Benefits of Using Oil Resistant Conveyor Belt in Industry
Oil resistant conveyor belt is essential in industries where belts are exposed to oils and other greasy substances. These specialized belts are designed to resist the damaging effects of oil, ensuring durability and efficiency in harsh environments. This section provides an overview of the leading manufacturers of oil resistant conveyor belts and their offerings in the market.
Oil Resistant Conveyor Belt Manufacturers
Leading Manufacturers
- ContiTech: A division of Continental AG, ContiTech is a global leader in rubber and plastics technology. They offer a range of oil resistant conveyor belts designed for various industrial applications. Their belts are known for high durability, resistance to wear, and reliable performance under challenging conditions.
- Bridgestone: Bridgestone’s industrial products division manufactures high-quality oil resistant conveyor belts. Their products are engineered to withstand oil exposure, maintaining flexibility and strength. Bridgestone belts are widely used in industries like automotive, manufacturing, and food processing.
- Fenner Dunlop: Known for their innovative conveyor belt solutions, Fenner Dunlop offers oil resistant conveyor belts that provide superior performance and longevity. Their belts are designed to handle heavy loads and resist oil penetration, making them ideal for demanding environments.
- Yokohama: Yokohama Rubber Company produces a variety of conveyor belts, including oil resistant models. Their belts are designed to resist the effects of oil, ensuring a long service life and minimal maintenance. Yokohama belts are used in industries such as mining, agriculture, and chemical processing.
- Mitsuboshi Belting Ltd.: This Japanese manufacturer is renowned for producing high-quality industrial belts. Their oil resistant conveyor belts are designed to deliver excellent performance in environments where oil exposure is a concern. Mitsuboshi belts are durable, flexible, and resistant to wear and tear.
- Goodyear: Goodyear Engineered Products offers a range of oil resistant conveyor belts that are built to last. Their belts are designed to resist oil absorption and degradation, ensuring reliable operation in tough industrial settings. Goodyear belts are used in a variety of applications, from food processing to automotive manufacturing.
Product Offerings
- Standard Oil Resistant Belts: These belts are designed for general industrial use where oil resistance is required. They are made from high-quality rubber compounds that resist oil penetration, ensuring long-lasting performance.
- Heat and Oil Resistant Belts: These belts are designed for applications where both heat and oil resistance are necessary. They are made from specialized rubber compounds that can withstand high temperatures and oil exposure without losing their strength and flexibility.
- Heavy-Duty Oil Resistant Belts: These belts are designed for heavy-duty applications where the conveyor belts are exposed to oils and other harsh substances. They are reinforced with high-strength materials to ensure durability and reliability under extreme conditions.
- Food-Grade Oil Resistant Belts: These belts are designed for use in the food processing industry, where oil resistance and food safety are critical. They are made from FDA-approved materials that resist oil absorption and are safe for contact with food products.
- Custom Oil Resistant Belts: Many manufacturers offer custom oil resistant conveyor belts tailored to specific industrial needs. These belts can be designed to meet unique requirements, such as specific dimensions, load capacities, and resistance levels.
Factors Influencing Oil Resistant Conveyor Belt Price
The price of oil resistant conveyor belts is influenced by a variety of factors. Understanding these factors can help businesses make informed decisions when purchasing conveyor belts for their operations. This section provides a detailed discussion on the various factors that affect the pricing of oil resistant conveyor belts.
Material Composition
- Rubber Compounds: The quality and type of rubber used in the manufacture of oil resistant conveyor belts significantly impact the price. High-quality, oil-resistant rubber compounds are more expensive but offer better performance and longevity.
- Reinforcements: The type and quality of reinforcement materials used in the belts also affect the price. Belts reinforced with materials like steel, polyester, or nylon are generally more expensive due to their enhanced strength and durability.
Belt Construction
- Layering and Thickness: The number of layers and the overall thickness of the belt influence its cost. Thicker belts with multiple layers of reinforcement are more durable and resistant to wear, but they are also more expensive to produce.
- Special Coatings: Belts with special coatings, such as heat-resistant or food-grade coatings, are typically more expensive. These coatings provide additional protection and functionality, justifying the higher cost.
