In many industrial sectors, conveyor systems are pivotal for the seamless movement of goods, playing a critical role in maintaining operational efficiency. These systems are especially crucial in environments where heat-intensive processes are routine, necessitating the use of robust equipment capable of withstanding extreme conditions. This is where high temperature conveyor rollers become essential. Designed to endure the rigors of high heat, high temperature conveyor rollers are tailored to meet the specific demands of industries such as metalworking, glass manufacturing, and food processing. Their durability not only ensures the continuous flow of production but also minimizes downtime caused by equipment failure, highlighting their significance in maintaining high industrial standards and safety.
Read moreConveyor systems are integral to the manufacturing and distribution sectors, facilitating the efficient movement of goods across facilities. Central to these systems are the rollers that support and drive conveyor belts. Among these, metric conveyor rollers are particularly vital due to their standardization and adaptability in various industrial applications globally. These rollers are designed to meet specific metric measurements, which ensures consistency and interchangeability across different machinery and setups. The widespread use of metric conveyor rollers is attributed to their ability to enhance operational efficiency and reduce downtime in production lines. Industries ranging from automotive to food processing rely heavily on these robust and precise components to maintain smooth operational flows and meet stringent production demands.
Read moreUHMW conveyor rollers, made from Ultra-High Molecular Weight Polyethylene (UHMW-PE), are renowned for their exceptional durability and performance across various industries. These rollers offer a unique combination of high impact strength, low friction, and excellent resistance to wear and corrosion, making them ideal for heavy-duty applications. As critical components in material handling systems, UHMW conveyor rollers significantly reduce operational costs by minimizing maintenance requirements and extending equipment life.
Read moreIn industrial material handling, precision conveyor rollers play a pivotal role, facilitating seamless movement of goods across diverse sectors. These rollers are essential components in conveyor systems, ensuring efficient and reliable transportation of goods, materials, and products. From manufacturing and logistics to mining and agriculture, precision conveyor rollers are indispensable in maintaining smooth operations. For instance, in automotive assembly lines, these rollers enable precise positioning of components, enhancing production efficiency. Similarly, in distribution centers, they facilitate the swift sorting and distribution of packages, optimizing logistics processes. Amidst this landscape, Precision Pulley & Idler (PPI) stands out as a pioneering force, offering cutting-edge conveyor solutions. With a reputation for excellence, PPI remains at the forefront of innovation, delivering high-quality precision conveyor rollers tailored to meet the unique needs of various industries.
Read moreSelecting the appropriate type of conveyor belt rubber glue is crucial for effective maintenance and repair of conveyor systems. The right adhesive not only ensures durable bonding of torn or worn sections but also significantly extends the lifespan of the belt. Effective repair with quality rubber glue can restore the structural integrity of conveyor belts, preventing costly downtimes and maintaining continuous, efficient operations. Utilizing the correct type of rubber glue enhances the belt’s resistance to wear and tear under various operational conditions, including exposure to chemicals, temperature variations, and mechanical stress. This guide provides detailed insights into various types of conveyor belt rubber glues, their applications, and how to select and apply them correctly to achieve optimal performance and durability of conveyor systems.
Read moreThe performance and longevity of conveyor belts significantly depend on the quality of rubber used, specifically its density. Conveyor belt rubber density is a critical parameter that determines the belt’s structural integrity and functionality under various industrial conditions. Measured in kilograms per cubic meter (kg/m^3), this density affects key aspects of a conveyor belt’s performance, including tensile strength, elasticity, and wear resistance. High-density rubber typically offers better durability and resistance to deformations such as stretching, abrasions, or tears, thereby enhancing the conveyor belt’s efficiency and lifespan. Understanding the rubber density is essential for selecting the right conveyor belt, as it directly impacts the belt’s ability to handle different weights and speeds of materials over time, ensuring reliable and safe operations in facilities that depend heavily on automated transport systems.
