Replacement Gravity Rollers: Essential for Smooth Operations
Gravity rollers play a pivotal role in the seamless operation of conveyor systems, serving as the backbone for material handling across numerous industries. These rollers facilitate the movement of goods with minimal effort, leveraging gravity to propel items along the conveyor belt. However, like all mechanical components, gravity rollers are subject to wear and tear, necessitating timely replacements to maintain operational efficiency. This is where the significance of replacement gravity rollers comes into play. By integrating high-quality replacement gravity rollers into conveyor systems, businesses can significantly enhance their efficiency and productivity. This upgrade not only ensures the smooth running of operations but also minimizes downtime caused by equipment failure, making it a critical consideration for industries aiming to optimize their material handling processes and maintain a competitive edge.
What Are Replacement Gravity Rollers
Replacement gravity rollers are integral components of conveyor systems, specifically designed to facilitate the autonomous movement of goods across various distances within industrial and commercial environments. These rollers rely on the force of gravity to propel items forward, making them an energy-efficient solution for material handling. The need for replacement gravity rollers arises when existing rollers become worn out or damaged, affecting the system’s efficiency and productivity. By integrating high-quality replacements, businesses can ensure their conveyor systems operate smoothly, maintain high throughput rates, and extend the lifespan of the entire system. Below, we explore the definition, function, and role of replacement gravity rollers in greater detail.
Definition and Function of Replacement Gravity Rollers
Before diving into the specifics, it’s essential to understand the broader context in which replacement gravity rollers operate and their significance in the material handling industry.
- Core Component: At their core, replacement gravity rollers are cylindrical devices that facilitate the movement of goods by allowing them to roll effortlessly from one location to another within a conveyor system.
- Material Diversity: These rollers are manufactured from a variety of materials, such as steel, aluminum, and plastic, each selected for its durability, weight, and suitability for different operational environments and types of cargo.
- Energy Efficiency: Leveraging gravity means these rollers require no external power source for operation, making them an environmentally friendly and cost-effective choice for moving goods.
- Ease of Maintenance and Replacement: Designed for quick installation and minimal maintenance, replacement gravity rollers can be easily swapped out, minimizing downtime and maintaining productivity.
- Adaptability: They are versatile enough to handle a wide range of products, from lightweight packages to heavy pallets, across industries like manufacturing, distribution, and retail.
- Cost Savings: Regularly replacing worn or damaged rollers can significantly extend the life of conveyor systems, offering a cost-effective alternative to complete system overhauls.
- Customization Options: Available in various sizes and with different surface treatments, replacement gravity rollers can be tailored to meet specific operational needs, enhancing efficiency and performance.
The Role of Replacement Gravity Rollers in Material Handling and Logistics
The adoption of replacement gravity rollers within conveyor systems plays a pivotal role in optimizing material handling and logistics operations across several fronts:
- Enhancing Operational Efficiency: They are crucial for maintaining the smooth flow of goods, ensuring timely and efficient transport from one stage of the operation to the next.
- Improving Workplace Safety: Automating the movement of goods reduces the need for manual handling, thereby lowering the risk of workplace injuries.
- Maximizing Space Utilization: Conveyor systems designed with gravity rollers can be configured to make the most of available space, improving the overall layout and efficiency of warehouses and distribution centers.
- Streamlining Inventory Management: The orderly movement of goods facilitated by gravity rollers aids in better inventory control and accuracy.
- Providing Operational Flexibility: The ease of integrating replacement gravity rollers into existing systems allows for quick adjustments to meet changing operational demands.
- Facilitating Scalability: As business needs grow, the system can be expanded by adding more rollers, offering a scalable solution to increasing demand.
- Ensuring Product Integrity: The gentle handling of items on gravity rollers minimizes the risk of damage during processing and transport.
- Seamless Integration with Automation: They can be easily incorporated into automated systems, further enhancing efficiency and reducing manual intervention.
Understanding the definition, function, and role of replacement gravity rollers underscores their importance in the efficient operation of conveyor systems and the broader context of material handling and logistics. By prioritizing the maintenance and timely replacement of these components, businesses can achieve higher operational efficiency, safety, and productivity.
Types of Replacement Gravity Rollers
The selection of replacement gravity rollers is critical for maintaining the efficiency and longevity of conveyor systems. These rollers come in various types, each designed to meet specific operational needs and applications. Below, we explore six types of replacement gravity rollers, detailing their characteristics and uses.
