Innovations in Powered Roller Design and Function
In the fast-paced world of modern material handling and logistics, the significance of powered rollers cannot be overstated. These innovative components form the backbone of powered roller conveyors, systems that have revolutionized the way goods are moved within manufacturing plants, distribution centers, and warehouses. Powered roller conveyors leverage motorized rollers to automate the transportation of items across short and long distances, seamlessly integrating into various stages of production and distribution processes. This automation not only enhances efficiency by speeding up operations and reducing manual labor but also improves safety by minimizing the physical handling of goods. The introduction of powered roller technology marks a pivotal development in the logistics sector, offering a scalable and flexible solution to meet the ever-growing demands of global supply chains. By understanding the role and functionality of powered rollers, businesses can unlock new levels of operational efficiency and productivity.
The Basics of Powered Roller Conveyors
Powered roller conveyors represent a significant leap forward in the automation of material handling processes. These systems utilize powered rollers to move goods across facilities, streamlining operations in industries ranging from manufacturing to distribution. At their core, powered roller conveyors consist of rollers that are directly powered by motors, eliminating the need for manual effort or gravity to move items along the conveyor belt. This automation allows for precise control over the speed and direction of the conveyed items, making it an ideal solution for a variety of material handling needs.
Key Components of Powered Roller Conveyors
The efficiency and versatility of powered roller conveyors are attributed to their key components, which include motorized drive rollers and interroll conveyor rollers. Here are five specific examples of each, showcasing the diversity and functionality that these components bring to power roller conveyor system systems:
Motorized Drive Rollers
- Direct Drive Rollers: These rollers have built-in motors that provide direct power, offering high torque and precise control over conveyor movements.
- Chain-Driven Rollers: Utilizing a chain mechanism connected to a motor, these rollers ensure uniform movement across longer conveyor systems.
- Belt-Driven Rollers: Similar to chain-driven rollers but using a belt for power transmission, offering quieter operation and smoother handling.
- Variable Speed Rollers: Equipped with motors that allow speed adjustments, these rollers can adapt to different phases of the production process.
- Zero-Pressure Accumulation Rollers: Designed to prevent items from touching while on the conveyor, these rollers use sensors and motors to regulate the flow of goods.
Interroll Conveyor Rollers
- Heavy-Duty Rollers: Built for durability and capable of handling heavy loads, ideal for industrial applications.
- High-Speed Rollers: Designed for operations requiring fast movement of goods, such as sorting and packaging lines.
- Antistatic Rollers: These rollers prevent the buildup of static electricity, crucial for safely conveying electronic components.
- Food-Grade Rollers: Made from materials that meet hygiene standards, suitable for food processing and pharmaceutical industries.
- Temperature-Resistant Rollers: Capable of operating in extreme temperatures, these rollers are used in cold storage and high-heat environments.
Each of these components plays a crucial role in the functionality of powered roller conveyors, enabling them to meet a wide range of material handling requirements. From the precision control offered by motorized drive rollers to the specialized capabilities of interroll conveyor rollers, these systems are engineered to improve efficiency, safety, and productivity in automated material handling processes.
Advantages of Powered Roller Conveyors
Powered roller conveyors offer a multitude of benefits that significantly enhance the efficiency, flexibility, and safety of material handling operations. These systems are designed to automate the movement of goods, providing a seamless flow of materials across various stages of production, packaging, and distribution. Below, we delve into the specific advantages of powered roller conveyors, highlighting examples that illustrate their impact on productivity, adaptability, and workplace safety.
Efficiency in Material Handling and Productivity Enhancement
The primary advantage of powered roller conveyors is their ability to streamline operations and boost productivity.
- Continuous Operation: Unlike manual handling, powered roller conveyors can operate continuously, moving goods without interruption and significantly increasing throughput.
- Speed Control: The ability to adjust the speed of the conveyor allows for synchronization with different phases of the production process, optimizing workflow and reducing bottlenecks.
- Reduced Product Damage: Gentle handling of products by powered rollers minimizes damage during transit, ensuring higher product quality and reducing waste.
