How a Multi Ply Conveyor Belt Enhances Efficiency
Conveyor belts are the backbone of industrial applications, ensuring the smooth and efficient transport of materials across various sectors. Whether in mining, manufacturing, or recycling, these belts streamline operations and boost productivity. Among the different types of conveyor belts, the multi ply conveyor belt stands out for its durability and versatility. Comprising multiple layers of fabric, each with a rubber interface, these belts are designed to withstand the most demanding conditions. They play a crucial role in heavy-duty industries such as mining, stone quarries, and cement plants, providing reliable performance and extending the lifespan of the conveyor systems.
What is a Multi Ply Conveyor Belt
A multi ply conveyor belt is an essential component in many industrial applications, known for its robust construction and ability to handle heavy loads. These belts are constructed with multiple layers of fabric, typically ranging from four to six, bonded together with a rubber interface. This design not only enhances the strength and durability of the belt but also provides flexibility and resistance to impact and abrasion. Multi-ply conveyor belts are commonly used in environments where high performance and reliability are crucial, such as in mining, stone quarries, and cement plants.
A multi ply conveyor belt is characterized by its layered construction, which provides superior strength and durability compared to single-ply belts.
- Multiple Layers: Each layer of fabric, known as a ply, is reinforced with synthetic materials like polyester or nylon, offering high tensile strength.
- Rubber Interface: The layers are bonded with rubber, which enhances flexibility and resistance to impacts and abrasion.
- Transport Efficiency: Designed for efficient material transport, these belts are used in heavy-duty industrial applications.
- Material Handling: Suitable for a wide range of materials, from fine powders to coarse aggregates.
- Harsh Environments: Ideal for use in extreme temperatures and high-abrasion areas.
- Structural Integrity: Maintains integrity under heavy loads, reducing the risk of operational failures.
- Consistent Performance: Engineered for minimal downtime and maintenance costs.
- Versatile Applications: Widely used in mining, recycling, and cement production for their reliability.
Components of a Multi Ply Conveyor Belt
The construction of a multi ply conveyor belt involves three primary components, each playing a crucial role in its performance and durability. These components include the cloth cover, carcass cover, and skim cloth, each designed to provide specific benefits and enhance the overall functionality of the belt.
- Cloth Cover: The outermost layer provides additional protection and wear resistance. It often features special coatings or treatments to resist environmental factors such as heat or chemicals.
- Carcass Cover: The core strength member, made of fabric layers, provides tensile strength and flexibility. It is typically reinforced with materials like polyester or nylon to withstand high stress and heavy loads.
- Skim Cloth: Positioned between the plies, this rubber layer acts as an adhesive, enhancing the bonding between fabric layers. It also helps absorb impacts, reducing the likelihood of belt damage.
- Protective Coatings: The cloth cover may include protective coatings to enhance resistance to specific environmental challenges.
- Reinforcement Materials: The carcass cover’s reinforcement materials ensure the belt’s ability to handle heavy loads without compromising flexibility.
- Impact Absorption: The skim cloth’s rubber composition not only bonds the layers but also absorbs impacts, prolonging the belt’s lifespan.
Layer Information
The number of layers in a multi ply conveyor belt is a critical factor that determines its strength and suitability for various applications. Typically, these belts consist of four to six layers, each contributing to the belt’s overall performance. The choice of the number of layers depends on the specific requirements of the application, such as load weight and the nature of the materials being transported.
- Four-Ply Belts: Commonly used in medium-duty applications, offering a balance between strength and flexibility. These belts are suitable for transporting moderately heavy materials.
- Five-Ply Belts: Provide additional strength for more demanding applications. These belts are ideal for environments where higher loads are encountered regularly.
- Six-Ply Belts: Designed for the most extreme conditions, offering maximum strength and durability. These belts can handle the toughest materials and the heaviest loads.
- Layer Engineering: Each layer is meticulously engineered to ensure optimal performance, with rubber interfaces ensuring seamless cooperation between the layers.
