Maximizing Productivity with Plastic Conveyor Roller Suppliers
In the dynamic world of material handling and logistics, plastic conveyor rollers stand out as essential components across various industries, from food processing to pharmaceuticals and beyond. These rollers, known for their durability, lightweight nature, and corrosion resistance, play a pivotal role in the efficient operation of conveyor systems. This article shines a spotlight on plastic conveyor roller suppliers, a crucial link in the supply chain that ensures businesses have access to rollers that meet their specific needs. Whether it’s sourcing used rollers for cost-effective solutions, heavy-duty options for industrial applications, or specialized rollers designed for unique operational requirements, plastic conveyor roller suppliers offer a range of products to keep conveyor systems running smoothly. Their expertise and extensive product range make them invaluable partners in enhancing operational efficiency and productivity.
The Role of Plastic Conveyor Roller
Plastic conveyor rollers, supplied by specialized plastic conveyor roller suppliers, play a critical role in the seamless operation of material handling and logistics systems across various sectors. These rollers are pivotal in facilitating the smooth and efficient transport of goods along conveyor systems, minimizing manual handling and optimizing workflow. The advantages of opting for plastic rollers over their metal counterparts are numerous and significant, impacting both operational efficiency and the working environment.
- Corrosion Resistance: Plastic conveyor rollers are inherently resistant to corrosion, making them ideal for use in environments where moisture or corrosive substances are present. This is particularly beneficial in industries such as food processing or chemical manufacturing, where exposure to aggressive cleaning agents or corrosive materials is common.
- Noise Reduction: Operations within enclosed spaces or in industries where noise pollution is a concern, such as packaging or distribution centers, greatly benefit from the reduced operational noise offered by plastic rollers. The material’s natural dampening properties contribute to a quieter working environment, enhancing worker comfort and compliance with noise regulations.
- Lightweight Properties: The reduced weight of plastic rollers, compared to metal rollers, facilitates easier installation and handling, leading to lower labor costs and faster setup times. This lightweight nature also means reduced wear on conveyor systems and potentially lower energy consumption during operation.
- Cost-Effectiveness: Plastic conveyor roller suppliers often highlight the cost benefits of their products. Not only are plastic rollers generally less expensive to manufacture than metal rollers, but their durability and low maintenance requirements also contribute to a lower total cost of ownership over the lifespan of the conveyor system.
- Versatility and Customization: Suppliers of plastic conveyor rollers offer a wide range of customization options to meet specific operational needs. This includes varying roller sizes, colors for visual sorting and safety, and the incorporation of specialized bearings or coatings to enhance performance in unique environments.
By leveraging the expertise of plastic conveyor roller suppliers, businesses can access tailored solutions that enhance the efficiency, safety, and cost-effectiveness of their material handling operations. The shift towards plastic rollers reflects a broader trend in industry preferences for components that offer durability, operational efficiency, and environmental resilience.
Types of Plastic Conveyor Roller Suppliers
The diversity in the types of plastic conveyor rollers available on the market is a testament to the innovation and adaptability of plastic conveyor roller suppliers. These suppliers offer a range of rollers designed to meet the varied demands of industries, ensuring that there is a solution for virtually every application. From heavy-duty rollers capable of withstanding substantial loads to miniature rollers designed for compact systems, the variety is extensive.
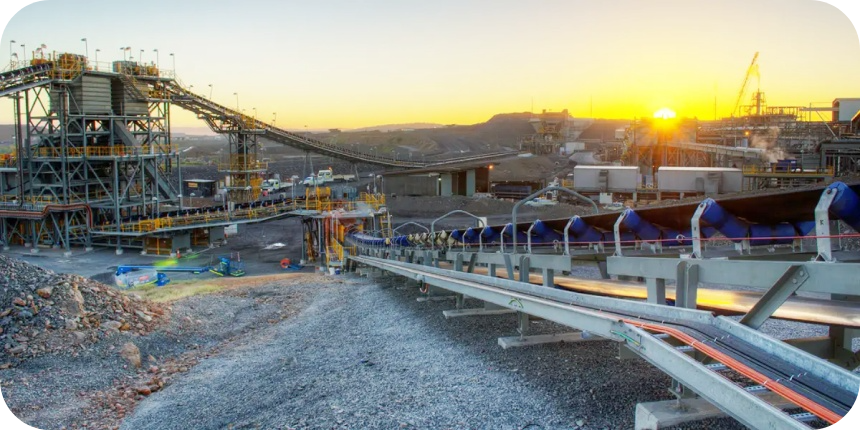
Heavy-Duty Rollers for Industrial Applications
- High-Impact Rollers: Designed for environments where the conveyor system is subject to heavy loads and high impact. These rollers are made from materials such as reinforced polyamide for extra durability.
