Prok Conveyor Rollers: Revolutionizing Industrial Operations
PROK Conveyor Rollers represent a pinnacle of innovation and reliability in the material handling industry, backed by decades of expertise and growth within Australia. Originating from humble beginnings, PROK has burgeoned into a leader in conveyor technology, offering products known for their durability and efficiency. These rollers are integral components used across various industries, including mining, manufacturing, and logistics, to facilitate the smooth and effective transport of materials.The reputation of PROK Conveyor Rollers is built on a foundation of quality and customer-centric innovations. Over the years, PROK has expanded its reach and technological capabilities, consistently staying ahead of industry demands. This growth is not just in size but in the vast array of products tailored to meet specific industry needs, driving material handling systems towards minimal downtime and maximum productivity.
Overview of PROK Conveyor Rollers Products
Quality and reliability are paramount when it comes to the components that make up material handling systems, and PROK Conveyor Rollers exemplify these traits through their comprehensive range of products. The importance of employing top-notch conveyor components cannot be overstated, as they significantly enhance the efficiency and longevity of any conveyor system.
- Low Noise Rollers: Specifically designed to minimize operational noise, these rollers are ideal for environments where noise reduction is critical, improving workplace safety and comfort.
- High Load Rollers: Built to withstand extremely heavy loads, these rollers ensure reliability and durability even under the most strenuous conditions, reducing downtime and maintenance costs.
- Energy Efficient Rollers: Engineered to reduce energy consumption by minimizing drag, these rollers offer an eco-friendly solution that can significantly lower operational costs over time.
- Impact and Rubber Disc Rollers: Perfect for high-impact zones, these rollers absorb shocks and vibrations, protecting the belt and the conveyed materials from damage.
The range of PROK Conveyor Rollers is extensive, each tailored to meet specific industrial needs. From standard rollers that cater to general transportation needs to specialized rollers designed for specific functions such as weight measurement or alignment correction, PROK’s offerings are versatile and inclusive. This diversity not only allows for customized solutions that can fit any system’s requirements but also underscores PROK’s commitment to innovation and customer satisfaction.
With such a wide array of products, PROK Conveyor Rollers are instrumental in facilitating optimal material flow, which is critical for maximizing productivity and efficiency in various operational setups. Whether upgrading an existing system or implementing a new one, PROK’s rollers offer the robustness, precision, and performance needed to enhance material handling processes. This overview not only highlights the capabilities of PROK rollers but also establishes a solid foundation for discussing their specific applications and benefits in subsequent sections.
Features of PROK Conveyor Rollers
PROK Conveyor Rollers stand out in the material handling industry due to their superior design and manufacturing qualities, which provide tangible advantages over competitors. Below are detailed comparisons and key features that highlight the durability and build quality of PROK Conveyor Rollers.
Advantages of Choosing PROK Rollers Over Competitors
The following table compares PROK Conveyor Rollers with generic competitors on various parameters that are critical to conveyor system performance:
Highlighting the Durability and Build Quality of PROK Rollers
PROK Conveyor Rollers are engineered to not only meet but exceed the rigorous demands of industrial applications. The durability of these rollers is a direct result of meticulous design processes, choice of materials, and advanced manufacturing techniques. Here are some key aspects:
- Material Selection: PROK uses high-grade steel, engineered plastics, and specialized rubber compounds, each selected for its durability and performance characteristics.
- Build Quality: The rollers are constructed with precision tolerances and robust designs that ensure they can handle heavy loads and high speeds without significant wear, which is critical for maintaining long-term functionality and efficiency.
- Protective Coating: Each roller is treated with protective coatings that resist corrosion, abrasion, and other environmental challenges, prolonging their lifespan significantly.
- Sealing Technology: PROK rollers include superior sealing technology that protects against dust, water, and other contaminants, which can degrade performance and increase maintenance needs.
The combination of these features makes PROK Conveyor Rollers a prudent choice for businesses looking to enhance their conveyor systems. They not only offer improved performance metrics but also decrease overall lifecycle costs due to their enhanced durability and build quality. This ensures that systems equipped with PROK rollers remain more productive and cost-effective over time, emphasizing their superiority in a competitive market.
