The World’s Longest Phosphate Conveyor Belt
The phosphate conveyor belt, an engineering marvel stretching across vast landscapes, plays a pivotal role in the global agricultural sector. This conveyor belt system, specifically designed for the transportation of phosphate ore, is not just a testament to human ingenuity but also a crucial component in the production of agricultural fertilizers worldwide. Phosphate, a key element in fertilizers, is essential for the growth and health of crops, making the efficient and reliable transportation of phosphate ore from mines to processing plants and then to global markets, a matter of food security and agricultural productivity. The significance of the phosphate conveyor belt extends beyond its impressive length and engineering; it represents a lifeline for global agriculture, ensuring that essential nutrients reach farmlands across the globe, thus supporting the world’s food supply chain.
The Bou Craa Phenomenon: World’s Longest Phosphate Conveyor Belt
Spanning an astonishing 61 miles (approximately 98 kilometers) across the Sahara Desert, the Bou Craa phosphate conveyor belt in Morocco holds the title of the world’s longest conveyor belt system. This remarkable feat of engineering was designed to transport phosphate ore from the heart of the Sahara in Bou Craa to the coastal town of El Marsa, facilitating the global distribution of one of the most important components for agricultural fertilizers.The Bou Craa phosphate conveyor belt transports 2,000 tons of phosphate rock per hour over 100 kilometers in Western Sahara.
Engineering Ingenuity and Capacity
The construction of the Bou Craa conveyor belt system is a story of engineering triumph. Designed to endure the harsh desert conditions, the system comprises several interconnected belts that seamlessly transport the phosphate ore across the landscape. The capacity of this conveyor belt system to move thousands of tons of phosphate ore daily is a critical factor in its design, ensuring that the global demand for phosphate, essential for agricultural fertilizers, is met efficiently and reliably.
The Conveyor Belt’s Journey
The journey of phosphate ore on this conveyor belt is not just a marvel of distance but also of resilience. As the belt weaves its way through the desert, it battles extreme temperatures, shifting sands, and the abrasive nature of the phosphate rock itself. The system’s design accounts for these challenges, incorporating advanced materials and technologies to minimize wear and tear and ensure continuous operation.
The Bou Craa conveyor belt is more than just a transportation system; it is a vital artery in the body of global agriculture, enabling the flow of essential nutrients from the remote mines of Western Sahara to farms worldwide. Its construction not only showcases human ingenuity and engineering prowess but also highlights the importance of phosphate in sustaining global food production.
Visibility from Space
One of the most remarkable aspects of the Bou Craa conveyor belt is its visibility from space. Astronauts aboard the International Space Station have reported seeing the conveyor belt as a distinct line cutting across the desert landscape. This visibility is enhanced by the white dust from the phosphate ore, which stands out against the desert backdrop. The sight is a powerful reminder of humanity’s capacity to modify the environment on a grand scale, achieving feats of engineering that have a direct impact on life across the planet.

Secure high-quality conveyor belts – contact us for a free consultation
Phosphate Rock: A Cornerstone of Global Agriculture
Phosphate rock is not just another mineral extracted from the earth; it is a lifeline for global agriculture, providing the essential nutrient phosphorus that fuels plant growth, development, and reproduction. As the primary source of phosphorus, phosphate rock’s role in agricultural fertilizers cannot be overstated, making it a cornerstone of food production systems worldwide.
The Critical Role of Phosphorus in Agriculture
Phosphorus, one of the three primary nutrients in commercial fertilizers, alongside nitrogen and potassium, is crucial for the health and growth of plants. It plays a pivotal role in energy transfer, photosynthesis, transformation of sugars and starches, and nutrient movement within the plant. Without adequate phosphorus, plants exhibit stunted growth, leading to reduced crop yields and lower-quality produce.
Bou Craa: A Major Source of Phosphate
The Bou Craa mine in Western Sahara stands as one of the largest sources of phosphate rock in the world. Its significance extends beyond its size; it represents a major contributor to the global phosphate market, supplying the raw material that is eventually processed into fertilizers used across continents. The mine’s vast reserves ensure a steady supply of phosphate rock, crucial for meeting the growing global demand for food.
Extraction and Transportation Challenges
Extracting phosphate rock in the harsh desert environment of Bou Craa presents numerous challenges, from the extreme heat and sandstorms to the logistical difficulties of transporting the extracted ore. The solution—a sophisticated conveyor belt system stretching over 61 miles—epitomizes human ingenuity in overcoming natural obstacles to harness essential resources.
