
- Install guards around moving parts and pinch points to protect workers from injury. Ensure guards are easily removable for maintenance access.
Emergency Stop Systems:
- Integrate emergency stop systems along the conveyor length, including pull cords and push buttons, to quickly shut down the system in case of an emergency.
Warning Systems:
- Use audible and visual warning systems to alert workers of conveyor operation and potential hazards.
6. Environmental Considerations
Dust Control:
- Implement dust control measures, such as skirting, dust suppression systems, and enclosed transfer points, to minimize airborne particles and improve air quality.
Temperature and Weather Resistance:
- Design the conveyor system to withstand temperature extremes and weather conditions specific to the mining site. Use materials and coatings that can resist corrosion and UV damage.
7. Automation and Monitoring
Automated Controls:
- Incorporate automated control systems for real-time monitoring and adjustment of conveyor operations. This includes sensors for belt speed, tension, and load.
Predictive Maintenance:
- Use predictive maintenance technologies, such as vibration analysis and thermal imaging, to identify potential issues before they cause system failures.
Data Collection and Analysis:
- Implement data collection systems to monitor conveyor performance and analyze trends. Use this data to optimize operations and plan maintenance schedules.
8. Cost and Efficiency Considerations
Energy Efficiency:
- Choose energy-efficient motors and components to reduce power consumption and operational costs. Consider regenerative drives that recover energy during braking.
Operational Costs:
- Evaluate the total cost of ownership, including initial investment, maintenance, and operating expenses. Aim for a design that minimizes long-term costs while maximizing efficiency.
Return on Investment (ROI):
- Calculate the ROI by considering increased productivity, reduced downtime, and extended equipment lifespan. Ensure the design delivers a favorable ROI for the mining operation.
Designing a heavy-duty conveyor system for mining sites requires a comprehensive approach that addresses material characteristics, structural integrity, safety, environmental impact, automation, and cost efficiency. By carefully considering these factors, engineers can create robust conveyor systems that enhance productivity, ensure safety, and withstand the demanding conditions of mining operations.
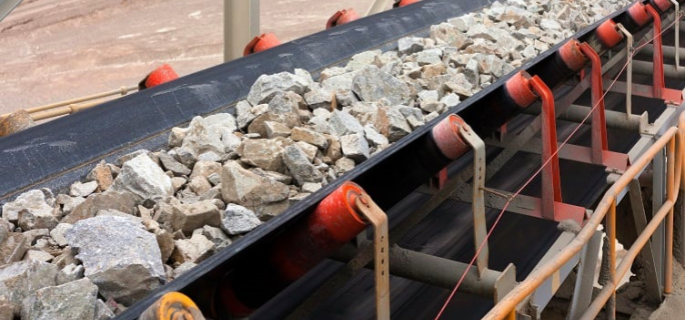
Design Considerations for Optimal Efficiency in Mining Conveyor Design
Achieving optimal efficiency in mining conveyor design requires a comprehensive understanding of various factors that influence performance. This section explores these factors and the significance of drive assembly design, providing specific examples to illustrate their impact on mining conveyor efficiency.
Factors Influencing Conveyor Efficiency
Belt Speed
- High-Speed Conveyors: Designed for rapid material transport, reducing transit time.
- Variable-Speed Conveyors: Allow adjustment based on operational needs, enhancing adaptability.
- Optimized Speed for Material Type: Tailored speeds prevent spillage for fine or bulky materials.
- Energy-Efficient Speed Settings: Lower speeds for non-critical operations save energy.
- Synchronized Speed with Processing Equipment: Ensures smooth integration with crushers, screens, etc.
- Speed Sensors: Monitor and adjust speed in real-time for consistent flow rates.
Belt Width
- Wide Belts for High Volume: Accommodate larger loads, increasing throughput.
- Narrow Belts for Precision Handling: Suitable for detailed sorting and smaller operations.
- Custom Widths for Specific Applications: Tailored design for unique material types or conditions.
