Parts of Belt Conveyor System: Types, Functions, Materials
Belt conveyors stand as the lifelines of myriad industries, facilitating the seamless flow of goods and materials with unmatched efficiency. From the intricate pathways of mining operations to the bustling floors of packaging plants, these conveyors ensure that productivity remains at its peak. However, the true backbone of their unwavering performance lies in the meticulous assembly of various parts of belt conveyor system. Each component, meticulously engineered, plays a pivotal role in the conveyor’s operation, dictating its reliability, efficiency, and adaptability to diverse industrial needs. Thus, a profound understanding of these parts is not just beneficial but essential for anyone involved in the design, maintenance, or optimization of these systems. It ensures not only the longevity of the conveyor but also the safety and productivity of the operations it supports.
Decoding the Parts of Belt Conveyor System
The Key Parts of Belt Conveyor System
Delving into the anatomy of a belt conveyor system reveals a complex structure made up of several key components, each playing a vital role in the system’s operation and efficiency. Understanding these parts of belt conveyor system is crucial for anyone involved in the operation, maintenance, or design of these systems.
Conveyor Belt
At the heart of every belt conveyor system lies the conveyor belt itself, a continuous loop of material that transports goods from one point to another. The choice of conveyor belt material is critical and varies based on the application. Common materials include rubber, polymer, and even metal for more demanding industrial environments. The conveyor belt’s role is pivotal, as it directly contacts and moves the material, making its durability, texture, and strength key factors in the system’s overall performance. Various types of conveyor belts are designed to meet specific needs, such as heat-resistant belts for high-temperature environments, anti-static belts for sensitive electronic components, and food-grade belts for the food processing industry.
Head Pulley and Tail Pulley
The head pulley and tail pulley are essential components at either end of the belt conveyor system. The head pulley, located at the discharge end, is driven by the conveyor’s motor, propelling the conveyor belt and the materials it carries. The tail pulley, found at the loading end, serves as a return point for the belt. The size and material of these pulleys are significant because they must withstand the system’s operational stresses and strains. For instance, larger pulleys are used to increase the belt’s contact area, improving traction and reducing slippage, while the choice of material, such as steel or ceramic, can enhance durability and reduce wear.
Idler Rollers
Idler rollers are the unsung heroes of the belt conveyor system, providing crucial support to the conveyor belt and the materials it transports. These rollers help maintain the belt’s tension and alignment, preventing sagging and ensuring smooth operation. Various types of idler rollers are used in belt conveyor systems, including troughing idlers, which shape the belt into a trough for carrying bulk materials; rubber disk idlers, which prevent material buildup on the belt; screw idler rollers, designed for challenging environments where traditional scrapers cannot be used; and trainer idlers, which correct any misalignment of the belt.
Conveyor Frame
The conveyor frame acts as the skeleton of the belt conveyor system, providing the necessary structural support. It holds the rollers, pulleys, and the drive system in place, ensuring the conveyor maintains its shape and alignment under the weight of the materials it carries. The design and construction of the conveyor frame are critical for the system’s durability and dependability, with materials ranging from steel for heavy-duty industrial applications to aluminum for lighter operations.
Drive System
The drive system is the powerhouse of the belt conveyor, comprising the motor and gearbox that energize the entire operation. The motor provides the necessary power to turn the head pulley, which in turn moves the conveyor belt. The gearbox adjusts the motor’s speed to the desired conveyor speed, ensuring efficient and controlled material transport. Selecting the right motor and gearbox is crucial, as they must match the conveyor’s load requirements and operational conditions, such as speed, torque, and power needs.
Understanding these parts of belt conveyor system is essential for optimizing the conveyor’s performance, ensuring its reliability, and extending its service life. Each component, from the conveyor belt to the drive system, plays a pivotal role in the system’s operation, and their proper selection, maintenance, and operation are key to the success of any conveyor-dependent operation.
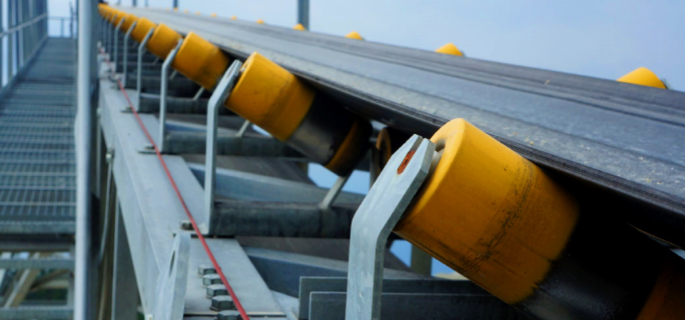
Exploring Additional Parts of Belt Conveyor System
Beyond the primary components that form the backbone of a belt conveyor system, there are additional parts of the belt conveyor system that play crucial roles in ensuring its efficient operation, safety, and longevity. These components, often overlooked, are vital in maintaining the conveyor’s performance and reliability.
