NN Conveyor Belt: Enhancing Industrial Efficiency
NN conveyor belt systems are essential components in a wide range of industrial applications. These belts, known for their high tensile strength and durability, are critical in industries such as mining, manufacturing, and logistics. The NN conveyor belt, constructed with nylon fabric, offers excellent resistance to wear and tear, ensuring reliable performance under heavy load conditions. Its ability to operate efficiently in harsh environments makes it a preferred choice for many industries. By integrating the NN conveyor belt into their operations, businesses can enhance productivity and reduce maintenance costs, leading to overall operational efficiency.
NN Conveyor Belt: What is EP Conveyor Belt
EP conveyor belts are a type of synthetic rubber conveyor belt that is widely used in various industries for handling bulk materials. The “EP” stands for polyester (E) and polyamide (P), which are the two materials used in the fabric of the belt. These materials provide the belt with high tensile strength and low elongation, making it suitable for heavy-duty applications.
Construction of EP Conveyor Belts
EP conveyor belts are constructed with multiple layers of synthetic fabric that are bonded together with rubber. The typical structure of an EP conveyor belt includes:
- Top Cover The top cover is made of a high-quality rubber compound that is resistant to abrasion, heat, and chemicals. This layer protects the belt from the harsh conditions it encounters during operation.
- Carcass The carcass is the core of the EP conveyor belt and is made up of multiple layers of synthetic fabric. The fabric layers are bonded together with rubber, providing the belt with its tensile strength and flexibility. The polyester fabric (E) in the warp direction provides high tensile strength, while the polyamide fabric (P) in the weft direction provides low elongation and excellent resistance to impacts and tears.
- Bottom Cover Similar to the top cover, the bottom cover is also made of rubber. It protects the belt from wear and tear caused by the pulleys and conveyor structure.
Advantages of EP Conveyor Belts
EP conveyor belts offer several advantages over other types of conveyor belts:
- High Tensile Strength The polyester fabric in the EP conveyor belt provides high tensile strength, making it suitable for heavy-duty applications where the belt needs to carry large loads over long distances.
- Low Elongation The low elongation property of the polyamide fabric ensures that the belt maintains its shape and does not stretch excessively during operation. This results in consistent performance and reduced maintenance.
- Excellent Impact Resistance The combination of polyester and polyamide fabrics gives the EP conveyor belt excellent resistance to impacts and tears, ensuring durability and longevity.
- Heat and Chemical Resistance The rubber covers of the EP conveyor belt are formulated to resist heat and chemicals, making the belt suitable for handling hot and corrosive materials.
- Flexibility The synthetic fabrics used in the EP conveyor belt provide flexibility, allowing the belt to bend and flex around the pulleys and conveyor structure without cracking or breaking.
Applications of EP Conveyor Belts
EP conveyor belts are used in a wide range of industries and applications, including:
- Mining EP conveyor belts are commonly used in the mining industry for transporting ores, coal, and other bulk materials over long distances. The high tensile strength and durability of the belts make them ideal for the harsh conditions of mining operations.
- Construction In the construction industry, EP conveyor belts are used for transporting construction materials such as sand, gravel, and cement. The belts’ resistance to abrasion and impact ensures reliable performance in demanding construction environments.
- Agriculture EP conveyor belts are used in agricultural applications for transporting grains, seeds, and other agricultural products. The belts’ flexibility and resistance to chemicals make them suitable for use in agricultural settings.
- Manufacturing In manufacturing facilities, EP conveyor belts are used for conveying raw materials, components, and finished products. The belts’ high tensile strength and low elongation ensure efficient and reliable material handling.
EP conveyor belts are a versatile and durable type of synthetic rubber conveyor belt that offers high tensile strength, low elongation, and excellent resistance to impacts, heat, and chemicals. Their construction with multiple layers of synthetic fabric bonded with rubber makes them suitable for a wide range of heavy-duty applications in various industries.
NN Conveyor Belt Parts
NN conveyor belts, also known as nylon conveyor belts, are widely used in industrial applications for handling bulk materials. The “NN” stands for nylon, which is the primary material used in the fabric of the belt. NN conveyor belts are known for their high tensile strength, flexibility, and resistance to wear and tear. This section explores the different parts that make up an NN conveyor belt and their respective functions.
