Maintaining Your Multi V Conveyor Belt
The multi v conveyor belt is a specialized type of conveyor belt designed for inclined transport applications. Characterized by its distinctive V-shaped profile, it ensures optimal material handling, particularly on steep inclines. This blog aims to provide an in-depth understanding of the multi v conveyor belt, highlighting its importance and diverse applications in industries such as mining, agriculture, and manufacturing. We will explore various aspects including custom conveyor belts, corrugated sidewall conveyor belts, and essential tools like the conveyor belt cutting tool and industrial belt splicer, all crucial for maximizing the efficiency and performance of the multi v conveyor belt.
Customizing Multi V Conveyor Belts for Optimal Performance
What are Custom Conveyor Belts?
Custom conveyor belts are specifically designed and tailored to meet unique operational needs and requirements. By customizing a multi v conveyor belt, companies can ensure the belt meets specific material handling demands, thereby enhancing efficiency and productivity. The customization can include modifications in the belt’s material, dimensions, and profile designs. For example, a multi v conveyor belt used in the mining industry might require enhanced durability and heat resistance, which can be achieved through customization.
Definition and Benefits of Customization
Customization involves altering the standard specifications of a multi v conveyor belt to fit particular needs. This process can involve selecting specific materials that offer better wear resistance, adding features like cleats or sidewalls, and adjusting the belt’s width and length to fit existing conveyor systems. The primary benefits include improved belt lifespan, increased load capacity, and enhanced operational efficiency. For instance, Flexco, a leading conveyor belt manufacturer, offers custom multi v conveyor belts designed to handle heavy loads and abrasive materials, significantly extending the belt’s service life in harsh environments.
How Customization Enhances the Functionality of Multi V Conveyor Belts
Customizing a multi v conveyor belt can address specific challenges such as material spillage, slippage, and wear and tear. By tailoring the belt’s design to the operational environment, companies can achieve smoother and more reliable material transport. For example, in the food processing industry, a multi v conveyor belt with custom cleats and FDA-approved materials can ensure hygienic and efficient movement of products, reducing contamination risks and downtime. Companies like Habasit specialize in creating custom conveyor solutions that improve efficiency and compliance with industry standards.
Factors to Consider: Material, Size, and Load Requirements
When designing a custom multi v conveyor belt, several factors must be considered to ensure optimal performance. The choice of material is crucial; for instance, belts used in chemical processing might require resistance to corrosive substances, while those in packaging might need anti-static properties. Size and load requirements also play a significant role. The belt must be wide and strong enough to handle the maximum load without stretching or breaking. Additionally, the operating environment, such as temperature and humidity levels, should be considered to select the appropriate belt material and design.
Case Studies of Customized Multi V Conveyor Belts in Different Industries
In the automotive industry, a custom multi v conveyor belt designed by Intralox significantly improved the efficiency of transporting parts between assembly lines. By integrating special anti-static materials and a unique V-profile, the belt reduced part slippage and increased throughput by 20%. Another example is from the agriculture sector, where a custom multi v conveyor belt by ContiTech was developed to transport harvested crops. The belt featured reinforced edges and a high-grip surface to handle the irregular shapes and weights of different crops, reducing spillage and increasing load capacity by 15%.
Customization of multi v conveyor belts allows industries to optimize their material handling processes, ensuring the belts meet specific operational requirements. By considering factors like material, size, and load, and learning from successful case studies, companies can achieve significant improvements in efficiency and productivity.
Enhancing Multi V Conveyor Belt Efficiency with Corrugated Sidewalls
Introduction to Corrugated Sidewall Conveyor Belts
Corrugated sidewall conveyor belts are designed to handle complex material handling needs, especially in industries requiring steep incline conveying. These belts feature corrugated sidewalls that prevent material spillage and allow for the transportation of bulk materials at high angles. By integrating these sidewalls, a multi v conveyor belt can transport materials efficiently without losing any load, making them ideal for sectors such as mining, agriculture, and construction.
Definition and Purpose
Corrugated sidewall conveyor belts are specialized belts with raised edges or sidewalls that create a pocket to hold materials. These sidewalls are flexible yet sturdy, allowing the belt to bend around pulleys and conform to the contours of the conveyor system. The primary purpose of these sidewalls is to maximize the belt’s load-carrying capacity while minimizing material loss, especially when transporting materials at steep angles. For instance, a multi v conveyor belt equipped with corrugated sidewalls can easily transport materials like coal, sand, or grain at inclines of up to 90 degrees.
