Choosing the Right Power Roller Bed Conveyor for Your Business
In the realm of modern logistics and manufacturing, the power roller bed conveyor emerges as a pivotal innovation, streamlining operations and enhancing efficiency. This sophisticated system, distinguished by its motorized rollers, facilitates the automated movement of goods across various stages of production and distribution. Unlike traditional conveyor systems that rely on manual intervention or gravity, power roller bed conveyors offer a dynamic solution, capable of handling a wide range of materials with precision and ease. The integration of these conveyors into the industrial workflow not only accelerates the transport of products but also minimizes labor costs and reduces the potential for errors. By optimizing material handling processes, power roller bed conveyors significantly contribute to the operational efficiency of facilities, underscoring their indispensable role in the fast-paced sectors of logistics and manufacturing. The benefits of adopting such advanced conveying technology are manifold, including improved productivity, enhanced safety, and increased scalability, making power roller bed conveyors a preferred choice for businesses aiming to thrive in competitive markets.
What is Power Roller Bed Conveyors
The power roller bed conveyor represents a significant leap in the technology of material handling systems. At its core, a power roller bed conveyor is an automated system designed to transport goods and materials along a predefined path with minimal human intervention. This system is characterized by a series of rollers powered by motors, which propel items forward, making it an ideal solution for moving heavy or bulky items efficiently across manufacturing floors or warehouse spaces.
Basic Operation Principle
The operation of a power roller bed conveyor is straightforward yet ingenious. Each roller in the conveyor is equipped with a motor that is activated to rotate the roller. When an item is placed on the conveyor, these motorized rollers rotate, creating a smooth and continuous movement of goods along the conveyor path. This automation allows for the rapid and consistent transport of items, significantly reducing manual handling and increasing productivity.
Types of Power Roller Bed Conveyors
There are primarily two types of power roller bed conveyors, each catering to different material handling needs:
- Powered Belt Conveyors: These conveyors use a belt that is wrapped around the series of rollers. The belt can be made of various materials, including fabric, rubber, or plastic. Powered belt conveyors are particularly useful for transporting small or irregularly shaped items that might slip between rollers.
- Powered Roller Conveyors: This type directly utilizes motorized rollers to move items. It is highly efficient for transporting larger and heavier items that have a flat bottom, ensuring stability as they move along the conveyor.
Comparison with Gravity Conveyors
While gravity conveyors rely on the force of gravity to move items along a downward slope, power roller bed conveyors use motorized rollers for movement, offering several advantages:
- Control: Power roller bed conveyors provide precise control over the speed and direction of the items being transported, which is not possible with gravity conveyors.
- Versatility: They can move items uphill, horizontally, and on level surfaces, unlike gravity conveyors that require a slope.
- Efficiency: Power roller bed conveyors can continuously operate at a consistent speed, improving the efficiency of material handling operations.
- Safety: The risk of items colliding or getting damaged is reduced with power roller bed conveyors, as they allow for better spacing and control of the items being moved.
- Energy Saving: Modern power roller bed conveyors can be designed to conserve energy by activating rollers only when items are detected, reducing power consumption.
The power roller bed conveyor system offers a dynamic and efficient solution for automating the transport of goods in various industrial settings. Its ability to handle a wide range of item types and sizes, combined with the advantages over traditional gravity conveyors, makes it an indispensable tool in modern manufacturing and logistics operations.
Key Features and Technical Specifications of Power Roller Bed Conveyors
Power roller bed conveyors stand out in the material handling industry due to their robust design and advanced technical specifications. These conveyors are engineered to meet the diverse needs of various industrial applications, offering unparalleled efficiency and reliability. Below is a detailed exploration of their key features and technical specifications.
Standard Design Features
The standard design of a power roller bed conveyor includes several critical features that ensure its effectiveness in transporting goods:
- Load Capacity: Power roller bed conveyors are designed to handle a wide range of load capacities, typically from a few kilograms to several thousand kilograms, accommodating the needs of different industries.
- Dimensions: The dimensions of these conveyors can vary greatly, with lengths extending up to 100 feet or more, widths ranging from a few inches to several feet, and heights adjustable to suit operational requirements.
- Travel Speed: The travel speed of power roller bed conveyors is adjustable, with standard speeds ranging from a few feet per minute to over 100 feet per minute, allowing for the precise control of material flow.