Construction of NN Conveyor Belts
NN conveyor belts are constructed with multiple layers of nylon fabric that are bonded together with rubber. The typical structure of an NN conveyor belt includes the following parts:
- Top Cover The top cover of an NN conveyor belt is made of a high-quality rubber compound that provides protection against abrasion, heat, and chemicals. This layer is designed to withstand the harsh conditions encountered during material handling and to protect the underlying fabric layers.
- Carcass The carcass is the core of the NN conveyor belt and consists of multiple layers of nylon fabric. The nylon fabric provides the belt with high tensile strength, flexibility, and resistance to impacts and tears. The carcass is bonded together with rubber to ensure the integrity and durability of the belt.
- Bottom Cover The bottom cover of the NN conveyor belt is also made of rubber. It protects the belt from wear and tear caused by contact with the pulleys and conveyor structure. The bottom cover ensures smooth operation and reduces the risk of damage to the belt.
- Skim Coats Skim coats are thin layers of rubber applied between the fabric plies in the carcass. These layers improve the adhesion between the fabric layers and enhance the overall strength and flexibility of the belt. Skim coats also provide additional protection against impacts and wear.
- Breaker Plies Breaker plies are additional layers of fabric or rubber that are placed between the top cover and the carcass. These layers help to distribute the load evenly across the belt and reduce the risk of punctures and tears. Breaker plies enhance the belt’s resistance to impact and improve its overall durability.
Advantages of NN Conveyor Belts
NN conveyor belts offer several advantages due to their construction with nylon fabric:
- High Tensile Strength The nylon fabric used in NN conveyor belts provides high tensile strength, making them suitable for heavy-duty applications where the belt needs to carry large loads over long distances.
- Flexibility Nylon fabric is known for its flexibility, allowing NN conveyor belts to bend and flex around the pulleys and conveyor structure without cracking or breaking. This flexibility ensures smooth operation and reduces the risk of belt damage.
- Resistance to Wear and Tear NN conveyor belts have excellent resistance to abrasion, impacts, and tears. The nylon fabric and rubber covers provide a durable and long-lasting solution for material handling applications.
- Heat and Chemical Resistance The rubber covers of NN conveyor belts are formulated to resist heat and chemicals, making the belts suitable for handling hot and corrosive materials.
- Lightweight Nylon fabric is lightweight, which reduces the overall weight of the NN conveyor belt. This lightweight nature contributes to energy efficiency and reduces the load on the conveyor system.
Applications of NN Conveyor Belts
NN conveyor belts are used in a wide range of industries and applications, including:
- Mining NN conveyor belts are commonly used in the mining industry for transporting ores, coal, and other bulk materials. The belts’ high tensile strength and durability make them ideal for the harsh conditions of mining operations.
- Construction In the construction industry, NN conveyor belts are used for transporting construction materials such as sand, gravel, and cement. The belts’ resistance to abrasion and impact ensures reliable performance in demanding construction environments.
- Agriculture NN conveyor belts are used in agricultural applications for transporting grains, seeds, and other agricultural products. The belts’ flexibility and resistance to chemicals make them suitable for use in agricultural settings.
- Manufacturing In manufacturing facilities, NN conveyor belts are used for conveying raw materials, components, and finished products. The belts’ high tensile strength and flexibility ensure efficient and reliable material handling.
NN conveyor belts are a versatile and durable type of conveyor belt that offers high tensile strength, flexibility, and resistance to wear and tear. Their construction with multiple layers of nylon fabric bonded with rubber makes them suitable for a wide range of heavy-duty applications in various industries.
NN Conveyor Belt: EP Conveyor Belt Specification
EP conveyor belts are designed to meet specific performance requirements and are manufactured according to industry standards. This section provides an in-depth discussion of the specifications of EP conveyor belts, including the EP 400/3 type.
Key Specifications of EP Conveyor Belts
EP conveyor belts are specified based on several key parameters, including tensile strength, number of plies, cover thickness, and belt width. These specifications ensure that the belt meets the performance requirements of the application.
- Tensile Strength The tensile strength of an EP conveyor belt is a measure of its ability to withstand pulling forces without breaking. It is typically specified in newtons per millimeter (N/mm) or pounds per inch (lbs/in). EP conveyor belts are available in various tensile strengths, ranging from 100 N/mm to 2,500 N/mm, depending on the application requirements.