Global Impact of Phosphate Mining
The global impact of phosphate mining, particularly in regions like Bou Craa, extends far beyond agriculture. It influences geopolitical dynamics, with countries vying for access to this critical resource. Moreover, the environmental implications of phosphate mining, including water usage and the disruption of local ecosystems, are subjects of ongoing debate and research.
Sustainability and the Future of Phosphate Mining
As the world grapples with the dual challenges of increasing food production and preserving environmental integrity, the sustainability of phosphate mining comes into focus. Innovations in mining technology, more efficient fertilizer use, and the exploration of alternative sources of phosphorus are part of the discourse on ensuring the long-term viability of phosphate rock as a cornerstone of global agriculture.
Phosphate rock, with its indispensable role in global agriculture, stands as a testament to the interconnectedness of natural resources, technological innovation, and food security. It is important for phosphate conveyor belt. The Bou Craa phosphate mine, with its monumental conveyor belt system, not only highlights the lengths to which humanity will go to secure essential nutrients but also prompts a reflection on the sustainability of such endeavors in the face of environmental concerns and the imperative of feeding a growing global population.
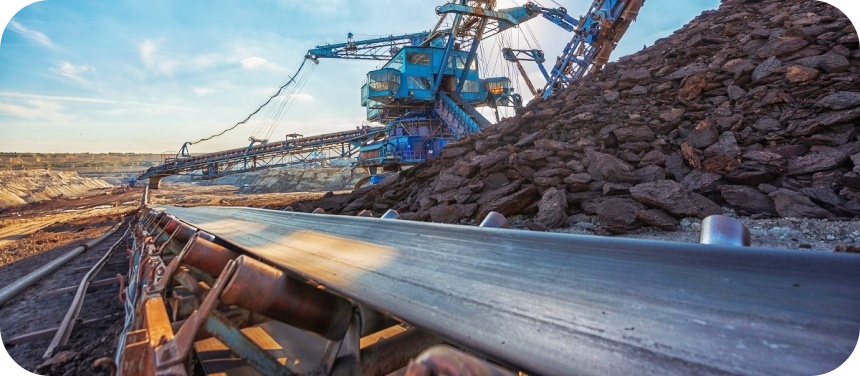
Types of Phosphate Conveyor Belts
Phosphate conveyor belts are used to transport phosphate materials in various stages of production and processing. There are several types of conveyor belts suitable for handling phosphate, each designed for specific needs and conditions. Here are some common types:
- Suitable for long-distance and high-tension applications.
- Offer high durability and resistance to impact and wear.
Fabric Conveyor Belts:
- Made from layers of fabric, often polyester or nylon, with rubber or PVC covers.
- Flexible and cost-effective for medium to short distance conveying.
- Feature a chevron pattern on the surface to prevent slipping.
- Ideal for inclined transport of bulk materials like phosphate.
Pipe Conveyor Belts:
- Enclosed belts that form a pipe-like shape during transport.
- Minimize spillage and environmental contamination, suitable for handling dusty materials like phosphate.
Heat-Resistant Conveyor Belts:
- Designed to withstand high temperatures.
- Suitable for transporting phosphate materials that are hot or processed at high temperatures.
Oil-Resistant Conveyor Belts:
- Resistant to oils and chemicals.
- Suitable for environments where phosphate materials might come into contact with oils or other chemicals.
Flame-Resistant Conveyor Belts:
- Made from flame-resistant materials.
- Essential for use in environments with fire hazards, ensuring safety during phosphate transport.
Ripstop Conveyor Belts:
- Reinforced with a special weave to prevent tearing and ripping.
- Ideal for transporting sharp or abrasive phosphate materials.
- Feature raised edges or sidewalls to contain materials.
- Suitable for steep inclines and vertical lifting of phosphate materials.
Modular Plastic Conveyor Belts:
- Made from interlocking plastic modules.
- Easy to clean and maintain, suitable for certain phosphate processing applications.
Each type of phosphate conveyor belt is designed to meet specific requirements of the industry, ensuring efficient and safe transportation of materials.

How to Select Phosphate Conveyor Belts
Selecting the right phosphate conveyor belt involves considering various factors to ensure optimal performance, durability, and efficiency. Here are some key considerations to guide your selection process:
Material Characteristics:
- Abrasiveness: Phosphate can be abrasive, so choose belts with high wear resistance.
