Innovations in Mining Conveyor Equipment
Mining conveyor equipment plays a pivotal role in the efficiency and success of mining operations worldwide. These systems are the lifeline of mining sites, facilitating the swift and continuous flow of materials such as ore, coal, and other valuable resources from extraction points to processing facilities or storage areas. The evolution of mining conveyor equipment has been significantly influenced by advancements in technology and engineering. Innovations in materials science, automation, and mechanical design have not only improved the durability and reliability of these systems but also enhanced their capacity to handle diverse and challenging mining environments. As a result, modern conveyor systems are more adaptable, energy-efficient, and capable of meeting the high demands of today’s mining industry, underscoring their indispensable role in the extraction and transportation of minerals.
The Backbone of Mining Operations: Mining Conveyor Equipment
Mining conveyor equipment stands as the foundational infrastructure within the mining industry, enabling the streamlined and efficient movement of materials across both open-pit and underground operations. High availability, low-cost mining conveyor equipment systems efficiently transport materials, including rock, with minimal environmental impact. Essential for the industry.This equipment encompasses a wide array of systems, each tailored to meet the unique demands of different mining environments and material handling requirements.
Variety of Conveyor Systems in Mining
The diversity of mining conveyor equipment includes belt conveyors, shuttle conveyors, and trunk conveyors, each serving specific operational needs:
- Belt Conveyors: These are the most common type of mining conveyor equipment, used for transporting materials over long distances at a low cost. Examples include overland belt conveyors that connect mining pits with processing plants, inclined belt conveyors for moving materials uphill, flat belt conveyors for transporting materials across level ground, curved belt conveyors that navigate around obstacles, and downhill belt conveyors that utilize gravity to transport materials.
- Shuttle Conveyors: Shuttle conveyors offer flexibility in mining operations by moving back and forth on a track, allowing for material to be dumped at multiple points. Examples include reversible shuttle conveyors for filling multiple bins, mobile shuttle conveyors used in heap leaching processes, rail-mounted shuttle conveyors for blending materials, telescopic shuttle conveyors for precise loading, and automated shuttle conveyors integrated with mining operations for efficient material handling.
- Trunk Conveyors: Trunk conveyors are designed for the primary transportation of mined materials from the face to the processing site or lift shaft. Examples include high-capacity trunk conveyors for coal transport, modular trunk conveyors for easy installation in complex mining operations, extendable trunk conveyors for deep mining operations, heavy-duty trunk conveyors for abrasive materials, and flexible trunk conveyors that can be adjusted as mining operations evolve.
Critical Role in Efficient Material Movement
The critical role of mining conveyor equipment in the efficient movement of materials is evident in both open-pit and underground mining operations:
- Open-Pit Mining: In open-pit mining, belt conveyors are used to transport overburden and ore from the excavation site to the processing area or waste dump sites. Examples include conveyors that span several kilometers to connect different parts of the mine, conveyors with large capacities for moving thousands of tons of material per hour, conveyors designed for rugged terrain, environmentally friendly conveyors that minimize dust and noise, and energy-efficient conveyors that reduce operational costs.
- Underground Mining: Underground mining relies on conveyor equipment to transport mined material from deep within the earth to the surface. Examples include flame-resistant conveyors for safety in coal mining, steep incline conveyors for vertical transport of materials, narrow conveyors for tight mining shafts, flexible conveyors that can navigate the complex routes of underground mines, and durable conveyors designed to withstand the abrasive nature of mined materials.
In both scenarios, mining conveyor equipment is indispensable for the timely and cost-effective transportation of materials, highlighting its role as the backbone of mining operations. These systems not only enhance productivity but also contribute to the safety and environmental sustainability of mining practices, making them a critical component in the modern mining industry.
Key Components of Mining Conveyor Equipment
The efficiency and durability of mining conveyor equipment hinge on the quality and reliability of its components. Essential parts such as rollers, idlers, drives, and belts are the building blocks that ensure the smooth operation and longevity of these systems. Understanding the role and variety of these components can provide insights into how conveyor systems are optimized for the demanding conditions of mining operations.