- Number of Plies The number of plies in an EP conveyor belt refers to the number of layers of synthetic fabric in the carcass. Common configurations include 2-ply, 3-ply, and 4-ply belts, although belts with more plies are available for heavy-duty applications. The number of plies affects the belt’s strength, flexibility, and durability.
- Cover Thickness The cover thickness of an EP conveyor belt is specified for both the top and bottom covers. The thickness is typically measured in millimeters (mm) or inches (in) and ranges from 1.5 mm to 15 mm. The cover thickness affects the belt’s resistance to abrasion, heat, and chemicals.
- Belt Width EP conveyor belts are available in various widths to accommodate different conveyor systems. Common widths range from 300 mm to 2,400 mm, with custom widths available upon request. The belt width should match the width of the conveyor system to ensure proper fit and performance.
EP 400/3 Conveyor Belt
The EP 400/3 conveyor belt is a specific type of EP conveyor belt that is widely used in various industries. The “400/3” designation refers to the belt’s tensile strength and the number of plies in the carcass.
- Tensile Strength The EP 400/3 conveyor belt has a tensile strength of 400 N/mm, making it suitable for medium to heavy-duty applications. This tensile strength ensures that the belt can handle significant loads without breaking.
- Number of Plies The “3” in the EP 400/3 designation indicates that the belt has three plies of synthetic fabric in the carcass. The three-ply construction provides a balance of strength, flexibility, and durability.
- Cover Thickness The cover thickness of the EP 400/3 conveyor belt can be customized to meet specific application requirements. Common configurations include a top cover thickness of 6 mm and a bottom cover thickness of 2 mm, although other thicknesses are available.
- Applications The EP 400/3 conveyor belt is used in a wide range of applications, including mining, construction, agriculture, and manufacturing. Its high tensile strength, durability, and flexibility make it suitable for transporting bulk materials over long distances.
Industry Standards for EP Conveyor Belts
EP conveyor belts are manufactured according to industry standards to ensure consistent quality and performance. These standards provide guidelines for the design, manufacturing, testing, and installation of EP conveyor belts. Some of the key standards include:
- ISO 14890 The International Organization for Standardization (ISO) 14890 standard specifies the requirements for rubber and plastic conveyor belts, including EP conveyor belts. The standard covers the classification, marking, and physical properties of conveyor belts.
- DIN 22102 The German Institute for Standardization (DIN) 22102 standard specifies the requirements for textile-reinforced conveyor belts, including EP conveyor belts. The standard covers the dimensions, tolerances, and physical properties of conveyor belts.
- AS 1332 The Australian Standard (AS) 1332 specifies the requirements for conveyor belting, including EP conveyor belts. The standard covers the classification, dimensions, and physical properties of conveyor belts.
- CEMA The Conveyor Equipment Manufacturers Association (CEMA) provides guidelines and standards for the design, manufacturing, and installation of conveyor belts, including EP conveyor belts. CEMA standards ensure the safety and performance of conveyor systems.
Conveyor Belt Specification Standards PDF
For detailed information on the specifications and standards for EP conveyor belts, several PDF documents are available from industry organizations and manufacturers. These documents provide comprehensive guidelines for the selection, design, and installation of EP conveyor belts. Examples include:
- ISO 14890 Conveyor Belts – Specification for Rubber or Plastics Covered Conveyor Belting This PDF document provides detailed information on the classification, marking, and physical properties of EP conveyor belts, as specified by ISO 14890.
- DIN 22102 Textile Conveyor Belts for General Purposes This PDF document provides detailed information on the dimensions, tolerances, and physical properties of EP conveyor belts, as specified by DIN 22102.
- AS 1332 Conveyor Belting – Textiles Reinforced This PDF document provides detailed information on the classification, dimensions, and physical properties of EP conveyor belts, as specified by AS 1332.
- CEMA Belt Conveyors for Bulk Materials This PDF document provides guidelines and standards for the design, manufacturing, and installation of EP conveyor belts, as specified by CEMA.
EP conveyor belts are designed and manufactured according to industry standards to ensure consistent quality and performance. The specifications of EP conveyor belts, including tensile strength, number of plies, cover thickness, and belt width, are critical for meeting the performance requirements of various applications. The EP 400/3 conveyor belt is a specific type of EP conveyor belt that is widely used in various industries due to its high tensile strength, durability, and flexibility. Industry standards and PDF documents provide comprehensive guidelines for the selection, design, and installation of EP conveyor belts.
