Motorized Conveyor Roller Advantages for Modern Industries
Conveyor systems have been pivotal in industries for over a century, evolving from basic manual rail systems to sophisticated automated conveyance mechanisms. Among these advancements, motorized conveyor rollers represent a significant leap in technology and efficiency. These rollers, embedded with their own motors, propel the conveyor belt and the materials it carries with enhanced precision and control. This innovation not only streamlines the movement of goods through complex manufacturing lines and distribution centers but also drastically cuts down on energy consumption and operational noise. The significance of motorized conveyor rollers lies in their ability to improve system reliability, extend service life, and reduce maintenance costs, making them a cornerstone of modern industrial operations. Their integration into existing conveyor systems is transforming traditional practices, leading to smarter, safer, and more sustainable production environments.
What are Motorized Conveyor Rollers
The Basics of Motorized Conveyor Rollers
Motorized Conveyor Rollers are conveyor rollers equipped with integrated motors, designed to drive the movement of goods or materials along the conveyor path. Unlike traditional conveyor systems that rely on external drive mechanisms such as belts or chains, motorized conveyor rollers incorporate motors directly into the roller design, eliminating the need for separate drive components. This integrated design offers several advantages, including simplified installation, reduced maintenance, and improved efficiency.
Differences from Traditional Conveyor Systems:
Motorized conveyor rollers differ from traditional conveyor systems in their design and operation. Traditional conveyors typically use external drive mechanisms such as belts, chains, or shafts to power the movement of rollers or belts. In contrast, motorized conveyor rollers feature built-in motors that directly drive the rotation of the rollers, providing precise control and efficient material handling without the need for external drive components.
Key Components
1. Roller: The roller is the main component of the motorized conveyor roller, serving as the contact point between the conveyed items and the conveyor surface. Motorized conveyor rollers are typically equipped with cylindrical or tapered rollers made of durable materials such as steel or plastic, designed to withstand heavy loads and frequent use.
2. Motor: The motor is the power source that drives the rotation of the conveyor rollers. Motorized conveyor rollers incorporate integrated motors directly into the roller design, typically using brushless DC motors for efficient and reliable operation. These motors provide controlled movement and precise positioning of materials along the conveyor path, enhancing productivity and throughput.
3. Control Systems: Control systems regulate the operation of motorized conveyor rollers, allowing for speed control, direction reversal, and synchronization of multiple rollers within the conveyor system. Advanced control systems may include programmable logic controllers (PLCs), sensors, and human-machine interfaces (HMIs) to enable automation and customization of conveyor operations based on specific application requirements.
Conveyor Roller Parts and Their Functions:
- Roller Shell: The outer cylindrical surface of the roller that comes into contact with conveyed items.
- Bearings: Bearings support the roller shaft and facilitate smooth rotation of the roller.
- Shaft: The shaft provides structural support and serves as the axis of rotation for the roller.
- End Caps: End caps enclose the roller ends, securing bearings and providing protection against contamination.
- Motor Housing: The motor housing encases the motor assembly, providing protection and support for the motor components.
- Wiring and Connectors: Wiring and connectors facilitate electrical connections between the motor and control systems, enabling seamless integration and operation of the motorized conveyor rollers.
By understanding the basics and key components of motorized conveyor rollers, businesses can leverage this advanced technology to optimize material handling operations and enhance productivity in various industrial applications.
Advantages of Motorized Conveyor Rollers
Efficiency and Energy Savings
Motorized conveyor rollers offer significant advantages in terms of efficiency and energy savings:
24VDC Powered Roller Conveyors: Motorized conveyor rollers powered by 24VDC (direct current) systems are known for their energy efficiency. Unlike traditional conveyor systems that rely on continuous operation of motors or drives, 24VDC powered roller conveyors operate on-demand, powering up only when needed to move materials along the conveyor path. This on-demand operation minimizes energy consumption and reduces overall operating costs, making motorized rollers an environmentally friendly and cost-effective solution for material handling applications.
Reduction in Operational Costs: Motorized rollers contribute to cost savings by reducing operational costs associated with energy consumption and maintenance. By operating only when required, motorized conveyor rollers minimize idle time and energy wastage, leading to lower electricity bills and improved resource utilization. Additionally, the simplified design of motorized rollers reduces the need for maintenance and repairs, further lowering operational costs over the lifespan of the conveyor system.