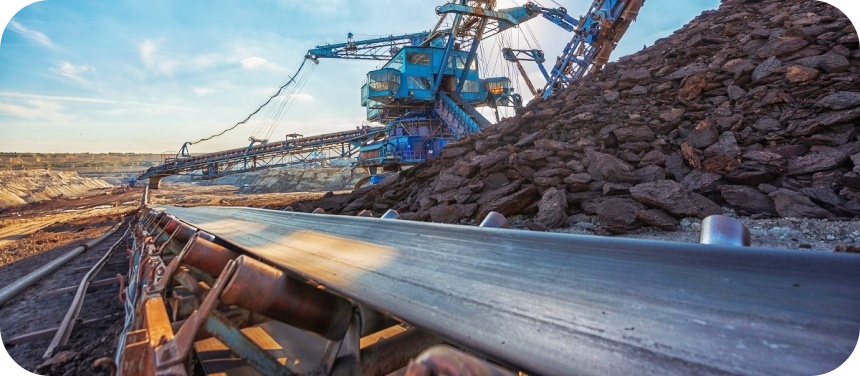
Manufacturing Process
- Advanced Technologies: The use of advanced manufacturing technologies and processes can increase the cost of production. Techniques like precision engineering, vulcanization, and automated production lines ensure high-quality belts but add to the overall expense.
- Quality Control: Rigorous quality control measures and testing procedures ensure that the belts meet industry standards and perform reliably. These measures, while essential, contribute to the cost of the final product.
Customization Options
- Tailored Solutions: Custom-designed oil resistant conveyor belts tailored to specific industrial needs tend to be more expensive. Customization can include specific dimensions, reinforcement materials, and resistance levels to meet unique operational requirements.
- Brand Reputation: Established manufacturers with a strong reputation for quality and reliability often charge a premium for their products. Customers are willing to pay more for belts from reputable brands, knowing they are investing in reliable and durable solutions.
Market Dynamics
- Supply and Demand: Market conditions, such as the balance between supply and demand, influence the price of oil resistant conveyor belts. High demand and limited supply can drive prices up, while an oversupply can lead to lower prices.
- Raw Material Costs: Fluctuations in the cost of raw materials, such as rubber and reinforcement fibers, directly impact the price of conveyor belts. Manufacturers may adjust their prices based on the current cost of these materials.
Regional Factors
- Geographic Location: The location of the manufacturer and the buyer can affect the price due to factors like transportation costs, import/export duties, and regional economic conditions. Locally produced belts may be cheaper due to lower transportation costs and tariffs.
- Regulations and Standards: Compliance with regional regulations and industry standards can also influence the price. Manufacturers may incur additional costs to meet specific regulatory requirements, which are then passed on to the buyer.
Additional Features
- Specialized Features: Belts with specialized features, such as flame resistance, anti-static properties, or enhanced oil resistance, are generally more expensive. These features provide added value and functionality, justifying the higher price.
- Warranty and Support: Manufacturers that offer extended warranties, after-sales support, and maintenance services may charge a premium for their products. These additional services ensure the longevity and reliability of the belts, providing peace of mind to the buyers.
The price of oil resistant conveyor belts is influenced by various factors, including material composition, belt construction, manufacturing processes, customization options, market dynamics, regional factors, and additional features. By understanding these factors, businesses can make informed decisions when selecting and purchasing oil resistant conveyor belts that meet their specific needs and budget constraints. Investing in high-quality, durable belts from reputable manufacturers can result in long-term cost savings and improved operational efficiency.
Choosing the Best Oil Resistant Conveyor Belt for Your Needs
Selecting the best oil resistant conveyor belt is crucial for industries where materials containing oils and fats are frequently handled. The right belt not only ensures efficient and smooth operations but also significantly extends the lifespan of your conveyor system. This guide will help you understand the key factors to consider when choosing an oil resistant conveyor belt tailored to your specific industrial requirements.
Oil Resistance Grades
The first step in selecting the best oil resistant conveyor belt is understanding the different grades of oil resistance. Conveyor belts are classified into various grades based on their ability to resist oil. The common grades include:
- MOR (Moderate Oil Resistance): Suitable for environments where the belt is exposed to moderate levels of oils and fats. This grade provides a balance between cost and oil resistance, making it ideal for industries such as food processing and packaging.
- OR (Oil Resistant): Designed for environments with higher oil exposure. This grade offers enhanced resistance to oils and is commonly used in industries such as automotive manufacturing and metal processing.
- Super Oil Resistant: These belts provide the highest level of oil resistance and are used in extreme conditions where the belt is exposed to high concentrations of oils and fats. Industries such as recycling and chemical processing often require this grade of belt.