Read moreThe introduction of the plastic conveyor roller belt has revolutionized the way industries handle material transport. These belts, crafted from durable plastic, offer a lightweight yet robust solution for moving goods across various distances and environments. In this article, we will delve into the plastic conveyor roller belt, exploring its functions, benefits, and the vast array of options available on the market. We will cover topics such as the availability of used plastic conveyor roller belts, what to consider when purchasing a belt for sale, and the distinctions between standard and heavy-duty models. Additionally, we will discuss the different specifications that can influence the choice of belt to best suit specific industrial needs. By the end of this article, you’ll have a thorough understanding of how these belts can enhance operational efficiency and adaptability in your operations.
What is the Plastic Conveyor Roller Belt
The plastic conveyor roller belt is an essential component in modern material handling and manufacturing processes, designed specifically to facilitate the smooth and efficient transport of goods within a facility. These belts are made from high-grade plastic materials, which provide a lightweight yet durable solution compared to traditional metal belts.
Definition and Purpose
A plastic conveyor roller belt consists of a series of plastic rollers attached at intervals along a flexible belt. This setup is engineered to support and move goods across different sections of a manufacturing or distribution facility. The primary purpose of a plastic conveyor roller belt is to minimize labor, reduce handling time, and increase the speed of production processes.
Advantages of Using Plastic Materials in Conveyor Systems
The advantages of using plastic materials in conveyor systems are numerous:
- Corrosion Resistance: Plastic conveyor roller belts are highly resistant to corrosion, making them ideal for use in environments where moisture or chemical exposure is common. This durability extends the life of the conveyor system and reduces maintenance costs.
- Noise Reduction: Plastic materials tend to generate less noise during operation compared to metal alternatives. This creates a quieter work environment, which is beneficial for facilities that prioritize reducing noise pollution and enhancing worker comfort.
- Reduced Weight: Plastic is considerably lighter than metal, which makes the entire system easier and cheaper to install and maintain. The lightweight nature of plastic conveyor roller belts also means less energy is required to operate them, leading to energy cost savings.
- Versatility in Design: Plastic allows for greater flexibility in the design of conveyor belts. Manufacturers can easily customize the shape, size, and properties of plastic belts to meet specific operational needs, such as varying load capacities and the handling of different types of goods.
Utilizing a plastic conveyor roller belt in a conveyor system not only improves the efficiency and speed of operations but also offers significant long-term benefits in terms of cost savings and operational flexibility. These factors make the plastic conveyor roller belt a vital tool in optimizing the performance of a wide array of industrial applications.
Types of Plastic Conveyor Roller Belts
Exploring the various types of plastic conveyor roller belts is crucial for selecting the right belt for specific industrial applications. Each type of belt is designed to meet different operational demands, from light-duty packaging tasks to heavy-duty industrial processes.
Overview of Different Types
Here are four common types of plastic conveyor roller belts:
- Modular Plastic Belts: These are constructed from plastic modules that are interlocked in a bricklay pattern, providing high strength and versatility. They are ideal for handling various product sizes and shapes and are particularly useful in food processing applications due to their ease of cleaning.
- Flat Plastic Belting: Known for their flat surfaces, these belts are suitable for transporting large and small items that require stable support. They are widely used in sorting and packing lines where precision is key.
- Plastic Chain Belts: These feature a chain-like plastic structure that offers flexibility and durability. They are commonly used in bottling plants or in applications requiring curved sections for product transportation.
- Ribbed Plastic Belts: These belts have raised ribs across the belt width, which help in transporting goods on inclines or declines without slippage. They are perfect for applications where grip and positioning of the product are critical.
Distinctions between Standard and Heavy-Duty Models
The choice between standard and heavy-duty plastic conveyor roller belts depends on several factors, including the expected load and the environmental conditions of the operation. Below is a comparative table outlining key differences:
Feature | Standard Plastic Conveyor Roller Belt | Heavy-Duty Plastic Conveyor Roller Belt |
---|---|---|
Material Thickness | Less thick, suitable for lighter loads | Thicker, designed to handle heavy loads |
Durability | Suitable for moderate use | Enhanced durability for high-demand environments |
Flexibility | More flexible, easier to install | Less flexible, prioritizes strength |
Application | Packaging, light manufacturing | Mining, construction, heavy manufacturing |
Cost | Generally more cost-effective | More expensive due to stronger materials and construction |
Understanding these distinctions helps in choosing the appropriate plastic conveyor roller belt for your specific needs, ensuring both efficiency and longevity in your conveyor system. Whether your operation requires a standard model for light applications or a heavy-duty belt for challenging conditions, there is a plastic conveyor roller belt designed to meet those needs.
