Boosting Efficiency with Nylon Conveyor Rollers
What is a Nylon Conveyor Roller?
In the world of material handling and industrial processes, the nylon conveyor roller has emerged to become one of the most vital components driving efficiency and productivity. Understanding what a nylon conveyor roller is, its significance in various industries, and the primary factors contributing to its rising demand helps us appreciate the effectiveness of this remarkable invention.
Definition and Role of a Nylon Conveyor Roller
A nylon conveyor roller is a cylindrical device that facilitates the movement of objects along a conveyor belt system. Made out of nylon, a sturdy and versatile synthetic polymer, these rollers function as the rotating elements that propel the conveyor belt and the items placed upon it, maintaining the smooth flow of operations in numerous industries. The nylon component is crucial as it lends exceptional strength and rigidity to the roller, enabling it to sustain heavy loads and withstand intense industrial environments. At the same time, nylon reduces noise and friction, thus making for an operationally efficient nylon conveyor roller system design.
The Rising Demand for Nylon Conveyor Rollers
In recent years, there has been a sharp rise in the demand for nylon conveyor rollers. This demand is largely due to these rollers’ significant advantages over their counterparts made from other materials. Nylon conveyor rollers are known for their superior durability and operational efficiency, two of the most sought-after qualities in material handling applications.
Durability is a prime factor. Nylon, as a material, is highly resistant to wear and tear, corrosion, and various environmental factors. This means that a nylon conveyor roller tends to have a longer operational life than those made from other materials, translating into lower replacement costs and less downtime for businesses.
The efficiency of a nylon conveyor roller system is another factor driving its demand. Nylon’s low-friction surface allows for smoother rolling, reducing the energy required to move items along the conveyor. Besides, this characteristic helps reduce noise levels generated during operation, leading to a quieter and more conducive working environment.
The nylon conveyor roller’s vital role in the conveyor system and its ever-increasing reliance across industries testify to its effectiveness and ultimate utility. As advanced material handling and logistical requirements continue to evolve, so will the widespread utilization and continuous development of the nylon conveyor roller.
The Importance of Nylon Conveyor Rollers in Modern Industries
Conveyor rollers are essential components utilized extensively in various sectors for the transportation and handling of materials. The adoption of nylon conveyor rollers has brought about significant advancements in these industries by improving efficiency and productivity. This discussion emphasizes the integral part these rollers play, particularly focusing on the unique benefits that bolster their necessity in today’s industrial landscape.
Nylon Conveyor Roller Applications Across Industries
Nylon conveyor rollers are employed across a myriad range of industries, each with its requirements and demands. Below is a table presenting how specific industries leverage these rollers for their operations:
Industry | Application of Nylon Conveyor Rollers |
---|---|
Warehouse Work | In warehouses, nylon conveyor rollers facilitate the seamless movement of goods, reducing physical labor and simplifying inventory management processes. |
Construction | On construction sites, they are used to transport materials over varying terrain while resisting wear from abrasive substances. |
Food & Beverage | Conveyors fitted with nylon rollers maintain cleanliness and handle food products gently to avoid damage. |
Chemical Processing | In environments dealing with chemicals, nylon’s corrosion-resistant properties ensure longevity and safe handling of potentially aggressive substances. |
The table reveals the versatility of nylon conveyor rollers and their tailored adaptation to various industrial activities.
Advantages of Nylon Conveyor Rollers in Industrial Applications
The incorporation of nylon conveyor rollers within these fields stems from their array of unique benefits. Nylon outperforms many materials due to its inherent qualities, which cater to the high standards required in modern industrial processes.
Firstly, it’s their durability that sets nylon rollers apart. They can withstand substantial loads, resist wear and corrosion, and maintain performance in extreme temperatures, which is essential for industries like chemical processing and construction.
Secondly, the reduction of operation noise is a considerable advantage, one that greatly contributes to creating a more pleasant and compliant work environment, especially crucial in sectors like warehouse work where machinery operates continuously.
Lastly, efficiency enhancements are notable, as nylon conveyor rollers require less power to move due to their low friction coefficients. This results in reduced operational costs and energy savings – factors highly prized in energy-intensive industries such as food & beverage production.
The significance of nylon conveyor rollers in modern industries is clear. They not only uphold the systems’ functionality but also serve to optimize operations comprehensively, reinforcing their importance in sustaining industrial productivity.
Why Choose a Nylon Conveyor Roller?
In the realm of industrial operations, conveyor systems play a vital role in ensuring the efficient movement of goods and materials within the production process. The choice of a nylon conveyor roller over alternatives made from other materials like steel or PVC is primarily based on its distinct advantages, which significantly boost productivity and cost-effectiveness. In this discussion, we highlight the characteristics of nylon, emphasizing why it is the superior choice for conveyor rollers in today’s demanding industrial environments.