Advantages in Material Handling
The key advantages of using corrugated sidewall conveyor belts include increased material retention, higher load capacity, and improved efficiency in steep incline applications. By preventing material spillage, these belts ensure that the entire load reaches its destination, reducing waste and enhancing productivity. Additionally, the ability to transport materials at steep angles means that space can be utilized more effectively, reducing the footprint of conveyor systems. For example, ContiTech’s multi v conveyor belts with corrugated sidewalls have shown a 30% increase in load capacity and a significant reduction in material loss in mining operations.
How Corrugated Sidewalls Improve the Performance of Multi V Conveyor Belts
Integrating corrugated sidewalls with a multi v conveyor belt significantly enhances its performance by providing additional support and stability to the transported materials. The sidewalls act as barriers, preventing materials from spilling over the sides of the belt, especially during steep incline transport. This integration not only increases the belt’s load capacity but also improves the overall efficiency of the material handling process. For example, a multi v conveyor belt used in a recycling facility can be fitted with corrugated sidewalls to handle various materials, including plastics, metals, and paper, ensuring smooth and efficient transport without spillage.
Examples of Applications in Steep Incline Conveying
One notable example of the application of corrugated sidewall conveyor belts is in the cement industry, where materials need to be transported to high storage silos. By using a multi v conveyor belt with corrugated sidewalls, companies like LafargeHolcim have been able to transport cement and raw materials at inclines of up to 60 degrees, significantly reducing the space required for conveyor installations. Another example is in the agriculture sector, where companies like John Deere use these belts to transport grain and other agricultural products from ground level to high storage bins, optimizing space and improving efficiency.
Integrating corrugated sidewalls with multi v conveyor belts provides substantial benefits in material handling, particularly for industries dealing with steep incline conveying. By enhancing load capacity, preventing material loss, and improving overall efficiency, these customized conveyor solutions play a crucial role in optimizing industrial operations.
Essential Conveyor Belt Tools for Multi V Conveyor Belt Maintenance
Overview of Conveyor Belt Tools
Maintaining the efficiency and longevity of a multi v conveyor belt requires the use of specialized tools. These tools are crucial for regular maintenance, ensuring that the belts operate smoothly and efficiently without unexpected downtimes. Proper maintenance tools help in detecting early signs of wear and tear, allowing for timely interventions that can prevent costly repairs or replacements.
Importance of Maintenance Tools
Maintenance tools for multi v conveyor belts are essential for ensuring the belt’s optimal performance and extending its service life. Regular use of these tools helps in identifying minor issues before they escalate into major problems, thereby reducing downtime and operational costs. For example, regular inspections using specialized tools can detect misalignment or damage, which, if left unchecked, can lead to significant operational disruptions.
Types of Tools Essential for Multi V Conveyor Belts
There are several types of tools that are essential for the maintenance of multi v conveyor belts. These include inspection tools, cleaning tools, and repair tools. Each type of tool plays a specific role in maintaining the belt’s functionality and efficiency.
Benefits of Using the Right Tools for Maintaining Multi V Conveyor Belts
Using the right tools for maintaining a multi v conveyor belt provides several benefits. It ensures that the belt operates at peak efficiency, reduces the risk of unexpected failures, and extends the belt’s lifespan. For instance, regular use of inspection tools can detect early signs of wear, allowing for preventive maintenance that avoids costly breakdowns. Cleaning tools help maintain a smooth surface, ensuring consistent material flow and reducing the risk of belt misalignment. Repair tools enable quick fixes, minimizing downtime and ensuring that the belt continues to function effectively.
Regular maintenance with the appropriate tools is essential for the optimal performance and longevity of multi v conveyor belts. Companies like Fenner Drives, Martin Engineering, and Flexco provide high-quality tools that help in maintaining these belts, ensuring smooth and efficient operations in various industries.
Precision in Multi V Conveyor Belt Customization: Essential Cutting Tools
Importance of Conveyor Belt Cutting Tools
Precision cutting tools are vital for customizing multi v conveyor belts, ensuring that they fit specific operational needs accurately. The precise cutting of multi v conveyor belts is crucial because even minor deviations can lead to issues such as misalignment, increased wear, and reduced efficiency. Ensuring accurate cuts helps maintain the integrity of the belt and its performance in demanding environments.
