Maximizing Efficiency with Precision Idler Rollers
In the realm of conveyor systems, precision idler rollers stand as critical components, ensuring the seamless operation and efficiency of material handling processes across various industries. These rollers, crafted with meticulous attention to detail, uphold the conveyor belt’s integrity, facilitating smooth and uninterrupted movement of goods. The importance of precision in the manufacturing of idler rollers cannot be overstated; it is the cornerstone upon which the reliability and efficiency of a conveyor system rest. Precision idler rollers are designed to meet exacting specifications, reducing wear and tear on the conveyor belt and minimizing downtime caused by maintenance and repairs. This precision directly translates to enhanced operational efficiency, longer system lifespans, and improved overall reliability. As such, understanding the role and significance of precision idler rollers is essential for anyone looking to optimize their conveyor system’s performance and durability.
What is Precision Idler Rollers
Precision idler rollers play a pivotal role in the functionality and efficiency of conveyor systems, which are integral to numerous industries worldwide. These components are designed to support and guide conveyor belts, ensuring smooth operation and the effective transportation of materials. This section delves into the definition, function, and importance of precision in idler rollers, providing specific examples to illustrate their critical role in enhancing conveyor belt performance and lifespan.
Definition and Function of Idler Rollers in Conveyor Belts
Idler rollers are cylindrical rods that form part of the conveyor framework, around which conveyor belts rotate. They are strategically placed along the conveyor belt system to provide support, reduce friction, and maintain tension within the belt. Precision idler rollers, in particular, are manufactured with exacting standards to ensure optimal performance.
- Support and Shape: They support the weight of the belt and the materials being transported. For instance, in mining operations, idler rollers support heavy loads of mined materials.
- Reduce Belt Wear: By minimizing friction and preventing unnecessary strain, they extend the belt’s lifespan, crucial in packaging lines where belts move at high speeds.
- Maintain Tension: They help maintain the correct tension, ensuring the belt operates smoothly, which is essential in food processing conveyors to prevent slippage of food items.
- Guide the Belt: Precision idler rollers ensure the belt moves in a straight line, critical in airport baggage handling systems to ensure luggage reaches the correct destination.
- Facilitate Material Flow: In agricultural applications, they help in the gentle handling of grains and other products, preventing damage during transport.
The Role of Precision in Enhancing Performance and Lifespan
The precision in manufacturing idler rollers significantly impacts the performance and lifespan of conveyor systems. Precision ensures that the rollers have the exact dimensions, tolerances, and material properties needed for their specific application, leading to several benefits.
- Increased Efficiency: In automotive assembly lines, precision idler rollers ensure smooth transitions and precise movements, reducing downtime and increasing production efficiency.
- Reduced Maintenance Costs: In the logistics and distribution sector, precisely engineered rollers minimize the need for frequent replacements, lowering maintenance costs.
- Enhanced Product Quality: In the pharmaceutical industry, precision rollers contribute to maintaining the integrity of sensitive products by ensuring gentle handling and consistent speeds.
- Improved Safety: In heavy industries, such as steel manufacturing, precision in rollers contributes to safer operations by reducing the risk of belt slippage and accidents.
- Longer System Lifespan: In mining operations, precision-engineered idler rollers can withstand harsh conditions, extending the conveyor system’s overall lifespan.
Understanding precision idler rollers involves recognizing their critical role in supporting and guiding conveyor belts across various industries. The precision in their design and manufacture is key to enhancing the performance, efficiency, and lifespan of conveyor systems. By ensuring that these components meet high standards of quality and accuracy, industries can achieve smoother operations, reduced maintenance costs, and improved safety in material handling processes.
Key Features of Precision Idler Rollers
Precision idler rollers are essential components in the material handling industry, offering support and stability to conveyor belts while ensuring smooth and efficient operations. These rollers are meticulously designed and manufactured to meet high standards of precision and durability. Below, we delve into the key features of precision idler rollers, highlighting their significance in enhancing conveyor system performance.