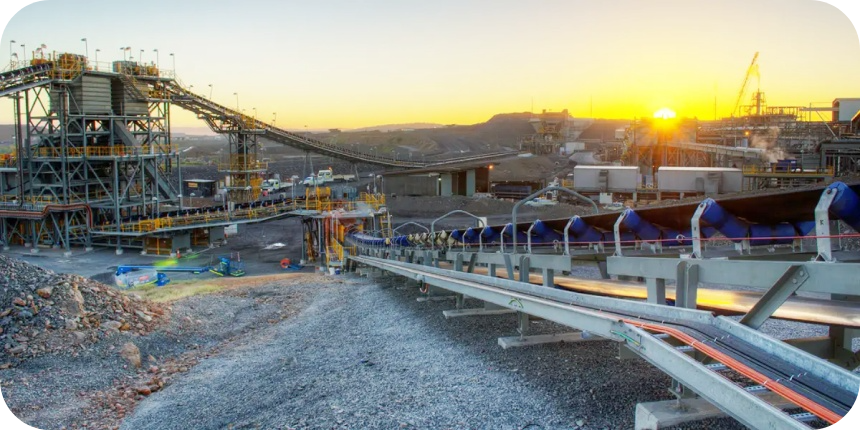
🔒Submit your request now and receive a detailed quote on our plastic conveyor roller belt.
Key Features of Plastic Conveyor Roller Belts
Understanding the key features of plastic conveyor roller belts can significantly impact the selection and operation of these systems within various industries. These belts are engineered not only for efficiency but also for durability and adaptability in challenging environments.
Specifications of Plastic Rollers with Bearings
Plastic rollers equipped with bearings are a fundamental component of the plastic conveyor roller belt. These rollers are typically made from high-quality thermoplastic materials, which offer excellent wear resistance. The bearings within these rollers are crucial as they allow for smooth and consistent movement of the belt, minimizing friction and resistance. This setup ensures a longer operational life and reduces the need for frequent maintenance. Bearings are often sealed to protect against dust, water, and other contaminants, enhancing the system’s reliability even in harsh conditions.
Benefits of Plastic Roller Wheels in the Operation of the Conveyor System
The inclusion of plastic roller wheels in conveyor systems brings several advantages:
- Reduced Maintenance Costs: Plastic roller wheels generally require less maintenance than metal counterparts because they are less prone to rust and corrosion. This can significantly lower the long-term costs associated with upkeep and replacement.
- Increased System Longevity: The durability of high-quality plastics used in these rollers contributes to the extended lifespan of the conveyor system. Plastic is less likely to deform under stress and can withstand repeated use without significant wear.
- Noise Reduction: One of the standout features of plastic conveyor roller belts is their ability to operate quietly. The plastic material absorbs operational noises better than metal, contributing to a quieter work environment, which is beneficial for facilities that operate around the clock or in noise-sensitive areas.
- Versatility: Plastic roller wheels are versatile in their application. They can be used in various environments, from dry to moist, and are capable of handling a range of temperatures. This makes plastic conveyor roller belts suitable for industries like food processing, pharmaceuticals, and manufacturing.
Each of these features of the plastic conveyor roller belt enhances the overall functionality and efficiency of conveyor systems, making them a preferred choice for many sectors seeking reliable and effective material handling solutions.
Sourcing Your Plastic Conveyor Roller Belt
When it comes to sourcing your plastic conveyor roller belt, whether you’re looking for a used option to reduce costs or a new belt to guarantee longevity and performance, there are several avenues you can explore. Here we provide practical tips and guidance on where and how to find the right plastic conveyor roller belt for your needs.