NN Conveyor Belt: NN Belt Construction and Features
NN belts, also known as nylon conveyor belts, are widely used in industrial applications for handling bulk materials. The construction and features of NN belts make them suitable for a wide range of applications. This section provides a detailed description of the construction and key features of NN belts.
Construction of NN Belts
NN belts are constructed with multiple layers of nylon fabric that are bonded together with rubber. The typical structure of an NN belt includes the following components:
- Top Cover The top cover of an NN belt is made of a high-quality rubber compound that provides protection against abrasion, heat, and chemicals. This layer is designed to withstand the harsh conditions encountered during material handling and to protect the underlying fabric layers.
- Carcass The carcass is the core of the NN belt and consists of multiple layers of nylon fabric. The nylon fabric provides the belt with high tensile strength, flexibility, and resistance to impacts and tears. The carcass is bonded together with rubber to ensure the integrity and durability of the belt.
- Bottom Cover The bottom cover of the NN belt is also made of rubber. It protects the belt from wear and tear caused by contact with the pulleys and conveyor structure. The bottom cover ensures smooth operation and reduces the risk of damage to the belt.
- Skim Coats Skim coats are thin layers of rubber applied between the fabric plies in the carcass. These layers improve the adhesion between the fabric layers and enhance the overall strength and flexibility of the belt. Skim coats also provide additional protection against impacts and wear.
- Breaker Plies Breaker plies are additional layers of fabric or rubber that are placed between the top cover and the carcass. These layers help to distribute the load evenly across the belt and reduce the risk of punctures and tears. Breaker plies enhance the belt’s resistance to impact and improve its overall durability.
Key Features of NN Belts
NN belts offer several key features due to their construction with nylon fabric:
- High Tensile Strength The nylon fabric used in NN belts provides high tensile strength, making them suitable for heavy-duty applications where the belt needs to carry large loads over long distances.
- Flexibility Nylon fabric is known for its flexibility, allowing NN belts to bend and flex around the pulleys and conveyor structure without cracking or breaking. This flexibility ensures smooth operation and reduces the risk of belt damage.
- Resistance to Wear and Tear NN belts have excellent resistance to abrasion, impacts, and tears. The nylon fabric and rubber covers provide a durable and long-lasting solution for material handling applications.
- Heat and Chemical Resistance The rubber covers of NN belts are formulated to resist heat and chemicals, making the belts suitable for handling hot and corrosive materials.
- Lightweight Nylon fabric is lightweight, which reduces the overall weight of the NN belt. This lightweight nature contributes to energy efficiency and reduces the load on the conveyor system.
Applications of NN Belts
NN belts are used in a wide range of industries and applications, including:
- Mining NN belts are commonly used in the mining industry for transporting ores, coal, and other bulk materials. The belts’ high tensile strength and durability make them ideal for the harsh conditions of mining operations.
- Construction In the construction industry, NN belts are used for transporting construction materials such as sand, gravel, and cement. The belts’ resistance to abrasion and impact ensures reliable performance in demanding construction environments.
- Agriculture NN belts are used in agricultural applications for transporting grains, seeds, and other agricultural products. The belts’ flexibility and resistance to chemicals make them suitable for use in agricultural settings.
- Manufacturing In manufacturing facilities, NN belts are used for conveying raw materials, components, and finished products. The belts’ high tensile strength and flexibility ensure efficient and reliable material handling.
Maintenance of NN Belts
Proper maintenance is essential for ensuring the long-term performance and durability of NN belts. Regular inspections and maintenance can help detect issues early and prevent costly downtime and repairs. Key maintenance practices for NN belts include:
- Regular Inspections Conduct regular inspections of the NN belt to check for signs of wear, damage, or misalignment. Look for any visible defects such as cracks, grooves, or tears on the belt’s surface.
- Alignment Checks Ensure that the NN belt is properly aligned and that there are no signs of misalignment. Misaligned belts can cause increased friction, leading to excessive wear and potential failure.
- Lubrication Proper lubrication is essential for the smooth operation of NN belts. Ensure that the belt is receiving adequate lubrication and that the lubrication system is functioning correctly.
- Tension Adjustment Maintain the proper tension in the NN belt to ensure optimal performance. Over-tensioning or under-tensioning can cause excessive wear and reduce the belt’s lifespan.