Take-Up Unit
The take-up unit is an integral part of belt conveyor system, responsible for maintaining the appropriate tension in the conveyor belt. Proper belt tension is essential for effective grip between the belt and the pulleys and for preventing the belt from sagging or slipping. The take-up unit can be gravity-operated, where a counterweight maintains tension, or it can be mechanically adjusted using screws or hydraulic systems. The choice between these types depends on the conveyor length, the load it carries, and the operational conditions.
Cleaning Devices
Keeping the conveyor belt clean is not just about maintaining hygiene, especially in food processing applications; it’s also about ensuring the longevity and efficiency of the belt. Cleaning devices such as belt scrapers, brushes, and air knives remove debris and residues that can adhere to the belt surface during operation. These devices help prevent material buildup that can lead to belt misalignment, excessive wear, and even the harboring of bacteria in food-grade applications.
Loading and Discharge Chutes
Loading and discharge chutes are critical parts of belt conveyor system, designed to efficiently guide materials onto or off the conveyor belt. The design of these chutes is crucial to minimize spillage and ensure a smooth transfer of materials. Well-designed chutes can also help control the flow of materials, reduce dust and noise, and prevent damage to the conveyor belt and the materials being conveyed.
Safety and Control Devices
Safety and control devices are indispensable in any belt conveyor system, ensuring the safety of the operators and the smooth operation of the conveyor. Emergency stop buttons, belt misalignment switches, speed monitors, and pull cord switches are some of the safety devices that can halt the conveyor in case of an emergency or malfunction. Control devices, on the other hand, such as sensors, counters, and weigh scales, help in monitoring and controlling the flow of materials, ensuring the conveyor operates within the desired parameters.
Each of these additional components plays a specific role in enhancing the functionality, safety, and efficiency of a belt conveyor system. From the take-up unit that maintains the necessary tension in the belt to the safety devices that protect the operators and the system itself, these parts are integral to the smooth operation of any belt conveyor system. Understanding the functions and importance of these additional parts of belt conveyor system is crucial for anyone involved in the design, operation, or maintenance of these systems.
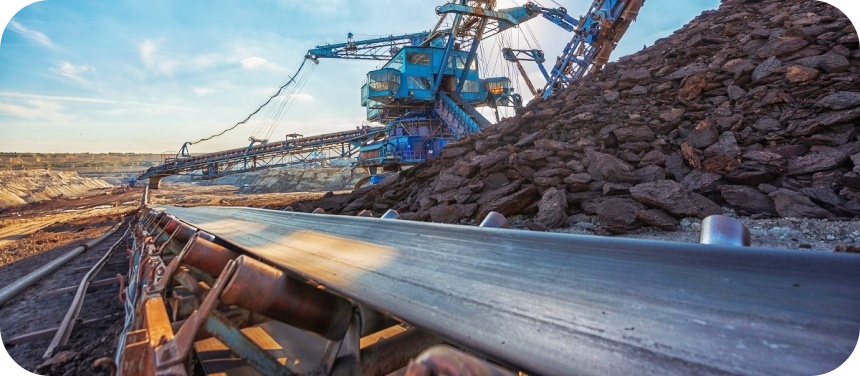
The Functions of Parts of Belt Conveyor System
A belt conveyor system is an essential and versatile part of many industrial operations, used for transporting materials from one location to another. Here are the main functional parts of a belt conveyor system:
1. Belt
- Function: The belt is the carrying medium of the conveyor system, typically made from layers of rubber and fabric, and designed to withstand the load it will carry.
- Materials: Rubber, fabric, metal, or a combination of these materials.
2. Conveyor Frame
- Function: The structure that supports and holds the conveyor components, ensuring the belt remains aligned and runs smoothly.
- Materials: Steel, aluminum, or other sturdy materials.
3. Drive Unit
- Function: Powers the conveyor belt, enabling it to move and transport materials.
