Mining Conveyor Belt Rollers: Types and Unique Benefits
In the heart of the mining industry, conveyor belt rollers stand as the unsung heroes, ensuring the smooth flow of operations deep within the earth’s crust. These rollers, integral to the conveyor systems, bear the heavy burden of transporting vast quantities of materials across the mining sites, from the extraction points to the processing areas. The efficiency and reliability of mining conveyor belt rollers are paramount, as they directly influence the operational tempo and the overall productivity of mining ventures. Their role extends beyond mere transportation; they contribute to the safety, durability, and cost-effectiveness of the mining operations. Understanding the pivotal role of these rollers helps in appreciating the complex orchestration required to sustain the demanding environment of mining conveyance, making them indispensable assets in the pursuit of mineral extraction and processing.
What are Mining Conveyor Belt Rollers
Mining conveyor belt rollers are critical components in the vast network of conveyance systems that facilitate the efficient movement of materials within mining operations. These rollers, positioned along the length of the conveyor belt, play a pivotal role in supporting and propelling the belt forward, laden with mined materials such as coal, minerals, and ores. The seamless operation of these rollers is essential for the uninterrupted flow of materials, contributing significantly to the productivity and efficiency of mining processes.
The Role of Mining Conveyor Belt Rollers

Mining conveyor belt rollers serve a dual purpose: they provide support to the conveyor belt and ensure the smooth transportation of materials across the mining site. These rollers are strategically placed beneath the belt to prevent sagging and reduce the tension and stress exerted on the belt itself. By doing so, they minimize the risk of belt misalignment and potential breakdowns, which are critical in maintaining the continuous operation of mining activities.
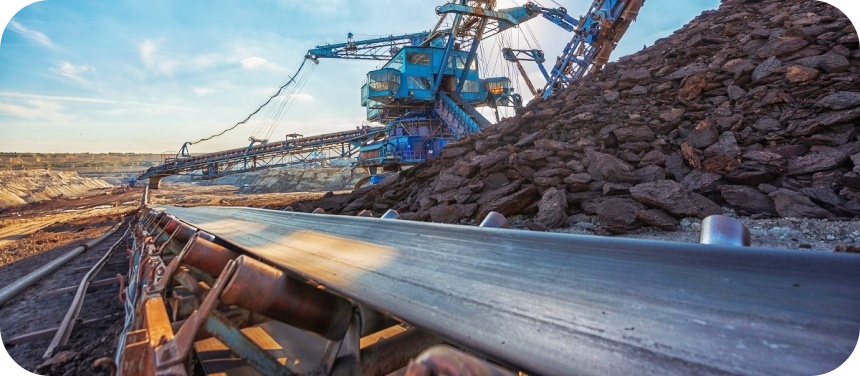
Importance of Quality and Reliability
In the harsh and demanding environment of mining operations, the quality and reliability of conveyor belt rollers cannot be overstated. Here are eight reasons why high-quality and reliable mining conveyor belt rollers are indispensable:
- Durability: High-quality rollers are designed to withstand the abrasive nature of mined materials and the extreme conditions of mining environments, ensuring longevity and reducing the need for frequent replacements.
- Efficiency: Reliable rollers contribute to the optimal performance of conveyor systems, ensuring materials are moved swiftly and smoothly, thereby enhancing overall operational efficiency.
- Reduced Downtime: Quality rollers have a lower failure rate, which significantly reduces downtime caused by maintenance and repairs, keeping productivity levels high.
- Cost Savings: Investing in high-quality rollers may have a higher initial cost, but it leads to significant savings in the long run by reducing maintenance costs and minimizing the potential for costly operational disruptions.
- Safety: Reliable rollers contribute to the safety of mining operations by reducing the risk of accidents associated with conveyor belt malfunctions.
- Energy Efficiency: High-quality rollers are designed to minimize friction and resistance, which in turn reduces the energy consumption of conveyor systems.
- Noise Reduction: Quality rollers are engineered to operate quietly, contributing to a better working environment and complying with noise regulations.
- Customization and Adaptability: High-quality mining conveyor belt rollers can be customized to meet the specific requirements of different mining operations, ensuring compatibility and optimal performance under varying conditions.
Mining conveyor belt rollers are fundamental to the efficiency and productivity of mining operations. Their role in supporting and propelling conveyor belts, laden with valuable materials, underscores the necessity for quality and reliability in their design and manufacture. By prioritizing these aspects, mining operations can achieve smoother, safer, and more cost-effective material handling processes.
