Fabric Nylon Conveyor Belt Manufacturers Suppliers
Nylon Canvas Conveyor Belt has good flexibility and elasticity, high strength, fatigue resistant, impact resistant, anti-tear and long use life. It works well with all types of trough rollers.
It is used for long distance and heavy-duty conveying with loose density, medium or small particle size materials.
It is used for small or medium particles, or powder-like materials, like wood chips, grains, coal, cement etc.
In the ever-evolving field of material transport and handling, nylon conveyor belts emerge as essential tools across various industries due to their unique combination of strength, flexibility, and longevity. Meticulously engineered by expert manufacturers, these belts have transformed operational processes in sectors like mining, agriculture, and food processing. This introduction explores the critical role and wide-ranging applications of nylon conveyor belts, highlighting their key features such as superior abrasion resistance, low maintenance requirements, and the ability to handle diverse materials, making them invaluable in today’s industrial landscape.
What is a Nylon Conveyor Belt?
Nylon conveyor belts, a pivotal component in the realm of material handling, are distinguished by their robust and adaptable nature. Crafted from strong and resilient nylon fabric, these belts are essential to the functioning of various nylon belt conveyor systems,because nylon’s high conveyor belt tensile strength allows the belt to withstand significant mechanical stress.
Parts of a Nylon Belt
The nylon conveyor belt’s strength and flexibility come from its core fabric made of nylon fibers, strategically woven in the warp and weft to create a balanced, durable structure, crucial in multi-ply belts for enhanced load-bearing capacity and durability.In terms of nylon conveyor belt specification, these belts are designed to meet various industrial requirements. The conveyor belts’ thickness, width, and length are varied to match specific applications and systems, with the choice of single-ply or multi-ply nylon fabric crucial for meeting different operational needs.
Nylon conveyor belts are composed of several key components that contribute to their functionality and durability in various industrial applications. Here’s a breakdown of the main parts:
- Top Cover: This is the upper layer of the belt that comes into direct contact with the materials being transported. It is typically made from nylon due to its excellent wear resistance and flexibility, which helps in handling materials smoothly and efficiently.
- Carcass: The carcass acts as the core structure of the belt and is crucial for providing strength and shape. It is usually made from layers of fabric such as nylon and polyester. Nylon fabrics are prized for their high strength and elasticity, which are essential for the belt’s performance under tension and dynamic conditions.
- Bottom Cover: Similar to the top cover, the bottom cover protects the carcass from wear and damage from the rollers and support structures underneath. It is also made from abrasion-resistant materials like nylon to ensure durability and longevity.
- Edges: The edges of a nylon conveyor belt are treated or sealed to prevent fraying and wear. In some designs, the edges are reinforced with additional material to enhance durability, particularly in harsh operational environments.
- Reinforcement Layers: In some nylon belts, additional reinforcement layers such as steel cords conveyor belt or Kevlar might be added between the nylon fabric layers. These reinforcements provide greater strength and help the belt handle heavier loads or operate over longer distances without stretching excessively.
These parts work together to give nylon conveyor belts their advantageous properties, making them suitable for a wide range of industrial applications where durability, flexibility, and strength are crucial.
Unique Properties of Nylon Conveyor Belt
Nylon conveyor belts are highly regarded in various industries for their unique properties that enhance performance and durability in demanding applications. Here are some of the distinctive characteristics of nylon conveyor belts:
- High Tensile Strength: Nylon is renowned for its excellent tensile strength, which allows the conveyor belts to handle heavy loads. This strength is crucial for minimizing stretch under tension, especially in long-distance conveying systems.
- Good Elasticity: The elasticity of nylon helps the conveyor belt to absorb shocks and impacts during operation, which is particularly useful in industries like mining where sharp and heavy materials are transported.
- Superior Abrasion Resistance: Nylon’s resistance to abrasion makes it ideal for use in environments with high wear and tear. This property extends the life of the conveyor belt, reducing the need for frequent replacements and maintenance.
- Low Moisture Absorption: While nylon does absorb some moisture, its impact on the mechanical properties of the conveyor belt is minimal at normal operating temperatures. This makes nylon conveyor belts suitable for environments where exposure to moisture is inevitable.
- Resistance to Chemicals: Nylon conveyor belts are resistant to many chemicals, making them suitable for chemical processing industries where belts might come into contact with corrosive substances.