Versatility and Adaptability
Power roller bed conveyors are highly versatile and adaptable, making them suitable for a wide range of industrial applications:
- Manufacturing: For the assembly line operations, where parts need to be moved smoothly through various stages of assembly.
- Warehousing: For sorting, packing, and dispatching goods, where efficient material handling is crucial.
- Distribution Centers: For loading and unloading goods, facilitating quick turnaround times.
- Food and Beverage: For handling packaged food and beverages, where hygiene and speed are paramount.
- Pharmaceuticals: For transporting sensitive pharmaceutical products, requiring precise control and gentle handling.
Customizable Options
To meet the specific needs of different industries, power roller bed conveyors come with a range of customizable options:
- Stainless Steel Structure: For environments requiring high levels of hygiene and corrosion resistance, such as food processing or pharmaceutical manufacturing.
- Rollers with PU Coating: Polyurethane-coated rollers provide additional grip and protection for delicate items, reducing the risk of damage during transport.
- Automation Features: Advanced automation features, including sensors, programmable logic controllers (PLCs), and software integration, allow for the automation of complex tasks, such as sorting and quality control, enhancing operational efficiency.
- Adjustable Speeds: The ability to adjust conveyor speeds provides flexibility to accommodate different operational tempos and product types.
- Modular Design: Modular designs offer the flexibility to expand or reconfigure the conveyor layout as the needs of the business change, ensuring a long-term material handling solution.
The power roller bed conveyor is a sophisticated material handling solution that combines standard and customizable features to meet the diverse needs of modern industries. Its technical specifications and versatility make it an indispensable tool for enhancing efficiency and productivity in a wide range of industrial applications.
Choosing the Right Power Roller Bed Conveyor for Your Needs
Selecting the appropriate power roller bed conveyor for your operational needs is crucial to achieving optimal efficiency and productivity. This decision should be informed by several key factors, each playing a pivotal role in how well the conveyor will perform in your specific environment. Here are the essential considerations and examples to guide you through the selection process.
Factors to Consider
Material to be Transported: The type of materials or goods the conveyor will carry significantly influences the choice of conveyor. For instance, a conveyor designed for lightweight packages may not be suitable for heavy machinery parts. Examples:
- Lightweight packages might require a conveyor with gentle handling features.
- Heavy machinery parts demand a conveyor with a high load capacity and robust construction.
- Fragile goods such as glassware necessitate conveyors with smooth transitions and the ability to control speed precisely.
- Bulk materials like grains or chemicals might need conveyors with specialized belt materials to prevent contamination.
- Electronics require conveyors that can prevent static build-up.
Load Capacity: The weight of the items the conveyor needs to transport directly impacts the required load capacity of the system. Examples:
- A distribution center for consumer goods may need conveyors that can handle loads up to 50 kg.
- An automotive assembly line might require conveyors with a capacity of several hundred kilograms for engine parts.
- A furniture manufacturing plant needs conveyors that can support large, bulky items, exceeding 100 kg.
- E-commerce warehouses handling a diverse range of products require versatile conveyors with adjustable load capacities.
- Agricultural operations transporting sacks of produce might need conveyors capable of supporting loads of up to 200 kg.
Specific Application Requirements: The intended use of the conveyor influences its design and features. Examples:
- Assembly lines need conveyors with precise speed control and the ability to integrate with other machinery.
- Packaging operations benefit from conveyors with easy-to-clean surfaces and minimal gaps.
- Sorting facilities require conveyors that can be easily reconfigured or expanded as sorting needs change.
- Cold storage environments need conveyors made from materials that can withstand low temperatures without becoming brittle.
- Pharmaceutical applications demand conveyors with high hygiene standards, including stainless steel construction and easy-to-sanitize surfaces.
The Importance of Consulting with Manufacturers
Custom solutions are often necessary to meet the unique demands of different industries and applications. Consulting with manufacturers can ensure that your power roller bed conveyor is perfectly tailored to your needs.
Examples:
- A food processing plant may require a custom conveyor with a washdown-capable design for easy cleaning.
- A heavy equipment manufacturer might need a conveyor system designed to integrate with robotic assembly stations.
- An e-commerce fulfillment center could benefit from a conveyor with advanced sorting and tracking capabilities to handle a high volume of orders.