- Energy Efficiency: Modern powered roller conveyors are designed to consume less energy, with systems that activate rollers only when needed, leading to lower operational costs.
- Integration with Automated Systems: Powered roller conveyors can be easily integrated with automated sorting systems, robotic arms, and other machinery, creating a cohesive and efficient production line.
Flexibility of Design and Application Across Various Industries
Powered roller conveyors are celebrated for their versatility, catering to a wide range of industries with specific material handling needs.
- E-commerce Fulfillment: Adaptable to varying package sizes and weights, ensuring efficient handling of diverse product ranges.
- Pharmaceuticals: Configurable for cleanroom environments, supporting the stringent hygiene standards required in pharmaceutical manufacturing.
- Automotive Manufacturing: Capable of handling heavy components and integrating with assembly line operations for seamless production flow.
- Food and Beverage: Designed with food-grade materials and washdown capabilities, suitable for direct contact with food products.
- Parcel and Logistics: Customizable for high-volume sorting and distribution centers, improving parcel sorting accuracy and speed.
Safety Improvements and Reduced Labor Requirements
By automating material handling, powered roller conveyors not only enhance safety but also reduce the need for manual labor.
- Minimized Manual Handling: Reduces the risk of injuries associated with lifting, carrying, and manual sorting, promoting a safer workplace.
- Ergonomic Design: Engineered to eliminate awkward movements and positions, protecting workers from strain and repetitive motion injuries.
- Controlled Movement of Goods: Automated speed and direction control reduce the chances of collisions and accidents on the production floor.
- Reduced Congestion: The efficient flow of goods minimizes congestion in work areas, lowering the risk of workplace accidents.
- Labor Reallocation: With reduced need for manual handling, employees can be reassigned to more critical tasks, optimizing workforce utilization and focusing on quality control and maintenance.
Powered roller conveyors bring significant advantages to material handling, including enhanced efficiency, flexibility, and safety. These systems are tailored to meet the specific needs of various industries, improving productivity, adapting to different operational requirements, and creating a safer work environment.
Innovations in Powered Roller Technology
The landscape of powered roller technology is constantly evolving, driven by the pursuit of efficiency, adaptability, and intelligence in material handling systems. Leading manufacturers are at the forefront of this innovation, introducing advanced features that redefine the capabilities of powered roller conveyors. The DynaRoller™ and Itoh Denki motorized conveyor rollers stand as prime examples of this technological advancement, showcasing the potential of modern powered rollers to transform industrial operations.
Recent Advancements from Leading Powered Roller Manufacturers
Innovation in powered roller technology is marked by several key developments that enhance the performance and functionality of these systems.
- Integrated Motor and Control Systems: The DynaRoller™ exemplifies this trend, incorporating motorized rollers with built-in control systems. This integration simplifies conveyor design, reduces installation time, and enhances system reliability by minimizing external wiring and components.
- Energy-Efficient Operation: Itoh Denki has pioneered motorized conveyor rollers that consume less power without sacrificing performance. These rollers use energy-efficient motors and intelligent activation technologies to operate only when necessary, significantly reducing energy consumption.
- Smart Sensors and Connectivity: Modern powered rollers are equipped with sensors that monitor performance metrics such as speed, load, and operational efficiency. These sensors enable predictive maintenance by identifying potential issues before they lead to downtime, and they facilitate integration with IoT (Internet of Things) platforms for real-time monitoring and control.
- Modular and Scalable Designs: Flexibility is a key focus, with manufacturers offering modular powered roller systems that can be easily expanded or reconfigured to meet changing operational needs. This modularity allows businesses to scale their material handling capacity in line with growth, ensuring that their investment remains relevant and effective over time.
- Advanced Material Technologies: The use of new materials and coatings has improved the durability and performance of powered rollers. For example, rollers with non-stick coatings prevent material buildup, while corrosion-resistant materials extend the life of rollers in harsh environments.