Types of Mining Conveyor Belt Rollers
Mining conveyor belt rollers are essential components of the conveyor system, each type designed to fulfill a specific function within the mining operation. Understanding the variety and purpose of these rollers is crucial for optimizing the conveyor’s performance and longevity. Below is a detailed overview of the different types of mining conveyor belt rollers:
Each type of mining conveyor belt roller plays a specific role in the overall efficiency and safety of the conveyor system. From supporting and aligning the belt to absorbing impacts and maintaining cleanliness, these rollers are integral to the smooth operation of mining conveyance systems. Selecting the appropriate type and quality of rollers is essential for optimizing the performance and longevity of the conveyor system in the demanding environment of mining operations.
Innovative Technologies in Mining Conveyor Belt Rollers
The conveyor belt for mining industry continually seeks advancements in technology to enhance the efficiency, safety, and longevity of its operations. This pursuit of innovation extends to the development of mining conveyor belt rollers, where new materials and designs are being employed to meet the challenging demands of mining environments. Here’s a closer look at some of the innovative roller technologies that are setting new standards in the mining sector:
PROK Hybrid Steel Roller
The PROK Hybrid Steel Roller is a testament to the innovation in mining conveyor belt rollers, designed to offer the best of both worlds: the strength of steel and the corrosion resistance often associated with alternative materials. This hybrid construction makes it an ideal choice for operations in harsh mining environments where rollers are exposed to extreme wear and tear. The steel core provides the necessary strength to withstand heavy loads, while the corrosion-resistant coating ensures longevity and reliability, even in the presence of abrasive materials and corrosive elements.
PROK HDPE Composite Roller
In response to the industry’s need for lighter and more durable solutions, the PROK HDPE Composite Roller was developed. Constructed from high-density polyethylene (HDPE), these rollers are significantly lighter than their steel counterparts, making them easier to handle and install. Despite their lightweight nature, HDPE rollers are incredibly wear-resistant and are designed to operate with low noise, making them an environmentally friendly option for mining operations. Their resistance to corrosion and abrasion also means they are well-suited to the challenging conditions of mining environments.
Polyurethane Disc Roller
The Polyurethane Disc Roller introduces an innovative approach to preventing material buildup on the roller surface, a common issue in mining conveyance that can lead to operational inefficiencies and increased maintenance requirements. The roller is equipped with abrasion-resistant polyurethane discs that actively resist material adhesion, ensuring the roller remains clean and functional. This not only enhances the lifespan of the roller but also contributes to the smooth operation of the conveyor system.
Rubber Disc and Formed Steel Rollers
Addressing the issue of high material carryback, Rubber Disc and Formed Steel Rollers offer a robust solution. These rollers are designed with rubber discs or formed steel surfaces that effectively dislodge and repel materials that might otherwise adhere to the roller. This design feature is particularly beneficial in applications where sticky or wet materials are being conveyed. The durability and efficiency provided by these rollers make them a valuable addition to any mining conveyor system, ensuring reliable operation and reduced maintenance needs.
The introduction of these innovative mining conveyor belt rollers represents a significant step forward in the optimization of conveyor systems within the mining industry. By incorporating advanced materials and designs, these rollers offer enhanced performance, durability, and efficiency, meeting the evolving needs of modern mining operations.