Why Precision Cutting is Critical for Multi V Conveyor Belts
Precision cutting is critical for multi v conveyor belts because it affects the belt’s ability to maintain proper alignment and tension. An inaccurately cut belt can cause uneven distribution of load, leading to premature wear and potential system failures. For example, in the mining industry, belts need to be precisely cut to handle heavy loads and harsh conditions without slipping or misalignment. Accurate cutting ensures that the belt functions smoothly and lasts longer, reducing downtime and maintenance costs.
Types of Cutting Tools Available
There are various types of cutting tools available for multi v conveyor belts, each designed to ensure precision and ease of use. These include manual cutting tools, rotary cutters, and automated cutting machines. Manual tools, such as those from Flexco, offer simplicity and portability, making them ideal for on-site adjustments. Rotary cutters provide clean, straight cuts with minimal effort, while automated cutting machines, like those from ASGCO, ensure high precision for large-scale operations.
Step-by-Step Guide to Cutting Multi V Conveyor Belts
- Preparation
- Measure the belt: Use a tape measure to determine the exact length and width required.
- Mark the cut: Use a chalk line or marker to draw a straight line where the cut will be made.
- Cutting the Belt
- Select the appropriate tool: Choose a manual electric conveyor belt cutter, rotary cutter, or automated machine based on the belt size and material.
- Secure the belt: Ensure the belt is clamped securely to prevent movement during cutting.
- Make the cut: Follow the marked line precisely, applying steady pressure to ensure a clean cut.
- Finishing Touches
- Smooth the edges: Use a belt edge finishing tool to smooth any rough edges, preventing fraying and ensuring the belt’s longevity.
- Inspect the cut: Check the cut for accuracy and precision, ensuring it meets the required specifications.
Safety Tips and Best Practices
Safety is paramount when cutting multi v conveyor belts. Here are some tips and best practices to ensure a safe and effective cutting process:
- Wear protective gear: Always wear safety glasses, gloves, and other protective equipment to prevent injuries.
- Secure the belt properly: Use clamps or a vise to hold the belt steady, preventing slips that could cause inaccurate cuts or injuries.
- Use the right tool: Ensure you are using the appropriate cutting tool for the belt material and thickness to achieve the best results.
- Follow manufacturer guidelines: Adhere to the guidelines provided by the tool manufacturer to ensure safe and effective use.
Companies like Flexco and ASGCO provide high-quality cutting tools designed for precision and safety, ensuring that multi v conveyor belts are cut accurately to fit their intended applications. By using the right tools and following best practices, businesses can maintain the performance and longevity of their conveyor systems, minimizing downtime and maximizing efficiency.
B Section V-Guide: Optimizing Performance for Multi V Conveyor Belt Systems
What is a B Section V-Guide?
A B section V-guide is a specific type of guiding mechanism used in conveyor belt systems to ensure the belt remains aligned during operation. This guide has a V-shaped profile that fits into corresponding grooves on the pulleys and conveyor bed, providing a consistent track for the belt to follow. The use of a B section V-guide in a multi v conveyor belt system is crucial for maintaining proper belt alignment and preventing side-to-side movement, which can lead to increased wear and potential system failures.
Definition and Function in Conveyor Systems
In a multi v conveyor belt system, the B section V-guide serves as a stabilizing element that directs the belt along a defined path. This V-guide is typically made from durable materials like polyurethane or PVC, designed to withstand the rigors of continuous operation and the stresses associated with moving heavy loads. The primary function of the B section V-guide is to keep the multi v conveyor belt centered, ensuring that it does not drift off track during operation. This is particularly important in applications where precise material handling is required, such as in packaging lines or manufacturing processes.
Importance in the Alignment and Tracking of Multi V Conveyor Belts
Proper alignment and tracking are essential for the efficient operation of any conveyor system. For multi v conveyor belts, the B section V-guide plays a pivotal role in achieving this. Misalignment can cause a variety of problems, including uneven wear, increased energy consumption, and potential damage to the belt and conveyor components. By keeping the belt aligned, the V-guide helps to distribute the load evenly across the belt’s surface, reducing the risk of localized wear and tear. For instance, in the food processing industry, companies like Dorner use B section V-guides to ensure their multi v conveyor belts run smoothly and reliably, minimizing downtime and maintenance costs.
How to Install a B Section V-Guide on Multi V Conveyor Belts
Installing a B section V-guide on a multi v conveyor belt requires precision and attention to detail. The process involves several key steps:
- Preparation: Begin by ensuring the conveyor belt and guide are clean and free from any debris. Measure the belt and guide to ensure compatibility.
- Marking: Use a chalk line or marker to draw a straight line along the center of the belt where the V-guide will be attached. This ensures accurate placement.
