Replacing or Refurbishment Repair Conveyor Pulley
The importance of maintaining and repairing conveyor pulleys cannot be overstated. Conveyor pulleys play a crucial role in industrial operations, ensuring the smooth and efficient transport of materials. Over time, these pulleys can experience wear and tear, leading to potential system failures and costly downtime. To mitigate these risks, it is essential to repair conveyor pulley components promptly. Timely repairs help maintain the overall efficiency and longevity of the conveyor system, preventing disruptions in the production process and ensuring continuous, reliable operations. Proper maintenance and repair of conveyor pulleys are vital for optimizing industrial workflow and productivity.
Common Issues Requiring Repair Conveyor Pulley
Wear and Tear
Wear and tear are among the most common issues necessitating the repair of a conveyor roller pulley. Over time, the repetitive motion and constant contact with the conveyor belt cause the pulley surface to deteriorate. The lagging, or the material covering the pulley, can wear down, reducing its effectiveness in providing traction and increasing the likelihood of slippage. This wear can lead to inefficient operation, increased energy consumption, and even potential damage to the conveyor belt.
Misalignment
Misalignment is another prevalent issue that requires the repair of a conveyor pulley. Misalignment can occur due to improper installation, shifting of the conveyor structure, or gradual loosening of the pulley components. When a pulley is misaligned, it can cause the conveyor belt to run off-track, leading to uneven wear and potentially severe damage to both the belt and the pulley. Misalignment also places additional strain on the motor and other components, potentially causing a complete system failure if not addressed promptly.
Damage from Foreign Objects
Conveyor systems often operate in environments where debris and foreign objects can come into contact with the pulleys. Items such as rocks, metal pieces, and other debris can cause significant damage to the pulley surface and the conveyor belt. Foreign objects can become lodged between the belt and the pulley, leading to punctures, tears, and other forms of damage. In severe cases, foreign objects can cause the pulley to seize, halting the conveyor system and necessitating immediate repair.
Bearing Failure
The bearings within a conveyor pulley are crucial for smooth operation. Bearing failure is a common issue that requires repair. Bearings can fail due to inadequate lubrication, contamination, overloading, or simply reaching the end of their operational life. When bearings fail, they can cause excessive noise, increased friction, and even lead to the pulley becoming immobile. Timely detection and replacement of faulty bearings are essential to maintain conveyor efficiency and prevent further damage.
Shaft Wear
The shaft of the conveyor pulley can experience wear over time, particularly at the points where it interacts with bearings and other components. Shaft wear can result in a loose fit, leading to vibrations, misalignment, and additional wear on the pulley and conveyor belt. Repairing or replacing worn shafts is necessary to ensure the proper functioning of the conveyor system.
Corrosion
Conveyor pulleys operating in harsh environments, especially those exposed to moisture, chemicals, or extreme temperatures, are susceptible to corrosion. Corrosion weakens the structural integrity of the pulley, reducing its effectiveness and lifespan. Regular inspections and timely repairs are essential to mitigate the effects of corrosion and maintain the conveyor system’s reliability.
Impact on Conveyor System Performance
The issues outlined above significantly impact the performance of a conveyor system. Wear and tear reduce the efficiency of the conveyor, leading to increased operational costs and downtime for repairs. Misalignment and bearing failure can cause the conveyor belt to run unevenly, leading to accelerated wear and potential breakdowns. Damage from foreign objects can halt operations entirely, requiring immediate attention to remove the debris and repair the pulley.
Addressing these common issues promptly through regular inspections and maintenance can prevent extensive damage and ensure the continuous, efficient operation of conveyor systems. Repairing conveyor pulleys when these problems arise is crucial to maintaining system performance and minimizing downtime.
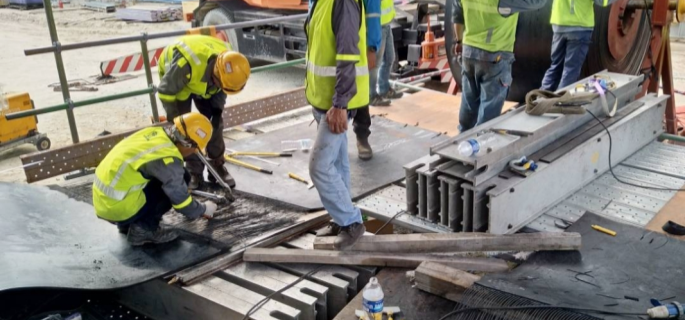
Tools Needed for Repair Conveyor Pulley
Wrenches
Wrenches are fundamental tools required for repairing conveyor pulleys. They are used to tighten and loosen bolts and nuts that secure the pulley components. A set of wrenches in various sizes is essential, as different parts of the pulley system may require different wrench sizes. Adjustable wrenches can also be handy for accommodating various bolt sizes.