Selecting the Right Mining Conveyor Belt Rollers
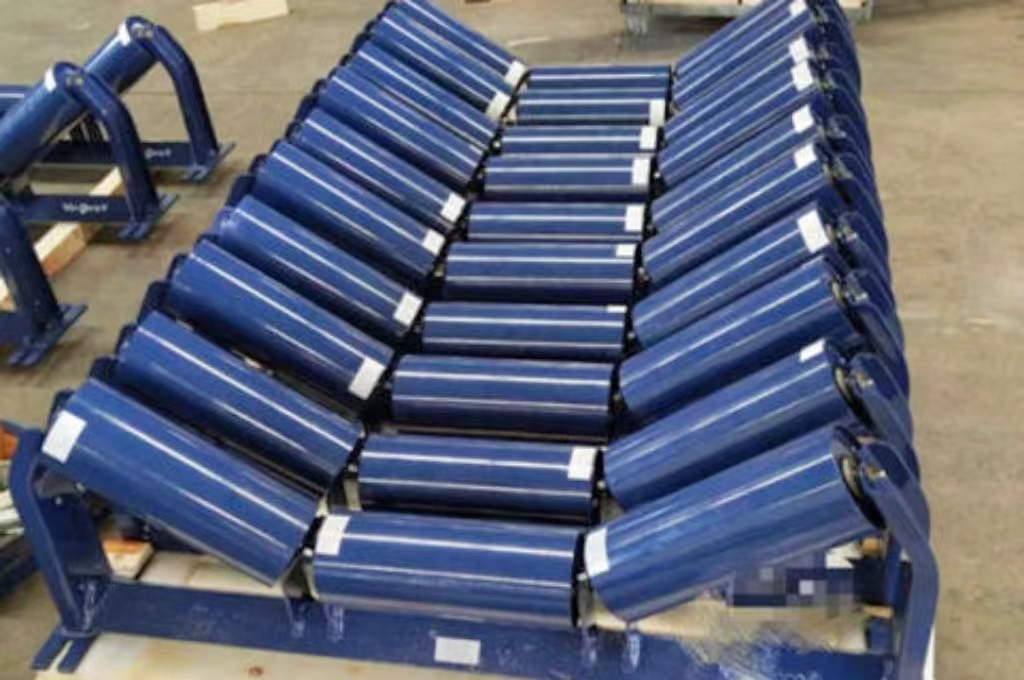
Choosing the appropriate mining conveyor belt rollers is a critical decision that significantly impacts the efficiency, longevity, and safety of mining conveyor systems. Given the diverse and challenging environments in which these systems operate, selecting the right rollers requires careful consideration of various factors. Here are ten key factors to consider and six reasons why selecting rollers based on application-specific requirements is crucial:
Factors to Consider
- Operating Environment: The environmental conditions such as temperature, humidity, and exposure to corrosive substances can affect roller performance and lifespan.
- Material Type: The type of materials being conveyed (e.g., abrasive, corrosive, fine, or large lump size) directly influences the choice of conveyor roller material and design.
- Conveyor Speed: Higher conveyor speeds may require conveyor rollers designed for reduced rotational resistance and enhanced durability. Regular conveyor roller repair is also essential to maintain optimal performance.
- Load Capacity: The weight of the conveyed materials necessitates rollers that can withstand the load without deforming or failing.
- Belt Width and Length: The dimensions of the conveyor belt determine the required roller size and spacing to ensure adequate support and minimize belt sag.
- Troughing Angle: The angle of troughed idler rollers must be compatible with the belt to ensure proper material containment and transport efficiency.
- Impact Zones: Areas where materials are loaded onto the conveyor might need impact rollers designed to absorb shocks and protect the belt.
- Moisture and Contaminants: Presence of water, oils, or other contaminants requires rollers with appropriate sealing and conveyor belt material properties to resist degradation.
- Maintenance and Accessibility: Consideration for ease of maintenance and replacement can influence roller design and material choice.
- Regulatory and Safety Requirements: Compliance with industry standards and safety regulations may dictate specific roller features or materials.
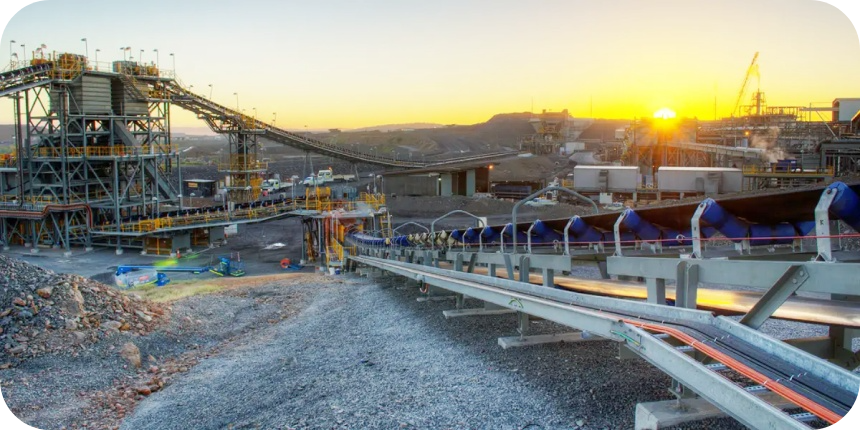
Importance of Application-Specific Selection
- Enhanced Efficiency: Rollers chosen for their suitability to the specific application ensure optimal conveyor performance, reducing energy consumption and improving material handling speed.