- Width Selection for Load Distribution: Ensures even material spread, reducing wear.
- Scalable Designs for Future Expansion: Allows for width adjustments as operation scales.
- Width Compatibility with Feeders and Chutes: Ensures seamless material transfer.
Idler Size and Spacing
- Large-Diameter Idlers for Heavy Loads: Support and distribute weight effectively.
- Close Spacing in High-Impact Areas: Reduces belt sag and material spillage.
- Variable Spacing for Curved Sections: Adapts to changing belt tension and curvature.
- Specialized Idlers for Load Support: Conveyor troughing idlers increase carrying capacity.
- Maintenance-Friendly Idler Designs: Facilitate easy replacement and servicing.
- Impact Idlers for Shock Absorption: Protect the belt at loading points.
Loading Techniques
- Controlled Feed Rates: Prevent overloading and ensure smooth operation.
- Centralized Loading: Reduces belt wear and misalignment issues.
- Adjustable Chutes for Direct Loading: Minimize impact and material dispersion.
- Pre-Screening of Material: Removes fine particles before loading, reducing cleanup.
- Automated Loading Systems: Ensure consistent, efficient material placement.
- Dust Suppression at Loading Points: Improves air quality and reduces material loss.
Significance of Drive Assembly Design
Fluid Couplings
- Smooth Startups: Reduce mechanical stress during startup, extending equipment life.
- Overload Protection: Automatically limit torque, protecting the conveyor from damage.
- Variable Torque Control: Adjust torque based on load, improving efficiency.
- Energy Savings: Reduce power consumption during partial load conditions.
- Shock Absorption: Minimize impacts from load variations.
- Thermal Protection: Prevent overheating in high-torque applications.
Soft-Start Packages
- Gradual Acceleration: Minimizes wear on belts and pulleys.
- Reduced Power Spikes: Lower initial power demand during startup.
- Programmable Profiles: Tailor startup sequences to specific operational needs.
- Integration with Control Systems: Allows for automated control and monitoring.
- Enhanced Safety Features: Include emergency stop and restart protocols.
- Compatibility with Various Motors: Can be used with electric and hydraulic drives.
Variable Frequency Drives (VFDs)
- Speed Adjustment: Precisely control conveyor speed to match processing rates.
- Energy Efficiency: Operate at optimal speeds for energy savings.
- Ramp-Up and Ramp-Down Control: Protects the conveyor during start and stop cycles.
- Load Balancing: Adjusts for varying load conditions without manual intervention.
- Reduced Mechanical Stress: Less wear on gears, belts, and bearings.
- Advanced Diagnostics: Monitor and diagnose system performance for preventative maintenance.
Incorporating these considerations into mining conveyor design not only enhances operational efficiency but also contributes to the longevity and reliability of the conveyor system. By carefully selecting and designing each component and assembly, mining operations can achieve a balance between performance, energy consumption, and maintenance requirements, leading to a more sustainable and cost-effective material handling solution.
Essential Considerations in Belt Conveyor Design
Designing a belt conveyor system for mining applications involves careful planning and detailed attention to various factors. Here are the essential considerations in belt conveyor design that ensure efficient and reliable operation in mining environments.
1. Safety
Guarding:
- Guarding is crucial to protect workers from moving parts and pinch points in the conveyor system. Heavy-duty materials should be used for guards to withstand impacts and harsh conditions.
Emergency Shut-offs:
- Emergency stop mechanisms should be installed at regular intervals along the conveyor. Full-length pull cords are a common safety feature to ensure immediate shutdown in case of emergencies.
Training:
- Proper training for operators and maintenance personnel is vital to minimize risks. Regular safety drills and updates on safety protocols should be conducted.
2. Reliability
Build Quality:
- The conveyor system must be constructed with high-quality, durable materials to withstand the harsh conditions of mining operations. This includes using robust frames, heavy-duty belts, and resilient rollers.
