Integrating Power and Free Roller Conveyor into Modern Industries
Conveyor systems are integral components of material handling processes, designed to efficiently move items from one location to another within industrial and commercial environments. Among the various types of conveyor systems, Power and Free Roller Conveyors stand out as a versatile solution, offering unparalleled flexibility and efficiency. These systems combine the simplicity of traditional roller conveyors with the advanced capabilities of overhead chain conveyors, allowing for controlled movement of goods across complex routes. The unique design of Power and Free Roller Conveyors enables the simultaneous handling of diverse products with varying sizes and weights, making them an ideal choice for industries seeking to optimize their material handling operations while accommodating future growth and changes in production demands.
What is a Power and Free Roller Conveyor?
A Power and Free Roller Conveyor is an advanced material handling system that integrates the efficiency of powered conveyor belts with the flexibility of free roller conveyors. This hybrid system is designed to provide optimal control over the movement and positioning of goods across manufacturing, assembly, and distribution centers. Unlike traditional conveyor systems that move at a constant speed and direction, a power and free roller conveyor offers the ability to start, stop, accumulate, and divert products through complex pathways without interrupting the flow of other items on the line.
Comparison with Traditional Conveyor Systems
The power and free roller conveyor system stands out for its unparalleled flexibility and control over material handling processes. This system is particularly beneficial in environments where production workflows are subject to change, requiring the conveyor layout to adapt without significant downtime or reconfiguration costs. Its ability to efficiently manage a diverse range of product types and sizes while offering precise control over each item’s movement makes it a superior choice for industries looking to enhance their operational efficiency and productivity.
Key Features of Power and Free Roller Conveyors
Power and Free Roller Conveyors are renowned for their versatility and adaptability in various industrial environments, making them a preferred choice for complex material handling needs. These systems offer several key features that distinguish them from traditional conveyor solutions.
Versatility and Adaptability
The design of a Power and Free Roller Conveyor allows it to be highly versatile and adaptable, catering to a wide range of industrial applications. Here are five specific examples of each:
Versatility:
- Automotive Assembly Lines: Can handle different car models and parts on the same line, adjusting routes as needed.
- Food and Beverage Packaging: Adapts to various packaging sizes and shapes, ensuring gentle handling of delicate products.
- Pharmaceuticals: Meets strict cleanliness standards while accommodating diverse product lines.
- Aerospace Manufacturing: Manages large, heavy components with precision, moving them through assembly and inspection processes.
- E-commerce Fulfillment Centers: Sorts and routes a vast array of product types and sizes, optimizing order fulfillment.
Adaptability:
- Layout Changes: Easily reconfigured to accommodate changes in manufacturing processes or plant layouts.
- Production Volume Changes: Scalable to handle increases or decreases in production volume without significant downtime.
- Product Variability: Can adjust to handle new product types or changes in product dimensions and weights.
- Process Integration: Integrates seamlessly with other manufacturing systems, such as robotic workstations or inspection stations.
- Environmental Conditions: Designed to operate in various conditions, including extreme temperatures, cleanrooms, or hazardous environments.
Automatic Stopping and Starting of Parts
A Power and Free Roller Conveyor system is equipped with sophisticated control systems that allow for the automatic stopping and starting of parts. This feature is crucial for processes that require precise timing or positioning, such as assembly operations, quality inspections, and loading/unloading stations.
Load Handling Capabilities
These conveyors are designed to handle a wide range of load capacities, from light components a few grams in weight to heavy loads several tons heavy. This flexibility ensures that a single system can accommodate the entire production line’s needs, from small parts to large assemblies.
Variable Chain Speeds and High-Speed Indexing
Power and Free Roller Conveyors offer variable chain speeds and high-speed indexing, providing optimal control over product movement and positioning. Here are five specific examples of each:
Variable Chain Speeds:
- Assembly Lines: Adjusts speed for different assembly stages, allowing more time for complex tasks.
- Paint Lines: Varies speeds to ensure proper drying times between coats.