Replacement Gravity Rollers for Sale
Finding the right gravity conveyor rollers replacement for sale involves understanding the specific needs of your conveyor system. Here’s what to consider:
- Material Options: Rollers are available in steel, aluminum, and plastic, each offering different benefits in terms of weight, durability, and cost.
- Load Capacity: Ensure the rollers can support the weight of your products without deforming or failing.
- Surface Finish: Options include smooth, grooved, or coated surfaces to improve grip and reduce noise.
- Environmental Suitability: Some rollers are designed for harsh environments, including high moisture or temperature conditions.
- Compatibility: Rollers must fit existing conveyor frames and systems seamlessly.
- Supplier Reputation: Purchase from reputable suppliers known for quality products and support.
- Customization: Some suppliers offer custom sizes and configurations to meet unique operational requirements.
- Price vs. Quality: Balance cost with the need for durability and long-term performance.
Heavy Duty Gravity Roller Conveyor
Heavy-duty gravity roller conveyors are designed for applications requiring the movement of heavy loads. They are characterized by:
- Robust Construction: Made from high-grade materials like thick-walled steel tubing for increased durability.
- High Load Capacity: Engineered to handle heavier loads, often exceeding several hundred pounds per roller.
- Larger Diameter Rollers: Typically feature larger diameters to distribute weight more effectively and reduce the impact on individual rollers.
- Enhanced Bearings: Equipped with heavy-duty bearings to ensure smooth operation under high loads.
- Increased Roller Width: Wider rollers provide better support for large or unevenly distributed loads.
- Frame Strength: Accompanied by stronger frames to support the weight and force exerted by the rollers.
- Application Specificity: Ideal for industrial environments, including manufacturing plants and distribution centers.
- Maintenance Requirements: May require more frequent maintenance checks due to the heavy-duty nature of the applications.
Belt Conveyor Rollers
Belt conveyor rollers differ from gravity rollers in their application and design. Understanding these differences is key:
- Powered Movement: Unlike gravity rollers, belt conveyor rollers are part of systems that use a belt to move materials.
- Friction Requirement: These rollers are designed to create friction that drives the conveyor belt.
- Material Composition: Often made from materials that enhance grip and reduce wear on the belt.
- Load Distribution: Designed to support the belt and evenly distribute the load across its width.
- Speed Considerations: Engineered to match the speed requirements of the belt system without slipping.
- Integration: Must be seamlessly integrated with the conveyor belt system for efficient operation.
- Energy Efficiency: While not relying on gravity, they still aim for energy efficiency in their design.
- Maintenance and Replacement: Easier to replace and maintain due to their critical role in the conveyor’s operation.
4 Inch Diameter Conveyor Rollers
4-inch diameter conveyor rollers are a common choice for a variety of applications:
- Versatility: Suitable for both light and medium-duty applications.
- Load Capacity: Offers a good balance between weight capacity and flexibility.
- Surface Area: Larger diameter provides increased surface area for product support.
- Material Handling: Ideal for handling a wide range of product sizes and shapes.
- Operational Speed: Capable of supporting higher operational speeds due to their size.
- Durability: Generally more durable than smaller rollers, offering a longer service life.
- Noise Reduction: Larger rollers can operate more quietly than smaller counterparts.
- Application Range: Used in industries from packaging to distribution centers.
1 Inch Diameter Conveyor Roller
1-inch diameter conveyor rollers are designed for specific applications where space and load requirements are limited:
- Compact Design: Ideal for systems where space is at a premium.
- Light-Duty Applications: Best suited for small, lightweight products.
- Material Options: Available in various materials to suit different operational environments.
- Low Profile: Their small size allows for low-profile conveyor designs.
- Flexibility: Easily integrated into existing systems with limited modification.
- Cost-Effective: Smaller rollers can be more cost-effective for certain applications.
- Ease of Replacement: Their size makes them easy to handle and replace.
- Specialized Use Cases: Often used in electronic, pharmaceutical, and food industries for delicate or small items.
PVC Conveyor Rollers
PVC conveyor rollers offer a lightweight and corrosion-resistant alternative to metal rollers, suitable for a variety of environments:
- Corrosion Resistance: PVC is naturally resistant to moisture and chemicals, making these rollers ideal for harsh environments.
- Lightweight Design: Easier to install and handle, reducing labor costs and improving workplace safety.
- Noise Reduction: PVC rollers operate more quietly than metal rollers, contributing to a more pleasant working environment.
- Low Maintenance: The material’s inherent properties reduce the need for frequent maintenance.