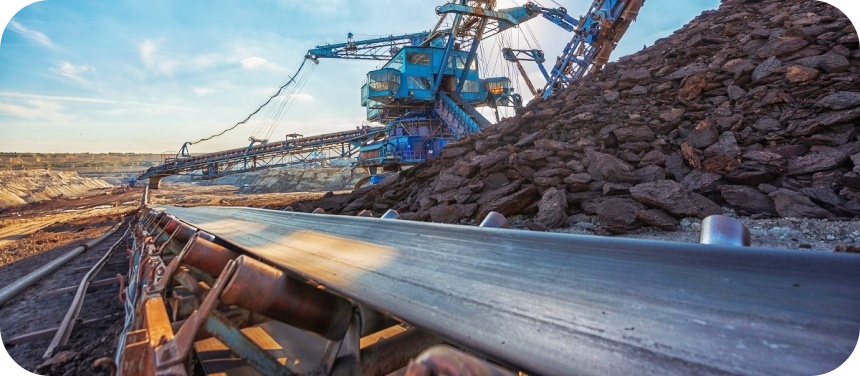
Essential Components and Their Varieties
- Rollers: Rollers support the conveyor belt and material load throughout its length. Examples include impact rollers that absorb the shock of heavy materials falling onto the belt, return rollers that support the belt on its return journey, guide rollers that prevent the belt from straying off its intended path, troughing rollers that shape the belt into a ‘U’ for holding material, and spiral rollers designed to reduce the accumulation of debris on the belt.
- Idlers: Idlers, a type of roller, are specifically designed to maintain the shape and tension of the conveyor belt. Examples include carrying idlers that support the weight of the material, impact idlers placed at loading points to absorb impact forces, adjustable idlers for fine-tuning the belt’s alignment, self-aligning idlers that automatically correct any misalignment of the belt, and suspended idlers used in areas where mounting from the top is not possible.
- Drives: The drive system powers the conveyor belt, dictating its speed and the amount of material moved. Examples include gear motor drives that offer high torque for heavy loads, variable frequency drives (VFDs) that allow for speed adjustment, hydraulic drives for operations requiring shock resistance, direct drives for efficiency and low maintenance, and regenerative drives that can recover energy during the conveyor’s downhill segments.
- Belts: The conveyor belt itself is the surface that carries the material from one point to another. Examples include multi-ply belts made from layers of fabric and rubber for general use, steel-cord belts for high tensile strength in long distances, heat-resistant belts designed to withstand high temperatures, oil-resistant belts that prevent contamination from oils and greases, and flame-resistant belts used in environments where there’s a risk of fire.
Importance of Each Component
Each component of mining conveyor equipment plays a critical role in its overall performance:
- Rollers ensure the belt moves smoothly and efficiently, reducing friction and wear on the belt.
- Idlers maintain the belt’s shape and tension, preventing sagging and misalignment that can lead to operational issues or downtime.
- Drives provide the necessary power to move the belt and its load, allowing for precise control over the speed and handling of materials.
- Belts are the carrying medium of the conveyor system, designed to withstand the specific conditions of the mining environment, including abrasion, temperature, and chemical exposure.
Together, these components ensure the mining conveyor equipment operates smoothly, efficiently, and reliably, contributing to the productivity and safety of mining operations. Regular maintenance and timely replacement of these components are crucial for extending the lifespan of conveyor systems and minimizing operational disruptions.

Advancements in Conveyor Belt Construction and Application in Mining Conveyor Equipment
The mining industry has witnessed significant advancements in the construction and application of mining conveyor equipment, particularly in the areas of carcass design, cover materials, and belt joining techniques. These innovations have been pivotal in enhancing the durability, efficiency, and safety of conveyor belts used in mining operations.
Advancements in Carcass Design
- High-Tensile Strength Materials: The use of high-tensile strength materials like Kevlar and steel cords in carcass design has increased the load-carrying capacity of conveyor belts, allowing them to handle heavier loads over longer distances.
- Flexible Carcass Structures: Developments in flexible carcass structures have improved the belts’ ability to navigate tight curves and steep inclines, expanding the versatility of conveyor system layouts.
- Energy-Efficient Carcass Designs: Innovations in carcass design have led to the development of energy-efficient belts that reduce power consumption by minimizing rolling resistance.
- Impact-Resistant Carcass: The integration of impact-resistant materials into the carcass construction helps absorb shock loads, reducing damage from heavy or sharp materials.
- Eco-Friendly Materials: The adoption of eco-friendly materials in carcass construction supports sustainability goals by reducing the environmental impact of mining conveyor equipment.
Advancements in Cover Materials
- Abrasion-Resistant Covers: New rubber compounds and synthetic materials offer superior resistance to abrasion, extending the life of conveyor belts in harsh mining environments.
- Chemical-Resistant Covers: Advances in chemical-resistant cover materials protect belts from corrosive substances, ensuring reliability in mines with exposure to oils, acids, or other chemicals.