Key Factors to Consider
When choosing an oil resistant conveyor belt, several factors must be taken into account to ensure optimal performance and durability. These factors include:
- Material Composition: The material of the belt plays a significant role in its oil resistance. Common materials include rubber, PVC, and polyurethane. Rubber belts are known for their durability and flexibility, while PVC and polyurethane belts offer excellent resistance to oils and fats.
- Belt Thickness: The thickness of the belt is crucial in determining its strength and durability. Thicker belts can handle heavier loads and provide better resistance to wear and tear. However, they may also require more power to operate.
- Temperature Resistance: Depending on the operating environment, you may need a belt that can withstand extreme temperatures. Ensure that the oil resistant conveyor belt you choose can handle the temperature range of your application.
- Load Capacity: Consider the load capacity of the belt, which depends on the weight and size of the materials being transported. Choose a belt with an appropriate load capacity to avoid overloading and potential damage.
- Surface Pattern: The surface pattern of the belt affects its grip and ability to transport materials without slipping. Smooth surfaces are ideal for transporting packaged goods, while cleated or rough surfaces are better for bulk materials.
- Chemical Compatibility: In addition to oil resistance, consider the belt’s compatibility with other chemicals it may come into contact with. This is particularly important in industries such as chemical processing and waste management.
Industry-Specific Requirements
Different industries have specific requirements when it comes to choosing an oil resistant conveyor belt. Here are some considerations for various sectors:
- Food Processing: In the food industry, hygiene and safety are paramount. Choose belts made from food-grade materials that comply with industry standards. Look for belts that are easy to clean and resistant to oils, fats, and other food substances.
- Automotive Manufacturing: The automotive industry requires belts that can handle heavy loads and exposure to oils and lubricants. Opt for belts with high tensile strength and superior oil resistance to ensure smooth and reliable operations.
- Recycling: Recycling facilities often deal with mixed materials, including oily and greasy substances. Select belts that offer excellent oil resistance and durability to withstand the abrasive nature of the materials being processed.
- Chemical Processing: In chemical plants, belts must resist a wide range of chemicals, including oils. Choose belts with high chemical and oil resistance to prevent degradation and ensure long-term reliability.
Installation and Maintenance
Proper installation and maintenance are essential to maximizing the lifespan and performance of your oil resistant conveyor belt. Follow these tips:
- Correct Installation: Ensure that the belt is installed according to the manufacturer’s guidelines. Proper tensioning and alignment are crucial to prevent slippage and uneven wear.
- Regular Inspections: Conduct regular inspections to check for signs of wear, damage, or oil degradation. Address any issues promptly to prevent further damage.
- Cleaning and Lubrication: Keep the belt and surrounding components clean and free from oil buildup. Use appropriate cleaning agents and lubricants recommended by the manufacturer.
- Replacement of Worn Parts: Replace worn or damaged parts, such as the scraper blade and rollers, to maintain optimal performance.
By considering these factors and industry-specific requirements, you can select the best oil resistant conveyor belt for your needs, ensuring efficient and reliable operations.
Advantages of Using Oil Resistant Conveyor Belt
Oil resistant conveyor belts offer numerous benefits that make them indispensable in various industrial applications. These belts are specially designed to withstand the degrading effects of oils and fats, ensuring durability and efficiency. This section provides an overview of the advantages and applications of oil resistant conveyor belts in different industries.
Enhanced Durability
One of the primary advantages of using an oil resistant conveyor belt is its enhanced durability. These belts are made from materials that resist the harmful effects of oils and fats, preventing premature wear and tear. This durability translates to a longer lifespan for the belt, reducing the frequency and cost of replacements.
Improved Performance
Oil resistant conveyor belts maintain their structural integrity and flexibility even when exposed to oils. This ensures consistent performance, minimizing downtime and enhancing productivity. The belts are designed to handle various types of materials, from oily food products to automotive parts, without compromising on efficiency.
Versatility
Oil resistant conveyor belts are highly versatile and can be used in a wide range of industries. Their ability to resist oil degradation makes them suitable for applications in food processing, automotive manufacturing, recycling, chemical processing, and more. This versatility allows businesses to standardize their conveyor systems across different applications, simplifying maintenance and inventory management.
Safety and Compliance
In industries such as food processing, safety and compliance with health standards are critical. Oil resistant conveyor belts made from food-grade materials ensure that the conveyed products remain uncontaminated. These belts comply with industry regulations, providing a safe and hygienic solution for transporting food and other sensitive materials.