- Versatility: Suitable for a wide range of applications, including food processing, pharmaceuticals, and other clean environments.
- Cost-Effectiveness: Generally more affordable than stainless steel rollers, offering a cost-effective solution for many applications.
- Customization: Available in various diameters and lengths to suit different conveyor systems and applications.
- Non-Marking: PVC rollers do not mark products or conveyor belts, maintaining the integrity of transported items.
Each type of replacement gravity roller offers unique benefits and is suited to specific applications within material handling and logistics. Understanding these distinctions is crucial for selecting the right rollers to maintain and enhance conveyor system performance.
How to Choose the Right Replacement Gravity Rollers
Selecting the appropriate replacement gravity rollers is crucial for the efficiency, longevity, and safety of your conveyor system. This section will guide you through sourcing the best replacement gravity rollers, ensuring compatibility with your conveyor belt, and understanding the critical components of rollers.
Replacement Gravity Rollers Near Me
Sourcing replacement gravity rollers locally offers several advantages, including reduced shipping costs and faster delivery times. Here are tips on finding them:
- Local Suppliers: Start by searching for material handling equipment suppliers in your area. Local businesses often provide personalized service and quick delivery.
- Manufacturing Directories: Use online industrial and manufacturing directories to find nearby manufacturers of replacement gravity rollers.
- Trade Shows: Attend local trade shows and industry events where suppliers showcase their products. It’s an excellent opportunity to see the rollers firsthand and discuss your needs.
- Referrals: Ask for referrals from other businesses in your network that have recently purchased replacement gravity rollers.
- Online Marketplaces: Some suppliers may offer local pickup options through online marketplaces, combining the convenience of online shopping with local availability.
- Installation Services: Local suppliers often provide installation services, ensuring that the rollers are correctly integrated into your system.
- After-Sales Support: Proximity to the supplier means better after-sales support, including maintenance and repair services.
- Customization Options: Local manufacturers may offer customization options to meet specific requirements, providing a tailored solution for your conveyor system.
Conveyor Belt Rollers for Sale
When selecting conveyor belt rollers, compatibility with your existing system is paramount. Here’s how to ensure you make the right choice:
- Roller Diameter: Match the diameter of the rollers to the requirements of your conveyor belt to ensure smooth operation.
- Material: Choose a roller material compatible with your product and environment to prevent damage and wear.
- Load Capacity: Ensure the rollers can support the weight of your products along with the conveyor belt.
- Bearing Type: Select the appropriate bearing type for your operational speed and load requirements.
- Surface Texture: Consider the surface texture of the rollers for optimal grip and movement of the conveyor belt.
- Spacing: Correct roller spacing is crucial to support the belt and the products being transported effectively.
- Maintenance Requirements: Opt for rollers that offer ease of maintenance without needing to dismantle the entire conveyor system.
- Supplier Expertise: Choose a supplier with expertise in conveyor systems to get professional advice on the best rollers for your application.
Conveyor Roller Parts
Understanding the components of conveyor rollers is essential for maintenance and ensuring optimal performance. Here are the key components:
- Tube: The outer shell of the roller, which comes in contact with the conveyed material.
- Shaft: The inner rod that connects the roller to the conveyor frame, providing stability.
- Bearings: Facilitate smooth rotation of the roller around the shaft. Quality bearings reduce friction and wear.
- End Caps: Protect the bearings and internal components from dust, debris, and impact.
- Seals: Prevent contaminants from entering the bearing and lubricant from escaping.
- Axle: The fixed rod that runs through the roller, providing an axis of rotation.
- Spring Retaining Clips: Allow for easy installation and removal of rollers from the conveyor frame.
- Lubrication: Essential for maintaining smooth operation and extending the life of the roller.
- Material: The choice of material (steel, aluminum, PVC) affects the roller’s weight, durability, and suitability for different environments.
By carefully considering these aspects when choosing replacement gravity rollers, you can ensure that your conveyor system operates efficiently, safely, and reliably.
Heavy Duty Solutions with Replacement Gravity Rollers
In the realm of material handling and logistics, the demand for durable and robust solutions is ever-present. Heavy-duty replacement gravity rollers stand out as the backbone for systems requiring the transportation of heavy loads over long periods. This section delves into the specifics of heavy-duty conveyor rollers and the advantages of integrating these sturdy components into your operations.
Heavy Duty Conveyor Rollers
Heavy-duty conveyor rollers are engineered to withstand the rigors of intense operational demands, making them ideal for high-load applications. Here’s what sets them apart:
- Enhanced Material Strength: Constructed from high-grade steel or reinforced plastics, these rollers are built to support substantial weights without deformation.