- A chemical processing facility may need a conveyor with materials resistant to corrosion and chemical exposure.
- An airport baggage handling system requires a highly durable conveyor designed for continuous operation and capable of handling irregularly shaped luggage.
Selecting the right power roller bed conveyor involves careful consideration of the materials to be transported, the required load capacity, and specific application needs. Consulting with manufacturers for tailored solutions can address these considerations, ensuring that the conveyor system enhances operational efficiency and meets the unique demands of your business.
Manufacturers and Suppliers of Power Roller Bed Conveyor
When it comes to optimizing your material handling processes, selecting the right power roller bed conveyor is only half the battle. Equally crucial is choosing a manufacturer or supplier that can deliver a product tailored to your specific needs. Here’s an overview of what sets apart leading manufacturers and tips for selecting the right one for your business.
Leading Manufacturers and What Sets Them Apart
- Innovative Design: Top manufacturers like Ultimation Inc. and Hytrol offer innovative power roller bed conveyor designs that incorporate the latest technology for efficiency and reliability. Their products often feature modular designs for easy integration and scalability.
- Customization Capabilities: Companies such as Titan Conveyors and Dorner Conveyors specialize in providing customizable conveyor solutions. They can tailor the conveyor’s dimensions, load capacity, and even the type of rollers used to suit specific industry requirements.
- Robust Construction: Manufacturers like Dematic and Interroll are known for the durability of their conveyors. They use high-quality materials and construction techniques to ensure their conveyors can withstand the rigors of heavy industrial use.
- Advanced Automation Features: Some manufacturers stand out for their incorporation of advanced automation features into their power roller bed conveyors. These features include programmable logic controllers (PLCs), sensors, and software integration for enhanced control and efficiency.
- Exceptional Support Services: Leading suppliers offer comprehensive support services, from initial consultation and custom design to installation, maintenance, and repair services. This ensures that businesses not only receive a product that fits their needs but also the ongoing support to keep it running smoothly.
Tips on Choosing the Right Supplier
- Assess Technical Expertise: Look for suppliers with a proven track record in your industry. For instance, if you’re in the food and beverage sector, choose a supplier experienced in designing conveyors for food-grade applications.
- Evaluate Customization Options: Ensure the supplier can offer customization options that align with your specific needs. Whether it’s adjustable speeds, special roller materials, or integration capabilities, the right supplier should be able to accommodate your requirements.
- Consider After-Sales Support: A supplier’s job isn’t done after the sale. Opt for suppliers who offer comprehensive after-sales support, including maintenance, parts replacement, and technical assistance.
- Check References and Reviews: Before making a decision, check the supplier’s references and reviews from other businesses. This can give you insight into their reliability, product quality, and customer service.
- Compare Costs and Value: While cost is an important factor, consider the overall value the supplier brings. This includes not just the purchase price but also the long-term benefits of efficiency gains, reduced downtime, and the quality of after-sales support.
When selecting a manufacturer or supplier for your power roller bed conveyor, it’s essential to consider their expertise, customization capabilities, construction quality, automation features, and support services. By carefully evaluating these factors, you can ensure that you choose a partner that will not only provide a conveyor that meets your needs but also supports your business’s growth and efficiency goals.
Pricing and Purchasing Options for Power Roller Bed Conveyor
Navigating the pricing and purchasing options for a power roller bed conveyor can be complex, given the variety of factors that influence cost and the different strategies for securing the best deal. Understanding these elements can help you make an informed decision tailored to your budget and operational needs.
Price Range and Factors Affecting Cost
The price of power roller bed conveyors can vary widely, typically ranging from a few thousand dollars for basic models to tens of thousands for highly customized or large-scale systems. Several factors contribute to this cost variability:
- Size and Length: Larger and longer conveyors require more materials and labor to construct, directly impacting the price.
- Material Construction: Conveyors made with high-grade materials like stainless steel are more expensive than those made with aluminum or coated steel due to the cost of raw materials.
- Customization: Custom features such as adjustable speeds, special roller coatings, or integration with existing systems can add to the cost.
- Load Capacity: Conveyors designed to handle heavier loads require more robust construction and more powerful motors, increasing the price.
- Advanced Features: Incorporating advanced automation features, sensors, and controls can significantly raise the price due to the additional technology and programming required.