- Flexibility: Despite its strength and durability, nylon remains flexible, which is beneficial for conveyor systems that require belts to navigate curves and other complex routes without compromising performance.
- Thermal Stability: Nylon can perform under a range of temperatures, maintaining its integrity under most industrial conditions, though it may lose some strength in very high temperatures.
These properties make nylon conveyor belts a preferred choice for a variety of applications, from heavy-duty mining and material handling to agricultural and food processing tasks. The combination of durability, flexibility, and resistance to environmental factors ensures that nylon belts provide a reliable and efficient means of material transport.
The Manufacturing Process of Nylon Conveyor Belts
The manufacturing of nylon conveyor belts is a detailed process focused on meeting industry demands and specific specifications, ensuring the durability and functionality of the nylon belt conveyor system.
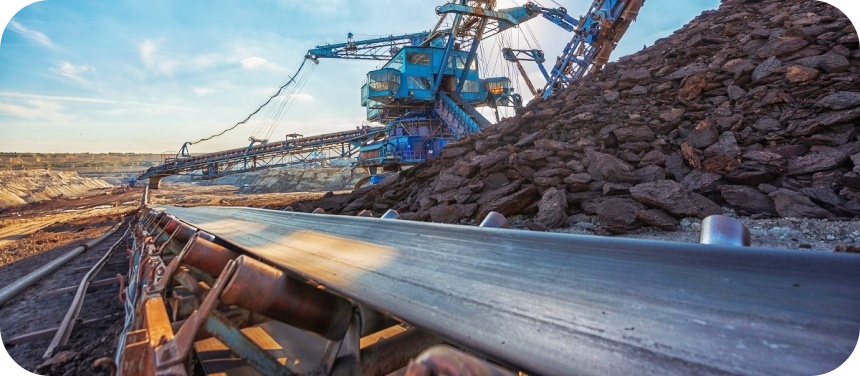
Nylon Conveyor Belt Production Steps
The manufacturing process of nylon conveyor belts involves several key steps to create a durable and efficient product used in various industries for transporting materials. Here’s an overview of the typical process:
- Materials Preparation: The primary material used is nylon fabric, which is known for its strength and elasticity. This fabric is prepared and treated to ensure it can handle the wear and tear of moving heavy loads.
- Compounding: Raw materials like rubber are mixed with certain chemicals and additives to form the rubber compound. This mixture is critical for defining the belt’s characteristics, such as its resistance to abrasion, heat, and other environmental factors.
- Calendering: The rubber compound is then processed through a calendering machine, where it is pressed into thin sheets. These sheets are layered on the nylon fabric to create a strong bonding.
- Assembly of Layers: Multiple layers of the coated fabric are assembled together. The number of layers depends on the intended use and required strength of the belt. These layers typically include the top and bottom covers, and the carcass which is the main structural component.
- Vulcanization: The assembled belt is then subjected to vulcanization. This process involves heating and pressurizing the belt to cure the rubber, which enhances the belt’s strength and ensures the layers are firmly bonded.
- Quality Control and Finishing: After vulcanization, the conveyor belt is inspected for any defects. Edges are trimmed, and the belt is finished to ensure it meets quality standards.
- Testing: Finally, the belt undergoes various tests to assess its performance under different conditions, including its tensile strength and resistance to wear and tear.
Each of these steps must be carefully controlled to ensure that the final product can perform effectively in its specific application, handling the required load and operating conditions.
Receiving and Twisting Yarn
The journey of a nylon conveyor belt begins with the procurement of high-quality nylon yarn. This yarn is the fundamental building block of the belt and is responsible for its core characteristics. Upon receiving, the nylon yarn undergoes a twisting process. This involves combining multiple strands of yarn to form a stronger, more resilient thread. The twisting process is crucial as it significantly enhances the tensile strength of the nylon, making it suitable for the heavy-duty performance expected from nylon belt conveyors.
Weaving Process
Once the yarn is twisted, it moves to the weaving stage. Weaving is where the actual formation of the nylon fabric takes place. There are several weaving styles used in this process, each contributing differently to the belt’s properties:
- Plain Weaving: This is the simplest form of weaving, where the warp and weft yarns cross each other at right angles. Plain weaving is generally used for lighter applications, as it offers a balance between flexibility and strength.
