Benefits of Reinforced Conveyor Belt Material
Reinforced conveyor belt material is fundamental to the operation of multiple industries, including mining, construction, and agriculture. These belts are designed to meet the rigorous demands of transporting materials over great distances and through challenging environments. The durability and efficiency of conveyor belts are enhanced by using reinforced materials such as rubber and steel cord, which provide essential properties like high tensile strength and resistance to wear and tear. This introduction focuses on the varied applications and the critical role of reinforced conveyor belt material in ensuring operational success across different sectors. The options available typically include robust materials that cater to specific industry needs, emphasizing the adaptability and importance of these reinforced solutions in modern industrial operations.
Types of Reinforced Conveyor Belt Materials
Reinforced conveyor belt material vary widely,each offers its functional and specific advantages can effectively protect the conveyor belt.Reinforced conveyor belt materials are integral to modern industrial operations, offering enhanced durability and functionality in diverse settings. Below, we detail various types of reinforced belts and their specific advantages and applications:
This table outlines the diverse types of reinforced conveyor belt material available, emphasizing their tailored design to meet specific industrial needs. Each belt type brings unique features to the table, enhancing the efficiency and safety of transportation systems in various sectors.
Steel Mesh Reinforced Conveyor Belt
A steel mesh reinforced conveyor belt is designed for demanding applications where high strength, durability, and resistance to extreme conditions are required. Here are the key aspects and benefits of using steel mesh reinforced conveyor belts, along with considerations for their selection:
Key Aspects of Steel Mesh Reinforced Conveyor Belts
- Structure and Composition
- Steel Mesh Reinforcement: These belts consist of a robust steel mesh embedded within the belt material, providing exceptional tensile strength and resistance to impact.
- Cover Materials: The outer covers of the belt are typically made of rubber or other durable materials to protect the steel mesh and enhance resistance to wear and environmental factors.
- Benefits
- High Strength: The steel mesh reinforcement allows the belt to handle heavy loads and resist stretching.
- Durability: Steel mesh belts are highly resistant to wear, abrasion, and impact, making them ideal for harsh environments.
- Heat Resistance: Steel mesh can withstand high temperatures, making these belts suitable for applications involving hot materials.
- Flexibility: Despite their strength, steel mesh belts can be designed to maintain flexibility, allowing them to navigate complex conveyor systems.
- Longevity: The durability and resistance to damage extend the lifespan of the belt, reducing maintenance and replacement costs.
- Applications
- Mining and Quarrying: Transporting heavy and abrasive materials such as ores, rocks, and minerals.
- Construction: Moving materials like sand, gravel, and concrete.
- Recycling: Handling sharp and heavy recyclable materials.
- High-Temperature Environments: Conveying hot materials such as in foundries or metal processing plants.
Considerations for Selection
- Load and Stress Requirements
- Tensile Strength: Ensure the belt can handle the maximum load capacity of your application without failing.
- Impact Resistance: Consider the impact resistance needed if your materials are dropped onto the belt from a height.
- Environmental Conditions
- Temperature: Choose belts that can withstand the operational temperatures, whether they are high or low.
- Corrosion Resistance: In corrosive environments, ensure the steel mesh and cover materials are resistant to corrosion.
- Belt Size and Configuration
- Width and Length: Specify the belt dimensions to fit your conveyor system.
- Belt Speed: Ensure the belt can operate at the required speed without compromising performance.
- Maintenance and Repair
- Ease of Maintenance: Choose belts that are easy to inspect and maintain. Steel mesh belts can sometimes be more challenging to repair on-site compared to fabric belts.
- Availability of Spare Parts: Ensure that spare parts and repair kits are readily available.
- Cost and Budget
- Initial Investment: Steel mesh belts tend to have a higher initial cost due to the materials and manufacturing processes involved.
- Long-Term Savings: Evaluate the total cost of ownership, considering the longer lifespan and reduced maintenance costs.