- Customization: The number of layers can be customized based on specific needs, allowing for tailored solutions for different industrial environments.
- Performance Optimization: The layered construction helps distribute loads evenly, reducing stress on individual layers and extending the belt’s operational life.
Types of Multi Ply Conveyor Belt
Multi-ply conveyor belts come in various configurations, each designed to meet specific industrial requirements. The number of plies in a conveyor belt affects its strength, flexibility, and suitability for different applications. Below, we explore three common types of multi-ply conveyor belts: two-ply, three-ply, and four-ply.
Two-Ply Conveyor Belts
Two-ply conveyor belts are the simplest form of multi-ply belts, consisting of two layers of fabric bonded together with a rubber interface. These belts are often used in applications where moderate strength and flexibility are required.
- Moderate Strength: Two-ply conveyor belts offer sufficient strength for light to medium-duty applications, making them ideal for industries like food processing and packaging.
- Flexibility: The dual-layer construction provides good flexibility, allowing the belt to navigate smaller pulleys and complex conveyor systems without excessive wear.
- Cost-Effective: Two-ply belts are generally more affordable than belts with more layers, making them a cost-effective solution for many applications.
- Easy Maintenance: With fewer layers, these belts are easier to maintain and repair, reducing downtime and maintenance costs.
- Lightweight: The reduced number of layers makes these belts lighter, which can be advantageous in applications where weight is a concern.
- Customization: Two-ply belts can be customized with various cover materials and treatments to enhance their performance in specific environments.
Three-Ply Conveyor Belts
Three-ply conveyor belts offer a balance between strength and flexibility, making them suitable for a wider range of applications compared to two-ply belts. They consist of three layers of fabric, each bonded with a rubber interface.
- Enhanced Strength: The additional layer provides greater tensile strength, making three-ply conveyor belts suitable for more demanding applications such as bulk material handling and heavy industrial use.
- Increased Durability: Three layers of fabric enhance the belt’s durability, allowing it to withstand higher loads and more frequent use.
- Improved Flexibility: Despite the added strength, three-ply belts maintain good flexibility, which helps in applications requiring sharp turns and complex conveyor routes.
- Versatile Applications: These belts are used in a variety of industries, including mining, construction, and agricultural processing.
- Abrasion Resistance: The rubber interfaces between the layers provide excellent abrasion resistance, extending the belt’s lifespan in harsh environments.
- Load Distribution: The three-layer construction helps distribute the load more evenly across the belt, reducing stress on individual layers and preventing premature wear.
Four-Ply Conveyor Belts
Four-ply conveyor belts are designed for the most demanding industrial applications, offering maximum strength and durability. These belts consist of four layers of fabric, each separated by a rubber interface, making them suitable for the toughest conditions.
- Maximum Strength: Four-ply conveyor belts provide the highest tensile strength, making them ideal for transporting heavy and abrasive materials.
- Exceptional Durability: With four layers, these belts are highly durable and can withstand extreme conditions, including high-impact loads and harsh operating environments.
- High Load Capacity: The increased number of layers allows these belts to carry heavier loads over longer distances without compromising performance.
- Extreme Conditions: Four-ply belts are used in industries such as mining, steel production, and heavy manufacturing, where they must endure extreme temperatures, chemicals, and mechanical stress.
- Long Service Life: The robust construction of four-ply belts ensures a longer service life, reducing the need for frequent replacements and minimizing downtime.
- Customization Options: These belts can be tailored with specific cover materials and treatments to meet the unique needs of different industrial applications, enhancing their resistance to heat, chemicals, and other challenging conditions.
Each type of multi ply conveyor belt is engineered to meet specific operational needs, ensuring efficient and reliable performance across various industries. Whether you need moderate strength and flexibility or maximum durability and load capacity, there is a multi-ply conveyor belt designed to meet your requirements.