- Components: Motor, gearbox, drive pulley, and other drive mechanisms.
4. Pulleys
- Function: Guide and support the conveyor belt, ensuring it stays on track.
- Types: Drive pulley, tail pulley, bend pulley, take-up pulley, and snub pulley.
5. Idlers/Rollers
- Function: Support the belt and the load being carried, reducing friction and wear on the belt.
- Types: Carrying idlers, return idlers, impact idlers, and training idlers.
6. Take-up Unit
- Function: Maintains the necessary tension on the conveyor belt to prevent slippage and ensure smooth operation.
- Types: Screw take-up, gravity take-up, and automatic take-up.
7. Belt Cleaner/Scraper
- Function: Removes material that adheres to the belt, preventing buildup and ensuring efficient operation.
- Types: Primary cleaner, secondary cleaner, and tertiary cleaner.
8. Skirt Board and Skirting
- Function: Prevents material spillage at transfer points by containing the load on the belt.
- Materials: Rubber or other flexible materials.
9. Feed Chute
- Function: Directs the material onto the conveyor belt at the loading point.
- Materials: Metal, plastic, or other wear-resistant materials.
10. Discharge Chute
- Function: Directs the material off the conveyor belt at the unloading point.
- Materials: Metal, plastic, or other wear-resistant materials.
11. Control System
- Function: Manages the operation of the conveyor system, including starting, stopping, and speed control.
- Components: Sensors, switches, controllers, and software systems.
12. Safety Devices
- Function: Ensure the safe operation of the conveyor system.
- Types: Emergency stop switches, safety guards, warning alarms, and interlocks.
13. Support Structures
- Function: Provide stability and support to the conveyor system, particularly over long spans.
- Materials: Steel beams, trusses, and other structural components.
14. Hoppers and Bins
- Function: Store and feed materials onto the conveyor belt.
- Materials: Metal, plastic, or other durable materials.
15. Belt Fasteners
- Function: Join the ends of the conveyor belt to form a continuous loop.
- Types: Mechanical fasteners, vulcanized splices, and endless belts.
These components work together to create a cohesive and efficient belt conveyor system that can handle a wide range of materials and operating conditions.
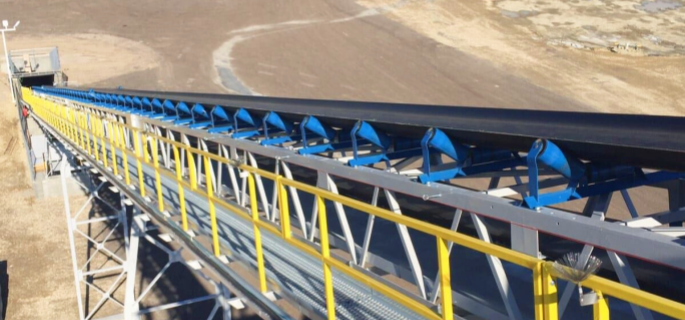
Exploring the Parts of Belt Conveyor System Across Different Types
The versatility of belt conveyors is evident in the variety of types available, each designed to meet specific industrial needs. Understanding the parts of belt conveyor system in each type is crucial for optimizing its function and efficiency. Below is a detailed look at some common types of belt conveyors and the unique components that constitute their design.
Each type of belt conveyor is designed with specific parts of belt conveyor system that cater to its intended use, ensuring efficiency and reliability in operations. For a more in-depth understanding, diagrams and PDFs can provide a visual representation of these conveyor types, illustrating how each component fits into the system and contributes to its overall functionality.
Selecting The Parts of Belt Conveyor System
Selecting the parts of a belt conveyor system requires understanding the specific requirements of the application, including the type of material being transported, the environment, and the desired performance. Here are the key components to consider:
Conveyor Belt
- Material: Depending on the type of material being transported (e.g., abrasive materials, food items), the belt material can vary (e.g., rubber, PVC, fabric, metal).
- Width and Length: Determined by the material load and the conveyor system layout.
- Strength: Should match the load requirements and operating conditions.
Conveyor Rollers
- Carrying Rollers: Support the loaded belt. They should be selected based on the belt width and load capacity.
- Return Rollers: Support the empty belt on the return side. They should be robust enough to handle the belt tension.
- Impact Rollers: Placed at loading points to absorb impact forces and protect the belt.
Pulleys
- Drive Pulley: Drives the belt. It should be sized appropriately for the load and motor power.
