Prok Conveyor Idlers: Brand Excellence and Features
In the realm of material handling, Prok conveyor idlers stand as a pivotal component, essential for the efficient functioning of conveyor systems. Fundamentally, a conveyor idler is a cylindrical rod, pivotal in supporting and guiding the conveyor belt. These idlers, particularly the ones from Prok, are designed to facilitate the smooth movement of the belt, reducing friction and wear. The role of Prok conveyor idlers extends beyond mere support; they play a crucial role in maintaining the belt’s alignment and tension, ensuring the longevity and efficiency of the conveyor system. Their importance is underscored in heavy-duty industries where the reliability and durability of conveyor systems are paramount. Prok’s expertise in crafting these idlers ensures they meet the rigorous demands of various industrial applications, making them an indispensable part of modern conveyor systems.
Overview of Prok Conveyor Idlers
The Prok Brand and Industry Standing: Prok has established itself as a leader in the conveyor idler market, known for its commitment to quality and innovation. With years of experience and a focus on technological advancement, Prok has earned a reputation for reliability and excellence in the material handling industry. Their products are widely recognized for their durability and efficiency, making Prok a go-to brand for businesses seeking dependable conveyor solutions.
Unique Features of Prok Conveyor Idlers: What sets Prok conveyor idlers apart are their distinctive design elements. These idlers incorporate advanced sealing technologies, which are crucial for protecting against environmental elements like dust and water. This feature extends the life of the idlers and maintains their efficiency. Additionally, Prok idlers are equipped with high-grade bearings, ensuring smooth operation and reducing the risk of breakdowns.
Market Advantages of Prok Conveyor Idlers: The design and construction of Prok conveyor idlers bring significant market advantages. They are specifically engineered to minimize conveyor downtime and maintenance requirements, which is a critical factor for industries where time is money. These idlers enhance the overall efficiency of conveyor systems, making them more cost-effective in the long run. Prok’s focus on customer needs and continuous improvement has led to idlers that perform exceptionally well in various operational environments, from mining to bulk material handling.
Prok conveyor idlers stand out in the market due to their robust design, innovative features, and the brand’s commitment to quality and customer satisfaction. These factors collectively contribute to Prok’s esteemed position in the conveyor industry.
Sizes and Specifications of Prok Conveyor Idlers
Prok conveyor idlers are designed to cater to a wide range of industrial needs, with sizes varying to suit different applications. Below is a table showcasing the different sizes of Prok idlers and their typical applications:
Prok Idler SizeBelt Width RangeTypical Applications Small Up to 500 mmLight-duty operations such as packaging lines, small-scale mining Medium 500mm to 1000 mmGeneral-purpose conveyors, manufacturing, and processing plantsLarge1000 mm to 1800 mmHeavy-duty applications like bulk material handling, large-scale miningExtra-Large1800 mm and aboveExtreme-duty operations, high-volume bulk handling, large-scale mining operations:
Prok Idler Size | Belt Width Range | Typical Applications |
Small | Up to 500 mm | Light-duty operations such as packaging lines, small-scale mining |
Medium | 500 mm to 1000 mm | General-purpose conveyors, manufacturing, and processing plants |
Large | 1000 mm to 1800 mm | Heavy-duty applications like bulk material handling, large-scale mining |
Extra-Large | 1800 mm and above | Extreme-duty operations, high-volume bulk handling, large-scale mining operations |
When selecting the appropriate Prok idler size, it’s essential to consider both the belt width and the load capacity of the conveyor system. The belt width determines the physical space available for the idler, while the load capacity dictates the amount of support needed. For instance, a conveyor system with a narrow belt width and low load capacity would be best served by a small-sized Prok idler. Conversely, a system with a wide belt and high load capacity would require a large or extra-large Prok idler to ensure stability and efficiency.