Space Optimization and Noise Reduction
Motorized conveyor rollers offer space optimization and noise reduction benefits in industrial environments:
Compact Design: Motorized drive rollers feature a compact design with integrated motors, eliminating the need for external drive components such as motors, chains, or belts. This compact design saves valuable floor space in warehouses, distribution centers, and production facilities, allowing for more efficient layout and utilization of space. Additionally, the absence of external drive mechanisms simplifies installation and maintenance, further optimizing space utilization and enhancing operational efficiency.
Reduced Noise Levels: Motorized conveyor rollers operate with reduced noise levels compared to traditional conveyor systems, providing a quieter working environment for employees. The integrated motor design minimizes noise generated by external drive components such as belts, chains, and gears, resulting in a more comfortable and productive workplace. Reduced noise levels also contribute to improved worker satisfaction, safety, and overall well-being, making motorized rollers an ideal choice for noise-sensitive applications or environments requiring quiet operation.
By leveraging the efficiency, energy savings, space optimization, and noise reduction benefits of motorized conveyor rollers, businesses can enhance productivity, reduce operational costs, and create a more comfortable and efficient working environment for their employees.
Industry Applications of Motorized Conveyor Rollers
Motorized conveyor rollers find extensive applications across various industries, offering versatility and efficiency in material handling processes:
Manufacturing Industry
In the manufacturing sector, motorized conveyor rollers are utilized for assembly lines, production processes, and material transportation. They facilitate the movement of raw materials, components, and finished products between different stages of manufacturing operations, streamlining production workflows and increasing efficiency.
Warehousing and Distribution
In warehousing and distribution centers, motorized conveyor rollers play a crucial role in sorting, picking, packing, and shipping operations. They enable fast and efficient movement of goods within the facility, from receiving docks to storage areas and outbound shipping lanes, enhancing order fulfillment and logistics efficiency.
Automotive Industry
In the automotive industry, motorized conveyor rollers are used for assembly lines, paint lines, and material handling applications. They transport vehicle components, parts, and assemblies between manufacturing stations, ensuring smooth and seamless production processes while maintaining high levels of precision and quality control.
Food and Beverage Industry
In the food and beverage industry, motorized conveyor rollers are employed for packaging, bottling, and processing operations. They handle a wide range of products, including packaged foods, beverages, and perishable goods, while adhering to strict hygiene and safety standards. Motorized rollers facilitate efficient material flow and product handling, minimizing contamination risks and ensuring product integrity.
E-commerce and Retail
In e-commerce fulfillment centers and retail distribution facilities, motorized conveyor rollers support order processing, sorting, and shipping operations. They enable rapid order fulfillment and shipment processing, handling a diverse range of products and order volumes with speed and accuracy. Motorized rollers help e-commerce and retail businesses meet customer demand for fast and reliable order delivery.
Pharmaceutical and Healthcare
In the pharmaceutical and healthcare industries, motorized conveyor rollers are used for packaging, labeling, and distribution of medical products and supplies. They ensure the safe and efficient handling of pharmaceuticals, medical devices, and healthcare supplies, complying with strict regulatory requirements and quality standards. Motorized rollers support pharmaceutical manufacturing processes and healthcare supply chain operations, contributing to the delivery of critical healthcare products to patients worldwide.
The versatility of motorized conveyor rollers makes them indispensable in various industrial settings, providing efficient and reliable material handling solutions for a wide range of applications. Whether in manufacturing, warehousing, automotive, food and beverage, e-commerce, retail, pharmaceutical, or healthcare, motorized conveyor rollers offer enhanced productivity, efficiency, and operational flexibility to meet the diverse needs of modern industries.
Leading Manufacturers and Brands
Overview of Top Manufacturers
Leading manufacturers of motorized conveyor rollers offer innovative solutions for various industrial applications:
- Interroll: As a global leader in material handling solutions, Interroll specializes in motorized conveyor rollers and offers a comprehensive range of products for efficient and reliable material handling. With a focus on quality, reliability, and innovation, Interroll has established itself as a trusted partner for businesses worldwide.
- Hytrol: Hytrol is a leading manufacturer of conveyor systems and components, including motorized conveyor rollers. Known for their reliability and durability, Hytrol’s motorized rollers are widely used in manufacturing, distribution, and warehousing applications.
- Daifuku: Daifuku is a Japanese multinational company that provides material handling solutions, including motorized conveyor rollers and automated systems. With a focus on automation and efficiency, Daifuku’s motorized rollers are utilized in automotive, airport, and retail industries worldwide.