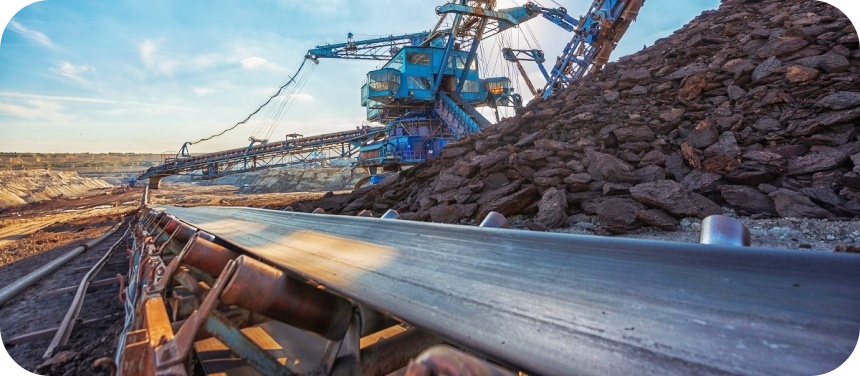
Durability and Longevity of a Nylon Conveyor Roller
The endurance and lifespan of a nylon conveyor roller offer significant benefits in comparison to rollers made from other materials. Nylon, a robust synthetic polymer, has a high strength-to-weight ratio, enabling it to withstand substantial loads without incurring deformation. Consequently, this makes nylon rollers highly durable and resistant to wear and tear.
Furthermore, nylon possesses excellent resistance to various environmental factors. It is not affected by moisture and is resistant to many chemicals, making it an ideal choice in hostile industrial environments, thereby extending the longevity of the conveyor system. On the other hand, materials like steel, although strong, can easily rust when exposed to hostile environments, and PVC, although resistant to corrosion, lacks the sheer strength delivered by nylon.
Reduced Noise Levels and Low Maintenance Needs
Another deciding factor favoring the adoption of a nylon conveyor roller is the reduction in operation noise. Noise pollution can be a significant problem in many large-scale industrial operations, affecting the working environment’s quality and potentially causing compliance issues. Nylon, due to its low friction coefficient and sound-absorbent properties, makes for a quieter operation when compared to steel or other hard materials.
In terms of maintenance, the robust and resilient nature of a nylon conveyor roller translates into low servicing requirements. Given its excellent wear resistance and ability to function under various conditions, nylon rollers demand fewer replacements and repairs. This scenario contrasts with steel rollers that may require regular treatment to prevent rust or PVC rollers that may crack or degrade, requiring replacement.
Choosing the Best Nylon Conveyor Roller
Selecting the best nylon conveyor roller is crucial to ensuring your conveyor system operates efficiently and withstands the test of time. Various factors come into play, each essential to cater to specific operational needs. It’s important to consider each aspect carefully to make a well-informed decision that would best serve your industrial operations. Here, we’ll explore the critical factors to weigh when making a selection.
Assessing Load Capacity
When considering the right nylon conveyor roller for your application, understanding the load capacity is paramount. The roller must be able to support the weight of the products it will carry without compromising performance or safety. Overburdening a roller can lead to premature wear and failure, which in turn can cause downtime and increased maintenance costs.
Therefore, it’s vital to choose a nylon conveyor roller with a load capacity that meets or exceeds the heaviest load it will encounter. The strength of nylon as a material offers excellent support, but it is crucial to match this capacity with your system’s demands.
Evaluating Environment Adaptation
The environmental conditions in which the nylon conveyor roller will operate must be carefully considered. The roller should be able to withstand the range of temperatures it will be exposed to, which could otherwise affect its performance and durability. Nylon’s thermal properties typically allow it to perform well in a wide range of temperatures but confirming compatibility with your specific conditions is key.
Moreover, if the nylon conveyor roller is to be utilized in areas where it may come into contact with chemicals or corrosive substances, it’s critical to ensure that the nylon material is suitable for such exposure. Its chemical resistance can protect against degradation and maintain the integrity of the roller over time.
Determining Speed Requirements
Finally, the operational speed of the conveyor is a determining factor. The selected nylon conveyor roller should be able to accommodate the desired speed of your conveyor belt without causing excessive wear or generating too much heat due to friction.
High-speed applications may require specially designed nylon rollers that can handle the rotational speed and the associated dynamic loads. Ensuring that your rollers are capable of operating at the required speeds will facilitate smooth and efficient conveyor operations.
In essence, choosing the best nylon conveyor roller necessitates a thorough evaluation of load capacity, environmental adaptation, and speed requirements. By addressing each of these considerations, you can ensure that the nylon conveyor roller you select will be ideally suited to your system’s needs, resulting in prolonged operational efficiency and reduced maintenance demands.
