ITOH DENKI AC Power Moller Rollers Unveiled
Itoh Denki stands at the forefront of innovation in motorized rollers, particularly renowned for its expertise in power moller rollers. With decades of experience and a reputation for excellence, Itoh Denki has revolutionized conveyor systems worldwide. Power moller rollers, the cornerstone of their offerings, embody efficiency, reliability, and precision. Understanding the concept of power moller rollers is crucial for grasping their transformative impact on material handling processes. Moreover, the comprehensive Power Moller Catalogue provided by Itoh Denki serves as a valuable resource for engineers and designers, enabling them to select the most suitable rollers for their conveyor systems. As we delve deeper into the intricacies of power moller rollers, it becomes evident why Itoh Denki remains a trusted name in the industry.
Unveiling the Itoh Denki Power Moller Roller Catalogue
Overview of Available Power Moller Roller Models
Itoh Denki offers a diverse range of power moller roller models tailored to various applications:
- PM486: This model features a 24-inch between-frame dimension and is ideal for medium-duty applications such as parcel handling and distribution centers.
- PM500FE: With a robust design capable of handling loads up to 300kg, the PM500FE is perfect for heavy-duty applications in manufacturing and automotive industries.
- PM360: Designed for high-speed conveying, the PM360 boasts a compact form factor and is suitable for industries requiring rapid material handling, such as food processing and pharmaceuticals.
- PM250H: Featuring a corrosion-resistant construction, the PM250H is specially designed for use in harsh environments such as outdoor applications or facilities with high moisture levels.
- PM200S: This model offers exceptional flexibility with adjustable speed settings, making it suitable for dynamic environments where conveying speeds may vary, such as assembly lines and sortation systems.
Highlighting Key Features and Capabilities
The power moller rollers from Itoh Denki come equipped with advanced features to enhance performance and efficiency:
- Integrated Motor: Each roller incorporates a high-efficiency motor directly into the roller tube, eliminating the need for external drive mechanisms and reducing maintenance requirements.
- Precision Control: With precise speed and direction control capabilities, Itoh Denki power moller rollers ensure accurate product handling and positioning on the conveyor system.
- Quiet Operation: The rollers operate quietly, minimizing noise pollution in the workplace and providing a conducive environment for employees.
- Modular Design: The modular design of the power moller rollers allows for easy installation, maintenance, and scalability, enabling seamless integration into existing conveyor systems.
- Energy Efficiency: Utilizing advanced motor technology, Itoh Denki power moller rollers are energy-efficient, helping to reduce operational costs and environmental impact.
Applications and Industries Served
Itoh Denki power moller rollers find applications across a wide range of industries, including:
- E-commerce: Power moller rollers facilitate the efficient sorting and distribution of packages in e-commerce fulfillment centers.
- Manufacturing: These rollers are used in assembly lines for transporting components between workstations, increasing production efficiency.
- Logistics: Power moller rollers play a crucial role in logistics centers for loading and unloading goods from trucks and containers, optimizing supply chain operations.
- Food and Beverage: With sanitary design options available, power moller rollers are suitable for conveying food and beverage products in processing and packaging facilities.
- Airport Baggage Handling: Itoh Denki power moller rollers are employed in airport baggage handling systems for smooth and reliable luggage transport, ensuring timely departures and arrivals.
What is the Dynamics of Power Moller Roller
Differentiating Power Rollers from Traditional Conveyors
Power moller rollers revolutionize material handling with their distinct characteristics compared to traditional conveyors:
- Integrated Motor: Unlike traditional conveyors that rely on external drive mechanisms, power moller rollers feature an internal motor for autonomous operation.
- Variable Speed Control: Power moller rollers offer precise speed control, allowing for adjustable conveying speeds to accommodate different material handling requirements.
- Modular Design: Power moller rollers can be easily integrated into conveyor systems, offering flexibility for layout modifications and system expansions.
- Reduced Maintenance: Traditional conveyors often require frequent maintenance due to wear and tear on external components, while power moller rollers have a maintenance-free design with life-long lubrication.