The Role of Technology in Improving Functionality
The incorporation of technology into powered roller conveyor system designs has significantly improved their functionality, making them more intelligent, efficient, and adaptable. Smart sensors embedded in rollers provide valuable data that can be used to optimize conveyor operations, predict maintenance needs, and prevent system failures. Modular designs offer the flexibility to adapt to changing business needs, supporting a wide range of applications and industries. Furthermore, the integration of powered rollers with automated systems and robotics has opened new possibilities for fully automated material handling solutions, reducing labor costs and enhancing operational efficiency.
The innovations in powered roller technology represent a leap forward in the capabilities of conveyor systems. By leveraging advancements such as integrated motor and control systems, energy-efficient operation, smart sensors, modular designs, and advanced materials, powered roller conveyors are set to play a pivotal role in the future of material handling and logistics.
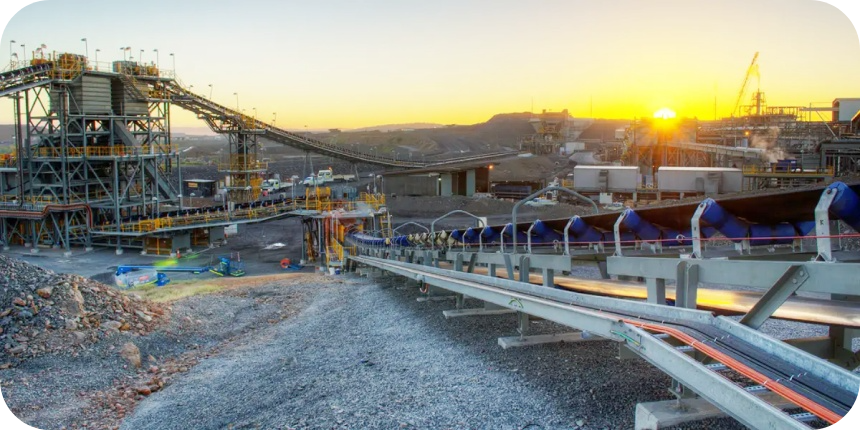
Selecting the Right Powered Roller Conveyor for Your Needs
Choosing the appropriate powered roller conveyor system is crucial for optimizing your material handling processes. The selection process involves considering a variety of factors to ensure the system meets your operational requirements, environmental conditions, and efficiency goals. Understanding these factors and consulting powered roller conveyor design PDFs for technical guidance can help you make an informed decision.
Factors to Consider When Choosing a Powered Roller Conveyor System
When selecting a powered roller conveyor, it’s essential to evaluate several key aspects to find a solution that aligns with your specific needs. Here are five critical factors to consider, along with examples for each:
Application-Specific Requirements
- Product Type and Size: Ensure the conveyor can handle the dimensions and weight of your products, whether they are small electronic components or large automotive parts.
- Throughput Requirements: Consider the volume of goods the system needs to transport per hour to maintain your production pace.
- Integration with Existing Systems: The conveyor should seamlessly integrate with your current material handling setup, including sortation systems and packaging lines.
- Future Scalability: Choose a system that can be easily expanded or reconfigured as your business grows and your operational needs change.
- Special Handling Needs: If your products require gentle handling, look for conveyors designed to minimize impact and reduce product damage.
Environmental Conditions
- Temperature Extremes: For operations in cold storage or high-temperature environments, select rollers made from materials that can withstand these conditions.
- Wet or Humid Environments: Opt for corrosion-resistant rollers and waterproof motor enclosures to prevent moisture-related damage.
- Dusty or Dirty Conditions: Consider powered rollers with sealed bearings and dust-resistant designs to ensure longevity in challenging environments.
- Cleanroom Applications: For pharmaceutical or electronic manufacturing, choose conveyors that meet cleanroom standards for particulate emissions.
- Outdoor Use: If the conveyor will be used outdoors, ensure it is constructed with UV-resistant materials and designed to withstand weather conditions.
Efficiency Goals
- Energy Consumption: Look for energy-efficient motorized rollers that can reduce operational costs.
- Maintenance Requirements: Select systems with self-lubricating bearings and easy-access components to minimize maintenance downtime.
- Speed and Precision: Ensure the conveyor can operate at the required speed and precision for your sorting and assembly processes.