Finding Used Plastic Conveyor Roller Belts
Used plastic conveyor roller belts can be a cost-effective solution, especially for smaller operations or for those looking to reduce upfront investment. Here are four places to consider when searching for used belts:
- Industrial Surplus Stores: These stores often carry a wide range of used industrial equipment, including conveyor belts. Shopping at a surplus store allows you to inspect the belt physically before purchasing.
- Online Marketplaces: Websites like eBay, Alibaba, or even specialized industrial equipment sites have listings for used plastic conveyor roller belts. These platforms offer a broad geographic reach and potentially lower prices.
- Auctions and Liquidation Sales: Companies going out of business or upgrading their facilities often sell their old equipment at auctions. These events can be great opportunities to acquire a plastic conveyor roller belt at a reduced price.
- Direct Purchases from Factories: Sometimes factories will sell their old equipment directly when they upgrade their conveyor systems. Contacting local manufacturers directly can lead you to good deals on used equipment.
Purchasing a New Plastic Conveyor Roller Belt
When buying a new plastic conveyor roller belt, consider the following steps to ensure you get the best product for your money:
- Identify Reputable Manufacturers: Research and select manufacturers known for their quality conveyor systems. Brands that specialize in conveyor technology are often a good bet.
- Assess Specifications and Features: Make sure the specifications of the plastic conveyor roller belt meet your operational requirements. Consider factors such as belt width, load capacity, and material properties.
- Compare Prices and Warranty Offers: Get quotes from multiple suppliers to compare prices. Also, check the warranty terms to ensure they provide adequate coverage against defects or premature wear.
- Consult with Industry Experts: If possible, consult with industry experts or engineers to ensure that the plastic conveyor roller belt you are considering is suitable for your specific applications.
By following these guidelines, you can make a well-informed decision whether you are buying a new or used plastic conveyor roller belt, ensuring that you acquire a system that fits your needs and budget.
Heavy-Duty Solutions for Industrial Needs with Plastic Conveyor Roller Belt
For industries operating under demanding conditions, choosing the right conveyor system is critical. Heavy-duty plastic conveyor roller belts are engineered to meet these challenging requirements, combining durability with high functionality.
Features and Functionalities of Heavy-Duty Plastic Conveyor Roller Belt
Heavy-duty plastic conveyor roller belts are designed with several key features that make them suitable for intense industrial applications:
- Enhanced Load Capacity: These belts are built to withstand higher weight loads, making them ideal for industries like mining, metal processing, or any sector where heavy materials are moved regularly.
- High Impact Resistance: The materials used in heavy-duty belts are selected for their ability to absorb shocks and impacts without deforming or breaking. This is crucial for operations involving rough or sharp materials.
- Resistance to Harsh Chemicals: Many heavy-duty belts are treated to resist corrosion and damage from harsh chemicals, which is essential in industries such as chemical manufacturing or waste processing.
- Extreme Temperature Tolerance: These belts can operate under extreme temperatures, both high and low, which is a necessity for businesses like foundries or cold storage facilities.
The Importance of Durability in Challenging Environments
Durability is a non-negotiable aspect of heavy-duty plastic conveyor roller belts, particularly when operating in environments that pose numerous challenges:
- Abrasive Materials Handling: In sectors such as construction and mining, where materials can be exceptionally rough and abrasive, durable belts prevent frequent replacements and downtime, ensuring continuous operation.
- Moisture and Humidity Resistance: In food processing or paper industries, exposure to moisture is inevitable. Durable plastic belts prevent moisture absorption, which can lead to bacterial growth and belt degradation.
- Prevention of Breakdowns in High-Speed Applications: In automotive and packaging industries, where conveyor speeds are high, the durability of the belt ensures that it can handle the stress of rapid movements without failure.
- Longevity in Outdoor or Variable Environments: For industries that operate partially or entirely outdoors, such as agriculture or bulk material handling, belts must withstand environmental factors like UV rays, rain, and temperature fluctuations.
The selection of a heavy-duty plastic conveyor roller belt for demanding applications not only enhances efficiency but also significantly reduces the risk of operational disruptions. This focus on durability ensures that industries can maintain high productivity levels and reduce overall maintenance costs, making heavy-duty plastic belts an essential component of any robust industrial setup.