- High-Temperature Resistant Covers: The development of high-temperature resistant cover materials allows conveyor belts to operate in extreme heat conditions without compromising integrity.
- Fire-Retardant Covers: Fire-retardant cover materials have become crucial in enhancing safety, preventing the spread of fire along the conveyor belt.
- Antimicrobial Covers: In specific mining operations where hygiene is a concern, antimicrobial cover materials inhibit the growth of bacteria and fungi on the conveyor belt.
Advancements in Belt Joining Techniques
- Hot Vulcanization: Hot vulcanization techniques have improved, creating seamless and strong belt joints that withstand harsh mining conditions and heavy loads.
- Cold Vulcanization: Cold vulcanization offers a quick and efficient method for belt joining, reducing downtime and maintenance costs.
- Mechanical Fastening: Advances in mechanical fastening systems provide reliable belt joints that can be easily installed and replaced, enhancing operational flexibility.
- Laser Welding: The introduction of laser welding for synthetic belts offers precise and strong joints, contributing to the overall reliability of the conveyor system.
- Induction Welding: Induction welding techniques for belt joining have improved efficiency and strength, ensuring minimal downtime and extended belt life.
Contribution to Durability, Efficiency, and Safety
These advancements in mining conveyor equipment have significantly contributed to the durability, efficiency, and safety of conveyor belts in the mining industry. High-tensile strength materials and flexible carcass designs have increased the operational life and versatility of conveyor systems. Innovations in cover materials have enhanced the belts’ resistance to abrasion, chemicals, and extreme temperatures, ensuring reliable operation under challenging conditions. Improved belt joining techniques have resulted in stronger and more durable joints, reducing maintenance requirements and enhancing safety by minimizing the risk of belt failure. Together, these advancements ensure that mining conveyor equipment can meet the demanding requirements of modern mining operations, supporting productivity and sustainability goals.
Enhance your operations with our conveyor belts.
Types of Conveyor Belts Used in Mining Conveyor Equipment
The diversity of mining conveyor equipment is evident in the variety of conveyor belts designed to meet the unique demands of different mining operations. These belts are engineered to transport materials efficiently over varying distances and through challenging environments, whether in open-pit mines or deep underground.
Different Types of Conveyor Belts and Their Applications
- Multi-ply Belts: Ideal for general use, multi-ply belts consist of several layers of fabric and rubber, providing strength and flexibility. They are commonly used in overland conveying for transporting mined materials over long distances.
- Steel Cord Belts: Known for their high tensile strength, steel cord belts are used in overland and high-lift conveying applications where durability and load-carrying capacity are critical. They are particularly suited for transporting heavy loads over long distances in open-pit mines.
- Solid Woven Belts: Primarily used in underground mining operations, solid woven belts are designed to be fire-resistant and durable, capable of transporting materials through confined spaces and harsh underground environments.
- Chevron Belts: With a patterned surface that increases grip, Chevron belts are used for incline conveying, preventing material rollback. They are ideal for transporting loose materials up steep inclines, such as in-pit conveying systems.
- Pipe Belts: Offering an enclosed transport system, pipe belts prevent material spillage and are used for transporting materials that need to be protected from environmental conditions. They are suitable for both overland and in-pit conveying where environmental protection and material containment are priorities.
Selection Criteria for Conveyor Belts in Mining
The selection of the appropriate type of conveyor belt for mining conveyor equipment depends on several critical factors:
- Material Characteristics: The type of material being transported significantly influences belt selection. Abrasive materials require belts with high wear resistance, while sticky materials might need belts with special surface textures to prevent adhesion.
- Conveying Distance: Long-distance conveying, such as overland transport from the mine to the processing plant, typically requires belts with high tensile strength and durability, like steel cord belts.
- Incline Angle: Steep incline conveying necessitates the use of belts with enhanced grip, such as Chevron belts, to prevent material rollback.
- Load Capacity: The volume and weight of the material being transported dictate the load capacity requirements of the belt. Heavy-duty operations might require steel cord belts for their superior strength and load-carrying capacity.
- Operational Environment: The environmental conditions of the operation, such as exposure to extreme temperatures, chemicals, or fire hazards, influence the selection of belt materials and designs. For example, underground mining operations often require fire-resistant solid woven belts for safety.