Cost Savings
Although oil resistant conveyor belts may have a higher initial cost compared to standard belts, they offer significant cost savings in the long run. The extended lifespan and reduced maintenance requirements lead to lower operational costs. Additionally, the improved performance and reduced downtime contribute to higher productivity and profitability.
Applications in Different Industries
- Food Processing: In the food industry, oil resistant conveyor belts are essential for handling products that contain oils and fats. These belts prevent contamination and ensure a hygienic process. They are used in applications such as meat and poultry processing, baking, and snack production.
- Automotive Manufacturing: The automotive industry benefits from oil resistant belts for transporting oily and greasy components. These belts are used in assembly lines, parts handling, and material transport within the manufacturing plant.
- Recycling: Recycling facilities handle a variety of materials, including those contaminated with oils and grease. Oil resistant conveyor belts provide the durability and performance needed to efficiently process these materials without frequent belt replacements.
- Chemical Processing: In chemical plants, oil resistant belts are crucial for transporting materials that may contain oils or chemicals. These belts ensure safe and efficient handling, preventing chemical degradation and maintaining productivity.
- Packaging: The packaging industry uses oil resistant conveyor belts to handle products with oil-based lubricants and coatings. These belts ensure smooth transport and packaging processes without contamination.
Oil resistant conveyor belts offer numerous advantages that make them essential for various industrial applications. Their enhanced durability, improved performance, versatility, safety, and cost savings contribute to efficient and reliable operations. By understanding the benefits and selecting the right oil resistant conveyor belt for your specific needs, you can ensure optimal performance and longevity of your conveyor system.
Maintenance Tips for Oil Resistant Conveyor Belt
Maintaining oil resistant conveyor belts is essential to ensure their longevity, efficiency, and optimal performance in industries exposed to oil and greasy substances. Proper maintenance can prevent costly downtime, reduce the risk of belt failure, and extend the belt’s lifespan. This section provides practical advice on how to maintain oil resistant conveyor belts effectively.
Regular Inspections
- Visual Inspections: Conduct regular visual inspections to check for signs of wear, damage, or contamination. Look for cracks, cuts, abrasions, and oil buildup on the belt surface. Early detection of issues can prevent more significant problems and costly repairs.
- Check for Misalignment: Misalignment can cause uneven wear and reduce the belt’s efficiency. Inspect the conveyor system to ensure the belt runs straight and true. Adjust the tracking and alignment as needed to prevent premature wear and tear.
- Inspect Belt Tension: Proper belt tension is crucial for efficient operation. Regularly check the tension to ensure it is within the manufacturer’s recommended range. Over-tensioning can cause excessive wear, while under-tensioning can lead to slippage and reduced efficiency.
Cleaning and Lubrication
- Cleaning: Regularly clean the oil resistant conveyor belt to remove any accumulated oil, grease, and debris. Use appropriate cleaning agents that do not damage the belt material. Avoid using harsh chemicals that can degrade the rubber compounds.
- Lubrication: Lubricate the conveyor system’s moving parts, such as bearings, rollers, and pulleys, to reduce friction and wear. Use lubricants that are compatible with oil resistant conveyor belts to prevent contamination and ensure smooth operation.
Preventive Maintenance
- Scheduled Maintenance: Implement a preventive maintenance schedule to address potential issues before they become major problems. Regularly replace worn-out components, such as rollers, pulleys, and bearings, to maintain the conveyor system’s efficiency.
- Condition Monitoring: Use condition monitoring tools, such as vibration analysis and thermal imaging, to detect early signs of mechanical issues. Monitoring the condition of the conveyor system can help identify problems before they lead to belt failure.
Proper Storage and Handling
- Storage: Store oil resistant conveyor belts in a cool, dry, and well-ventilated area away from direct sunlight, heat sources, and chemicals. Proper storage conditions can prevent degradation and extend the belt’s shelf life.
- Handling: Handle the belts with care to avoid damage during transportation and installation. Use appropriate lifting equipment and techniques to prevent cuts, abrasions, and other forms of damage.
Belt Splicing and Repair
- Splicing: Proper splicing techniques are essential for maintaining the belt’s integrity and performance. Use the manufacturer’s recommended splicing methods and materials to ensure a strong and durable splice.
- Repair: Promptly repair any damage to the oil resistant conveyor belt to prevent further deterioration. Use repair materials compatible with the belt’s rubber compounds to ensure a seamless and effective repair.