Types of Nylon Conveyor Rollers
The industrial landscape touts various nylon conveyor rollers, each designed to meet distinct material handling requirements. These rollers, fabricated from durable nylon, are integral to conveyor systems, facilitating efficient transport of goods across numerous sectors. This article details different sorts of nylon conveyor rollers, showcasing shapes, sizes, and special features, which collectively establish their versatility and functionality in different conveyor setups.
Heavy-Duty Nylon Conveyor Rollers
Heavy-duty nylon conveyor rollers are designed to endure strenuous conditions and manage high-load capacities. These rollers are typically utilized in industries where they must withstand substantial weight, impact, and continuous use without faltering. Their robust design helps minimize downtime and maintenance, making them a reliable choice for demanding environments.
4″ Nylon Conveyor Roller
The 4″ nylon conveyor roller is a medium-sized option commonly used in various applications, from light to moderate material handling. Its size makes it versatile for different products and packages. It offers a balance between durability and the ability to handle an array of goods without over-specifying the roller for lighter applications.
1 Inch Diameter Nylon Conveyor Roller
When precision and agility are at the forefront of conveyor needs, the 1 inch diameter nylon conveyor roller comes into play. Ideal for lightweight applications and smaller goods, this roller provides a smooth and controlled movement. Its smaller diameter enables it to fit into more compact spaces and perform with agility not found in larger rollers.
Versatility in Conveyor Roller Types
Nylon conveyor rollers are not a one-size-fits-all solution; their versatility extends to the systems in which they operate. Gravity roller conveyors, which rely on the force of gravity to move items, commonly employ nylon rollers for their lightweight and low-friction properties. Conversely, powered roller conveyors utilize these nylon rollers for their durability and the ease with which they can be integrated into powered systems.
Conveyor Rollers with Brackets
Additional specialized features such as nylon conveyor rollers with brackets are available to cater to specific installation requirements. Rollers with brackets can be easily mounted into frameworks and adjusted as necessary, providing flexibility and ease of maintenance. This feature is particularly useful in custom conveyor system configurations where roller positions and angles may need to be varied.
The nylon conveyor roller is a key component of modern industry, adaptable to a wide range of applications. From heavy-duty rollers capable of handling significant loads to nimble 1-inch diameter rollers suited for precise, lightweight operations, these rollers are customizable with features such as brackets to ensure versatility across conveyor systems. Whether integrated into gravity or powered conveyors, the nylon conveyor roller remains an essential selection for efficient material handling solutions.
Nylon Conveyor Roller Custom and Ready-Made Solutions
Ready-Made Nylon Conveyor Rollers
- Availability: Widely available, providing a quick solution for conveyor system needs.
- Cost-efficiency: Tend to be more budget-friendly due to mass production.
- Immediate Use: Ideal for urgent needs since they minimize downtime with their off-the-shelf availability.
- Standard Specifications: Produced to standard sizes and specifications, suitable for a broad range of applications without customization.
- Limitations: Might not meet specific unique requirements of more complex or specialized conveyor systems.
Custom Nylon Conveyor Rollers
- Tailored Design: Specifically designed to meet the unique requirements of a particular system or project.
- Adaptability: Can be tailored for non-standard sizes, bearing types, or specific operational conditions.
- Optimal Performance: Ensures that the roller fits perfectly within the system, meeting all necessary performance criteria.
- Special Features: Allows incorporating specific features or materials needed for the conveyor to function in specific environments or conditions.
- Cost and Time: Typically more expensive and time-consuming to produce than ready-made options, due to the customization process.
Overview of Leading Nylon Conveyor Roller Manufacturers
The market for conveyor systems spotlights a variety of manufacturers specializing in nylon conveyor rollers, each brandishing unique qualities that cater to different industrial needs. An exploration into leading nylon conveyor roller manufacturers reveals the diversity and expertise behind these essential components of material handling and logistics.
Distinguishing Attributes of Manufacturers
What truly sets these nylon conveyor roller manufacturers apart are several key attributes – their tenure in the industry, breadth of their product offerings, and custom solutions they provide. To synthesize these characteristics, the table below presents a comparative glance at select manufacturers:
Manufacturer | Experience | Product Range | Customization Capabilities |
---|---|---|---|
ABC Rollers | 20 years | Wide, including heavy-duty, lightweight, and specialized rollers | High: Offers design-to-delivery custom solutions |
XYZ ConveyTech | 35 years | Extensive, from standard rollers to advanced motion control systems | Medium: Custom sizes and features on existing models |
RollerWorks | 15 years | Specialized in food-grade and chemical-resistant rollers | Limited: Select customizable features on a base model |
GlobalConvey | 25 years | Broad, encompassing a vast array of industries | High: Complete custom engineering services |
QuickRoll Manufacturers | 10 years | Focused on quick-ship standard rollers and components | None: Standard products only with no customization |
This table aids in discerning the best-suited nylon conveyor roller manufacturer based on a project’s unique scope and specifications. Each company has its strengths and specialties, ensuring the market is equipped to serve a wide range of customer needs. Whether the priority is experience, a specific type of roller, or the flexibility to customize, there is a manufacturer ready to deliver the necessary solutions.