- Abrasion-Resistant Rollers: Ideal for applications where the conveyor belt carries abrasive materials. These rollers are coated with materials like polyurethane to resist wear and extend their lifespan.
- Chemical-Resistant Rollers: Used in chemical processing plants or places where rollers are exposed to corrosive substances. These are typically made from polypropylene or similar materials.
- High-Load Capacity Rollers: Specifically designed to support heavier weights, these rollers are reinforced with a robust internal structure to prevent deformation under load.
- Temperature-Resistant Rollers: Suitable for applications involving extreme temperatures, whether high or low. These rollers are manufactured from plastics that maintain their integrity in challenging thermal conditions.
Miniature Rollers for Compact Systems
- Small-Diameter Rollers: Perfect for tight spaces and lightweight applications, these rollers can be as small as 20mm in diameter, allowing for the design of compact conveyor systems.
- Low-Profile Rollers: These rollers are designed with a slim profile for systems where space is at a premium, ensuring efficient material handling without the need for large setups.
- Flexible Rollers: Ideal for curved or flexible conveyor systems, these miniature rollers can adapt to various layouts while maintaining smooth operation.
- Drive Rollers: Even in miniature systems, drive rollers are essential for propelling the conveyor belt. These are equipped with internal motors for a seamless drive mechanism.
- Guide Rollers: Used to guide materials along the conveyor path, these small rollers are crucial for maintaining alignment and preventing derailments in compact systems.
Specialized Rollers
- Rollers with Bearings: These rollers include precision bearings to reduce friction and enhance the smooth movement of the conveyor system, crucial for high-speed applications.
- Plastic Roller Wheels: For applications requiring lateral movement, plastic roller wheels can be integrated into conveyor systems, providing flexibility in material handling.
- Grooved Rollers: Designed to interact with specific types of conveyor belts or to handle items with unusual shapes, grooved rollers ensure compatibility and efficiency.
- Sprocketed Rollers: These rollers are equipped with sprockets to engage with chain-driven conveyor systems, offering reliable propulsion in heavy-duty applications.
- Anti-Static Rollers: In environments where static electricity could pose a risk, anti-static rollers made from conductive materials help to safely dissipate electrical charges.
Plastic conveyor roller suppliers play a crucial role in providing these diverse roller types, ensuring that businesses can find the perfect match for their specific conveyor system needs. Whether for heavy industrial use, compact applications, or specialized requirements, the right plastic conveyor rollers can significantly enhance operational efficiency and system reliability.
Choosing the Right Plastic Conveyor Roller Suppliers
Selecting the right plastic conveyor roller suppliers is crucial for ensuring the efficiency and reliability of your conveyor system. The market is filled with numerous suppliers, each offering a variety of products and services. To make an informed decision, several key factors need to be considered.
Factors to Consider
- Product Range: Look for suppliers with a comprehensive product range that covers various types of plastic conveyor rollers, including heavy-duty, miniature, and specialized rollers. This diversity ensures you can find the exact type of roller for your specific application.
- Quality of Materials: The durability and performance of conveyor rollers heavily depend on the quality of materials used. Suppliers who use high-grade plastics, such as reinforced polyamide for high-impact rollers or polyurethane for abrasion-resistant rollers, are preferable.
- Customization Options: Each conveyor system has unique requirements. Suppliers that offer customization options, allowing you to specify roller dimensions, material types, and additional features like anti-static properties or integrated bearings, can significantly enhance the functionality of your system.
- After-Sales Support: Reliable after-sales support is essential for addressing any issues that may arise post-purchase. Suppliers who provide comprehensive after-sales services, including technical support, warranty claims, and product returns, offer added value.
