Optimizing Industrial Efficiency with Pipe Conveyor Rollers
Pipe conveyor rollers are pivotal components of the pipe conveyor systems widely utilized across various industrial sectors for the transportation of materials. These systems are especially significant in industries where the secure and efficient movement of bulk materials is critical. The unique design of pipe conveyor rollers allows the belt to form a pipe shape, enclosing the materials and offering protection against spillage, contamination, and environmental factors. This feature is particularly beneficial in sensitive environments or when handling hazardous materials. The efficiency and durability of a pipe conveyor system heavily rely on the quality and performance of its rollers. These rollers not only support and drive the belt but also play a crucial role in maintaining the integrity of the belt’s pipe shape throughout the conveying process. High-quality pipe conveyor rollers contribute to reduced maintenance costs, increased system lifespan, and improved operational efficiency, making them a key focus area for industries aiming to optimize their material handling operations.
Types of Pipe Conveyor Rollers
Used Pipe Conveyor Rollers
When considering used pipe conveyor rollers, several factors must be evaluated to ensure they meet your system’s requirements. Firstly, inspect the rollers for signs of wear and tear, such as surface damage or deformation, which can affect performance. Secondly, compatibility with your existing conveyor system is crucial to avoid operational issues. Thirdly, examine the bearing condition, as bearings are critical for smooth operation. Fourth, assess the roller’s material and surface coating for suitability with the materials being conveyed. Lastly, inquire about the previous application environment to gauge potential longevity and reliability. These considerations help ensure that used pipe roller conveyor will efficiently integrate into and support your material handling processes.
Pipe Conveyor Rollers for Sale
Finding the best new pipe conveyor rollers for sale involves identifying suppliers that specialize in conveyor components. Key considerations include supplier reputation, quality certifications, product range, and after-sales support. First, look for suppliers with ISO certifications, indicating adherence to quality standards. Second, evaluate the range of roller types offered, ensuring they meet your specific application needs. Third, consider suppliers offering custom solutions for unique system requirements. Fourth, assess the warranty and maintenance support to safeguard your investment. Lastly, seek suppliers with positive industry reviews and testimonials, as these indicate reliability and customer satisfaction. Choosing the right supplier is essential for acquiring high-quality pipe conveyor rollers that enhance your system’s efficiency and longevity.
Best Pipe Conveyor Rollers
The best pipe conveyor rollers are characterized by several key features. Durability is paramount, with materials such as hardened steel or reinforced plastics ensuring long service life. Load capacity is also critical; the rollers must support the weight of both the materials being conveyed and the conveyor belt itself without deformation. Compatibility with various materials, whether abrasive, corrosive, or sensitive, dictates the roller’s surface material and design. Maintenance requirements are another consideration, with sealed bearings and low-wear surfaces reducing downtime. Finally, the roller’s design, whether trough-shaped or flat, should match the specific needs of the pipe conveyor system, enhancing efficiency and reducing spillage. These characteristics ensure the rollers contribute positively to the conveyor system’s overall performance.
Homemade Pipe Conveyor Rollers
For those looking to craft homemade pipe roller conveyor, a DIY approach can be both rewarding and economical. Begin with selecting a durable tube material, such as steel or PVC, that matches the diameter requirements of your system. Bearings are crucial; choose sealed units to minimize maintenance. For the shaft, a robust material like stainless steel ensures strength and durability. Assembling the rollers might require welding or mechanical fasteners, depending on the materials used. Finally, applying a surface treatment, such as rubber coating, can improve traction and material handling. By following these steps and carefully sourcing materials, creating custom pipe conveyor rollers tailored to specific system needs is achievable, offering a personalized solution to material handling challenges.
Material and Design Considerations for Pipe Conveyor Rollers
When selecting pipe conveyor rollers, material and design are two pivotal factors that influence the system’s efficiency, durability, and applicability to various industrial needs. These considerations dictate how well the rollers will perform in different environments and with diverse materials.
Benefits of Coated Pipe Conveyor Rollers
Coated pipe conveyor rollers, whether with rubber, polyurethane, or specialized coatings, offer enhanced performance characteristics for specific applications. These coatings can improve grip, reduce material adhesion, and protect the roller from environmental factors, extending the roller’s lifespan. For instance, coated rollers are crucial in food processing for hygiene, in chemical industries for resistance to corrosive substances, and in packaging industries where gentle handling of materials is necessary.