Types of PROK Conveyor Rollers
PROK Conveyor Rollers encompass a diverse range of product lines, each designed to meet specific industrial needs with precision and efficiency. Below is an in-depth look at each type of PROK Roller, illustrating their unique benefits and applications in various environments:
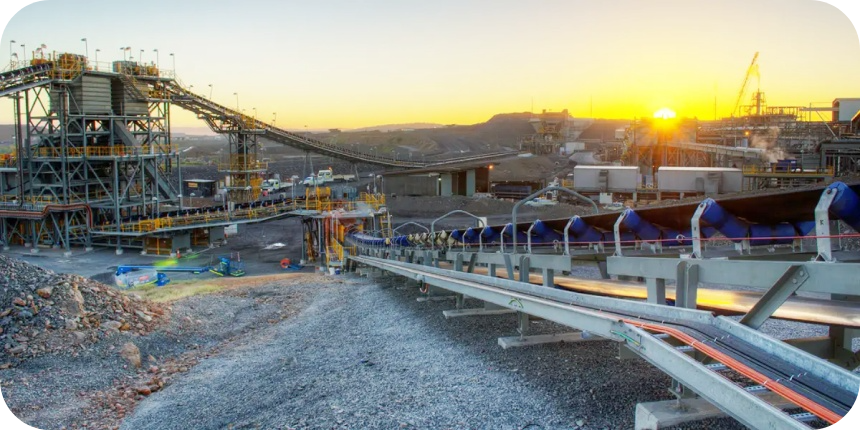
Low Noise Aluminium Roller
The Low Noise Aluminium Roller is specifically engineered for noise-sensitive environments where operational quietness is paramount. These rollers are constructed from high-grade aluminum, which naturally offers excellent noise dampening properties. Key benefits include:
- Reduced Noise Output: Ideal for facilities that require minimal disturbance, such as packaging lines or operations located in noise-regulated areas.
- Lightweight Design: Easier to install and replace, reducing labor costs and downtime.
- Corrosion Resistance: Naturally resistant to rust and corrosion, suitable for humid or corrosive environments.
Hybrid Steel Roller
Hybrid Steel Rollers combine the strengths of different materials to enhance functionality and performance. These rollers typically feature a steel shell integrated with other materials like rubber or plastic to improve impact resistance and reduce wear.
- Versatility: Can be customized to the specific needs of the operation, whether it’s load capacity or impact resistance.
- Durability: Steel’s robustness with the added benefit of secondary materials to enhance wear life.
- Cost-Effectiveness: Offers a balanced cost solution by integrating high-performance materials only where needed.
PROK HDPE Roller
PROK HDPE Rollers are renowned for their lightweight and highly corrosive resistant material. High-Density Polyethylene (HDPE) provides these rollers with several distinct advantages:
- Extreme Corrosion Resistance: Perfect for chemical plants or coastal facilities where salt air or corrosive substances are prevalent.
- Reduced Weight: About half the weight of traditional steel rollers, leading to lower energy consumption and easier handling.
- Low Maintenance: HDPE’s properties reduce the need for frequent replacements due to wear and tear.
PU Disc Roller
PU Disc Rollers are tailored for environments where conveyors frequently handle sticky or wet materials. The polyurethane disc helps to prevent material build-up on the roller itself, enhancing the conveyor’s overall efficiency.
- Self-Cleaning: The smooth surface of PU discs prevents materials from sticking, reducing downtime for cleaning.
- Moisture Resistance: Does not degrade with exposure to water or other liquids.
- Impact Resistance: Absorbs shocks and helps distribute the load evenly across the belt.
PROK Steel Roller
PROK Steel Rollers are the traditional choice for robust and heavy-duty applications. These rollers are designed to withstand high loads and harsh conditions without significant wear.
- High Load Capacity: Suitable for mining and quarrying applications where high load support is necessary.
- Long Lifespan: Made with specially treated steel to ensure longevity and resistance to harsh environmental conditions.
- Economical: Offers a cost-effective solution with low maintenance needs over its service life.