The careful selection of mining conveyor equipment, including the type of conveyor belt, is essential for optimizing operational efficiency, ensuring the safety of the operation, and extending the lifespan of the conveyor system. By considering the specific requirements of the material to be conveyed, the distance of transport, and the operational environment, mining operations can choose the most suitable conveyor belt type to meet their needs, enhancing productivity and operational efficiency.

Underground Mining Conveyor Equipment
Underground mining conveyor equipment refers to systems used to transport materials efficiently and safely in underground mining operations. These systems are designed to withstand the harsh conditions of underground environments, ensuring robustness and reliability.
Key Components
- Conveyor Belts: Designed to handle heavy loads and abrasive materials. Available in various materials and configurations to meet the specific needs of the mine.
- Belt Cleaners and Scrapers: Keep conveyor belts clean and prevent material build-up.
- Drive Systems: Include motors, reducers, and drives that power the conveyor belts.
- Idlers and Rollers: Support the conveyor belt and the materials being transported. Impact rollers are often used to absorb the shock of material loading.
- Take-Up Systems: Maintain proper belt tension to ensure efficient operation and minimize wear.
- Belt Conveyors: Used for horizontal or inclined transport of materials, adaptable to different terrains and capable of handling various capacities.
- Shuttle Cars: Transport materials from the mining face to the conveyor belt.
- Feeder Breakers: Combine feeding and crushing in one machine, facilitating smoother material handling.
- Safety Features: Include emergency stop systems, guard rails, and warning signals to ensure personnel safety.
- Dust Control Systems: Manage and reduce dust levels in the mining environment, improving air quality and safety.
- Automated Systems: Advanced controls and automation for monitoring and managing the conveyor system, improving efficiency and reducing downtime.
Advantages and Benefits
- Efficient Transport: Underground mining conveyor equipment enables the high-speed and efficient transport of large quantities of materials, reducing the need for manual handling and increasing productivity.
- Safety: By reducing the risk of personnel coming into direct contact with transported materials, conveyor systems enhance the safety of mining operations.
- Cost-Effective: Although the initial investment may be high, conveyor equipment has low maintenance costs and high energy efficiency, reducing overall operational costs in the long run.
- Environmentally Friendly: Modern conveyor equipment is equipped with dust control systems and low-noise designs, helping to minimize the environmental impact of mining operations.
- Continuous Operation: Conveyor systems can operate 24/7 without interruption, significantly increasing the overall production capacity of the mine.
- Flexibility: Conveyor equipment can be customized to meet the specific needs of the mine, adapting to various terrains and transport requirements.
- Reliability: Designed to be robust and durable, these systems can operate reliably in harsh underground environments, reducing downtime and maintenance costs.
- Automation and Monitoring: Advanced automation systems allow for real-time monitoring and control, improving operational efficiency and reducing human errors.
Underground mining conveyor equipment plays a crucial role in modern mining operations. By enhancing transport efficiency, ensuring safety, reducing costs, and minimizing environmental impact, these systems provide significant advantages and benefits for mining operations.
Choosing the Right Mining Conveyor Equipment for the Coal Mining Industry
Selecting the appropriate conveyor equipment for coal mining involves considering various factors to ensure efficiency, safety, and cost-effectiveness. Here’s a detailed guide to help you choose the right mining conveyor equipment for the coal mining industry:
Understand Your Requirements
- Material Characteristics: Consider the abrasiveness, size, moisture content, and density of the coal. This will influence the type of belt and other components needed.
- Transport Distance and Elevation: Determine the length and incline of the conveyor path. Longer distances and steeper inclines require more robust systems.
- Capacity: Calculate the volume of coal that needs to be transported per hour. This will help in selecting the belt width, speed, and motor power.
Types of Conveyor Systems
- Belt Conveyors: The most common type for coal transport, suitable for both horizontal and inclined paths. Look for belts with high tensile strength and resistance to abrasion.
- Shuttle Conveyors: Useful for loading and unloading coal at different points, providing flexibility in operations.
- Feeder Breakers: Combine feeding and crushing operations, ideal for managing large lumps of coal.
- Stacker Conveyors: Used for stacking coal in stockpiles, ensuring efficient storage and retrieval.
Key Components and Features
- High-Quality Belts: Opt for belts made from durable materials like reinforced rubber or steel cord. Ensure they have appropriate fire resistance ratings for safety in coal mines.
- Robust Idlers and Rollers: Choose rollers designed to withstand heavy loads and harsh conditions. Impact rollers are crucial for absorbing shocks during loading.
- Efficient Drive Systems: Select motors and drives that match your operational needs, considering factors like speed, torque, and energy efficiency.