Sizes and Thickness of Multi Ply Conveyor Belt
The dimensions and thickness of multi ply conveyor belts are critical factors that determine their suitability for various industrial applications. The right size and thickness ensure optimal performance, durability, and efficiency in material handling processes.
Standard Sizes
Multi ply conveyor belts come in a range of standard sizes to accommodate different material handling requirements. These sizes ensure compatibility with various conveyor systems and facilitate easy installation and maintenance.
- Width Range: Multi ply conveyor belts are available in a wide range of widths, typically from 300 mm (12 inches) to 2400 mm (96 inches), accommodating different material handling requirements.
- Length Options: These belts can be manufactured in custom lengths to fit specific conveyor system configurations, ensuring seamless integration and operation.
- Standard Widths: Common standard widths include 400 mm (16 inches), 600 mm (24 inches), 800 mm (32 inches), and 1000 mm (40 inches), widely used in various industries.
- Special Sizes: In addition to standard sizes, custom sizes can be produced to meet unique application needs, providing flexibility in design and installation.
- Edge Options: Belts can be supplied with cut edges or molded edges, depending on the specific requirements of the application and the desired durability.
- Metric and Imperial Units: Sizes are available in both metric and imperial units, catering to global industry standards and preferences.
- Multi-Ply Variants: Each standard size can be manufactured with different ply configurations (e.g., two-ply, three-ply, four-ply) to meet varying strength and durability needs.
- Stock Availability: Many standard sizes are kept in stock by manufacturers, ensuring quick delivery and minimal downtime for industrial operations.
Thickness Information
The thickness of multi ply conveyor belts varies based on the number of plies and the intended application. Understanding thickness variations is essential for selecting the right belt for specific operational demands. Thickness is a crucial aspect of multi ply conveyor belts, impacting their load-bearing capacity, flexibility, and durability. Different applications require different thicknesses to ensure optimal performance and longevity.
- Varied Thickness: Multi ply conveyor belts come in a variety of thicknesses, typically ranging from 5 mm to 25 mm, depending on the number of plies and the specific application requirements.
- 4-Ply Thickness: Four-ply belts are a common choice for heavy-duty applications, with typical thicknesses ranging from 10 mm to 20 mm, providing robust strength and durability.
- Thin Belts: For lighter applications, thinner belts (e.g., 5 mm to 8 mm) are used, offering flexibility and ease of installation while maintaining adequate strength.
- Medium Thickness: Medium thickness belts (e.g., 8 mm to 12 mm) are suitable for general industrial use, balancing strength and flexibility.
- Thick Belts: Thick belts (e.g., 20 mm to 25 mm) are designed for the most demanding applications, where maximum load capacity and durability are essential.
- Customized Thickness: Thickness can be customized to meet specific needs, allowing for tailored solutions that optimize performance and longevity in particular environments.
- Cover Thickness: The thickness of the rubber cover on the belt can also vary, with options for thicker covers to enhance abrasion resistance and extend the belt’s lifespan.
- Layer Contribution: Each additional ply layer increases the overall thickness and strength of the belt, making it suitable for more challenging material handling tasks.
Material Composition of Multi Ply Conveyor Belt
The material composition of a multi ply conveyor belt is crucial to its performance, durability, and suitability for various industrial applications. These belts are made from high-quality rubber and fabric materials, each selected for specific properties that enhance the belt’s overall functionality.
Rubber Material
The rubber used in multi ply conveyor belts plays a significant role in determining the belt’s resistance to abrasion, heat, chemicals, and other environmental factors. Different types of rubber compounds are used in the manufacturing of multi ply conveyor belts, each offering distinct advantages tailored to specific operational needs.
- Natural Rubber: Known for its excellent elasticity and tensile strength, natural rubber is used in applications requiring flexibility and resistance to wear. Ideal for handling materials in moderate conditions, providing a balance between durability and cost-effectiveness.
- Styrene-Butadiene Rubber (SBR): Offers good abrasion resistance and durability, making it suitable for general-purpose conveyor belts. SBR is commonly used in environments where the belt is exposed to abrasive materials, extending the belt’s lifespan.