Alignment Tools
Proper alignment is crucial for the efficient operation of conveyor pulleys. Alignment tools, such as laser alignment devices or alignment bars, help ensure that the pulley is correctly positioned relative to the conveyor belt. These tools provide precise measurements and visual guides, making it easier to achieve accurate alignment and prevent misalignment issues that can lead to excessive wear and operational inefficiencies.
Bearing Pullers
Bearing pullers are specialized tools designed to remove bearings from the pulley shaft without causing damage to the bearing or the shaft. Bearings often fit tightly and can be challenging to remove manually. Bearing pullers come in various designs, including mechanical and hydraulic types, providing the necessary force to extract the bearings safely and efficiently.
Safety Equipment
Safety equipment is paramount when repairing conveyor pulleys. This includes personal protective equipment (PPE) such as gloves, safety glasses, and hard hats to protect against potential injuries. Additionally, hearing protection may be necessary in noisy environments. Ensuring that all repair personnel are equipped with the appropriate safety gear is essential for preventing accidents and injuries during the repair process.
Lubrication Tools
Lubrication tools, such as grease guns, are necessary for maintaining the bearings and other moving parts of the conveyor pulley. Proper lubrication reduces friction, prevents wear, and extends the lifespan of the components. Having the right tools and lubricants on hand ensures that the pulley operates smoothly and efficiently after repairs.
Measuring Tools
Accurate measurements are vital for the successful repair and maintenance of conveyor pulleys. Measuring tools, such as calipers, micrometers, and tape measures, help ensure that components are correctly sized and aligned. These tools are essential for verifying dimensions, checking tolerances, and ensuring that all parts fit together as intended.
Hammers and Mallets
Hammers and mallets are useful for various tasks during pulley repair, such as tapping components into place or gently persuading parts during disassembly and reassembly. Soft-faced mallets are particularly useful for applying force without damaging the surfaces of the components.
Torque Wrenches
Torque wrenches are critical for ensuring that bolts and nuts are tightened to the correct specifications. Over-tightening or under-tightening can lead to component failure or operational issues. Torque wrenches provide precise control over the amount of torque applied, ensuring that all connections are secure and properly tensioned.
Pulling and Lifting Equipment
Depending on the size and weight of the conveyor pulley, pulling and lifting equipment, such as chain hoists, come-alongs, and jacks, may be necessary to move and position the pulley during repairs. These tools provide the mechanical advantage needed to handle heavy components safely and efficiently.
Cleaning Supplies
Cleaning supplies, such as brushes, rags, and solvents, are essential for preparing the pulley and its components for repair. Cleaning the parts thoroughly removes dirt, grease, and contaminants, ensuring that repairs are performed on clean surfaces and reducing the risk of further issues.
Having the right tools is crucial for the successful repair of conveyor pulleys. These tools not only make the repair process more efficient but also ensure that the repairs are performed correctly and safely. Investing in quality tools and maintaining them properly can significantly extend the lifespan of conveyor systems and improve their overall performance.
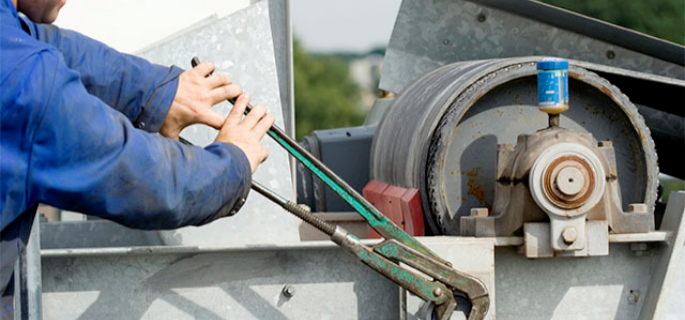
Step-by-Step Guide to Repair Conveyor Pulley
Initial Inspection
The first step in repairing a conveyor pulley is to conduct a thorough inspection. This involves examining the pulley and its components to identify the specific issues that need to be addressed. Look for signs of wear and tear, misalignment, damage from foreign objects, bearing failure, and corrosion. Document all findings to create a comprehensive repair plan.
- Visual Inspection: Start with a visual inspection of the pulley surface, looking for wear patterns, cracks, and other visible damage. Check the condition of the lagging and note any areas that need replacement.
- Operational Check: Run the conveyor system and observe the pulley in operation. Listen for unusual noises and watch for irregular belt movement, which can indicate misalignment or bearing issues.
- Component Inspection: Examine the bearings, shaft, and mounting hardware for signs of wear or damage. Ensure that all components are secure and functioning correctly.
Disassembly
Once the inspection is complete, proceed with disassembling the pulley. This step involves removing the pulley from the conveyor system and taking apart its components for repair.
- Safety Preparation: Ensure the conveyor system is shut down and locked out to prevent accidental start-up. Use appropriate safety gear and follow all safety protocols.
- Remove the Belt: Carefully remove the conveyor belt from the pulley. This may involve loosening tensioning devices and sliding the belt off the pulley.
- Detach the Pulley: Use wrenches and other appropriate tools to remove the bolts and nuts securing the pulley to the conveyor structure. Carefully lift the pulley away from the system using lifting equipment if necessary.