Wear Liners:
- Installing wear liners made of materials such as UHMW (Ultra-High Molecular Weight Polyethylene), Tivar, or abrasion-resistant steel helps reduce wear and extend the life of conveyor components.
Material Characteristics:
- The design must account for the specific characteristics of the material being transported, such as bulk density, moisture content, abrasiveness, and particle size.
Maintenance:
- Regular maintenance schedules should be established to replace worn components, check belt tension, and lubricate moving parts. Preventive maintenance is key to avoiding unexpected downtime.
3. Efficiency
Belt Speed:
- The belt speed should be optimized to balance material throughput and wear on the belt. Faster speeds increase capacity but also wear out the belt quicker.
Belt Width:
- Selecting the appropriate belt width is crucial for ensuring the conveyor can handle the expected volume of material. Wider belts can transport more material but require more space and support.
Idler Spacing:
- Proper spacing of idlers (support rollers) is essential to prevent belt sag and maintain alignment. Closer spacing provides better support but increases the number of components and maintenance points.
Pulleys:
- Pulleys should be designed to handle the tension and load requirements of the conveyor. High-quality, precision-engineered pulleys reduce wear and improve system reliability.
4. Environmental Considerations
Dust Control:
- Dust generation can be a significant issue in mining operations. Implementing dust control measures such as skirting, dust suppression systems, and enclosed transfer points can minimize airborne particles.
Temperature Extremes:
- The conveyor design must account for the operating temperature range. Materials that can withstand high temperatures or extreme cold should be selected based on the specific mining environment.
Corrosion Resistance:
- Components exposed to corrosive materials or environments, such as saline or acidic conditions, should be made from corrosion-resistant materials or coated to prevent degradation.
5. Load and Structural Considerations
Load Capacity:
- The conveyor system must be designed to handle the maximum expected load without overloading. This includes considering peak load scenarios and ensuring that all components can support the weight.
Structural Support:
- The conveyor structure must be robust and stable, with proper foundations and supports to handle the dynamic forces exerted by the moving belt and material load.
Conveyor Length and Elevation Changes:
- The design should accommodate the required length and any changes in elevation. Overland conveyors may need additional supports and tensioning systems to maintain proper operation over long distances.
6. Automation and Monitoring
Automated Control Systems:
- Integrating automated control systems can improve the efficiency and safety of conveyor operations. These systems can monitor belt speed, tension, and load, and make real-time adjustments to optimize performance.
Instrumentation:
- Installing sensors and monitoring equipment allows for continuous data collection on conveyor performance. This data can be used for predictive maintenance and to identify potential issues before they cause failures.
7. Cost Considerations
Initial Investment:
- While cost is always a consideration, investing in high-quality components and a well-designed system can save money in the long run by reducing maintenance and downtime.
Operational Costs:
- Energy efficiency and maintenance requirements should be considered in the design phase to minimize operational costs. Energy-efficient motors and low-friction components can reduce power consumption.
Return on Investment (ROI):
- The overall design should be evaluated based on its ROI, considering factors such as increased productivity, reduced downtime, and extended equipment lifespan.
In mining conveyor design, careful consideration of safety, reliability, efficiency, environmental factors, load capacity, structural support, automation, and cost is essential. By addressing these key areas, designers can create conveyor systems that are not only effective and efficient but also safe and durable, meeting the demanding requirements of mining operations.
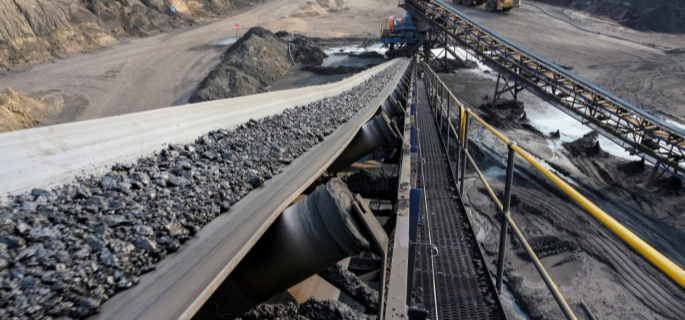
Advanced Design Tools and Techniques in Mining Conveyor Design
The evolution of mining conveyor design has been significantly influenced by the advent of advanced design tools and techniques. These innovations have revolutionized how engineers approach the design process, enabling the creation of more efficient, safe, and cost-effective conveyor systems. This section explores the modern design tools at the disposal of mining conveyor designers and the pivotal role they play in shaping the future of conveyor technology.