- Cooling Zones: Slows down to allow products to cool after heat treatments.
- Inspection Stations: Reduces speed to allow detailed inspections without stopping the line.
- Packaging Areas: Modulates speed based on packaging operations’ complexity and throughput requirements.
High-Speed Indexing:
- Automated Picking Systems: Quickly moves to the next pick location, increasing throughput.
- Machine Feeding: Delivers parts to machines at high speeds, reducing cycle times.
- Sorting Systems: Rapidly sorts products into different lanes for further processing or shipping.
- Buffering Zones: Quickly clears products from a production area to a temporary storage or buffering zone.
- Load/Unload Stations: Increases efficiency in loading and unloading areas by quickly positioning items for pick-up or placement.
The combination of these key features makes Power and Free Roller Conveyors an essential component of modern manufacturing and distribution facilities, offering unparalleled efficiency, flexibility, and control.
How Power and Free Roller Conveyors Work
The operation of a Power and Free Roller Conveyor is a marvel of modern engineering, combining the efficiency of powered conveyors with the flexibility of non-powered systems. This unique system is characterized by its dual-track design, consisting of a “power” track and a “free” track, which work together to move materials through a facility with precision and versatility.
Dual-Track System
- Power Track: This is the component of the conveyor that provides the motive force. It typically consists of a chain driven by motors, which runs continuously along the path of the conveyor. The power track is responsible for the movement of the entire system, propelling trolleys attached to the free track.
- Free Track: Running parallel to the power track, the free track carries the trolleys that directly support and transport the loads. Unlike the power track, the free track does not move on its own. Instead, it is moved by the action of the power track, allowing the trolleys to either follow the power track’s motion or remain stationary, depending on the operational requirements.
Role of “Pusher Dogs”
Pusher dogs are critical components that link the power track to the trolleys on the free track. These mechanisms engage and disengage with the trolleys to move them along the conveyor track.
- Engagement for Movement: Pusher dogs engage with a trolley to move it along the conveyor, providing the force necessary for its motion.
- Disengagement for Accumulation: When products need to be accumulated, pusher dogs disengage, allowing trolleys to stop and collect products without stopping the entire conveyor system.
- Controlled Speed Regulation: By engaging and disengaging at specific intervals, pusher dogs can regulate the speed of the trolleys, ensuring that products move at the optimal speed for processing.
- Directional Control: Pusher dogs can engage trolleys in a way that allows for directional changes, facilitating the movement of products through horizontal and vertical turns within the system.
- Sequencing and Spacing: They play a crucial role in sequencing and spacing products on the conveyor, engaging with trolleys to ensure proper spacing between products for processing and inspection.
Accumulation and Separation of Loads
Power and Free Roller Conveyors excel in their ability to accumulate and separate loads efficiently. This is achieved through the controlled engagement and disengagement of pusher dogs with the trolleys, allowing for the temporary storage of products on the conveyor line without halting the movement of the entire system. This feature is particularly useful in processes that require a buffering of products before the next stage of manufacturing or packaging.
Incorporation of Horizontal and Vertical Turns
The flexibility of Power and Free Roller Conveyors is further demonstrated in their ability to incorporate both horizontal and vertical turns. This allows the conveyor system to navigate complex facility layouts, moving products across different levels and around obstacles. The system’s design ensures that despite these turns, the flow of products remains smooth and uninterrupted, enhancing the efficiency of material handling operations.
Power and Free Roller Conveyors offer a sophisticated solution for material handling, combining the benefits of powered and non-powered systems to provide flexibility, control, and efficiency in moving products through manufacturing and distribution processes.
Types of Power and Free Roller Conveyors
Power and Free Roller Conveyors are versatile systems used in a variety of industrial settings to transport materials and products efficiently. These systems can be categorized into several types, each with its unique features and applications. Below, we explore the different types of Power and Free Roller Conveyors, providing specific examples of their uses.
I-Beam Power and Free
I-Beam Power and Free Conveyors are characterized by their robust I-beam construction, making them suitable for heavy-duty applications.