- Neoprene Rubber: Provides excellent resistance to oils, chemicals, and heat, making it suitable for harsh industrial environments. Neoprene belts are used in applications where the conveyor system handles oily or chemically aggressive substances.
- Nitrile Rubber (NBR): Known for its exceptional oil and fuel resistance, nitrile rubber is ideal for applications in the automotive and recycling industries. NBR belts maintain their integrity and performance in environments where oil and fuel exposure is frequent.
- Ethylene Propylene Diene Monomer (EPDM): Offers excellent heat, ozone, and weather resistance, suitable for outdoor and high-temperature applications. EPDM belts are used in settings where the conveyor is exposed to sunlight, extreme temperatures, and varying weather conditions.
- Butyl Rubber: Provides superior resistance to chemicals and gases, making it ideal for specialized applications in the chemical industry. Butyl belts are used in environments where the belt needs to withstand exposure to acids, alkalis, and other corrosive substances.
- Silicone Rubber: Known for its high-temperature resistance and flexibility, silicone rubber is used in food processing and packaging applications. Silicone belts ensure compliance with food safety regulations while maintaining performance under high temperatures.
- Chloroprene Rubber: Combines good physical properties with resistance to heat, oils, and aging, suitable for demanding industrial applications. Chloroprene belts are versatile, providing reliable performance in a variety of challenging operational conditions.
Fabric Materials
The fabric materials used in multi ply conveyor belts contribute to the belt’s strength, flexibility, and overall performance. High-quality fabrics are selected based on the specific requirements of different industrial applications. Premium quality fabrics used in multi ply conveyor belts ensure the belts can withstand high loads, impact, and harsh conditions, maintaining their structural integrity over time.
- Polyester Fabric: Known for its high tensile strength and low stretch properties, polyester fabric is commonly used in multiply conveyor belt. Polyester belts provide excellent dimensional stability, making them suitable for high-load applications.
- Nylon Fabric: Offers exceptional flexibility and resistance to impact, making it ideal for applications requiring frequent directional changes. Nylon belts are used in industries such as logistics and warehousing, where flexibility and durability are crucial.
- Cotton Fabric: Provides good flexibility and is often used in light to medium-duty applications. Cotton belts are suitable for industries like food processing, where gentle handling of materials is required.
- Aramid Fabric: Known for its high strength and heat resistance, aramid fabric is used in heavy-duty and high-temperature applications. Aramid belts are ideal for mining and metal processing industries, where durability and resistance to heat are essential.
- Kevlar Fabric: Offers superior strength and cut resistance, making it suitable for applications involving sharp or abrasive materials. Kevlar belts are used in recycling and material recovery facilities, where the belt needs to withstand sharp objects.
- Fiberglass Fabric: Provides excellent heat resistance and is used in applications requiring thermal stability. Fiberglass belts are suitable for industries like glass manufacturing and metal smelting, where high temperatures are common.
- Polyamide Fabric: Known for its high resistance to wear and tear, polyamide fabric is used in applications requiring longevity and durability. Polyamide belts are ideal for heavy industrial applications, ensuring long-term performance under constant use.
- Blended Fabrics: Combining different materials to optimize performance characteristics, blended fabrics offer customized solutions for specific industrial needs. Blended belts provide a balance of strength, flexibility, and resistance properties, tailored to unique operational requirements.
By understanding the material composition of a multi ply conveyor belt, industries can select the appropriate belt that meets their specific needs, ensuring optimal performance and longevity.
Features and Benefits of Multi Ply Conveyor Belt
Multi ply conveyor belts offer a range of features and benefits that make them suitable for various industrial applications. These belts are engineered to handle demanding conditions and provide reliable performance over extended periods. Here are the key features and benefits of multiply conveyor belt.