Introduction to Modern Design Tools
Mining Conveyor Design PDFs
Comprehensive guides and reference materials are available in PDF format, offering in-depth insights into best practices, standards, and technical specifications for mining conveyor design. These documents serve as a valuable resource for engineers, providing a solid foundation for understanding the complexities of conveyor systems.
Excel Templates for Precise Calculations
Excel templates have become indispensable in the mining conveyor design process, allowing for precise calculations related to load distribution, belt strength, motor power requirements, and other critical parameters. These templates enable designers to quickly assess various scenarios and optimize the conveyor design for performance and efficiency.
Software for Simulation
Simulation software represents the cutting edge of mining conveyor design tools, offering the ability to model conveyor operations in a virtual environment. This allows for the identification of potential issues and the testing of different design solutions without the need for physical prototypes.
The Role of These Tools in Creating Efficient, Safe, and Cost-Effective Conveyor Designs
Enhancing Efficiency
- Optimized Material Flow: Simulation software can predict material flow and identify bottlenecks, enabling adjustments that enhance throughput.
- Energy Consumption Analysis: Excel templates calculate the energy requirements of different design configurations, helping to select the most efficient option.
- Load Distribution Optimization: Advanced tools ensure even load distribution, reducing wear and extending the lifespan of conveyor components.
Ensuring Safety
- Hazard Identification: Simulation software identifies potential safety hazards, allowing for the design of mitigation strategies before construction.
- Safety Compliance Checks: PDFs provide guidelines and standards for safety, which can be directly applied during the design process.
- Emergency System Design: Tools facilitate the integration of emergency stop systems and other safety features, ensuring quick response to potential incidents.
Cost-Effectiveness
- Material and Component Selection: Excel templates help in selecting cost-effective materials and components that meet the design requirements.
- Lifecycle Cost Analysis: Simulation software evaluates the total cost of ownership, including maintenance and operational costs, guiding more economical design choices.
- Design Iteration Speed: The use of advanced tools accelerates the design process, reducing the time and cost associated with manual calculations and trial-and-error methods.
The integration of advanced design tools and techniques in mining conveyor design has not only streamlined the design process but also significantly improved the quality and performance of conveyor systems. By leveraging these tools, engineers can create conveyor designs that are not only aligned with the operational goals of mining projects but also contribute to the sustainability and profitability of mining operations.
Inquire here for top-quality conveyor products.
Case Studies and Industry Examples in Mining Conveyor Design
The practical application of mining conveyor design principles can be best understood through real-world case studies and industry examples. These instances not only showcase the versatility and efficiency of conveyor systems in various mining operations but also highlight the innovative approaches taken by engineers and manufacturers. This section delves into successful mining conveyor designs, ranging from small-scale projects to large-scale installations, and provides insights from leading conveyor belt manufacturers.
Successful Mining Conveyor Designs
Small Mining Conveyor Projects
- Underground Gold Mine, Australia: A compact conveyor system was designed to navigate tight spaces while transporting gold ore from the mine face to the processing facility.
- Coal Mine, Kentucky, USA: A small-scale conveyor system was implemented to efficiently move coal over short distances, reducing reliance on truck haulage and lowering operational costs.
- Quartz Sand Mine, Germany: A specialized small conveyor was developed to handle the abrasive nature of quartz sand, optimizing material handling and minimizing wear.
- Diamond Mine, Botswana: A custom-designed conveyor system was created for the precise handling and sorting of diamonds, ensuring the integrity of the gems throughout the process.