- Noise Levels: For environments where noise is a concern, such as retail or office settings, choose conveyors designed for quiet operation.
- Automation and Control: Consider powered roller conveyors with advanced control systems for improved efficiency and integration with automated processes.
Insights into Powered Roller Conveyor Design PDFs for Technical Guidance
Powered roller conveyor design PDFs are invaluable resources that provide detailed technical specifications, layout options, and customization possibilities. These documents offer insights into:
- Component Specifications: Detailed information on roller dimensions, motor types, and material options.
- System Layouts: Examples of standard and custom conveyor configurations to accommodate different operational needs.
- Installation Guidelines: Step-by-step instructions for assembling and installing the conveyor system.
- Maintenance and Troubleshooting: Tips for regular maintenance and troubleshooting common issues to ensure optimal performance.
- Customization Options: Information on available accessories and customization options to tailor the conveyor to specific applications.
By carefully considering these factors and utilizing powered roller conveyor design PDFs for guidance, you can select the right powered roller conveyor system that meets your operational needs, adapts to your environment, and achieves your efficiency goals.
Leading Manufacturers and Products in Powered Roller Technology
The powered roller conveyor market is rich with innovative solutions designed to meet the diverse needs of material handling across various industries. Leading manufacturers have set themselves apart through relentless innovation, quality craftsmanship, and responsive customer service. Among these, Interroll stands out with its motorized roller products, alongside other notable brands that have made significant contributions to the industry. This section provides an overview of these top manufacturers and their standout products, along with a comparison of features and benefits to help readers identify the best powered roller options for their needs.
Interroll Motorized Roller and Other Notable Brands
Interroll is renowned for its range of motorized rollers, designed to offer efficiency, reliability, and seamless integration into existing systems. Their products are a testament to the company’s commitment to innovation and sustainability. Alongside Interroll, several other manufacturers have made their mark:
- Interroll: Known for the Interroll Drum Motor, a compact, high-performance drive solution that powers the conveyor belt directly without external motors and gears. This design reduces maintenance, increases efficiency, and enhances safety by eliminating external moving parts.
- Itoh Denki: Specializes in motorized drive rollers (MDR) that provide a versatile and energy-efficient solution for automated conveyor systems. Their products are celebrated for their quiet operation, ease of installation, and low energy consumption.
- Hytrol: Offers a comprehensive range of conveyor solutions, including powered roller conveyors that are customizable for various applications. Hytrol’s emphasis on robust design and reliability makes their products a favorite among logistics and distribution centers.
- Dematic: A global leader in integrated automated technology, Dematic provides powered roller conveyors that are engineered for durability and performance. Their solutions are tailored to optimize workflow, increase throughput, and reduce operational costs.
- Dorner: Dorner’s powered roller conveyors are designed for precision handling and flexibility. Their products stand out for their modular design, allowing for easy adjustments and expansions to meet changing business needs.
Comparison of Features and Benefits
When comparing these leading manufacturers and their powered roller products, several key features and benefits emerge:
- Energy Efficiency: Itoh Denki and Interroll both offer solutions that minimize energy consumption, but Itoh Denki’s focus on motorized drive rollers provides exceptional efficiency for systems that operate intermittently.
- Ease of Integration: Interroll’s Drum Motor is designed for easy integration into existing conveyor systems, offering a plug-and-play solution that reduces installation time and complexity.
- Customization and Flexibility: Dorner and Hytrol excel in providing customizable conveyor solutions, with Dorner’s modular design allowing for greater flexibility in system layout and expansion.
- Durability and Performance: Dematic’s powered roller conveyors are built for high-demand environments, offering superior durability and performance that can withstand continuous operation in challenging conditions.
- Quiet Operation: Itoh Denki’s motorized rollers are engineered for quiet operation, making them ideal for environments where noise reduction is a priority, such as in close proximity to workstations or in customer-facing areas.
By understanding the unique features and benefits offered by each manufacturer, businesses can make informed decisions when selecting the best powered roller conveyor system solutions to meet their operational needs. Whether prioritizing energy efficiency, integration ease, customization, durability, or quiet operation, there is a solution available that aligns with every requirement.