- Cleaning Keep the NN belt clean and free from debris, dirt, and contaminants. Regular cleaning helps prevent damage to the belt and ensures smooth operation.
NN belts are a versatile and durable type of conveyor belt that offers high tensile strength, flexibility, and resistance to wear and tear. Their construction with multiple layers of nylon fabric bonded with rubber makes them suitable for a wide range of heavy-duty applications in various industries. Proper maintenance is essential for ensuring the long-term performance and durability of NN belts.
NN Conveyor Belt: Conveyor Belt Nomenclature
The nomenclature of conveyor belts, including NN conveyor belt, is essential for understanding and selecting the appropriate belt for specific industrial applications. Conveyor belt nomenclature involves a series of abbreviations, numbers, and specifications that describe the belt’s construction, materials, and performance characteristics. This section provides a detailed guide on the nomenclature used for conveyor belts, focusing on EP and NN types.
General Nomenclature Components
Conveyor belt nomenclature typically includes the following components:
- Type of Fabric The type of fabric used in the belt’s carcass is denoted by abbreviations such as EP (polyester/nylon) and NN (nylon/nylon). This indicates the materials used in the warp and weft directions, which affect the belt’s tensile strength, flexibility, and resistance to wear.
- Tensile Strength The tensile strength of the conveyor belt is usually expressed in newtons per millimeter (N/mm) or pounds per inch (lbs/in). This specification indicates the maximum stress the belt can withstand without breaking.
- Number of Plies The number of plies refers to the layers of fabric in the belt’s carcass. Common configurations include 2-ply, 3-ply, and 4-ply belts. The number of plies affects the belt’s strength, flexibility, and durability.
- Cover Thickness The thickness of the top and bottom covers is specified in millimeters (mm) or inches (in). This affects the belt’s resistance to abrasion, heat, and chemicals.
- Belt Width The width of the conveyor belt is specified in millimeters (mm) or inches (in). It should match the width of the conveyor system to ensure proper fit and performance.
EP Conveyor Belt Nomenclature
EP conveyor belts are identified by the abbreviation “EP” followed by the tensile strength and number of plies. For example, EP 400/3 indicates an EP conveyor belt with a tensile strength of 400 N/mm and three plies of fabric. The construction and specifications of EP conveyor belts are as follows:
- EP (Polyester/Nylon) EP conveyor belts are made with polyester fabric in the warp direction and nylon fabric in the weft direction. This combination provides high tensile strength and low elongation, making EP belts suitable for heavy-duty applications.
- Tensile Strength The tensile strength is indicated by a number following the “EP” abbreviation. For example, EP 400/3 has a tensile strength of 400 N/mm.
- Number of Plies The number of plies is indicated by a number after the tensile strength. For example, EP 400/3 has three plies of fabric.
- Cover Thickness The cover thickness is specified separately for the top and bottom covers. For example, a common configuration is 6/2, where the top cover is 6 mm thick, and the bottom cover is 2 mm thick.
- Belt Width The belt width is specified in millimeters (mm) or inches (in). For example, a belt with a width of 1,000 mm is suitable for a 1,000 mm wide conveyor system.
NN Conveyor Belt Nomenclature
NN conveyor belts are identified by the abbreviation “NN” followed by the tensile strength and number of plies. For example, NN 300/2 indicates an NN conveyor belt with a tensile strength of 300 N/mm and two plies of fabric. The construction and specifications of NN conveyor belts are as follows:
- NN (Nylon/Nylon) NN conveyor belts are made with nylon fabric in both the warp and weft directions. This provides high tensile strength, flexibility, and resistance to wear and tear.
- Tensile Strength The tensile strength is indicated by a number following the “NN” abbreviation. For example, NN 300/2 has a tensile strength of 300 N/mm.
- Number of Plies The number of plies is indicated by a number after the tensile strength. For example, NN 300/2 has two plies of fabric.
- Cover Thickness The cover thickness is specified separately for the top and bottom covers. For example, a common configuration is 4/2, where the top cover is 4 mm thick, and the bottom cover is 2 mm thick.
- Belt Width The belt width is specified in millimeters (mm) or inches (in). For example, a belt with a width of 800 mm is suitable for an 800 mm wide conveyor system.