Equal Troughing Idlers for Carrying Side Support
One of the standout features of precision idler rollers is the inclusion of equal troughing idlers. These idlers are specifically engineered for the carrying side of conveyor systems, providing optimal support for the belt as it transports materials. The equal troughing design ensures that the belt maintains a uniform and stable shape over the length of the conveyor, minimizing spillage and enhancing the efficiency of material transport. By evenly distributing the load, these idlers reduce conveyor belt wear and tear, extending its lifespan and reducing maintenance requirements.
PPI Retro Rolls for Compatibility with Various Frames
Another key feature of precision idler rollers is the integration of PPI (Precision Pulley & Idler) Retro Rolls. These rolls are designed for seamless compatibility with a wide range of conveyor frames, making them a versatile choice for upgrading existing systems or integrating into new installations. The PPI Retro Rolls feature a unique design that allows for easy replacement and installation, ensuring minimal downtime and enhancing operational efficiency. Their compatibility with various frames also means that they can be used in a diverse range of applications, from mining and aggregate processing to packaging and distribution.
Spring Impact Rolls for Flexible Impact Absorption
Precision idler rollers also incorporate spring impact rolls, a critical feature for applications where the conveyor system is subject to heavy loads or impact. These rolls are equipped with a spring mechanism that provides flexible impact absorption, protecting the conveyor belt and the structure from damage. The spring impact rolls are particularly beneficial at loading points, where the material drops onto the conveyor belt, as they help to dissipate the energy of the impact. This not only prolongs the life of the conveyor belt but also reduces noise and vibration, contributing to a safer and more pleasant working environment.
Precision idler rollers are equipped with a range of features designed to enhance the performance and longevity of conveyor systems. From equal troughing idlers that provide stable support to the carrying side, to PPI Retro Rolls that offer compatibility with various frames, and spring impact rolls that ensure flexible impact absorption, these components are integral to the efficient operation of material handling systems. By incorporating precision idler rollers into their conveyor systems, businesses can achieve higher levels of productivity and reliability, ensuring smooth and effective material transport.
Guide Rollers: Enhancing Conveyor Performance with Precision Idler Rollers
Guide rollers, particularly when designed as precision idler rollers, play a pivotal role in enhancing the performance of conveyor systems. These specialized rollers are integral to maintaining the conveyor framework’s integrity and ensuring optimal belt alignment. By doing so, they not only protect the conveyor belt from undue wear and tear but also contribute significantly to the system’s overall efficiency and reliability.
Protecting Conveyor Framework and Belt Alignment
Precision idler rollers are engineered to provide steadfast support and guidance to the conveyor belt, ensuring it remains correctly aligned with the conveyor’s structural framework. This alignment is crucial for preventing the belt from drifting off its intended path, which can lead to uneven wear, potential damage to the conveyor framework, and even unexpected downtime. By maintaining proper alignment, precision idler rollers help extend the lifespan of both the belt and the conveyor structure, ensuring smooth and efficient operations.
Belt Protection and Damage Prevention Strategies
The design and implementation of precision idler rollers incorporate various strategies aimed at protecting the conveyor belt and preventing damage.
- Impact Absorption: Precision idler rollers are often equipped with shock-absorbing features that mitigate the impact of heavy or abrasive materials as they are loaded onto the conveyor. This reduces the risk of punctures, tears, or other forms of damage to the belt.
- Reduced Friction: The materials and finishes used in manufacturing precision idler rollers are selected to minimize friction between the belt and the rollers. This not only prolongs the belt’s life by reducing wear but also lowers energy consumption by the conveyor system.
- Material Compatibility: Precision idler rollers are available in a variety of materials and coatings to ensure compatibility with the type of goods being conveyed. For instance, rollers with non-stick coatings are used to prevent adhesive materials from sticking to the belt and rollers, thereby avoiding damage and contamination.
- Temperature Resistance: For applications involving extreme temperatures, precision idler rollers are designed with materials that can withstand such conditions without degrading. This is essential for preventing heat-related damage to the belt in high-temperature environments or cracking in cold conditions.
- Corrosion Resistance: In environments where corrosive substances are present, precision idler rollers are constructed from materials resistant to corrosion. This ensures the longevity of the rollers themselves and protects the conveyor belt from being damaged by corroded particles or weakened roller structures.