- Expertise and Reputation: Consider the supplier’s expertise in the field and their market reputation. Suppliers with extensive experience and positive customer feedback are more likely to provide high-quality products and services.
Importance of Conveyor Spare Parts and Maintenance Services
- Availability of Spare Parts: Regular wear and tear can lead to the need for replacement parts. Suppliers that maintain a stock of essential spare parts, such as bearings, sprockets, and roller tubes, ensure minimal downtime for your conveyor system.
- Maintenance Services: Some suppliers offer maintenance services to help keep your conveyor system in optimal condition. These services can range from periodic inspections to comprehensive maintenance packages.
- Technical Support: Access to technical support allows for quick troubleshooting of any issues that may arise, ensuring that your conveyor system continues to operate efficiently.
- Custom Maintenance Solutions: Suppliers that offer custom maintenance solutions tailored to your specific system can significantly extend the lifespan of your conveyor rollers and reduce the total cost of ownership.
- Training and Consultation: Suppliers who provide training and consultation services can help your staff better understand the operation and maintenance of the conveyor system, leading to improved efficiency and reduced risk of downtime.
Choosing the right plastic conveyor roller suppliers involves careful consideration of their product range, material quality, customization options, and after-sales support. Additionally, the availability of spare parts and maintenance services is crucial for ensuring the long-term reliability and efficiency of your conveyor system. By evaluating these factors, you can select a supplier that not only meets your immediate needs but also supports the ongoing success of your operations.
Leading Plastic Conveyor Roller Suppliers
The landscape of plastic conveyor roller suppliers is diverse, with several leading companies setting the standard for quality, innovation, and customer service. These suppliers have carved out niches for themselves by specializing in various aspects of conveyor roller production, from heavy-duty applications to sustainable manufacturing practices. Here’s a closer look at what sets these industry leaders apart.
Top Suppliers in the Industry
- Interroll Group: Renowned for its wide range of conveyor solutions, Interroll offers plastic rollers that are a benchmark for durability and efficiency. Their commitment to innovation is evident in their modular conveyor platforms, which are adaptable to a multitude of industrial applications.
- Rolcon Rollers: Specializing in both standard and custom-designed rollers, Rolcon has established itself as a go-to supplier for businesses needing tailored solutions. Their use of high-quality materials ensures the longevity and reliability of their products.
- UHMW Plastic Rollers: This supplier stands out for its focus on ultra-high molecular weight (UHMW) plastic rollers, offering exceptional wear resistance and impact strength. Their products are ideal for harsh industrial environments where durability is paramount.
- Conveyor Systems & Engineering, Inc.: With an extensive product catalog that includes a variety of plastic roller options, this supplier is known for its ability to meet the specific needs of its customers, regardless of the complexity of their conveyor systems.
- igus®: igus® is at the forefront of incorporating high-performance polymers in the design of plastic conveyor rollers. Their focus on self-lubricating materials that require no maintenance is a testament to their commitment to innovation and sustainability.
What Sets These Suppliers Apart
- Commitment to Sustainability: Many leading suppliers, such as igus®, prioritize the use of recyclable materials and energy-efficient manufacturing processes, appealing to environmentally conscious businesses.
- Extensive Product Catalogs: Suppliers like Conveyor Systems & Engineering, Inc., offer a wide range of roller types and sizes, ensuring that businesses can find the perfect fit for their specific conveyor needs.
- Customization Capabilities: Companies such as Rolcon Rollers excel in providing custom solutions, allowing businesses to specify roller dimensions, materials, and additional features to optimize their conveyor systems.
- Innovative Technologies: The adoption of advanced technologies, such as the use of UHMW plastics by UHMW Plastic Rollers, demonstrates these suppliers’ dedication to improving product performance and durability.
- Global Reach and Support: Leading suppliers often have a global presence, offering international shipping and localized customer support to ensure businesses around the world have access to top-quality conveyor rollers.
By choosing one of these leading plastic conveyor roller suppliers, businesses can benefit from high-quality products, innovative solutions, and a commitment to sustainability. Whether the need is for heavy-duty rollers capable of withstanding extreme conditions or for custom-designed rollers to fit a unique system, these suppliers have the expertise and product range to meet the diverse needs of the industry.