- Moisture Content: Consider belts that can handle wet or dry phosphate to avoid slippage or clogging.
- Temperature: Select heat-resistant belts if the material is hot or processed at high temperatures.
Conveyor Length and Incline:
- Distance: For long-distance transport, steel cord belts might be more suitable due to their strength and durability.
- Incline Angle: Chevron or sidewall belts are ideal for inclined conveying to prevent material rollback.
Load and Speed:
- Load Capacity: Ensure the belt can handle the maximum load without excessive stretching or wear.
- Speed: Match the belt’s speed capabilities with your conveyor system to maintain efficiency and prevent damage.
Environmental Conditions:
- Temperature: Use heat-resistant belts in high-temperature environments.
- Chemical Exposure: Oil-resistant or chemical-resistant belts are necessary if the phosphate is exposed to chemicals.
- Flame Resistance: Consider flame-resistant belts for environments with fire hazards.
Maintenance and Durability:
- Durability: Choose belts with high tensile strength and resistance to tearing and puncturing.
- Maintenance: Opt for belts that are easy to maintain and clean, such as modular plastic belts if appropriate.
Cost and Efficiency:
- Budget: Balance the initial cost with the expected lifespan and maintenance costs of the belt.
- Energy Efficiency: Consider belts that reduce energy consumption by optimizing friction and load distribution.
Regulatory Compliance:
- Safety Standards: Ensure the belt meets industry safety standards and regulations for handling phosphate.
- Environmental Regulations: Choose belts that comply with environmental regulations, especially if the phosphate handling process involves dust or spillage control.
Specific Application Requirements:
- Pipe Conveyor Belts: Use these for enclosed transportation to prevent spillage and contamination.
- Ripstop Conveyor Belts: Ideal for handling sharp or coarse phosphate materials to prevent tearing.
Supplier Expertise and Support:
- Reputation: Choose a reputable supplier with experience in manufacturing and supplying conveyor belts for phosphate handling.
- Technical Support: Ensure the supplier provides adequate technical support and after-sales service.
Steps to Select the Right Phosphate Conveyor Belt
- Assess Material Properties: Analyze the properties of the phosphate material to determine the required belt specifications.
- Evaluate Conveyor Design: Consider the design and layout of your conveyor system, including length, incline, and load capacity.
- Consult with Suppliers: Discuss your specific needs with conveyor belt suppliers to get recommendations and technical advice.
- Compare Options: Compare different types of belts based on their features, performance, and cost.
- Test Samples: If possible, test sample belts in your operating environment to evaluate their performance and suitability.
- Make an Informed Decision: Choose the belt that best meets your operational requirements, budget, and long-term performance goals.
Selecting the right phosphate conveyor belt involves a comprehensive evaluation of your specific needs and conditions to ensure efficient and reliable material handling.
The Phosphate Conveyor Belt’s Capacity and Global Impact
The phosphate conveyor belt, stretching from the Bou Craa phosphate mine to the coastal town of El Marsa, is not just an engineering marvel; it’s a critical artery in the body of global agriculture. Its capacity to transport massive quantities of phosphate ore is a testament to human ingenuity and a pivotal factor in the global food supply chain.
Unparalleled Capacity
The conveyor belt’s design allows for the continuous, efficient transport of phosphate ore across the Sahara Desert, covering a distance of over 61 miles. This system can move thousands of tons of phosphate ore daily, directly impacting global phosphate availability. The sheer volume of material transported is crucial for meeting the high demand for phosphate-based fertilizers essential for crop production worldwide.
Impact on Global Food Production
Phosphate fertilizers, derived from the ore transported by this conveyor belt, play a vital role in enhancing soil fertility, increasing crop yields, and improving food quality. By providing a steady supply of phosphate, the conveyor belt system supports the agricultural sectors of numerous countries, thereby contributing to global food security. In regions where soil nutrient depletion poses a significant challenge to food production, the impact of these fertilizers is particularly pronounced.
Technological Ingenuity and Sustainability
The conveyor belt system exemplifies technological ingenuity, showcasing how engineering solutions can overcome geographical and environmental barriers. However, this innovation also prompts a discussion on sustainability. The global dependency on a single source of phosphate raises questions about the long-term viability of current agricultural practices and the need for sustainable mining and fertilizer use.