- Disassemble Components: With the pulley removed, disassemble its components, such as the bearings, shaft, and lagging. Use bearing pullers and other specialized tools to extract the bearings without causing damage.
Repair and Replacement
With the pulley disassembled, address the specific issues identified during the inspection. This step involves repairing or replacing damaged components.
- Lagging Replacement: If the lagging is worn or damaged, remove the old lagging material and clean the pulley surface. Apply new lagging according to the manufacturer’s instructions, ensuring a secure and even application.
- Bearing Replacement: If the bearings are faulty, replace them with new ones. Ensure that the new bearings are correctly sized and lubricated before installation. Use bearing pullers and installation tools to avoid damaging the new bearings.
- Shaft Repair: If the shaft is worn or damaged, repair or replace it as necessary. Machining or welding may be required to restore the shaft to its original specifications.
- Component Refurbishment: Clean and refurbish other components as needed. This may involve removing corrosion, reapplying protective coatings, and replacing worn hardware.
Reassembly
After completing the necessary repairs, reassemble the pulley and its components. This step involves putting the pulley back together and ensuring all parts are correctly aligned and secured.
- Reassemble Components: Begin by reassembling the individual components of the pulley, such as the bearings, shaft, and lagging. Use torque wrenches to apply the correct amount of torque to bolts and nuts, ensuring secure connections.
- Align the Pulley: Use alignment tools to ensure that the pulley is correctly aligned with the conveyor system. Proper alignment is crucial for preventing wear and ensuring smooth operation.
- Reattach the Pulley: Carefully reattach the pulley to the conveyor structure, using lifting equipment if necessary. Secure the pulley with the appropriate bolts and nuts, tightening them to the specified torque.
Final Inspection and Testing
Once the pulley is reassembled and reinstalled, conduct a final inspection and testing to ensure that the repair was successful and that the pulley operates correctly.
- Visual Check: Perform a visual check to ensure that all components are correctly assembled and that there are no loose or missing parts.
- Operational Test: Run the conveyor system and observe the pulley in operation. Check for smooth movement, proper alignment, and absence of unusual noises. Ensure that the conveyor belt tracks correctly and that there is no slippage.
- Adjustments: Make any necessary adjustments to the pulley alignment, tensioning devices, or other components to achieve optimal performance. Repeat the operational test to verify that the adjustments were successful.
Maintenance and Monitoring
After completing the repair, implement a maintenance and monitoring plan to ensure the long-term reliability of the conveyor pulley. Regular maintenance helps prevent future issues and extends the lifespan of the pulley and conveyor system.
- Lubrication Schedule: Establish a regular lubrication schedule for the bearings and other moving parts. Use the appropriate lubricants and follow the manufacturer’s recommendations for frequency and application methods.
- Inspection Routine: Implement a routine inspection program to regularly check the condition of the pulley and its components. Look for signs of wear, misalignment, and other potential issues.
- Record Keeping: Maintain detailed records of all repairs, maintenance activities, and inspections. Document any issues identified and the actions taken to address them. This information is valuable for tracking the pulley’s performance and identifying trends that may indicate the need for further maintenance or repairs.
Training and Safety
Ensure that all personnel involved in the repair and maintenance of conveyor pulleys are properly trained and aware of safety protocols. Proper training and adherence to safety standards are essential for preventing accidents and ensuring safe and effective repairs.
- Safety Training: Provide comprehensive safety training for all personnel, covering topics such as lockout/tagout procedures, proper use of tools and equipment, and personal protective equipment (PPE) requirements.
- Technical Training: Offer technical training on the specific procedures and techniques for repairing and maintaining conveyor pulleys. Ensure that personnel are familiar with the tools and methods used in the repair process.
- Safety Protocols: Establish and enforce strict safety protocols for all repair and maintenance activities. Conduct regular safety audits and address any potential hazards promptly.
The process of repairing a conveyor pulley involves several critical steps, from initial inspection to final testing and ongoing maintenance. By following a detailed and systematic approach, it is possible to effectively repair and maintain conveyor pulleys, ensuring the continuous and efficient operation of conveyor systems. Proper training and adherence to safety protocols are essential for achieving successful repairs and preventing accidents.
6 Repair Conveyor Pulley Practices to Get You Back Up and Running
Regular Inspection and Maintenance
- Visual Checks: Regularly inspect pulleys for visible signs of wear, cracks, or damage. Check for alignment issues and unusual noise.
- Scheduled Maintenance: Implement a routine maintenance schedule to catch potential problems early. This should include lubrication, checking for proper tension, and ensuring all components are in good condition.
Use of Non-Destructive Testing (NDT)
- Ultrasonic Testing: Utilize ultrasonic testing to detect internal cracks or flaws that are not visible externally.
- Magnetic Particle Inspection: Apply magnetic particle inspection for detecting surface and slightly subsurface discontinuities in ferromagnetic materials.