The Importance of Metric Pipe Conveyor Rollers for International Operations
For businesses operating on a global scale, the integration of metric pipe conveyor rollers is crucial for several reasons:
- Standardization: Metric rollers adhere to international standards, facilitating easier integration and replacement parts procurement in operations across different countries.
- Compatibility: Ensures compatibility with machinery and conveyance systems designed in metric specifications, reducing engineering conversion errors.
- Supply Chain Efficiency: Streamlines the supply chain, as metric components are widely available, simplifying logistics and inventory management.
- Regulatory Compliance: Meets global regulatory requirements, especially in regions where metric is the standard, avoiding legal and operational complications.
- Global Market Accessibility: Enhances the ability to operate and compete in international markets, where metric system adoption simplifies collaboration and trade.
These material and design considerations is vital when selecting pipe conveyor rollers. It allows for the customization of the conveyor system to meet specific operational needs, environmental conditions, and international standards, thereby optimizing the performance and efficiency of material handling processes.
Key Components of Pipe Conveyor Rollers
The efficiency and longevity of pipe conveyor systems significantly depend on the quality and design of their rollers. Understanding the key components of pipe conveyor rollers is essential for selecting the right rollers for your system and ensuring its optimal performance. Here, we break down the essential parts, including bearings, shafts, and coatings, and provide insight into common technical jargon associated with conveyor roller parts.
Bearings
Bearings are crucial for the smooth operation of pipe conveyor rollers. They allow the roller to rotate with minimal friction, facilitating efficient material transport. There are two main types of bearings used in conveyor rollers: precision ball bearings, ideal for high-speed applications and capable of handling both radial and axial loads, and roller bearings, suited for heavier loads with slower speeds. The choice of bearing type affects the roller’s durability and maintenance requirements.
Shafts
The shaft is the core component that connects the roller to the conveyor frame, ensuring the roller’s proper alignment and stability. Typically made from steel or stainless steel for strength and durability, shafts must be precisely manufactured to fit securely within the roller and the conveyor framework. The diameter and length of the shaft are critical dimensions that are determined by the load requirements and the width of the conveyor system.
Coatings
Coatings on conveyor pipe rollers serve multiple purposes: they protect the roller from environmental damage, reduce wear and tear, and can even influence the movement of materials along the conveyor. Rubber and polyurethane are common coating materials, offering enhanced grip and resistance to abrasion. Specialty coatings may also be applied for specific applications, such as Teflon for heat resistance or zinc plating for corrosion protection.
Demystifying Technical Jargon
Understanding the names and functions of conveyor roller parts is vital for effective communication with suppliers and maintenance teams. Here are a few key terms:
- Shell: The outer tube of the roller, where the material is in direct contact. It can be made of metal, plastic, or coated with various materials for different applications.
- End Cap: Also known as the sealing system, end caps are located at both ends of the roller to protect the bearings from dust, debris, and other contaminants.
- Casing: Refers to the housing or frame that encloses the bearing and shaft, providing structural support to the roller.
- Spacer: A component used inside the roller to maintain the correct distance between bearings and ensure proper alignment.
These key components and terms associated with pipe conveyor rollers is fundamental in ensuring the selection of appropriate parts for your conveyor system, ultimately leading to enhanced operational efficiency and longevity of the conveyor system.
Advanced Features in Pipe Conveyor Rollers
The evolution of pipe conveyor systems has led to the integration of advanced features in pipe conveyor rollers, enhancing automation, efficiency, and overall system performance. Innovations such as live roller conveyor parts and the synergistic use of roller conveyor belts with pipe rollers are at the forefront of this development, offering significant benefits to industries reliant on material handling systems.
Live Roller Conveyor Parts
Live roller conveyor parts represent a leap forward in the automation of pipe conveyor systems. These components are designed to be powered, either individually or through a centralized system, allowing for precise control over the movement of materials. This capability is particularly advantageous in applications requiring variable speeds, accumulation, or sorting of materials. The integration of sensors and control systems with these live rollers enables real-time monitoring and adjustments, significantly reducing manual intervention and enhancing operational efficiency. For pipe conveyor rollers, this means smoother transitions, improved handling of delicate materials, and increased throughput.