Additional Nomenclature Elements
In addition to the basic components, conveyor belt nomenclature may include additional elements that specify specific properties or features of the belt. These elements include:
- Cover Grade The cover grade indicates the type of rubber compound used in the top and bottom covers. Common grades include abrasion-resistant (AR), heat-resistant (HR), oil-resistant (OR), and flame-resistant (FR). These grades ensure the belt’s suitability for specific environmental conditions.
- Special Features Special features may be indicated by additional abbreviations or numbers. For example, a belt with enhanced flexibility may be denoted as “FLEX,” while a belt with extra resistance to impacts may be denoted as “IMPACT.”
- Temperature Range The temperature range indicates the operating temperature limits of the conveyor belt. This is crucial for applications involving extreme temperatures, such as high-temperature furnaces or freezing environments.
Examples of Conveyor Belt Nomenclature
Here are some examples of conveyor belt nomenclature and their interpretations:
- EP 500/4 6/2 1000 AR
- EP: Polyester/nylon fabric
- 500: Tensile strength of 500 N/mm
- 4: Four plies of fabric
- 6/2: Top cover thickness of 6 mm and bottom cover thickness of 2 mm
- 1000: Belt width of 1,000 mm
- AR: Abrasion-resistant cover grade
- NN 400/3 5/3 1200 HR
- NN: Nylon/nylon fabric
- 400: Tensile strength of 400 N/mm
- 3: Three plies of fabric
- 5/3: Top cover thickness of 5 mm and bottom cover thickness of 3 mm
- 1200: Belt width of 1,200 mm
- HR: Heat-resistant cover grade
Importance of Conveyor Belt Nomenclature
Understanding conveyor belt nomenclature is crucial for selecting the appropriate belt for specific applications. Proper selection ensures optimal performance, durability, and efficiency of the conveyor system. Key benefits of understanding conveyor belt nomenclature include:
- Accurate Selection Conveyor belt nomenclature provides detailed information about the belt’s construction, materials, and performance characteristics. This information helps in selecting the right belt for the specific requirements of the application.
- Compatibility Properly understanding the nomenclature ensures that the selected belt is compatible with the existing conveyor system. This prevents issues related to fit, alignment, and performance.
- Performance Optimization Selecting the right conveyor belt based on its nomenclature ensures that the belt meets the performance requirements of the application. This includes factors such as load capacity, speed, and resistance to environmental conditions.
- Cost Efficiency Understanding conveyor belt nomenclature helps in selecting a belt that provides the best balance of performance and cost. This ensures that the investment in the conveyor system is optimized for long-term efficiency and reliability.
Conveyor belt nomenclature, including that of NN conveyor belts, provides essential information about the belt’s construction, materials, and performance characteristics. Understanding the nomenclature helps in selecting the appropriate belt for specific applications, ensuring compatibility, performance optimization, and cost efficiency. By following the guidelines provided in this detailed guide, users can make informed decisions when selecting conveyor belts for their industrial applications.
Maintenance Tips for NN Conveyor Belt
Proper maintenance of NN conveyor belts is essential for ensuring their long-term performance and reliability. Regular maintenance practices help prevent costly downtime, reduce the risk of belt failure, and extend the lifespan of the conveyor system. This section provides practical tips and best practices for maintaining NN conveyor belts.
Regular Inspections
Conducting regular inspections of NN conveyor belts is crucial for identifying potential issues early and preventing them from escalating into major problems. Key areas to inspect include:
- Belt Surface Inspect the belt surface for signs of wear, damage, or contamination. Look for cracks, grooves, tears, or any other visible defects. Address any issues promptly to prevent further damage.
- Alignment Check the alignment of the NN conveyor belt to ensure it is running straight and true. Misaligned belts can cause increased friction, leading to excessive wear and potential failure. Adjust the alignment as needed to maintain optimal performance.
- Tension Ensure that the NN conveyor belt is properly tensioned. Over-tensioning or under-tensioning can cause excessive wear and reduce the belt’s lifespan. Use a tension meter to measure the tension and adjust it according to the manufacturer’s recommendations.
- Pulleys and Rollers Inspect the pulleys and rollers for signs of wear, damage, or misalignment. Ensure that they are clean and free from debris. Replace any worn or damaged components to prevent damage to the belt.
- Bearings Check the bearings for signs of wear, noise, or excessive play. Properly functioning bearings are essential for smooth operation and reduced wear on the belt. Lubricate or replace bearings as needed.
