Maximizing Efficiency with Plastic Conveyor Rollers in Industry
Conveyor rollers are pivotal components in the smooth operation of material handling systems across various industries. Serving as the backbone of conveyor systems, these rollers facilitate the efficient and effortless movement of goods, from production lines to packaging and distribution. Historically, metal and other materials were the go-to choices for manufacturing these essential parts. However, a significant shift towards plastic conveyor rollers has been observed in recent years. This transition is driven by the numerous advantages that plastic offers over traditional materials, including reduced weight, corrosion resistance, and lower operational noise. The adoption of plastic roller conveyor signifies an industry-wide move towards more sustainable, cost-effective, and versatile material handling solutions, underscoring their increasing importance in modern manufacturing and logistics processes.
What is Plastic Conveyor Rollers
Plastic conveyor rollers are an innovative solution designed to improve the functionality and efficiency of conveyor systems. Unlike their metal counterparts, these rollers are crafted from high-quality, durable plastic materials, such as polyvinyl chloride (PVC) or high-density polyethylene (HDPE). This transition from traditional materials to plastic has not only revolutionized the design and operation of conveyor systems but also introduced a host of benefits that enhance their performance across various applications.
The benefits of using plastic conveyor rollers over metal or other materials are numerous and significant. Firstly, plastic rollers are considerably lighter than metal rollers, which reduces the overall weight of the conveyor system. This reduction in weight translates to lower energy consumption, as less power is required to move the rollers and, subsequently, the materials they carry. Secondly, plastic roller conveyor systems offer exceptional corrosion resistance, making them ideal for use in environments where moisture or chemicals might cause metal rollers to degrade over time.
Thirdly, these rollers operate much more quietly than metal rollers, reducing noise pollution in the workplace and creating a more pleasant environment for employees. Fourthly, the inherent properties of plastic provide a smoother surface, reducing the wear and tear on the conveyor belts that interact with the rollers. This leads to longer belt life and lower maintenance costs. Lastly, plastic conveyor rollers can be manufactured with a high degree of precision, ensuring uniformity in size and shape, which improves the stability and reliability of the conveyor system as a whole.
By integrating plastic conveyor rollers into their systems, industries can achieve more efficient, cost-effective, and durable material handling solutions, reflecting the evolving demands and environmental considerations of modern manufacturing and logistics operations.
Types of Plastic Conveyor Rollers
The diversity among plastic conveyor rollers caters to a wide range of industrial needs, ensuring there’s a type of roller that’s perfectly suited for almost any application. Understanding the different types of plastic roller conveyor systems can help businesses and project managers select the most appropriate option for their specific requirements.
Used Plastic Conveyor Rollers
Purchasing used plastic conveyor rollers can be a cost-effective solution for many businesses. The advantages include lower initial costs, reduced waste contributing to environmental sustainability, and immediate availability, bypassing potential manufacturing wait times. However, potential drawbacks might include shorter lifespan compared to new rollers, unknown wear and tear history, possible compatibility issues with existing systems, and limited warranty or no warranty coverage. It’s crucial to carefully inspect used rollers for any signs of excessive wear or damage before integrating them into a conveyor system.
Heavy-Duty Plastic Conveyor Rollers
Designed for applications requiring robust performance, heavy-duty plastic conveyor rollers are capable of handling substantial loads and operating in harsh environments. These rollers find their use in industries such as mining, construction, and heavy manufacturing. They offer benefits including high impact resistance, ability to withstand extreme temperatures, reduced maintenance needs, noise reduction, and enhanced durability. The versatility of heavy-duty rollers makes them suitable for moving heavy materials, functioning in outdoor environments, and applications where traditional rollers might fail.
Plastic Rollers with Bearings
Plastic rollers equipped with bearings are designed to provide smoother operation and higher efficiency. The inclusion of bearings minimizes friction, allowing the roller to move more freely and thus reducing the energy required to operate the conveyor system. These rollers are ideal for applications where precision and reduced resistance are crucial, such as in packaging lines, food processing, and pharmaceutical manufacturing.