Abrasion Resistance
- Enhanced Durability: Abrasion-resistant multi ply conveyor belts are designed to withstand the wear and tear caused by abrasive materials, ensuring a longer lifespan. These belts are ideal for handling materials such as sand, gravel, and ore, which can cause significant abrasion damage to standard belts.
- Reduced Maintenance Costs: With higher resistance to wear, abrasion-resistant belts require less frequent replacement and maintenance. This results in lower operational costs and reduced downtime, enhancing overall productivity.
- Improved Safety: Abrasion-resistant belts reduce the risk of belt failures and breakdowns, contributing to a safer working environment. By maintaining integrity under harsh conditions, these belts minimize the chances of accidents and material spills.
Heat Resistance
- High-Temperature Performance: Heat-resistant multi ply conveyor belt is capable of operating in environments with elevated temperatures without degrading. These belts are used in industries such as cement, steel, and glass manufacturing, where they must endure high heat levels.
- Extended Belt Life: Heat-resistant properties prevent the belt from hardening, cracking, or losing flexibility over time. This ensures that the belt maintains its performance and durability, even under constant exposure to heat.
- Operational Efficiency: By withstanding high temperatures, these belts reduce the risk of thermal damage, ensuring continuous and efficient operation. This reliability is crucial for processes that involve heating or high-temperature materials.
Cold Resistance
- Flexibility in Low Temperatures: Cold-resistant multi ply conveyor belts remain flexible and functional even in freezing conditions. These belts are essential for industries operating in cold climates, such as mining and outdoor material handling.
- Crack Resistance: Cold-resistant belts are formulated to resist cracking and brittleness that can occur at low temperatures. This enhances the belt’s longevity and reliability, ensuring it can handle the rigors of cold environments.
- Consistent Performance: These belts maintain their strength and performance despite temperature fluctuations. This consistency is vital for operations that must continue without interruption, regardless of the weather.
Oil and Acid Resistance
- Chemical Resistance: Multi ply conveyor belts resistant to oils and acids are designed to operate in environments where exposure to these substances is common. These belts are used in industries such as chemical processing, recycling, and food production, where resistance to harsh chemicals is necessary.
- Enhanced Longevity: The resistance to oil and acid prevents the belt from deteriorating quickly, ensuring a longer service life. This durability reduces the frequency of belt replacements and associated downtime.
- Operational Safety: By withstanding chemical exposure, these belts reduce the risk of chemical-related damage and accidents. This enhances the safety of the working environment, protecting both the equipment and personnel.
- Versatility: Oil and acid-resistant belts can handle a variety of materials without compromising their structural integrity. This versatility makes them suitable for diverse applications where chemical exposure is a concern.
Overall Benefits
- Cost-Effectiveness: The durability and long service life of multi ply conveyor belts lead to lower overall costs. Investing in high-quality belts reduces the need for frequent replacements and maintenance, saving money in the long run.
- High Load Capacity: Multi ply conveyor belts can handle heavy loads and high-stress conditions without failing. This makes them suitable for industries requiring robust and reliable material handling solutions.
- Customization Options: These belts can be tailored to specific needs, including custom sizes, thicknesses, and material compositions. This customization ensures that the belts meet the precise requirements of various industrial applications.
- Environmental Resistance: In addition to abrasion, heat, cold, oil, and acid resistance, multi ply conveyor belts can be designed to resist other environmental factors. This includes resistance to UV light, moisture, and microbial growth, making them suitable for outdoor and sanitary applications.
By understanding the features and benefits of multi ply conveyor belts, industries can choose the right belt that meets their specific operational needs, ensuring efficiency, safety, and cost-effectiveness.
Applications of Multi Ply Conveyor Belt
Multi ply conveyor belts are essential in various industries due to their durability, flexibility, and ability to handle heavy loads. These belts are engineered to meet the specific demands of different sectors, ensuring efficient material handling and processing.
Mining
- Heavy Load Handling: Multi ply conveyor belts in mining are designed to transport heavy loads of extracted minerals and ores from mining sites to processing plants.