Lubrication
Proper lubrication is essential for the smooth operation of NN
conveyor belts and the associated components. Key lubrication practices include:
- Lubricate Bearings Regularly lubricate the bearings to ensure smooth rotation and reduce friction. Use the appropriate type of lubricant as specified by the manufacturer. Over-lubrication or under-lubrication can cause issues, so follow the recommended lubrication schedule.
- Lubricate Pulleys and Rollers Lubricate the pulleys and rollers to reduce friction and wear. Ensure that the lubricant does not contaminate the belt surface. Use lubricants that are compatible with the materials used in the conveyor system.
Cleaning
Keeping NN conveyor belts clean is essential for maintaining their performance and longevity. Key cleaning practices include:
- Regular Cleaning Regularly clean the belt surface to remove dirt, debris, and contaminants. Use a soft brush or cloth to gently clean the belt. Avoid using harsh chemicals or abrasive tools that can damage the belt.
- Prevent Contamination Prevent contamination of the belt surface by ensuring that the work environment is clean and free from debris. Implement measures to contain spills and prevent foreign objects from coming into contact with the belt.
- Cleaning Solutions Use appropriate cleaning solutions that are compatible with the materials used in the NN conveyor belt. Avoid using solvents or chemicals that can degrade the belt’s rubber covers or nylon fabric.
Repairing Minor Damage
Addressing minor damage promptly can prevent it from escalating into major issues. Key repair practices include:
- Patch Repairs For small cuts or tears on the belt surface, use patch repairs to reinforce the damaged area. Use repair materials that are compatible with the belt’s rubber covers and nylon fabric.
- Edge Repairs For damage to the edges of the belt, use edge repair kits to restore the belt’s integrity. Properly repaired edges prevent further wear and reduce the risk of belt failure.
- Vulcanized Splicing For larger damage or when joining sections of the belt, use vulcanized splicing techniques to create strong and durable joints. Vulcanized splices provide seamless connections that maintain the belt’s strength and flexibility.
Monitoring and Documentation
Monitoring the condition of NN conveyor belts and maintaining detailed documentation are essential for effective maintenance management. Key practices include:
- Condition Monitoring Use condition monitoring tools and techniques to track the performance and condition of NN conveyor belts. This includes monitoring belt tension, alignment, and wear. Implement predictive maintenance techniques to identify potential issues before they lead to failure.
- Maintenance Records Maintain detailed records of all maintenance activities, including inspections, repairs, lubrication, and cleaning. Document the condition of the belt and any issues identified during inspections. Use this information to track the belt’s performance and schedule preventive maintenance activities.
- Replacement Planning Plan for the replacement of NN conveyor belts based on their condition and performance. Use the maintenance records to determine the optimal replacement intervals and avoid unexpected downtime.
Training and Safety
Proper training and safety practices are essential for maintaining NN conveyor belts. Key practices include:
- Training Ensure that maintenance personnel are properly trained in the inspection, maintenance, and repair of NN conveyor belts. Provide training on the specific procedures and tools required for maintaining the belts. Regularly update training programs to include new techniques and best practices.
- Safety Procedures Implement safety procedures to protect maintenance personnel during inspections and repairs. This includes using appropriate personal protective equipment (PPE), following lockout/tagout (LOTO) procedures, and adhering to safety guidelines.
- Risk Assessment Conduct risk assessments to identify potential hazards associated with maintaining NN conveyor belts. Implement measures to mitigate identified risks and ensure a safe working environment.
Proper maintenance of NN conveyor belt is essential for ensuring their long-term performance and reliability. Regular inspections, lubrication, cleaning, and repairs help prevent costly downtime and extend the lifespan of the conveyor system. Monitoring and documentation, along with proper training and safety practices, further enhance the effectiveness of maintenance activities. By following these practical tips and best practices, operators can ensure the continued smooth operation of NN conveyor belts in various industrial applications.
FAQs about NN Conveyor Belt
NN in conveyor belts stands for “Nylon-Nylon.” It refers to the type of fabric used in the construction of the conveyor belt. Nylon-Nylon conveyor belts are made with both the warp and weft (lengthwise and crosswise threads) using nylon fibers. This type of construction provides several advantages:
High Strength: Nylon-Nylon belts are known for their high tensile strength, making them suitable for heavy-duty applications.
Durability: They offer excellent resistance to wear and tear, ensuring a long service life.