- Dorner: Dorner is a prominent manufacturer of precision conveyors and automation equipment, offering a range of motorized conveyor rollers for various applications. Dorner’s motorized rollers are known for their precision, reliability, and versatility, making them suitable for a wide range of industries.
Highlight on Interroll’s Contributions to Motorized Roller Technology
Interroll has made significant contributions to motorized roller technology, including:
- Integrated Motor Design: Interroll pioneered the concept of integrating motors directly into conveyor rollers, eliminating the need for external drive components and simplifying installation and maintenance.
- Energy Efficiency: Interroll’s motorized rollers feature energy-efficient designs, including 24VDC power systems and regenerative braking technology, to minimize energy consumption and reduce operational costs.
- Modular Design: Interroll’s motorized rollers feature a modular design, allowing for easy customization and scalability to accommodate various conveyor layouts and applications.
- Advanced Control Systems: Interroll offers advanced control systems and software solutions for motorized conveyor rollers, enabling precise speed control, synchronization, and integration with other automated systems.
- Durability and Reliability: Interroll’s motorized rollers are built to withstand heavy-duty usage and harsh operating conditions, ensuring long-term reliability and performance in demanding industrial environments.
- Safety Features: Interroll prioritizes safety in motorized roller design, incorporating features such as overload protection, emergency stop functions, and safety interlocks to prevent accidents and ensure operator safety.
- Global Reach: With a worldwide network of manufacturing facilities, distribution centers, and service locations, Interroll provides comprehensive support and service to customers across the globe, ensuring timely delivery and efficient after-sales support.
- Innovation and Continuous Improvement: Interroll is committed to innovation and continuous improvement, investing in research and development to introduce new technologies and product enhancements that address evolving customer needs and industry trends.
Comparison: Interroll Motorized Roller vs. Others
When comparing Interroll’s motorized roller offerings with those of other major brands, several factors set Interroll apart:
- Quality and Reliability: Interroll’s reputation for quality and reliability is unmatched, with a track record of delivering durable and high-performance motorized rollers that meet the most demanding industrial requirements.
- Innovative Features: Interroll’s motorized rollers incorporate innovative features such as dynamic load balancing, predictive maintenance capabilities, and advanced control algorithms, enhancing operational efficiency and productivity.
- Customization Options: Interroll offers extensive customization options for motorized rollers, allowing customers to tailor solutions to their specific application requirements, including roller length, diameter, and motor specifications.
- Global Support Network: Interroll’s global presence and service network ensure timely delivery, installation, and ongoing support for motorized roller systems, providing peace of mind to customers worldwide.
- Comprehensive Product Portfolio: Interroll offers a comprehensive portfolio of motorized roller solutions for various industries and applications, ranging from standard conveyors to specialized systems for unique requirements.
- Commitment to Sustainability: Interroll is committed to sustainability, offering energy-efficient motorized rollers and eco-friendly materials to minimize environmental impact and support customers’ sustainability goals.
- Value for Money: Interroll’s motorized rollers offer excellent value for money, providing long-term reliability, performance, and ROI (Return on Investment) compared to other brands in the market.
- Customer Satisfaction: Interroll prioritizes customer satisfaction, providing responsive support, technical expertise, and ongoing innovation to ensure customer success and satisfaction with motorized roller solutions.
By choosing Interroll’s motorized roller solutions, customers can benefit from industry-leading technology, reliability, and support, empowering them to optimize their material handling processes and achieve operational excellence.
Choosing the Right Motorized Conveyor Roller
When selecting the right motorized conveyor roller for your application, it’s crucial to consider various factors to ensure optimal performance and efficiency:
Factors to Consider
- Load Capacity: Determine the maximum weight or load that the motorized conveyor roller needs to handle. Choose rollers with sufficient load capacity to accommodate the heaviest items in your application without compromising performance or safety.
- Speed Requirements: Consider the desired conveyor speed for your operation. Select motorized rollers with adjustable speed settings or variable frequency drives (VFDs) to meet specific speed requirements and adapt to changing production demands.
- Environment Conditions: Assess the operating environment, including temperature, humidity, dust, and moisture levels. Choose motorized rollers with appropriate enclosure ratings and corrosion-resistant materials to ensure durability and reliability in harsh conditions.
- Duty Cycle: Determine the expected duty cycle or operating hours of the motorized conveyor roller. Choose rollers with duty cycle ratings that match or exceed your application’s requirements to avoid premature wear and ensure long-term reliability.