Training and Documentation
- Training: Provide training to maintenance personnel on proper maintenance practices and procedures for oil resistant conveyor belts. Well-trained staff can effectively identify and address issues, ensuring the belt’s longevity and efficiency.
- Documentation: Keep detailed records of maintenance activities, including inspections, cleaning, lubrication, repairs, and replacements. Documenting maintenance activities can help track the belt’s condition and identify recurring issues.
By following these practical maintenance tips, businesses can ensure the longevity and efficiency of their oil resistant conveyor belts. Regular inspections, proper cleaning and lubrication, preventive maintenance, and proper storage and handling are essential for maintaining optimal performance. Additionally, using proper splicing and repair techniques, providing training to maintenance personnel, and maintaining detailed documentation can further enhance the belt’s reliability and longevity.
Innovations in Oil Resistant Conveyor Belt Technology
The conveyor belt industry continually evolves, with manufacturers developing innovative technologies to improve the performance and durability of oil resistant conveyor belts. These advancements enhance the belts’ resistance to oil, reduce maintenance requirements, and extend their lifespan. This section explores the latest technological advancements in oil resistant conveyor belts and their impact on performance.
Advanced Rubber Compounds
- High-Performance Rubber: Manufacturers are developing advanced rubber compounds that offer superior oil resistance and durability. These high-performance rubber compounds maintain their flexibility and strength, even when exposed to harsh oils and chemicals.
- Hybrid Materials: The use of hybrid materials, combining synthetic and natural rubber, enhances the oil resistance and overall performance of the conveyor belts. These materials provide better resistance to oil penetration and degradation.
Enhanced Reinforcements
- Kevlar Reinforcement: Kevlar, known for its high strength and resistance to abrasion, is being used to reinforce oil resistant conveyor belts. Kevlar-reinforced belts offer improved durability and resistance to wear, making them ideal for heavy-duty applications.
- Steel Cord Reinforcement: Steel cord-reinforced conveyor belts provide exceptional strength and durability. These belts are designed to withstand high loads and resist oil penetration, ensuring long-lasting performance in demanding environments.
Innovative Coatings and Surface Treatments
- Nano-Coatings: Nano-coatings are being applied to oil resistant conveyor belts to enhance their resistance to oil and other contaminants. These coatings create a barrier that prevents oil absorption and extends the belt’s lifespan.
- Anti-Stick Surface Treatments: Anti-stick surface treatments reduce the adhesion of oil and other substances to the belt surface. This innovation makes cleaning and maintenance easier, improving the overall efficiency of the conveyor system.
Smart Conveyor Belt Technologies
- Embedded Sensors: Smart conveyor belts with embedded sensors monitor the belt’s condition in real-time. These sensors detect wear, tension, and misalignment, providing valuable data for predictive maintenance and reducing the risk of unexpected failures.
- IoT Integration: The integration of Internet of Things (IoT) technology enables remote monitoring and control of oil resistant conveyor belts. IoT-enabled systems provide real-time data on belt performance, allowing for proactive maintenance and optimizing operational efficiency.
Environmentally Friendly Solutions
- Eco-Friendly Materials: Manufacturers are developing eco-friendly oil resistant conveyor belts made from sustainable materials. These belts are designed to minimize environmental impact while maintaining high performance and durability.
- Recyclable Belts: Innovations in recycling technology have led to the development of recyclable conveyor belts. These belts can be recycled at the end of their life cycle, reducing waste and promoting sustainability.
Improved Manufacturing Processes
- Precision Engineering: Advances in precision engineering have led to the production of oil resistant conveyor belts with tighter tolerances and consistent quality. This innovation ensures that the belts perform reliably and last longer.
- Automated Production: The use of automated production lines improves the efficiency and consistency of manufacturing oil resistant conveyor belts. Automated processes reduce human error and ensure high-quality products.
Customized Solutions
- Tailored Designs: Manufacturers are offering customized oil resistant conveyor belts tailored to specific industrial needs. These tailored designs include specific dimensions, load capacities, and resistance levels to meet unique operational requirements.
- Application-Specific Belts: Development of application-specific belts addresses the unique challenges of different industries. For example, food-grade oil resistant conveyor belts are designed to meet the stringent requirements of the food processing industry.
The latest technological advancements in oil resistant conveyor belt have significantly improved their performance, durability, and efficiency. Advanced rubber compounds, enhanced reinforcements, innovative coatings, and smart technologies are driving the industry forward. Environmentally friendly solutions, improved manufacturing processes, and customized designs further enhance the belts’ reliability and sustainability. By embracing these innovations, businesses can ensure optimal performance and longevity of their oil resistant conveyor belts, reducing maintenance costs and improving operational efficiency.