- Tail Pulley: Provides tension to the belt. It should match the belt width and tension requirements.
- Snub Pulley: Increases the belt wrap angle on the drive pulley for better traction.
- Bend Pulley: Used to change the direction of the belt or provide additional belt tension.
Motor and Drive System
- Motor: Sized based on the conveyor load and speed requirements. It can be electric or hydraulic.
- Drive System: Can include gearboxes, V-belts, and chains, depending on the application.
Idlers
- Troughing Idlers: Support the belt in the load-carrying section, usually in sets of three or five rollers.
- Return Idlers: Support the empty belt on the return side, typically single rollers.
Belt Cleaners and Scrapers
- Primary Cleaners: Positioned at the head pulley to remove most of the material adhering to the belt.
- Secondary Cleaners: Provide additional cleaning to ensure minimal material carryback.
Skirt Boards and Rubber
- Skirt Boards: Prevent spillage at loading points. They should be adjustable and durable.
- Skirt Rubber: Seals the edges of the belt to prevent material spillage.
Conveyor Frame
- Structure: Provides support for all the components. It should be sturdy and designed for the specific application.
- Leg Supports: Ensure the conveyor is stable and can handle the load.
Belt Tensioning System
- Take-Up Units: Maintain proper belt tension. Can be manual, spring-loaded, or gravity-based.
Safety Features
- Emergency Stop Switches: Placed along the conveyor for quick shutdown in case of an emergency.
- Belt Misalignment Switches: Detect and correct belt misalignment to prevent damage.
Accessories
- Load Zones: Designed to minimize impact and wear at loading points.
- Transfer Points: Ensure smooth transfer of materials between conveyors or other equipment.
- Dust Control Systems: Minimize dust generation and improve air quality.
Monitoring Systems
- Condition Monitoring: For real-time monitoring of conveyor performance and maintenance needs.
- Automation and Control: Integration with automated systems for improved efficiency and control.
Selecting the right components for your belt conveyor system is crucial for ensuring efficiency, reliability, and longevity. Each part should be carefully chosen based on the specific requirements of your application.
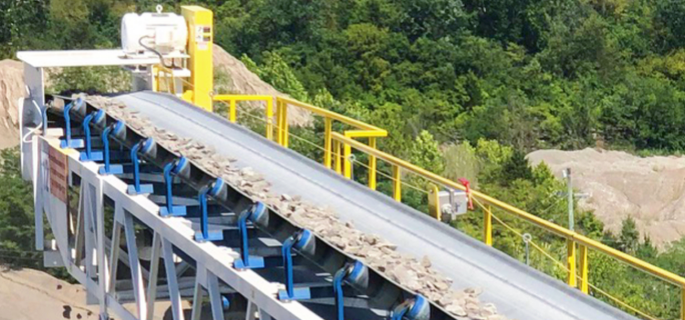
Key Design Considerations for the Parts of Belt Conveyor System
When it comes to the design of a belt conveyor system, meticulous attention to the parts of the belt conveyor system is paramount. These considerations are not just about ensuring the conveyor’s functionality but also about extending its service life and maximizing its efficiency. Here are some critical design considerations for the parts of a belt conveyor system:
- Material Compatibility: The materials used for the conveyor belt and other components must be compatible with the products being transported. This includes considering factors like abrasion resistance, chemical resistance, and temperature tolerance to prevent premature wear and failure.
- Load Capacity: The system must be designed to handle the maximum expected load without strain. This involves calculating the tensile strength required for the conveyor belt and ensuring the frame, rollers, and pulleys are robust enough to support the load.
- Belt Speed: The speed at which the conveyor belt moves must be optimized for the specific application. Too fast, and it may lead to product damage or spillage; too slow, and it could reduce throughput and efficiency.
- Conveyor Length and Layout: The overall length of the conveyor and its layout, including any curves, inclines, or declines, must be carefully planned. This impacts the choice of drive system, belt type, and tensioning mechanisms.
- Drive System Power: Selecting an appropriately sized motor and gearbox to provide sufficient power for the conveyor’s intended use is crucial. This includes considering factors like starting torque and the ability to maintain consistent belt speed under varying load conditions.
- Safety Features: Incorporating safety features such as emergency stops, guards, and warning signals is essential to protect operators and maintenance personnel. These features should be an integral part of the design from the outset.
- Ease of Maintenance: Designing the conveyor for easy access to critical parts for maintenance and cleaning can significantly reduce downtime and extend the system’s lifespan. This includes considerations for modular designs that allow for quick replacement of worn or damaged components.