Prok provides comprehensive guidelines to help customers choose the right idler size. These guidelines take into account the specific requirements of each conveyor system, ensuring that the selected Prok conveyor idlers enhance the system’s performance and longevity. By carefully matching the idler size to the conveyor’s specifications, Prok ensures optimal functionality and reduced wear and tear, leading to longer service life and lower maintenance costs.
Components and Construction of Prok Conveyor Idlers
Prok conveyor idlers are engineered with precision, incorporating various components that contribute to their high performance and durability. The main components and construction aspects include:
Bearings: Prok idlers are equipped with high-quality bearings that are key to their smooth operation. These bearings are designed to withstand heavy loads and reduce rotational friction, which is crucial in maintaining the efficiency of the conveyor system. Prok’s bearings are also known for their longevity, significantly reducing the need for frequent replacements.
Sealing Systems: The sealing systems in Prok conveyor idlers are advanced and robust, providing excellent protection against dust, water, and other contaminants. This feature is vital for maintaining the integrity of the bearings and other internal components, especially in harsh operating environments.
Materials: Prok idlers are constructed using premium-grade materials that ensure strength and durability. The materials are chosen for their wear resistance and ability to withstand various environmental conditions, from extreme temperatures to corrosive substances.
Manufacturing Processes: Prok employs state-of-the-art manufacturing processes to produce its conveyor idlers. This includes precision engineering techniques to ensure that each component fits perfectly and functions optimally. The manufacturing process also involves rigorous testing and quality control measures, ensuring that every Prok idler meets the highest standards of quality and reliability.
The combination of these components and manufacturing processes makes Prok conveyor idlers stand out in the market. They are not only reliable and efficient but also require minimal maintenance, making them a cost-effective solution for conveyor systems in various industrial applications.
Types of Prok Conveyor Idlers
Prok conveyor idlers come in various types, each designed to meet specific functional requirements of conveyor systems. The characteristics, applications, and advantages of these idler types are as follows:
Type of Prok Idler | Characteristics | Applications | Advantages |
Carrying Idlers | Designed to support the conveyor belt and material weight on the carrying side of the belt. Typically come in sets of 3-5 rollers. | Used in the main conveying section of the conveyor system. | Provide optimal support and maintain belt alignment, enhancing the belt’s lifespan. |
Return Idlers | Support the return side of the conveyor belt. Usually, a single roller design. | Installed on the underside of the conveyor system where the belt returns after carrying the material. | Prevent sagging and misalignment of the belt, ensuring smooth operation. |
Impact Idlers | Equipped with rubber rings or discs to absorb the impact of falling materials. | Positioned at loading points where material is dropped onto the belt. | Protect the belt and structure from damage due to impact, reducing maintenance costs. |
Guide Idlers | Designed to control the belt’s lateral movement. | Used in areas where the conveyor belt may experience side movement. | Prevent belt misalignment and reduce wear on the edges of the belt. |
Self-aligning Idlers | Automatically adjust the belt alignment. | Used in sections of the conveyor where misalignment is likely to occur. | Reduce maintenance time by automatically correcting belt misalignment. |
Each type of Prok conveyor idler serves a specific purpose, enhancing the efficiency and longevity of conveyor systems. The carrying idlers provide crucial support for the belt and material, while return idlers ensure the belt returns smoothly. Impact idlers are essential for protecting the belt at loading zones, and guide idlers maintain the belt’s path. Self-aligning idlers are particularly beneficial in maintaining optimal belt alignment with minimal manual adjustment. Prok’s range of idlers is designed to meet the diverse needs of various industries, ensuring reliable and efficient conveyor operations.
Prok Conveyor Idler Dimensions
Prok conveyor idlers are designed to meet a wide range of industrial requirements, offering both standard dimensions and custom options. The standard dimensions of Prok idlers cater to the most common conveyor sizes and are readily available for various applications. These standard sizes are meticulously engineered to ensure compatibility with a broad spectrum of conveyor systems, providing optimal performance in terms of load-bearing capacity and belt alignment.