Steel mesh reinforced conveyor belts offer a combination of high strength, durability, and resistance to harsh conditions, making them suitable for heavy-duty applications. By considering factors such as load requirements, environmental conditions, and maintenance needs, you can select the most appropriate belt for your operation. Consulting with manufacturers and testing the belts can further ensure optimal performance and longevity.

Advantages of Reinforced Conveyor Belt Material
Reinforced conveyor belt material, which typically includes robust materials like rubber and steel, offers significant advantages over traditional conveyor belts. This section explores the distinctive benefits and superior features of reinforced conveyor belt materials.
Comparative Analysis of Rubber and Steel in Reinforced Conveyor Belts
Reinforced conveyor belts often utilize materials such as rubber and steel to enhance their functional capabilities. Here are ten specific advantages of using these reinforced materials:
- Durability: Reinforced conveyor belt material is exceptionally durable. Steel cords or mesh embedded in rubber provide increased resistance to wear and tear, substantially extending the belt’s lifespan.
- Strength: The integration of steel within these belts delivers superior tensile strength, which prevents elongation and maintains the belt’s integrity under heavy loads.
- Customization Options: Reinforced belts can be customized extensively. For instance, belts can be manufactured in widths up to 2.4 meters and roll lengths up to 700 meters, accommodating various industrial needs.
- Temperature Resistance: Steel-reinforced rubber belts can operate efficiently in extreme temperatures, whether high or low, without losing flexibility or strength.
- Corrosion Resistance: Steel used in these belts often undergoes treatment to resist corrosion, making them suitable for damp or chemically active environments.
- Energy Efficiency: The smooth operation of reinforced conveyor belt material reduces energy consumption by minimizing friction and improving load distribution.
- Low Maintenance: The robust nature of these materials means less frequent maintenance and lower long-term costs.
- Impact Resistance: Reinforced materials absorb and distribute impacts more effectively, crucial for handling heavy or sharp objects without damage.
- Flexibility: Despite their strength, reinforced belts maintain flexibility, essential for curving around the conveyors without compromising performance.
- Safety: Enhanced structural integrity reduces the risk of belt rupture, which can be crucial for worker safety and operational continuity.
Eight Additional Benefits of Reinforced Conveyor Belt Material
Beyond the comparative advantages of rubber and steel, reinforced conveyor belt materials offer several other benefits:
- Enhanced Load Support: These belts can support heavier loads compared to non-reinforced variants, crucial for industries like mining and construction.
- Improved Impact Resistance: The incorporation of resilient materials allows these belts to withstand significant impacts, reducing the risk of damage during rough handling.
- Long-Distance Suitability: The strength and durability of reinforced materials make these belts ideal for long-distance transportation, reducing the frequency of conveyor changes.
- Reduced Operational Downtime: With enhanced durability and impact resistance, reinforced belts contribute to reduced downtime, as they require fewer repairs and replacements.
- Cost-Effectiveness: Although the initial investment may be higher, the long-term savings in maintenance and replacement costs make reinforced belts a cost-effective choice.
- Versatility: These belts can be used in a variety of environments, from indoor warehouses to outdoor industrial sites, making them extremely versatile.
- Noise Reduction: The structure of reinforced belts often results in quieter operation, which is beneficial in noise-sensitive environments.
- Ease of Installation: Despite their robust nature, these belts are designed for easy installation, ensuring quick setup and minimal disruption.
The reinforced conveyor belt material provides numerous advantages that can significantly enhance the efficiency, safety, and cost-effectiveness of industrial operations across various sectors.