- Automotive Assembly Lines: Used for transporting car bodies through various stages of assembly.
- Heavy Machinery Manufacturing: Ideal for moving large and heavy machine parts through the production process.
- Foundries: Employed in the harsh environments of foundries for moving castings and molds.
- Shipbuilding: Utilized in shipyards for transporting large sections of ships.
- Aerospace: Used for moving aerospace components, such as wings and fuselage sections, through assembly.
Enclosed Track Power and Free
Enclosed Track Power and Free Conveyors feature a track that is enclosed, protecting the chain and trolleys from dust and debris. This design is well-suited for cleaner environments.
- Pharmaceutical Manufacturing: Ideal for environments requiring cleanliness and precision.
- Food and Beverage Processing: Used in food production lines where hygiene is paramount.
- Electronics Assembly: Suitable for transporting delicate electronic components.
- Packaging Lines: Employed in packaging facilities for moving products through various packaging stages.
- Automated Warehouses: Used for efficient material handling and storage retrieval processes.
Inverted I-Beam Power Free
Inverted I-Beam Power Free Conveyors are similar to the standard I-Beam but are designed with the track located below the load. This configuration is beneficial for certain applications:
- Automotive Paint Shops: Allows for easy access to the underside of car bodies for painting and coating.
- Clean Room Applications: Keeps the conveyor mechanism away from the clean area to prevent contamination.
- Assembly Lines: Provides workers with unobstructed access to the sides and top of the product.
- Inspection and Testing: Facilitates easy access for inspecting and testing products during manufacturing.
- Material Handling: Used in various industries for efficient material transport while allowing for easy loading and unloading.
Over-Under and Tandem Configurations
Over-Under and Tandem configurations offer flexibility in material handling by utilizing space efficiently and allowing for simultaneous processing:
- Sequential Processing: In tandem configurations, products can be processed in sequence without manual intervention.
- Space Saving: Over-Under configurations maximize vertical space, ideal for facilities with limited floor space.
- Continuous Flow: Allows for a continuous loop of products, enhancing efficiency in production lines.
- Sorting and Distribution: Facilitates the sorting and distribution of products to different areas of a facility.
- Buffer Storage: Provides temporary storage of products as they move through the production process.
Special Mention of 24v Roller Conveyor Systems
24v Roller Conveyor Systems deserve special mention for their precise control over product movement. These systems use individually powered rollers, allowing for:
- Accurate Positioning: Precise control over the position of products on the conveyor.
- Gentle Handling: Ideal for delicate products that require careful handling.
- Energy Efficiency: Power is used only where and when needed, reducing energy consumption.
- Modularity: Easily reconfigurable to meet changing production needs.
- Integration: Can be seamlessly integrated with other conveyor types for a comprehensive material handling solution.
Each type of Power and Free Roller Conveyor offers unique advantages, making them suitable for a wide range of industrial applications. From heavy-duty manufacturing to delicate product handling, these systems provide the flexibility and efficiency required to meet the demands of modern production environments.
Advantages of Power and Free Roller Conveyors
Power and Free Roller Conveyors offer a multitude of advantages that make them a preferred choice for a wide range of industrial applications. Their design combines the efficiency of powered conveyors with the flexibility of manual systems, providing a solution that is both durable and reliable. Below, we delve into the specific benefits of these systems, highlighting examples that illustrate their high volume capacity, durability, reliability, reduced malfunctions due to fewer motors and moving parts, and flexibility in installation.
High Volume, Durability, and Reliability
- Automotive Manufacturing: Power and Free Roller Conveyors handle the high-volume production demands of the automotive industry, moving parts and assemblies through various stages of manufacturing with durability and reliability.
- Aerospace Industry: These conveyors transport large and heavy aerospace components, demonstrating their durability and reliability in handling high-value items.
- Heavy Machinery Production: The conveyors’ robust design supports the weight and volume of heavy machinery parts, ensuring reliable transport through the production process.