Rubber Disc Roller
Rubber Disc Rollers are utilized primarily in high-impact zones where they absorb shocks and vibrations, protecting both the conveyor belt and the materials being transported.
- Shock Absorption: Ideal for the loading zones where materials are dropped onto the conveyors.
- Durability: Rubber discs enhance the roller’s lifespan by reducing direct impact wear.
- Material Adherence Prevention: Helps in preventing the adherence of wet or sticky materials to the belt.
Formed Steel Roller
Formed Steel Rollers are crafted to fit specific container shapes, making them ideal for specialized applications that involve container transport.
- Customization: Designed to match the contours of specific containers, ensuring stability and reducing spillage.
- Robust Construction: Maintains structural integrity even under high loads, suitable for industrial environments.
- Enhanced Safety: Prevents containers from tipping, which could pose risks in the workplace.
Weigh Roller
Weigh Rollers are integrated with weighing systems to provide real-time load monitoring without disrupting the conveyor operation.
- Load Management: Allows for precise monitoring of material flow, essential for inventory control and process management.
- Integration Ease: Designed to fit seamlessly into existing conveyor systems.
- Accuracy: High precision in weight measurement enhances operational efficiency.
Impact Roller
Impact Rollers are designed to absorb the intense forces at loading points, reducing wear on the conveyor belt and other components.
- Heavy-Duty Use: Customizable to withstand varying degrees of impact depending on the application needs.
- Protective: Helps extend the lifespan of the conveyor belt by absorbing shocks.
- Customization Options: Available in different sizes and materials depending on the specific requirements of the operation.
Each type of PROK Conveyor Roller offers specific benefits that can significantly improve the efficiency, safety, and cost-effectiveness of material handling operations. These rollers are integral to the success of industries ranging from mining to food processing and play a critical role in maintaining the continuous, reliable operation of conveyor systems.
PROK Conveyor Rollers Parts and Maintenance
Maintaining the integrity and efficiency of conveyor systems is crucial, and PROK Conveyor Rollers parts and maintenance services are designed to ensure long-lasting performance and reliability. This section covers essential information on parts availability and provides detailed guidelines on maintaining these rollers effectively.
Availability of PROK Parts for Maintenance
PROK Conveyor Rollers are supported by a comprehensive range of spare parts, available through PROK’s extensive distribution network.
- Replacement Tubes and Shafts: Whether due to wear and tear or damage, replacement tubes and shafts for any PROK roller type are available, ensuring quick and easy substitution to keep systems running smoothly.
- Bearing Kits: Bearings are critical for the smooth operation of conveyor rollers. PROK offers specialized bearing kits that include all necessary components for a complete overhaul, which helps in extending the rollers’ service life.
- Seal Kits: To protect bearings and internal components from dust, water, and other contaminants, PROK provides seal kits that are tailored to fit various roller types and sizes, ensuring a tight and secure fit.
- Lubrication Packs: Proper lubrication is essential for the longevity of conveyor rollers. PROK’s lubrication packs contain high-grade lubricants designed to reduce friction and wear, even under high-load conditions.
Guidelines for Maintaining PROK Conveyor Rollers
To maximize the life and efficiency of PROK Conveyor Rollers, regular and proper maintenance is crucial. Below are comprehensive guidelines designed to help maintain these rollers:
- Regular Inspection: Conduct routine inspections to check for signs of wear and tear, alignment issues, or any damage to the rollers. This should include checking for smooth rotation, listening for irregular noises, and examining the condition of the seals and bearings.
- Cleaning Procedures: Keep the rollers clean from dust, debris, and other materials that can build up and cause damage. Use appropriate cleaning agents that will not degrade the roller materials. Ensure that cleaning schedules are adhered to, to prevent build-up that can affect performance.
- Lubrication: Follow the manufacturer’s recommendations for lubrication. Regularly apply lubricant to bearings and other moving parts to reduce friction and prevent overheating, which can lead to premature failure.
- Replacement and Repair: Replace parts such as bearings, seals, and even entire rollers when inspection reveals that they cannot be effectively repaired. Using genuine PROK parts ensures compatibility and reliability, thus maintaining the system’s efficiency.