Timely Replacement of Worn Components
- Bearings: Replace worn or damaged bearings promptly to prevent further damage to the pulley and conveyor system.
- Shafts and Lagging: Inspect and replace worn shafts and lagging. Ensure that the materials used for replacement match the operational requirements of the pulley.
Dynamic Balancing
- Balancing Process: Ensure the pulley is dynamically balanced to prevent excessive vibration during operation. This involves rotating the pulley at operational speed and making adjustments to balance it.
- Regular Rebalancing: Perform rebalancing periodically, especially after significant repairs or modifications.
Proper Reassembly Techniques
- Alignment: Ensure all components are correctly aligned during reassembly. Misalignment can cause uneven wear and operational inefficiencies.
- Torque Specifications: Use proper torque specifications when reassembling components to ensure they are securely fastened without causing damage.
Final Testing and Quality Assurance
- Operational Testing: After reassembly, test the pulley under operational conditions to ensure it functions correctly. Check for any abnormal noise, vibration, or misalignment.
- Quality Checks: Perform a thorough quality check to ensure all repairs meet the required standards. Document the repair process and results for future reference.
Implementation Example
Step-by-Step Repair Scenario
- Initial Inspection:
- Conduct a visual and NDT inspection of the conveyor pulley.
- Identify wear on the bearings and cracks on the pulley surface.
- Disassembly:
- Disconnect the pulley from the conveyor system.
- Remove the damaged bearings and worn lagging.
- Cleaning and Component Replacement:
- Clean all parts thoroughly.
- Replace the bearings and lagging with new, suitable materials.
- Balancing:
- Perform dynamic balancing to ensure the pulley runs smoothly.
- Reassembly:
- Reassemble the pulley, ensuring all components are aligned and securely fastened.
- Use torque specifications to avoid over-tightening.
- Final Testing:
- Test the pulley under operational conditions.
- Conduct a final quality check and document the process.
By following these best practices, you can ensure a quick and efficient repair process, minimizing downtime and maintaining the operational efficiency of your conveyor system.
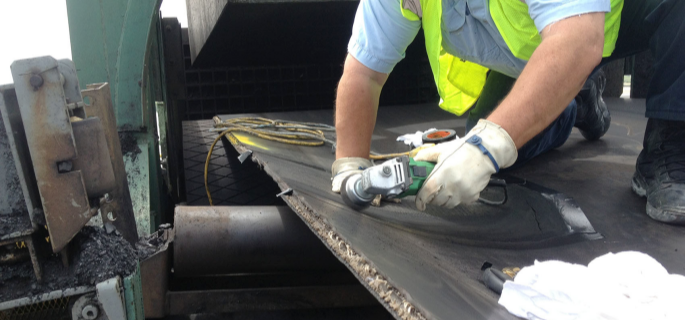
Refurbishment Repair Conveyor Pulley
Refurbishment and repair of conveyor pulleys involve several detailed steps to ensure they function efficiently and have a prolonged lifespan. Here’s a detailed description in English:
Refurbishment Process of Conveyor Pulleys
- Inspection and Assessment: The first step involves a thorough inspection of the conveyor pulley to assess its condition. This includes checking for wear, damage, and alignment issues.
- Disassembly: The pulley is carefully disassembled, separating it from the conveyor system and removing any components that need to be refurbished or replaced.
- Cleaning: All parts of the pulley are cleaned to remove dirt, debris, and old lubricants. This ensures that any damage or wear is clearly visible and that the components are ready for refurbishment.
- Non-Destructive Testing (NDT): Techniques like ultrasonic testing, magnetic particle inspection, or dye penetrant inspection are used to detect cracks, flaws, or weaknesses in the pulley structure that are not visible to the naked eye.
- Bearing Replacement: Worn or damaged bearings are replaced to ensure smooth and efficient operation of the pulley. This may also include the replacement of seals and housings.
- Shaft Repair or Replacement: The pulley shaft is inspected for wear and damage. If necessary, the shaft is repaired or replaced. This step is critical for maintaining the structural integrity and alignment of the pulley.
- Lagging Replacement: The pulley lagging, which provides grip and protects the pulley surface, is inspected and replaced if worn out. Various types of lagging materials, such as rubber, ceramic, or polyurethane, can be used depending on the application.
- Balancing: The pulley is dynamically balanced to ensure it rotates evenly without causing excessive vibration. This is crucial for maintaining the longevity and efficiency of the conveyor system.
- Reassembly: Once all repairs and replacements are complete, the pulley is reassembled. This includes reinstalling the bearings, shaft, and any other components.
- Final Testing and Quality Check: The refurbished pulley undergoes final testing to ensure it meets operational standards. This may include load testing, alignment checks, and a final inspection to ensure all components are correctly installed and functioning properly.
- Reinstallation: The refurbished pulley is reinstalled in the conveyor system. Proper alignment and secure installation are crucial to ensure efficient operation.
Benefits of Refurbishment
- Cost Savings: Refurbishing a conveyor pulley is often more cost-effective than purchasing a new one.
