High-Performance NN Rubber Belt for Quarry Conveying Systems
NN (Nylon-Nylon) rubber conveyor belts are widely used in various industrial applications, particularly in heavy-duty material handling systems. Constructed with nylon fibers woven in both the longitudinal (warp) and lateral (weft) directions, these belts offer exceptional strength, flexibility, and resistance to wear and tear. The unique structure of the NN belt provides high tensile strength and low elongation, ensuring durability even in the toughest working conditions.
NN belts are commonly found in industries such as mining, manufacturing, agriculture, and logistics, where they are used to transport bulk materials like coal, cement, ores, grains, and aggregates over long distances. Their ability to operate efficiently in harsh environments—resisting moisture, abrasion, and exposure to oils and chemicals—makes them ideal for demanding applications.
The design of NN belts typically includes three key layers: a top cover, a carcass made from nylon fabric that provides longitudinal strength and shape, and a bottom cover for added protection. These features ensure the belts maintain high performance while minimizing maintenance costs. The versatility and reliability of NN rubber conveyor belt make them essential components in many industrial conveyor systems, supporting continuous and efficient material transport.
Key Features of NN Rubber Belt
NN (Nylon/Nylon) rubber belts are known for their durability, flexibility, and strength, making them ideal for a wide range of industrial applications. Similarly, the HR rubber belt offers exceptional heat resistance and durability, making it a great choice for high-temperature applications where reliability and performance are critical.
High Tensile Strength
NN rubber belts are designed with high tensile strength, allowing them to withstand heavy loads and significant tension without losing their structural integrity. This makes them ideal for industries where conveyor belt must handle large volumes of materials over long distances, such as in mining, construction, and heavy manufacturing. Their ability to endure substantial stress and weight ensures consistent performance even in the most demanding applications.
Good Elasticity and Flexibility
One of the standout features of NN rubber belts is their excellent elasticity and flexibility. This enables them to bend and adapt to the layout of various conveyor systems, including those that require navigating curves or inclined planes. Their flexibility ensures smooth material transport, making them suitable for industries that rely on continuous and reliable material movement, such as food processing, packaging, and logistics.
Low Elongation
NN rubber belts exhibit low elongation, which means they stretch minimally even under heavy loads. This feature ensures that the belts maintain consistent performance, with reduced need for frequent re-tensioning or adjustments. Low elongation helps to maintain the proper alignment and smooth operation of the conveyor system, ensuring efficient material transport and minimizing maintenance downtime.
Wear and Tear Resistance
The durability of NN rubber belts makes them highly resistant to wear and tear, even in abrasive environments. They are designed to endure the rigors of transporting rough and sharp materials, such as gravel, sand, and ores, which makes them a popular choice in industries like mining, construction, and recycling. Their resistance to wear ensures a longer service life, reducing the need for frequent replacements and keeping operational costs low.
Good Groove Formation
NN rubber belts are effective at forming well-defined grooves, which improve material transport efficiency, especially in inclined conveyor systems. These grooves help prevent material slippage, ensuring that materials are conveyed safely and reliably even at steeper angles. This feature is particularly advantageous in bulk material handling industries where maintaining material stability and control is crucial. It significantly enhances the performance of bulk material handling equipment, ensuring smooth operation and reducing the likelihood of material loss or disruption.
Heat-Resistant NN Rubber Belt
Heat-resistant NN rubber belts are designed to withstand extreme temperatures, making them essential for industries where high heat exposure is a common challenge. These belts maintain their performance and structural integrity even under the most demanding thermal conditions, ensuring reliable material transport in environments such as steel mills, cement plants, and mining operations. Below is an expanded look at the key aspects of heat-resistant NN rubber belts.
Specification of Heat-Resistant Belts
Heat-resistant NN rubber belts are engineered with materials that can endure high temperatures without losing their functional properties. The specific temperature range that these belts can withstand typically varies depending on the grade of heat-resistant coating applied, but in general, heat-resistant NN rubber belts can operate effectively at temperatures ranging from 100°C (212°F) to 250°C (482°F), with some specialized variants designed to handle even higher temperatures. This makes them suitable for industries that involve continuous exposure to heat, such as cement production or steel manufacturing.
To further enhance their heat resistance, these belts often incorporate advanced compounds, which help protect the rubber from thermal degradation. These belts are designed to maintain flexibility and strength, even in environments where conventional belts might fail due to the stress induced by high heat.
