Mining Conveyor Parts: Durability and Performance
In the mining industry, conveyor systems stand as the lifeline of operations, facilitating the swift and efficient movement of materials across various stages of the mining process. From extraction to processing and finally to the delivery of the minerals, these systems rely heavily on a myriad of mining conveyor parts to maintain their functionality and efficiency. Each component, from belts to rollers, idlers, and motors, plays a pivotal role in the seamless operation of the conveyor system. The durability and performance of these parts are paramount, as they directly impact the productivity and safety of mining operations. Understanding the intricacies of mining conveyor parts is not just about recognizing their functionality but also about appreciating their contribution to the overall success of mining activities. As such, the selection, maintenance, and optimization of these parts are crucial aspects that demand attention and expertise to ensure the uninterrupted flow of operations within the mining sector.
What is Mining Conveyor Parts
Delving into the realm of mining conveyor parts reveals a complex array of components, each serving a unique and indispensable function within the conveyor system. These parts ensure the smooth, efficient, and continuous flow of materials, which is critical in the high-stakes environment of mining operations.
Mining Conveyor Parts List:
At the heart of these systems lie several key components. For instance, conveyor belts are the moving platforms that carry ore and other materials. Idlers are cylindrical rods that support the belt and the material being transported. Rollers facilitate the belt’s movement with minimal friction, and scrapers keep the belts clean from any debris that might stick to them and hinder their operation. Each of these parts is engineered to withstand the harsh conditions of mining environments, from abrasive materials to extreme weather.
Types of Conveyor Belts Used in Mining:
The choice of conveyor belt is critical, as it must be suited to the type of material being transported and the conditions of the mining site. Fabric belts, made from layers of fabric coated with rubber, are commonly used for their flexibility and durability. Steel-cord belts are preferred for their high strength and long-distance capabilities, essential in large-scale mining operations. Heat-resistant belts are designed to withstand high temperatures, ideal for transporting hot materials. Oil-resistant belts prevent the belt from degrading in oily environments. Fire-resistant belts are crucial in coal mining to reduce the risk of fire hazards. Lastly, specialty belts with unique features like rip detection and energy-saving properties are also employed to meet specific mining requirements.
Understanding these mining conveyor parts and the types of belts used is not just about ensuring the operational efficiency of the conveyor systems but also about maximizing safety, reducing downtime, and optimizing the overall productivity of mining operations.
Sourcing Mining Conveyor Parts
The process of sourcing mining conveyor parts is a critical aspect of maintaining and optimizing the efficiency of conveyor systems in the mining industry. It involves not only finding the right components that meet the specific requirements of the mining operations but also ensuring that these parts are of high quality, compatible with existing systems, and durable enough to withstand the harsh mining environment.
Used Mining Conveyor Parts:
Opting for used mining conveyor parts can be a cost-effective and sustainable choice for many mining operations. The benefits include lower costs and reduced environmental impact due to recycling parts. However, it’s essential to consider the wear and tear on these parts and ensure they meet safety and operational standards before integration into existing systems.
Mining Conveyor Parts Catalog:
Utilizing a mining conveyor parts catalog is an efficient way to identify and select the necessary components for your conveyor system. These catalogs typically provide detailed information about each part, including specifications, compatibility, and application guidelines, making it easier to find the exact parts needed for specific conveyor models and functions.
Mining Conveyor Parts Near Me:
Finding reliable suppliers and service providers nearby can significantly reduce downtime when parts need replacement or maintenance. Look for suppliers with a strong reputation in the mining industry, offering a wide range of parts from belts to rollers and idlers. Consider those who provide on-site support and maintenance services, have a comprehensive inventory of parts, and offer custom fabrication services to meet specific needs. Networking with industry peers and attending mining expos can also connect you with reputable suppliers in your area.
Mining Conveyor Parts for Sale:
When purchasing new mining conveyor parts, focus on quality, compatibility with your existing system, and the durability of the parts. High-quality materials and construction are crucial for parts that will be exposed to abrasive materials, heavy loads, and extreme conditions. Compatibility ensures that the new parts will integrate seamlessly with your existing conveyor system, avoiding operational issues. Durability is essential for minimizing maintenance requirements and extending the lifespan of the conveyor system. Look for suppliers who offer warranties, technical support, and have a proven track record in the mining industry.
Sourcing the right mining conveyor parts is a strategic process that impacts the efficiency, safety, and longevity of conveyor systems in mining operations. By carefully selecting used or new parts, utilizing catalogs, finding reputable local suppliers, and focusing on quality and compatibility, mining operations can ensure their conveyor systems operate smoothly and reliably.