- Durability: These belts are built to withstand the harsh conditions of mining environments, including exposure to sharp rocks and abrasive materials.
- Impact Resistance: Mining operations often involve high-impact activities, and multi ply conveyor belts provide the necessary resistance to prevent damage.
- Longevity: The belts’ robust construction ensures a long service life, reducing the need for frequent replacements and maintenance.
- Safety: Using multi ply conveyor belts in mining enhances operational safety by reducing the risk of belt failures and associated accidents.
Stone Quarries
- Material Transport: Multi ply conveyor belts efficiently transport heavy stones and aggregates within stone quarries, from extraction points to processing units.
- Abrasion Resistance: These belts are resistant to abrasion, which is crucial when handling sharp and rough materials like stones and gravel.
- High Load Capacity: They can carry large volumes of materials, making them ideal for high-output operations in stone quarries.
- Stability: The belts maintain stability and performance under heavy loads, ensuring consistent operation.
- Operational Efficiency: By providing reliable material transport, multi ply conveyor belts contribute to the overall efficiency of quarry operations.
Sand Pits
- Smooth Transport: In sand pits, multi ply conveyor belts are used to transport sand from extraction areas to processing facilities.
- Flexibility: The belts’ flexibility allows them to adapt to the varied terrain of sand pits without compromising performance.
- Wear Resistance: They are designed to resist wear caused by the abrasive nature of sand, extending the belt’s lifespan.
- High Throughput: Multi ply conveyor belts can handle the large quantities of sand typically processed in sand pits.
- Low Maintenance: The belts require minimal maintenance, which is beneficial in sandy environments where equipment upkeep can be challenging.
Recycling
- Versatile Material Handling: Multi ply conveyor belts are crucial in recycling facilities, where they transport a variety of recyclable materials, including metals, plastics, and paper.
- Chemical Resistance: These belts are resistant to oils, acids, and other chemicals commonly encountered in recycling processes.
- Durability: The belts’ durability ensures they can withstand the rigorous conditions of recycling operations, including exposure to sharp and heavy objects.
- Efficiency: They improve the efficiency of recycling plants by providing a reliable means of material transport, reducing manual handling.
- Environmental Compliance: Using multi ply conveyor belts supports sustainable practices in recycling by ensuring efficient and safe material handling.
Concrete and Cement Plants
- Heavy Material Transport: Multi ply conveyor belts in concrete and cement plants handle heavy materials like cement, sand, and aggregates.
- Heat Resistance: These belts are designed to withstand high temperatures often encountered in cement production processes.
- Load Capacity: They can carry large loads, making them suitable for high-demand operations in cement plants.
- Longevity: The belts’ construction ensures a long service life, reducing downtime and maintenance costs.
- Efficiency: By providing reliable material transport, they contribute to the overall efficiency of concrete and cement production.
Sugar Factories
- Bulk Handling: In sugar factories, multi ply conveyor belts are used to transport bulk quantities of sugarcane and processed sugar.
- Moisture Resistance: These belts are resistant to moisture, which is essential when handling raw sugarcane that contains high water content.
- Durability: The belts’ robust construction ensures they can handle the tough conditions of sugar processing.
- Consistency: They provide consistent performance, ensuring smooth and efficient transport of materials.
- Hygiene: Multi ply conveyor belts used in sugar factories are often designed to meet hygiene standards required in food processing industries.
Wood, Paper, and Pulp Production
- Material Transport: Multi ply conveyor belts are essential in the transport of wood logs, pulp, and paper products within production facilities.
- Impact Resistance: These belts are built to withstand the impacts of heavy logs and sharp wood chips.
- Chemical Resistance: In pulp production, the belts need to resist chemicals used in processing wood into pulp.
- Flexibility: They offer the flexibility needed to navigate the complex conveyor systems in paper and pulp mills.
- Durability: The belts’ durability ensures they can handle the continuous and demanding operations typical in wood and paper production facilities.