- Alignment Checks: Ensure that conveyor tracks are properly aligned. Misalignment can cause excessive wear and energy consumption, as well as increase the risk of the conveyor malfunctioning. Regular alignment checks should be part of the maintenance routine.
- Training for Maintenance Staff: Provide regular training for personnel responsible for maintenance. Understanding the correct procedures for inspection, cleaning, and replacement ensures that maintenance is done effectively, which prolongs the life of the rollers and reduces downtime.
By following these guidelines, the performance of PROK Conveyor Rollers can be optimized, resulting in a conveyor system that operates smoothly with minimal interruptions, thus enhancing overall productivity and efficiency. Regular maintenance not only extends the life of the rollers but also ensures they continue to operate at their peak capacity, contributing to a more cost-effective and reliable operation.
Technical Aspects of PROK Conveyor Rollers
Delving into the technical aspects of PROK Conveyor Rollers provides a clearer understanding of their design and capabilities, essential for selecting the right components for specific applications. This section covers the critical dimensions and the comprehensive cataloging of these rollers, which are crucial for engineers and industry professionals.
PROK Idler Dimensions
PROK Conveyor Rollers are available in a variety of sizes and configurations, designed to meet diverse industrial needs. The dimensions of these rollers play a critical role in their suitability for different conveyor systems. Key aspects include:
- Diameter Range: PROK rollers are available in diameters from 89mm to 219mm, catering to a wide range of industrial applications. This variety ensures that whether the system is designed for light, medium, or heavy loads, there is a PROK roller to match.
- Length Options: The length of the rollers can also vary, typically starting from 150mm to over 2500mm, depending on the application’s specific requirements. Custom lengths are also available to ensure a perfect fit for any conveyor setup.
- Shaft Diameter: Essential for the roller’s structural integrity, shaft diameters are tailored to the roller size and load requirements, with options usually ranging from 20mm to 60mm.
- Customization: PROK understands that not all conveyor setups are the same, which is why they offer custom-sized rollers. These are designed to exact client specifications, ensuring seamless integration and optimal performance.
Here is a table summarizing the standard dimensions available:
PROK Idler Catalogue
The PROK Idler Catalogue is an essential resource for anyone needing detailed product specifications of PROK Conveyor Rollers. This catalogue is comprehensive, offering in-depth information on all aspects of their rollers, including:
- Material Specifications: Details on the types of materials used (e.g., steel, HDPE, aluminium), which influence the roller’s durability and suitability for different environments.
- Bearing Types and Arrangements: Information on the bearings used, which are crucial for the roller’s operational efficiency and lifespan.
- Dimensional Details: Exact measurements of each roller type, including diameter, length, and shaft size, as well as the tolerances adhered to.
- Load Capacities: Maximum recommended load capacities for each roller type, ensuring that clients choose rollers that match their system’s load requirements.
- Sealing and Lubrication Options: Details on the sealing systems used to protect the bearings from contaminants, as well as lubrication recommendations to ensure long-term smooth operation.
- Installation Guidelines: Instructions on proper installation techniques to maximize the efficiency and lifespan of the rollers.
The catalogue is available both online and in print, ensuring that detailed, accurate information is accessible for planning, maintenance, and replacement purposes. It serves not only as a buying guide but also as a comprehensive reference tool throughout the lifecycle of the conveyor system.
By providing precise dimensions and a detailed catalogue, PROK Conveyor Rollers ensure that engineering and maintenance teams have all the necessary information to select, install, and maintain the ideal roller components, leading to enhanced system performance and reliability. This detailed technical documentation underscores PROK’s commitment to quality and customer support, making it a leader in the conveyor industry.
Fill Out the Form to Explore Our Conveyor Roller Options.
PROK Conveyor Rollers Equipment and Components
PROK Conveyor Rollers are integral to a wide array of conveyor equipment and components, ensuring optimized operation across various industries. This section discusses how these rollers fit seamlessly into the broader conveyor systems and highlights several example setups and industrial applications where these components are critical.