- Environmental Considerations: The operating environment can greatly affect the design choices for a conveyor system. For example, systems used outdoors or in harsh industrial environments may require special materials and protective coatings to withstand the conditions.
For those seeking a deeper understanding of these design considerations, numerous belt conveyor design handbooks and PDFs are available. These resources provide valuable insights into best practices and detailed guidance on designing a belt conveyor system that is both efficient and durable. By carefully considering each aspect of the parts of belt conveyor system, designers can create solutions that meet the specific needs of their applications while ensuring long-term reliability and performance.
Improve efficiency with our reliable conveyor belt products.
FAQs about Parts of Belt Conveyor System
A belt conveyor is a complex system with many components working in harmony to transport materials from one point to another. The primary parts of a belt conveyor system include the conveyor belt, which is the medium of transport; the idler rollers, which support the belt and the materials being conveyed; the pulleys (head and tail pulleys), which drive the belt and provide tension to it; the drive system, consisting of a motor and a gearbox, which powers the conveyor; and the conveyor frame, which provides structural support. Additionally, there are various accessory components such as the take-up unit for maintaining belt tension, cleaning devices for belt maintenance, loading and discharge chutes for material handling, and safety and control devices to ensure the safe operation of the conveyor system. Each of these parts plays a crucial role in the conveyor’s functionality and efficiency, making it essential to understand their purpose and how they contribute to the system’s overall performance.
The structure of a conveyor belt is designed to provide durability, flexibility, and the ability to transport a variety of materials efficiently. At its core, a conveyor belt consists of two main elements: the carcass and the cover. The carcass, often made from materials like fabric, steel, or polyester, provides the belt with tensile strength and shape. It is the backbone of the belt, designed to withstand the operational stresses it faces. The cover, typically made from rubber, PVC, or other durable materials, protects the carcass from wear and environmental factors like moisture, chemicals, and temperature variations. The cover can be customized with various textures, patterns, or cleats to suit specific material handling needs, such as providing extra grip for inclined conveyance or resistance to particular chemicals. The combination of these elements results in a conveyor belt that can reliably transport materials across different distances and conditions.
A conveyor belt system is an assembly of various components working together to transport materials from one location to another. It is a highly efficient, reliable, and cost-effective solution for material handling in numerous industries, including mining, manufacturing, agriculture, and logistics. The system typically consists of a continuous loop of a conveyor belt that moves over rollers and pulleys, driven by a motor. The materials to be transported are placed on the belt, which moves them to their intended destination. Conveyor belt systems can be customized with various features such as speed controls, directional changes, and inclines or declines to accommodate specific operational requirements. They are favored for their ability to move large volumes of materials over significant distances with minimal human intervention, enhancing productivity and safety in industrial operations.
The working principle of a belt conveyor is relatively straightforward. It operates on the concept of using a powered pulley system to move a continuous loop of a conveyor belt, which in turn transports materials placed upon it. The system typically consists of a motor that drives a pulley (often referred to as the drive pulley or head pulley) at one end of the conveyor. As the drive pulley rotates, it imparts motion to the conveyor belt. The belt then moves over additional pulleys and idler rollers, which support the belt and help to maintain its tension and alignment. The materials placed on the moving belt are carried from the loading point to the discharge point, where they are offloaded. The belt then loops back to the starting point, passing over a tail pulley, which may serve to adjust the belt’s tension. This continuous loop allows for the efficient and continuous transport of materials, making belt conveyors an essential component of many material handling systems.
Last Updated on July 10, 2024 by Jordan Smith
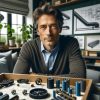
Jordan Smith, a seasoned professional with over 20 years of experience in the conveyor system industry. Jordan’s expertise lies in providing comprehensive solutions for conveyor rollers, belts, and accessories, catering to a wide range of industrial needs. From initial design and configuration to installation and meticulous troubleshooting, Jordan is adept at handling all aspects of conveyor system management. Whether you’re looking to upgrade your production line with efficient conveyor belts, require custom conveyor rollers for specific operations, or need expert advice on selecting the right conveyor accessories for your facility, Jordan is your reliable consultant. For any inquiries or assistance with conveyor system optimization, Jordan is available to share his wealth of knowledge and experience. Feel free to reach out at any time for professional guidance on all matters related to conveyor rollers, belts, and accessories.