- Twill Weaving: In twill weaving, the weft thread crosses over two or more warp threads, creating a diagonal ribbing pattern. This style is preferred for heavier applications as it provides greater strength and durability.
- Basket Weaving: This style is similar to plain weaving but with two or more threads combined as one in the warp and weft. Basket weaving results in a more porous fabric, offering better air permeability and flexibility.
Treatment and Calendaring
After weaving, the nylon fabric undergoes a treatment process. This involves the application of various chemicals and adhesives to enhance the fabric’s properties, such as its resistance to heat, chemicals, and abrasion. The treated fabric is then passed through a calendaring process. Calendaring involves pressing the fabric between rollers to improve its density and surface smoothness. This step is crucial for ensuring that the nylon fabric meets the specific nylon conveyor belt specification required for different industrial applications.
Lamination
The final step in the manufacturing process is lamination. This is where multiple layers of the treated and calendared nylon fabric are bonded together to form the conveyor belt. The lamination process ensures that the belt has the necessary thickness and strength to handle the intended load. It also contributes to the overall flexibility and durability of the belt, making it an ideal choice for various nylon belt conveyor systems.
Applications of Nylon Conveyor Belts
Nylon conveyor belts, produced by skilled nylon conveyor belt manufacturers, have become an integral part of various industrial operations due to their versatility and robustness. These belts are designed to meet specific nylon conveyor belt specifications, making them suitable for a wide range of applications across different sectors.
Wide Range of Industrial Applications
Nylon conveyor belts are incredibly versatile, making them indispensable in a wide range of industrial applications due to their durability, flexibility, and strength. Here’s a broad overview of their applications across different industries:
- Mining and Quarrying: Nylon conveyor belts are extensively used in the mining industry to transport materials such as coal, ore, and other mined materials over long distances, often under harsh conditions.
- Agriculture: These belts are used for handling grain, feed, and other agricultural products, aiding in the processes of distribution and storage.
- Manufacturing: In the manufacturing sector, nylon belts help in the movement of bulk materials and finished products, facilitating efficient production lines in industries like electronics, automotive, and furniture.
- Food Processing: Due to their resistance to oils and greases, nylon belts are suitable for food processing industries where they help in transporting food items from one stage of production to another without contamination.
- Packaging: These belts are critical in packaging facilities, handling everything from lightweight packages to heavy boxes, improving efficiency in packing lines.
- Textiles: In textile mills, nylon conveyor belts are used to transport raw fibers, threads, and finished fabrics, contributing to streamlined operations.
- Airports: For luggage handling systems, nylon belts offer a reliable solution that ensures smooth and efficient movement of baggage.
Each of these applications highlights the essential role that nylon conveyor belts play in various sectors, attributed mainly to their robustness, flexibility, and ability to operate effectively under different environmental conditions.
Suitability for Different Materials
- Wood Chips and Grains: These materials are relatively light but can be bulky. Nylon belts are suitable for such applications due to their good troughability, which helps in containing the material on the belt.
- Coal: Coal, abrasive and heavy, demands a strong and wear-resistant conveyor belt, making nylon belts with high tensile strength and abrasion resistance ideal for the job.
- Cement: Cement handling can be dusty and abrasive. Nylon conveyor belts are capable of withstanding these conditions, and their flexibility allows for effective handling of cement in various stages of processing.
Advantages of Nylon Conveyor Belts
Nylon belt conveyor, crafted by experienced nylon conveyor belt manufacturers, stand out in the material handling industry for their exceptional qualities. These belts are designed to meet specific nylon conveyor belt specifications, ensuring they deliver optimal performance in various industrial applications.
Strength and Durability
Nylon conveyor belts stand out due to their remarkable strength, thanks to the high tensile strength of the nylon fibers they incorporate. This strength is essential for industries like mining and construction, where the belts handle heavy loads and abrasive materials, enduring constant stress. The durability of nylon also means these belts are less prone to tearing and wear, contributing to a longer service life. This durability is a testament to the quality standards upheld by nylon conveyor belt manufacturers in their production processes.
Flexibility and Adaptability
Despite their strength, nylon conveyor belts are incredibly flexible. This flexibility allows the belts to easily navigate corners and curves in a conveyor system, making them highly adaptable to various layouts. This adaptability is particularly beneficial in complex industrial setups where space constraints require conveyor systems to follow unique paths. The flexibility also contributes to the belt’s ability to handle different types of materials, from fine grains to bulky items, without compromising efficiency or causing damage to the materials being transported.