Key Suppliers and Manufacturers of Mining Conveyor Parts
In the realm of mining conveyor parts, the role of key suppliers and manufacturers cannot be overstated. These entities are the backbone of the mining conveyor system, providing the essential components that ensure operational efficiency, safety, and reliability.
Mining Conveyor Belt Manufacturers:
Among the leading manufacturers in the mining conveyor belt sector, companies like Fenner Dunlop, Bridgestone, ContiTech, and Bando stand out for their commitment to quality and innovation. Fenner Dunlop is renowned for its engineered conveyor solutions, designed to withstand the most challenging mining environments. Bridgestone offers high-quality, durable belts that are tailored to meet specific mining applications. ContiTech is recognized for its innovative conveyor belt technology, including high-strength fabric and steel cord belts. Bando excels in producing energy-efficient, high-performance conveyor belts that reduce operational costs and environmental impact.
West River Conveyors:
As a prominent player in the mining conveyor parts market, West River Conveyors specializes in providing custom-built conveyor systems and parts. Their offerings include robust conveyor belts designed for mining applications, durable rollers and idlers that ensure smooth operation, advanced motorized pulleys that enhance system efficiency, and reliable gearboxes engineered for the demanding conditions of mining operations. West River Conveyors’ commitment to quality, innovation, and customer service makes them a go-to source for mining companies seeking reliable conveyor solutions.
These key suppliers and manufacturers of mining conveyor parts play a pivotal role in the mining industry, offering products that meet the highest standards of quality and innovation. Their contributions not only ensure the smooth functioning of conveyor systems but also drive advancements in conveyor technology, making mining operations more efficient, safe, and sustainable.
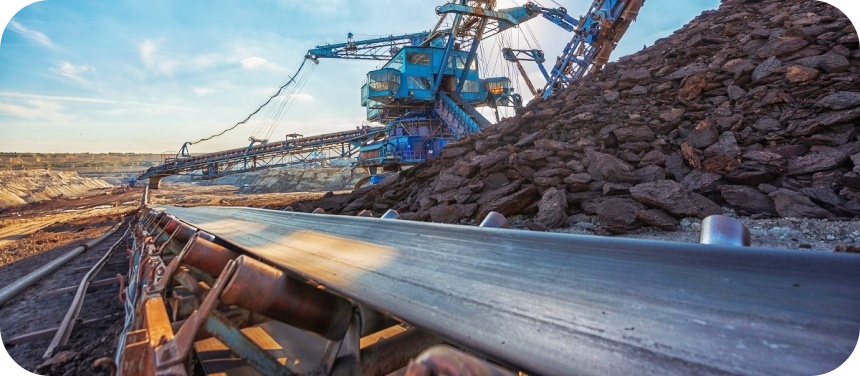
Advanced Conveyor Technologies in Mining Conveyor Parts
The mining industry continually seeks advancements in conveyor technologies to enhance efficiency, safety, and sustainability. These innovations in mining conveyor parts address the unique challenges posed by different mining environments, particularly in underground settings and in applications requiring flexible material handling solutions.
Underground Mining Conveyor System:
The underground mining environment presents distinct challenges such as limited space, harsh conditions, and the need for high safety standards. Advanced mining conveyor parts for these systems include self-extinguishing belts that reduce fire risk, heavy-duty rollers designed to withstand harsh conditions, compact and modular belt designs that optimize space, and sensors and monitoring systems that enhance safety and efficiency by detecting potential issues before they lead to downtime or accidents.
Shuttle Conveyor Mining:
Shuttle conveyors offer a versatile solution for mining operations, allowing for the reversible movement of materials. Key advancements in shuttle conveyor mining include automated control systems for precise material placement, variable speed drives that adjust the conveyor speed according to the load, robust and durable design to withstand the mining environment, and integrated weighing systems that ensure accurate material tracking and inventory management.
Conveyor Belt Systems Mining PDF:
A wealth of information is available in PDF resources that delve into the intricacies of conveyor belt systems in mining. These documents often cover topics such as best practices for installation and maintenance, innovative design features that improve performance and safety, case studies highlighting successful implementations and the challenges overcome, and future trends in conveyor technology that could further transform mining operations.
These advanced conveyor technologies and mining conveyor parts not only address the specific needs of the mining industry but also pave the way for future developments that will continue to improve the efficiency, safety, and environmental impact of mining operations worldwide.