- Extended Equipment Life: Regular refurbishment can significantly extend the life of the pulley and the conveyor system.
- Improved Performance: Refurbished pulleys can operate more efficiently, reducing downtime and maintenance costs.
- Environmental Benefits: Refurbishment is a sustainable option, reducing waste and the need for new materials.
Common Issues Addressed in Refurbishment
- Surface Wear: Replacing lagging and resurfacing the pulley.
- Bearing Failure: Replacing or upgrading bearings and seals.
- Shaft Wear or Damage: Repairing or replacing the pulley shaft.
- Misalignment: Correcting alignment issues to prevent further wear and tear.
By following these steps, the refurbishment and repair process ensures that conveyor pulleys are restored to optimal condition, thereby enhancing the overall efficiency and reliability of the conveyor system.
Safety Precautions During Repair Conveyor Pulley
Ensuring safety during the process to repair conveyor pulley systems is paramount. The environment where conveyor pulleys operate is often hazardous, involving heavy machinery, moving parts, and potentially dangerous materials. Therefore, adherence to safety protocols is essential to protect personnel and maintain a safe working environment.
Safety Measures and Best Practices
- Risk Assessment and Planning:
- Conduct a thorough risk assessment before commencing any repair work. Identify potential hazards, and plan appropriate control measures.
- Prepare a detailed repair plan that outlines each step of the repair process, including the tools and equipment needed.
- Personal Protective Equipment (PPE):
- Ensure all personnel involved in the repair wear appropriate PPE. This includes hard hats, safety glasses, gloves, steel-toed boots, and high-visibility clothing.
- For certain tasks, additional PPE such as hearing protection or respirators may be necessary.
- Lockout/Tagout (LOTO) Procedures:
- Implement strict LOTO procedures to ensure that the conveyor system is completely de-energized before starting any repair work.
- Verify isolation by testing the system to confirm that all energy sources have been effectively isolated.
- Proper Training:
- Ensure that all personnel involved in the repair are adequately trained in both the repair techniques and the safety protocols.
- Conduct regular safety drills and refresher courses to keep everyone up-to-date with the latest safety practices.
- Safe Handling of Tools and Equipment:
- Use tools and equipment that are in good condition and appropriate for the task. Regularly inspect tools for wear and damage.
- Follow proper lifting techniques and use lifting aids where necessary to prevent injuries from manual handling.
- Clear Communication:
- Establish clear communication channels among the repair team. Use hand signals or communication devices to ensure that everyone is aware of ongoing operations.
- Post safety signs and warnings in the repair area to alert other workers to the ongoing repair work.
- Housekeeping:
- Maintain a clean and organized work area to prevent trips, slips, and falls. Remove any unnecessary tools or debris from the repair site.
- Ensure that all materials and tools are stored safely and securely when not in use.
Emergency Procedures
- Emergency Equipment:
- Ensure that emergency equipment, such as first aid kits, fire extinguishers, and emergency eyewash stations, are readily accessible.
- Regularly inspect and maintain emergency equipment to ensure it is in working order.
- Emergency Response Plan:
- Develop and communicate an emergency response plan to all personnel. This plan should outline the steps to take in case of an accident or emergency.
- Conduct regular emergency drills to ensure that all workers are familiar with the response procedures.
By following these safety measures and best practices, the risk of accidents and injuries during the repair conveyor pulley process can be significantly reduced. A safe working environment not only protects personnel but also enhances the efficiency and effectiveness of the repair work.
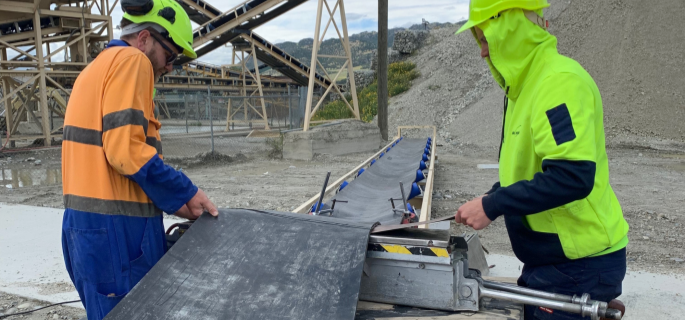
Lubrication and Maintenance Tips for Repair Conveyor Pulley
Proper lubrication and maintenance are key to extending the lifespan of conveyor pulleys and minimizing the frequency of repairs. Effective lubrication reduces friction, wear, and the risk of breakdowns, while regular maintenance ensures that any potential issues are identified and addressed before they escalate.
Lubrication Tips
- Choosing the Right Lubricant:
- Select lubricants that are specifically designed for conveyor pulley applications. These lubricants should have the appropriate viscosity and additives to withstand the operational conditions.
- Consider the operating environment, such as temperature and humidity, when choosing a lubricant. Some lubricants are formulated for high-temperature environments, while others are better suited for wet or dusty conditions.