Long Service Life
Nylon conveyor belts are known for their longevity. The resilience of nylon as a material contributes to a belt that can withstand the rigors of daily use over extended periods. This long service life is not only cost-effective for businesses but also reduces the need for frequent replacements, thereby minimizing downtime in industrial operations. The long service life of these belts is a direct result of the stringent nylon conveyor belt specifications followed during manufacturing, ensuring that each belt is robust and capable of enduring various industrial conditions.
Good Troughability and Efficiency
Troughability refers to the belt’s ability to form a trough shape, which is essential for efficiently carrying bulk materials. Nylon conveyor belts exhibit excellent troughability, ensuring that materials stay on the belt and are transported effectively from one point to another. This feature is particularly important in industries like agriculture and food processing, where preventing spillage is crucial. The good troughability of nylon belts not only enhances efficiency but also contributes to a cleaner and safer working environment, as it reduces the likelihood of material spillage along the conveyor path.
Nylon Belt Conveyor’s Technical Considerations and Limitations
Simple Design and Cleaning Challenges
One of the notable drawbacks of nylon belt conveyor is their relatively simple design. While this simplicity contributes to their strength and durability, it can also limit their functionality in certain specialized applications. For instance, the smooth surface of a standard nylon belt may not be ideal for incline or decline conveyors where a more textured surface is needed to prevent slippage of materials.
Cleaning nylon belt conveyor can also present challenges. Material properties can pose challenges in fully removing residues and contaminants, a critical concern in hygiene-focused industries like food processing. Maintaining hygiene standards requires regular and thorough cleaning, which can be labor-intensive and time-consuming. Nylon conveyor belt manufacturers often provide specialized coatings or treatments to facilitate cleaning, but these solutions may not be universally applicable.
Water Absorption and Its Implications
Another technical consideration is the absorption of water by nylon. Nylon can absorb up to 10% of its weight in water, which can lead to changes in the belt’s dimensions when used in wet conditions. This characteristic is particularly relevant in environments where the belt is exposed to moisture, either due to the nature of the materials being transported or the operating conditions.
The absorption of water can cause the belt to swell, potentially affecting its alignment and tension. Over time, this can lead to premature wear and tear, and in some cases, may even cause the belt to malfunction. Additionally, in environments with fluctuating humidity levels, the repeated absorption and drying can lead to material fatigue, further shortening the belt’s lifespan.
To mitigate these issues, nylon belt conveyor specifications often include treatments or coatings that reduce water absorption. However, these modifications can impact the belt’s other properties, such as its flexibility or grip. Therefore, it’s important for businesses to work closely with nylon conveyor belt manufacturers to select a belt that not only meets their operational requirements but also can withstand the specific environmental conditions of their application.
Our Popular Products
Strong Tensile Strength Good Quality Competitive Price Nylon Conveyor Belt
Nylon Conveyor Belt, Belt Thickness: 15 mm
3 Inch Also available 12 Inch Width Nylon Conveyor Belt
CONTACT US
Let us help you find a better solution!
FAQs about Nylon Conveyor Belt
What are the benefits of nylon belts?
In heavy industries such as mining, nylon belts offer numerous benefits, making them a popular choice for various applications. Nylon belts are known for their exceptional strength and durability, capable of handling heavy loads and high-stress conditions typical in mining environments. They provide excellent flexibility and resilience, which helps in withstanding the constant movement and bending as materials are conveyed. Nylon belts also exhibit good resistance to abrasion and wear, ensuring a longer lifespan even when transporting abrasive materials like ores and coal. Additionally, they have a high resistance to impact and shock loads, reducing the risk of belt damage during heavy-duty operations. Their lightweight nature compared to other materials further enhances operational efficiency by reducing energy consumption and facilitating easier installation and maintenance.
How long do nylon belts last?
The lifespan of nylon belts in heavy industries such as mining depends on various factors, including the operating conditions, the materials being transported, and the maintenance practices in place. Under optimal conditions and with regular maintenance, nylon belts can last several years. However, in harsh environments with heavy loads and abrasive materials, the lifespan may be shorter. Typically, a well-maintained nylon conveyor belt can last anywhere from 3 to 10 years. Factors such as proper tensioning, regular inspection for wear and tear, timely repairs, and ensuring the belt is not exposed to extreme temperatures or corrosive substances can significantly extend the belt’s operational life, ensuring reliable performance and minimizing downtime.