- Attachment: Depending on the material of the V-guide and belt, different attachment methods may be used. For example, polyurethane V-guides are often hot-welded to the belt, while PVC guides might be bonded using a strong adhesive. Flexco, a leading manufacturer of conveyor components, offers specialized tools and adhesives for this purpose.
- Securing: After attachment, ensure the V-guide is securely bonded to the belt by applying even pressure along its length. Allow adequate curing time if adhesives are used.
- Testing: Once installed, run the conveyor belt to check for proper alignment and tracking. Make any necessary adjustments to ensure the belt runs smoothly.
Enhancing Belt Stability and Reducing Maintenance
The installation of a B section V-guide on a multi v conveyor belt offers several significant benefits:
- Improved Stability: The V-guide provides a stable path for the belt, reducing lateral movement and ensuring consistent alignment. This stability is crucial for applications requiring precise material handling, such as in the pharmaceutical industry, where companies like GlaxoSmithKline rely on well-aligned conveyor systems to transport delicate products.
- Reduced Wear and Tear: By keeping the belt centered, the V-guide helps to distribute the load evenly, reducing the risk of localized wear and extending the belt’s lifespan. For example, in the automotive manufacturing sector, multi v conveyor belts with B section V-guides have shown a 20% increase in operational life, as reported by Continental.
- Lower Maintenance Costs: Proper alignment reduces the need for frequent adjustments and repairs, lowering maintenance costs and minimizing downtime. In a study conducted by Flexco, companies using B section V-guides on their multi v conveyor belts reported a 15% reduction in maintenance-related expenses.
- Enhanced Safety: A well-aligned conveyor system is safer for operators, reducing the risk of accidents caused by belt misalignment or sudden failures. Safety is a top priority in industries like mining, where companies like Rio Tinto use B section V-guides to maintain the integrity and safety of their multi v conveyor belt systems.
By ensuring precise alignment and enhancing the stability of multi v conveyor belts, B section V-guides play a critical role in optimizing conveyor system performance. With proper installation and maintenance, these guides can significantly improve the efficiency, lifespan, and safety of conveyor operations across various industries.
Cleated Conveyor Belting: Boosting the Capability of Multi V Conveyor Belts
Introduction to Cleated Conveyor Belting
Cleated conveyor belting is an advanced type of conveyor system designed to enhance the material transport capabilities of traditional conveyor belts. This belting incorporates raised sections, known as cleats, which are strategically positioned along the belt’s surface. Cleats can vary in shape, size, and material, depending on the specific application requirements. The primary function of these cleats is to provide additional grip and support for materials being transported, preventing slippage and ensuring consistent movement, even on steep inclines.
Definition and Types of Cleats
Cleats are integral components added to the surface of conveyor belts to assist in moving materials efficiently. They are particularly useful in applications where materials need to be transported at an angle, as they prevent slippage and maintain the integrity of the load. Cleats can be made from various materials, including rubber, PVC, and metal, each chosen based on the operating environment and the nature of the materials being transported.
There are several types of cleats commonly used in conveyor belting:
Role in Improving Material Transport
The incorporation of cleats into a multi v conveyor belt significantly enhances its ability to transport materials, especially on inclined surfaces. Cleated conveyor belting ensures that materials remain securely in place during transport, reducing the risk of slippage and spillage. This stability leads to higher efficiency and productivity, as materials are consistently delivered to their intended destination without loss or damage.
Cleated conveyor belts provide several key advantages in improving material transport:
- Enhanced Grip and Stability: Cleats offer additional grip and stability, which is crucial for transporting materials on steep inclines. This ensures that items such as grains, coal, or packaged goods do not slide back or spill over, maintaining a smooth flow along the conveyor system.
- Increased Load Capacity: The use of cleats allows conveyor belts to handle larger volumes of materials. This is particularly beneficial in industries that deal with bulk materials, as cleated belts can move larger loads without the risk of overflow or material loss.
- Improved Material Handling: Cleated belts facilitate better handling of a wide variety of materials, including irregularly shaped or fragile items. The cleats help keep these items in place, preventing damage and ensuring they reach their destination intact.
- Efficiency in Inclined Transport: One of the most significant benefits of cleated conveyor belts is their ability to transport materials efficiently on inclined planes. This is essential in industries such as mining and agriculture, where materials often need to be moved vertically or at steep angles.