- Lubrication Schedule:
- Develop a lubrication schedule based on the manufacturer’s recommendations and the operating conditions of the conveyor system.
- Regularly apply lubricant to all moving parts, including bearings, shafts, and gears. Over-lubrication and under-lubrication can both cause issues, so it’s important to follow the recommended quantities.
- Lubrication Techniques:
- Use appropriate tools for applying lubricants, such as grease guns or oil dispensers, to ensure even distribution.
- Clean the application points before applying lubricant to prevent contamination with dirt and debris.
Maintenance Tips
- Regular Inspections:
- Conduct regular inspections of the conveyor pulley system to check for signs of wear, damage, or misalignment. Look for unusual noises, vibrations, and visible wear on the pulley surface.
- Inspect the belt alignment and tension to ensure that the conveyor system operates smoothly.
- Preventive Maintenance:
- Implement a preventive maintenance program that includes scheduled checks and servicing of all components.
- Replace worn or damaged parts promptly to prevent them from causing further damage to the system.
- Cleaning and Housekeeping:
- Keep the conveyor system clean and free of debris. Accumulated dirt and material can cause additional wear and increase the risk of breakdowns.
- Regularly clean the pulleys, belts, and surrounding areas to maintain optimal performance.
- Record Keeping:
- Maintain detailed records of all maintenance activities, including lubrication schedules, inspections, and repairs. This helps in tracking the performance of the conveyor system and planning future maintenance.
- Use maintenance software to schedule and record maintenance activities, ensuring that nothing is overlooked.
Benefits of Proper Lubrication and Maintenance
- Extended Equipment Life: Regular lubrication and maintenance can significantly extend the lifespan of conveyor pulleys and other components, reducing the need for frequent replacements.
- Improved Efficiency: A well-maintained conveyor system operates more efficiently, with fewer interruptions and breakdowns.
- Cost Savings: Preventive maintenance helps avoid costly repairs and downtime, resulting in overall cost savings for the operation.
- Enhanced Safety: Proper maintenance reduces the risk of accidents caused by equipment failures, ensuring a safer working environment.
By following these lubrication and maintenance tips, businesses can keep their conveyor systems running smoothly and efficiently, reducing the likelihood of needing to repair conveyor pulley components frequently.
Signs That Indicate the Need to Repair Conveyor Pulley
Early detection of issues in conveyor pulley systems can prevent major breakdowns and costly repairs. Understanding the warning signs that indicate a need to repair conveyor pulley components is crucial for maintaining optimal operation and preventing unexpected downtime.
Warning Signs to Watch For
- Unusual Noises:
- Squeaking or Grinding: These noises often indicate that there is insufficient lubrication or that bearings are worn out.
- Banging or Clunking: These sounds can signal loose or misaligned components that need immediate attention.
- Vibrations:
- Excessive Vibrations: Vibrations that are more pronounced than usual can indicate misalignment, unbalanced pulleys, or worn bearings.
- Intermittent Vibrations: Occasional vibrations can also point to irregularities in the pulley surface or material buildup.
- Visible Wear or Damage:
- Surface Wear: Look for signs of wear on the pulley surface, such as grooves, scratches, or deformation. This can result from improper belt tension or material abrasion.
- Cracks or Breaks: Any visible cracks or breaks in the pulley or its components should be addressed immediately to prevent further damage.
- Belt Issues:
- Belt Slippage: If the conveyor belt slips frequently, it can indicate issues with pulley alignment or tension.
- Fraying or Damage: A damaged or frayed belt can cause uneven wear on the pulley and should be replaced promptly.
- Overheating:
- Excessive Heat: If the pulley or surrounding components are unusually hot, it may indicate friction due to poor lubrication or mechanical issues.
- Burnt Smell: A burnt smell can be a sign of overheating and potential damage to the pulley or belt.
- Operational Inefficiencies:
- Reduced Performance: A noticeable drop in the performance or speed of the conveyor system can be a sign of underlying issues with the pulley.
- Increased Energy Consumption: If the system is consuming more energy than usual, it may be due to increased friction or mechanical resistance.
Diagnostic Techniques
- Visual Inspection:
- Regular visual inspections can help identify signs of wear and damage early. Use a checklist to ensure all components are thoroughly examined.
- Auditory Inspection:
- Listening for unusual sounds during operation can provide early warning signs of potential issues.
- Thermal Imaging:
- Thermal imaging cameras can detect hotspots and areas of excessive heat, indicating friction or mechanical problems.
- Vibration Analysis:
- Vibration analysis tools can measure the frequency and amplitude of vibrations, helping to diagnose misalignment or imbalance issues.
- Performance Monitoring:
- Monitor the performance of the conveyor system, including speed, load capacity, and energy consumption, to identify any deviations from normal operation.
Addressing Identified Issues
- Immediate Repairs:
- Address any identified issues promptly to prevent further damage and avoid unexpected downtime.
- Use the appropriate tools and techniques to repair or replace damaged components.