Applications
Heat-resistant NN rubber belts are used across a range of industries where high temperatures are a constant challenge. These include:
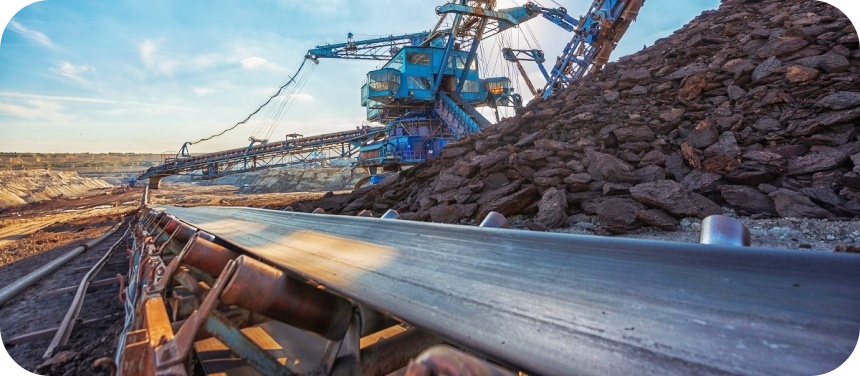
Material Composition
Heat-resistant NN rubber belts are constructed with specialized materials that enable them to withstand high temperatures while maintaining strength and flexibility. These materials include heat-resistant coatings and compounds that provide a protective layer against thermal degradation. The rubber itself may be compounded with additives such as carbon black, silica, or other heat-stabilizing agents, which significantly improve its resistance to heat-induced wear.
In addition to the rubber composition, heat-resistant belts may also be reinforced with special fabric layers, such as nylon or polyester, to enhance the structural integrity of the belt. This multi-layer construction ensures that the belt can handle not just high temperatures, but also the physical stresses of carrying heavy or abrasive materials over long distances.
Performance Characteristics
The primary performance characteristic of heat-resistant NN rubber belts is their ability to operate in high-temperature environments without losing their strength, flexibility, or resistance to wear. Unlike standard rubber belts, which can degrade and lose elasticity under extreme heat, heat-resistant NN belts maintain their form and functionality, even under prolonged exposure to high temperatures.
- Strength and Flexibility: Despite being exposed to intense heat, these belts retain their tensile strength, enabling them to carry heavy loads without stretching or deforming. The conveyor belt tensile strength is crucial in ensuring the belt’s reliability and longevity under extreme conditions, maintaining its performance even in demanding environments. The belts remain flexible enough to adapt to curves and bends in the conveyor system, ensuring smooth and efficient material transport.
- Durability: The heat-resistant properties of these belts ensure that they can withstand the rigors of high-heat environments over extended periods. The materials used in their construction are designed to resist thermal wear, which extends the life of the belt and reduces maintenance costs.
- Minimal Degradation: Heat-resistant NN rubber belts are engineered to resist degradation from prolonged exposure to heat, such as cracking, hardening, or becoming brittle. This durability ensures that the belt continues to operate effectively, even when exposed to fluctuating temperature extremes or sudden thermal shocks.
- Consistency in Performance: These belts are designed to maintain consistent performance even under fluctuating temperature conditions. Whether exposed to brief spikes in temperature or sustained heat, they continue to transport materials efficiently, minimizing disruptions in the production process.
Fire-Retardant and Fire-Resistant NN Rubber Belt
Fire-retardant and fire-resistant NN rubber belts are critical in industries where there is a heightened risk of fire or exposure to combustible materials. These specialized belts are designed to slow the spread of fire or completely prevent combustion, ensuring safer operations in high-risk environments. While fire-retardant and fire-resistant belts share some similarities, they differ significantly in how they respond to heat, flames, and ignition sources. Below, we explore these two types of belts in greater detail.
Fire-Retardant Belts
Fire-retardant NN rubber belts are designed with materials and compounds that help to delay or slow down the spread of fire. These belts are treated with special fire-retardant additives that reduce the risk of flames propagating along the surface or throughout the belt. While fire-retardant belts are not necessarily immune to catching fire, their primary function is to inhibit the rapid spread of fire, giving workers and equipment more time to respond in the event of a fire.