For unique or specialized conveyor systems, Prok offers custom idler solutions. These are tailored to specific requirements, such as unusual belt widths, higher load capacities, or unique environmental conditions. Prok’s custom idlers are designed with the same attention to detail and quality as their standard counterparts, ensuring they meet the specific needs of each application.
When choosing the right size and dimensions of Prok conveyor idlers, several factors need to be considered:
1. Conveyor Belt Width: The width of the conveyor belt is the primary determinant of the idler size. Prok idlers are designed to accommodate a range of belt widths, ensuring proper support and alignment.
2. Load Capacity: The weight and volume of the material being conveyed influence the choice of idler size. Heavier loads require robust idlers with larger dimensions to ensure stability and longevity.
3. Application Environment: Factors such as the operating environment (e.g., temperature, humidity, exposure to chemicals) can dictate the need for custom idler dimensions. Prok can provide idlers made from materials and with coatings that are suited to specific environmental conditions.
4. Operational Speed: The speed at which the conveyor operates can also impact the choice of idler size. Higher speeds may require idlers designed for more dynamic loads.
By considering these factors, users can select the most appropriate Prok idler dimensions for their conveyor system, ensuring efficient operation and reduced wear and tear. Prok’s expertise in conveyor technology allows them to provide valuable guidance in this selection process, ensuring that each conveyor system is equipped with the ideal idler solution.
Specifications and Technical Parameters of Conveyor Idlers
Prok conveyor idlers are characterized by a set of technical specifications and performance parameters that define their suitability for various applications. These specifications typically include:
Roller Diameter: Indicates the size of the idler and is chosen based on the belt width and load requirements.
Bearing Type and Size: Determines the load-bearing capacity and operational life of the idler.
Shell Thickness: Refers to the thickness of the idler’s tube, impacting its strength and durability.
Shaft Diameter: Affects the idler’s ability to withstand load and rotational forces.
Seal Type: Defines the idler’s resistance to environmental factors like dust and moisture.
Load Capacity: Specifies the maximum load the idler can support.
Speed Rating: Indicates the maximum operational speed at which the idler can function effectively.
Interpreting and applying these technical data involves understanding the specific requirements of the conveyor system. For instance, a conveyor system with a wide belt carrying heavy loads would require idlers with a larger roller diameter, robust bearings, and a higher load capacity. Similarly, in environments with high levels of dust or moisture, idlers with better sealing and thicker shells would be more appropriate.
When selecting Prok conveyor idlers, it’s crucial to match these technical specifications with the operational conditions of the conveyor system. This ensures that the idlers not only fit the system physically but also perform optimally under the given load, speed, and environmental conditions. Proper interpretation and application of these technical parameters lead to increased efficiency, reduced maintenance costs, and extended lifespan of both the idlers and the conveyor system as a whole. Prok’s expertise in conveyor technology provides valuable guidance in this selection process, ensuring that each conveyor system is equipped with idlers that meet its specific needs.
How to Choose the Right Conveyor Idler
Selecting the right Prok conveyor idlers is a critical decision that impacts the efficiency and longevity of a conveyor system. To ensure the optimal choice of Prok conveyor idlers, several key factors must be considered:
1. Belt Width: The width of the conveyor belt is the primary factor in selecting idler size. Prok offers idlers that are compatible with a range of belt widths. The idler must be wide enough to support the belt and the material being conveyed without causing overhang or instability.
2. Load Capacity: The weight of the material being transported is crucial. Heavier loads require idlers with stronger construction and higher load-bearing capacity. Prok provides idlers designed for both light-duty and heavy-duty applications.
3. Operating Speed: The speed at which the conveyor operates affects the choice of idlers. High-speed conveyors need idlers that can handle the increased forces and potential vibrations. Prok idlers are rated for different speeds to ensure reliable performance.
4. Material Characteristics: The type of material being conveyed (e.g., abrasive, corrosive, fine, large lumps) influences the choice of idler type and material. Prok offers specialized idlers for different material types to enhance durability and efficiency.