Applications and Industries Benefiting from Plastic Conveyor Roller Suppliers
The versatility and efficiency of plastic conveyor rollers make them an indispensable component in a wide array of industries. Supplied by dedicated plastic conveyor roller suppliers, these rollers are tailored to meet the specific demands of various sectors, ensuring smooth operations and enhancing overall productivity. Here’s a closer look at the industries that benefit significantly from these components and the real-world applications that underscore their importance.
Industries Benefiting from Plastic Conveyor Rollers
- Food Processing: In this industry, plastic rollers are preferred for their non-corrosive properties and ease of cleaning, essential for maintaining hygiene standards. Suppliers often provide FDA-approved materials suitable for direct contact with food products.
- Pharmaceuticals: Precision and cleanliness are paramount in pharmaceutical manufacturing. Plastic rollers offer a contamination-free solution for moving sensitive products through production lines, contributing to the industry’s stringent quality control measures.
- Packaging: The packaging industry relies on plastic conveyor rollers for their lightweight and low-noise operation, facilitating the swift and efficient packaging of goods without adding unnecessary weight to the conveyor system.
- Distribution Centers: High throughput and reliability are critical in distribution operations. Plastic rollers, known for their durability and low maintenance, ensure uninterrupted flow of goods, from sorting to shipping.
- Automotive Manufacturing: Even in heavy-duty applications like automotive parts assembly, plastic rollers are used for their resistance to chemicals and oils, providing a durable solution for moving components along the production line.
Real-World Applications of Plastic Rollers
- Assembly Lines: Plastic conveyor rollers are extensively used in assembly lines to move parts between workstations smoothly. Their impact resistance and durability minimize downtime, enhancing line efficiency.
- Sorting Systems: In distribution centers, plastic rollers facilitate the automated sorting of packages by size and weight. Their smooth surface reduces package wear, ensuring that items reach their destination in pristine condition.
- Cleanroom Environments: In pharmaceutical and electronics manufacturing, where cleanroom conditions are required, plastic rollers offer an antistatic and contamination-free solution for transporting components.
- Temperature-Controlled Storage: For industries requiring refrigerated storage, such as food and beverage, plastic rollers remain operational in cold environments, unlike metal rollers that can seize up.
- Loading Docks: Plastic rollers are used in loading dock conveyors to efficiently load and unload goods. Their resistance to environmental factors like moisture ensures longevity and reliability in these critical areas.
By partnering with specialized plastic conveyor roller suppliers, industries can access customized solutions that address their unique operational challenges. Whether it’s enhancing the hygiene in food processing, ensuring precision in pharmaceuticals, or improving efficiency in packaging and distribution, plastic conveyor rollers play a pivotal role in optimizing conveyor system performance while maintaining safety and reliability across various applications.
Maintenance and Care of Plastic Conveyor Roller Suppliers
Ensuring the longevity and optimal performance of plastic conveyor rollers is crucial for maintaining the efficiency of conveyor systems. Plastic conveyor roller suppliers often provide guidelines and support for the proper maintenance and care of these components. Here are practical tips and insights into maintaining plastic conveyor rollers and how suppliers can assist with parts that may require regular replacement or upgrades.
Tips on Maintaining Plastic Conveyor Rollers
- Regular Cleaning: Keep the rollers clean from debris and dust accumulation that can cause friction and wear. Use mild detergents and soft brushes to avoid damaging the roller surface.
- Inspection for Wear and Damage: Periodically inspect rollers for signs of wear, cracks, or deformation. Early detection of damage can prevent system failures and extend the life of the rollers.
- Lubrication of Bearings: While plastic rollers themselves require minimal lubrication, their bearings may need occasional lubrication. Use the lubricants recommended by your plastic conveyor roller suppliers to ensure compatibility.
- Alignment Checks: Ensure that the conveyor rollers are correctly aligned. Misalignment can lead to uneven wear and reduced efficiency. Adjustments should be made according to the manufacturer’s guidelines.
- Load Capacity Adherence: Do not exceed the recommended load capacity for the rollers. Overloading can cause premature wear and potential failure. Consult with your supplier for load specifications.
Common Conveyor Roller Parts for Replacement or Upgrades
- Bearings: Bearings are critical for smooth roller operation. Suppliers can provide replacement bearings or suggest upgrades for higher load capacities or better contamination resistance.