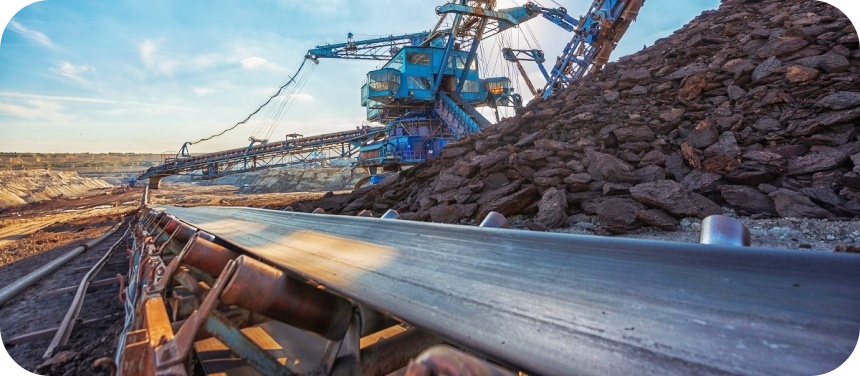
Market Availability and Pricing of Reinforced Conveyor Belt Material
The market for reinforced conveyor belt material is dynamic, with a range of options available to meet the diverse needs of various industries. This section delves into the availability and pricing of these materials, highlighting factors that influence their cost and outlining where they can be purchased.
Availability of Reinforced Conveyor Belt Material
Reinforced conveyor belt materials are readily available in both new and used conditions, catering to a wide range of budgetary and operational requirements. New conveyor belts are preferred for their longevity and reliability, whereas used belts might be opted for cost savings or less demanding applications.
- New Belts: These are available directly from manufacturers or through specialized dealers. They come with the latest technology and material advancements, offering peak performance and durability.
- Used Belts: Often sourced from industrial surplus, auctions, or businesses that are downsizing or updating their equipment. While they offer significant cost savings, it’s crucial to assess their condition and suitability for specific applications.
Factors Affecting the Pricing of Reinforced Conveyor Belt Material
The cost of reinforced conveyor belt material is influenced by several factors, making it important for buyers to consider these elements when budgeting for their conveyor systems:
- Material Type: The choice of materials (e.g., rubber, steel, or composites) significantly impacts the price due to varying production costs and performance characteristics.
- Belt Dimensions: Larger and thicker belts, which require more material and labor to produce, naturally cost more.
- Manufacturing Process: The complexity of the manufacturing process, including the type of weave or layering of materials, can affect the price.
- Special Features: Features such as anti-static properties, food-grade coatings, or high temperature resistance add to the production costs.
- Market Demand: Prices can fluctuate based on demand in key industries such as mining, agriculture, and manufacturing.
- Economic Factors: Changes in raw material costs, labor costs, and import tariffs can influence the final price of the belts.
- Supplier and Geographic Location: Prices may vary depending on where the belts are produced and the logistics costs of shipping them to the customer.
- Customization: Customized belts designed for specific applications or with unique specifications can significantly increase the cost.
Where to Purchase Reinforced Conveyor Belt Material
Reinforced conveyor belt materials can be purchased through a variety of channels, ensuring accessibility for all types of buyers:
- Manufacturer Direct: Purchasing directly from manufacturers is often the most reliable way to obtain new, high-quality belts designed to specific industrial standards.
- Industrial Supply Companies: These companies typically offer a wide range of conveyor belts, including reinforced options, catering to both general and specialized needs.
- Online Platforms: E-commerce websites and online industrial marketplaces provide opportunities to compare prices and products from different suppliers.
- Local Dealers and Distributors: For those who prefer a hands-on approach to purchasing, local dealers provide the advantage of direct inspections and negotiations.
- Trade Shows and Industrial Expos: These events are ideal for networking with multiple suppliers, comparing products, and negotiating deals all in one place.
- Used Equipment Vendors: Specialized in selling pre-owned industrial equipment, these vendors can be a source for more affordable reinforced conveyor belt options.
Understanding the market availability and pricing dynamics of reinforced conveyor belt material helps businesses make informed purchasing decisions, balancing cost with operational needs and ensuring that they select the most suitable product for their specific applications.