Integration of PROK Conveyor Rollers with Conveyor Equipment
PROK Conveyor Rollers are designed to be versatile, fitting into numerous types of conveyor equipment and components. Here are four key examples of such integrations:
Belt Conveyor Systems:
- Role of Rollers: PROK Conveyor Rollers support the conveyor belt’s weight and the material being transported. Their smooth rotation allows the belt to move efficiently with minimal friction and wear.
- Components Involved: Includes the belt itself, rollers, frame, and drive system, where PROK rollers can be used as both carry and return rollers.
Roller Bed Conveyors:
- Role of Rollers: In these systems, PROK Conveyor Rollers are laid out in a dense grid to support heavier loads over longer distances than standard belt conveyors.
- Components Involved: Roller beds, which are sections of heavy-duty rollers placed closely together to support the active conveyor belt.
Powered Roller Conveyors:
- Role of Rollers: These conveyors use powered rollers embedded within the conveyor frame to facilitate the movement of goods. PROK Conveyor Rollers can be individually powered to control the speed and direction of the material handling.
- Components Involved: Each roller is connected to a motor through a chain, belt, or direct gear mechanism, which is part of the overall power transmission system.
Gravity Roller Conveyors:
- Role of Rollers: PROK Conveyor Rollers are used to create a natural decline system, where gravity moves the conveyed items. These rollers spin freely, which reduces the energy needed to move goods.
- Components Involved: Typically involves a slight downward tilt of the roller frame besides the rollers themselves, harnessing gravity to facilitate movement.
Example Setups and Industrial Applications
PROK Conveyor Rollers are utilized in various setups, tailored to meet the specific needs of different industries:
- Mining and Quarrying:
- Setup: Heavy-duty roller conveyors with reinforced frames and robust PROK Conveyor Rollers designed to handle the high loads and abrasive materials typically found in mining operations.
- Application: Transporting raw extracted materials from the mining site to processing facilities.
- Manufacturing Plants:
- Setup: Assembly lines equipped with powered roller conveyors that use PROK Conveyor Rollers for precise movement and positioning of products.
- Application: Assembly and processing of products ranging from small electronics to large automotive components.
- Packaging Industries:
- Setup: Gravity and powered roller conveyors integrated into packaging lines, where PROK Conveyor Rollers ensure gentle handling to maintain product integrity.
- Application: Conveying products through various stages of packaging, from bulk handling to individual packaging processes.
- Distribution and Logistics:
- Setup: Sortation systems that utilize both belt and roller conveyors fitted with PROK Conveyor Rollers to efficiently sort, organize, and dispatch goods.
- Application: Managing inventory and orders within warehouses, facilitating rapid shipment and reducing handling times.
These examples highlight the flexibility and adaptability of PROK Conveyor Rollers, proving their effectiveness in a broad spectrum of industrial applications. By integrating these rollers into complex conveyor systems, industries can achieve enhanced operational efficiency, reduced maintenance costs, and improved product handling. This versatility not only positions PROK as a leader in conveyor technology but also as a crucial partner in the global industrial landscape.
Where to Buy PROK Conveyor Rollers
When it comes to integrating reliable material handling systems in your operations, selecting top-quality components like PROK conveyor rollers is crucial. These rollers are renowned for their durability and efficiency, enhancing conveyor performance and system reliability. Here’s a detailed guide on where you can purchase PROK conveyor rollers, including information on sales, distribution, and service networks.
Purchasing PROK Conveyor Rollers
PROK conveyor rollers can be purchased through a variety of channels that ensure you receive products that are not only high in quality but also backed by excellent customer service and support. Whether you are upgrading your current system or building a new one, here are the primary sources for acquiring PROK conveyor rollers:
PROK Direct Sales Offices
PROK directly sells its conveyor rollers through its dedicated sales offices located worldwide. These offices are staffed with knowledgeable professionals who can provide detailed product information, pricing, and support.
- Main Office – Perth, Australia
- Offers a full range of PROK conveyor rollers, specializing in both standard and custom solutions.
- Provides comprehensive customer support, from product selection to post-installation services.