- Food Processing Plants: In environments where cleanliness and efficiency are paramount, these conveyors prove their reliability by operating smoothly in high-volume food processing operations.
- Pharmaceuticals: The conveyors’ reliability is crucial in the pharmaceutical industry, where precision and volume are key to maintaining production schedules and compliance with health regulations.
Fewer Motors and Moving Parts for Reduced Malfunctions
- Reduced Maintenance Needs: With fewer motors and moving parts, Power and Free Roller Conveyors require less maintenance, minimizing downtime in critical production environments.
- Lower Operational Costs: The reduction in moving parts leads to fewer wear-and-tear replacements and repairs, directly impacting operational costs positively.
- Increased System Longevity: Fewer motors and moving parts mean there are fewer points of failure, which extends the lifespan of the conveyor system.
- Simplified Troubleshooting: When malfunctions do occur, the simplicity of the system makes it easier to diagnose and rectify issues, reducing the time and expertise needed for troubleshooting.
- Energy Efficiency: Operating with fewer motors, these conveyors can be more energy-efficient, contributing to lower energy costs and a smaller carbon footprint.
Flexibility in Installation: Floor-Supported or Above-Supported Structures
- Floor-Supported Installation in Manufacturing Plants: Allows for easy integration into existing production lines without the need for extensive overhead structures, ideal for facilities with limited ceiling height or heavy load requirements.
- Above-Supported Installation in Warehouses: Maximizes floor space by utilizing overhead space for conveyor paths, essential for storage and sorting operations in warehouses.
- Flexible Layouts in Automotive Assembly Lines: The ability to choose between floor-supported and above-supported installations allows for customized layouts that can evolve with changing production needs.
- Adaptability in Food Processing Facilities: Depending on hygiene requirements and floor space utilization, food processors can choose the installation method that best suits their operational needs.
- Versatile Configuration Options for Distribution Centers: The flexibility to install conveyors either on the floor or overhead enables distribution centers to optimize material handling paths and improve efficiency.
The advantages of Power and Free Roller Conveyors, including their capacity for handling high volumes, their durability and reliability in various industrial settings, the reduced likelihood of malfunctions due to fewer motors and moving parts, and their flexible installation options, make them an invaluable asset in modern manufacturing and distribution operations. These benefits underscore the conveyors’ role in enhancing productivity, reducing costs, and improving operational efficiency across a wide range of industries.
Considerations for Choosing a Power and Free Roller Conveyor
When selecting a Power and Free Roller Conveyor for your material handling needs, several critical considerations come into play. These considerations range from cost and safety to the system’s suitability for specific environments and applications. Understanding these factors can help ensure that you choose the most appropriate conveyor system for your operations.
Cost Considerations and Comparison with Other Conveyor Types
The table highlights that while Power and Free Roller Conveyors may have a higher initial cost compared to traditional roller and belt conveyors, they offer superior flexibility and suitability for complex layouts. These factors can lead to long-term savings and efficiency gains that offset the initial investment.
Safety and Installation Considerations
When implementing a Power and Free Roller Conveyor, safety and installation are paramount.
Safety Considerations:
- Emergency Stops: Ensure that emergency stop buttons are accessible along the conveyor path.
- Guardrails: Install guardrails where necessary to prevent accidents and ensure load stability.
- Warning Signs: Place warning signs at appropriate locations to alert workers to potential hazards.
- Regular Maintenance: Schedule regular maintenance checks to prevent malfunctions that could lead to safety incidents.
- Training: Provide comprehensive training for operators and maintenance personnel on safe operation and emergency procedures.
Installation Considerations:
- Space Requirements: Assess the available space to ensure the conveyor system fits without obstructing workflows.
- Integration with Existing Systems: Consider how the new conveyor will integrate with existing material handling systems.
- Load Requirements: Evaluate the types of materials and their weights to ensure the conveyor system can handle the expected loads.
- Future Scalability: Plan for future expansion or reconfiguration needs to ensure the system can adapt to changing operational requirements.
- Professional Installation: Utilize experienced professionals for installation to ensure the system is set up correctly and safely.