How to Choose Reinforced Conveyor Belt Material
Choosing the right material for a reinforced conveyor belt is crucial for ensuring efficient operation, longevity, and cost-effectiveness. Here are the key factors to consider:
1. Type of Material Being Transported
- Abrasion Resistance: For materials that are abrasive, such as coal or rock, choose a belt with high abrasion resistance.
- Chemical Resistance: If the materials are chemically active, such as fertilizers or chemicals, select a belt material that can resist corrosion.
- Temperature Resistance: For transporting hot or cold materials, choose belts that can withstand extreme temperatures without degrading.
2. Load Capacity and Belt Strength
- Tensile Strength: Ensure the belt material can handle the maximum load without stretching or breaking.
- Ply and Fabric Layers: More layers generally mean higher strength. Common materials include polyester, nylon, and steel cord.
3. Environmental Conditions
- Moisture and Humidity: In damp or wet environments, choose materials that are water-resistant or have minimal water absorption.
- UV Resistance: For outdoor belts, UV resistance can prevent degradation from sunlight.
- Oil and Grease Resistance: In environments where the belt might be exposed to oils or greases, ensure the material is resistant to such substances.
4. Belt Construction
- Reinforcement Types: Common reinforcement materials include steel, fabric, and aramid fibers. Steel provides high strength, fabric offers flexibility, and aramid fibers are strong and lightweight.
- Cover Materials: The top and bottom covers of the belt protect the reinforcement and can be made from various materials like rubber or PVC, each suited to different conditions.
5. Maintenance and Lifespan
- Ease of Repair: Consider how easy it is to repair the belt in case of damage. Some materials might be easier to patch or splice.
- Expected Lifespan: Higher quality materials may have a higher upfront cost but could last longer, reducing the overall cost of ownership.
6. Cost
- Initial Investment vs. Long-Term Savings: Balancing initial cost with long-term durability and maintenance needs can optimize overall expenditure.
Final Steps
- Consult with Manufacturers: Manufacturers can provide detailed specifications and recommendations based on your specific needs.
- Test Samples: If possible, test different belt materials under actual operating conditions to see which performs best.
- Review Industry Standards: Ensure the selected belt material meets relevant industry standards for safety and performance.
Choosing the right reinforced conveyor belt material involves a careful analysis of the working environment, material characteristics, and operational requirements. Taking the time to select the appropriate material will lead to better performance, increased longevity, and lower operational costs.

Accessories and Additional Services for Reinforced Conveyor Belt Material
When it comes to maximizing the efficiency and lifespan of reinforced conveyor belt material, accessories and additional services play critical roles. Below, we explore the essential accessories designed to enhance the functionality of these belts, along with comprehensive services offered by companies like Truco to ensure optimal performance.
Essential Accessories for Reinforced Conveyor Belt Material
- Skirting: This accessory is used to reduce material spillage along the conveyor path. It helps in containing the material at the transfer points, improving the overall efficiency and cleanliness of the operation.
- Pulley Lagging: Provides added grip between the conveyor belt and the pulleys, reducing slippage and extending the life of the belt.
- Idlers: These are rollers that support the conveyor belt and material load, ensuring smooth belt movement and less wear on the belt.
- Impact Bars: Positioned at the loading points, impact bars absorb the shock and distribute the load uniformly to prevent damage to the belt.
- Conveyor Rollers: These are designed to facilitate smooth and effective belt motion, essential for minimizing wear and energy consumption.
- Belt Cleaners: Used to keep the conveyor belt clean, these accessories prevent build-up and potential belt damage from material residue.
- Wear Liners: Installed along the conveyor system, wear liners protect the conveyor structure from abrasion and impact from the conveyed material.
Comprehensive Services for Reinforced Conveyor Belt Material
- On-Site Conveyor Belt Analysis: Experts analyze the conveyor system on-site to ensure it meets operational requirements and to identify any potential issues.