DIY PVC Conveyor Rollers: A Custom Approach to Plastic Conveyor Roller Belt
For those looking to tailor their conveyor systems to specific needs or constraints, creating DIY PVC conveyor rollers is an innovative and cost-effective solution. This section offers a detailed guide on building your own plastic conveyor roller belt using PVC materials and explores the various benefits of going the DIY route.
Step-by-Step Guide to Creating DIY PVC Conveyor Rollers
Building your own plastic conveyor roller belt with PVC can be a rewarding project. Here’s how you can start:
- Materials Needed: Gather PVC pipes, PVC end caps, bearings suitable for the pipe’s inner diameter, metal rods or bolts (for axles), and tools like a drill and saw.
- Cutting the PVC: Measure and cut the PVC pipe into sections that match the width of your desired conveyor belt. Ensure each piece is cut squarely to avoid wobble.
- Preparing the Axles: Insert metal rods or bolts through the center of each PVC roller. These will serve as axles. It’s crucial to ensure they fit snugly within the bearings.
- Attaching the Bearings: Secure bearings into the PVC end caps. Then, attach the end caps to both ends of each PVC roller. This setup will allow your rollers to spin freely.
- Assembling the Conveyor Frame: Construct a frame to hold the rollers. Space the rollers evenly and make sure they are level and aligned for smooth operation.
- Mounting the Rollers: Attach the rollers to the frame using your axles. Check that all rollers move freely and adjust if necessary.
- Adding the Belt: Place your plastic conveyor roller belt over the rollers, ensuring it’s tight but not overstretched. Secure the belt at both ends of the conveyor frame.
The Customization Benefits of DIY Rollers
Creating DIY PVC conveyor rollers offers several customization benefits, particularly for specific or unusual applications:
- Cost Efficiency: Building your own rollers can be significantly cheaper than purchasing pre-made systems, especially if you source materials wisely.
- Custom Sizes and Shapes: You can cut and shape your rollers to exact dimensions needed for your operation, which is ideal for non-standard sizes that might not be readily available on the market.
- Adjustable Specifications: You have the control to select materials and designs that best suit the environmental conditions and load requirements of your application, such as using thicker PVC for heavier loads.
- Personal Satisfaction and Adaptability: There’s a personal satisfaction in building something tailored specifically to your needs. Additionally, if operational needs change, you can easily modify or expand your DIY plastic conveyor roller belt system.
By adopting a DIY approach to your plastic conveyor roller belt, you not only gain a deeper understanding of the mechanics behind conveyor systems but also create a system that is perfectly suited to your specific operational needs.
Additional Applications of Plastic Conveyor Roller Belt
The versatility of the plastic conveyor roller belt extends far beyond traditional industrial uses. These durable and adaptable systems can be creatively repurposed for various non-industrial applications, showcasing their flexibility and utility in unexpected areas.
Creative Uses of Plastic Conveyor Roller Belts
The adaptability of plastic conveyor roller belts allows them to be utilized in unique and innovative ways.
- Event Management and Decor: Lightweight and flexible, plastic conveyor roller belts can be transformed into mobile display systems for events. They can carry decorations or even serve as moving walkways for fashion shows, providing a dynamic element to the presentation.
- Fitness and Sports Training: The smooth and continuous surface of a plastic conveyor roller belt makes it ideal for sports training equipment. It can be used in the construction of treadmill-like devices for athletes, providing a controlled environment for endurance training and technique refinement.
- Theater and Stage Productions: In theater productions, plastic conveyor roller belts can be used to create moving stages or automate scene changes, adding a dramatic effect and enhancing the fluidity of performance transitions.
- Education and Demonstrations: Educational institutions can utilize small-scale plastic conveyor roller belts for demonstrations in physics and engineering classes, helping students understand mechanics and motion principles.
- Home and Lifestyle: Beyond industrial and commercial applications, these belts can be creatively used in home improvement projects. For instance, they can be installed in large home libraries or storage rooms to create an automated retrieval system for books or items stored in hard-to-reach places.