- Salt Mine, Poland: A compact, corrosion-resistant conveyor system was installed to transport salt from the mining area to the surface, withstanding the harsh mining environment.
- Limestone Quarry, France: A small, flexible conveyor system was designed to adjust to the quarry’s changing landscape, enhancing material transport efficiency.
Large-Scale Installations
- Iron Ore Mine, Brazil: One of the world’s longest single-flight conveyor systems was installed to transport iron ore across vast distances, significantly reducing transportation costs.
- Copper Mine, Chile: A high-capacity conveyor belt system was deployed to move copper ore from the mine to the processing plant, showcasing advanced control and drive technologies.
- Coal Handling Facility, Australia: A comprehensive conveyor network was designed for a coal export terminal, incorporating numerous conveyors for material handling efficiency.
- Bauxite Mine, Guinea: A large-scale conveyor system was implemented to transport bauxite over hilly terrain, demonstrating advanced engineering and design capabilities.
- Phosphate Mine, Morocco: An extensive conveyor belt system was designed to handle the abrasive nature of phosphate, optimizing throughput and reducing maintenance needs.
- Gold Mine, Peru: A state-of-the-art conveyor system was installed to move gold ore across challenging terrain, incorporating advanced safety and monitoring features.
Insights from Leading Mining Conveyor Belt Manufacturers
Application of Shuttle Conveyor Systems
- Flexibility in Material Handling: Shuttle conveyors offer the ability to move in multiple directions, providing flexibility in directing materials to different processing lines.
- Efficient Use of Space: Manufacturers highlight how shuttle conveyors maximize space utilization, especially in confined areas of mining operations.
- Customization for Specific Mining Needs: Leading manufacturers have developed customized shuttle conveyor systems tailored to the unique requirements of various mines.
- Integration with Existing Systems: Insights reveal the seamless integration of shuttle conveyors with existing conveyor networks, enhancing overall system efficiency.
- Enhanced Material Distribution: Shuttle conveyors are praised for their ability to evenly distribute material across storage facilities or processing equipment.
- Innovative Design Features: Manufacturers have incorporated advanced design features into shuttle conveyors, such as variable speed controls and automated positioning, to improve operational efficiency and safety.
These case studies and insights from leading manufacturers underscore the critical role of innovative mining conveyor design in addressing the diverse challenges faced by the mining industry. By leveraging advanced technologies and customized solutions, mining operations can achieve enhanced efficiency, safety, and cost-effectiveness in material handling.
Mining Conveyor Belt Manufacturers
Leading Manufacturers in the Mining Conveyor Industry
In the field of mining conveyor design, selecting the right manufacturer is crucial to ensuring the efficiency, durability, and reliability of conveyor systems. Several leading manufacturers specialize in creating high-quality conveyor belts and related components tailored for mining applications. These manufacturers offer a wide range of products and services designed to meet the unique challenges of the mining industry.
List of Top Manufacturers and Suppliers
- GRAM Conveyor
- Fenner Dunlop
- ContiTech
- Bridgestone
- Goodyear
- Phoenix Conveyor Belt Systems
- Flexco
- Dunlop Conveyor Belting
- Metso
- Bando
Overview of Products and Services Offered by Each Manufacturer
GRAM Conveyor
- Products: High-tensile strength belts, flame-resistant belts, heat-resistant belts, oil-resistant belts.
- Services: Custom design and manufacturing, installation, maintenance, and repair services.
- Innovations: Advanced materials for increased durability and performance under extreme conditions.
Fenner Dunlop
- Products: Heavy-duty mining belts, steel cord belts, fabric-reinforced belts, fire-resistant belts.
- Services: Comprehensive conveyor belt lifecycle management, including design, installation, monitoring, and maintenance.
- Innovations: Enhanced monitoring technologies for real-time belt performance tracking.
ContiTech
- Products: Textile and steel cord conveyor belts, special-purpose belts, chevron belts.
- Services: Belt splicing, maintenance, diagnostics, and predictive maintenance services.