DIY PVC Conveyor Rollers
For those looking to customize their conveyor system or undertake a small-scale project, DIY PVC conveyor rollers offer a flexible and cost-effective solution. PVC, being lightweight, easy to work with, and corrosion-resistant, is an excellent material for homemade rollers. Guides on creating your own rollers usually include selecting the right PVC pipe diameter, cutting it to the desired length, and fitting it with bearings or bushings. This approach is particularly suited for light-duty applications or environments where customization is necessary.
Plastic Roller Wheels and Applications
The application of plastic roller wheels extends beyond traditional conveyor systems. These wheels are utilized in furniture moving, sliding door mechanisms, material handling carts, and even in some types of skateboards. The versatility of plastic roller wheels is evident in their durability, low maintenance requirements, ease of installation, and resistance to corrosion, making them suitable for both indoor and outdoor applications.
Specialized Rollers
Specialized plastic conveyor rollers, such as grooved, sprocket, and urethane rollers, are tailored for specific functions within conveyor systems. Grooved rollers are used to guide belts or accommodate drive belts, sprocket rollers are involved in chain-driven conveyors, and urethane rollers offer a non-marking, abrasion-resistant surface for delicate materials. These custom designs address unique challenges, providing solutions that enhance the efficiency and functionality of conveyor systems across a broad spectrum of industries.
By understanding the various types of plastic roller conveyor available, businesses can make informed decisions that optimize their operations, improve efficiency, and reduce costs.
Choosing the Right Plastic Conveyor Rollers
Selecting the right plastic conveyor rollers is critical for the efficiency, reliability, and longevity of your conveyor system. Whether for industrial use, commercial sale, or DIY projects, understanding the specific requirements and factors that influence the choice of rollers is key.
For Industrial Use
When choosing plastic conveyor rollers for industrial applications, it’s essential to consider both the load they need to support and the environmental conditions they’ll be exposed to. Heavy-duty rollers are best suited for environments where they will be required to carry heavy loads, such as in mining or construction settings. These rollers are designed to withstand not just the weight but also the abrasive conditions they might encounter. For lighter industrial use, such as in packaging or assembly lines, standard plastic rollers might suffice. They offer the advantages of being quieter and less costly, with sufficient durability for less demanding conditions. Environmental factors, such as exposure to chemicals, extreme temperatures, or moisture, should also guide the selection process, ensuring the chosen rollers can withstand these conditions without degrading.
For Commercial Sale
Businesses looking to stock and sell plastic conveyor rollers should consider a variety of factors to meet the diverse needs of their customers. Firstly, offering a range of rollers suitable for different industrial environments—from light-duty to heavy-duty applications—can cater to a broader market. Including rollers with specific features, such as corrosion resistance or anti-static properties, addresses the niche requirements of certain industries. Providing rollers in various sizes and with different bearing options can also be beneficial, as it allows customers to select products that match their precise specifications. Educating the sales team on the advantages and applications of different types of roller conveyor plastic can enhance customer service by enabling informed recommendations. Finally, maintaining a stock of commonly used rollers ensures quick fulfillment of customer orders, enhancing business reputation for reliability.
For DIY Projects
DIY enthusiasts looking to create custom conveyor rollers at home should focus on selecting the right materials and tools for their project. Choosing the correct type of plastic, such as PVC or HDPE, is crucial based on the intended use and durability requirements. The plastic should be easy to work with, using common household tools, and capable of supporting the expected load without deformation. Bearings are an essential component for ensuring smooth operation, so selecting high-quality bearings that fit the plastic tubing precisely is important. Tools for cutting the plastic tubing to size, drilling holes for bearings, and assembling the rollers should be considered for the project. Additionally, understanding the basics of conveyor roller design, such as the importance of roller spacing and alignment, can greatly impact the success of DIY conveyor projects. By considering these aspects, DIY enthusiasts can create efficient, durable, and customized plastic conveyor rollers for their specific needs.
Installation and Maintenance of Plastic Conveyor Rollers
Ensuring the correct installation and regular maintenance of plastic conveyor rollers is crucial for the smooth operation of conveyor systems. Properly installed and maintained rollers can significantly extend the lifespan of the conveyor system, reduce downtime, and maintain high levels of efficiency and productivity.