Nylon Conveyor Roller Pricing and Availability
In the marketplace for material handling equipment, knowing the ins and outs of nylon conveyor roller pricing and availability is essential for businesses aiming to optimize their operations without overspending. Discerning the best deals, understanding price points, and discovering cost-saving strategies are key elements when investing in nylon conveyor rollers for sale.
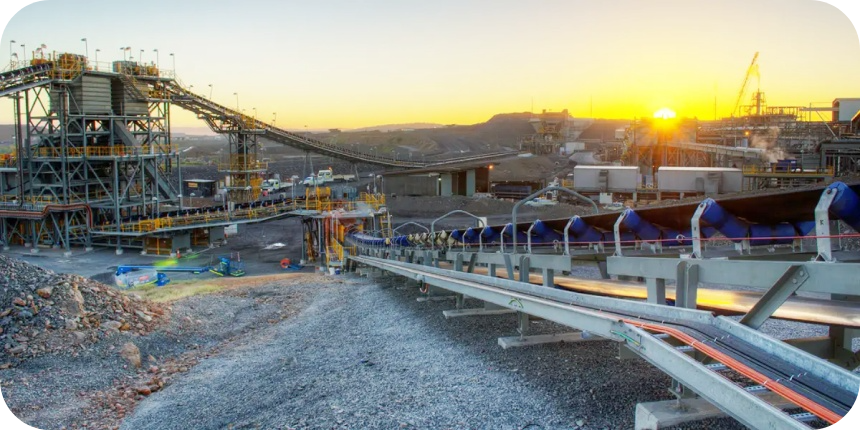
Strategies for Finding the Best Deals
When searching for nylon conveyor rollers, the strategies below can be employed to secure the best deals:
- Compare Suppliers: Obtain quotes from multiple suppliers for a detailed cost comparison.
- Bulk Purchases: Consider buying in bulk to capitalize on volume discounts.
- Off-Season Shopping: Purchase during off-peak times when prices might be lower due to decreased demand.
- Subscribe to Newsletters: Get updates on promotions and sales from manufacturers and distributors.
Understanding Nylon Conveyor Roller Pricing
To get a sense of the pricing landscape for nylon conveyor rollers, here’s a rough guide:
- Standard Rollers: Prices for standard rollers can range from $15 to $100 each, depending on the size and specifications.
- Custom Solutions: Tailored designs will significantly vary in price, starting at around $100 and potentially exceeding several hundred dollars per roller.
- Consider Quality and Longevity: Higher-priced rollers may offer better quality and longer life, potentially reducing long-term costs.
Budgeting and Cost Savings Tips
When planning finances around the acquisition of nylon conveyor rollers, keep the following tips in mind:
- Forecast Requirements: Accurately predict your usage to avoid over-purchasing, which ties up funds unnecessarily.
- Quality Over Quantity: Invest in higher-quality rollers that may have a higher upfront cost but will save you money on replacements in the long run.
- Maintenance Costs: Factor in the maintenance costs of rollers, as lower maintenance options may reduce costs over time.
- Negotiate Payment Terms: Work with suppliers to achieve favorable payment terms that can ease cash flow.
With strategic sourcing, a proper understanding of pricing, and budget-wise approaches, businesses can balance the scales between cost and quality, ensuring they obtain the right nylon conveyor rollers without compromising their financial planning.
Nylon Conveyor Roller Replacement and Maintenance
Optimal performance and longevity of a conveyor system largely depend on regular maintenance and timely replacement of its components. Within this domain, focusing on nylon conveyor roller replacement and maintenance is crucial, as these rollers play a pivotal role in the smooth operation of conveyor systems. This expanded outline describes detailed processes and valuable tips for maintaining and replacing nylon conveyor rollers.
Step-by-Step Conveyor Roller Replacement Process
When the time comes for replacing nylon conveyor rollers, following a systematic approach ensures efficiency and safety:
- Inspection: Regularly inspect rollers for signs of wear, damage, or misalignment.
- Shutdown and Lockout: Before starting the replacement process, ensure the conveyor system is shut down and locked out to prevent accidental activation.