Environmental Considerations
While the conveyor belt system is a feat of engineering, it also highlights the environmental challenges associated with large-scale mining operations. The extraction and transportation of phosphate ore have ecological impacts, including habitat disruption and resource depletion. Balancing the need for phosphate with environmental conservation is an ongoing challenge, necessitating advancements in mining practices and conveyor technology.
The Future of Phosphate Transportation
Looking ahead, the future of phosphate transportation may involve innovations aimed at increasing efficiency, reducing environmental impact, and diversifying sources of phosphate. Developments in conveyor belt technology, such as energy-efficient motors or materials that minimize dust generation, could further enhance the sustainability of these essential systems.
The global impact of the phosphate conveyor belt system extends far beyond its impressive capacity and engineering. It underscores the critical role of phosphate in agriculture, the challenges of sustainable resource management, and the potential for technological innovation to address these issues. As the world seeks to balance food production needs with environmental stewardship, the conveyor belt system stands as a symbol of both the possibilities and the challenges that lie ahead.

Phosphate Conveyor Belt: Geopolitical and Environmental Dimensions
The phosphate conveyor belt in Western Sahara is not only an industrial marvel but also a focal point of geopolitical tensions and environmental concerns. Its operation within a region rich in phosphate resources underscores the complex interplay between resource extraction, territorial disputes, and sustainable development.
Geopolitical Significance of Phosphate Reserves
Western Sahara’s phosphate reserves, among the largest globally, are at the heart of geopolitical interests and conflicts. The region’s phosphate wealth has made it a subject of contention, with Morocco controlling the majority of the territory and its resources. This control extends to the Bou Craa mine and the world’s longest conveyor belt, which are pivotal for Morocco’s phosphate exportation to the global market. The geopolitical dynamics surrounding these reserves highlight the critical nature of phosphate as a resource, essential for global agriculture but also a point of leverage and dispute on the international stage.
Environmental Impact of the Conveyor Belt System
The environmental implications of operating the world’s longest conveyor belt in a desert landscape are significant. While the system efficiently transports phosphate ore, it also raises concerns about habitat disruption, dust pollution, and the broader ecological footprint of large-scale mining operations. The visible trail of phosphate dust, while a testament to the conveyor belt’s operation, also serves as a reminder of the environmental costs associated with extracting and transporting natural resources.
Sustainable Mining and Conveyor Operations
Amid growing awareness of environmental sustainability and resource conservation, the phosphate mining industry faces pressure to adopt more sustainable practices. This includes the conveyor belt operation, where improvements in energy efficiency, dust control measures, and habitat restoration efforts are increasingly important. Balancing the economic benefits of phosphate extraction with the need to protect and preserve the environment is a critical challenge, requiring innovative solutions and international cooperation.
The Role of International Regulations and Agreements
The operation of the phosphate conveyor belt and the exploitation of Western Sahara’s phosphate reserves are subject to international regulations and agreements. These aim to ensure that resource extraction benefits local populations and does not exacerbate environmental degradation. Compliance with international environmental standards and engagement in fair trade practices are essential for the sustainable and ethical operation of the conveyor belt system.
The phosphate conveyor belt system, while a symbol of industrial achievement, sits at the nexus of geopolitical interests and environmental stewardship. Its operation in Western Sahara highlights the challenges of managing valuable natural resources in contested territories, emphasizing the need for sustainable practices that reconcile economic objectives with ecological and social responsibilities. As the demand for phosphate continues to grow, the conveyor belt’s future will likely reflect broader trends in global resource management, sustainability, and international diplomacy.
Optimize your operations with our conveyor belts. Reach out now.
Comparing Giants: The Bou Craa Conveyor Belt in a Global Context
The Bou Craa phosphate conveyor belt, renowned for its extraordinary length and capacity, is a marvel of modern engineering. When placed in a global context alongside other significant conveyor systems, its unique characteristics and the challenges it addresses become even more pronounced.
Global Comparison of Conveyor Systems
- United States: The United States boasts several extensive conveyor systems, particularly in mining operations. For instance, the Long Belt Conveyor System in the coal mines of Wyoming is one of the longest overland conveyor systems in the country. Comparing it with Bou Craa’s system highlights differences in terrain, climate challenges, and the materials transported.
- Africa: Apart from Bou Craa, Africa is home to other significant conveyor belt systems, especially in the mining sector. The comparison sheds light on how geographical and economic factors influence the design and operation of these systems across the continent.