Setting up your Plastic Conveyor Rollers
The installation of plastic conveyor rollers should follow a structured process to ensure they are set up correctly and safely. Here’s a step-by-step guide:
- Preparation: Begin by gathering all necessary tools and equipment. Ensure you have the correct size and type of plastic conveyor rollers for your system. Verify that the conveyor frame is clean and free from debris.
- Alignment: Carefully place the rollers in the conveyor frame. Rollers should be aligned with the frame to ensure they are straight. Misalignment can cause wear and tear on both the rollers and the conveyor belt.
- Spacing: Follow the manufacturer’s recommendations for roller spacing. This ensures that the conveyor belt is adequately supported without putting unnecessary strain on the rollers.
- Securing: Once aligned and spaced correctly, secure the rollers to the conveyor frame. Depending on the design, this may involve tightening bolts or clamps.
- Testing: Before putting the conveyor into full operation, conduct a test run to ensure the rollers move smoothly and the belt tracks correctly. Adjust as necessary.
Maintaining Your Rollers
Regular maintenance of plastic conveyor rollers is essential to prevent breakdowns and extend their service life. Here are some best practices:
- Regular Inspection: Schedule periodic inspections of the rollers to identify any signs of wear, damage, or misalignment. Early detection of issues can prevent more significant problems down the line.
- Cleaning: Keep the rollers clean from debris, dust, and other materials that could cause jamming or degradation of the roller surface. Use appropriate cleaning agents that won’t damage the plastic.
- Lubrication: If the rollers have bearings that require lubrication, ensure this is done according to the manufacturer’s guidelines. Use the correct type of lubricant and apply it carefully to avoid over-lubrication.
- Replacement: Replace rollers that show signs of significant wear or damage. Continuing to use damaged rollers can harm the conveyor belt and other system components.
- Record Keeping: Maintain records of inspections, maintenance activities, and replacements. This can help identify recurring issues and plan for future maintenance, ensuring the longevity and efficiency of the plastic conveyor rollers.
By following these guidelines for installation and maintenance, you can maximize the performance and lifespan of your plastic conveyor roller, contributing to the overall effectiveness of your conveyor system.
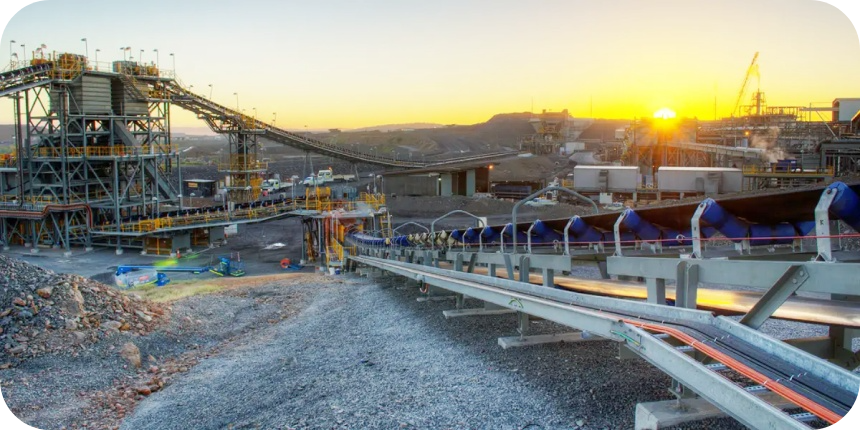
Where to Buy Plastic Conveyor Rollers
Finding the right source for purchasing plastic conveyor rollers, whether new or used, is essential for businesses looking to maintain or upgrade their conveyor systems. Various resources are available for acquiring these components, each offering distinct advantages. Here are some insights and tips on where to find roller conveyor plastic for sale.
Online Vendors
One of the most convenient ways to purchase plastic conveyor rollers is through online vendors. These platforms often provide a wide selection of roller types, sizes, and materials to suit different industrial needs. Online shopping allows you to compare products and prices easily, read customer reviews, and access detailed product specifications. When purchasing from online vendors, look for those with a strong reputation, customer support, and return policies to ensure you receive quality products and assistance if needed.