5. Environmental Conditions: The operating environment, including temperature, humidity, and exposure to chemicals or moisture, dictates the need for specific idler types. Prok idlers come with various sealing and coating options to withstand different environmental conditions.
6. Maintenance and Accessibility: Consider the ease of maintenance and accessibility of the idlers. Prok designs idlers that are easy to install and maintain, reducing downtime and labor costs.
7. Lifespan and Durability: Evaluate the expected lifespan and durability of the idlers. Prok’s high-quality materials and manufacturing processes ensure that their idlers have a long service life, even in demanding conditions.
By carefully considering these factors, you can select Prok conveyor idlers that are perfectly suited to your conveyor system’s requirements. This not only ensures efficient operation but also minimizes maintenance needs and prolongs the lifespan of the conveyor system. Prok’s expertise and wide range of idler options make it possible to find the ideal solution for any conveyor application.
Application Cases of Prok Conveyor Idlers
Prok conveyor idlers have been successfully implemented in a variety of industries, demonstrating their versatility and effectiveness. These application cases highlight the adaptability and performance of Prok idlers across different sectors:
1. Mining Industry: In one of the largest iron ore mines, Prok idlers were used extensively. Their robust design and durability were crucial in handling the heavy and abrasive nature of iron ore. The idlers performed exceptionally well, leading to reduced downtime and maintenance costs.
2. Bulk Material Handling: A coal handling plant utilized Prok idlers for their conveyor systems. The idlers’ high load-bearing capacity and resistance to harsh conditions ensured smooth coal transportation, enhancing overall efficiency.
3. Agricultural Sector: Prok idlers were chosen for a grain handling conveyor system. Their gentle handling and reliability were key in preventing grain damage and loss during transport.
4. Manufacturing Industry: A leading car manufacturer implemented Prok idlers in their assembly line conveyors. The precision and smooth operation of Prok idlers contributed to an efficient and uninterrupted production process.
Customer feedback and case studies further reinforce the effectiveness of Prok conveyor idlers. Clients across these industries have reported significant improvements in conveyor performance, including longer operational life, reduced maintenance needs, and increased system reliability. These positive outcomes are a testament to Prok’s commitment to quality and customer satisfaction, making Prok conveyor idlers a trusted choice in diverse industrial applications.
Prok conveyor idlers have firmly established themselves as a leading solution in the conveyor industry, renowned for their reliability, durability, and innovative design. Their position in the market is not just a reflection of their current success but also a testament to their ongoing commitment to quality and customer satisfaction. Looking ahead, the future trends for Prok conveyor idlers are geared towards further innovations in durability, efficiency, and environmental sustainability. As industries continue to evolve, Prok is expected to remain at the forefront, adapting to new challenges and opportunities, particularly in areas like automation and smart conveyor technologies.
For readers considering Prok conveyor idlers, the recommendation is clear: these idlers offer a blend of reliability, efficiency, and innovation that is hard to match. Whether your operation is in mining, manufacturing, bulk material handling, or any other field with conveyor system needs, Prok idlers are designed to meet a wide range of challenges. As you move forward, consider the long-term benefits of investing in quality conveyor components. Prok’s commitment to excellence not only ensures optimal conveyor performance but also contributes to the overall success and sustainability of your operations.
FAQs on Prok conveyor idlers
1. What is the longest belt conveyor system?
The longest belt conveyor system in the world is located in the Western Sahara. It spans a length of about 98 kilometers (61 miles) and is used to transport phosphate from the mines in Bou Craa to the coast near El-Aaiún. This remarkable system can be seen from space and stands as a testament to the engineering capabilities in the field of material handling. The conveyor belt operates continuously, moving thousands of tons of phosphate ore every day across the desert landscape. This system not only exemplifies the scale at which conveyor technology can operate but also highlights its efficiency and effectiveness in transporting bulk materials over long distances. The longevity and durability of such a system are underpinned by meticulous maintenance and the use of high-quality components, including robust conveyor belts and precisely engineered idlers.