- Space Constraints: Consider the available space for roller installation within your conveyor system. Choose compact motorized rollers that can fit seamlessly into your existing layout without compromising throughput or efficiency.
- Integration Compatibility: Ensure compatibility with your existing conveyor equipment and control systems. Choose motorized rollers that can be easily integrated into your conveyor system architecture, minimizing installation time and costs.
- Maintenance Requirements: Evaluate the maintenance needs of different motorized roller options. Choose rollers with minimal maintenance requirements, such as sealed bearings and brushless motors, to reduce downtime and operating costs.
- Energy Efficiency: Opt for energy-efficient motorized rollers to minimize operating costs and environmental impact. Look for rollers with high-efficiency motors and regenerative braking technology to maximize energy savings and reduce carbon footprint.
- Brand Reputation: Research and compare different brands of motorized conveyor rollers. Choose reputable manufacturers with a proven track record of quality, reliability, and customer satisfaction, such as Interroll.
- Cost: Consider the upfront cost of motorized conveyor rollers in relation to their long-term benefits and return on investment. Choose rollers that offer the best value for money based on their performance, durability, and total cost of ownership.
Price Range and Investment
Motorized conveyor roller prices can vary depending on factors such as load capacity, speed capabilities, and additional features. Generally, prices range from a few hundred to several thousand dollars per roller, depending on the specifications and customization options.
While the initial investment in motorized conveyor rollers may seem significant, businesses can expect a favorable return on investment (ROI) over time. By improving efficiency, throughput, and reliability, motorized rollers can help businesses reduce labor costs, minimize downtime, and optimize material handling processes, leading to increased productivity and profitability in the long run.
When evaluating the price range and investment in motorized conveyor rollers, businesses should consider not only the upfront cost but also the potential savings and benefits they can achieve through improved operational performance and efficiency. By choosing the right motorized conveyor roller solution based on their specific needs and requirements, businesses can maximize their ROI and achieve sustainable growth and success.
Motorized Conveyor Rollers’ Installation and Maintenance
Setting Up Your Motorized Conveyor System
Installing motorized conveyor rollers involves several steps to ensure proper setup and functionality:
- Preparation: Gather all necessary tools and equipment for installation, including mounting brackets, fasteners, and electrical connections.
- Positioning: Position the motorized conveyor rollers along the conveyor path according to your layout plan, ensuring proper alignment and spacing between rollers.
- Mounting: Secure the motorized rollers to the conveyor frame using mounting brackets or supports, ensuring they are securely fastened and level.
- Electrical Wiring: Connect the electrical wiring of the motorized rollers to the power source and control system, following manufacturer guidelines and safety protocols.
- Testing: Test the motorized conveyor system to ensure all rollers are functioning correctly and moving smoothly along the conveyor path.
- Adjustments: Make any necessary adjustments to roller spacing, alignment, or speed settings to optimize conveyor performance and material handling efficiency.
- Safety Measures: Install safety guards, barriers, and emergency stop controls as required to ensure safe operation of the motorized conveyor system.
Maintenance Tips
To maintain optimal performance and longevity of motorized conveyor rollers, follow these maintenance tips:
- Regular Inspection: Conduct regular visual inspections of motorized rollers to check for signs of wear, damage, or misalignment.
- Lubrication: Lubricate roller bearings and moving parts according to manufacturer recommendations to prevent friction and reduce wear.
- Cleaning: Keep motorized rollers clean and free of debris, dust, and contaminants that can affect performance and cause premature failure.
- Tension Adjustment: Periodically check and adjust roller tension to ensure proper belt tracking and alignment.
- Electrical Checks: Inspect electrical connections, wiring, and components for signs of damage or deterioration, and repair or replace as needed.
- Temperature Monitoring: Monitor motor and roller temperatures during operation to detect overheating or abnormal conditions that may indicate a malfunction.
- Belt Alignment: Check belt alignment and tension regularly to prevent slippage or excessive wear on the rollers.
- Bearing Replacement: Replace worn or damaged bearings promptly to prevent further damage to the roller and conveyor system.
- Motor Inspection: Inspect motor components, such as brushes, brushes, or brushes, regularly to ensure proper functioning and longevity.
- Preventive Maintenance: Implement a preventive maintenance schedule for motorized conveyor rollers, including regular cleaning, lubrication, and inspection tasks.
- Training: Train maintenance personnel on proper procedures for inspecting, servicing, and troubleshooting motorized conveyor rollers to ensure safe and effective maintenance practices.