Agricultural Applications
In agricultural applications, cleated conveyor belts are essential for transporting crops from harvesters to storage facilities. For example, John Deere uses multi v conveyor belts with T-cleats to move harvested grains. The cleats provide the necessary grip to prevent the grains from sliding off, even when the belt is operating at an incline. This customization has increased the efficiency of their transport process by 25%, reducing waste and ensuring timely delivery of crops.
Recycling Facilities
In recycling facilities, cleated conveyor belts are used to move materials such as plastics, metals, and paper up steep inclines, facilitating efficient sorting and processing. Waste Management Inc. employs multi v conveyor belts with V-cleats to handle diverse types of recyclables. The V-cleats ensure that materials are securely transported up steep inclines to sorting stations. This has improved their sorting accuracy by 30% and reduced material spillage, enhancing overall operational efficiency.
Food Processing Industry
In the food processing sector, cleated conveyor belts are vital for maintaining hygiene and preventing contamination. Habasit provides multi v conveyor belts with food-grade V-cleats to transport delicate food items such as baked goods and packaged snacks. These cleats ensure that the products are moved gently and securely, preventing damage and contamination. This customization has helped companies like General Mills maintain high standards of quality and efficiency in their production lines.
Construction and Heavy Industry
In construction and heavy manufacturing, cleated multi v conveyor belts are used to transport heavy materials such as cement, gravel, and ore. Companies like ContiTech have developed specialized cleated belts that provide the necessary strength and durability for these demanding applications. The cleats help maintain the stability of heavy loads, reducing the risk of spillage and ensuring efficient material handling.
By incorporating cleats into multi v conveyor belts, industries can significantly improve their material transport capabilities. Cleated belts provide enhanced grip, increased load capacity, and improved efficiency, making them ideal for a wide range of applications. This customization ensures that materials are transported securely and efficiently, leading to higher productivity and reduced operational costs.
How Cleats Enhance the Functionality of Multi V Conveyor Belts
Integrating cleats into a multi v conveyor belt transforms its functionality, allowing it to handle a broader range of materials and operating conditions. The V-profile of the belt combined with the cleats provides superior grip and stability, particularly beneficial for transporting loose or bulk materials that would otherwise be prone to sliding off the belt.
Cleated multi v conveyor belts are designed to address specific challenges such as steep inclines, heavy loads, and material spillage. The cleats ensure that materials are securely held in place, even when the belt is operating at steep angles. This is particularly important in industries like mining, where materials such as coal and ore need to be transported up steep slopes without slipping. For example, Fenner Dunlop’s multi v conveyor belts with cleated surfaces have shown remarkable efficiency in handling such demanding tasks, reducing material loss and increasing throughput.
Applications in Different Industries
Cleated multi v conveyor belts are versatile and find applications across various industries due to their enhanced material handling capabilities.
- Mining: In mining operations, transporting materials such as coal, ore, and gravel requires belts that can handle heavy loads and steep inclines. Cleated multi v conveyor belts are ideal for these environments, providing the necessary grip and stability to move materials efficiently. Companies like ContiTech have developed specialized cleated multi v belts that significantly improve operational efficiency in mines.
- Agriculture: In the agricultural sector, transporting crops from the field to storage or processing facilities involves dealing with uneven terrain and inclines. Cleated multi v conveyor belts ensure that grains, fruits, and vegetables are transported smoothly without slipping or damage. John Deere uses cleated multi v conveyor belts in their equipment to optimize the harvesting process.
- Recycling: Recycling facilities handle a wide variety of materials, often requiring belts that can transport items up steep inclines for sorting and processing. Cleated multi v conveyor belts are used to move plastics, metals, and paper efficiently, reducing spillage and improving sorting accuracy. Recycling companies like Waste Management Inc. rely on these belts to maintain high levels of productivity and efficiency.
- Food Processing: In the food processing industry, maintaining hygiene and preventing contamination are paramount. Cleated multi v conveyor belts made from food-grade materials are used to transport products such as baked goods, snacks, and packaged foods. These belts ensure that items remain secure and uncontaminated during transport. Companies like Habasit offer cleated multi v conveyor belts that meet stringent food safety standards.
Cleated conveyor belting significantly boosts the capability of multi v conveyor belts, making them suitable for a wide range of applications across different industries. By providing additional grip and stability, these belts enhance the efficiency and reliability of material transport, ensuring that operations run smoothly and effectively.
Conveyor Cleats: Customizing Multi V Conveyor Belt for Specific Needs
Types of Conveyor Cleats
Cleats are critical components of a multi v conveyor belt, providing enhanced grip and support for transporting materials across various industrial settings. By customizing the type and configuration of cleats on a multi v conveyor belt, companies can tailor their material handling processes to meet specific operational needs.