- Art Installations and Interactive Displays: Artists and designers can use plastic conveyor roller belts to create kinetic sculptures or interactive displays that involve movement, allowing viewers to engage with art in dynamic ways.
- Beauty Industry Innovations: Mimicking the idea of using plastic rollers for hair, these belts can be adapted for use in large-scale beauty salons to automate parts of the hairstyling process, such as the movement of hair through drying or treatment stations.
Each of these applications demonstrates the innovative potential of repurposing plastic conveyor roller belts. By thinking outside the traditional confines of industrial utility, these belts can be integrated into various aspects of daily life and specialized activities, adding efficiency and creative flair to a wide range of endeavors.
Choosing the Right Plastic Conveyor Roller Belt
Selecting the appropriate plastic conveyor roller belt for your application is critical to ensure efficiency, durability, and cost-effectiveness. This section outlines key considerations to keep in mind when choosing a belt, compares pre-made and DIY options, and provides advice on assessing quality and compatibility.
Considerations When Selecting a Plastic Conveyor Roller Belt
When it comes to choosing the right plastic conveyor roller belt, several factors should be considered to ensure it meets the specific demands of your operation:
- Load Capacity: Consider the weight and type of materials the belt will carry. Ensure the belt’s load capacity aligns with your operational requirements to prevent premature wear or failure.
- Operating Environment: Assess the environmental conditions in which the belt will operate, such as temperature extremes, exposure to chemicals, or moisture. Choose a belt material and design that can withstand these conditions.
- Belt Speed and Throughput: Determine the required speed and volume of material transport. Higher speeds and throughput may require belts with enhanced durability and precise engineering.
- Maintenance and Longevity: Evaluate the expected lifespan and maintenance needs of the belt. Opt for belts that offer ease of maintenance and replacement parts availability to reduce downtime.
Comparisons Between Pre-made and DIY Options
To further assist in decision-making, here is a table comparing the key aspects of pre-made versus DIY plastic conveyor roller belts:
Feature | Pre-made Plastic Conveyor Roller Belt | DIY Plastic Conveyor Roller Belt |
---|---|---|
Cost | Generally higher initial cost but comes with guarantees and support. | Lower initial cost, but may incur extra expenses in tools or materials not readily available. |
Quality | Consistent quality and performance, as it is manufactured to industry standards. | Quality varies depending on the skill level and materials used; potentially less reliable. |
Customization | Limited to available models and specifications; custom orders might be expensive. | Highly customizable to specific needs and dimensions, offering flexibility. |
Time and Effort | Immediate use upon purchase; no assembly required. | Requires time and effort to design, source materials, and assemble. |
Support and Warranty | Typically includes customer support and a manufacturer warranty. | No formal support or warranty; reliant on personal ability to troubleshoot and repair. |
Advice on Assessing Quality and Compatibility for Specific Uses
When assessing the quality and compatibility of a plastic conveyor roller belt, consider the following:
- Material Composition: Research the materials used in the belt’s construction. High-quality plastics like polyurethane or nylon offer better wear resistance and durability.
- Manufacturer Reputation: Choose belts from reputable manufacturers known for quality. Read reviews and case studies to gauge user satisfaction and product performance.
- Compatibility Testing: If possible, test the belt under conditions similar to those in your facility to observe its performance. This can include load tests, speed assessments, and durability trials.
- Consult Experts: Engage with conveyor system experts or engineers who can provide insights based on experience and industry knowledge, ensuring that the belt you choose is ideally suited to your specific needs.
By carefully considering these aspects, you can make an informed decision on whether a pre-made or DIY plastic conveyor roller belt is right for you, and ensure that the belt you select will perform optimally in your specific application.
Fill out this form to get a prompt response about our plastic conveyor roller belt.
FAQs About Plastic Conveyor Roller Belt
In belt conveyors, rollers are a critical component, serving to support and move the conveyor belt along its length. The most common type of roller used is the idler roller. These rollers are strategically spaced along the conveyor path and are not powered; they simply spin freely to allow the conveyor belt to move smoothly. Other types include drive rollers, which are powered and help propel the belt, and return rollers, which support the belt on its return path. Materials used for rollers vary depending on the specific needs of the application, including steel, stainless steel, or heavy-duty plastic. Each material offers different benefits, such as durability, resistance to corrosion, and suitability for different environmental conditions.