- Innovations: Smart conveyor belt systems with integrated monitoring and diagnostics.
Bridgestone
- Products: High-performance rubber conveyor belts, heat-resistant belts, abrasion-resistant belts.
- Services: Design, installation, and after-sales support.
- Innovations: Development of eco-friendly and energy-saving conveyor belt materials.
Goodyear
- Products: Heavy-duty belts, steel cord belts, high-temperature belts.
- Services: Engineering support, belt installation, and maintenance services.
- Innovations: Proprietary rubber compounds for enhanced durability and performance.
Phoenix Conveyor Belt Systems
- Products: Steel cord belts, textile belts, special application belts.
- Services: Belt splicing, system engineering, and after-sales service.
- Innovations: Highly durable and long-lasting conveyor belts for demanding mining environments.
Flexco
- Products: Mechanical belt fasteners, belt cleaners, conveyor belt accessories.
- Services: Field support, training, installation, and maintenance services.
- Innovations: Advanced belt cleaning systems and fasteners to improve operational efficiency.
Dunlop Conveyor Belting
- Products: Multi-ply belts, steel cord belts, fire-resistant belts.
- Services: On-site belt splicing and repair, belt condition monitoring.
- Innovations: High-quality rubber compounds and manufacturing techniques for improved belt longevity.
Metso
- Products: High-strength conveyor belts, overland conveyor systems, portable conveyors.
- Services: Complete conveyor system design, installation, and maintenance.
- Innovations: Integrated digital solutions for conveyor system monitoring and optimization.
Bando
- Products: General-purpose belts, high-temperature belts, oil-resistant belts.
- Services: Custom belt design, installation, and maintenance services.
- Innovations: Development of high-performance belts tailored for specific mining applications.
Key Considerations When Selecting a Manufacturer
When selecting a manufacturer for mining conveyor design, consider the following factors:
- Quality and Durability: Ensure the manufacturer uses high-quality materials and manufacturing processes to produce durable conveyor belts that can withstand the harsh conditions of mining environments.
- Customization: Look for manufacturers that offer custom design services to tailor conveyor belts to your specific requirements.
- Technical Support: Choose a manufacturer that provides comprehensive technical support, including design assistance, installation, and maintenance services.
- Innovations: Evaluate the manufacturer’s commitment to innovation and their ability to integrate advanced technologies into their products.
- Reputation: Consider the manufacturer’s reputation in the industry and their track record of delivering reliable and efficient conveyor solutions.
Insights into the Latest Innovations and Technologies from Leading Manufacturers
Leading manufacturers in mining conveyor design are continuously innovating to improve the performance and efficiency of their products. Some of the latest advancements include:
- Smart Conveyor Systems: Integration of sensors and monitoring technologies to provide real-time data on belt performance, wear, and potential issues. This allows for predictive maintenance and reduces downtime.
- Advanced Materials: Development of new rubber compounds and reinforcement materials that offer enhanced resistance to wear, heat, and chemicals, extending the lifespan of conveyor belts.
- Energy-Efficient Designs: Engineering conveyor belts that reduce energy consumption and improve overall system efficiency, contributing to lower operational costs and environmental impact.
- Eco-Friendly Products: Focus on creating conveyor belts with environmentally friendly materials and manufacturing processes to minimize the ecological footprint of mining operations.
By partnering with leading manufacturers who are at the forefront of mining conveyor design, companies can ensure they have access to the most advanced and reliable conveyor systems available, enhancing their operational efficiency and competitiveness in the mining industry.
Future Trends in Mining Conveyor Design
The landscape of mining conveyor design is poised for transformative changes, driven by emerging trends and technologies. These advancements promise to redefine efficiency, safety, and sustainability in mining operations. This section explores these future trends and their potential impact on the mining industry.
Emerging Trends and Technologies in Mining Conveyor Design
Automation
- Autonomous Conveyor Systems: Fully automated conveyors that adjust operations in real-time for optimal efficiency.