Each of these applications highlights the versatility and reliability of multiply conveyor belt, making them indispensable across various industrial sectors. Their ability to handle different materials and withstand harsh conditions ensures efficient and effective material handling, contributing to the productivity and safety of industrial operations.
Innovations and Advancements in Multi Ply Conveyor Belt
The multi ply conveyor belt industry has seen significant innovations and advancements, enhancing their performance, durability, and adaptability to various industrial needs. These developments include specialty belts and customization options that cater to specific requirements, ensuring optimal performance and efficiency.
Specialty Belts
Recent innovations in multi ply conveyor belts have led to the development of specialty belts designed to meet the unique demands of various industrial applications. These specialty belts offer enhanced features that provide additional benefits over standard conveyor belts.
- FRAS/FRASS Belts: Fire Resistant and Anti-Static (FRAS) belts are designed to prevent fire hazards and reduce static electricity, making them ideal for use in underground mining and other hazardous environments. These belts ensure safety and compliance with industry regulations, reducing the risk of accidents and improving operational safety.
- Corrugated Sidewall Belts: These belts feature corrugated sidewalls that allow for the transportation of materials at steep inclines or even vertically. This design maximizes space utilization and increases the efficiency of material transport in confined spaces.
- Kevlar Belts: Incorporating Kevlar fibers, these belts offer exceptional strength and cut resistance, suitable for handling sharp and abrasive materials. Kevlar belts are used in recycling facilities and heavy-duty industrial applications where standard belts might fail.
- High-Temperature Belts: Designed to withstand extreme temperatures, these belts are used in industries like metal processing and glass manufacturing. They maintain their integrity and performance in high-heat environments, ensuring continuous operation without degradation.
- Oil-Resistant Belts: These belts are formulated to resist damage from oils and greases, commonly used in automotive and machinery industries. They prevent swelling and weakening caused by oil exposure, maintaining strength and durability.
- Acid-Resistant Belts: Made to resist chemical corrosion, these belts are used in chemical plants and processing facilities. They ensure longevity and reliability in environments exposed to acidic substances.
- Anti-Microbial Belts: These belts are designed with anti-microbial properties to prevent the growth of bacteria and mold. Ideal for food processing and pharmaceutical industries where hygiene is crucial.
- Cleated Belts: Featuring raised sections or cleats, these belts enhance material handling by preventing material slippage, especially in incline applications. They improve the transport of bulk materials, reducing spillage and increasing throughput.
Customization Options
Customization is a significant advancement in the multi ply conveyor belt industry, allowing manufacturers to design belts that meet specific operational needs and challenges. This flexibility ensures that belts are tailored to provide optimal performance in any given application.
- Tailored Sizes: Customizing the width and length of conveyor belts to fit specific machinery and space requirements ensures seamless integration into existing systems, reducing installation time and costs.
- Specialized Materials: Selecting specific rubber compounds and fabric materials based on the operational environment and material being transported provides enhanced resistance to environmental factors such as heat, cold, abrasion, and chemicals.
- Layer Configuration: Customizing the number of plies to match the load capacity and durability requirements of the application ensures the belt can handle the specific weight and stress conditions of the transported materials.
- Custom Cover Thickness: Adjusting the thickness of the rubber cover to provide additional protection and longevity extends the belt’s life by enhancing resistance to wear and tear.
- Cleat and Sidewall Design: Customizing cleats and sidewalls to improve material handling, especially for inclined or vertical transport, increases the efficiency and reliability of material transport in challenging conditions.
- Color Coding: Using different colors for belts to indicate specific uses or to improve safety and organization in complex systems helps in identifying the purpose of each belt, reducing the risk of operational errors.
- Edge Treatments: Customizing the edges of belts, such as adding sealed or reinforced edges to prevent fraying and improve longevity, enhances the durability and performance of the belt in harsh environments.
- Integration of Sensors: Embedding sensors within the belts to monitor conditions such as temperature, load, and wear in real-time provides real-time data to improve maintenance schedules and prevent unexpected downtimes.