Real-World Applications and Success Stories of Powered Roller Conveyors
The versatility and efficiency of powered roller conveyors have led to their successful implementation across a wide range of industries. From logistics and manufacturing to packaging, these systems have proven to be invaluable in optimizing operations, enhancing productivity, and solving complex logistical challenges. Below, we explore five case studies that highlight the transformative impact of powered roller conveyors in various sectors.
Logistics and Distribution
- E-Commerce Fulfillment Center: A leading online retailer implemented a network of powered roller conveyors to automate their order fulfillment process. This upgrade resulted in a 40% increase in order processing speed, significantly reducing delivery times and improving customer satisfaction.
- International Airport Baggage Handling: An international airport overhauled its baggage handling system with powered roller conveyors, improving baggage transfer accuracy and reducing lost luggage incidents by over 50%.
- Automotive Parts Distribution: An automotive parts distributor integrated powered roller conveyors into their warehouse, streamlining the sorting and distribution process. This led to a 30% reduction in processing time and a significant decrease in manual handling errors.
Manufacturing
- Automobile Assembly Line: A major car manufacturer incorporated powered roller conveyors into their assembly line, enhancing the movement of car parts between stations. This integration boosted production efficiency by 25% and allowed for more precise assembly processes.
- Electronics Factory: By adopting powered roller conveyors, an electronics manufacturer was able to automate the transport of delicate components through the assembly process, minimizing handling damage and increasing throughput by 35%.
Packaging Industry
- Food Packaging Facility: A food processing and packaging company utilized powered roller conveyors to automate the movement of packaged goods into storage and shipping areas. This change resulted in a 20% increase in packaging speed and improved hygiene by reducing direct contact with the products.
- Pharmaceutical Packaging Line: In a pharmaceutical company, powered roller conveyors were implemented to streamline the packaging of medicines. This led to a 15% increase in packaging efficiency and enhanced traceability of packaged products.
- Beverage Bottling Plant: A beverage company integrated powered roller conveyors into their bottling line, significantly improving the speed and efficiency of the bottling and packaging process, and reducing product spillage and waste.
Problem-Solving Capabilities
- Retail Distribution Center: Faced with seasonal demand spikes, a retail distribution center employed powered roller conveyors with modular designs. This flexibility allowed them to quickly adjust their operations, handling up to 50% more goods during peak periods.
- Cold Storage Warehouse: A cold storage facility implemented powered roller conveyors designed for low-temperature environments, solving the problem of equipment malfunction due to freezing conditions and improving overall logistics efficiency within the cold chain.
These real-world applications and success stories demonstrate the significant advantages powered roller conveyors offer across various sectors. By enhancing efficiency, solving logistical challenges, and adapting to specific industry needs, powered roller conveyors have become a cornerstone of modern material handling and operational optimization.
Have questions about our conveyor rollers? Reach out today!
Future Trends in Powered Roller Conveyor Systems
The landscape of powered roller conveyor systems is on the brink of transformative changes, driven by advancements in technology and shifting industry needs. As businesses continue to seek more efficient, flexible, and sustainable material handling solutions, powered roller technology is evolving to meet these demands. Below, we explore the future trends in powered roller conveyor systems, focusing on automation, AI integration, sustainability efforts, and their growing importance in global supply chains.
Predictions for the Future Development of Powered Roller Technology
The future of powered roller technology is marked by several key advancements that promise to redefine the capabilities and applications of these systems:
- Increased Automation: Future powered roller conveyors will feature even higher levels of automation, reducing the need for manual intervention and allowing for more seamless operations across various industries.
- AI Integration: Artificial intelligence will play a crucial role in optimizing the performance of powered roller conveyors. AI algorithms can predict maintenance needs, adjust conveyor speeds in real-time based on workflow, and even autonomously reconfigure layouts to meet changing operational demands.
- Advanced Material Handling: Innovations in roller design and materials will enable the handling of a wider range of products, including those with unique shapes, sizes, or sensitivity requirements, expanding the versatility of powered roller conveyors.