- Extended Lifespan: Application-specific rollers are designed to withstand the particular stresses and wear conditions of the operation, leading to longer service life and fewer replacements.
- Reduced Maintenance: Selecting the right rollers minimizes the risk of failures and maintenance requirements, thereby reducing downtime and maintenance costs.
- Improved Safety: Rollers that are well-suited to the application and environment reduce the risk of malfunctions and accidents, enhancing overall workplace safety.
- Cost-Effectiveness: While the initial investment in high-quality, application-specific rollers might be higher, the long-term savings in maintenance, replacements, and improved efficiency can be substantial.
- Customization Opportunities: Choosing rollers based on specific requirements allows for customization that can address unique challenges of the mining operation, such as extreme temperatures, high load capacities, or abrasive materials.
The selection of mining conveyor belt rollers is a complex process that requires careful consideration of numerous factors related to the operational environment, material characteristics, and conveyor specifications. By prioritizing application-specific requirements, mining operations can achieve higher efficiency, safety, and cost-effectiveness in their material handling processes.
Manufacturers and Suppliers of Mining Conveyor Belt Rollers
The market for mining conveyor belt rollers is served by a variety of manufacturers and suppliers worldwide, each bringing unique innovations, quality standards, and services to the industry. Among these, several key players stand out due to their reputation, product range, and commitment to quality and innovation. Here’s an overview of eight leading manufacturers in the field and the importance of consulting their detailed product catalogues for making informed decisions.
Leading Manufacturers
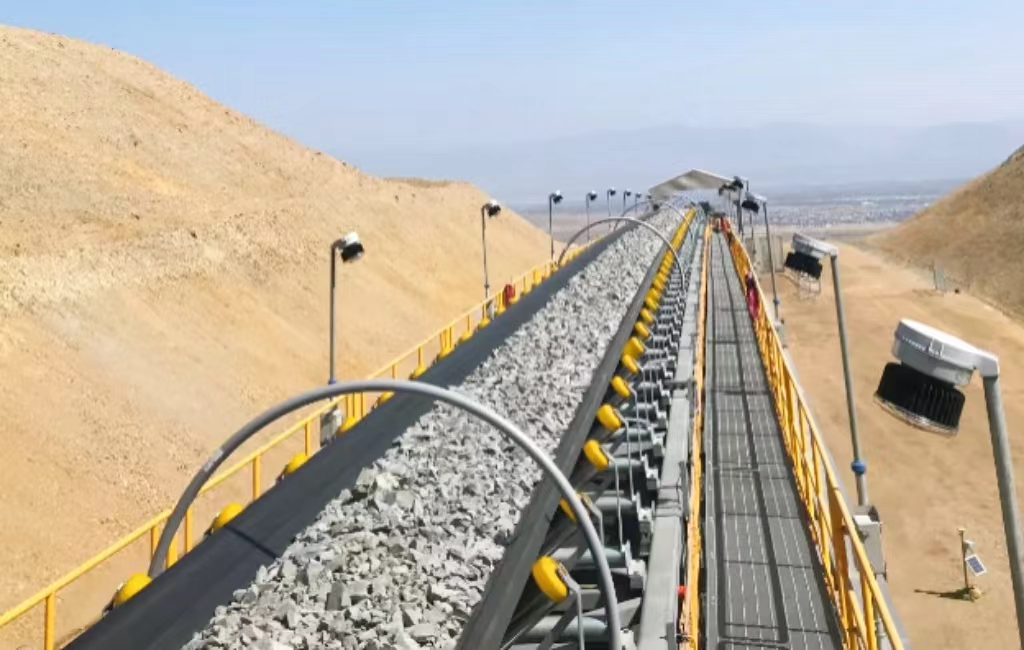
- Rulmeca: Renowned for its robust and high-quality rollers, Rulmeca offers products designed for heavy-duty mining applications. What sets Rulmeca apart is their emphasis on energy-efficient, durable, and maintenance-friendly rollers, making them a preferred choice for mining operations globally.
- PROK: Specializing in high-performance conveyor components, PROK’s innovative solutions like the Hybrid Steel Roller and HDPE Composite Roller are tailored for the demanding conditions of the mining industry.
