Custom Solutions: Polyurethane Guide Rollers for Every Need
Polyurethane guide rollers are pivotal components in the seamless operation of machinery across a multitude of industries, from manufacturing to logistics. These rollers, crafted from the versatile polymer polyurethane, stand out for their exceptional durability, resistance to wear and tear, and ability to operate under varying environmental conditions. Their widespread application underscores their importance, making the search for “polyurethane guide rollers near me” a frequent quest for businesses aiming to enhance their operational efficiency. The adaptability of polyurethane allows these rollers to meet specific industry needs, ensuring smooth operations and contributing significantly to the productivity and longevity of the machinery they are part of. This brief overview highlights the critical role polyurethane guide rollers play in modern industry, underscoring their value in today’s technology-driven world.
The Superiority of Polyurethane Material in Polyurethane Guide Rollers
Polyurethane, a synthetic resin known for its exceptional elasticity and resilience, stands as the cornerstone material for polyurethane guide rollers. This versatile polymer, often referred to by chemical designations like polyurethane 11671, embodies a unique set of properties that distinctly positions it above traditional materials used in roller manufacturing. The inherent qualities of polyurethane not only contribute to the enhanced performance of guide rollers but also extend their operational lifespan, making them indispensable in various industrial applications. Here, we explore the defining properties of polyurethane that underscore its superiority and pivotal role in the fabrication of polyurethane guide rollers.
Properties of Polyurethane
Polyurethane’s formulation can be adjusted to meet a wide range of mechanical and physical requirements, making it an ideal choice for creating polyurethane guide rollers tailored to specific industrial needs. The following properties highlight why polyurethane is the preferred material for these applications:
- Durability: Polyurethane’s robust composition ensures that guide rollers can endure extensive operational demands without significant wear, providing a long service life.
- Load-Bearing Capacity: Its structural integrity allows it to support substantial loads, making it indispensable in heavy-duty applications where reliability is crucial.
- Abrasion Resistance: Exceptionally resistant to abrasion, polyurethane guide rollers maintain their form and functionality even when subjected to rough surfaces and materials.
- Chemical Resistance: Polyurethane stands up to a variety of chemicals, oils, and solvents, ensuring stability and longevity in environments where such exposures are common.
- Environmental Resistance: Capable of withstanding extreme environmental conditions, including wide temperature ranges, UV exposure, and moisture, polyurethane guide rollers are suited for both indoor and outdoor applications.
- Flexibility: Unlike many materials that stiffen in cold conditions, polyurethane retains its flexibility, ensuring consistent performance across a spectrum of temperatures.
- Tear Resistance: The material’s resistance to tearing and cutting protects it from damage during operation, especially in applications involving sharp or jagged edges.
- Customizability: The versatility of polyurethane allows for customization in hardness and other physical properties, enabling the creation of rollers that meet specific application requirements.
The unique combination of these properties makes polyurethane an unparalleled choice for the manufacture of guide rollers, offering durability, reliability, and performance that other materials simply cannot match. As we delve deeper into the comparison with other materials, it becomes evident why polyurethane guide rollers are the preferred option for a wide array of industrial applications.
Comparison with Other Materials
When compared to materials traditionally used in roller manufacturing, such as rubber, steel, or plastic, polyurethane offers several advantages:
- Superior Durability: Unlike rubber, which can wear down quickly under friction, polyurethane guide rollers offer extended service life.
- Enhanced Load-Bearing Capacity: Steel may carry heavy loads but lacks the shock-absorbing properties of polyurethane, which distributes weight more evenly.
- Outstanding Abrasion Resistance: Plastic rollers may succumb to abrasive surfaces, whereas polyurethane withstands such conditions with minimal wear.
- Broad Chemical Resistance: Rubber rollers may degrade when exposed to certain chemicals, a problem polyurethane often resists effectively.
- Greater Environmental Adaptability: Polyurethane outperforms plastics and metals in resisting environmental factors like UV exposure and temperature extremes.
- Maintained Flexibility: Unlike materials that become brittle in cold environments, polyurethane retains its flexibility, ensuring consistent performance.
- Higher Tear Resistance: Polyurethane is less likely to tear or cut compared to rubber, maintaining its integrity even when subjected to sharp objects or edges.