Suitability for Harsh Environments and Special Applications
Power and Free Roller Conveyors are particularly well-suited for harsh environments and special applications.
- Paint Ovens: Their design can withstand high temperatures, making them suitable for conveying parts through paint drying ovens.
- Food-Safe Environments: Certain models are designed with materials and coatings that meet food safety standards, making them suitable for food processing plants.
- Chemical Exposure: Resistant to corrosion and chemical damage, these conveyors can be used in chemical manufacturing or processing plants.
- Clean Rooms: Some conveyors are designed to operate in cleanroom environments, with minimal particle generation and easy cleaning.
- Outdoor Use: With weather-resistant options available, these conveyors can be used in outdoor applications, such as in lumber yards or shipping docks.
Choosing a Power and Free Roller Conveyor involves careful consideration of various factors, including cost, safety, installation requirements, and the specific needs of your operation. By thoroughly evaluating these considerations, you can select a conveyor system that enhances efficiency, safety, and productivity in your material handling processes.
R
Manufacturers and Buying Guide for Power and Free Roller Conveyor Systems
When it comes to enhancing your material handling processes with a Power and Free Roller Conveyor, selecting the right system and manufacturer is crucial. This guide provides an overview of leading manufacturers, tips for choosing the best system for your needs, and advice on where to find these conveyors for sale.
Overview of Leading Power and Free Roller Conveyor Manufacturers
Several manufacturers stand out in the production of Power and Free Roller Conveyors, each with its unique strengths:
- Daifuku Wynright: Renowned for their innovative material handling solutions, Daifuku Wynright offers a range of Power and Free Roller Conveyors designed for efficiency and reliability in various industrial applications.
- Dematic: With a global presence, Dematic provides versatile conveyor systems, including Power and Free Roller Conveyors, tailored to meet the specific needs of their clients.
- Hytrol Conveyor Company: Hytrol is known for its comprehensive range of conveyor systems, including customizable Power and Free Roller Conveyors that cater to a wide array of material handling requirements.
- Pacline Overhead Conveyors: Specializing in overhead conveyor systems, Pacline offers Power and Free Roller Conveyors that are ideal for applications requiring the efficient use of vertical space.
- Richards-Wilcox: This company’s Power and Free Roller Conveyors are well-regarded for their durability and adaptability, making them suitable for a broad spectrum of industrial environments.
Tips on Selecting the Best Power and Free Roller Conveyor for Your Needs
Choosing the right Power and Free Roller Conveyor involves several considerations to ensure the system meets your operational requirements:
- Assess Your Load Requirements: Consider the size, weight, and variety of the items you need to transport. Ensure the system you choose can handle your current and future load requirements.
- Consider Your Space Constraints: Evaluate the available space in your facility. Some systems are more flexible and can navigate tight spaces or complex layouts more effectively.
- Evaluate System Flexibility: Look for systems that offer modularity and flexibility, allowing for future reconfigurations as your business needs change.
- Understand Maintenance Needs: Consider the maintenance requirements of the system. Systems with fewer moving parts typically require less maintenance and have lower long-term costs.
- Compare Cost vs. Value: While initial cost is an important consideration, also evaluate the long-term value the system will bring to your operations in terms of efficiency, scalability, and reliability.
Where to Find Power and Free Roller Conveyors for Sale
Power and Free Roller Conveyors can be purchased from a variety of sources:
- Manufacturer Direct Sales: Contacting manufacturers directly often provides access to the latest models and customization options.
- Industrial Equipment Distributors: Many distributors carry a range of conveyor systems from various manufacturers, offering the advantage of comparing different brands.
- Online Marketplaces: Websites specializing in industrial equipment can be a good source for new and used Power and Free Roller Conveyors.
- Trade Shows and Expos: These events offer the opportunity to see the latest conveyor technologies in person and discuss your needs directly with manufacturers.
- Referrals: Ask for recommendations from other businesses in your industry. They can provide valuable insights into the systems they use and where they purchased them.