Roller conveyors can be made from a variety of materials, each selected based on the specific requirements of the application and operating environment. The most common materials include metal (such as steel or aluminum), plastic, and sometimes a combination of both. Steel rollers are favored for their strength and durability, making them suitable for heavy loads and harsh environments. Aluminum rollers are lighter and resist corrosion, suitable for lighter loads and cleaner environments, such as food processing or pharmaceutical industries. Plastic rollers are used for their quiet operation, corrosion resistance, and lighter weight, ideal for lighter loads and when cost is a consideration.
A belt over roller conveyor combines elements of belt and roller conveyors, featuring a belt driven by rollers underneath it. This design provides the smooth, continuous surface of a belt conveyor with the added support of rollers beneath. This setup enhances the conveyor’s ability to handle heavier loads with more control and less friction, making it ideal for transporting large or bulky items. The rollers help reduce the belt’s contact area with the load, decreasing wear and energy consumption. Belt over roller conveyors is particularly effective in facilities where sorting, packing, and assembly processes require precise control and positioning of items.
Belt roller support material refers to the materials used in the construction of the rollers that support and drive conveyor belts. These materials must be chosen based on their ability to withstand operational stresses, including load, speed, and environmental conditions. Common materials include high-impact plastics, such as polypropylene or nylon, and metals like steel or aluminum. Plastic rollers are lightweight and offer good resistance to corrosion and chemical exposure, while metal rollers provide greater strength and durability. The choice of material affects the conveyor’s performance, maintenance needs, and longevity, making it crucial to select based on the specific needs of the application and operational environment.
Conveyor systems play a pivotal role in numerous industries, fundamentally transforming the landscape of manufacturing, distribution, and warehousing. At the heart of these systems are the conveyor roller types, each selected to optimize efficiency and adapt to varying operational demands. Understanding the different conveyor roller types is crucial as they directly influence the effectiveness, speed, and reliability of a conveyor system. Industries ranging from automotive to food processing rely heavily on these systems to streamline operations and reduce labor costs. By exploring the variety and functionality of conveyor roller types, businesses can significantly enhance their production processes and operational efficiency. This introduction will delve into the significance of these components and their profound impact on industry dynamics.
Read moreUnderstanding the conveyor roller belt hs code is pivotal for companies involved in international trade, as these codes categorize products for tariffs and statistics. The general conveyor roller belt hs code used globally is 843139 can be used for an export declaration, affects shipment data, import eligibility… Harmonized System (HS) Codes play an essential role in streamlining customs operations and enhancing the accuracy of trade statistics globally. Within India, the Goods and Services Tax (GST) applies standardized taxation based on these HS classifications, directly affecting the financial outcomes for businesses. Conveyor systems, which often incorporate roller belts, are integral to industries like manufacturing, logistics, and warehousing due to their efficiency in moving goods. This introduction outlines the significance of knowing the conveyor roller belt hs code for optimizing trade operations and compliance with tax regulations.
Read moreConveyor rollers are fundamental components in the automation of manufacturing, distribution, and packaging processes. A conveyor roller company plays a critical role in enhancing the efficiency of production lines across various industries, from automotive to food processing. These rollers facilitate the smooth and rapid movement of goods and materials, significantly reducing labor costs and increasing throughput. Moreover, the versatility of conveyor rollers allows their application in diverse settings, accommodating different weights, sizes, and types of materials. As industries strive for higher productivity and lower operational costs, the demand for innovative solutions from a conveyor roller company continues to grow, highlighting their pivotal role in modern industrial operations.
Read moreContact us
No. 11, Bocheng Street, Boye County, Baoding City, Hebei Province, China
+86 13803289191
NEWS
- How a Multi Ply Conveyor Belt Enhances EfficiencyJune 18, 2024 -
- What is Conveyor Belt Ply and Conveyor Belt Ply AdhesionJune 18, 2024 -
- Necessary Cold Resistant Conveyor BeltJune 18, 2024 -