By leveraging these innovations and customization options, industries can select and design multi ply conveyor belt that precisely meets their operational needs, ensuring enhanced performance, safety, and cost-efficiency.
FAQs about Multi Ply Conveyor Belt
Ply in a conveyor belt refers to the layers of fabric that are used in the construction of the belt. These fabric layers, or plies, are bonded together with a rubber interface to create a strong, durable, and flexible conveyor belt. The number of plies determines the belt’s strength and load-carrying capacity. Typically, conveyor belts can have multiple plies, such as two-ply, three-ply, or four-ply configurations, with each additional ply adding to the belt’s overall strength. The fabric used in these plies can vary, with common materials including polyester, nylon, and cotton, each offering different benefits in terms of flexibility, tensile strength, and resistance to abrasion. The concept of ply is crucial in selecting the appropriate conveyor belt for specific industrial applications, as it directly affects the belt’s performance and longevity.
The primary difference between 2 ply and 3 ply conveyor belts lies in the number of fabric layers they contain. A 2 ply conveyor belt consists of two layers of fabric bonded together with a rubber interface, while a 3 ply conveyor belt has three layers of fabric. This additional layer in the 3 ply belt provides increased strength, durability, and load-carrying capacity compared to the 2 ply belt. The choice between 2 ply and 3 ply conveyor belts depends on the specific needs of the application. For example, 2 ply belts are often sufficient for lighter-duty tasks and applications where flexibility and ease of installation are essential. In contrast, 3 ply belts are more suitable for heavier-duty applications that require greater tensile strength and resistance to wear and tear. This difference in construction makes 3 ply belts more robust and capable of handling more demanding conditions than 2 ply belts.
A 3 ply conveyor belt is a type of conveyor belt that consists of three layers of fabric, or plies, bonded together with a rubber interface. This construction provides enhanced strength, durability, and load-carrying capacity compared to belts with fewer plies. The fabric layers in a 3 ply conveyor belt are typically made from materials such as polyester, nylon, or cotton, which offer different benefits in terms of flexibility, tensile strength, and resistance to abrasion. The rubber interface between the plies helps to bond them together securely, ensuring the belt can withstand high stress and heavy loads. 3 ply conveyor belts are commonly used in industrial applications where robust performance is required, such as in mining, construction, and heavy manufacturing. Their ability to handle demanding conditions and provide reliable material transport makes them a preferred choice for many heavy-duty operations.
The thickness of a 4 ply conveyor belt can vary depending on the specific construction and application requirements, but generally, these belts range from approximately 10 mm to 20 mm in thickness. Each ply in the belt adds to its overall thickness, with the fabric layers and rubber interfaces contributing to the belt’s total dimension. The precise thickness of a 4 ply conveyor belt is determined by factors such as the type of fabric used, the thickness of each ply, and the overall design specifications required to meet the operational demands. Thicker 4 ply belts offer greater strength and durability, making them suitable for heavy-duty applications that involve transporting large volumes of materials or operating under harsh conditions. The increased thickness ensures that the belt can handle higher loads and provides extended service life, reducing the need for frequent replacements and maintenance.
Last Updated on August 9, 2024 by Jordan Smith
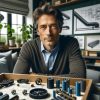
Jordan Smith, a seasoned professional with over 20 years of experience in the conveyor system industry. Jordan’s expertise lies in providing comprehensive solutions for conveyor rollers, belts, and accessories, catering to a wide range of industrial needs. From initial design and configuration to installation and meticulous troubleshooting, Jordan is adept at handling all aspects of conveyor system management. Whether you’re looking to upgrade your production line with efficient conveyor belts, require custom conveyor rollers for specific operations, or need expert advice on selecting the right conveyor accessories for your facility, Jordan is your reliable consultant. For any inquiries or assistance with conveyor system optimization, Jordan is available to share his wealth of knowledge and experience. Feel free to reach out at any time for professional guidance on all matters related to conveyor rollers, belts, and accessories.