- Removal: Carefully remove the worn or damaged nylon conveyor roller from its support frame, which might involve loosening brackets or mounts.
- Installation: Position the new nylon conveyor roller into place and secure it firmly, ensuring it is properly aligned with the conveyor’s belt path.
- Testing: Once installed, unlock the system and perform a test run to check the new roller’s operation, looking for smooth motion and proper belt tracking.
Vital Maintenance Tips for Nylon Conveyor Rollers
Proper maintenance of nylon conveyor rollers can dramatically extend their lifecycle, reduce downtime, and promote efficiency. Consider these essential maintenance protocols:
- Regular Cleaning: Keep rollers free from debris and build-up that can cause wear or impair movement.
- Lubrication: If applicable, periodically lubricate bearings in accordance with the manufacturer’s guidelines to ensure smooth operation.
- Alignment Checks: Frequently verify that rollers are correctly aligned to prevent uneven wear or belt slippage.
- Tension Adjustments: Monitor and adjust the tension of the conveyor belt to prevent excessive load on the rollers.
By adhering to systematic replacement procedures and consistent maintenance regimens, the performance of the nylon conveyor roller can be optimized, leading to a more reliable and durable conveyor system.
How to Purchase Nylon Conveyor Roller
The process of acquiring a nylon conveyor roller requires a calculated approach, not only to get the best value for investment but also to ensure the acquired machinery aligns perfectly with logistical needs. Understanding the significance of consultation and design services is equally important. These services are essential in customizing purchases to specific requirements, confirming that every nylon conveyor roller purchased meets operational demands.
Steps to Purchasing Nylon Conveyor Rollers
Embarking on the purchase of nylon conveyor rollers involves a series of steps that aid in making an informed and suitable choice:
- Requirement Analysis: Define the specific needs of your conveyor system, including roller size, load capacity, and environmental factors.
- Supplier Research: Look for reputable suppliers with positive reviews and a track record of quality products.
- Quotes and Comparison: Gather quotes from several suppliers for comparison. Don’t just compare prices but also warranty, durability, and after-sales service.
- Technical Specifications: Ensure that the technical specifications of the nylon conveyor roller align with your conveyor system’s requirements.
- Order Samples: If possible, order samples to test the quality and compatibility of the rollers with your system.
The Role of Consultation and Design Services
Consultation and custom design services stand as pillars in the procurement process of nylon conveyor rollers, ensuring a seamless integration into your conveyor system:
- Expert Guidance: Leverage the expertise of professionals to navigate the complexities of choosing the right rollers.
- Custom Solutions: Design services can customize rollers to your specific needs, which is critical for non-standard systems.
- Cost-Benefit Analysis: Consultants can provide a cost-benefit analysis to determine the most economical solutions without compromising on performance.
- Future Proofing: Designing with future needs in mind, consultants can help purchase nylon conveyor rollers that can scale with your business growth.
When looking into how to purchase nylon conveyor rollers, it’s imperative to meticulously follow these steps and consult with professionals for tailored design solutions. This strategic approach not only caters to immediate requirements but ensures long-term satisfaction and efficiency of the conveyor system.
Benefits of Nylon Conveyor Roller
Nylon conveyor rollers offer a range of advantages that can significantly improve the efficiency and durability of conveyor systems. These benefits stem from the material properties of nylon and its performance in various operational contexts. Below is a table that summarizes the key advantages of the nylon conveyor roller from multiple aspects:
Aspect | Benefit of Nylon Conveyor Roller |
---|---|
Durability | Nylon is highly resistant to wear and abrasion, which extends the life of the conveyor rollers and reduces the need for frequent replacements. |
Corrosion Resistance | Unlike metal rollers, nylon does not corrode when exposed to harsh chemicals or moist environments, making it ideal for use in various industries. |
Reduced Noise Levels | Nylon rollers operate more quietly than their metal counterparts, contributing to a more pleasant and less disruptive working environment. |
Weight | Being significantly lighter than metal, nylon rollers reduce the overall weight of the conveyor system, which can lower energy consumption. |
Cost-Effectiveness | While offering superior durability and performance, nylon conveyor rollers can be more cost-effective in the long run due to their longevity. |
Low Maintenance | The resilience of nylon to many types of damage means that nylon conveyor rollers require less maintenance, saving time and money. |
Friction | Nylon has a low coefficient of friction, which can reduce wear on the conveyor belt and itself, further increasing the lifespan of the system. |
Versatility | Thanks to their chemical and physical properties, nylon rollers can be used in a wide range of applications, from general manufacturing to specialized industries like food processing or pharmaceuticals. |
Utilizing nylon conveyor rollers in conveyor systems offers a compelling array of benefits that can lead to cost savings, improved operational efficiency, and a better working environment. Their unique advantages make them an excellent choice for businesses looking to enhance their material handling capabilities.