- Intelligent Monitoring Systems: Advanced sensors and AI for predictive maintenance, detecting potential failures before they occur.
- Remote Operation Centers: Centralized control rooms where operators can monitor and manage conveyor systems across multiple sites.
- Automated Loading and Unloading: Systems that precisely control the material flow, reducing spillage and improving safety.
- Robotics Integration: Robotic arms and drones for inspections and minor repairs, minimizing downtime and human exposure to hazardous conditions.
- Energy Management Software: AI-driven tools that optimize energy use across conveyor systems, significantly reducing operational costs.
Advanced Materials
- Ultra-High-Molecular-Weight Polyethylene (UHMWPE) Rollers: Offering reduced weight, lower friction, and increased lifespan.
- Self-Healing Conveyor Belts: Materials that repair minor cuts and abrasions, extending belt life and reducing maintenance.
- High-Temperature Resistant Belts: New compounds capable of withstanding extreme temperatures without compromising integrity.
- Eco-Friendly Materials: Conveyor components made from recycled or sustainable materials, reducing environmental impact.
- Smart Fabrics: Conveyor belts embedded with sensors to monitor wear, temperature, and other critical parameters in real-time.
- Corrosion-Resistant Alloys: For rollers and frames, offering enhanced durability in harsh mining environments.
Secure your conveyor with our expert help now.
Potential Impact of These Trends on the Mining Industry’s Future
Efficiency and Productivity
- Reduced Operational Downtime: Predictive maintenance and intelligent monitoring lead to fewer unexpected breakdowns.
- Increased Throughput: Automated systems optimize loading and belt speed, maximizing material movement.
- Lower Energy Consumption: Energy management software and efficient materials reduce the carbon footprint of mining operations.
Safety and Sustainability
- Enhanced Worker Safety: Automation and remote operation minimize human exposure to dangerous conditions.
- Reduced Environmental Impact: Eco-friendly materials and energy-efficient designs contribute to more sustainable mining practices.
- Compliance with Regulations: Advanced systems ensure operations meet increasingly stringent safety and environmental standards.
Cost Management
- Lower Maintenance Costs: Durable materials and self-healing technologies decrease the need for frequent replacements and repairs.
- Optimized Resource Allocation: Automation allows for precise control over material handling, reducing waste and improving resource use.
- Long-Term Savings: Although initial investments in advanced technologies may be higher, the long-term savings in operational and maintenance costs are significant.
The future of mining conveyor design is on the cusp of a technological revolution, with automation and advanced materials leading the charge. These trends not only promise to enhance operational efficiency and safety but also pave the way for a more sustainable and cost-effective mining industry. As these technologies mature and become more widely adopted, mining operations will likely see profound changes in how materials are transported, with positive impacts on productivity, environmental stewardship, and profitability.
FAQs About Mining Conveyor Design
Conveyors are essential components in various industries, facilitating the efficient transport of materials. Three primary types of conveyors are Belt Conveyors, Roller Conveyors, and Chain Conveyors.
Belt Conveyors are the most common type, consisting of a continuous belt that moves between two or more pulleys. They are versatile and can transport a wide range of materials over long distances, either horizontally or on an incline. Belt conveyors are widely used in industries like mining, agriculture, and manufacturing for their efficiency and ability to handle both bulk and packaged goods.
Roller Conveyors utilize a series of rollers to move materials. They are best suited for transporting solid items of various sizes. Roller conveyors are categorized into gravity roller conveyors, where items move by gravity or manual force, and powered roller conveyors, which use motors for movement. They’re commonly found in warehousing, distribution centers, and assembly lines.
Chain Conveyors involve a series of chain segments connected in a continuous loop. They are robust and designed to carry heavy, bulky items such as pallets, industrial containers, and large manufactured parts. Chain conveyors are often used in automotive, heavy manufacturing, and packaging industries due to their durability and capacity to handle substantial weights.
Each conveyor type offers unique advantages, making them suitable for specific applications based on material type, weight, transport distance, and environmental conditions.