- Comprehensive Maintenance: Regular maintenance services help in prolonging belt life and preventing unforeseen failures.
- Installation Services: Professional installation ensures that the conveyor belt is set up correctly, maximizing its performance and longevity.
- Condition Monitoring: Continuous monitoring of the conveyor belt’s condition to preemptively address wear and tear.
- 24/7 Emergency Services: Round-the-clock services to address and resolve any urgent issues that may arise with the conveyor system.
- Training Programs: Training for onsite personnel on proper operation and maintenance of the conveyor belts to ensure safe and efficient use.
- Performance Monitoring: Tracking and analyzing the performance of the conveyor belt to optimize throughput and efficiency.
- Customization Services: Tailoring conveyor belt systems to meet specific industrial needs, including custom belt designs.
- Warranty and Support: Offering warranties and support services to ensure reliable operation and peace of mind for users.
By investing in the right accessories and availing of expert services, users of reinforced conveyor belt material can significantly enhance the performance and longevity of their conveyor systems. Companies like Truco provide these accessories and services, ensuring that their reinforced conveyor belts deliver optimal results under various industrial conditions.
Learn more about our high-performance conveyor belt options.
FAQs about Reinforced Conveyor Belt Material
Conveyor belt reinforcement is crucial for providing the belt with the requisite strength and durability needed for various operational demands. Several materials are employed for reinforcement, each adding specific properties to the conveyor belt. Polyester, nylon, and steel cords are among the most common reinforcements. Polyester offers low stretch and excellent strength, making it suitable for medium to heavy applications. Nylon, known for its high impact and abrasion resistance, is perfect for heavy-duty applications requiring toughness and resilience. Steel cords are used for ultra-heavy-duty applications; they provide exceptional tensile strength, allowing the conveyor to carry large volumes of material over long distances without significant elongation. These materials can be used individually or in combination, depending on the application’s requirements, to ensure the conveyor belt’s performance and longevity.
A conveyor belt can be made from a variety of materials, each chosen for its suitability to the application’s specific needs. The main materials include rubber, PVC, polyurethane, and fabric. Rubber conveyor belts are widely used for their flexibility, strength, and durability, making them suitable for both general and heavy-duty applications. PVC conveyor belts offer excellent resistance to chemicals, abrasion, and weather, making them suitable for a wide range of industries, including food processing and pharmaceuticals. Polyurethane belts are preferred in the food industry due to their non-toxic and hygienic properties. Fabric belts, often made from materials like polyester, nylon, or cotton, are used for lightweight applications and offer good resistance to abrasion and environmental conditions. The choice of material directly impacts the belt’s efficiency, maintenance needs, and lifespan.
To construct a conveyor belt, various materials are required, each serving a unique purpose in the belt’s structure and functionality. The core materials needed are cover material (such as rubber, PVC, or polyurethane) and reinforcement material (like fabric or steel cords). The cover material is selected based on the belt’s intended application, with considerations for environmental resistance (chemicals, temperature, abrasion) and compliance with health and safety standards. The reinforcement material is chosen based on the required strength and load-carrying capacity, with materials like polyester, nylon, and steel providing varying levels of tensile strength and durability. Additional components may include adhesives for bonding layers together, sidewalls or cleats for specific transport conditions, and coatings for enhanced performance characteristics.
The best material for a conveyor system depends largely on the specific application, including the type of materials being transported, environmental conditions, and operational requirements. For general purpose applications, rubber and fabric-reinforced belts are commonly used due to their versatility and cost-effectiveness. For food processing or pharmaceutical applications, polyurethane or PVC is preferred for their hygienic properties and resistance to chemicals and contamination. In heavy-duty or harsh environmental conditions, belts with steel cord reinforcement are ideal for their high tensile strength and durability. Ultimately, the optimal material choice is one that balances performance requirements, cost-effectiveness, and operational efficiency, ensuring the conveyor system runs smoothly and effectively under its intended conditions.