Traditional Materials like Steel or Rubber VS Nylon Conveyor Rollers
Material Type | Advantages | Disadvantages |
---|---|---|
Steel Rollers | Strong and durable | Heavier, prone to corrosion, require more maintenance, potentially higher operational costs |
Rubber Rollers | Good grip, good shock absorption | Can wear down quickly, susceptible to damage from oils and chemicals |
Nylon Conveyor Rollers | Lightweight, robust, resistant to various environmental factors, less maintenance required |
This table succinctly compares the benefits and drawbacks of steel, rubber, and nylon conveyor rollers, highlighting the balanced advantages that nylon offers.
CONTACT US
Let us help you find a better solution!
Most Popular Nylon Conveyor Roller for Sale in Gram Conveyor
Professional Nonstandard Low Friction Nylon Conveyor Roller
Applicable: Industries Machinery Repair Shops, Manufacturing Plant, Energy & Mining
Weight (KG): 30
Material: Nylon
Color: Customized Size
Size: Customized Color
Mining Industry Standard Nylon Conveyor Roller
Applicable: Industries Machinery Repair Shops, Manufacturing Plant, Energy & Mining
Weight (KG): 30
Material: Nylon
Color: Customized Size
Size: Customized Color
High-quality Plastic Roller, Polymer Roller, Nylon Conveyor Roller
Applicable: Industries Machinery Repair Shops, Manufacturing Plant, Energy & Mining
Weight (KG): 30
Material: Nylon
Color: Customized Size
Size: Customized Color
High Quality Factory Direct Sales Nylon Conveyor Roller Waterproof Dustproof Nylon Roller
Applicable: Industries Machinery Repair Shops, Manufacturing Plant, Energy & Mining
Weight (KG): 30
Material: Nylon
Color: Customized Size
Size: Customized Color
High Quality Dustproof Waterproof Carrier Plastic Belt Conveyor Idler Roller Nylon Conveyor Rollers
Applicable: Industries Machinery Repair Shops, Manufacturing Plant, Energy & Mining
Weight (KG): 30
Material: Nylon
Color: Customized Size
Size: Customized Color
Heavy Duty Industrial Coal Material Conveying Nylon Conveyor Roller
Applicable: Industries Machinery Repair Shops, Manufacturing Plant, Energy & Mining
Weight (KG): 30
Material: Nylon
Color: Customized Size
Size: Customized Color
Good Quality Nylon Conveyor Idler Roller Carrier Idler Roller Nylon Conveyor Roller
Applicable: Industries Machinery Repair Shops, Manufacturing Plant, Energy & Mining
Weight (KG): 30
Material: Nylon
Color: Customized Size
Size: Customized Color
For Friction Nylon Conveyor Roller
Applicable: Industries Machinery Repair Shops, Manufacturing Plant, Energy & Mining
Weight (KG): 30
Material: Nylon
Color: Customized Size
Size: Customized Color
Dust Proof Waterproof Carrier Plastic Belt Conveyor Idler Roller Nylon Conveyor Rollers
Applicable: Industries Machinery Repair Shops, Manufacturing Plant, Energy & Mining
Weight (KG): 30
Material: Nylon
Color: Customized Size
Size: Customized Color
Are nylon rollers quieter?
Yes, nylon rollers are generally quieter compared to metal rollers. They produce less noise due to their smoother operation and ability to absorb vibrations.
Is nylon more durable than steel?
Nylon is not generally more durable than steel. Steel is significantly stronger and more durable, especially under heavy loads or harsh conditions. Nylon is more suitable for applications where noise reduction and resistance to corrosion are important, but it may not withstand the same level of stress as steel.
What is the best plastic material for rollers?
The best plastic material for rollers depends on the application. Commonly used plastics include:
Nylon: Offers good strength, durability, and low friction.
Polyurethane: Provides excellent wear resistance and flexibility.
PVC: Suitable for lightweight applications and resistance to chemicals.
What is the best material for roller bearings?
The best material for roller bearings typically includes:
Chrome Steel: Known for its high hardness and durability.
Stainless Steel: Offers corrosion resistance and strength.
Ceramics: Provides high hardness, low friction, and resistance to high temperatures.
Are nylon wheels strong?
Nylon wheels are reasonably strong for many applications, but they are not as strong as metal wheels. They are suitable for moderate loads and offer advantages in terms of reduced noise and resistance to corrosion.
What is the smoothest roller?
The smoothest rollers are often those made from ceramic or high-grade stainless steel, as they offer very low friction and a highly polished surface. Nylon rollers can also be smooth but may not match the precision of ceramic or metal rollers.