The integration of precision idler rollers into conveyor systems is a testament to the importance of detail-oriented engineering in material handling technologies. By focusing on protecting the conveyor framework and ensuring belt alignment, along with implementing belt protection and damage prevention strategies, these rollers significantly enhance the performance, efficiency, and reliability of conveyor systems.
Precision Rolls by Maxcess International: Elevating Performance with Precision Idler Rollers
Maxcess International stands at the forefront of innovation in the material handling and processing industry, offering a comprehensive range of precision-engineered rolls designed to meet the exacting demands of high-precision applications. Their portfolio of precision idler rollers is meticulously crafted to enhance efficiency, accuracy, and reliability across various sectors, including printing, packaging, and manufacturing. This section delves into the specifics of Maxcess International’s precision rolls, highlighting their product subcategories and the unique solutions they provide.
Overview of Precision-Engineered Rolls for High-Precision Applications
Maxcess International’s precision idler rollers are synonymous with unparalleled precision and quality. Engineered with state-of-the-art technology and materials, these rollers are designed to deliver optimal performance in the most demanding environments. Whether it’s for guiding, tensioning, or supporting conveyor belts, these precision rolls ensure smooth operation, minimal downtime, and extended equipment lifespan. Their commitment to precision engineering is evident in every product, making them a go-to solution for businesses seeking to optimize their operations with high-quality components.
Highlighting Product Subcategories and Specific Solutions
Maxcess International’s range of precision idler rollers is diverse, catering to a wide array of industrial needs.
- Ultra-Precision Rolls: Designed for applications requiring the highest level of accuracy, these rolls feature ultra-precise bearings and surface finishes. They are ideal for the printing industry, where even the slightest deviation can lead to significant quality issues.
- Thermal Transfer Rolls: These precision idler rollers are engineered to manage temperature effectively, making them perfect for processes involving heat-sensitive materials. They find extensive use in the packaging industry, where maintaining material integrity is paramount.
- Corrosion-Resistant Rolls: Constructed from materials that withstand corrosive environments, these rollers are suited for chemical processing or outdoor applications. They ensure long-term reliability and performance, despite exposure to harsh conditions.
- Lightweight Rolls: Maxcess offers precision idler rollers made from advanced composites or lightweight metals, reducing overall system weight. This feature is particularly beneficial in aerospace and automotive manufacturing, where every ounce matters.
- Custom-Engineered Solutions: Recognizing that each application has unique requirements, Maxcess International provides custom-engineered precision idler rollers. Whether it’s a specific diameter, length, or material composition, they can tailor their products to meet the exact needs of their clients, such as specialized rollers for the food processing industry that require compliance with strict hygiene standards.
Maxcess International’s precision idler rollers embody the pinnacle of precision engineering, offering tailored solutions that meet the diverse needs of high-precision applications. By continuously innovating and expanding their product line, Maxcess ensures that industries reliant on precision rolls have access to the highest quality components, thereby enhancing their operational efficiency, product quality, and overall competitiveness.
Coast Controls’ Approach to Precision Idler Rollers
Since its inception in 1992, Coast Controls has established a sterling reputation for its uncompromising quality in the manufacturing of precision idler rollers. Their approach combines advanced engineering, meticulous manufacturing processes, and a deep commitment to customer satisfaction. This section explores how Coast Controls has set a benchmark in the industry for precision idler rollers, highlighting their customization capabilities, balancing expertise, and unparalleled customer service.
High-Quality Manufacturing Since 1992
Coast Controls has been at the forefront of precision idler roller manufacturing for over three decades. Their longevity in the industry is a testament to their dedication to quality and innovation.
- Use of Premium Materials: Coast Controls selects only the finest materials for their precision idler rollers, ensuring durability and performance under demanding conditions.
- Advanced Manufacturing Techniques: Leveraging the latest in manufacturing technology, they achieve tolerances that exceed industry standards, ensuring each roller operates with exceptional precision.