- Reliable Take-Up Systems: Ensure proper belt tension to maintain efficient operation and reduce wear.
- Advanced Belt Cleaners: Prevent coal build-up on the belts, enhancing efficiency and reducing maintenance needs.
- Dust Control Measures: Implement systems to minimize dust generation and improve air quality, such as enclosed conveyors and dust suppression systems.
Safety Considerations
- Emergency Stop Systems: Essential for quickly halting operations in case of an emergency.
- Guard Rails and Safety Gates: Prevent accidents and ensure safe operation.
- Fire Detection and Suppression: Critical in coal mines to detect and extinguish fires promptly.
- Automated Monitoring and Control Systems: Enable real-time monitoring of the conveyor system, identifying issues before they escalate and improving overall safety.
Cost and Maintenance
- Initial Investment vs. Long-Term Savings: While high-quality equipment may have a higher upfront cost, it often results in lower maintenance costs and longer service life.
- Ease of Maintenance: Choose systems that are easy to maintain and have readily available spare parts to minimize downtime.
- Energy Efficiency: Opt for energy-efficient motors and drives to reduce operational costs.
Supplier Reputation and Support
- Experienced Suppliers: Partner with suppliers who have a proven track record in the coal mining industry.
- After-Sales Support: Ensure the supplier offers comprehensive after-sales support, including maintenance, spare parts, and technical assistance.
Choosing the right conveyor equipment for the coal mining industry requires careful consideration of material characteristics, transport requirements, system components, safety features, cost, and supplier reliability. By selecting high-quality, efficient, and safe equipment, coal mining operations can enhance productivity, reduce operational costs, and ensure the safety of their workforce.

Choosing the Right Mining Conveyor Equipment Manufacturer
Selecting the right manufacturer for mining conveyor equipment is crucial for ensuring operational efficiency, safety, and longevity of the conveyor system. The market is filled with manufacturers, but focusing on quality, reliability, and after-sales support can guide you to the best choice for your mining operation.
Advice on Selecting the Right Manufacturer
- Experience and Reputation: Look for manufacturers with a long-standing presence in the industry and a solid reputation for quality. Companies like West River Conveyors, Fenner Dunlop, Continental Conveyor, Joy Global, and ThyssenKrupp have established themselves as leaders in manufacturing mining conveyor equipment, known for their innovation and reliability.
- Product Range: Choose a manufacturer that offers a wide range of conveyor equipment options and accessories. This diversity ensures that you can find all necessary components that are compatible and optimized for your specific operation.
- Customization Capabilities: Mining operations are unique, and the ability of a manufacturer to provide customized solutions is invaluable. Manufacturers that can tailor conveyor systems to your specific needs, such as adapting to challenging terrains or specific material handling requirements, will contribute significantly to your operation’s efficiency.
- Technical Support and Service: Evaluate the level of technical support and service options the manufacturer provides. Reliable manufacturers offer comprehensive support, from initial design and installation to maintenance and troubleshooting, ensuring your conveyor system operates smoothly throughout its lifecycle.
- Sustainability and Innovation: With increasing focus on environmental sustainability, select a manufacturer that invests in research and development to produce energy-efficient and eco-friendly conveyor solutions. This commitment not only helps in reducing operational costs but also aligns with global sustainability goals.
Importance of Quality, Reliability, and After-Sales Support
- Quality: High-quality mining conveyor equipment reduces the risk of operational failures, minimizes maintenance requirements, and extends the lifespan of the system. Manufacturers that adhere to strict quality control standards in their production processes ensure that their products meet the highest performance and safety criteria.
- Reliability: The reliability of conveyor equipment is paramount in maintaining continuous operations and achieving production targets. Manufacturers with a track record of producing durable and dependable equipment help minimize downtime and enhance productivity.
- After-Sales Support: Comprehensive after-sales support is essential for addressing any issues that may arise during the operation of the conveyor system. This includes access to spare parts, on-site repair services, and technical assistance. Manufacturers like Fenner Dunlop and West River Conveyors, known for their exceptional after-sales service, provide peace of mind and ensure that any disruptions are swiftly resolved.
- Warranty and Guarantees: A manufacturer’s warranty is a testament to the confidence they have in their products. Look for manufacturers that offer substantial warranties and guarantees, as this can significantly reduce future repair or replacement costs.
- Training and Documentation: Adequate training for your staff on the operation and maintenance of the conveyor system is crucial for its longevity and efficiency. Manufacturers that provide comprehensive training and detailed documentation enable your team to properly manage and maintain the equipment, ensuring optimal performance.