- Customization Potential: The ability to customize the hardness of polyurethane surpasses that of steel or plastic, offering solutions tailored to specific roller applications.
- Cost-Effectiveness Over Time: Considering its longevity and reduced need for replacement, polyurethane guide rollers prove to be more cost-effective than those made from other materials.
The superiority of polyurethane material in manufacturing polyurethane guide rollers is evident through its remarkable properties and advantages over other materials. Its durability, load-bearing capacity, and resistance to abrasion, chemicals, and environmental factors make it the material of choice for high-performance rollers in a wide range of industrial applications.
Applications of Polyurethane Guide Rollers
Polyurethane guide rollers, with their exceptional durability and versatility, have become indispensable in a wide array of industrial applications. Their unique properties allow them to perform under challenging conditions, making them a preferred choice across diverse sectors. Here, we explore the extensive applications of polyurethane guide rollers and provide illustrative examples of their use in various industries, showcasing their adaptability and critical role in enhancing operational efficiency.
Diverse Applications of Polyurethane Rollers
Polyurethane guide rollers are not just components; they are essential tools that enhance efficiency and reliability in numerous applications. Their unique material properties allow them to meet the demands of various operational environments, making them indispensable in both general and specialized machinery. Here, we explore the broad spectrum of applications where these rollers are utilized, demonstrating their critical role in industry.
- Conveyor Systems: Polyurethane guide rollers are widely used in conveyor systems across manufacturing and packaging industries due to their ability to reduce friction and wear, enhancing the longevity of the conveyor belts.
- Manufacturing Lines: In automotive, electronics, and appliance manufacturing, these rollers facilitate the smooth and precise movement of components along the production line.
- Printing and Paper Industry: Their non-marking properties make polyurethane rollers ideal for use in printing presses and paper feed systems, where they minimize damage to delicate surfaces.
- Textile Machinery: Polyurethane guide rollers are employed in textile machines for their gentle handling of fabrics and resistance to chemicals and heat.
- Food Processing Equipment: Due to their compliance with food safety regulations, these rollers are used in food conveyance systems, ensuring hygienic contact with food products.
- Material Handling Equipment: In warehouses and distribution centers, polyurethane rollers are essential for the smooth operation of pallet jacks, forklifts, and automated guided vehicles (AGVs).
- Agricultural Machinery: Their resistance to environmental factors makes them suitable for use in agricultural equipment, where they endure exposure to dirt, moisture, and chemicals.
- Specialized Machinery: Polyurethane guide rollers are also found in fitness equipment, escalators, and cleanroom applications, where their specific properties, such as non-marking and low-noise operation, are particularly beneficial.
Case Studies and Examples
The practical applications of polyurethane guide rollers extend far beyond theoretical advantages, as demonstrated by their successful implementation in various industries. These case studies and examples provide a glimpse into how polyurethane rollers solve real-world challenges, improving processes and outcomes across different sectors. From automotive assembly to the delicate handling required in pharmaceutical packaging, these instances underscore the adaptability and value of polyurethane guide rollers.
- Automotive Assembly Lines: Polyurethane rollers are used to transport car bodies through the assembly process, where their durability withstands the weight and their surface properties prevent damage to the vehicles.
- Pharmaceutical Packaging: In the pharmaceutical industry, these rollers ensure the gentle handling of sensitive packaging materials through the filling and sealing processes.
- Aerospace Component Manufacturing: For the production of aerospace components, polyurethane guide rollers offer precision movement and resistance to the chemicals used in the manufacturing process.
- Logistics and Sorting Centers: E-commerce fulfillment centers utilize polyurethane rollers in their sorting systems to handle packages of varying sizes and weights efficiently.
- Paper Mills: In paper production, these rollers support the paper as it moves through the drying and coating machines, resisting the high temperatures and moisture levels encountered.
- Textile Dyeing Machines: Polyurethane rollers are used in dyeing machines for their chemical resistance and ability to operate smoothly under wet conditions, ensuring even dye application.
- Renewable Energy Sector: In the manufacturing of solar panels and wind turbine blades, polyurethane guide rollers facilitate the movement of delicate components through the production line, minimizing the risk of damage.