- Documentation: Keep detailed records of maintenance activities, including inspection dates, repairs, and replacements, to track the condition and performance of motorized conveyor rollers over time.
By following these installation and maintenance tips, businesses can ensure the reliable operation and longevity of their motorized conveyor roller systems, minimizing downtime and maximizing productivity in material handling operations.
FAQs about Motorized Conveyor Roller
A motorized roller conveyor, also known as a driven roller conveyor, is a material handling system designed to move goods and materials efficiently through a predetermined path within industrial or commercial settings. Each conveyor roller is equipped with an internal motor that enables individual rotation, providing the driving force necessary to transfer loads. This mechanism differs from traditional conveyor systems where a single external motor moves the entire roller assembly via belts or chains.
This type of conveyor optimizes the movement of items that vary in size, shape, and weight, offering precision control over the speed and distribution of goods. With the motorized system, items can be transported smoothly and consistently, reducing the need for manual handling and increasing productivity. The integration of modern control systems, such as sensors and automation software, allows for the precise coordination of motorized rollers, facilitating complex material handling processes and sortation tasks.
The specific type of motor used in a motorized roller conveyor can vary depending on the application, load requirements, and the manufacturer’s design. However, the most common types of motors integrated into conveyor rollers are brushless DC motors (BLDC) and geared motors. BLDC motors are favored for their efficiency, longevity, and high starting torque, making them ideal for systems that require precise speed control and frequent starting and stopping.
Geared motors, which combine a motor with a gear reducer, are also commonly used. They are beneficial in applications where the load is too heavy for a standard motor to drive it directly. The gear reduction provides higher torque at lower speeds, which is often necessary to move heavy objects on the conveyor. The choice of motor is critical, as it must match the required performance criteria, including speed, torque, power consumption, and maintenance needs.
There are several different types of conveyor rollers, each with unique advantages and suited to particular applications:
Gravity Rollers: These rollers operate without power and rely on gravitational forces or manual pushing to move items. They are often used for light to medium weight items and in areas where flexibility and cost-effectiveness are priorities.
Motorized Rollers: Built with internal motors, these rollers can control the movement and direction of materials on the line. They are used in automated handling systems where precise movement and positioning are necessary.
Grooved Rollers: Designed with grooves that can be used for driving belts or as guides for products; these are often seen in packaging and light manufacturing sectors.
Impact Rollers: Positioned at conveyor loading points, impact rollers are designed to absorb the shock of heavy materials and protect the conveyor belt and system from damage.
Tapered Rollers: Commonly used in curves, these rollers help to maintain the alignment of the materials as they move through curved sections of the conveyor system.
Each type of roller is built to address specific operational challenges within diverse industry sectors, ranging from logistics and distribution to manufacturing and food processing.
The principal difference between powered and unpowered roller conveyors lies in the method of actuation. Powered or motorized roller conveyors have integrated motors within each roller or a single motor driving the entire roller assembly through belts or chains. This design enables the automatic and controlled movement of goods along the conveyor system, which can be regulated for speed and handling.
Unpowered roller conveyors, commonly referred to as gravity conveyors, rely on natural forces or manual effort to move goods. The conveyor is typically installed with a slight incline, and the weight of the items themselves generates the movement as they slide down or are pushed along the rollers.
The choice between the two systems is influenced by factors such as the nature of the items being handled, the desired speed of operation, control requirements, and cost constraints. Powered roller conveyors are more expensive and complex but offer significant advantages in automation, control, and efficiency for high-volume or heavy-duty operations. In contrast, unpowered systems are more cost-effective, easier to install and maintain, and are suitable for lighter loads and simpler material handling tasks.
Last Updated on July 25, 2024 by Jordan Smith
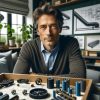
Jordan Smith, a seasoned professional with over 20 years of experience in the conveyor system industry. Jordan’s expertise lies in providing comprehensive solutions for conveyor rollers, belts, and accessories, catering to a wide range of industrial needs. From initial design and configuration to installation and meticulous troubleshooting, Jordan is adept at handling all aspects of conveyor system management. Whether you’re looking to upgrade your production line with efficient conveyor belts, require custom conveyor rollers for specific operations, or need expert advice on selecting the right conveyor accessories for your facility, Jordan is your reliable consultant. For any inquiries or assistance with conveyor system optimization, Jordan is available to share his wealth of knowledge and experience. Feel free to reach out at any time for professional guidance on all matters related to conveyor rollers, belts, and accessories.