Selecting the right Power and Free Roller Conveyor system and manufacturer is a critical decision that can significantly impact the efficiency and productivity of your operations. By considering your specific needs, evaluating the offerings of leading manufacturers, and following the tips provided, you can make an informed decision that will serve your business well for years to come.
FAQs About Power and Free Roller Conveyor
A Power and Free Conveyor is an advanced type of overhead conveyor system that offers unparalleled flexibility and control in material handling. Unlike traditional conveyor systems, Power and Free conveyors combine the benefits of both powered and non-powered conveyors. They consist of two tracks: one powered, where trolleys are propelled by a chain, and a free track that allows individual trolleys to disengage from the powered chain and move independently. This unique feature enables the simultaneous transport of materials at varying speeds, accumulation of products, and even routing to different destinations without stopping the entire system. Ideal for complex manufacturing environments, Power and Free conveyors are highly adaptable to changes in production processes, making them a preferred choice for industries requiring high levels of customization and efficiency in their operations.
Powered and Unpowered Roller Conveyors differ primarily in their mechanism of moving materials along the conveyor line. Powered Roller Conveyors are equipped with motors that drive the rollers, propelling materials forward without the need for manual effort. This automation makes them suitable for heavy loads or long distances where manual transportation would be inefficient or impractical. On the other hand, Unpowered Roller Conveyors, also known as Gravity Roller Conveyors, rely on gravity or manual force to move items. They are typically inclined or rely on operators to push items along the rollers. Unpowered conveyors are simpler and more cost-effective but are best suited for lighter loads and shorter distances. The choice between the two depends on the specific requirements of the operation, including load weight, distance, speed, and the level of automation desired.
A Power Roller Conveyor is a type of conveyor system where individual rollers are powered by motors, enabling the automated movement of goods along the conveyor belt. These conveyors are designed to handle a wide range of product sizes and weights, making them versatile for various applications in manufacturing, distribution, and packaging industries. Power Roller Conveyors can be customized with different roller sizes, materials, and configurations to meet specific operational needs. They are particularly useful in settings that require controlled movement, accumulation, and sorting of products, offering efficiency and reliability in material handling processes.
Roller Conveyors are categorized based on their functionality and the method of propulsion. The primary types include:
Gravity Roller Conveyors: Utilize the force of gravity to move items along the conveyor. Best suited for lightweight products and require a slight incline or manual assistance to facilitate movement.
Powered Roller Conveyors: Employ motors to power the rollers, automating the movement of goods. Ideal for heavier loads and longer distances, providing consistent and controlled product movement.
Live Roller Conveyors: A subtype of powered conveyors where each roller is powered, allowing for the accumulation of products without the need for additional systems.
Flexible Roller Conveyors: Designed for versatility and portability, these conveyors can be expanded, curved, and contracted, accommodating various spaces and applications.
Line Shaft Roller Conveyors: Powered by a shaft beneath the rollers, these conveyors are suitable for lightweight to medium-weight products and allow for easy accumulation.
Each type of Roller Conveyor serves distinct purposes and is chosen based on the specific requirements of the material handling process, including the nature of the products, the required speed of transport, and the layout of the facility.
Last Updated on August 5, 2024 by Jordan Smith
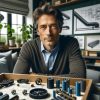
Jordan Smith, a seasoned professional with over 20 years of experience in the conveyor system industry. Jordan’s expertise lies in providing comprehensive solutions for conveyor rollers, belts, and accessories, catering to a wide range of industrial needs. From initial design and configuration to installation and meticulous troubleshooting, Jordan is adept at handling all aspects of conveyor system management. Whether you’re looking to upgrade your production line with efficient conveyor belts, require custom conveyor rollers for specific operations, or need expert advice on selecting the right conveyor accessories for your facility, Jordan is your reliable consultant. For any inquiries or assistance with conveyor system optimization, Jordan is available to share his wealth of knowledge and experience. Feel free to reach out at any time for professional guidance on all matters related to conveyor rollers, belts, and accessories.