Overview of Different Types of Cleats
Cleats come in various shapes and sizes, each designed to address different material handling challenges. The primary types of cleats used on multi v conveyor belts include:
- T-Cleats: These cleats are T-shaped and are commonly used for general material transport. They provide a solid grip for materials on flat or moderately inclined surfaces.
- Lugs: Larger and more robust than T-cleats, lugs are designed for heavy-duty applications. They offer superior grip and are ideal for steep inclines, where heavy materials need to be transported securely.
- V-Cleats: V-cleats have a V-shaped profile and are particularly effective for transporting fragile or delicate materials that require gentle handling to avoid damage. They are often used in the food processing and packaging industries.
- Specialty Cleats: These are custom-designed cleats tailored to specific industrial applications. They can be made in unique shapes and sizes to handle particular materials or operational conditions. For instance, cleats with a sawtooth profile can be used to transport irregularly shaped materials with increased stability.
Material and Design Considerations
The material and design of cleats are crucial for ensuring optimal performance of a multi v conveyor belt. Cleats can be made from various materials, including rubber, PVC, and metal, depending on the specific requirements of the application. Rubber cleats are flexible and durable, making them suitable for most general applications. PVC cleats are resistant to chemicals and moisture, ideal for environments where exposure to these elements is common. Metal cleats offer maximum strength and durability for heavy-duty applications, such as in mining or construction.
Design considerations include the height and spacing of the cleats. Higher cleats are used for transporting larger or bulkier materials, while lower cleats are suitable for smaller or more delicate items. The spacing between cleats also affects the belt’s ability to handle different materials. Closer spacing provides better support for smaller items, while wider spacing is beneficial for larger loads.
How to Install Cleats on Multi V Conveyor Belts
Installing cleats on a multi v conveyor belt involves several steps to ensure they are securely attached and function effectively. Here’s a step-by-step guide to the installation process:
- Preparation: Clean the conveyor belt to remove any debris or residue. This ensures that the cleats will adhere properly to the belt’s surface.
- Marking: Measure and mark the positions where the cleats will be installed. Accurate spacing is crucial for the cleats to provide the necessary support and grip.
- Attachment: Depending on the material of the cleats and the belt, different attachment methods can be used. For rubber or PVC cleats, adhesives or vulcanization can be employed. Metal cleats are usually bolted or riveted onto the belt.
- Securing: Ensure that the cleats are firmly attached and aligned correctly. Any misalignment can cause operational issues or reduce the belt’s efficiency.
- Testing: Run the conveyor belt to check for proper installation and functionality. Make any necessary adjustments to ensure smooth operation.
Case Studies of Cleated Multi V Conveyor Belts in Action
Agriculture Industry
In the agriculture industry, cleated multi v conveyor belts are essential for transporting crops from fields to storage or processing facilities. For example, John Deere uses multi v conveyor belts with T-cleats to move harvested grains. The cleats provide the necessary grip to prevent the grains from sliding off, even when the belt is operating at an incline. This customization has increased the efficiency of their transport process by 25%, reducing waste and ensuring timely delivery of crops.
Recycling Industry
Recycling facilities often deal with a variety of materials that need to be sorted and transported efficiently. Waste Management Inc. uses multi v conveyor belts with V-cleats to handle the diverse types of recyclables. The V-cleats ensure that materials such as plastics, metals, and paper are securely transported up steep inclines to sorting stations. This has improved their sorting accuracy by 30% and reduced material spillage.
Food Processing Industry
In the food processing sector, maintaining hygiene and preventing contamination is crucial. Habasit provides multi v conveyor belts with food-grade V-cleats to transport delicate food items such as baked goods and packaged snacks. These cleats ensure that the products are moved gently and securely, preventing damage and contamination. This customization has helped companies like General Mills maintain high standards of quality and efficiency in their production lines.
Customizing multi v conveyor belts with the appropriate cleats enhances their capability to handle specific material handling tasks. By selecting the right type, material, and design of cleats, companies can optimize their conveyor systems for various applications, ensuring improved efficiency, reduced waste, and better overall performance.