- Axles: Axles may wear down or bend under heavy use. Suppliers often offer stronger or corrosion-resistant axle options for harsh environments.
- Roller Tubes: The outer tube of the roller can become worn or damaged. Suppliers can provide replacement tubes or materials with enhanced properties, such as increased impact resistance or antistatic features.
- Sprockets and Drive Components: For powered systems, sprockets and other drive components may require replacement. Suppliers can assist with compatible parts to ensure continuous operation.
- End Caps and Seals: End caps protect the internal components of the roller, while seals prevent the ingress of contaminants. Suppliers can offer replacements to maintain the integrity of the roller.
Plastic conveyor roller suppliers play a vital role in the maintenance and care of conveyor systems. By following their maintenance guidelines and utilizing their support for replacement parts and upgrades, businesses can ensure the longevity and optimal performance of their plastic conveyor rollers. Proper care not only extends the life of the rollers but also maintains the efficiency and reliability of the entire conveyor system.
Submit Your Request for Conveyor Roller Technical Support.
FAQs About Plastic Conveyor Roller Suppliers
Conveyor rollers are manufactured by a wide array of companies specializing in material handling and industrial equipment. These manufacturers range from large multinational corporations to specialized small and medium-sized enterprises. Companies like Interroll, Rolcon Rollers, and Hytrol are renowned for their high-quality conveyor rollers, catering to diverse industries including manufacturing, logistics, and retail. Each manufacturer offers unique features and benefits, with some focusing on heavy-duty applications and others on specific industries like food processing or pharmaceuticals. When selecting a manufacturer, it’s essential to consider factors such as the company’s reputation, product quality, customization options, and after-sales support to ensure that you’re choosing the best partner for your conveyor system needs.
The best plastic material for conveyor rollers depends on the specific application and environment in which they will be used. High-Density Polyethylene (HDPE) is popular for its durability, low friction, and resistance to chemicals, making it suitable for harsh industrial environments. Polyvinyl Chloride (PVC) is another common choice, known for its strength and versatility, often used in food processing and packaging applications due to its compliance with hygiene standards. Acetal (Delrin) offers excellent wear resistance and low moisture absorption, ideal for precision applications requiring smooth operation. Ultimately, the choice of material should be based on factors such as load capacity, speed requirements, environmental conditions, and compatibility with the goods being transported.
Conveyors utilize various types of rollers to accommodate different materials, weights, and operational requirements. Gravity rollers, powered rollers, and grooved rollers are among the most commonly used. Gravity rollers rely on the force of gravity to move items and are suitable for lightweight packages and manual operations. Powered rollers, equipped with motors, are used for heavier loads and automated processes, providing controlled movement. Grooved rollers are designed to interact with belts or chains for precise item handling. Additionally, specialized rollers like impact rollers and brake rollers are used in specific applications to absorb shocks or control the speed of the conveyor.
Conveyor rollers come in a wide range of sizes to suit various applications and conveyor designs. The diameter of conveyor rollers can vary significantly, with common sizes ranging from as small as 20mm for lightweight applications to over 200mm for heavy-duty industrial use. The length of the rollers also varies, typically matching the width of the conveyor belt or frame to ensure even support and smooth operation. When selecting the size of conveyor rollers, it’s crucial to consider the size and weight of the items being transported, the type of conveyor system, and the space available. Custom sizes are often available to meet specific requirements, ensuring optimal performance and efficiency.
Last Updated on July 30, 2024 by Jordan Smith
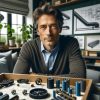
Jordan Smith, a seasoned professional with over 20 years of experience in the conveyor system industry. Jordan’s expertise lies in providing comprehensive solutions for conveyor rollers, belts, and accessories, catering to a wide range of industrial needs. From initial design and configuration to installation and meticulous troubleshooting, Jordan is adept at handling all aspects of conveyor system management. Whether you’re looking to upgrade your production line with efficient conveyor belts, require custom conveyor rollers for specific operations, or need expert advice on selecting the right conveyor accessories for your facility, Jordan is your reliable consultant. For any inquiries or assistance with conveyor system optimization, Jordan is available to share his wealth of knowledge and experience. Feel free to reach out at any time for professional guidance on all matters related to conveyor rollers, belts, and accessories.