In heavy industries such as mining, steel is commonly used in conveyor belts due to its exceptional strength and durability. Steel cords or steel mesh reinforcement provides the necessary tensile strength to handle heavy loads and resist impacts from sharp or abrasive materials. The use of steel ensures that the conveyor belts can operate efficiently under demanding conditions, including high-stress environments and extreme temperatures. Additionally, stainless steel may be used in certain applications to provide resistance to corrosion, especially when the belt is exposed to moisture or chemicals.
For industrial applications like mining, Grade M rubber is often used for conveyor belts. This grade offers superior abrasion resistance and tensile strength, which are critical for handling rough, abrasive materials such as ores and rocks. Grade M rubber is designed to withstand the harsh conditions typical of heavy industry, providing durability and longevity to the conveyor belt. Additionally, it maintains its integrity under various environmental conditions, ensuring consistent performance in both high and low temperatures and in the presence of moisture or chemicals.
The surface of a conveyor belt in heavy industrial applications is typically made of a durable rubber compound, which can be natural rubber, SBR (Styrene-Butadiene Rubber), or synthetic rubber like nitrile or neoprene. This surface material is designed to resist wear and tear, abrasion, and impact from transported materials. For specific conditions, the rubber surface can be treated or layered with additional materials, such as PVC or polyurethane, to enhance properties like heat resistance, chemical resistance, or grip. The robust surface ensures that the belt can handle heavy-duty usage in mining and other industrial operations.
The strength of a rubber conveyor belt, especially in heavy industrial applications, is measured by its tensile strength and is usually in the range of 250 to 5000 N/mm (Newton per millimeter). This strength allows the belt to withstand the substantial stresses and loads typical in industries such as mining, where large quantities of heavy and abrasive materials are transported. The combination of multiple fabric plies or steel cords embedded within the rubber enhances the belt’s overall durability and load-bearing capacity, ensuring it can operate effectively and reliably under extreme conditions.
Grade 1 and Grade 2 conveyor belts differ mainly in their abrasion resistance. Grade 1 belts have higher abrasion resistance, making them suitable for applications where materials are highly abrasive, such as in mining and quarrying. These belts are designed to withstand significant wear and tear, providing a longer service life in harsh conditions. Grade 2 belts, while still durable, offer moderate abrasion resistance and are more suited for general-purpose applications where the materials being transported are less abrasive. The choice between the two grades depends on the specific demands of the operational environment and the nature of the materials being conveyed.
In heavy industrial applications, synthetic rubbers such as Neoprene (chloroprene rubber), Nitrile (NBR), and Styrene-Butadiene Rubber (SBR) are commonly used in conveyor belts. Neoprene offers excellent resistance to oils, chemicals, and heat, making it ideal for harsh environments. Nitrile is known for its resistance to oils and fuels, suitable for applications involving petroleum-based products. SBR provides good abrasion resistance and is cost-effective, making it a popular choice for general-purpose belts. These synthetic rubbers enhance the durability, flexibility, and overall performance of conveyor belts in demanding industrial conditions.
Last Updated on July 29, 2024 by Jordan Smith
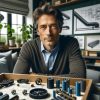
Jordan Smith, a seasoned professional with over 20 years of experience in the conveyor system industry. Jordan’s expertise lies in providing comprehensive solutions for conveyor rollers, belts, and accessories, catering to a wide range of industrial needs. From initial design and configuration to installation and meticulous troubleshooting, Jordan is adept at handling all aspects of conveyor system management. Whether you’re looking to upgrade your production line with efficient conveyor belts, require custom conveyor rollers for specific operations, or need expert advice on selecting the right conveyor accessories for your facility, Jordan is your reliable consultant. For any inquiries or assistance with conveyor system optimization, Jordan is available to share his wealth of knowledge and experience. Feel free to reach out at any time for professional guidance on all matters related to conveyor rollers, belts, and accessories.