Are nylon belts good?
Yes, nylon belts are considered very good for heavy industrial applications, including mining. Their high tensile strength and durability make them suitable for handling large, heavy loads and enduring the rigorous demands of industrial environments. Nylon belts offer excellent flexibility and shock resistance, which is essential for operations involving frequent starts, stops, and varying loads. They are also resistant to abrasion and wear, which is critical when dealing with abrasive materials like rocks, ores, and minerals. Additionally, nylon belts tend to have a longer lifespan compared to some other materials, making them a cost-effective choice in the long run. Their performance in harsh conditions and adaptability to various conveyor system requirements underscore their reliability and efficiency in heavy industries.
Are nylon belts waterproof?
Nylon belts are not inherently waterproof, but they do possess a degree of water resistance. In heavy industries such as mining, this can be beneficial in environments where moisture or wet materials are present. To enhance their waterproof properties, nylon belts are often coated or treated with waterproofing agents. This treatment helps prevent water absorption, which can degrade the belt material over time and reduce its tensile strength and durability. Properly treated nylon belts can effectively resist the negative effects of moisture, such as mold growth and material weakening, ensuring reliable performance in wet conditions. However, for applications requiring complete waterproofing, other materials or additional protective coatings may be preferred.
What material is used to make conveyor belts?
Conveyor belts used in heavy industries like mining are typically made from a combination of materials to ensure durability, flexibility, and strength. The most common materials include rubber, nylon, polyester, and steel. Rubber is widely used for its excellent flexibility and resistance to abrasion, impact, and harsh environmental conditions. Nylon and polyester fabrics are used to reinforce the belt, providing high tensile strength and flexibility. Steel cord belts are preferred for extremely heavy-duty applications due to their superior strength and durability, capable of handling large, heavy loads over long distances. The combination of these materials results in conveyor belts that can withstand the demanding conditions of mining operations, ensuring efficient and continuous material transport.
Why are conveyor belts made rough?
Conveyor belts are often made rough to enhance their grip and prevent materials from slipping during transport. In heavy industries such as mining, the rough texture is crucial for effectively moving materials like ores, coal, and aggregates, which can be heavy and abrasive. The rough surface increases friction between the belt and the materials, ensuring stable and controlled movement, especially on inclines or declines. This texture also helps in the efficient transfer of materials to and from different sections of the conveyor system, reducing spillage and maintaining a steady flow. Additionally, the rough surface can assist in cleaning the belt by dislodging debris and preventing material buildup, thereby reducing maintenance needs and prolonging the belt’s lifespan.
What makes a good conveyor belt?
A good conveyor belt for heavy industries, such as mining, must possess several key characteristics. Durability is paramount; the belt should be able to withstand constant wear and tear from abrasive materials like ores and rocks. High tensile strength is also crucial to handle the heavy loads typical in mining operations without stretching or breaking. Flexibility is important for navigating various conveyor configurations and maintaining smooth operation. Resistance to extreme environmental conditions, such as temperature fluctuations, moisture, and chemical exposure, ensures longevity and reliability. Additionally, a good conveyor belt should have a rough surface to prevent material slippage and facilitate efficient transport. Regular maintenance and quality materials, such as reinforced rubber or steel cords, further enhance the belt’s performance and lifespan, ensuring it can meet the rigorous demands of heavy industrial applications.
Which artificial Fibre is commonly used to make conveyor belt?
Nylon is the most commonly used artificial fiber in the manufacturing of conveyor belts, particularly in heavy industries such as mining. Nylon fibers offer several advantages, including high tensile strength, excellent flexibility, and resistance to abrasion. These properties make nylon an ideal material for reinforcing conveyor belts, allowing them to handle heavy loads and withstand harsh working conditions. Additionally, nylon’s resistance to impact and shock loads ensures that the belts can operate smoothly and reliably, even in demanding environments. The use of nylon in conveyor belts enhances their durability and performance, making them suitable for transporting a wide range of materials, from ores and coal to aggregates and other bulk goods in mining and other industrial applications.
What material makes most belts?