In the mining industry, the choice of conveyor belt is critical due to the harsh conditions and the need for transporting heavy and abrasive materials. The most commonly used types of conveyor belts in mining are:
Multi-ply Belts: Made of several layers of fabric with rubber interlays, multi-ply belts are versatile and durable, suitable for carrying heavy loads over long distances. They are particularly effective in resisting impact and abrasion, making them ideal for transporting coal, ore, and other mined materials.
Steel Cord Belts: These belts are reinforced with steel cables running longitudinally. Steel cord belts are known for their high strength, low elongation, and long service life, making them suitable for long-distance, high-tensile applications in mining operations.
Solid Woven Belts: Constructed from a single, solid woven fabric layer, these belts are highly resistant to tearing and impact. They are often used in underground mining applications due to their flame-resistant properties and ability to handle sharp and abrasive materials.
The selection of a conveyor belt in mining depends on several factors, including the material being transported, the conveying distance, and the operation’s specific environmental conditions.
The thickness of mining conveyor belts can vary significantly based on the belt’s construction, material, and intended use. Typically, the thickness ranges from about 10mm to 30mm.
Multi-ply Conveyor Belts: These belts have multiple layers of fabric and rubber, with total thicknesses ranging from 10mm to 20mm. The thickness is crucial for durability and impact resistance, especially when transporting heavy or sharp materials.
Steel Cord Conveyor Belts: These belts are generally thicker, with thicknesses ranging from 15mm to 30mm. The inclusion of steel cords adds to the belt’s overall strength and thickness, providing the necessary support for heavy loads and long-distance transportation.
Solid Woven Conveyor Belts: Often used in underground mining, these belts have a more consistent thickness, usually between 10mm and 15mm. Their construction is designed to be durable yet flexible, with added emphasis on fire resistance and safety.
The specific thickness required for a mining operation will depend on the conveyor belt’s material, the type of materials being transported, and the operational demands of the mining environment.
Mining conveyors work by using a motorized system to move a belt around a series of rollers and pulleys. This continuous loop allows for the efficient transport of materials from one point to another. Here’s a simplified overview of the process:
Loading: Materials extracted from the mine, such as ore, coal, or aggregates, are loaded onto the conveyor belt at the tail end. This can be done manually, via a loader, or through a feeding mechanism.
Transportation: Once loaded, the materials are carried along the conveyor belt as it moves. The belt’s movement is powered by motors, which drive the pulleys. These pulleys, in turn, move the belt around the conveyor’s frame.
Support and Guidance: Rollers positioned along the conveyor’s length provide support to the belt and help guide it smoothly. These rollers reduce friction and wear on the belt, ensuring efficient operation.
Unloading: At the end of the conveyor, materials are offloaded for further processing, storage, or shipping. This can be achieved through automatic discharge mechanisms, such as trippers or plows, or the belt can lead to another conveyor for continued transportation.
Mining conveyors are designed to operate in challenging conditions, handling heavy loads and operating over long distances, inclines, or declines. They are a critical component in the mining industry, enhancing productivity and safety by automating the transportation of materials.
Last Updated on June 21, 2024 by Jordan Smith
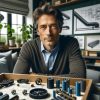
Jordan Smith, a seasoned professional with over 20 years of experience in the conveyor system industry. Jordan’s expertise lies in providing comprehensive solutions for conveyor rollers, belts, and accessories, catering to a wide range of industrial needs. From initial design and configuration to installation and meticulous troubleshooting, Jordan is adept at handling all aspects of conveyor system management. Whether you’re looking to upgrade your production line with efficient conveyor belts, require custom conveyor rollers for specific operations, or need expert advice on selecting the right conveyor accessories for your facility, Jordan is your reliable consultant. For any inquiries or assistance with conveyor system optimization, Jordan is available to share his wealth of knowledge and experience. Feel free to reach out at any time for professional guidance on all matters related to conveyor rollers, belts, and accessories.