- Martin Engineering: Known for their focus on safety and efficiency, Martin Engineering produces conveyor rollers that reduce maintenance requirements and enhance operational safety.
- Sandvik: With a strong focus on research and development, Sandvik provides cutting-edge roller solutions that are designed to improve the reliability and efficiency of mining conveyor systems.
- Continental Conveyor: Offering a wide range of conveyor components, Continental Conveyor’s rollers are known for their quality and durability, suitable for various mining applications.
- Precision Pulley & Idler (PPI): PPI is recognized for its comprehensive range of conveyor components, including idlers and rollers that cater to the specific needs of the mining sector.
- Fenner Dunlop: Specializing in conveyor belting, Fenner Dunlop also offers a range of rollers that are engineered for optimal performance in mining environments.
- Melco Conveyor Equipment: Based in South Africa, Melco manufactures high-quality conveyor rollers that are designed to withstand the harsh conditions of mining operations.
Importance of Consulting Manufacturers’ Catalogues
When selecting mining conveyor belt rollers, consulting the manufacturers’ catalogues, such as the Rulmeca rollers catalogue PDF, is crucial for several reasons:
- Detailed Product Specifications: Catalogues provide comprehensive details about the specifications, dimensions, materials, and capabilities of each roller type, helping buyers make informed choices based on their specific requirements.
- Custom Solutions: Many manufacturers offer custom-engineered solutions to meet unique operational challenges. Catalogues often highlight these capabilities, showcasing the manufacturer’s ability to tailor products to specific needs.
- Innovation Highlights: Manufacturers use their catalogues to introduce new and innovative products. By reviewing these catalogues, buyers can stay informed about the latest advancements in roller technology.
- Quality Standards: Catalogues often detail the quality standards and certifications that the manufacturer adheres to, giving buyers confidence in the reliability and safety of the products.
- Technical Support and Services: Information about after-sales support, maintenance services, and warranty terms is typically included in catalogues, providing a complete overview of what to expect from the manufacturer beyond the purchase.
The selection of mining conveyor belt rollers is a critical decision that can significantly impact the efficiency and safety of mining operations. Leading manufacturers like Rulmeca offer a range of high-quality rollers designed to meet the rigorous demands of the mining industry. Consulting detailed product catalogues is an essential step in the selection process, ensuring that buyers have access to comprehensive information on product specifications, custom solutions, and technical support.
Pricing and Availability of Mining Conveyor Belt Rollers
The cost and availability of mining conveyor belt rollers can vary widely based on several factors. Understanding these variables is crucial for budgeting and planning purposes in mining operations. Below, we discuss eight key factors that influence the pricing of mining conveyor belt rollers and provide ten tips for securing the best deals, including options for both new and used rollers.
Factors Influencing Price
- Material Quality: High-grade materials such as specialized steels or composites typically command higher prices due to their durability and performance in harsh mining environments.
- Design Complexity: Rollers designed with advanced features for specific applications, such as self-cleaning or self-aligning capabilities, can be more expensive.
- Technological Advancements: Rollers incorporating the latest technology, such as sensors for monitoring wear and performance, may carry a premium.
- Size and Weight: Larger and heavier rollers, required for wide and high-capacity conveyor belts, often cost more due to the increased material and manufacturing efforts.
- Brand Reputation: Established brands known for quality and reliability might price their products higher, reflecting their market position and perceived value.
- Customization: Custom-engineered rollers designed to meet specific operational requirements can be more costly than standard off-the-shelf models.
- Quantity: Bulk orders may attract discounts, whereas smaller orders might have a higher per-unit cost due to fixed manufacturing and setup expenses.
- Market Demand and Availability: Fluctuations in demand and raw material availability can impact prices. Limited availability of certain materials or components may lead to higher prices.
Tips for Finding the Best Deals
- Request Multiple Quotes: Obtain quotes from several suppliers to compare prices and negotiate better terms.
- Consider Bulk Purchases: If possible, consolidate orders or plan for future needs to leverage bulk purchase discounts.
- Explore Different Brands: While established brands offer reliability, lesser-known manufacturers might provide competitive pricing for comparable quality.
- Look for Promotions and Discounts: Suppliers may offer seasonal promotions, clearance sales, or discounts on older models.
- Evaluate Total Cost of Ownership: Consider not just the purchase price but also the expected lifespan, maintenance costs, and efficiency gains.