- Quiet Operation: Power moller rollers operate quietly, minimizing noise pollution in the workplace compared to traditional conveyors with noisy external drive systems.
The Role of DC Rollers in Modern Conveyor Systems
DC rollers play a crucial role in enhancing the efficiency and flexibility of modern conveyor systems:
- Energy Efficiency: DC rollers, powered by low-voltage direct current, consume less energy compared to traditional AC-powered rollers, resulting in lower operational costs.
- Precise Control: DC rollers offer precise speed and torque control, enabling accurate positioning and handling of items on the conveyor system.
- Compact Design: DC rollers feature a compact and lightweight design, making them ideal for applications where space is limited or weight restrictions apply.
- Versatility: DC rollers are versatile and can be integrated into various conveyor configurations, including straight sections, curves, merges, and diverges, to meet specific material handling needs.
- Compatibility with Automation: DC rollers seamlessly integrate with automation systems, allowing for seamless communication and control in automated material handling processes.
Advantages of 24VDC Powered Roller Conveyors
24VDC powered roller conveyors offer numerous advantages over traditional conveyor systems:
- Reduced Energy Consumption: 24VDC powered roller conveyors consume less energy compared to their AC-powered counterparts, resulting in cost savings and reduced environmental impact.
- Flexible Layouts: With individual motorized rollers, 24VDC powered roller conveyors offer flexibility in layout design, allowing for easy reconfiguration and adaptation to changing production needs.
- Quiet Operation: 24VDC powered roller conveyors operate quietly, creating a more comfortable and productive work environment compared to traditional conveyor systems with noisy drive mechanisms.
- Maintenance Efficiency: The modular design of 24VDC powered roller conveyors simplifies maintenance tasks, as individual rollers can be easily replaced or serviced without affecting the entire conveyor system.
- Enhanced Safety: With decentralized control and built-in safety features, such as overload protection and emergency stop capabilities, 24VDC powered roller conveyors contribute to a safer working environment for operators.
Leveraging the Itoh Denki Power Moller Roller Manual for Optimal Performance
Importance of Proper Installation and Maintenance
Proper installation and maintenance are crucial for maximizing the performance and longevity of power moller rollers:
- Alignment: Ensuring proper alignment during installation prevents premature wear and tear on power moller roller components, maintaining optimal performance.
- Lubrication: Regular lubrication of bearings and gears according to the manufacturer’s guidelines reduces friction and extends the lifespan of power moller rollers.
- Cleaning: Keeping power moller rollers free from debris and contaminants prevents damage to internal components and ensures smooth operation.
- Inspection: Regular inspection of power moller rollers helps identify potential issues early, allowing for timely repairs and preventing costly downtime.
- Training: Providing adequate training to maintenance personnel on proper installation and maintenance procedures ensures consistent performance and minimizes the risk of operational issues.
Utilizing the Manual for Troubleshooting and Optimization
The Itoh Denki manual serves as a comprehensive resource for troubleshooting and optimizing the performance of power moller rollers:
- Diagnostic Guidelines: The manual provides step-by-step instructions for diagnosing common issues with power moller rollers, such as motor malfunctions or conveyor misalignment.
- Troubleshooting Tips: Detailed troubleshooting tips help identify the root cause of performance issues and guide users in implementing corrective actions.
- Optimization Techniques: The manual includes optimization techniques to enhance the efficiency and reliability of power moller rollers, such as adjusting speed settings or optimizing conveyor layout.
- Safety Precautions: Safety precautions outlined in the manual ensure that troubleshooting and maintenance procedures are performed safely, minimizing the risk of accidents or injuries.
- Technical Support: In addition to written instructions, the manual may also provide contact information for technical support, allowing users to seek assistance from qualified professionals when needed.
Maximizing the Lifespan of Itoh Denki Rollers
Maximizing the lifespan of Itoh Denki rollers requires proactive maintenance and adherence to best practices:
- Regular Inspection: Conducting routine inspections helps identify potential issues early, allowing for timely repairs and preventing premature failure of power moller rollers.
- Preventive Maintenance: Implementing a preventive maintenance schedule, including tasks such as lubrication and alignment checks, prolongs the lifespan of power moller rollers and reduces the risk of unexpected breakdowns.