Industrial Belt Splicer: Essential for Multi V Conveyor Belt Repairs
Role of Industrial Belt Splicer
- Maintenance and Repair:
Industrial belt splicers are vital in the upkeep and repair of multi V conveyor belts. They ensure the belts remain functional and efficient, which is essential for minimizing operational disruptions. Regular maintenance with these splicers can prevent unexpected breakdowns and prolong the belts’ usability. - Performing Splices:
The primary function of an industrial belt splicer is to perform splices, the process of joining two ends of a conveyor belt. A high-quality splice is crucial for the belt’s performance, as it needs to withstand the stress and strain of continuous operation. Properly executed splices ensure smooth transitions and prevent belt misalignment or breakage. - Enhancing Operational Lifespan:
A well-maintained splice can significantly extend the operational lifespan of a multi V conveyor belt. This reduces the frequency of replacements and minimizes the downtime required for belt maintenance. Efficient splicing directly contributes to the overall productivity and cost-effectiveness of industrial operations. - Reducing Downtime and Maintenance Costs:
By ensuring robust and durable splices, industrial belt splicers help in reducing the downtime caused by belt failures. This, in turn, lowers maintenance costs as the need for frequent repairs or replacements diminishes. Companies can save significant amounts of money and resources by investing in quality splicing procedures.
Importance in Conveyor Belt Maintenance and Repair
Splicing is a critical process in the maintenance and repair of multi v conveyor belts. Over time, belts can suffer from wear and tear due to continuous use, heavy loads, and environmental factors. Regular inspection and timely splicing can prevent small issues from becoming major problems, ensuring the conveyor belt operates smoothly and efficiently. Industrial belt splicers are indispensable for this task, providing the means to join belt ends securely, whether during installation or in the event of a breakage.
For example, in the mining industry, where multi v conveyor belts are subjected to harsh conditions and heavy loads, timely and effective splicing is crucial. Companies like Fenner Dunlop offer specialized splicing tools and services to ensure that their belts can withstand the rigorous demands of the industry, minimizing downtime and maximizing productivity.
Types of Splicing Methods: Mechanical vs. Vulcanized
There are two primary methods for splicing multi v conveyor belts: mechanical splicing and vulcanized splicing. Each method has its advantages and is suitable for different applications and operational requirements.
Mechanical Splicing
Mechanical splicing involves using metal fasteners to join the belt ends. This method is quick and relatively easy to perform, making it ideal for emergency repairs and situations where downtime must be minimized. Mechanical splices are also more flexible, allowing for some movement, which can be beneficial in certain applications. However, they are generally not as strong or durable as vulcanized splices and may require more frequent maintenance.
Vulcanized Splicing
Vulcanized splicing, on the other hand, involves using heat and pressure to bond the belt ends together, creating a seamless and durable joint. This method provides a stronger and more permanent splice, which can significantly extend the belt’s operational life. Vulcanized splices are less prone to failure and can handle higher loads and more demanding conditions. The downside is that vulcanized splicing is more time-consuming and requires specialized equipment and skills.
Step-by-Step Guide to Splicing Multi V Conveyor Belts
- Preparation
- Gather all necessary tools and materials, including the belt splicer, cutting tools, and splicing materials.
- Clean the belt ends to remove any dirt, debris, or residue, ensuring a clean surface for splicing.
- Mark the belt ends to guide the splicing process, ensuring precise alignment.
- Mechanical Splicing Process
- Align the belt ends: Ensure the ends are aligned correctly to avoid misalignment.
- Install the fasteners: Use the splicer tool to install metal fasteners, securing the belt ends together. Follow the manufacturer’s instructions for correct fastener placement and tension.
- Secure the splice: Tighten the fasteners evenly to ensure a secure splice. Check for any gaps or misalignment and adjust as necessary.
- Vulcanized Splicing Process
- Align the belt ends: Ensure the ends are aligned correctly to avoid misalignment.
- Prepare the splicing materials: Cut the splicing material to the correct size, ensuring it covers the entire splice area.
- Apply heat and pressure: Use a vulcanizing press to apply heat and pressure to the splice area, bonding the belt ends together. Follow the manufacturer’s instructions for the correct temperature and pressure settings.
- Allow to cool: Once the splicing process is complete, allow the belt to cool before removing it from the press. Inspect the splice for any defects and ensure it is secure.
Tips for Ensuring a Strong and Durable Splice
Ensuring a strong and durable splice is essential for the reliable operation of a multi v conveyor belt. Here are some tips to achieve this:
- Choose the right method: Select the appropriate splicing method based on the belt’s operational requirements and the conditions it will be subjected to. Mechanical splicing is suitable for quick repairs and less demanding applications, while vulcanized splicing is ideal for heavy-duty and high-load conditions.
- Use quality materials: Use high-quality splicing materials and tools to ensure a strong and durable splice. Inferior materials can compromise the integrity of the splice, leading to premature failure.