Most conveyor belts in heavy industries like mining are made from a combination of materials to optimize performance and durability. The primary materials used are rubber and synthetic fibers such as nylon or polyester. Rubber provides flexibility, resilience, and resistance to abrasion, which is essential for handling rough and abrasive materials like ores and coal. Nylon and polyester fibers are used to reinforce the belts, adding high tensile strength and durability needed to support heavy loads and withstand harsh conditions. For extremely demanding applications, steel cords are integrated into the belts to provide additional strength and stability. This combination of materials ensures that conveyor belts can operate efficiently and reliably in the rigorous environments typical of heavy industrial operations.
What is a nylon conveyor belt used for?
A nylon conveyor belt is widely used in heavy industries such as mining for transporting a variety of materials, including ores, coal, and aggregates. The nylon fibers provide high tensile strength, flexibility, and excellent resistance to abrasion, making the belts suitable for the harsh conditions encountered in mining operations. These belts are designed to handle heavy loads and continuous operation, ensuring efficient material transport over long distances and through complex conveyor systems. The durability and reliability of nylon conveyor belts minimize downtime and maintenance needs, enhancing overall productivity. Additionally, their resistance to impact and shock loads makes them ideal for use in environments where materials are loaded and unloaded frequently, ensuring smooth and consistent operation.
What is a fabric conveyor belt?
A fabric conveyor belt is a type of belt that uses woven fabrics, such as polyester, nylon, or cotton, as the core material for reinforcement. In heavy industries like mining, fabric conveyor belts are used for their flexibility, strength, and resistance to wear and tear. These belts typically consist of multiple layers of fabric, which are coated with rubber or PVC to provide additional durability and resistance to environmental factors. Fabric conveyor belts are suitable for transporting a wide range of materials, including ores, coal, and aggregates, offering reliable performance in harsh conditions. Their construction allows for easy maintenance and repair, making them a cost-effective choice for continuous operation in demanding industrial environments. The combination of fabric and coating materials ensures a balance of strength, flexibility, and resilience, essential for efficient material handling in mining and other heavy industries.
What is the most durable material for a belt?
The most durable material for a conveyor belt in heavy industries such as mining is steel-reinforced rubber. Steel cords embedded within the rubber belt provide exceptional tensile strength, making these belts capable of handling extremely heavy loads and long distances without stretching or breaking. The rubber exterior offers excellent resistance to abrasion, impact, and harsh environmental conditions, such as temperature extremes and exposure to chemicals. This combination ensures that the belts can withstand the constant wear and tear from transporting abrasive materials like ores and coal. Additionally, steel-reinforced rubber belts are designed to resist punctures and cuts, further enhancing their durability and lifespan. Their robust construction makes them ideal for high-stress applications, ensuring reliable and efficient operation in the demanding conditions typical of heavy industrial environments.
What are plastic conveyor belts made of?
Plastic conveyor belts used in heavy industries such as mining are typically made from high-performance synthetic materials like polyethylene (PE), polypropylene (PP), and polyvinyl chloride (PVC). These materials offer several advantages, including resistance to corrosion, chemicals, and moisture, which are critical in harsh industrial environments. Polyethylene belts are known for their flexibility and impact resistance, making them suitable for handling bulk materials. Polypropylene belts offer excellent chemical resistance and are used in environments where exposure to aggressive substances is common. PVC belts provide durability and versatility, capable of handling a wide range of materials with varying weights and sizes. Additionally, these plastic materials can be reinforced with fabric or other composites to enhance their strength and load-bearing capacity, ensuring efficient and reliable performance in demanding mining operations.
What is the difference between Grade l and Grade 2 conveyor belts?
Grade 1 and Grade 2 conveyor belts differ primarily in their abrasion resistance and durability. Grade 1 conveyor belts offer superior abrasion resistance, making them suitable for handling highly abrasive materials like ores, coal, and aggregates found in mining and heavy industrial applications. These belts are designed to endure harsh conditions, providing longer operational life and reducing the frequency of maintenance and replacements. Grade 2 conveyor belts, while still durable, have moderate abrasion resistance and are typically used in less demanding environments where the materials being transported are not as abrasive. They provide a cost-effective solution for general material handling needs without the extreme wear and tear conditions seen in Grade 1 applications. Choosing between Grade 1 and Grade 2 depends on the specific requirements of the operation, including the type of material, environmental conditions, and desired lifespan.
What polymer is conveyor belt made of?