Key Features:
Fire-retardant belts are suitable for environments where the primary concern is controlling or preventing the rapid spread of fire, but they may not offer the same level of protection against intense, direct flames as fire-resistant belts.
Fire-Resistant Belts
Fire-resistant NN rubber belts are more robust in their ability to withstand direct exposure to flames or extreme heat. Unlike fire-retardant belts, which are designed to slow the spread of fire, fire-resistant belts are engineered to prevent combustion altogether. These belts are typically made with materials that do not catch fire under normal conditions and can endure high heat without breaking down or losing their functional properties.
Key Features:
The key difference between fire-resistant and fire-retardant belts lies in their ability to handle exposure to flames and high temperatures. While fire-retardant belts slow down the spread of fire, fire-resistant belts ensure that the material does not combust at all, providing a higher level of safety in hazardous environments.
Applications
Fire-retardant and fire-resistant NN rubber belts are particularly important in industries where flammable materials are handled or where there is a high risk of fire due to the presence of sparks, intense heat, or explosive materials. Key applications include:
Material Features
The fire-retardant and fire-resistant properties of NN rubber belts are achieved through the use of specialized compounds that provide enhanced heat and flame resistance. These belts are often made from a blend of rubber and additives that are specifically engineered to offer protection against fire hazards. The key material features include:
Key Advantages of NN Rubber Belt
NN (Nylon/Nylon) rubber belts are highly valued in a wide array of industrial applications due to their exceptional durability, cost-effectiveness, versatility, and safety features. These belts are engineered to withstand challenging environments, providing reliable performance even in the harshest conditions. Below are the key advantages that make NN rubber belts a preferred choice across various industries.
Durability in Extreme Conditions
One of the standout features of NN rubber belts is their remarkable durability, especially in extreme conditions. Whether exposed to high temperatures, abrasive materials, or heavy loads, NN belts are designed to withstand the most demanding environments. Their robust construction, which combines the strength of nylon with the flexibility of rubber, ensures that the belts perform efficiently even when subjected to extreme stress or harsh operating conditions.
Cost-Effectiveness
Despite offering superior performance in terms of durability and flexibility, NN rubber belts tend to be more affordable compared to other specialized belts, such as heat-resistant, fire-resistant, or steel cord conveyor belts. This makes them an attractive option for industries looking for a balance between quality and cost-efficiency.
Versatility
NN rubber belts are known for their versatility across a wide range of industries. These belts can be customized to meet specific requirements, making them suitable for a variety of material handling applications, from agriculture to heavy-duty industrial environments. Their flexibility allows them to be adapted for different belt widths, lengths, and designs, depending on the particular needs of the application.
Safety
Safety is a critical consideration in industrial environments, particularly when dealing with hazardous materials or high-risk conditions. NN rubber belts can be equipped with fire-retardant or fire-resistant coatings, providing an additional layer of safety in environments where fire or sparks are a concern.
Maintenance Tips for NN Rubber Belts
NN (Nylon/Nylon) rubber belts are integral components in many industrial operations, providing reliable performance even under challenging conditions. To ensure these belts continue to operate efficiently and last as long as possible, it’s important to implement a comprehensive maintenance strategy. Below are key maintenance tips that can help extend the lifespan of NN rubber belts and maintain their performance.
Regular Inspections
Regular inspections are one of the most critical aspects of NN rubber belt maintenance. Inspecting the belts on a scheduled basis helps identify issues before they develop into significant problems, reducing downtime and minimizing repair costs. Inspections should be thorough and should focus on several key areas:
Proper Tensioning
Tensioning the NN rubber belt correctly is vital for ensuring its optimal performance and longevity. If the belt is too tight or too loose, it can cause various issues that can lead to premature failure or reduced efficiency.
Correct Tension: Always check and maintain the correct tension level specified by the manufacturer. An overly tight belt can cause excessive wear on both the belt and the drive components, leading to faster degradation. On the other hand, a loose belt can slip, causing inefficient operation and further strain on the system, especially in high-load conditions.
Adjusting Tension: It’s important to periodically adjust the tension as needed. Over time, belts can stretch, leading to looser tension. Regular adjustments can help prevent slippage and ensure the belt maintains the proper grip on the pulleys, thus improving overall system efficiency.
Tools for Tensioning: Using the correct tools for tensioning, such as a belt tension gauge, can help achieve and maintain precise tensioning. This can prevent under-tensioning or over-tensioning, both of which can reduce the belt’s lifespan and performance.