Choosing the right mining conveyor equipment manufacturer is a decision that impacts the efficiency, safety, and cost-effectiveness of your mining operations. By prioritizing quality, reliability, and after-sales support, you can select a manufacturer that not only meets your current needs but also supports your operation’s future growth and success.
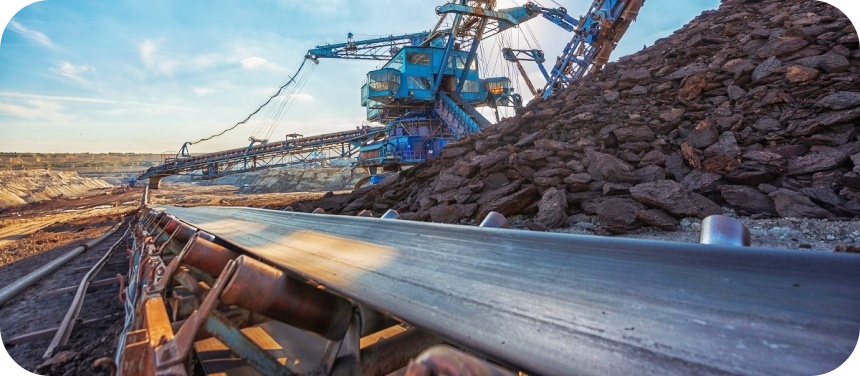
Case Studies: Successful Applications of Mining Conveyor Equipment
The implementation of advanced mining conveyor equipment has significantly transformed operations across the globe. These case studies highlight the impact of innovative conveyor systems on productivity, cost-efficiency, and environmental sustainability in the mining sector.
Successful Implementations
- The Australian Overland Conveyor Project: This project involved the installation of a long-distance overland conveyor system to transport coal from the mine to the processing plant. The system reduced the need for truck haulage, resulting in lower fuel consumption and decreased greenhouse gas emissions. The conveyor’s advanced design also allowed for minimal environmental impact over its route.
- The Chilean Copper Mine Incline Conveyor System: A copper mine in Chile implemented an incline conveyor system to move ore from the depths of the mine to the surface. This system increased the mine’s output by allowing continuous operation and reducing the reliance on traditional lift systems, which were a bottleneck in the production process.
- The Canadian Arctic Diamond Mine Conveyor System: In the challenging conditions of the Canadian Arctic, a diamond mine utilized a custom-designed conveyor system to operate in extreme cold. The system’s durability and reliability under such conditions led to a significant increase in productivity and a reduction in maintenance and operational costs.
- The South African Platinum Mine Conveyor Network: A platinum mine in South Africa introduced a comprehensive conveyor network, integrating multiple mining operations. This network streamlined the transportation of ore to the processing facility, enhancing efficiency and significantly reducing operational costs.
- The Indonesian Coal Mine Conveyor and Crushing System: An Indonesian coal mine integrated a conveyor system with a crushing facility, enabling direct loading of crushed coal onto the conveyors for transport to the shipping terminal. This integration not only improved productivity but also reduced coal handling costs and minimized environmental pollution.
Impact on Mining Operations
- Increased Productivity: Each of these case studies demonstrates how advanced conveyor systems can lead to a substantial increase in mining operations’ productivity by enabling continuous and efficient material handling.
- Cost-Efficiency: The reduction in reliance on truck haulage and the integration of conveyor systems with processing operations have led to significant savings in operational costs, including fuel, maintenance, and labor expenses.
- Environmental Sustainability: By minimizing the environmental footprint through reduced emissions and landscape disruption, these conveyor systems exemplify the mining industry’s move towards more sustainable practices.
- Enhanced Safety: The implementation of these systems has also contributed to safer working conditions by reducing the need for manual handling of materials and decreasing the number of vehicles required for transport within the mine.
- Operational Reliability: The case studies highlight the reliability of modern mining conveyor equipment, even in extreme conditions, ensuring consistent operation and reducing unexpected downtime.
These case studies of successful applications of mining conveyor equipment across various global locations underscore the transformative impact of these systems on the mining industry. By enhancing productivity, ensuring cost-efficiency, and promoting environmental sustainability, advanced conveyor systems continue to play a pivotal role in the evolution of mining operations.