- Training Programs: Providing training programs for maintenance personnel ensures that proper maintenance procedures are followed, optimizing the performance and longevity of power moller rollers.
- Genuine Parts: Using genuine Itoh Denki replacement parts ensures compatibility and quality, preserving the integrity of power moller rollers and maximizing their lifespan.
- Documentation: Keeping detailed records of maintenance activities and equipment history allows for better tracking of power moller roller performance and facilitates informed decision-making regarding maintenance and repairs.
Customization Options with Itoh Denki Power Moller Rollers
What is Tailored Solutions for Specific Applications
Itoh Denki offers tailored solutions to meet the unique requirements of various applications using power moller rollers:
- Parcel Sorting: Customized power moller rollers with integrated barcode scanning capabilities streamline parcel sorting processes in distribution centers.
- Food Processing: Sanitary design options ensure compliance with food safety regulations and prevent contamination in food processing facilities.
- Automotive Manufacturing: Power moller rollers with specialized coatings withstand harsh chemicals and oils commonly found in automotive manufacturing environments.
- Pharmaceutical Packaging: Custom roller configurations accommodate delicate pharmaceutical products, ensuring gentle handling and precise positioning on the conveyor system.
- E-commerce Fulfillment: Power moller rollers with built-in weight sensors enable automated sorting based on package weight, enhancing efficiency in e-commerce fulfillment operations.
Highlighting Available Customization Features
Itoh Denki offers a range of customization features to tailor power moller rollers to specific application needs:
- Roller Diameter: Custom roller diameters are available to accommodate different load sizes and weight capacities.
- Tube Length: Power moller rollers can be customized with varying tube lengths to fit specific conveyor layouts and space constraints.
- Motor Type: Customers can choose from AC or DC motor options based on power requirements and operational preferences.
- Speed Control: Variable speed control allows for adjustable conveying speeds to optimize material handling processes.
- Special Coatings: Optional coatings such as rubber lagging or polyurethane covers provide enhanced traction and durability for specific applications.
Addressing Unique Industry Requirements
Itoh Denki understands the unique requirements of different industries and offers customized solutions for:
- Retail Warehousing: Power moller rollers with anti-static properties prevent static buildup and protect sensitive electronic products during handling and storage.
- Textile Manufacturing: Custom roller materials and surface treatments prevent fabric snags and ensure smooth material flow in textile production facilities.
- Chemical Processing: Corrosion-resistant power moller rollers withstand exposure to corrosive chemicals and acids in chemical processing plants.
- Electronics Assembly: ESD (Electrostatic Discharge) protection features prevent damage to electronic components during assembly and handling processes.
- Aerospace Industry: Power moller rollers with precision bearings and vibration dampening features ensure delicate handling of aerospace components and parts during manufacturing and assembly.
Realizing the Potential: Applications of Power Moller Roller
Overview of Industries Benefiting from Power Moller Rollers
Power moller rollers find widespread applications across various industries, including:
- Logistics and Distribution: Power moller rollers streamline sorting, loading, and unloading processes in warehouses and distribution centers, improving efficiency and throughput.
- Manufacturing: Power moller rollers facilitate the movement of materials and components along assembly lines, enhancing production efficiency and reducing cycle times.
- E-commerce and Retail: Power moller rollers enable automated order fulfillment and sorting in e-commerce fulfillment centers, ensuring timely delivery to customers.
- Food and Beverage: Power moller rollers with sanitary design options are used in food processing and packaging facilities to convey food products safely and hygienically.
- Automotive: Power moller rollers play a crucial role in automotive manufacturing for conveying parts and components between production processes.
Case Studies Demonstrating Efficiency and Productivity Gains
Numerous case studies highlight the efficiency and productivity gains achieved with Itoh Denki power moller rollers:
- Case Study 1: A distribution center implemented power moller rollers, resulting in a 30% increase in sorting throughput and a significant reduction in processing time.
- Case Study 2: A manufacturing facility reduced downtime and maintenance costs by 50% after switching to power moller rollers with maintenance-free designs.
