Choosing the Right Return Idler Roller for Your Conveyor
In the intricate world of conveyor systems, idler rollers stand as the unsung heroes, playing a pivotal role in the seamless transportation of materials. Among these, the return idler roller is particularly crucial, tasked with supporting the underside of the conveyor belt on its journey back to the starting point. This not only aids in maintaining the belt’s structural integrity but also significantly contributes to the overall efficiency and longevity of the conveyor system. The return idler roller ensures that the conveyor belt is properly aligned and tensioned, preventing slippage and reducing wear and tear. By doing so, it not only safeguards the conveyor belt from premature degradation but also upholds the system’s operational efficiency, making it an indispensable component in the realm of material handling and transportation.
What is a Return Idler Roller
The return idler roller is a fundamental component of belt conveyor systems, designed to support the return path of the conveyor belt. These rollers are strategically positioned on the underside of the conveyor system, where they play a critical role in maintaining the belt’s alignment and tension. This, in turn, ensures smooth operation, reduces wear and tear on the belt, and extends the overall lifespan of the conveyor system. To delve deeper into the essence of return idler rollers, let’s explore their definition, primary function, and how they differ from carrying idler rollers.
Primary Function of Return Idler Rollers
- Support: They provide crucial support to the underside of the return belt, preventing sagging and misalignment.
- Alignment: By ensuring the belt remains aligned, return idler rollers contribute to the efficient operation of the conveyor system.
- Tension Maintenance: Proper tension is vital for the conveyor belt’s operation, and return idler rollers help maintain this tension, reducing slippage.
- Protection: They protect the belt from wear and tear, contributing to the belt’s longevity.
- Efficiency: By supporting smooth belt operation, return idler rollers help maintain the overall efficiency of the conveyor system.
Distinction Between Return Idler Rollers and Carrying Idler Rollers
To understand the specific roles within a conveyor system, it’s crucial to distinguish between return idler rollers and carrying idler rollers. Below are tables that highlight their differences:
Return Idler Rollers
Carrying Idler Rollers
Understanding the distinct roles and functionalities of return idler rollers and carrying idler rollers is essential for the optimal design, operation, and maintenance of conveyor systems. Each type of idler roller is tailored to meet specific operational needs, ensuring the conveyor system runs smoothly and efficiently.
Types of Return Idler Roller
The diversity in the design of return idler rollers is a testament to the varied applications and environments in which conveyor systems operate. Understanding the different types of return idler rollers, including flat, rubber disc, and self-aligning return idlers, is crucial for selecting the right components for your conveyor system. Additionally, the role of impact idler rollers in protecting the conveyor belt from damage cannot be overstated. Below, we delve into the specifics of each type, highlighting their unique features and applications.
Overview of Different Types of Return Idler Rollers
Flat Return Idler Rollers
Self-Aligning Return Idler Rollers
Impact Idler Rollers and Their Role
Impact Idler Rollers
Impact idler rollers are designed to absorb the shock and impact of falling materials at loading and transfer points, protecting the belt and structure from damage. Here are five specific examples of their application and benefits:
- Loading Zones: Absorbs the impact energy of heavy materials, preventing belt damage.
- Transfer Points: Minimizes the force transferred to the conveyor structure, enhancing durability.
- Heavy-Duty Operations: Ideal for mining and quarrying where large, heavy materials are handled.
- High-Speed Conveyors: Reduces the impact force on the belt, maintaining belt integrity.
- Variable Material Sizes: Adapts to the irregular impact of materials of varying sizes, ensuring consistent belt protection.
Each type of return idler roller serves a specific purpose in the operation and maintenance of a conveyor system. By selecting the appropriate return idler roller for your application, you can enhance the efficiency, longevity, and reliability of your conveyor system.
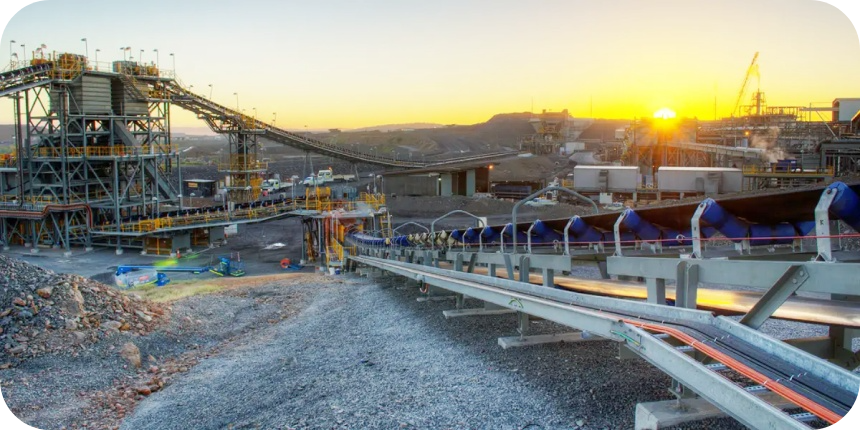
Key Features and Specifications of Return Idler Rollers
The design and construction of return idler rollers are pivotal for the efficient operation of conveyor systems. These rollers are crafted from various materials, each offering distinct advantages under different operational conditions. Moreover, selecting the right return idler roller requires understanding specific specifications such as diameter, length, and load capacity. This section delves into the common materials used in the construction of return idler rollers and the crucial specifications to consider.