Finding the Best Deals
Securing the best deal on a power roller bed conveyor requires a strategic approach, whether you’re purchasing new, used, or considering leasing options. Here are some tips to help you find the best value:
- Compare Quotes: Obtain quotes from multiple suppliers to compare prices and specifications. This can help you identify the best value for the features you need.
- Consider Used Options: Purchasing a used power roller bed conveyor can offer significant savings. Look for reputable dealers who offer certified pre-owned equipment with a warranty.
- Lease Instead of Buy: Leasing a conveyor can reduce upfront costs and may include maintenance and support, making it a cost-effective option for temporary or trial applications.
- Bulk Purchases: If you need multiple conveyors, inquire about bulk purchase discounts. Suppliers may offer reduced pricing for larger orders.
- Negotiate Added Value: Instead of focusing solely on lowering the price, negotiate for added value such as extended warranties, free installation, or discounted maintenance services.
The cost of a power roller bed conveyor is influenced by its size, construction materials, customization level, load capacity, and the inclusion of advanced features. To secure the best deal, it’s essential to compare quotes, consider used or leased options, explore bulk discounts, and negotiate for added value. By carefully evaluating these factors and options, you can find a power roller bed conveyor that meets your operational needs while staying within your budget.
Installation, Operation, and Maintenance of Power Roller Bed Conveyor
Ensuring the optimal performance of a power roller bed conveyor involves understanding the basics of installation, operation, and maintenance. These conveyors are designed for efficiency and durability, but their longevity and effectiveness are significantly influenced by proper setup, use, and care.
Installation Steps
The installation of a power roller bed conveyor typically follows these steps, as outlined in a standard manual:
- Site Preparation: Ensure the installation site is level and capable of supporting the weight and operational load of the conveyor. This may involve reinforcing the floor or constructing a dedicated platform.
- Unpacking and Inspection: Carefully unpack the conveyor components and inspect for any damage that may have occurred during shipping. Verify all parts against the shipping list to ensure completeness.
- Assembly: Follow the manufacturer’s instructions to assemble the conveyor. This usually involves connecting the frame sections, installing the rollers, and fitting any ancillary equipment like sensors or guards.
- Motor and Control System Setup: Install the motor and control system. Ensure electrical connections are made according to local codes and standards, and that the motor is correctly aligned with the rollers.
- Testing: Before full operation, test the conveyor with a few items to ensure everything moves smoothly and the control systems are functioning correctly.
Operational Guidelines
To operate a power roller bed conveyor efficiently and safely, adhere to the following guidelines:
- Training: Ensure all operators are trained on the proper use of the conveyor, including start-up, operation, and emergency stop procedures.
- Load Limits: Do not exceed the conveyor’s specified load capacity, as this can cause damage and pose safety risks.
- Regular Inspections: Conduct regular inspections to identify any potential issues before they lead to downtime.
- Clear Path: Keep the conveyor path clear of obstructions that could cause jams or damage to the items being transported.
- Safety Measures: Implement and follow all recommended safety measures, including the use of guards and emergency stop features.
Maintenance Tips
Regular maintenance is crucial for the longevity and efficient operation of a power roller bed conveyor. Key maintenance tips include:
- Lubrication: Regularly lubricate moving parts according to the manufacturer’s recommendations to reduce wear and tear.
- Cleaning: Keep the conveyor clean, especially the rollers and belt, to prevent material build-up that can affect performance.
- Belt Tension: Check and adjust the belt tension periodically to ensure it is neither too tight nor too loose.
- Roller Alignment: Inspect rollers for proper alignment and adjust as necessary to prevent tracking issues.
- Electrical System Checks: Regularly inspect the electrical system, including wiring and controls, for signs of wear or damage.
Common Parts for Replacement or Upgrades
Certain components of a power roller bed conveyor may require regular replacement or upgrades, including:
- Rollers: Worn or damaged rollers can affect conveyor performance and need to be replaced.
- Belts: Conveyor belts wear out over time, especially in high-use environments.
- Motors: Motors may require replacement or upgrading to accommodate increased loads or efficiency demands.
- Control Systems: Upgrading control systems can improve the functionality and efficiency of the conveyor.
- Bearings and Bushings: These components are critical for smooth operation and may wear out with regular use.