PROK Mackay Distribution Center
Located in Mackay, Queensland, this facility serves as a hub for sales and distribution throughout Australia. It features a large inventory of standard rollers and has the capability to supply custom requirements on request.
- Services Offered:
- Immediate availability of a wide range of roller types.
- Custom design and engineering support.
- Logistic services for timely and efficient delivery.
Authorized Distributors
PROK has established partnerships with authorized distributors across the globe to widen their reach and ensure local businesses have access to PROK conveyor rollers. These distributors are carefully selected to uphold PROK’s standards of quality and reliability.
- Example Locations:
- United States: Distributors located throughout major industrial states including Texas, California, and Illinois.
- Europe: Several partners across industrial hubs in Germany, France, and the United Kingdom.
- Asia: Extensive network including India, China, and Japan.
Online Retailers and B2B Platforms
For convenience, PROK conveyor rollers are also available through various online retailers and B2B marketplaces. This allows customers to make quick purchases and compare different product offerings easily.
- Platforms like Alibaba, ThomasNet, and DirectIndustry
- These platforms list a variety of PROK roller models, providing extensive choice regarding price and specifications.
- Often feature user reviews and ratings to help inform your purchase decision.
Purchasing PROK conveyor rollers is made accessible through multiple channels, whether directly from PROK, through their Mackay center, via authorized distributors, or online platforms. Each channel is supported by robust service and distribution frameworks, ensuring that customers not only receive their products in a timely manner but also gain access to expert support throughout their product’s lifecycle. Whether your operation is local or global, these purchasing avenues provide the solutions you need to enhance your conveyor systems effectively.
Customization and Service by PROK Conveyor Rollers
PROK’s commitment to providing high-quality PROK conveyor rollers extends beyond standard products to include comprehensive customization and after-sales service. Understanding that each material handling system has its unique challenges, PROK offers tailor-made solutions designed to meet specific operational requirements, along with dedicated support throughout the lifecycle of their products.
Custom Solutions for Unique Conveyor Needs
When standard products do not perfectly fit the operational requirements of a business, PROK steps in to engineer custom solutions. These are developed to enhance the functionality of PROK conveyor rollers, adapting them to the specific conditions and demands of different industrial environments.
Examples of Custom Solutions:
High-Temperature Applications:
- For industries like metalworking or cement manufacturing where temperatures may degrade standard rollers, PROK designs rollers with specialized heat-resistant materials and lubricants.
Corrosive Environments:
- In chemical processing or marine applications, rollers need to withstand corrosive substances. PROK utilizes stainless steel and other corrosion-resistant materials to prolong the life of conveyor rollers under harsh conditions.
Heavy-Duty Operations:
- For mining and quarrying, rollers must handle heavy loads and tough conditions. PROK engineers robust rollers with reinforced structures and enhanced load-bearing capacities.
Food Grade Rollers:
- In the food processing industry, hygiene and contamination are major concerns. PROK provides food-grade rollers made from materials that are easy to clean and resist bacteria buildup.
After-Sales Support and Services
PROK’s relationship with its clients doesn’t end at the sale. Comprehensive after-sales support is provided to ensure PROK conveyor rollers operate at peak efficiency and with minimal downtime.
Key After-Sales Services Include:
- Technical Support:
- Expert technicians are available to resolve issues and optimize performance. Support is available 24/7, ensuring that help is on hand whenever it is needed.
- Maintenance Services:
- Scheduled maintenance is offered to prolong the lifespan of the rollers and prevent breakdowns. Services include regular inspections and proactive replacements of worn parts.
- Training Programs:
- PROK conducts training sessions for clients’ operational teams to ensure they are well-versed in handling, maintaining, and troubleshooting the rollers.
- Spare Parts Supply:
- A full inventory of spare parts is maintained for quick replacement to minimize downtime. Parts are readily available across PROK’s key service centers worldwide.
PROK’s Innovation: The Conveyor Belt Lifter
PROK conveyor belt lifter represents a significant innovation in conveyor system maintenance and safety. This tool is designed to facilitate safer and more efficient belt maintenance activities.