- Check for Used or Refurbished Options: Quality used or refurbished rollers can offer significant savings, especially for operations with less demanding conditions.
- Engage in Long-Term Supplier Relationships: Building a long-term relationship with a supplier can lead to better pricing, priority availability, and customized service terms.
- Assess Compatibility with Existing Systems: Ensure that new rollers are compatible with existing conveyor systems to avoid additional costs for modifications.
- Consider Local Suppliers: Local suppliers can offer competitive pricing and lower shipping costs, along with easier access to service and support.
- Stay Informed About Market Trends: Understanding market trends can help anticipate price fluctuations and identify the best times to purchase.
The pricing and availability of mining conveyor belt rollers are influenced by a complex interplay of factors, including material quality, design complexity, and market dynamics. By carefully considering these factors and employing strategic purchasing practices, mining operations can secure the best deals on rollers, balancing cost with performance and reliability to optimize their conveyor systems.
Maintenance and Upkeep of Mining Conveyor Belt Rollers
Proper maintenance and upkeep are crucial for ensuring the operational efficiency and extending the lifespan of mining conveyor belt rollers. Given the harsh and demanding conditions of mining environments, a proactive approach to maintenance can prevent unexpected downtime and costly repairs. Here, we outline best practices for maintaining conveyor belt rollers and highlight the significance of regular inspections, cleaning, and timely replacements.
Best Practices for Maintenance
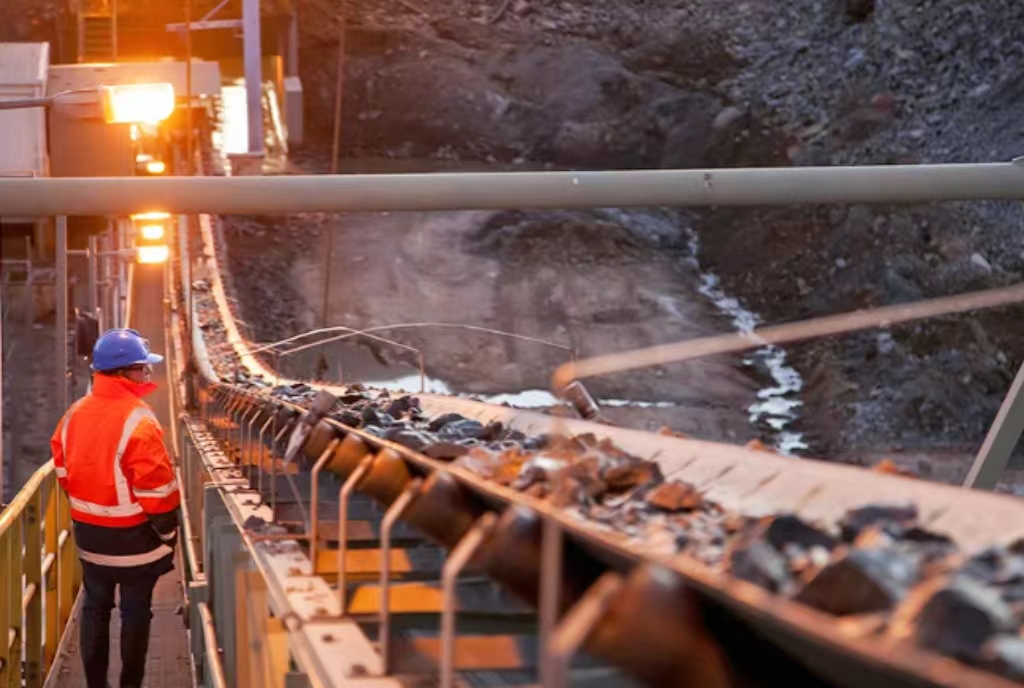
- Regular Inspections: Conduct routine inspections of conveyor belt rollers to identify signs of wear, damage, or misalignment early. This includes checking for smooth rotation, structural integrity, and proper alignment of the rollers.
- Scheduled Cleaning: Accumulation of dust, debris, and residues can impair roller function and lead to premature wear. Implement a regular cleaning schedule to remove any materials that could hinder roller performance.
- Lubrication: Ensure that rollers with bearings or moving parts are adequately lubricated according to the manufacturer’s recommendations. Proper lubrication reduces friction, wear, and the risk of overheating.