- Larger Diameter: Their increased diameter distributes weight more evenly, reducing the stress on individual rollers and prolonging their lifespan.
- Thicker Walls: The tubes of these rollers have thicker walls, enhancing their ability to handle heavy loads without compromising integrity.
- Specialized Bearings: Equipped with heavy-duty bearings, these rollers can endure higher loads and speeds, ensuring smooth operation under pressure.
- Increased Load Capacity: Specifically designed to support significantly higher load capacities, making them suitable for industrial applications.
- Resistance to Wear and Tear: The materials and construction methods used provide exceptional resistance to wear, tear, and environmental factors.
- Customization Options: Many heavy-duty rollers offer customization options, including length, diameter, and bearing types, to fit specific system requirements.
- Ease of Maintenance: Despite their robust nature, these rollers are designed for easy maintenance, ensuring long-term reliability and performance.
Advantages of Heavy Duty Gravity Roller Conveyors
Investing in heavy-duty gravity roller conveyors brings numerous benefits to operations, particularly where durability and efficiency are paramount:
- Increased System Longevity: The robust construction of heavy-duty rollers significantly extends the life of conveyor systems.
- Higher Efficiency: Capable of moving heavy loads smoothly, these conveyors optimize operational flow and reduce bottlenecks.
- Reduced Downtime: The durability of heavy-duty rollers means less frequent replacements and repairs, minimizing downtime.
- Cost Savings: Over time, the investment in heavy-duty solutions translates to cost savings on maintenance and replacement parts.
- Versatility: These systems can handle a wide range of product types and sizes, providing flexibility in operations.
- Improved Safety: By reliably transporting heavy loads, they reduce the risk of workplace injuries associated with manual handling.
- Enhanced Performance: The smooth operation of heavy-duty rollers contributes to overall system performance, ensuring timely delivery of goods.
- Environmental Resistance: Many heavy-duty rollers are designed to withstand harsh environments, including extreme temperatures and corrosive substances.
Incorporating heavy-duty replacement gravity rollers into your conveyor system not only enhances its durability and performance but also ensures that your operations can handle the demands of heavy loads with ease. This investment in quality components pays dividends in operational efficiency, safety, and long-term cost savings, making it a wise choice for businesses looking to optimize their material handling processes.
Installation and Maintenance of Replacement Gravity Rollers
The proper installation and ongoing maintenance of replacement gravity rollers are key to ensuring the smooth operation and longevity of conveyor systems. These tasks, when performed correctly, not only prevent downtime but also contribute to the safety and efficiency of material handling operations. This section outlines the essential steps for installing new rollers and provides comprehensive maintenance tips to maximize the performance and lifespan of your conveyor system.
Step-by-Step Guide on Replacing Replacement Gravity Rollers
Replacing worn or damaged gravity rollers is a straightforward process that can significantly improve the functionality of your conveyor system. Here’s how to ensure a successful replacement:
- Preparation: Begin with a thorough safety check. Ensure the conveyor system is powered off and properly locked out to prevent accidental activation during the replacement process.
- Assessment: Carefully inspect the conveyor to identify rollers that need replacement. Look for signs of wear, damage, or misalignment.
- Removal: Using the appropriate tools, carefully remove the damaged or worn-out rollers. This may involve loosening or removing fasteners and retaining clips that secure the roller in place.
- Measurement: Accurately measure the removed roller to ensure the new replacement gravity roller matches in size and specification.
- Selection: Choose a suitable replacement roller that meets the operational demands of your system, considering factors such as material, load capacity, and environmental conditions.
- Installation: Insert the new roller into the conveyor frame, ensuring it is correctly aligned with the system. Securely fasten any clips or fasteners to hold the roller in place.
- Functionality Test: Manually rotate the newly installed roller to check for free movement and correct alignment within the system.
- Operational Test: After all replacements are made, reactivate the conveyor system and observe the new rollers during operation to ensure they function as intended.
Maintenance Tips to Extend the Lifespan and Ensure Optimal Performance
Regular maintenance is crucial for maximizing the efficiency and lifespan of replacement gravity rollers. Implementing a consistent maintenance routine can prevent many common issues:
- Routine Inspections: Periodically inspect rollers for signs of wear, alignment issues, or accumulation of debris, which could impact their performance.
- Cleanliness: Maintain cleanliness around rollers and the conveyor path to prevent build-up that could impair roller functionality or cause damage.