Benefits of the PROK Conveyor Belt Lifter:
Enhanced Safety:
- Reduces the risk of injuries associated with manual lifting and shifting of heavy conveyor belts.
Increased Efficiency:
- Cuts down maintenance time as belts can be lifted and positioned easily and quickly, minimizing downtime.
Cost-Effective:
- By reducing the time and labor required for belt maintenance, the lifter decreases overall maintenance costs.
Adaptability:
- PROK’s belt lifter is compatible with a wide range of conveyor belt sizes and types, making it a versatile tool for multiple industries.
Incorporating PROK conveyor rollers and the innovative belt lifter into your systems ensures not only a high degree of operational efficiency but also adherence to safety standards, reflecting PROK’s commitment to quality and customer satisfaction. Through its bespoke solutions and robust after-sales services, PROK continues to be a leader in the conveyor technology sector.
Why Choose PROK Conveyor Rollers?
Selecting PROK conveyor rollers means choosing a path of reliability and efficiency for your conveyor systems. PROK’s commitment to quality and its comprehensive range of conveyor components set it apart in the industry. Here’s an in-depth look at why PROK should be your go-to choice for conveyor rollers, backed by specific benefits and real-world testimonials.
Key Benefits of PROK Conveyor Rollers
Durability
PROK conveyor rollers are designed to withstand the most demanding industrial environments. They are built using high-grade materials that enhance their lifespan and reduce the need for frequent replacements.
- Example: In mining operations, where rollers are subjected to extreme wear and tear, PROK’s heavy-duty rollers have proven to last significantly longer than standard rollers, reducing downtime and maintenance costs.
Efficiency
Each roller is engineered not just for durability but also for optimal performance. PROK’s precision engineering minimizes friction and energy consumption, boosting the overall efficiency of conveyor systems.
- Example: A manufacturing facility reported a 20% increase in conveyor efficiency after switching to PROK rollers, attributing this to the superior design that reduced drag and improved load handling.
Cost-Effectiveness
Despite the high quality, PROK conveyor rollers are cost-effective. The long-term savings in maintenance and replacement costs make them a smart investment.
- Example: A comparison study by a logistics company found that although PROK rollers are initially more expensive, the total cost of ownership over 5 years is lower than that of competitors due to reduced breakdowns and fewer replacements needed.
Customization
PROK stands out in its ability to provide customized solutions that precisely meet client specifications, ensuring that no matter the application, the rollers deliver maximum performance.
- Example: A food processing plant utilized PROK’s custom-designed food-grade rollers, which helped them meet stringent hygiene standards while maintaining high throughput rates.
Testimonials from Satisfied Customers
Mining Sector
- Challenge: A major mining company faced frequent roller failures due to the abrasive environment of iron ore processing.
- Solution: PROK provided custom-engineered rollers made with specially coated materials for enhanced wear resistance.
- Outcome: Roller lifespan increased by 40%, and the company saw a reduction in maintenance downtime by 25%.
Packaging Industry
- Challenge: A packaging company struggled with conveyor system inefficiencies, experiencing frequent jams and slowdowns.
- Solution: PROK analyzed the system and installed specially designed high-efficiency rollers.
- Outcome: System efficiency improved by 30%, with a significant decrease in product damages and jams.
Why Industry Leaders Prefer PROK
PROK conveyor rollers are not only about quality and efficiency but also about adding value to your business through innovative designs and customized solutions. The durability, cost-effectiveness, and specific customer-focused adaptations they offer make them a preferred choice for industries ranging from mining to food processing. The testimonials and case studies reflect the positive impact of PROK’s products on operational success, making them a trusted partner in the material handling industry. Whether upgrading an existing system or setting up a new installation, PROK’s expertise and dedicated service make them the ideal choice.
FAQs About Prok Conveyor Rollers
Conveyor rollers come in several types, each designed to fulfill specific needs within various industrial environments. The choice of roller type depends on the application, load requirements, and environmental conditions. Here are the main types of conveyor rollers:
Gravity Rollers: These rollers rely on gravity to move products across the horizontal or slightly inclined paths. They are typically used in pick modules, packing stations, and assembly areas.