Looking for pricing details? Use this form to request information about our conveyor belts.
FAQs about Oil Resistant Conveyor Belt
Oil resistance belts are specially designed to handle materials that contain oils and fats, which can degrade standard conveyor belts. These belts are classified into different grades based on their level of oil resistance. The common grades include MOR (Moderate Oil Resistance), which is suitable for less severe oil exposure, and OR (Oil Resistant), which is used for more intense oil conditions. Additionally, there are super oil resistant grades for environments with extreme oil exposure. The specific grade you need depends on the type and concentration of oil in your conveyed materials, ensuring durability and efficient performance in oily conditions.
HR (Heat Resistant) belts are designed to withstand high temperatures that can damage regular conveyor belts. There are several types of HR belts, each suited for different temperature ranges and applications:
HR T1: This type can handle temperatures up to 100°C. It is suitable for applications where materials are moderately hot.
HR T2: These belts can endure temperatures up to 125°C. They are used in applications with higher heat levels.
HR T3: Capable of withstanding temperatures up to 150°C, these belts are ideal for operations with very high-temperature materials.
Super Heat Resistant: These belts can handle even higher temperatures, often up to 200°C or more, making them suitable for extreme heat applications.
Each type of HR belt is designed to maintain structural integrity and performance despite high temperatures, ensuring long service life and reliability in demanding environments.
Conveyor belts come with various specifications tailored to different industrial applications. Key specifications include:
Material: Conveyor belts are made from materials such as rubber, PVC, PU, and fabric, each offering different properties like flexibility, strength, and resistance to chemicals or abrasion.
Width and Length: The width and length of a conveyor belt are customized based on the application requirements. Common widths range from a few inches to several feet.
Thickness: Belt thickness varies depending on the material and the load it needs to carry. Thicker belts are generally more durable and can handle heavier loads.
Tensile Strength: This indicates the belt’s ability to withstand stretching forces. It is measured in pounds per inch (PIW) or Newtons per millimeter (N/mm).
Temperature Resistance: Some belts are designed to withstand specific temperature ranges, making them suitable for either hot or cold environments.
Surface Pattern: The surface pattern (smooth, rough, cleated) can affect the belt’s grip and ability to move different types of materials.
These specifications ensure that the conveyor belt can perform efficiently in its intended application, providing reliability and longevity.
Belt conveyors are versatile systems used across various industries. Different types of belt conveyors are designed to meet specific needs:
Flat Belt Conveyor: This is the most common type of conveyor belt, featuring a flat surface ideal for transporting various goods horizontally.
Inclined/Declined Belt Conveyor: These conveyors are used to move products up or down between different levels, making them perfect for applications with height differences.
Cleated Belt Conveyor: Equipped with vertical cleats or barriers, these belts are suitable for transporting loose or bulk materials, preventing them from slipping.
Modular Belt Conveyor: Made of interlocking plastic segments, these belts are highly durable and easy to maintain. They are used in food processing and other hygienic applications.
Sidewall Belt Conveyor: Designed with corrugated sidewalls and cross cleats, these conveyors can carry materials at steep angles or even vertically.
Roller Bed Conveyor: These conveyors use rollers instead of a flat surface, reducing friction and making them ideal for transporting heavy loads over long distances.
Each type of belt conveyor is designed to optimize performance, efficiency, and safety for specific industrial tasks, ensuring smooth and reliable operation.
Last Updated on July 31, 2024 by Jordan Smith
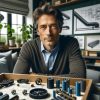
Jordan Smith, a seasoned professional with over 20 years of experience in the conveyor system industry. Jordan’s expertise lies in providing comprehensive solutions for conveyor rollers, belts, and accessories, catering to a wide range of industrial needs. From initial design and configuration to installation and meticulous troubleshooting, Jordan is adept at handling all aspects of conveyor system management. Whether you’re looking to upgrade your production line with efficient conveyor belts, require custom conveyor rollers for specific operations, or need expert advice on selecting the right conveyor accessories for your facility, Jordan is your reliable consultant. For any inquiries or assistance with conveyor system optimization, Jordan is available to share his wealth of knowledge and experience. Feel free to reach out at any time for professional guidance on all matters related to conveyor rollers, belts, and accessories.