Innovations in Mining Conveyor Equipment
The mining industry has seen a wave of innovations in mining conveyor equipment, aimed at enhancing performance, reducing downtime, and ensuring safety. These advancements include sophisticated belt monitoring systems, efficient conveyor belt cleaning systems, and advanced splicing technologies. Each innovation plays a crucial role in optimizing the operation of conveyor systems, making them more reliable and efficient.
Latest Innovations and Their Applications
Belt Monitoring Systems:
- Integrated Sensors: Sensors embedded along the conveyor belt monitor its health in real-time, detecting wear, tears, and misalignments.
- Wireless Monitoring: Wireless technology allows for remote monitoring of conveyor belt performance, facilitating timely maintenance decisions.
- Predictive Maintenance Software: Advanced software analyzes data from belt monitoring systems to predict potential failures before they occur.
- Thermal Imaging Cameras: These cameras detect overheating components along the conveyor system, preventing potential fires.
- Drone Inspections: Drones equipped with cameras and sensors offer a comprehensive overview of conveyor belt conditions, even in inaccessible areas.
Conveyor Belt Cleaning Systems:
- Air Knife Systems: These systems use a high-velocity air stream to remove dust and small particles from the conveyor belt surface.
- Motorized Brush Cleaners: Rotating brushes effectively clean conveyor belts, especially in removing sticky materials.
- Water Spray Systems: Utilized for both cleaning and dust suppression, these systems help maintain belt cleanliness and environmental compliance.
- Scrapers with Smart Pressure Adjustment: Automatically adjusting scrapers maintain optimal pressure against the belt for efficient cleaning without causing damage.
- Ultrasonic Cleaning Systems: These systems use high-frequency sound waves to clean belts, ideal for sensitive conveyor materials.
Splicing Technologies:
- Laser Splicing: Precision laser technology ensures accurate and strong splicing of conveyor belts, reducing splice-related downtime.
- Hot Vulcanization with Control Systems: Advanced control systems regulate temperature and pressure during hot vulcanization, improving splice quality.
- Cold Bonding Solutions: Improved adhesives and materials make cold bonding a viable alternative for quick and reliable belt repairs.
- Mechanical Fastening Devices: New designs in mechanical fasteners provide stronger and more reliable belt joints, suitable for heavy-duty applications.
- Seamless Splicing Techniques: Techniques that create virtually seamless splices reduce wear on pulleys and rollers, extending the life of the conveyor belt.
Impact on Performance, Downtime, and Safety
These innovations in mining conveyor equipment significantly contribute to the overall efficiency and safety of mining operations. Belt monitoring systems enable early detection of issues, allowing for preventive maintenance and reducing unexpected downtime. Conveyor belt cleaning systems ensure the belt operates efficiently, preventing material buildup that can lead to belt misalignment or failure. Advanced splicing technologies provide stronger, more reliable belt joints, reducing the risk of belt separation and accidents.
By optimizing conveyor belt performance, these innovations not only reduce operational downtime but also enhance the safety of the mining environment. The ability to monitor, clean, and repair conveyor belts effectively ensures that mining operations can maintain continuous, efficient, and safe material handling processes. As the mining industry continues to evolve, these advancements in conveyor technology play a pivotal role in supporting the sector’s growth and sustainability.
FAQs About Mining Conveyor Equipment
Conveyor systems in mining are integral components for the transportation of materials across various sections of a mine. They facilitate the efficient and continuous movement of bulk materials such as ores, coal, and other extracted resources from the mining site to processing plants or loading areas. These systems significantly reduce the reliance on heavy truck haulage, thereby lowering operational costs, minimizing environmental impact, and enhancing safety by reducing traffic within the mine.
Mining conveyor systems can vary widely in design, complexity, and size, tailored to the specific needs of the mining operation. They can range from short distance conveyors moving materials from the mining face to the primary crusher, to long-distance, high-capacity conveyors capable of transporting materials over kilometers from deep underground mines to the surface. The choice of a conveyor system in mining is influenced by factors such as the material to be transported, the mine’s layout, the mining method, and environmental considerations. By automating the material transport process, conveyor systems also contribute to increased productivity and efficiency in mining operations, making them a critical component of modern mining infrastructure.
In mining, conveyor belts are made from a variety of materials, each selected for durability, strength, and suitability to the environment and type of material being transported. The most common materials include:
Rubber: Often reinforced with metal or fabric layers known as carcasses, rubber conveyor belts are widely used due to their durability, flexibility, and resistance to abrasion and impact. Special compounds can be added to the rubber to enhance resistance to oils, chemicals, and heat.