- Alignment Checks: Misaligned rollers can cause uneven wear and tear on the conveyor belt and the rollers themselves. Regularly check and adjust the alignment of rollers to ensure smooth and efficient operation.
- Monitoring Load Capacity: Overloading the conveyor can lead to increased stress and wear on the rollers. Monitor and adhere to the recommended load capacities to prevent overburdening the system.
- Environmental Protection: In particularly harsh mining environments, consider additional protective measures such as covers or guards to shield rollers from extreme conditions and contaminants.
- Replacement of Worn Parts: Do not delay the replacement of worn or damaged rollers. Promptly replacing defective rollers helps maintain the integrity of the conveyor system and prevents further damage.
- Use of Quality Spare Parts: When replacements are necessary, use high-quality spare parts that meet or exceed the original specifications to ensure compatibility and reliability.
- Training for Maintenance Staff: Ensure that maintenance personnel are adequately trained in the proper care, inspection, and troubleshooting of conveyor belt rollers. Knowledgeable staff can identify and address issues more effectively.
- Record Keeping: Maintain detailed records of maintenance activities, inspections, and replacements. This documentation can help identify recurring issues and inform future maintenance practices.
Need conveyor belt rollers? Contact us for the best options!
Significance of Regular Inspections, Cleaning, and Replacements
Regular inspections and cleaning are fundamental to the proactive maintenance of mining conveyor belt rollers. These practices allow for the early detection of potential issues, preventing minor problems from escalating into major failures. Inspections can reveal signs of wear, corrosion, misalignment, or damage, enabling timely interventions that can avert operational disruptions.
Cleaning plays a vital role in maintaining roller efficiency, removing materials that could cause blockages, imbalances, or additional wear. A clean conveyor system operates more smoothly and is less likely to suffer from unexpected breakdowns.
Timely replacement of rollers that are worn or damaged is equally important. Delaying replacements can lead to further damage to the conveyor belt, increased energy consumption, and the risk of operational halts. Using quality spare parts for replacements ensures that the conveyor system retains its integrity and continues to operate at optimal efficiency.
Diligent maintenance and upkeep of mining conveyor belt rollers are essential for maintaining the efficiency, safety, and longevity of conveyor systems in mining operations. By adhering to best practices for inspections, cleaning, and replacements, mining operations can achieve reliable and continuous material handling processes, minimizing downtime and maximizing productivity.
FAQs about Mining Conveyor Belt Rollers
The type of roller used for a conveyor belt largely depends on the specific requirements of the conveyor system, including the material being transported, the environment in which the conveyor operates, and the load it must bear. Common types include troughed idler rollers, used for bulk material handling with a groove shape to cradle the material; impact rollers, placed at loading points to absorb shock and protect the belt; and return rollers, which support the return path of the belt. For precise belt tracking and alignment, self-aligning rollers are used. The choice of roller material, such as steel, composite, or rubber, also varies based on the application’s demands for durability, noise reduction, and resistance to environmental factors.
Rollers for the mining industry are designed to withstand the harsh conditions of mining operations, including dust, moisture, varying temperatures, and heavy loads. These rollers must be highly durable, reliable, and capable of handling abrasive materials without significant wear. Types of rollers specifically used in mining include troughed idler rollers for bulk material conveyance, impact rollers for shock absorption at loading zones, and return rollers to support the belt’s return side. Advanced materials like HDPE composites and technologies such as sealed bearings are often utilized to enhance the longevity and efficiency of these rollers in the demanding mining environment.
The mining industry typically uses heavy-duty conveyor belts designed to withstand the rigors of transporting large volumes of materials such as coal, ore, and overburden. These belts are made from durable materials like rubber, which is often reinforced with metal wires or fabrics such as polyester, nylon, or Kevlar to increase strength and resistance to tearing, abrasion, and impact. The choice of conveyor belt in mining also depends on the specific application, with options including flat belts for general material transport, chevron belts for incline transport to prevent load slippage, and steel-cord reinforced belts for long-distance and high-load conveyance.
Self-aligning rollers are specifically designed to maintain the proper alignment of a conveyor belt, ensuring smooth operation and preventing issues like belt drift or misalignment that can lead to operational disruptions and increased wear. These rollers can pivot and rotate to guide the belt back to its correct path automatically. They are particularly useful in long conveyor systems where maintaining belt alignment is challenging. Self-aligning rollers come in various designs, including troughing and flat configurations, to suit different conveyor belt types and operational requirements.