- Lubrication: Apply lubricant to bearings as recommended by the manufacturer to minimize friction and wear.
- Alignment Verification: Regularly check that rollers are properly aligned within the conveyor frame to ensure even wear and efficient operation.
- Even Load Distribution: Monitor load distribution to prevent overburdening specific sections of the conveyor, which can lead to premature roller wear.
- Environmental Considerations: Be mindful of the operating environment, as factors like temperature, humidity, and chemical exposure can affect roller materials and performance.
- Replacement Scheduling: Keep detailed records of maintenance and replacements to plan for future needs and prevent unexpected failures.
- Staff Training: Ensure that personnel responsible for maintenance are adequately trained to recognize and address potential issues with conveyor rollers.
- Adherence to Guidelines: Always follow the manufacturer’s maintenance and replacement recommendations to achieve the best results.
By prioritizing the correct installation and diligent maintenance of replacement gravity rollers, businesses can enhance the reliability and efficiency of their conveyor systems, ensuring smooth operations and extended equipment life.
Case Studies on Replacement Gravity Rollers
The integration of high-quality replacement gravity rollers into conveyor systems has proven to be a game-changer for numerous businesses across various industries. These real-world examples highlight the transformative impact of upgrading to superior replacement gravity rollers, showcasing improvements in efficiency, safety, and overall operational performance.
- E-Commerce Fulfillment Center: A leading e-commerce company faced frequent downtime due to worn-out rollers in their sorting and packaging lines. After upgrading to durable replacement gravity rollers, they reported a 30% increase in conveyor system uptime, significantly boosting their order fulfillment capacity.
- Automotive Manufacturing Plant: An automotive parts manufacturer struggling with inconsistent product flow and damage during assembly line processes switched to heavy-duty replacement gravity rollers. The new rollers provided smoother transitions and reduced product damage by 25%, enhancing product quality and customer satisfaction.
- Food Processing Facility: A food processing plant dealing with hygiene and cleaning challenges opted for stainless steel replacement gravity rollers. The upgrade facilitated easier cleaning and maintenance, meeting stringent hygiene standards and reducing cross-contamination risks.
- Distribution Warehouse: A distribution center experiencing bottlenecks in their material handling operations installed custom-sized replacement gravity rollers. This customization improved material flow efficiency by 40%, eliminating bottlenecks and improving delivery times.
- Pharmaceutical Packaging Line: A pharmaceutical company needed to minimize operational noise to create a better working environment. By replacing their old rollers with specially designed low-noise replacement gravity rollers, they achieved a significant reduction in noise levels, improving worker satisfaction and focus.
- Retail Goods Sorting Facility: Faced with the challenge of handling a wide variety of product sizes and weights, a retail goods sorting facility upgraded to adjustable replacement gravity rollers. This versatility allowed for quick adjustments between different product batches, increasing throughput by 35%.
- Logistics and Shipping Hub: A logistics hub struggling with roller failures and maintenance issues switched to high-quality replacement gravity rollers with enhanced bearing designs. The new rollers doubled the lifespan of their conveyor components, drastically reducing maintenance costs and improving reliability.
- Recycling Plant: A recycling facility dealing with heavy and abrasive materials upgraded to reinforced replacement gravity rollers. The new rollers were specifically designed to withstand harsh conditions, resulting in a 50% reduction in roller wear and tear and extending the conveyor system’s operational life.
These case studies demonstrate the significant benefits of investing in high-quality replacement gravity rollers. By addressing specific operational challenges with tailored roller solutions, businesses can achieve remarkable improvements in efficiency, safety, and productivity, ultimately enhancing their competitive edge in the market.
Last Updated on June 4, 2024 by Jordan Smith
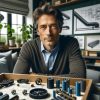
Jordan Smith, a seasoned professional with over 20 years of experience in the conveyor system industry. Jordan’s expertise lies in providing comprehensive solutions for conveyor rollers, belts, and accessories, catering to a wide range of industrial needs. From initial design and configuration to installation and meticulous troubleshooting, Jordan is adept at handling all aspects of conveyor system management. Whether you’re looking to upgrade your production line with efficient conveyor belts, require custom conveyor rollers for specific operations, or need expert advice on selecting the right conveyor accessories for your facility, Jordan is your reliable consultant. For any inquiries or assistance with conveyor system optimization, Jordan is available to share his wealth of knowledge and experience. Feel free to reach out at any time for professional guidance on all matters related to conveyor rollers, belts, and accessories.