- Preventive Measures:
- Implement preventive measures based on the identified issues, such as adjusting alignment, tightening loose components, or improving lubrication practices.
- Schedule regular maintenance checks to ensure that potential problems are addressed before they escalate.
By recognizing and addressing the warning signs that indicate the need to repair conveyor pulley systems, businesses can maintain the efficiency and reliability of their operations. Early detection and prompt action are key to preventing major breakdowns and ensuring the longevity of the conveyor system.
Replacing or Repair Conveyor Pulley
Comparison Table: Repair vs. Replacement of Conveyor Pulleys
This table provides a clear comparison between repairing and replacing conveyor pulleys, helping in decision-making based on various factors such as cost, downtime, damage extent, and operational impact.
Replacing Conveyor Pulleys
Steps for Replacing Conveyor Pulleys
- Specification and Selection:
- Determine the specifications of the required pulley, including size, type, and load capacity.
- Select a pulley that meets or exceeds these specifications.
- Procurement:
- Order the new pulley from a reputable supplier.
- Ensure it meets all necessary quality and performance standards.
- Removal of Old Pulley:
- Safely disconnect and remove the old pulley from the conveyor system.
- Dispose of or recycle the old pulley appropriately.
- Preparation for Installation:
- Ensure the mounting points and connections are clean and free from damage.
- Prepare any necessary mounting hardware.
- Installation of New Pulley:
- Install the new pulley, ensuring it is properly aligned and securely mounted.
- Connect all necessary components, such as bearings and shafts.
- Alignment and Testing:
- Align the pulley with the conveyor system to ensure smooth operation.
- Conduct initial testing to check for proper rotation and load handling.
- Final Adjustments:
- Make any necessary adjustments to ensure optimal performance.
- Secure all components and perform a final inspection.
Which Option Should I Choose:Replacing or Repair Conveyor Pulley
To decide between pulley repairing or replacement, consider the following points:
Repairing
When to Choose Repairing:
- Shell Condition:
- The shell of the pulley is not significantly worn, cracked, or deformed.
- There are no signs of structural compromise.
- Shaft Condition:
- The shaft is straight and free from severe wear or damage.
- There is no significant corrosion or weakening.
- Lagging, Bearings, and Locking Assembly:
- These components show signs of wear or damage but are replaceable.
- Lagging (the rubber or ceramic coating on the pulley) might be worn out but can be re-applied.
Benefits of Repairing:
- Cost Savings: Repairing conveyor pulley is cheaper than replacement since it involves repairing or replacing only the worn-out parts.
- Reduced Downtime: Reconditioning can be faster than waiting for a new pulley to be manufactured and delivered.
- Sustainability: Reconditioning is more environmentally friendly as it involves refurbishing existing components rather than discarding them.
Replacement
When to Choose Replacement:
- Shell Damage:
- The shell is cracked, deeply worn, or otherwise structurally compromised.
- There is extensive corrosion or deformation.
- Shaft Damage:
- The shaft is bent, cracked, or significantly worn.
- There is substantial corrosion or material loss.
- Economic Considerations:
- The cost of reconditioning approaches or exceeds the cost of a new pulley.
- The time required for reconditioning is not significantly shorter than the time for replacement.
Benefits of Replacement:
- Reliability: A new pulley provides the assurance of a fully functional, defect-free component.
- Long-Term Solution: New pulleys often come with warranties and are less likely to require immediate future repairs.
- Safety: Ensures that all components are in top condition, reducing the risk of accidents and unplanned downtime.
Potential Risks of Operating with Damaged Components:
- Conveyor Downtime: Operating with a damaged shell or shaft can lead to unexpected failures, causing significant downtime.
- Belt Tracking Issues: Damaged pulleys can cause the conveyor belt to track improperly, leading to misalignment and further damage.
- Conveyor Belt Damage: A compromised pulley can damage the conveyor belt, resulting in expensive repairs or replacements.
Practical Steps for Decision Making:
- Inspection: Conduct a thorough inspection of the pulley’s shell, shaft, lagging, bearings, and locking assembly.
- Cost Analysis: Compare the costs of reconditioning versus replacement, considering both immediate and long-term expenses.
- Risk Assessment: Evaluate the potential risks associated with continuing to operate a damaged pulley.
- Expert Consultation: Consult with a pulley or conveyor system expert to get a professional opinion on the best course of action.
By carefully evaluating the condition of your pulley and considering both the immediate and long-term implications, you can make a well-informed decision between reconditioning and replacement.
FAQs about Repair Conveyor Pulley
Yes, a pulley can be repaired, depending on the extent of the damage. Minor issues such as surface wear or slight misalignment can often be addressed through maintenance procedures such as re-lagging the pulley or adjusting its alignment. Re-lagging involves replacing the worn lagging material, which restores the friction surface and extends the pulley’s lifespan. For more severe damage, such as cracks or structural issues, the repair might involve welding or reinforcing the affected areas. In some cases, it might be more cost-effective and safer to replace the pulley entirely rather than attempting extensive repairs. Regular inspections and preventive maintenance can help identify issues early and determine the best course of action for pulley repair.