- Rigorous Quality Control: Every precision idler roller undergoes stringent quality checks, from initial design to final assembly, guaranteeing that only flawless products reach their customers.
- Innovative Design Solutions: Coast Controls continuously innovates, developing new designs that enhance roller performance and adaptability across various applications.
- Sustainability Practices: They incorporate sustainable manufacturing practices, reflecting their commitment to environmental responsibility alongside quality production.
Customization and Balancing for Specific Applications
Understanding that each application has unique requirements, Coast Controls excels in providing customized precision idler rollers tailored to specific needs. Their approach to customization and balancing includes:
- Tailored Dimensions: They manufacture rollers to exact customer specifications, including length, diameter, and material composition, ensuring a perfect fit for the intended application.
- Application-Specific Design: Whether for high-speed printing or delicate material handling, Coast Controls designs rollers with the application’s specific challenges in mind.
- Precision Balancing: Each roller is precisely balanced to eliminate vibration and wear, enhancing both the roller’s lifespan and the overall system’s efficiency.
- Specialized Coatings: Offering a variety of coatings, from non-stick to corrosion-resistant, they ensure the roller’s surface is suited to the material it will be in contact with.
- Rapid Prototyping: Coast Controls provides rapid prototyping services, allowing customers to test and refine roller designs before full-scale production.
Satisfaction Guarantee and Customer Service Focus
Coast Controls stands behind their precision idler rollers with a satisfaction guarantee, underpinned by a customer service focus that sets them apart.
- Consultative Approach: Their team works closely with clients to understand their needs and challenges, ensuring the proposed solutions are perfectly aligned with customer requirements.
- Responsive Support: Coast Controls prides itself on its responsive customer service, addressing queries and concerns promptly to ensure customer satisfaction.
- After-Sales Service: They offer comprehensive after-sales support, including maintenance tips, spare parts, and repair services, ensuring their rollers continue to perform optimally.
- Training and Education: Coast Controls provides training and educational resources to help customers maximize the benefits of their precision idler rollers.
- Continuous Improvement: Feedback from customers is taken seriously, driving continuous improvement in their products and services.
Coast Controls’ approach to precision idler rollers—emphasizing high-quality manufacturing, customization for specific applications, and a strong focus on customer satisfaction—has made them a trusted partner in industries requiring the utmost in precision and reliability. Their dedication to excellence ensures that their rollers not only meet but exceed customer expectations, setting a high standard in the field of material handling and processing.
Selecting the Right Precision Idler Roller
Choosing the appropriate precision idler rollers for your conveyor system is a critical decision that can significantly impact the efficiency, reliability, and overall performance of your operations. Several factors must be considered to ensure the selection of the most suitable rollers, including the material of the roller, the specific application it will be used for, and the environmental conditions it will be exposed to. Additionally, understanding the offerings and insights provided by leading manufacturers like Precision Pulley and Idler (PPI) can guide you in making an informed choice.
Factors to Consider
When selecting precision idler rollers, it’s essential to evaluate various aspects to ensure they meet the requirements of your specific application. Here are five examples for each of the key factors:
Material
- Steel Rollers: Ideal for heavy-duty applications where durability and strength are paramount, such as mining and quarrying.
- Stainless Steel Rollers: Best suited for corrosive environments or where hygiene is a concern, like in food processing or chemical industries.
- Plastic Rollers: A lightweight option for applications requiring low noise and gentle handling of delicate products, such as in packaging or electronics manufacturing.
- Rubber-Coated Rollers: Provide additional grip and protection against abrasion, useful in paper and printing industries.
- Composite Material Rollers: Offer a balance between strength and weight, suitable for applications with specific requirements, such as aerospace or automotive assembly lines.
Application
- High-Speed Conveyors: Require rollers designed for minimal vibration and noise, ensuring smooth operation.
- Bulk Material Handling: Rollers must be robust and capable of withstanding heavy loads without deformation.
- Precision Manufacturing: Rollers with extremely tight tolerances are necessary to maintain product placement accuracy.
- Temperature-Sensitive Processes: Rollers designed to operate efficiently in high or low temperatures, depending on the application.