The applications of polyurethane guide rollers are as varied as the industries they serve, demonstrating their essential role in modern manufacturing and processing. Their adaptability, combined with superior material properties, makes them a key component in enhancing efficiency, productivity, and product quality across a broad spectrum of industrial activities.
Custom Polyurethane Molding and Manufacturing for Polyurethane Guide Rollers
The manufacturing of polyurethane guide rollers involves a highly specialized process known as custom polyurethane molding. This process is pivotal in meeting the diverse needs of industries that rely on these rollers for their operations. Custom molding of polyurethane allows for the creation of rollers that are not only unique in shape, size, and hardness but also tailored to specific application requirements. Here, we delve into the intricacies of custom polyurethane molding and manufacturing, highlighting how this process caters to the production of high-quality polyurethane guide rollers.
Custom Polyurethane Molding Process
Custom polyurethane molding for polyurethane guide rollers is a detailed process that involves several key steps and considerations to ensure that the final product meets the exact specifications of the customer. The process includes:
- Design and Prototyping: Initially, detailed designs of the polyurethane guide rollers are created, often involving CAD software to ensure precision. Prototypes may be produced for testing and validation purposes.
- Mold Creation: Based on the design, molds are crafted from aluminum, steel, or other materials. The complexity of the mold depends on the roller’s design, including its shape and texture.
- Material Selection: Polyurethane comes in various formulations, each offering different properties. The selection of the right polyurethane material (e.g., hardness, resilience) is crucial to the roller’s performance.
- Casting: The polyurethane is poured or injected into the mold. This process can be done manually or through automated systems, depending on the precision and volume required.
- Curing and Post-Curing: After casting, the polyurethane undergoes curing, a chemical process that solidifies the material. Some applications may require post-curing to achieve the desired material properties.
- Machining and Finishing: Once cured, the rollers may undergo machining to achieve precise dimensions and finishing to create the desired surface texture or to add any necessary coatings.
- Quality Control: Each roller is inspected for dimensional accuracy, material properties, and overall quality to ensure it meets the specified requirements.
- Assembly: If the rollers include bearings or other components, assembly is performed under strict quality standards.
- Customization: Throughout the process, there is a strong emphasis on customization, allowing for adjustments in material properties, size, and design to meet specific operational needs.
Urethane Manufacturing Processes
The manufacturing processes for polyurethane guide rollers are designed to produce high-quality products that meet the rigorous demands of various industries. These processes include:
- High-Pressure Injection Molding: Ideal for producing rollers with complex shapes and high dimensional accuracy.
- Low-Pressure Processing: Used for larger rollers, allowing for better control over material properties.
- Open Casting: Suitable for custom shapes and sizes, open casting is versatile and allows for a wide range of hardness levels.
- Centrifugal Casting: Perfect for creating rollers with uniform density and material distribution, especially for cylindrical shapes.
- Compression Molding: This method is used for high-strength rollers, applying pressure to the polyurethane in a heated mold.
- Rotational Molding: For hollow or lightweight rollers, rotational molding ensures even distribution of material.
- Material Formulation: Custom formulation of the polyurethane material to achieve specific properties such as high abrasion resistance, load-bearing capacity, or chemical resistance.
- Post-Processing Treatments: Including heat treatments, UV stabilization, and anti-static coatings to enhance the performance and longevity of the rollers.
Through custom polyurethane molding and specialized manufacturing processes, producers can create polyurethane guide rollers that precisely meet the needs of their applications. This level of customization and quality control ensures that industries relying on these rollers can maintain efficient, reliable, and smooth operations.
Precision Urethane and Its Role in Polyurethane Guide Rollers
Precision urethane plays a pivotal role in the manufacturing of polyurethane guide rollers, embodying the essence of high-quality, durability, and performance in industrial applications. This specialized segment of polymer technology focuses on the precise formulation and molding of urethane to meet stringent specifications, ensuring that each roller produced meets the exact needs of its application. The significance of precision urethane in the production of polyurethane guide rollers cannot be overstated, as it directly impacts the rollers’ efficiency, lifespan, and overall performance in various machinery and equipment.