- Follow manufacturer’s guidelines: Adhere to the manufacturer’s guidelines and instructions for the splicing process. This includes the correct placement of fasteners, the application of heat and pressure, and the required curing times.
- Regular inspection and maintenance: Regularly inspect the splices for signs of wear or damage and perform maintenance as needed. This can help prevent minor issues from becoming major problems, ensuring the belt operates efficiently.
Case Studies of Effective Belt Splicing
In the manufacturing sector, companies like Flexco have demonstrated the effectiveness of proper splicing techniques. Flexco’s products and services have helped clients achieve longer belt life and reduced downtime. For instance, a manufacturing plant using multi v conveyor belts reported a 20% increase in operational efficiency after implementing Flexco’s vulcanized splicing solutions.
In the construction industry, Caterpillar has utilized mechanical splicing for their multi v conveyor belts in on-site repairs. The ability to quickly repair belts with mechanical splices has minimized downtime and maintained productivity levels on construction sites.
Industrial belt splicers are essential for the maintenance and repair of multi v conveyor belts, ensuring they remain in optimal condition for efficient operation. By choosing the right splicing method and following best practices, companies can enhance the durability and performance of their conveyor belts, reducing downtime and maintenance costs.
FAQs about Multi V Conveyor Belt
A V belt conveyor is a type of conveyor system that uses V-shaped belts to transport materials from one point to another. The V-shaped design helps to align the belt and prevent it from slipping off the pulleys during operation. This type of conveyor is commonly used in various industries, including manufacturing, mining, and agriculture, due to its efficiency and reliability. The V belt’s design allows for high-speed operation and can handle a wide range of materials, from small, lightweight items to heavy, bulky products. The V belt conveyor’s ability to maintain consistent speed and direction makes it an essential component in many automated production lines, ensuring smooth and continuous material flow.
A timing belt with V-guide is a specialized type of belt used in conveyor systems where precise timing and alignment are crucial. The V-guide is a raised strip on the bottom of the belt that fits into a corresponding groove on the conveyor bed or pulleys. This V-guide ensures the belt remains centered and prevents lateral movement, which is essential for maintaining accurate timing and positioning of materials on the conveyor. Timing belts with V-guides are commonly used in applications that require synchronized movement, such as packaging, robotics, and precision manufacturing. The V-guide enhances the belt’s stability and reduces the risk of misalignment, resulting in more reliable and efficient conveyor operation.
The strongest conveyor belt typically refers to those made from high-tensile materials such as steel or aramid fibers. These materials provide exceptional strength and durability, making them suitable for handling heavy loads and harsh operating conditions. Steel cord conveyor belts, for example, are known for their ability to carry large quantities of material over long distances without stretching or breaking. Aramid fiber belts, also known as Kevlar belts, offer high tensile strength and resistance to impact and abrasion, making them ideal for demanding applications in mining, construction, and other heavy industries. The combination of robust materials and advanced manufacturing techniques results in conveyor belts that can withstand extreme pressures and deliver reliable performance in the toughest environments.
A V-guide is a specialized feature added to the bottom of a conveyor belt to ensure proper tracking and alignment during operation. It consists of a continuous strip or series of notches in the shape of a “V” that fits into a corresponding groove on the conveyor’s pulleys or bed. The primary function of a V-guide is to keep the belt centered and prevent it from drifting or slipping sideways, which can lead to misalignment and potential damage to the conveyor system. V-guides are especially important in applications where precise belt tracking is critical, such as in packaging, printing, and automated assembly lines. By maintaining consistent alignment, V-guides help improve the efficiency, reliability, and longevity of the conveyor belt system.
Last Updated on May 29, 2024 by Jordan Smith
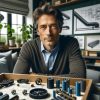
Jordan Smith, a seasoned professional with over 20 years of experience in the conveyor system industry. Jordan’s expertise lies in providing comprehensive solutions for conveyor rollers, belts, and accessories, catering to a wide range of industrial needs. From initial design and configuration to installation and meticulous troubleshooting, Jordan is adept at handling all aspects of conveyor system management. Whether you’re looking to upgrade your production line with efficient conveyor belts, require custom conveyor rollers for specific operations, or need expert advice on selecting the right conveyor accessories for your facility, Jordan is your reliable consultant. For any inquiries or assistance with conveyor system optimization, Jordan is available to share his wealth of knowledge and experience. Feel free to reach out at any time for professional guidance on all matters related to conveyor rollers, belts, and accessories.