What is least damaging hot rollers?
In heavy industries such as mining, selecting the least damaging hot rollers is crucial for improving production efficiency and extending equipment lifespan. Hot rollers with boride coatings are considered among the least damaging due to their exceptional hardness and wear resistance, effectively combating abrasion and corrosion. Additionally, hot rollers made from high-temperature alloys like Inconel demonstrate excellent heat resistance and oxidation properties, making them suitable for high-temperature operations. For heavy-duty applications in mining, reinforced steel hot rollers combined with advanced heat treatment processes can significantly enhance durability and impact resistance. Choosing the right materials and coatings for hot rollers can not only reduce downtime and maintenance costs but also improve overall production efficiency and safety.
Are hot rollers or regular rollers better?
Hot rollers are often preferred for their ability to set curls or waves quickly due to their heated nature. They can provide long-lasting curls with less damage compared to traditional curling methods. Regular rollers are used without heat and can be gentler but may take longer to achieve the desired results.
What is the function of the nylon roller?
Nylon rollers are widely used in conveyor systems and material handling due to their durability and efficiency. They facilitate smooth movement of materials by reducing friction, which minimizes resistance and enhances conveyor performance. Nylon’s resistance to abrasion, impact, and chemicals makes these rollers suitable for harsh industrial environments. Additionally, they operate more quietly than metal rollers, contributing to a quieter work environment. Their lightweight nature and cost-effectiveness make them an economical choice, and their versatility allows for use in various applications, including packaging and manufacturing. Overall, nylon rollers combine strength, low maintenance, and efficient performance, making them a popular choice for diverse industrial needs.
What are the benefits of stainless steel roller?
Benefits of stainless steel rollers include:
Corrosion Resistance: Ideal for harsh or wet environments.
Durability: High strength and long lifespan.
Low Maintenance: Requires less frequent replacement and maintenance.
Smooth Operation: Provides consistent and smooth performance.
How do you know when your rollers are bad?
In heavy industries such as mining, identifying faulty rollers on conveyor systems is crucial for maintaining operational efficiency. Key indicators of bad rollers include excessive noise, such as grinding or squealing, which often suggests internal damage or misalignment. Uneven wear patterns, such as visible flat spots or cracks, can signal that rollers are not functioning correctly. Additionally, if the conveyor belt shows signs of slippage or misalignment, it might be due to worn-out rollers failing to provide adequate support. Observing increased vibration or excessive heat around the rollers can also indicate issues. Regular visual inspections and performance monitoring are essential for early detection, helping to prevent potential breakdowns and maintain smooth operation. Prompt replacement of defective rollers minimizes downtime and ensures the conveyor system continues to operate efficiently in demanding mining environments.
How do you make rollers last longer?
To extend the lifespan of rollers:
Regular Lubrication: Apply appropriate lubricant to reduce friction and wear.
Keep Clean: Clean the rollers and tracks regularly to remove dirt and debris.
Check Alignment: Ensure rollers and tracks are properly aligned.
Inspect for Wear: Regularly check for signs of wear and replace damaged rollers promptly.
Does it matter how long you leave rollers in?
For most applications, it does not matter how long you leave rollers in, as long as they are properly maintained. However, for specific applications like hot rollers or certain machinery, following recommended usage times is important to ensure optimal performance and avoid potential damage.
How long does nylon last outside?
Nylon’s lifespan outdoors, especially in heavy industries like mining, depends on several factors including environmental conditions and exposure levels. Generally, nylon can last from 1 to 5 years outside, but this varies significantly based on its exposure to sunlight, moisture, and temperature extremes. UV radiation can degrade nylon over time, causing it to become brittle and lose strength. High humidity and direct contact with abrasive materials, common in mining environments, can also shorten its lifespan. To extend durability, nylon products can be treated with UV inhibitors or protective coatings. Regular inspection and maintenance are crucial in heavy industries to address wear and replace components as needed, ensuring that nylon components continue to perform effectively despite harsh outdoor conditions.
What are the three types of rollers?
Gravity Rollers: Use gravity to move items on inclined or horizontal conveyor systems.
Powered Rollers: Driven by motors to move items along conveyors. They can be used for horizontal or inclined applications.
Chain-Driven Rollers: Use chains to drive the rollers, suitable for heavy loads and robust applications.
What are the disadvantages of rollers?
Maintenance Requirements: Rollers require regular upkeep to ensure proper function and prevent issues.
Potential for Jamming: Debris or misalignment can cause rollers to jam.
Wear and Tear: Rollers can wear out over time, especially under heavy loads.
Noise: Rollers, particularly metal ones, can be noisy during operation.
What are the different types of industrial rollers?
Rollers are used for:
Conveyor Systems: To move materials or products efficiently.