Companies Specializing in Precision Urethane
Several companies have established themselves as leaders in the field of precision urethane, offering a range of services from custom formulation to advanced molding techniques. These companies are at the forefront of innovation in polyurethane manufacturing, ensuring the production of high-quality polyurethane guide rollers:
- Polyurethane Products Corporation: Known for their custom molding solutions, they offer a wide range of urethane formulations to suit different industrial needs.
- Urethane Systems Plus, Inc.: Specializes in precision casting and machining of urethane parts, providing rollers with exceptional durability and performance.
- Advanced Urethane Engineering: Focuses on high-precision urethane products, utilizing state-of-the-art equipment to achieve tight tolerances.
- Elite Urethane Manufacturers: Offers comprehensive services from design to production, ensuring each roller is crafted to meet specific operational requirements.
- Precision Urethane & Machine, Inc.: With decades of experience, they excel in producing custom polyurethane rollers designed for various applications.
- Urethane Innovators, Inc.: Prides itself on innovative solutions and custom formulations, catering to unique industry challenges.
- Custom Urethane Technologies: Specializes in high-quality, custom-designed urethane rollers, focusing on meeting the precise needs of each customer.
- Dynamic Urethane Manufacturing: Known for their rapid prototyping and advanced manufacturing processes, they produce rollers that meet high standards of quality and performance.
Ensuring High-Quality Production
These companies ensure the production of high-quality polyurethane guide rollers through several key practices:
- Custom Formulation: Tailoring the urethane’s chemical properties to match the specific requirements of the application, including hardness, abrasion resistance, and load-bearing capacity.
- Advanced Molding Techniques: Utilizing precision molding processes such as injection molding, compression molding, and rotational molding to achieve accurate shapes and sizes.
- Quality Control Protocols: Implementing stringent quality control measures at every stage of production, from raw material selection to final inspection, to ensure that each roller meets the highest standards.
- Innovative Design and Engineering: Working closely with clients to design rollers that not only meet but exceed performance expectations in their specific applications.
- State-of-the-Art Machining: Employing advanced machining and finishing techniques to ensure precise dimensions and surface finishes, enhancing the roller’s performance and longevity.
- Material Testing: Conducting comprehensive material testing to verify the urethane’s properties and performance under simulated operational conditions.
- Collaborative Approach: Engaging in a collaborative approach with clients to understand their needs fully and provide customized solutions that address their challenges.
- Continuous Improvement: Committing to ongoing research and development to improve materials, processes, and products, ensuring that they remain at the forefront of urethane technology.
The role of precision urethane in the manufacturing of polyurethane guide rollers is crucial, as it directly influences the quality, performance, and reliability of these essential industrial components. Companies specializing in precision urethane are dedicated to pushing the boundaries of what’s possible, ensuring that industries across the board have access to rollers that meet their exacting standards and help drive their success.
Polyurethane Guide Rollers with Bearings
The integration of bearings into polyurethane guide rollers represents a significant advancement in roller design, enhancing their functionality and operational efficiency. This combination not only leverages the superior material properties of polyurethane but also capitalizes on the mechanical advantages of bearings. The result is a component that offers unparalleled smoothness in operation and performance under a variety of conditions. Here, we delve into the benefits of incorporating bearings into polyurethane guide rollers and explore the customization options available to meet the diverse needs of different applications.
Benefits of Bearings in Polyurethane Rollers
Integrating bearings into polyurethane guide rollers brings about several key benefits that significantly enhance their performance:
- Reduced Friction: Bearings minimize surface contact during operation, drastically reducing friction and facilitating smoother roller movement.
- Increased Load Capacity: The addition of bearings allows the rollers to handle higher loads by distributing weight more evenly and efficiently.
- Enhanced Durability: Bearings protect the roller from direct impact and stress, prolonging the life of both the polyurethane surface and the core structure.
- Improved Precision: The stability provided by bearings leads to more precise movements, crucial in applications requiring high levels of accuracy.
- Higher Speed Capability: With reduced friction, rollers can achieve higher speeds without compromising on performance or safety.
- Ease of Maintenance: Bearings can be designed for easy replacement or maintenance, reducing downtime and operational costs.