Industrial Supply Stores
Industrial supply stores are another valuable resource for buying plastic conveyor rollers. These stores not only offer a range of products but also the expertise of sales personnel who can provide advice on the best roller types for specific applications. Visiting a physical store allows for a hands-on examination of the rollers, ensuring their quality and suitability for your conveyor system. It’s also an opportunity to establish a relationship with the supplier for future needs and support.
Manufacturers and Distributors
Purchasing directly from manufacturers or their authorized distributors can be a wise choice, especially for businesses requiring custom solutions or large quantities of plastic conveyor rollers. Direct purchases often come with the benefit of competitive pricing, technical support, and the option to customize products to meet specific requirements. Additionally, manufacturers and distributors can provide valuable insights into new technologies and products that could enhance your conveyor system.
Used Equipment Dealers
For businesses on a tight budget or looking for short-term solutions, used equipment dealers offer a cost-effective option. These dealers typically have a selection of used or refurbished plastic conveyor rollers that can meet various operational needs. When buying used rollers, it’s crucial to inspect them for wear and functionality or inquire about any refurbishment processes they’ve undergone. Purchasing from a reputable dealer with a good track record and warranty options is advisable.
Trade Shows and Industry Events
Trade shows and industry events are excellent places to explore the latest advancements in conveyor technology, including plastic conveyor rollers. These events offer the chance to meet directly with manufacturers, distributors, and other suppliers, compare products side by side, and negotiate deals. They also provide networking opportunities and the ability to stay updated on industry trends.
When searching for plastic conveyor roller, considering the specific needs of your conveyor system, including load capacity, environmental conditions, and the type of materials being transported, is essential. By exploring these resources and utilizing the tips provided, you can find the right plastic conveyor rollers to keep your conveyor system running smoothly and efficiently.
Innovative Uses of Plastic Conveyor Rollers
Plastic conveyor rollers, known for their durability and versatility, are finding innovative applications beyond their traditional roles in conveyor systems. Their use in automation and robotics, as well as in non-industrial settings, showcases their adaptability and potential to improve efficiency and functionality in various fields.
In Automation and Robotics
The integration of plastic conveyor rollers in automation and robotics has led to significant advancements in these technologies.
- Automated Warehousing Systems: Plastic rollers are used in automated storage and retrieval systems (AS/RS) to smoothly and efficiently move goods with minimal wear and tear, enhancing operational speed and reliability.
- Robotic Material Handling: In manufacturing, robots equipped with plastic rollers can transfer parts between processes without damaging them, increasing the precision and efficiency of production lines.
- Sorting Systems: Automation in postal and courier services utilizes plastic rollers in sorting systems to gently divert packages to their respective destinations, improving sorting accuracy and package handling.
- Mobile Robots: Plastic rollers are employed in the wheels and tracks of mobile robots, providing durability and reducing noise as these robots navigate through various environments, from warehouses to hospitals.
- Laboratory Automation: In pharmaceuticals and research labs, plastic rollers facilitate the automated handling of delicate samples and reagents, minimizing contamination risks and enhancing throughput.
Plastic Rollers for Non-Industrial Applications
Beyond the confines of industry, plastic rollers are being creatively used in everyday applications, demonstrating their utility and versatility.
- Hair Styling Tools: Plastic rollers are a staple in hair salons and home styling kits for curling hair. Their smooth surface and heat resistance make them ideal for creating curls without damaging the hair.
- Furniture Sliders: Heavy furniture can be moved easily without scratching the floor by using plastic rollers, making rearranging rooms or moving much less of a hassle.
- Exercise Equipment: In fitness, plastic rollers are used in ab wheels and other equipment, providing a smooth motion and durability for workout routines.
- Door and Window Tracks: Sliding doors and windows often incorporate plastic rollers for smooth operation, ensuring they open and close easily without the need for lubrication.
- Toys and Games: From rolling parts in board games to components in children’s toys, plastic rollers add a dimension of movement and interactivity, enhancing the play experience.