Common Materials Used in Return Idler Roller Construction
Steel Return Idler Rollers
High-Density Polyethylene (HDPE) Return Idler Rollers
Specifications to Consider When Selecting a Return Idler Roller
Diameter
Length
Load Capacity
Selecting the appropriate return idler roller based on these key features and specifications is crucial for ensuring the conveyor system operates efficiently, safely, and with minimal downtime. Understanding the advantages of different materials and accurately assessing the required specifications will lead to a well-informed decision, enhancing the overall performance of the conveyor system.
Importance of Quality and Durability in Return Idler Roller
The selection of high-quality return idler rollers is not merely a matter of operational preference but a critical investment in the efficiency and longevity of conveyor systems. Quality and durability in these components directly influence maintenance requirements, operational costs, and system performance. Here, we explore the significance of opting for high-quality return idler rollers and the impact of durability on the conveyor system’s overall efficiency.
Significance of Choosing High-Quality Return Idler Rollers
Reduced Maintenance Costs:
- Longevity: High-quality return idler rollers are designed to last longer, reducing the frequency of replacements and associated downtime.
- Wear Resistance: They are manufactured from materials that are resistant to wear and abrasion, ensuring that they maintain their integrity even under harsh conditions.
- Lower Failure Rates: Superior construction and materials reduce the likelihood of roller failure, which can lead to costly repairs and operational interruptions.
- Enhanced Performance: Quality rollers provide consistent and reliable support to the conveyor belt, minimizing instances of belt misalignment and slippage.
- Savings Over Time: While the initial investment in high-quality rollers may be higher, the long-term savings in maintenance and replacement costs justify the expense.
Enhancing Conveyor Performance:
- Smooth Operation: High-quality return idler rollers contribute to the smooth and efficient operation of the conveyor belt, reducing energy consumption and operational costs.
- Material Handling Efficiency: By ensuring the conveyor belt is properly supported and aligned, these rollers help in maintaining the optimal speed and flow of materials.
- Safety: Quality rollers are less likely to fail, reducing the risk of accidents and material spillage, which can pose safety hazards.
- Noise Reduction: Well-manufactured rollers operate more quietly, contributing to a better working environment and reducing noise pollution.
- Compliance: High-quality rollers often meet or exceed industry standards and regulations, ensuring compliance and avoiding potential fines or operational restrictions.
Impact of Durability on Conveyor System Efficiency
Durability in return idler rollers directly impacts the conveyor system’s efficiency in several ways:
- Continuous Operation: Durable rollers ensure that the conveyor system can operate continuously without unexpected breakdowns, maintaining productivity levels.
- Load Handling: They are capable of handling varying loads without degradation, ensuring that the system can adapt to different operational demands.
- Environmental Resistance: Durable rollers are designed to withstand environmental challenges, such as moisture, temperature variations, and corrosive materials, ensuring consistent performance.
- Reduced Wear on Other Components: By maintaining proper belt alignment and tension, durable rollers reduce wear on other conveyor components, such as belts and motors, extending their service life.
- Investment Protection: Ultimately, investing in durable return idler rollers protects the overall investment in the conveyor system, ensuring that it delivers value over its intended lifespan.
The importance of quality and durability in return idler rollers cannot be overstated. These characteristics are foundational to reducing maintenance costs, enhancing conveyor performance, and ensuring the system’s overall efficiency and reliability.
Discover our wide range of conveyor rollers today!
Return Idler Roller Replacement and Maintenance
Ensuring the longevity and efficiency of a conveyor system involves regular maintenance and timely replacement of its components, especially the return idler rollers. These rollers play a crucial role in maintaining the conveyor belt’s alignment and tension, directly impacting the system’s overall performance. This section provides guidelines on when and how to replace return idler rollers and offers tips for routine maintenance to extend their lifespan.
Guidelines on When and How to Replace Return Idler Rollers
When to Replace:
- Visible Wear and Tear: Replace the return idler roller if there are visible signs of wear, such as cracks, deformation, or significant surface abrasion.
- Unusual Noise: Squeaking, grinding, or other unusual noises during operation can indicate bearing failure or misalignment, necessitating replacement.