- Chemically Aggressive Environments: Rollers made from materials resistant to corrosion and chemical damage.
Environmental Conditions
- Dusty Environments: Rollers with sealed bearings to prevent dust ingress, ensuring longevity and reliability.
- Wet Conditions: Stainless steel or plastic rollers that resist water damage and prevent rust formation.
- High-Temperature Areas: Rollers fabricated from heat-resistant materials to maintain performance under extreme heat.
- Outdoor Applications: UV-resistant rollers that can withstand exposure to sunlight without degrading.
- Electrostatic Sensitive Areas: Antistatic rollers to prevent the buildup of static electricity, crucial in electronics manufacturing.
Precision Pulley and Idler (PPI) Offerings and Catalog Insights
PPI is renowned for its comprehensive range of precision idler rollers, designed to meet the diverse needs of various industries. Their catalog provides insights into the specifications, applications, and advantages of their precision rollers, including:
- Customization Options: PPI offers custom-engineered solutions to meet unique operational requirements, ensuring optimal performance.
- Technology Integration: Their rollers incorporate advanced technologies, such as self-aligning features for improved belt tracking and reduced maintenance.
- Material Selection Guide: The catalog includes a detailed guide on material properties and their suitability for different environmental conditions and applications.
- Installation and Maintenance Tips: PPI provides valuable information on the proper installation and maintenance of their rollers, extending their service life.
- Case Studies: Real-world applications and testimonials highlight the effectiveness of PPI’s precision idler rollers in enhancing conveyor system performance.
Selecting the right precision idler rollers involves careful consideration of the material, application, and environmental conditions, along with leveraging the expertise and offerings of industry leaders like PPI. By taking these factors into account, you can ensure the selection of idler rollers that will contribute to the efficiency, reliability, and success of your conveyor system.
Innovations and Trends in Precision Idler Rollers
The field of material handling and conveyor systems is witnessing rapid advancements, with precision idler rollers at the forefront of innovation. These developments are not only enhancing the efficiency and reliability of conveyor systems but are also setting new standards for performance in various industries. Here, we explore the latest innovations and trends in precision idler roller technology, highlighting five key advancements that are shaping the future of material handling.
Latest Developments and Advancements in Idler Roller Technology
- Smart Idler Rollers: Incorporating sensors and IoT (Internet of Things) technology, smart idler rollers can monitor their own condition and the environment around them. This innovation allows for real-time data collection on roller performance, wear levels, and operational temperatures, enabling predictive maintenance and reducing downtime.
- High-Performance Materials: The use of advanced materials such as carbon fiber, high-grade polymers, and specialized alloys is becoming more prevalent. These materials offer superior strength-to-weight ratios, corrosion resistance, and reduced inertia, leading to more energy-efficient operations, especially in high-speed applications.
- Self-Lubricating Roller Designs: New precision idler rollers feature self-lubricating bearing systems that significantly extend the life of the rollers while minimizing maintenance requirements. These systems are particularly beneficial in environments where maintenance access is challenging or where contamination from lubricants must be avoided.
- Thermal Management Technologies: With the rise in applications requiring high-speed operation, managing the heat generated by idler rollers has become critical. Innovations in thermal management, including heat-dissipating coatings and internal cooling systems, ensure that rollers maintain optimal performance levels even under intense operating conditions.
- Modular and Reconfigurable Designs: Flexibility is a key trend in conveyor system design, with precision idler rollers now available in modular configurations. These designs allow for easy reconfiguration of conveyor layouts to meet changing production needs, supporting scalability and adaptability in manufacturing and processing facilities.
These advancements in precision idler roller technology are driving significant improvements in conveyor system performance, efficiency, and reliability. By embracing these innovations, industries can achieve higher throughput, reduce operational costs, and enhance overall productivity. The future of material handling looks promising, with precision idler rollers continuing to play a pivotal role in the evolution of conveyor systems.
Case Studies: Success Stories of Precision Idler Rollers in Action
The deployment of precision idler rollers across a variety of sectors has underscored their critical role in enhancing operational efficiency and solving complex challenges. These real-world success stories illustrate the transformative power of precision idler rollers, showcasing their ability to streamline processes, mitigate issues, and drive productivity forward.