Motorized Rollers: Also known as driven rollers, they are powered by motors and are used when controlled movement of goods is necessary. They are ideal for heavy-load transportation over long distances within industrial plants.
Impact Rollers: Placed at conveyor feed and transfer points, impact rollers are designed to absorb the forces of falling material, which protects the belt and the structure from damage.
Grooved Rollers: These are used with round belts, ropes, or cables and are commonly used in pulley operated conveyor systems to guide and hold belts in place.
Tapered Rollers: Perfect for curves, tapered rollers help maintain the orientation of materials like packages through bends and turns in the conveyor path.
Understanding the different types of conveyor rollers helps in selecting the right roller for efficient and effective movement of materials within various systems.
The primary purpose of rollers in a conveyor is to facilitate the movement of goods along the conveyor belt. Rollers provide support and stability to the conveyor belt and enable smooth motion under the load of the goods being transported. Here are the key functions of conveyor rollers:
Support and Guide the Conveyor Belt: Rollers prevent sagging of the conveyor belt between frames, which helps in maintaining the belt’s alignment and tension.
Reduce Friction: By supporting the conveyor belt and providing a smooth surface for the belt to move over, rollers help to reduce the friction associated with the belt’s movement, which in turn reduces the power consumption.
Facilitate Material Handling: Rollers allow for the easy and efficient transport of goods across various sections of the manufacturing process, from production to packaging.
Increase System Lifespan: Properly functioning rollers help in evenly distributing the load on the conveyor, which reduces wear and tear on the belt and other conveyor components, thus extending the system’s operational life.
Effective use of rollers is critical for optimizing conveyor operations and ensuring the longevity of the conveyor system.
The distance between rollers in a conveyor, often referred to as the roller pitch, is crucial and can vary based on the type of goods being transported and the specific requirements of the conveyor system. Factors influencing roller pitch include:
Load Characteristics: Heavier and larger products require closer roller spacing to support the load adequately and prevent the conveyor belt from sagging.
Type of Conveyor: Gravity conveyors typically have closer roller spacing compared to motorized conveyors because the latter can handle larger gaps without affecting the stability of the goods.
Belt Properties: The material and build of the conveyor belt also determine optimal roller spacing. A thicker belt can span longer distances between rollers.
Typically, roller pitch ranges from 1.5 inches (38 mm) to 6 inches (152 mm), but must be adjusted carefully to balance conveyor efficiency with system durability and maintenance requirements.
The roller used to track a conveyor belt is known as a guide roller. Guide rollers are critical components that help maintain the alignment of the conveyor belt, preventing it from drifting sideways, which can lead to uneven wear, tearing of the belt, and operational issues. Here’s how guide rollers function:
Positioning: Guide rollers are positioned on the sides of the conveyor belts, often near the tail pulleys or along the return run of the belt.
Operation: They gently steer the belt back to the centerline if it begins to drift. This is crucial for maintaining the efficiency and longevity of the conveyor system.
Types: Some guide rollers are fixed while others are adjustable. Adjustable rollers provide the flexibility needed to accommodate slight variations in the belt’s path.
Using guide rollers is essential for preventing costly downtime and maintaining the smooth operation of conveyor systems, particularly in long and high-speed conveyor lines.
Last Updated on August 15, 2024 by Jordan Smith
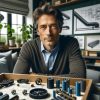
Jordan Smith, a seasoned professional with over 20 years of experience in the conveyor system industry. Jordan’s expertise lies in providing comprehensive solutions for conveyor rollers, belts, and accessories, catering to a wide range of industrial needs. From initial design and configuration to installation and meticulous troubleshooting, Jordan is adept at handling all aspects of conveyor system management. Whether you’re looking to upgrade your production line with efficient conveyor belts, require custom conveyor rollers for specific operations, or need expert advice on selecting the right conveyor accessories for your facility, Jordan is your reliable consultant. For any inquiries or assistance with conveyor system optimization, Jordan is available to share his wealth of knowledge and experience. Feel free to reach out at any time for professional guidance on all matters related to conveyor rollers, belts, and accessories.