PVC (Polyvinyl Chloride): PVC conveyor belts are used in mining operations that don’t involve excessive heat or abrasiveness. These belts are lighter than rubber belts but still offer good resistance to chemicals and abrasion.
Steel: For the most demanding mining applications, especially in underground mining, steel conveyor belts offer unmatched durability and capacity to withstand harsh conditions, including exposure to heat, heavy loads, and sharp objects.
Nylon and Polyester: Synthetic fabrics like nylon and polyester are used as carcass materials in conveyor belts to provide strength and resistance to stretching. These materials are often used in combination with rubber coverings to balance strength and flexibility.
The choice of material for a conveyor belt in mining is critical and depends on factors such as the type of mine (open pit or underground), the material being transported, environmental conditions, and the distance over which the material must be moved.
In the context of mining and industrial applications, conveyors can be broadly classified into three types based on their functionality and design:
Belt Conveyors: The most common type of conveyor, belt conveyors consist of a continuous belt made from a variety of materials (including rubber, PVC, or metal) that moves over a series of rollers. They are used to transport materials over both short and long distances, horizontally or at inclines.
Roller Conveyors: These conveyors use a series of rollers mounted on a frame to move goods. Roller conveyors are typically used for handling solid items or packages and are not as common in bulk material handling in mining as belt conveyors. However, they can be used for specific tasks such as moving heavy equipment or parts within a processing plant.
Chain Conveyors: Chain conveyors use a chain or multiple chains to move pallets or other large, heavy items. In mining, they are often used for moving large quantities of bulk materials in a controlled flow along a predetermined path, and they are especially useful for heavy or abrasive materials that might damage other types of conveyors.
Each type of conveyor has its own set of advantages and is chosen based on the specific requirements of the mining operation, including the nature of the material to be transported, the distance, and the operational environment.
The gear used in a conveyor system is critical for its operation, ensuring the movement of the belt or chain and the control of speed and torque. Key components include:
Motors: Electric motors provide the power needed to drive the conveyor belt or chain. The size and type of motor depend on the conveyor’s size, the weight of the materials being transported, and the speed at which the materials need to move.
Gearboxes: Also known as gear reducers, these are used to reduce the speed of the motor to the desired speed of the conveyor belt. They also increase the torque available to drive the conveyor, allowing it to move heavy loads.
Drive Units: These include the motor and gearbox and are the primary source of power transmission to the conveyor belt or chain. Drive units are strategically placed along the conveyor system to ensure efficient operation.
Pulleys and Rollers: These components guide and support the conveyor belt, maintaining tension and facilitating smooth and efficient movement of materials.
Bearings: Bearings are used in various parts of the conveyor system, including rollers and pulleys, to ensure smooth rotation and to reduce friction and wear.
Control Systems: Modern conveyors are often equipped with sophisticated control systems that allow for the adjustment of speed, monitoring of system performance, and integration with other operational processes for optimized efficiency.
The selection and maintenance of the gear used in a conveyor system are crucial for its reliability, efficiency, and longevity, directly impacting the productivity of mining operations.
In coal mining, the most commonly used type of conveyor is the belt conveyor. Belt conveyors are preferred for their efficiency, durability, and ability to handle large volumes of coal. These conveyors consist of a continuous belt made of rubber or other materials, which is supported by rollers and powered by motors. Belt conveyors can cover long distances, navigate through various terrain and inclines, and operate in harsh mining environments. They are designed to transport coal from the mining site to processing plants, storage facilities, or directly to transport systems such as trains or ships. Additionally, they can be customized with various accessories like impact rollers, scrapers, and conveyor covers to enhance performance and safety. Overall, belt conveyors play a crucial role in streamlining coal mining operations by ensuring a steady and efficient flow of material.
Last Updated on July 11, 2024 by Jordan Smith
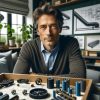
Jordan Smith, a seasoned professional with over 20 years of experience in the conveyor system industry. Jordan’s expertise lies in providing comprehensive solutions for conveyor rollers, belts, and accessories, catering to a wide range of industrial needs. From initial design and configuration to installation and meticulous troubleshooting, Jordan is adept at handling all aspects of conveyor system management. Whether you’re looking to upgrade your production line with efficient conveyor belts, require custom conveyor rollers for specific operations, or need expert advice on selecting the right conveyor accessories for your facility, Jordan is your reliable consultant. For any inquiries or assistance with conveyor system optimization, Jordan is available to share his wealth of knowledge and experience. Feel free to reach out at any time for professional guidance on all matters related to conveyor rollers, belts, and accessories.