Roller Conveyor Belts and Pipe Rollers
The combination of roller conveyor belts with pipe rollers brings forth a hybrid solution that leverages the advantages of both systems for increased performance. This approach enhances the pipe conveyor system’s flexibility, allowing it to handle a wider range of materials and shapes without compromising on the protection and spillage control offered by the enclosed pipe design. The use of roller conveyor belts in conjunction with pipe rollers can also distribute the load more evenly across the belt, reducing wear and extending the life of both the belt and rollers. Furthermore, this setup can improve energy efficiency by minimizing the friction and resistance encountered during material transport, leading to lower operational costs.
These advanced features in pipe conveyor rollers are indicative of the ongoing innovation within the field of material handling. By adopting these technologies, businesses can achieve not only greater efficiency and productivity but also enhanced sustainability through reduced energy consumption and longer-lasting equipment. The focus on automation and performance optimization underscores the industry’s commitment to meeting the evolving demands of global supply chains and manufacturing processes.
Maintenance and Care for Pipe Conveyor Rollers
Effective maintenance and care for pipe conveyor rollers are crucial for ensuring the longevity and efficient operation of conveyor systems. Regular upkeep not only extends the lifespan of the rollers but also prevents costly downtime and repairs. Here are five essential maintenance tips that can help keep your conveyor pipe rollers in top condition:
Regular Cleaning
- Dust and Debris Removal: Regularly clean pipe conveyor rollers to remove dust, dirt, and debris that can accumulate and impair the rollers’ functionality. Use compressed air or a soft brush for cleaning the outer surfaces and ensure that the areas around the bearings are free from particles that could cause wear.
Lubrication
- Bearing Lubrication: Proper lubrication of the bearings in pipe conveyor rollers is essential to reduce friction and wear. Use a suitable grease or oil according to the manufacturer’s recommendations. Regularly check the lubrication levels and replenish as needed to ensure smooth roller operation.
Inspection
- Routine Inspections: Conduct routine inspections of pipe conveyor rollers to identify wear and tear, misalignment, or any other issues that could escalate into more significant problems. Look for signs of uneven wear patterns on the rollers, cracks, or any deformation on the shell.
Replacement
- Timely Replacement of Worn Parts: Replace worn or damaged parts promptly to maintain the efficiency of the conveyor system. This includes swapping out worn bearings, shafts, or the roller shells themselves if they show signs of significant wear or damage.
Environmental Considerations
- Environmental Protection: Protect pipe conveyor rollers from harsh environmental conditions by implementing shields or covers if they are exposed to extreme temperatures, moisture, or corrosive substances. This protection helps prevent premature wear and prolongs the life of the rollers.
Adhering to these maintenance and care practices for pipe conveyor rollers ensures that the conveyor system operates smoothly, reduces the likelihood of unexpected breakdowns, and maintains optimal performance over an extended period. Regular and proactive maintenance is key to maximizing the efficiency and longevity of pipe conveyor rollers within any material handling system.
Choosing the Right Pipe Conveyor Rollers
Selecting the right pipe conveyor rollers is essential for optimizing the efficiency and longevity of your conveyor system. The choice of rollers should be informed by a thorough understanding of your application needs, budget constraints, and specific material handling requirements. Here are key considerations to guide you in choosing the most suitable pipe conveyor rollers:
Assessing Application Needs
- Material Characteristics: Understand the properties of the materials you are handling. Heavy, abrasive, or corrosive materials require rollers with robust construction and possibly specialized coatings to resist wear and corrosion.
- Conveyor Environment: Consider the operating environment of the conveyor. For environments with high humidity, temperature extremes, or exposure to chemicals, choose rollers designed to withstand these conditions.
- Load Requirements: Evaluate the weight and volume of materials the conveyor will carry. This will help determine the necessary load capacity of the rollers, which is critical to prevent overloading and ensure longevity.
Balancing Budget Constraints
- Initial Cost vs. Longevity: While it might be tempting to opt for the least expensive option, consider the long-term costs associated with replacement and maintenance. Investing in higher-quality rollers can reduce overall costs over the conveyor’s lifecycle.