The innovative uses of plastic conveyor rollers in both high-tech fields like automation and robotics and in everyday applications highlight their versatility and potential to transform a wide range of activities. Their durability, efficiency, and adaptability make them an invaluable component in modern technology and daily life alike.
Contact us to find the perfect conveyor roller for your needs.
FAQs About Plastic Conveyor Rollers
Conveyor rollers are critical components in the operation of conveyor systems, providing the necessary support and movement for the conveyor belt or materials being transported. These rollers can be made from various materials, including metal, rubber, and plastic, each offering different benefits. Metal rollers are known for their strength and durability, making them suitable for heavy-duty applications. Rubber rollers provide a softer surface, which can grip items on the conveyor better and reduce noise. However, plastic rollers have gained popularity due to their lightweight, corrosion resistance, and cost-effectiveness. They are available in different types, such as those designed for heavy loads, those with integrated bearings for smoother operation, and even customizable options for specific applications. The choice of roller material and type depends on the specific needs of the conveyor system, including the weight of the items being transported, the environment in which the system operates, and the desired longevity and maintenance requirements.
Plastic rollers are components of conveyor systems, designed to support and move the conveyor belt or the items being transported. Unlike their metal counterparts, these rollers are manufactured from plastic materials, offering a range of advantages that include reduced weight, resistance to corrosion, and lower operational noise. The use of plastic also allows for a high degree of customization in terms of size, shape, and functionality. These rollers can be designed to include features such as integrated bearings for smoother rotation, specialized surface textures for improved grip, and variations in hardness to suit different applications. Plastic rollers are particularly valued in industries where avoiding corrosion is essential, such as in food processing, chemical handling, and outdoor applications. Their versatility and cost-effectiveness make them a popular choice for both heavy-duty industrial applications and lighter, more specialized tasks.
The plastic materials most commonly used for conveyor rollers include polyvinyl chloride (PVC), high-density polyethylene (HDPE), and polyurethane (PU). PVC is prized for its durability, chemical resistance, and low cost, making it suitable for a wide range of applications, including light to medium-duty conveyance. HDPE offers excellent toughness and low friction, which makes it ideal for rollers that require high impact resistance and smooth operation. Polyurethane, known for its elasticity and abrasion resistance, is often used in rollers designed to handle delicate items or operate in environments where wear resistance is critical. Each of these materials brings specific advantages to the table, allowing for the customization of rollers to meet the unique demands of different conveyor systems and operational environments. The choice of material will depend on factors such as the weight of the conveyed items, the presence of chemicals or moisture, and the required durability of the rollers.
Conveyor rollers are indispensable in the efficient operation of conveyor systems. They serve several critical functions, including reducing the friction between the conveyor belt and the surface it moves over, supporting the weight of the items being transported, and helping to move the belt or items along the conveyor path. The use of rollers enables the smooth and consistent movement of goods, which is essential for optimizing production lines, packaging operations, and material handling processes. Rollers also contribute to the longevity of the conveyor belt by minimizing wear and tear, thereby reducing maintenance costs and downtime. Furthermore, the implementation of rollers in a conveyor system can significantly enhance workplace safety by automating the movement of heavy or hazardous materials, reducing the need for manual handling, and minimizing the risk of injuries. The efficiency, safety, and cost-effectiveness provided by conveyor rollers make them a fundamental component in industries ranging from manufacturing and logistics to retail and food services.
Last Updated on July 9, 2024 by Jordan Smith
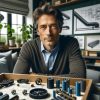
Jordan Smith, a seasoned professional with over 20 years of experience in the conveyor system industry. Jordan’s expertise lies in providing comprehensive solutions for conveyor rollers, belts, and accessories, catering to a wide range of industrial needs. From initial design and configuration to installation and meticulous troubleshooting, Jordan is adept at handling all aspects of conveyor system management. Whether you’re looking to upgrade your production line with efficient conveyor belts, require custom conveyor rollers for specific operations, or need expert advice on selecting the right conveyor accessories for your facility, Jordan is your reliable consultant. For any inquiries or assistance with conveyor system optimization, Jordan is available to share his wealth of knowledge and experience. Feel free to reach out at any time for professional guidance on all matters related to conveyor rollers, belts, and accessories.