- Asia: Asia’s rapid industrialization has seen the rise of extensive conveyor systems, especially in mining and manufacturing. Comparing these systems with Bou Craa’s offers insights into technological innovations and efficiency improvements in conveyor belt design and operation.
Unique Aspects of the Bou Craa Conveyor Belt
- Length and Visibility: The Bou Craa conveyor belt’s length is unmatched, making it visible even from space. This aspect not only showcases its scale but also the extent of human ingenuity in overcoming logistical challenges.
- Environmental Adaptation: Operating in the Sahara Desert, the Bou Craa conveyor belt is designed to withstand extreme weather conditions, showcasing adaptability in harsh environments unlike any other system.
- Economic and Social Impact: The conveyor belt’s role in transporting phosphate ore—a key ingredient in agricultural fertilizers—underscores its significance in supporting global food production, a critical aspect that sets it apart from other conveyor systems primarily focused on other industrial materials.
Technological Innovations and Sustainability
- Advancements in Conveyor Technology: The Bou Craa system’s operation has spurred innovations in conveyor belt technology, including durability, energy efficiency, and environmental protection measures. Comparing these advancements with those in other systems highlights the ongoing evolution of conveyor technology.
- Sustainability Practices: The environmental impact of such a large-scale operation in a delicate ecosystem prompts a discussion on sustainable practices in conveyor system operations worldwide. The Bou Craa system serves as a case study in balancing industrial needs with environmental conservation.
The Bou Craa phosphate conveyor belt stands as a testament to human ingenuity, significantly impacting both the local economy and global agriculture. When compared to other major conveyor systems around the world, it highlights the diverse challenges and solutions inherent in designing and operating these industrial lifelines. The future of such systems lies in the balance between technological advancement and sustainable practices, ensuring that they continue to serve as vital components of the global economy while minimizing their environmental footprint.

Maintenance of Phosphate Conveyor Belt
Maintaining a phosphate conveyor belt is crucial to ensure its longevity, performance, and safety. Regular maintenance helps prevent unexpected breakdowns, reduce downtime, and extend the life of the conveyor belt. Here are key maintenance practices:
Routine Inspection and Monitoring
Regular Visual Inspections:
- Check for any visible signs of wear, damage, or misalignment.
- Inspect the belt surface for cracks, cuts, or abrasions.
- Look for signs of material buildup or spillage.
Monitor Belt Tracking:
- Ensure the belt is running straight and centered on the conveyor.
- Adjust tracking devices to correct any misalignment.
Check Tension and Alignment:
- Verify the belt tension is within the recommended range.
- Adjust the tension to prevent slippage or excessive strain.
- Ensure all pulleys and rollers are properly aligned.
Cleaning and Lubrication
Regular Cleaning:
- Remove any accumulated material, debris, or buildup from the belt and conveyor components.
- Use appropriate cleaning agents and tools to prevent damage to the belt surface.
Lubricate Moving Parts:
- Apply lubrication to bearings, rollers, and other moving parts to reduce friction and wear.
- Use lubricants that are compatible with the conveyor components and the material being handled.
Component Maintenance and Replacement
Inspect and Replace Rollers and Pulleys:
- Check for worn or damaged rollers and pulleys.
- Replace any components that show signs of wear to ensure smooth operation.
Examine Splices and Joints:
- Inspect belt splices and joints for any signs of weakness or separation.
- Repair or replace splices as needed to maintain belt integrity.
Check Conveyor Structure:
- Inspect the conveyor frame, supports, and guards for any signs of damage or wear.
- Ensure all structural components are secure and in good condition.
Preventive Measures
Install Belt Scrapers and Cleaners:
- Use belt scrapers and cleaners to remove material from the belt surface and prevent buildup.
- Regularly inspect and adjust these devices for optimal performance.
Implement Dust Control Measures:
- Use dust control systems to minimize airborne particles and reduce material loss.
- Regularly clean and maintain dust control equipment.
Safety and Training
Conduct Safety Inspections:
- Perform regular safety inspections to identify and address potential hazards.
- Ensure all safety guards and devices are in place and functioning correctly.
Train Personnel:
- Train maintenance personnel on proper inspection, cleaning, and lubrication techniques.
- Ensure all workers understand the importance of regular maintenance and follow safety protocols.