- Maintenance Costs: Consider the ease of maintenance and the cost of potential downtime. Rollers that are easier to maintain and less prone to failure might cost more initially but save money in reduced downtime and maintenance over time.
Meeting Material Handling Requirements
- Speed and Efficiency: Choose rollers that can handle the speed requirements of your conveyor system without compromising efficiency. Rollers designed for high-speed operations can enhance throughput and productivity.
- Compatibility with Existing Systems: Ensure that the rollers are compatible with your existing conveyor setup. This includes checking the roller dimensions, mountings, and the type of bearing housings.
- Customization Options: Sometimes, standard rollers might not meet all your needs. Look for suppliers who offer customization options that can tailor rollers to your specific requirements, such as non-standard sizes, special bearing configurations, or unique coating materials.
Consultation with Experts
- Seek Expert Advice: Consulting with manufacturers or experts in conveyor systems can provide insights into the latest technologies and materials used in pipe conveyor rollers. This guidance can be invaluable in making an informed decision.
- Testing and Trials: If possible, conduct trials with different types of rollers to see which best suits your operational needs. This practical testing can reveal performance characteristics that are not apparent from product descriptions alone.
By carefully considering these factors, you can choose the right pipe conveyor rollers that best fit your needs, enhancing the operational efficiency, safety, and cost-effectiveness of your material handling system.
FAQs About Pipe Conveyor Rollers
Rollers used in conveyors are critical components designed to facilitate the smooth and efficient transport of materials across different distances and configurations. These rollers vary widely in design, material, and size, depending on their specific application requirements. Common types include steel rollers, which are highly durable and suitable for heavy loads; plastic rollers, favored for their lighter weight and corrosion resistance; and rubber-coated rollers, which provide additional grip and noise reduction. Specialty rollers, such as impact rollers and return rollers, are also used in specific sections of conveyor systems to absorb shock and support the belt as it cycles back to the beginning.
A roller conveyor is a type of conveyor system that utilizes a series of rollers mounted within a frame to transport materials across a horizontal or slightly inclined path. Roller conveyors are particularly versatile and can handle a wide range of products, from small boxes to large pallets. They can be powered by motors and belts, or they can be gravity-operated, where the items are moved by manual push or by the force of gravity on a decline. Roller conveyors are favored in manufacturing and distribution facilities for their efficiency and the ease with which they can be integrated into complex logistical sequences.
A pipe conveyor is a specialized type of belt conveyor that encloses materials completely in a tubular belt, thus preventing spillage, reducing contamination risks, and minimizing environmental impact. This type of conveyor is particularly useful for handling materials that are sensitive, hazardous, or prone to spillage, such as chemicals, mined materials, and grains. Pipe conveyors are highly advantageous in crowded or environmentally sensitive areas where keeping materials contained is critical. They can navigate tight turns and elevation changes, which allows for more flexible route planning compared to traditional conveyor systems.
The distance between rollers in a conveyor, often referred to as the roller pitch, is a critical factor in designing a conveyor system. This distance can vary widely based on the type of materials being transported, their weight, and the desired speed of the conveyor. A typical roller pitch may range from 3 inches (about 7.6 cm) to 5 feet (about 1.5 meters), with smaller, lighter items requiring closer spacing to prevent them from sagging or stalling between rollers. Correctly spacing the rollers ensures that the conveyor operates smoothly, supports the load adequately, and extends the lifespan of both the conveyor belt and the rollers themselves.
Last Updated on May 17, 2024 by Jordan Smith
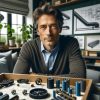
Jordan Smith, a seasoned professional with over 20 years of experience in the conveyor system industry. Jordan’s expertise lies in providing comprehensive solutions for conveyor rollers, belts, and accessories, catering to a wide range of industrial needs. From initial design and configuration to installation and meticulous troubleshooting, Jordan is adept at handling all aspects of conveyor system management. Whether you’re looking to upgrade your production line with efficient conveyor belts, require custom conveyor rollers for specific operations, or need expert advice on selecting the right conveyor accessories for your facility, Jordan is your reliable consultant. For any inquiries or assistance with conveyor system optimization, Jordan is available to share his wealth of knowledge and experience. Feel free to reach out at any time for professional guidance on all matters related to conveyor rollers, belts, and accessories.