Repairing a hole in a conveyor belt involves several steps to ensure the belt remains functional and safe for use. First, stop the conveyor system and clean the damaged area thoroughly, removing any debris or contaminants. Next, trim the edges of the hole to create a clean and smooth surface. Apply a suitable adhesive to the area around the hole and attach a patch made from the same material as the conveyor belt. Press the patch firmly to ensure it adheres properly, and allow the adhesive to cure according to the manufacturer’s instructions. For larger holes or more severe damage, a vulcanization process might be required, where heat and pressure are used to bond the patch to the belt permanently. Regular inspection and maintenance can help prevent holes and other damage from occurring.
Joining a broken conveyor belt typically involves a process called splicing. There are several methods of splicing, including mechanical splicing and vulcanized splicing. Mechanical splicing uses metal fasteners to join the ends of the belt. First, cut the belt ends squarely and clean them. Install the fasteners according to the manufacturer’s instructions, ensuring they are evenly spaced and securely attached. Vulcanized splicing, on the other hand, involves using heat and pressure to bond the belt ends together. This method creates a stronger and more durable joint. To vulcanize, prepare the belt ends by cutting them in a specified pattern and applying a bonding agent. Place the belt ends in a vulcanizing press and apply heat and pressure for a specific duration. After cooling, the belt will have a seamless joint that is as strong as the original belt. Each method has its advantages, and the choice depends on the application and belt type.
There are several signs that indicate a pulley might need replacing. Regular inspections are crucial to identify these signs early. Look for visible wear on the pulley’s surface, such as grooves, cracks, or excessive smoothness, which can reduce its grip on the conveyor belt. Listen for unusual noises like squeaking or grinding, which can indicate bearing issues or misalignment. Check for any signs of rust or corrosion, especially in environments with high humidity or exposure to chemicals. If the pulley frequently causes belt slippage or misalignment despite proper tension adjustments, it might be a sign of internal damage. Additionally, excessive vibration during operation can signal that the pulley is out of balance or worn out. If any of these symptoms are observed, it’s essential to assess the pulley thoroughly and consider replacement to prevent further damage to the conveyor system. Regular maintenance and prompt replacement of damaged pulleys ensure the system’s efficiency and longevity.
Assess the Tear: Inspect the tear to determine its size and the extent of damage.
Clean the Area: Clean the area around the tear to remove any dirt, grease, or debris.
Apply Adhesive: Use a high-quality conveyor belt repair adhesive to cover the tear.
Reinforce with Patches: Apply repair patches on both sides of the tear, ensuring they are firmly pressed into the adhesive.
Cure Time: Allow the adhesive to cure as per the manufacturer’s instructions.
Test: After the adhesive has cured, test the belt to ensure the repair is holding.
The best glue for repairing a conveyor belt is typically a high-strength, industrial-grade adhesive designed specifically for conveyor belts, such as SC2000 Cold Vulcanizing Cement or 3M Scotch-Weld Urethane Adhesive.
The pulley in a conveyor belt system is commonly referred to as a drive pulley (which drives the belt) and an idler pulley (which guides or supports the belt).
Clean the Ends: Clean the ends of the broken belt thoroughly.
Trim and Align: Trim the ends if necessary and align them correctly.
Splice: Use a splicing method suitable for your belt type (e.g., mechanical fasteners, vulcanizing).
Apply Adhesive: If using an adhesive method, apply the adhesive and press the ends together.
Reinforce: Use splicing materials to reinforce the joint.
Cure: Allow any adhesive or vulcanizing process to cure completely.
Test: Once cured, test the belt to ensure the joint is secure.
Conveyor belt splicing is the process of joining two pieces of conveyor belt together. This can be done through mechanical means (like using metal fasteners) or through vulcanizing, which uses heat and pressure to bond the belt ends together.
An idler pulley in a belt conveyor system is a pulley that supports the belt and maintains tension but does not drive the belt. Idler pulleys are used to guide the belt, provide tension, and help the belt to move smoothly over the conveyor system.
Last Updated on August 8, 2024 by Jordan Smith
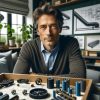
Jordan Smith, a seasoned professional with over 20 years of experience in the conveyor system industry. Jordan’s expertise lies in providing comprehensive solutions for conveyor rollers, belts, and accessories, catering to a wide range of industrial needs. From initial design and configuration to installation and meticulous troubleshooting, Jordan is adept at handling all aspects of conveyor system management. Whether you’re looking to upgrade your production line with efficient conveyor belts, require custom conveyor rollers for specific operations, or need expert advice on selecting the right conveyor accessories for your facility, Jordan is your reliable consultant. For any inquiries or assistance with conveyor system optimization, Jordan is available to share his wealth of knowledge and experience. Feel free to reach out at any time for professional guidance on all matters related to conveyor rollers, belts, and accessories.