- Versatility in Application: The combination of polyurethane and bearings makes these rollers suitable for a wide range of environments, including those with moisture, dust, or chemical exposure.
- Noise Reduction: Bearings contribute to quieter operation, an essential factor in environments where noise levels are a concern.
Customization Options for Polyurethane Rollers with Bearings
The customization of polyurethane guide rollers with bearings is key to their success in various applications. Manufacturers offer a range of options to tailor these components to specific requirements:
- Bearing Type: Selection from ball bearings, roller bearings, or needle bearings, depending on load requirements and operational speeds.
- Bearing Material: Options include stainless steel for corrosion resistance, chrome steel for durability, or plastic composites for chemical resistance.
- Polyurethane Hardness: Customization of the polyurethane’s durometer to match the application’s need for flexibility or rigidity.
- Roller Size and Shape: Tailoring the dimensions and profile of the roller to fit the machinery or conveyance system precisely.
- Surface Texture: Options for smooth, grooved, or patterned surfaces to enhance grip or facilitate movement of specific materials.
- Chemical and Environmental Resistance: Formulation adjustments to ensure the polyurethane can withstand specific chemicals or environmental conditions.
- Color Coding: Incorporation of colors into the polyurethane for identification, safety, or aesthetic purposes.
- Mounting Options: Customization of the roller’s mounting system to ensure compatibility with existing equipment, including fixed, flange, or threaded mounting styles.
The integration of bearings into polyurethane guide rollers and the extensive customization options available make these components highly adaptable and effective in a broad spectrum of industrial applications. By carefully selecting the appropriate configurations, businesses can significantly enhance the efficiency, reliability, and longevity of their operations, ensuring smooth and precise movement across various systems.
Choosing the Right Polyurethane Guide Rollers for Your Application
Selecting the appropriate polyurethane guide rollers for your specific application is crucial for ensuring optimal performance, durability, and efficiency in your operations. The process involves considering a variety of factors that can affect the roller’s suitability and effectiveness. Here, we outline essential guidelines for choosing the right polyurethane roller and provide tips on sourcing high-quality polyurethane guide rollers from reputable suppliers.
Guidelines for Selecting Polyurethane Rollers
When choosing polyurethane guide rollers, it’s important to consider several key factors to ensure they meet the demands of your application:
- Load Capacity: Assess the maximum load the rollers will need to support, ensuring the selected polyurethane material and design can withstand the operational stresses.
- Operating Environment: Consider environmental factors such as exposure to chemicals, temperature extremes, and moisture, which can affect the roller’s material composition and durability.
- Speed of Operation: Determine the operational speed requirements, as higher speeds may necessitate rollers with specialized bearings and dynamic balancing.
- Compatibility with Existing Systems: Ensure the rollers are compatible with your current machinery, including size, mounting configurations, and interface requirements.
- Abrasion Resistance: For applications involving rough surfaces or materials, choose rollers with high abrasion resistance to prolong their lifespan.
- Chemical Compatibility: Select a polyurethane formulation that is resistant to any chemicals or solvents present in the operating environment.
- Maintenance Requirements: Consider rollers designed for easy maintenance and replacement to minimize downtime and operational costs.
- Customization Options: Look for suppliers who offer customization in terms of hardness, size, and additional features to precisely meet your application needs.
Tips on Sourcing Polyurethane Guide Rollers
Finding the right supplier for polyurethane guide rollers is as important as selecting the roller itself. Here are some tips to help you identify quality manufacturers:
- Research Suppliers: Start with a comprehensive search for suppliers specializing in polyurethane rollers. Online directories and industry associations can be valuable resources.
- Check Experience and Reputation: Look for companies with a proven track record and positive reviews from customers in similar industries.
- Assess Customization Capabilities: Ensure the supplier offers the customization options you need, from material formulations to specific design requirements.
- Inquire About Material Quality: Ask about the types of polyurethane used and their suitability for different applications and environments.
- Evaluate Manufacturing Processes: Quality manufacturers will have advanced manufacturing processes in place, including precision molding and machining capabilities.
- Request Samples: If possible, obtain samples of the rollers to assess their quality and performance firsthand.