- Case Study 3: An e-commerce fulfillment center improved order accuracy and fulfillment speed by 25% with the implementation of power moller roller conveyor systems.
- Case Study 4: A food processing plant achieved compliance with food safety regulations and minimized product contamination incidents by using power moller rollers with sanitary design options.
- Case Study 5: An automotive assembly line optimized workflow and reduced assembly time by 20% with the integration of power moller rollers for material handling.
Future Prospects and Emerging Trends in Conveyor Systems
The future of conveyor systems, including power moller rollers, is marked by several emerging trends:
- Automation: Increasing adoption of automation technologies, such as robotics and AI, for enhanced efficiency and flexibility in material handling processes.
- IoT Integration: Integration of Internet of Things (IoT) sensors and connectivity for real-time monitoring, predictive maintenance, and data-driven decision-making.
- Sustainability: Growing emphasis on sustainability and eco-friendly practices, driving the development of energy-efficient and recyclable conveyor components, including power moller rollers.
- Customization: Demand for highly customizable conveyor solutions tailored to specific industry needs, driving innovation in modular and adaptable conveyor designs.
- Integration with Industry 4.0: Integration of conveyor systems with Industry 4.0 principles, such as digitalization, connectivity, and smart manufacturing, to create interconnected and intelligent production environments.
FAQs About Power Moller Roller
Power Moller, also known as motorized roller, is a type of conveyor roller equipped with an internal motor that drives the rotation of the roller. Unlike traditional gravity rollers, power mollers can independently move loads along a conveyor system without the need for external drive mechanisms. These rollers are commonly used in material handling and logistics applications to automate the movement of goods in warehouses, distribution centers, and manufacturing facilities. Power mollers offer enhanced efficiency, control, and flexibility in conveyor systems, making them essential components in modern automated environments.
A power roller conveyor is a conveyor system that utilizes power moller rollers to transport goods along a predefined path. These conveyors consist of a series of motorized rollers spaced apart to create a continuous surface for conveying items. Power roller conveyors can be configured in various layouts, including straight sections, curves, merges, and diverges, to accommodate different material flow requirements. They are widely used in industries such as e-commerce, automotive, food and beverage, and parcel handling, where efficient and reliable material handling is essential for operations.
A drive roller, also known as a power moller or motorized roller, operates by using an internal motor to generate rotational motion, which drives the movement of the roller surface. The motor inside the roller is typically connected to a gearbox, which transfers the motor’s rotational force to the roller shaft. As the motor turns, it causes the roller to rotate, allowing it to move items placed on the conveyor. Drive rollers are controlled by a central system that regulates their speed, direction, and timing to ensure smooth and precise material handling along the conveyor system.
The primary purpose of a roller conveyor is to facilitate the efficient and safe movement of goods or materials from one location to another within a facility. Roller conveyors utilize a series of rollers mounted on a frame to create a continuous conveying surface, allowing items to be transported manually or automatically along the conveyor path. These conveyors are commonly used for tasks such as loading and unloading trucks, sorting packages, assembling products on production lines, and transporting bulk materials. Roller conveyors offer advantages such as ease of installation, low maintenance requirements, and the ability to handle various types of loads, making them indispensable in material handling operations.
Last Updated on April 1, 2024 by Jordan Smith
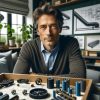
Jordan Smith, a seasoned professional with over 20 years of experience in the conveyor system industry. Jordan’s expertise lies in providing comprehensive solutions for conveyor rollers, belts, and accessories, catering to a wide range of industrial needs. From initial design and configuration to installation and meticulous troubleshooting, Jordan is adept at handling all aspects of conveyor system management. Whether you’re looking to upgrade your production line with efficient conveyor belts, require custom conveyor rollers for specific operations, or need expert advice on selecting the right conveyor accessories for your facility, Jordan is your reliable consultant. For any inquiries or assistance with conveyor system optimization, Jordan is available to share his wealth of knowledge and experience. Feel free to reach out at any time for professional guidance on all matters related to conveyor rollers, belts, and accessories.