Real-World Examples of Improved Efficiency
- Logistics and Distribution Hub: A major logistics company faced challenges with their conveyor system’s reliability, affecting parcel sorting speed and accuracy. By integrating precision idler rollers designed for high-speed applications, the hub increased its sorting capacity by over 25%, significantly improving parcel handling efficiency and reducing transit times for shipments.
- Automotive Parts Manufacturer: In an effort to reduce production line stoppages, an automotive parts manufacturer replaced their existing conveyor rollers with custom-designed precision idler rollers. These rollers featured enhanced load-bearing capabilities and reduced vibration, leading to a smoother operation and a 15% increase in production line uptime.
- Textile Manufacturing Plant: A textile manufacturer struggling with frequent conveyor belt misalignments implemented precision idler rollers with self-aligning properties. This upgrade resulted in a 20% increase in fabric production speed and a significant reduction in material waste, directly impacting the plant’s bottom line.
- Electronics Assembly Facility: To address electrostatic discharge (ESD) issues in their assembly line, an electronics manufacturer opted for precision idler rollers with antistatic features. This strategic change not only protected sensitive electronic components from ESD damage but also enhanced the assembly line’s efficiency by ensuring uninterrupted operations.
- Agricultural Equipment Manufacturer: Facing challenges with heavy and uneven loads on their assembly line, this manufacturer incorporated heavy-duty precision idler rollers. The new rollers improved load distribution and conveyor belt stability, leading to a 10% increase in assembly line speed and a reduction in equipment wear and tear.
Real-World Examples of Problem-Solving
- Pharmaceutical Packaging Line: A pharmaceutical company was experiencing product damage due to static buildup on their packaging line. By installing precision idler rollers with conductive properties, they eliminated static issues, ensuring the integrity of sensitive pharmaceutical products and significantly reducing product damage rates.
- Food Processing Facility: A food processing facility needed to meet stringent hygiene standards while maintaining production efficiency. By implementing stainless steel precision idler rollers, they not only adhered to hygiene regulations but also increased conveyor system reliability, reducing cleaning and maintenance downtime by 30%.
- Mining Operation: In a harsh mining environment, abrasive materials and heavy loads were causing frequent conveyor system failures. The introduction of ultra-durable precision idler rollers designed for extreme conditions led to a 50% reduction in maintenance interventions and extended the lifespan of the conveyor system.
- Recycling Plant: A recycling plant was facing inefficiencies due to frequent jams and material blockages. Precision idler rollers with a unique design for enhanced material flow were introduced, solving the jamming issue and increasing material processing capacity by 25%.
- Airport Baggage Handling System: An airport updated its baggage handling system with precision idler rollers equipped with shock-absorbing capabilities. This upgrade significantly reduced luggage damage and improved the overall efficiency of baggage handling, leading to higher passenger satisfaction and reduced claims for damaged luggage.
These case studies demonstrate the critical role precision idler rollers play in optimizing operations across various industries. By leveraging the unique features and benefits of precision idler rollers, organizations can address specific challenges, improve operational efficiency, and achieve significant advancements in their production and handling processes.
Last Updated on May 23, 2024 by Jordan Smith
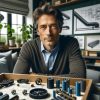
Jordan Smith, a seasoned professional with over 20 years of experience in the conveyor system industry. Jordan’s expertise lies in providing comprehensive solutions for conveyor rollers, belts, and accessories, catering to a wide range of industrial needs. From initial design and configuration to installation and meticulous troubleshooting, Jordan is adept at handling all aspects of conveyor system management. Whether you’re looking to upgrade your production line with efficient conveyor belts, require custom conveyor rollers for specific operations, or need expert advice on selecting the right conveyor accessories for your facility, Jordan is your reliable consultant. For any inquiries or assistance with conveyor system optimization, Jordan is available to share his wealth of knowledge and experience. Feel free to reach out at any time for professional guidance on all matters related to conveyor rollers, belts, and accessories.