Printing Presses: To apply or transfer ink onto surfaces.
Material Handling: To guide and transport items.
Construction Equipment: To compact and smooth surfaces.
What are polyester rollers used for?
Nylon Rope: Better for high-strength and elasticity applications. It is more resistant to abrasion, UV rays, and chemicals, making it suitable for a wide range of uses.
Polypropylene Rope: Better for applications where water resistance is crucial, as it floats and absorbs less moisture. However, it is less strong and durable compared to nylon.
What kind of roller do you use for?
In heavy industries like mining, different types of rollers serve specific purposes to enhance operational efficiency and durability. Conveyor rollers transport materials such as ores across various stages of processing, designed to handle heavy loads and harsh conditions. Crushing rollers are used in crushers to break down raw materials into smaller sizes for further processing, often made from hardened steel for durability. Grinding rollers in mills help grind raw materials into finer particles, typically coated with wear-resistant materials. Guide rollers ensure smooth and accurate movement of materials during processing, maintaining quality and consistency. Support rollers provide stability to moving parts in heavy machinery, distributing weight and reducing component wear. Selecting the appropriate roller type and material is crucial for optimizing performance, minimizing maintenance costs, and improving overall efficiency in industrial operations.
Which roller is used to track a conveyor belt?
Tracking Rollers or Guide Rollers are used to track a conveyor belt. They help to maintain the belt’s alignment and prevent it from drifting off the sides of the conveyor.
Which roller is used to apply or remove tension on the belt?
Tensioning Rollers or Take-Up Rollers are used to apply or remove tension on the conveyor belt. They help adjust the belt tension to ensure proper operation and avoid slack.
How roller chain can be used as conveyor belts?
Roller chains can effectively serve as conveyor belts in industrial applications due to their durability and reliability. In chain conveyor systems, roller chains form a continuous loop, efficiently transporting heavy or bulky items. Sprockets and attachments are used with roller chains to enhance functionality, allowing for precise movement and support of various materials. This design ensures consistent operation and accurate positioning, crucial for many industrial processes. The robust nature of roller chains makes them suitable for demanding environments, where their strength and longevity can handle significant loads. Regular maintenance, including lubrication and tension adjustments, helps maintain smooth operation and extends the chain’s lifespan. By incorporating roller chains into conveyor systems, industries benefit from a versatile and reliable solution for material handling and movement.
Which of the following are types of rollers found on conveyors?
Gravity Rollers
Powered Rollers
Chain-Driven Rollers
Idler Rollers
Guide Rollers
Return Rollers
What is belt roller support material?
Belt Roller Support Material typically refers to the material used for the rollers that support the conveyor belt. Common materials include:
Steel: For heavy-duty applications, providing strength and durability.
Plastic: For lighter applications, offering resistance to corrosion and wear.
Aluminum: Lightweight and resistant to corrosion, suitable for various conveyor systems.
What is a snub roller on a conveyor?
A Snub Roller is used to change the direction of the conveyor belt and increase the belt’s contact with the drive pulley. This helps improve the drive’s efficiency and grip on the belt, ensuring better movement and tension control.
What are guide rollers for conveyor belts?
Guide Rollers help to align and guide the conveyor belt, ensuring that it runs straight and does not drift. They are positioned along the sides of the conveyor belt to keep it centered and prevent it from misaligning.
How do l keep my conveyor belt from slipping?
To prevent a conveyor belt from slipping:
Maintain Proper Tension: Regularly adjust the tension using tensioning rollers or take-up devices.
Check for Wear: Ensure that rollers, pulleys, and the belt are not worn or damaged.
Clean the Belt and Rollers: Remove any debris or material buildup that could reduce traction.
Ensure Proper Alignment: Make sure the belt and rollers are aligned correctly to prevent slippage.
Is a roller on a conveyor belt a pinch point?
Yes, rollers on a conveyor belt can be considered pinch points. They can pose a risk of injury if body parts or clothing get caught between the rollers. Proper guarding and safety measures should be implemented to protect against these hazards.
What are conveyor belt wheels called?
Conveyor belt wheels are commonly referred to as conveyor rollers. They support and guide the conveyor belt as it moves.
What is the spacing for conveyor rollers?
The spacing for conveyor rollers depends on the type of conveyor system and the load being transported. Typically, roller spacing ranges from 3 to 6 inches (75 to 150 mm) for light to moderate loads. For heavy-duty applications, spacing may be closer to ensure adequate support.
What is idler roller conveyor?
An Idler Roller Conveyor uses idler rollers to support and guide the conveyor belt. Idler rollers do not drive the belt but help in maintaining belt alignment and supporting the return side of the conveyor. They are crucial for reducing friction and ensuring smooth belt movement.