- Energy Efficiency and Sustainability: Future developments will focus on reducing the energy consumption of powered roller systems and utilizing eco-friendly materials, aligning with global sustainability goals.
- Integration with IoT: The Internet of Things (IoT) will enhance the connectivity of powered roller conveyors, enabling comprehensive monitoring, data collection, and communication between different parts of the supply chain.
The Growing Importance of Powered Roller Conveyor Systems in Global Supply Chains
As global supply chains become more complex and demanding, the role of powered roller conveyor systems is set to become even more critical.
- Scalability: The modular nature of powered roller conveyors allows businesses to easily scale their operations up or down, making them ideal for coping with market fluctuations and growth.
- Efficiency in E-commerce: The e-commerce boom requires rapid and accurate order fulfillment. Powered roller conveyors can significantly increase the speed and accuracy of order processing, making them indispensable in e-commerce logistics.
- Globalization of Manufacturing: As manufacturing continues to globalize, powered roller conveyors facilitate the efficient movement of goods across international production lines, enhancing global supply chain integration.
- Customization and Personalization: The trend towards product customization and personalization increases the complexity of material handling. Powered roller conveyors, with their flexibility and adaptability, are well-suited to meet these challenges.
- Resilience and Reliability: In an era where supply chain disruptions have become more frequent, the reliability and resilience offered by advanced powered roller conveyor systems help ensure continuity of operations and mitigate risks.
The future of powered roller conveyor systems is characterized by technological advancements that promise enhanced automation, efficiency, and sustainability. As these systems become increasingly integral to global supply chains, their role in driving operational excellence and meeting the demands of tomorrow’s markets cannot be underestimated.
FAQs About Powered Roller
A power roller, also known as a motorized roller, is a conveyor system component designed to move materials efficiently along a path. Unlike traditional conveyor systems that may rely on an external power source and a series of belts or chains, each power roller contains its own motor. This design allows for more precise control over the movement and speed of materials on the conveyor, leading to improved efficiency and productivity in various industrial applications.
A powered roller conveyor is an automated material handling system composed of a series of power rollers. Each roller in the system is equipped with its own motor, enabling independent control of sections of the conveyor. This modularity allows for the accumulation of materials without the need for additional space or complex mechanisms, making powered roller conveyors ideal for industries requiring precise material handling, such as manufacturing, distribution, and packaging.
A motor roller works by incorporating a motor within the roller itself, which drives the rotation of the roller when activated. This self-contained unit receives power and control signals through connections in the conveyor frame or via wireless technology. When the motor is activated, it turns the roller, moving the conveyor belt or the materials resting on the roller. The design allows for individual control of each roller, enabling complex material handling operations like sorting, accumulation, and directional changes.
A drive roller operates by converting the power from a motor into rotational force, which is then applied to the conveyor belt or directly to the materials being conveyed. In powered roller conveyors, the drive roller is often a motorized roller equipped with an internal motor. The motor’s activation causes the drive roller to rotate, propelling the conveyor belt and any materials on it forward. Drive rollers are crucial for maintaining the desired movement and speed of the conveyor system, ensuring efficient material handling processes.
Last Updated on July 12, 2024 by Jordan Smith
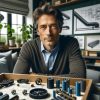
Jordan Smith, a seasoned professional with over 20 years of experience in the conveyor system industry. Jordan’s expertise lies in providing comprehensive solutions for conveyor rollers, belts, and accessories, catering to a wide range of industrial needs. From initial design and configuration to installation and meticulous troubleshooting, Jordan is adept at handling all aspects of conveyor system management. Whether you’re looking to upgrade your production line with efficient conveyor belts, require custom conveyor rollers for specific operations, or need expert advice on selecting the right conveyor accessories for your facility, Jordan is your reliable consultant. For any inquiries or assistance with conveyor system optimization, Jordan is available to share his wealth of knowledge and experience. Feel free to reach out at any time for professional guidance on all matters related to conveyor rollers, belts, and accessories.