Documentation and Scheduling
Maintain Records:
- Keep detailed records of all maintenance activities, inspections, and repairs.
- Use these records to identify trends and schedule preventive maintenance.
Schedule Regular Maintenance:
- Establish a maintenance schedule based on the conveyor’s usage and operating conditions.
- Perform maintenance tasks at regular intervals to prevent unexpected breakdowns.
Troubleshooting Common Issues
Address Belt Slippage:
- Check and adjust belt tension.
- Inspect pulleys for wear or misalignment.
Resolve Tracking Problems:
- Adjust tracking devices and ensure the belt is properly aligned.
- Check for any obstructions or buildup causing misalignment.
Fix Material Buildup:
- Clean the belt and conveyor components regularly.
- Install and maintain belt scrapers and cleaners.
By implementing these maintenance practices, you can ensure the efficient and reliable operation of your phosphate conveyor belt, minimizing downtime and extending its service life.
FAQs about Phosphate Conveyor Belt
Conveyor belts are made from a variety of materials, each selected based on the specific demands of the application. Common materials include:
Rubber: Widely used for general purpose applications; it’s flexible and durable.
PVC (Polyvinyl Chloride): Suitable for light to medium applications, where durability and resistance to chemicals are required.
PU (Polyurethane): Used in food processing industries due to its resistance to fats, oils, and chemicals, and for its ease of cleaning.
Metal: Provides high strength and durability, often used in heavy-duty applications such as mining.
Fabric: Materials like nylon, polyester, and cotton are used for various applications, offering flexibility and cost-effectiveness.
Thermoplastics: Including Teflon, for high heat applications, and others for their lightweight and corrosion resistance.
The world’s longest conveyor belt is the Western Sahara Conveyor Belt System. It extends over 98 kilometers (61 miles) from the phosphate mines of Bu Craa to the coast south of El-Aaiun in the Western Sahara. This system transports phosphate ore from the mines to the port for export, and it’s considered the longest belt conveyor system in the world.
The composition of a conveyor belt can vary significantly based on its intended use, but common ingredients include:
Rubber compounds: For elasticity and durability.
Fabric layers: Such as nylon, polyester, or cotton for strength and flexibility.
Steel cords: For high tensile strength in heavy-duty belts.
PVC or PU coatings: For chemical resistance and hygiene in food processing applications.
Carbon black: Added to rubber belts for UV protection and strength.
Plasticizers: To make the rubber more flexible.
Antioxidants and antiozonants: To prevent degradation by oxygen and ozone.
The phosphate from Western Sahara is a major resource extracted in the region, primarily from the mines in Bu Craa. Western Sahara’s phosphate is considered among the highest quality worldwide, used globally for fertilizer production. The extraction and export of phosphate from Western Sahara are subjects of international legal and ethical debates, due to the disputed status of the territory. The region’s phosphate industry is a significant part of the local economy but is also at the center of political tensions between Morocco (which controls the area) and the Sahrawi people’s representatives seeking independence.
Conveyor belts are typically powered by electric motors, which drive the belt through a system of pulleys and rollers. These motors can vary in size and power, depending on the length and load capacity of the conveyor system. The electricity used to power these motors is often sourced from the facility’s main power supply. In some cases, especially in remote or off-grid locations, alternative power sources such as diesel generators, solar panels, or other renewable energy sources might be used. Additionally, hydraulic or pneumatic systems can also be employed to power conveyor belts, particularly in specialized industrial applications where electrical power is impractical. The choice of power source depends on the specific requirements and constraints of the conveyor system’s operational environment.
Last Updated on July 15, 2024 by Jordan Smith
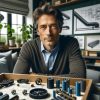
Jordan Smith, a seasoned professional with over 20 years of experience in the conveyor system industry. Jordan’s expertise lies in providing comprehensive solutions for conveyor rollers, belts, and accessories, catering to a wide range of industrial needs. From initial design and configuration to installation and meticulous troubleshooting, Jordan is adept at handling all aspects of conveyor system management. Whether you’re looking to upgrade your production line with efficient conveyor belts, require custom conveyor rollers for specific operations, or need expert advice on selecting the right conveyor accessories for your facility, Jordan is your reliable consultant. For any inquiries or assistance with conveyor system optimization, Jordan is available to share his wealth of knowledge and experience. Feel free to reach out at any time for professional guidance on all matters related to conveyor rollers, belts, and accessories.