Conveyor belts used in heavy industries like mining are commonly made of polymers such as rubber and thermoplastic materials. The primary polymer used is often rubber, specifically natural rubber or synthetic rubber compounds like styrene-butadiene rubber (SBR) and nitrile rubber (NBR). These materials offer excellent flexibility, durability, and resistance to abrasion and impact, essential for handling the harsh conditions of mining operations. In addition to rubber, thermoplastic polymers like polyvinyl chloride (PVC) and polyurethane (PU) are also used, particularly for belts that require specific properties such as chemical resistance or high-temperature performance. These polymers provide a balance of strength, flexibility, and resilience, making them ideal for constructing durable conveyor belts capable of withstanding heavy industrial use.
What is a type of polyester used for making conveyor belts called?
A type of polyester used for making conveyor belts is called polyethylene terephthalate (PET), commonly known as “polyester fabric.” PET is favored in the construction of conveyor belts due to its excellent tensile strength, flexibility, and resistance to stretching and shrinking. These properties make it ideal for reinforcing conveyor belts used in heavy industries like mining. Polyester fabric conveyor belts, often referred to as EP (polyester/nylon) belts, combine polyester fibers in the warp direction and nylon fibers in the weft direction. This combination enhances the belt’s overall strength and durability, allowing it to handle the demanding conditions and heavy loads typical of mining operations. The use of PET ensures that the belts maintain their structural integrity and performance over extended periods, even under harsh working conditions.
What are synthetic belts made of?
Synthetic conveyor belts are made from a variety of high-performance materials designed to meet specific industrial needs. In heavy industries like mining, these belts are commonly constructed from polymers such as polyvinyl chloride (PVC), polyurethane (PU), and thermoplastic elastomers (TPE). PVC belts are known for their durability and resistance to moisture and chemicals, making them suitable for a wide range of material handling applications. PU belts offer excellent flexibility, abrasion resistance, and a smooth surface, ideal for handling both bulk and individual items. TPE belts combine the properties of rubber and plastic, providing flexibility, strength, and resistance to wear and tear. These synthetic materials ensure that the belts can withstand the harsh conditions typical of mining environments, offering reliable and efficient performance in transporting heavy and abrasive materials.
What are the raw materials of conveyor belt?
The raw materials used in the manufacture of conveyor belts for heavy industries such as mining include rubber, fabric, and metal. Natural and synthetic rubbers, like styrene-butadiene rubber (SBR) and nitrile rubber (NBR), form the primary component, providing flexibility, durability, and resistance to abrasion and impact. Reinforcing fabrics, such as polyester, nylon, and aramid fibers, enhance the belt’s tensile strength and structural integrity. For added strength and durability in demanding applications, steel cords or wires are incorporated into the belts, offering superior load-bearing capacity and resistance to stretching. These materials are carefully selected and combined to create conveyor belts that can endure the rigorous conditions of mining operations, ensuring efficient and reliable material transport.
What ply material is a conveyor belt made of?
A conveyor belt used in heavy industries like mining is typically made of multiple layers, or plies, of fabric and rubber. The fabric plies, often made from materials such as polyester, nylon, or cotton, provide the belt with tensile strength and flexibility. These fabric layers are bonded together with layers of rubber, which offer durability and resistance to abrasion and impact. The number of plies can vary depending on the belt’s intended use, with more plies providing greater strength and load-bearing capacity. In some cases, steel cord reinforcement is used instead of fabric plies to provide additional strength and stability, particularly for long-distance or high-tension applications. This combination of fabric and rubber ensures that the conveyor belt can withstand the demanding conditions typical of mining operations.
What grade of rubber is used for conveyor belts?
In heavy industries such as mining, conveyor belts are often made using high-grade rubber compounds designed to withstand the rigorous demands of material handling. The rubber used typically falls into grades such as Grade M or Grade N, with Grade M rubber offering superior resistance to abrasion and wear, making it ideal for transporting highly abrasive materials like ores and coal. Grade N rubber provides a balance of durability, flexibility, and resistance to moderate abrasion, suitable for less demanding applications. These high-grade rubber compounds ensure that the conveyor belts can endure harsh conditions, including exposure to sharp materials, extreme temperatures, and heavy loads, thereby enhancing their longevity and reliability in industrial operations.
CONTACT US
Let us help you find a better solution!