Flexibility: These belts are highly flexible, which allows for better performance in systems with smaller pulley diameters.
Moisture Resistance: Nylon fibers provide good resistance to moisture, making NN belts suitable for wet environments.
NN conveyor belts are commonly used in industries such as mining, construction, and manufacturing due to their robustness and reliability.
Conveyor belts come in various types, each designed for specific applications. The three main types of conveyor belts are:
General Purpose Belts:
These belts are used in a wide range of industries and are designed to handle various materials. They are made from rubber or PVC and are suitable for transporting items in packaging, logistics, and manufacturing processes.
Heavy-Duty Belts:
Heavy-duty belts are designed for transporting large, heavy materials. They are typically used in mining, construction, and bulk material handling industries. These belts are made from robust materials such as steel-reinforced rubber, ensuring they can withstand high loads and harsh conditions.
Specialty Belts:
Specialty belts are designed for specific applications that require unique properties. Examples include heat-resistant belts for high-temperature environments, food-grade belts for the food processing industry, and magnetic belts for separating ferrous materials from non-ferrous materials.
Each type of conveyor belt is engineered to meet the specific needs of different applications, ensuring optimal performance and efficiency.
Several companies are recognized as leading manufacturers of conveyor belts, known for their innovation, quality, and reliability. Some of the top conveyor belt manufacturers include:
Continental AG:
Continental is a global leader in conveyor belt manufacturing, offering a wide range of products for various industries, including mining, agriculture, and manufacturing. They are known for their advanced technology and high-quality materials.
Fenner Dunlop:
With a strong presence in the mining industry, Fenner Dunlop specializes in producing heavy-duty conveyor belts that can withstand extreme conditions. Their products are known for their durability and reliability.
Bridgestone Corporation:
Bridgestone is renowned for its high-performance conveyor belts, particularly in the mining and construction sectors. Their belts are designed to handle heavy loads and challenging environments.
Habasit:
Habasit is a leading manufacturer of lightweight conveyor belts, catering to industries such as food processing, logistics, and automotive. They are known for their innovative designs and high-quality materials.
Ammeraal Beltech:
Ammeraal Beltech offers a wide range of conveyor belts for various applications, including food processing, logistics, and textile industries. They are recognized for their extensive product range and customization options.
These manufacturers are known for their commitment to quality and continuous innovation, ensuring their products meet the evolving needs of various industries.
Grade 1 and Grade 2 conveyor belts refer to the quality and strength of the rubber used in the belt’s construction. The primary differences between the two grades are:
Tensile Strength:
Grade 1: These belts have a higher tensile strength, making them suitable for heavy-duty applications where high impact and abrasion resistance are required. They are commonly used in mining, construction, and bulk material handling industries.
Grade 2: These belts have a lower tensile strength compared to Grade 1 belts but are still durable and reliable. They are used in less demanding applications where extreme strength is not necessary.
Abrasion Resistance:
Grade 1: Offers superior abrasion resistance, making them ideal for transporting abrasive materials such as rocks, ores, and minerals.
Grade 2: While still resistant to abrasion, these belts are better suited for transporting less abrasive materials, such as grains, packaged goods, and light industrial products.
Cost:
Grade 1: Generally more expensive due to the higher quality of rubber and enhanced performance characteristics.
Grade 2: More cost-effective, providing a balance between durability and affordability for less demanding applications.
Choosing between Grade 1 and Grade 2 conveyor belts depends on the specific requirements of the application, including the type of materials being transported and the operating conditions.
Last Updated on August 14, 2024 by Jordan Smith
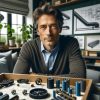
Jordan Smith, a seasoned professional with over 20 years of experience in the conveyor system industry. Jordan’s expertise lies in providing comprehensive solutions for conveyor rollers, belts, and accessories, catering to a wide range of industrial needs. From initial design and configuration to installation and meticulous troubleshooting, Jordan is adept at handling all aspects of conveyor system management. Whether you’re looking to upgrade your production line with efficient conveyor belts, require custom conveyor rollers for specific operations, or need expert advice on selecting the right conveyor accessories for your facility, Jordan is your reliable consultant. For any inquiries or assistance with conveyor system optimization, Jordan is available to share his wealth of knowledge and experience. Feel free to reach out at any time for professional guidance on all matters related to conveyor rollers, belts, and accessories.