2. How many types of idlers are there in conveyor systems?
In conveyor systems, there are several types of idlers, each serving a specific purpose. The most common types include carrying idlers, return idlers, impact idlers, self-aligning idlers, and guide idlers. Carrying idlers support the weight of the material on the conveyor belt and are typically spaced evenly along the carrying side. Return idlers support the belt on the return side. Impact idlers are located at loading points where material is dropped onto the belt; they have a robust design to absorb the impact of the falling material. Self-aligning idlers help in maintaining the proper alignment of the belt, especially in long conveyor systems. Guide idlers prevent the belt from wandering or misaligning. Each type of idler plays a crucial role in the efficient functioning and longevity of a conveyor system.
3. What is the function of idlers in a conveyor system?
Idlers in a conveyor system serve several critical functions. Primarily, their role is to support the conveyor belt, ensuring it follows the correct trajectory. This support is vital on both the carrying side, where the material is transported, and the return side. Idlers play a key role in evenly distributing the material’s weight across the belt. This even distribution is crucial as it lessens the wear and tear on the belt and helps prevent any sagging.Additionally, certain types of idlers, like impact idlers, absorb the shock and impact at loading points, protecting the belt from damage. Self-aligning idlers are designed to keep the conveyor belt properly aligned, preventing issues like belt drift. Overall, idlers are essential for the smooth, efficient, and continuous operation of a conveyor system, significantly contributing to its longevity and reliability.
4. What is the size of a conveyor idler?
The size of a conveyor idler typically depends on the width of the conveyor belt and the load it needs to support. Idler diameters commonly range from about 100 mm to 150 mm. However, they can be larger or smaller based on the specific requirements of the conveyor system. The length of the idler is usually designed to match the width of the conveyor belt. For instance, wider belts in heavy-duty applications would require larger idlers to adequately support the belt and the material being conveyed. The size of the idler is crucial as it affects the idler’s ability to support the belt and influences the spacing between idlers. Manufacturers often provide a range of idler sizes to suit different types of conveyor systems and their respective operational needs.
5. What is the distance between carrying idlers?
The spacing between carrying idlers in a conveyor system, also referred to as idler spacing, is determined by various significant factors. These factors encompass the type of material being transported, the material’s weight, the conveyor belt’s width, and the operating speed of the conveyor. Typically, idler spacing varies from approximately one meter (around three feet) to slightly over one and a half meters (close to five feet). When the conveyor belt is tasked with carrying heavier loads or larger material volumes, it is customary to arrange the idlers in closer proximity. This configuration is of paramount importance to ensure robust support and the smooth movement of materials.This arrangement is essential for providing adequate support and evenly distributing the load across the belt. By placing the idlers closer, it helps in preventing the belt from sagging and minimizes the stress exerted on both the belt and the overall structure of the conveyor system. Conversely, lighter loads and slower conveyor speeds might allow for wider spacing between idlers. The correct idler spacing is crucial for optimizing the performance and extending the lifespan of the conveyor belt and the system as a whole.
Last Updated on February 4, 2024 by gramconveyor_admin
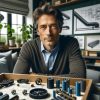
Jordan Smith, a seasoned professional with over 20 years of experience in the conveyor system industry. Jordan’s expertise lies in providing comprehensive solutions for conveyor rollers, belts, and accessories, catering to a wide range of industrial needs. From initial design and configuration to installation and meticulous troubleshooting, Jordan is adept at handling all aspects of conveyor system management. Whether you’re looking to upgrade your production line with efficient conveyor belts, require custom conveyor rollers for specific operations, or need expert advice on selecting the right conveyor accessories for your facility, Jordan is your reliable consultant. For any inquiries or assistance with conveyor system optimization, Jordan is available to share his wealth of knowledge and experience. Feel free to reach out at any time for professional guidance on all matters related to conveyor rollers, belts, and accessories.