Cleaning
Keeping NN rubber belts clean is essential for maintaining their functionality and prolonging their service life. Dirt, debris, and chemical residues can build up on the surface of the belt, leading to several problems, such as reduced grip, excessive wear, or even damage to the belt material.
Replacement and Repairs
Identifying when an NN rubber belt needs to be replaced or repaired is crucial to maintaining an efficient and safe conveyor system. Regular inspections will help spot signs of wear or damage early, allowing for timely intervention to prevent major breakdowns.
FAQs about NN Rubber Belt
What is NN in Conveyor Belt?
NN refers to Nylon/Nylon in conveyor belts, a common designation for belts made with two layers of nylon fabric. The “NN” stands for the use of nylon fibers in the carcass of the belt, which provides enhanced strength and durability. NN rubber conveyor belts are highly flexible, which makes them suitable for handling various materials in industries like mining, construction, and agriculture. The belts are designed to withstand tension, impact, and wear, making them ideal for transporting heavy and abrasive materials over long distances. The two layers of nylon fabric contribute to the belt’s ability to absorb shock and resist stretching, ensuring that the belt maintains consistent performance over time. Additionally, NN rubber belts offer excellent resistance to heat, water, and chemical exposure, making them versatile for different operating environments. As a result, NN belts are often chosen for their durability, reliability, and cost-effectiveness in industries that require high-performance conveyor systems.
How Long Do Rubber Belts Last?
The lifespan of a rubber conveyor belt can vary significantly depending on several factors, including the type of material being transported, environmental conditions, and the level of maintenance. On average, a rubber belt can last anywhere from 3 to 10 years. However, this can be shortened or extended based on how well the belt is maintained and how it is used. Conveyor belts that handle heavy, abrasive materials or operate in harsh environments may wear out faster, requiring replacement or repair sooner. Proper maintenance practices such as regular inspections, cleaning, and correct tensioning can extend the life of the belt. Similarly, belts that are exposed to extreme temperatures, chemicals, or constant heavy loads may require more frequent replacement. On the other hand, belts used in less demanding conditions, with good maintenance, can last longer. It’s also important to consider the quality of the belt; high-quality rubber belts are designed to offer more durability, providing better long-term performance and reliability.
What is the Difference Between Grade 1 and Grade 2 Conveyor Belts?
The primary difference between Grade 1 and Grade 2 conveyor belts lies in their material composition and the level of quality and strength they offer. Grade 1 belts are made from premium materials and are typically designed for more demanding applications that require higher tensile strength and durability. These belts are ideal for industries like mining, cement, and steel mills, where the belts need to withstand harsh conditions, heavy loads, and high-impact forces. Grade 2 belts, on the other hand, are made from lower-grade materials and are more cost-effective. While they still offer good performance for light to moderate applications, they are generally not as durable or resistant to wear, heat, or chemicals as Grade 1 belts. Grade 2 belts are commonly used in industries like agriculture, food processing, or logistics, where the operational environment is less extreme, and the material being conveyed is lighter and less abrasive. When choosing between Grade 1 and Grade 2 belts, businesses should consider the specific needs of their conveyor system and the operating conditions to ensure they select the right belt for optimal performance and cost-efficiency.
How Do You Measure a Rubber Drive Belt?
Measuring a rubber drive belt accurately is essential to ensure proper fit and performance. The first step is to determine the length of the belt. This can be done by measuring the distance around the pulleys that the belt will drive, from the start to the end of the loop. The length of the belt should be measured with the system at rest, not under tension, to avoid inaccuracies. For V-belts, the measurement is typically taken from the inside circumference, while for flat belts, the total length around the pulleys is measured.
Next, measure the width of the belt. This is particularly important for determining compatibility with pulley grooves and ensuring proper belt-to-pulley contact. The width is measured at the widest point of the belt, which is especially important for V-belts, where the angle of the sides affects the fit. Finally, the thickness of the belt is another important dimension, especially for determining the amount of load the belt can handle and the type of material the belt is suited for. Keep in mind that different types of drive belts (V-belts, timing belts, serpentine belts) may require specific measuring techniques, so it’s important to check manufacturer guidelines when measuring the belt for replacement or installation.
CONTACT US
Let us help you find a better solution!