- Consider Lead Times and Scalability: Choose a supplier that can meet your lead times and scale production up or down based on your needs.
- Look for Comprehensive Support: A quality supplier should offer not just products but also technical support, from selection guidance to after-sales service.
- Compare Pricing: While cost should not be the sole deciding factor, compare pricing among suppliers to ensure you are getting value for your investment.
By carefully considering these factors and tips, you can select the right polyurethane guide rollers for your application and source them from a supplier that meets your quality, customization, and service requirements. This approach will help ensure the longevity and efficiency of your operations, contributing to overall productivity and success.
FAQs about Polyurethane Guide Rollers
Polyurethane rollers offer a multitude of advantages over rollers made from other materials such as rubber, metal, or plastic, making them a preferred choice in a wide range of industrial applications. One of the primary benefits of polyurethane is its exceptional durability. This material is designed to withstand significant wear and tear, allowing the rollers to maintain their integrity and functionality over extended periods, even under harsh operating conditions.
Moreover, polyurethane possesses a high load-bearing capacity, making it suitable for heavy-duty applications where the rollers must support substantial weights without deforming or breaking. This material also boasts excellent abrasion resistance, which is crucial in environments where the rollers are exposed to rough surfaces or materials that could otherwise cause damage.
Another significant advantage is the chemical resistance of polyurethane. It can withstand exposure to various chemicals, oils, and solvents, making it ideal for use in industries where such substances are prevalent. Additionally, polyurethane rollers can be customized to a specific hardness level, allowing for a tailored approach to meet the unique needs of each application, whether that requires a softer touch for delicate materials or a firmer roller for more robust operations.
Polyurethane’s versatility extends to its environmental resistance, with the ability to perform in a wide range of temperatures and conditions, including exposure to UV light and moisture. This makes polyurethane rollers suitable for both indoor and outdoor applications. Lastly, the material’s noise-dampening properties contribute to a quieter operation, which can be particularly beneficial in settings where reducing noise pollution is a priority.
The manufacturing process of polyurethane rollers involves several key steps, each crucial to ensuring the final product meets the required specifications and quality standards. Initially, the process begins with the design phase, where precise dimensions and specifications of the roller are determined based on its intended application. This phase often involves computer-aided design (CAD) software to model the roller accurately.
Following the design phase, a mold is created to match the roller’s specifications. This mold can be made from various materials, including aluminum or steel, depending on the complexity and precision required. The choice of mold material also depends on the production volume and the specific properties desired in the final roller.
Once the mold is prepared, the polyurethane material is mixed and poured into the mold. The composition of the polyurethane mix can be adjusted to achieve different properties in the final product, such as hardness, resilience, and chemical resistance. This customization is one of the key advantages of using polyurethane, as it allows for a high degree of flexibility in the manufacturing process.
After the polyurethane is poured, the roller undergoes a curing process, where it is left to solidify. The curing time can vary depending on the thickness of the roller and the specific polyurethane formulation used. In some cases, post-curing treatments may be applied to enhance certain properties of the roller, such as its strength or chemical resistance.
The final steps in the manufacturing process include demolding, where the roller is removed from the mold, and any necessary finishing touches, such as machining or coating, are applied. Quality control measures are also implemented at this stage to ensure the roller meets all specified requirements. The result is a high-quality polyurethane roller, customized to the specific needs of its application, ready for use in a wide range of industrial settings.
Last Updated on April 12, 2024 by Jordan Smith
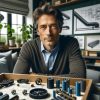
Jordan Smith, a seasoned professional with over 20 years of experience in the conveyor system industry. Jordan’s expertise lies in providing comprehensive solutions for conveyor rollers, belts, and accessories, catering to a wide range of industrial needs. From initial design and configuration to installation and meticulous troubleshooting, Jordan is adept at handling all aspects of conveyor system management. Whether you’re looking to upgrade your production line with efficient conveyor belts, require custom conveyor rollers for specific operations, or need expert advice on selecting the right conveyor accessories for your facility, Jordan is your reliable consultant. For any inquiries or assistance with conveyor system optimization, Jordan is available to share his wealth of knowledge and experience. Feel free to reach out at any time for professional guidance on all matters related to conveyor rollers, belts, and accessories.