Maintenance and Optimization of Mining Conveyor Parts
The longevity and efficiency of mining conveyor systems are heavily reliant on regular maintenance and the strategic optimization of mining conveyor parts. Ensuring that these systems operate at peak efficiency not only minimizes downtime but also extends the life of the equipment, ultimately contributing to the overall productivity and safety of mining operations.
Conveyor Spare Parts:
A well-thought-out inventory of conveyor spare parts is crucial for minimizing operational disruptions. Key components to keep on hand include belts, to quickly replace sections that may suffer from wear or damage; rollers and idlers, which are essential for the smooth operation of the conveyor and can wear down over time; motors and gearboxes, as the driving force behind the conveyor system, their failure can halt operations; electrical components like sensors and switches, which are critical for the automated aspects of the system; scrapers, to maintain belt cleanliness and efficiency; and bearings, which ensure the smooth rotation of rollers and pulleys. Having these parts readily available can significantly reduce downtime caused by unexpected failures.
Maintaining Your Mining Conveyor System:
Routine maintenance and inspections are paramount for the longevity and efficiency of mining conveyor systems. Best practices include regularly scheduled inspections to identify and address wear and tear before it leads to major failures; cleaning protocols to prevent material buildup that can hinder conveyor efficiency and pose a safety risk; lubrication schedules for moving parts to reduce friction and wear; monitoring system performance through sensors and software to predict potential failures; and training for personnel on the proper operation and maintenance procedures to ensure that the system is used and maintained correctly. Additionally, implementing a maintenance management system can help track maintenance activities, spare part inventories, and system performance, further optimizing the operation of mining conveyor systems.
By prioritizing the maintenance and optimization of mining conveyor parts, mining operations can ensure the reliability and efficiency of their conveyor systems, thereby enhancing overall productivity and safety.
Submit your request for conveyor belt options and pricing.
FAQs About Mining Conveyor Parts
Conveyors, integral to various industries for material handling, consist of several key parts. The belt is the surface on which materials are placed for transport. Pulleys, typically found at either end of the conveyor, drive the belt and control its tension. Rollers support the belt and help guide materials along the conveyor path. The motor provides the necessary power to drive the pulley and move the belt. Frames support the entire structure, ensuring stability and durability. Understanding these components is crucial for maintenance and troubleshooting.
A conveyor structure is designed to support and facilitate the smooth operation of the conveyor system. Key components include the frame, which provides the structural support, and is often made from materials like steel or aluminum for durability. Support legs or stands keep the conveyor at the desired height. Guide rails ensure materials stay on the conveyor and prevent spillage. Loading and discharge points are tailored to the specific needs of the operation, ensuring efficient material transfer. The integration of these components ensures the conveyor’s effectiveness and longevity.
In mining, conveyor systems are pivotal for the efficient and safe transport of materials such as coal, ore, and overburden. They are used in various stages of mining operations, from extraction to processing and waste disposal. Overland conveyors transport material over long distances, connecting different parts of a mining site. Underground conveyors navigate through mine shafts, facilitating material movement without disrupting surface activities. Stacker conveyors are used for creating large stockpiles of materials, optimizing space and managing resources effectively. These systems reduce reliance on truck haulage, lowering operational costs and environmental impact.
Conveyors can be broadly categorized into three types based on their functionality and application. Belt conveyors are the most common, consisting of a continuous belt that transports materials between two end points. They are versatile and can be used for a range of materials. Roller conveyors use a series of rollers to move goods, ideal for heavy or bulky items that require stable support. Overhead conveyors are mounted above the ground, saving floor space and are typically used in industrial applications for moving parts through production processes. Each type offers unique advantages, catering to different industry needs.
Last Updated on August 5, 2024 by Jordan Smith
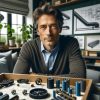
Jordan Smith, a seasoned professional with over 20 years of experience in the conveyor system industry. Jordan’s expertise lies in providing comprehensive solutions for conveyor rollers, belts, and accessories, catering to a wide range of industrial needs. From initial design and configuration to installation and meticulous troubleshooting, Jordan is adept at handling all aspects of conveyor system management. Whether you’re looking to upgrade your production line with efficient conveyor belts, require custom conveyor rollers for specific operations, or need expert advice on selecting the right conveyor accessories for your facility, Jordan is your reliable consultant. For any inquiries or assistance with conveyor system optimization, Jordan is available to share his wealth of knowledge and experience. Feel free to reach out at any time for professional guidance on all matters related to conveyor rollers, belts, and accessories.