Proper installation, operation, and maintenance are key to maximizing the efficiency and lifespan of a power roller bed conveyor. By following the manufacturer’s guidelines and implementing regular maintenance practices, businesses can ensure their conveyor systems operate smoothly and reliably for years to come.
FAQs About Power Roller Bed Conveyor
A power roller conveyor, often referred to as a motorized roller conveyor, is an automated conveyor system that utilizes a series of powered rollers to move materials and goods along a specified path. Unlike traditional conveyor systems that may rely on manual effort or gravity, power roller conveyors are driven by motors, making them ideal for transporting heavy or large items across flat or inclined paths with minimal human intervention. These conveyors are designed to improve efficiency and productivity in various settings, including manufacturing plants, distribution centers, and warehouses, by automating the movement of products.
Power roller conveyors can be customized with different roller sizes, materials, and motor capacities to handle a wide range of materials, from small packages to large pallets. The automation level can vary, with some systems featuring sensors and controls to regulate speed, direction, and the spacing of items on the conveyor, thereby optimizing the material handling process.
The primary purpose of a roller conveyor is to facilitate the smooth and efficient transport of goods and materials from one point to another within a facility. Roller conveyors are versatile systems that can be used for a wide range of applications, including sorting, assembling, loading, and packaging. They are designed to support the weight of the items being transported while minimizing friction, allowing for easy movement and reducing the need for manual handling.
Roller conveyors can significantly enhance productivity and efficiency in various industrial and commercial environments by automating the movement of goods, reducing labor costs, and improving workplace safety. They are particularly beneficial in settings where items need to be moved over long distances or where there is a need for continuous flow of materials.
Additionally, roller conveyors can be integrated with other conveyor types and material handling systems to create comprehensive logistics solutions that meet specific operational requirements.
Conveyors utilize different types of rollers depending on the application, material to be transported, and the environment in which the conveyor will operate. The most common types of rollers include:
Steel Rollers: Durable and capable of handling heavy loads, steel rollers are often used in industrial applications where strength and longevity are critical.
Plastic Rollers: Lightweight and corrosion-resistant, plastic rollers are suitable for lighter loads and environments where moisture or chemical exposure is a concern.
Rubber-Coated Rollers: These rollers have a rubber coating to provide additional grip and reduce slippage of materials being transported. They are ideal for handling fragile or slippery items.
Motorized Rollers: Equipped with internal motors, these rollers can individually power sections of a conveyor, allowing for precise control of the movement and spacing of items.
The choice of roller material and type is crucial for ensuring the conveyor’s efficiency, durability, and suitability for the specific materials it will carry.
Roller conveyors can be categorized into several types based on their mechanism of operation and the specific applications they serve. The main types include:
Gravity Roller Conveyors: These rely on gravity to move items along the conveyor, making them suitable for downward or inclined paths. They are often used for loading and unloading goods.
Powered Roller Conveyors: Equipped with motorized rollers, these conveyors can move items along flat surfaces or inclines, offering greater control over speed and item spacing.
Accumulating Roller Conveyors: Designed to allow items to accumulate without touching, these conveyors are ideal for applications where products need to be staged for packing or inspection.
Flexible Roller Conveyors: These conveyors are extendable and flexible, allowing for easy reconfiguration and movement to different locations as needed. They are ideal for temporary or dynamic workspaces.
Each type of roller conveyor offers unique advantages and is suited to specific tasks and environments, from simple material transfer to complex logistics and assembly operations.
Last Updated on May 23, 2024 by Jordan Smith
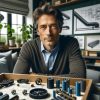
Jordan Smith, a seasoned professional with over 20 years of experience in the conveyor system industry. Jordan’s expertise lies in providing comprehensive solutions for conveyor rollers, belts, and accessories, catering to a wide range of industrial needs. From initial design and configuration to installation and meticulous troubleshooting, Jordan is adept at handling all aspects of conveyor system management. Whether you’re looking to upgrade your production line with efficient conveyor belts, require custom conveyor rollers for specific operations, or need expert advice on selecting the right conveyor accessories for your facility, Jordan is your reliable consultant. For any inquiries or assistance with conveyor system optimization, Jordan is available to share his wealth of knowledge and experience. Feel free to reach out at any time for professional guidance on all matters related to conveyor rollers, belts, and accessories.