Mining conveyor belt rollers can be purchased from manufacturers and suppliers specializing in conveyor components and systems for the mining industry. Leading companies like Rulmeca, PROK, and Sandvik offer a wide range of rollers designed to meet the specific needs of mining operations. These products can often be sourced directly from the manufacturers, through their distributors, or from industrial supply companies. Many suppliers provide detailed product catalogs and offer custom-engineered solutions to address unique challenges. It’s advisable to consult with experts or the manufacturers directly to ensure the selection of the most suitable rollers for your specific application, considering factors such as load capacity, environmental conditions, and material characteristics.
The rollers on a conveyor belt are commonly referred to as idlers. Idlers are crucial components in a conveyor system as they support the belt and the load being conveyed. These rollers are designed to ensure smooth, efficient operation and to reduce wear on the conveyor belt. There are several types of idlers, each serving different functions. For instance, carrying idlers support the loaded section of the belt, while return idlers support the empty belt on its return. Impact idlers, fitted with rubber discs, are used at loading points to absorb the impact of material being loaded onto the belt, thereby protecting both the belt and the idlers themselves. Troughing idlers, which consist of three rollers, are designed to form the belt into a trough shape, which helps in containing the material being transported. The proper selection and maintenance of idlers are essential for the efficient operation and longevity of a conveyor system in any mining operation.
In the mining industry, several types of conveyor belts are used, each designed for specific applications and environments. The most common types include:
Steel Cord Conveyor Belts: These belts are reinforced with steel cords, providing high tensile strength and allowing for long-distance transportation of heavy materials. They are highly durable and resistant to wear and tear, making them suitable for harsh mining conditions.
Textile Conveyor Belts: These belts are made of fabric layers, typically polyester and nylon. They are flexible, resistant to impact, and suitable for shorter distances and less demanding applications.
Solid Woven Conveyor Belts: These belts are woven from synthetic fibers, making them highly resistant to damage from abrasion, cuts, and impacts. They are ideal for underground mining operations where durability is crucial.
Chevron Conveyor Belts: These belts feature a V-shaped pattern on the surface, providing extra grip for inclined or steeply inclined conveyor systems. They are used to transport loose bulk materials such as coal, sand, and gravel.
Heat-Resistant Conveyor Belts: These belts are designed to withstand high temperatures, making them suitable for transporting materials like hot clinker, slag, and foundry sand.
Each type of conveyor belt has specific features and benefits tailored to different mining applications, ensuring efficient and safe material handling.
The primary difference between a drive roller and a driven roller lies in their functions within a conveyor system. A drive roller, also known as a drive pulley, is responsible for moving the conveyor belt. It is connected to a motor or another power source that generates the necessary force to rotate the roller, thereby propelling the belt and the materials on it. Drive rollers are typically located at the discharge end of the conveyor system and are designed to provide the necessary traction and torque to move the belt effectively.
On the other hand, a driven roller, or an idler roller, does not have any direct power source. Its main function is to support the conveyor belt and the load it carries. Driven rollers help maintain the belt’s tension and alignment, ensuring smooth and efficient operation. They come in various types, including carrying idlers, return idlers, and impact idlers, each designed to perform specific roles within the conveyor system.
While the drive roller is crucial for the movement of the conveyor belt, the driven rollers play a supportive role, ensuring the belt remains properly tensioned, aligned, and capable of handling the load efficiently. Both types of rollers are essential for the optimal performance of a conveyor system in mining operations.
Last Updated on August 27, 2024 by Jordan Smith
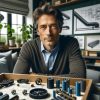
Jordan Smith, a seasoned professional with over 20 years of experience in the conveyor system industry. Jordan’s expertise lies in providing comprehensive solutions for conveyor rollers, belts, and accessories, catering to a wide range of industrial needs. From initial design and configuration to installation and meticulous troubleshooting, Jordan is adept at handling all aspects of conveyor system management. Whether you’re looking to upgrade your production line with efficient conveyor belts, require custom conveyor rollers for specific operations, or need expert advice on selecting the right conveyor accessories for your facility, Jordan is your reliable consultant. For any inquiries or assistance with conveyor system optimization, Jordan is available to share his wealth of knowledge and experience. Feel free to reach out at any time for professional guidance on all matters related to conveyor rollers, belts, and accessories.