- Rotation Issues: A roller that does not rotate freely or shows signs of seizing should be replaced to prevent belt damage.
- Misalignment: Persistent belt misalignment despite adjustments may indicate that the return idler roller is no longer functioning correctly.
- Routine Inspection Findings: Regular inspections may reveal issues not immediately apparent during operation, such as internal wear or bearing failure, prompting replacement.
How to Replace:
- Safety First: Ensure the conveyor system is powered off and locked out to prevent accidental activation during maintenance.
- Remove the Old Roller: Loosen and remove the mounting hardware securing the roller to the conveyor frame.
- Install the New Roller: Position the new return idler roller in place, ensuring it is aligned correctly with the conveyor belt’s path.
- Secure the Roller: Tighten the mounting hardware to secure the roller, checking for proper alignment and rotation.
- Test the System: Once installed, power on the conveyor system and observe the new roller in operation, making any necessary adjustments.
Tips for Routine Maintenance to Extend the Lifespan of Return Idler Rollers
Routine Maintenance Tips:
- Regular Inspections: Conduct periodic inspections of return idler rollers for signs of wear, damage, or misalignment, addressing issues promptly.
- Lubrication: Ensure that the roller bearings are adequately lubricated according to the manufacturer’s recommendations to reduce friction and wear.
- Cleaning: Keep the rollers and surrounding areas clean from debris and material build-up that could impede roller movement or cause premature wear.
- Alignment Checks: Regularly check and adjust the alignment of return idler rollers to ensure the conveyor belt runs smoothly and evenly.
- Record Keeping: Maintain detailed records of maintenance activities, replacements, and observations to track the performance and condition of return idler rollers over time.
Adhering to these replacement and maintenance guidelines will help ensure that return idler rollers continue to function effectively, contributing to the overall reliability and efficiency of the conveyor system. Regular attention to these components can prevent unexpected downtime and extend the service life of the conveyor system.
Selecting the Right Return Idler Roller
Choosing the appropriate return idler roller is pivotal for the optimal performance and longevity of conveyor systems. The selection process involves considering various factors that influence the efficiency and durability of these components. Additionally, understanding the role of specialized idlers, such as self-aligning return idlers, can further enhance conveyor operation by minimizing belt misalignment. This section explores the critical considerations for selecting the right return idler roller and the benefits of self-aligning models.
Factors to Consider When Choosing Return Idler Rollers
Material Being Conveyed:
- Abrasive Materials: For materials like sand or gravel, choose return idler rollers with wear-resistant surfaces to prevent premature wear.
- Sticky Materials: If the conveyor transports sticky substances, rubber disc return idlers can help clean the belt and prevent material build-up.
- Heavy Loads: For conveying heavy materials, select rollers with a higher load capacity and robust construction to withstand the weight without deformation.
- Corrosive Materials: In environments where corrosive materials are handled, opt for rollers made from materials like HDPE or coated with corrosion-resistant finishes.
- Food Products: When conveying food products, consider rollers made from FDA-approved materials that are easy to clean and resist bacterial growth.
Environment of Operation:
- High Humidity: For operations in high humidity or wet conditions, choose return idler rollers with sealed bearings to prevent water ingress and rust.
- Extreme Temperatures: In environments with extreme temperatures, select rollers with materials and lubricants rated for such conditions to ensure proper function.
- Dusty Environments: In dusty settings, dust-proof seals can protect the roller bearings from contamination and extend their service life.
- Chemical Exposure: If the conveyor system is exposed to chemicals, select rollers with chemical-resistant materials to prevent degradation.
- Outdoor Use: For outdoor applications, UV-resistant materials can help prevent the deterioration of roller components exposed to sunlight.
The Role of Self-Aligning Return Idlers in Minimizing Belt Misalignment
Self-aligning return idlers are specially designed to address the common issue of belt misalignment in conveyor systems. These idlers automatically adjust their position to realign the conveyor belt to the center of the conveyor structure. This capability is crucial for maintaining optimal operation and preventing wear and damage to the belt edges. The self-aligning feature is particularly beneficial in long conveyor systems where belt misalignment can lead to significant operational issues and maintenance challenges. By incorporating self-aligning return idlers, conveyor operators can:
- Reduce Downtime: Minimize interruptions caused by belt misalignment issues.
- Extend Belt Life: Prevent edge wear and damage by keeping the belt properly aligned.
- Lower Maintenance Costs: Reduce the need for manual adjustments and repairs related to misalignment.
- Improve Safety: Decrease the risk of accidents associated with belt misalignment.
- Enhance Efficiency: Ensure smooth and consistent material flow by maintaining proper belt alignment.
Selecting the right return idler roller, considering the specific requirements of the material being conveyed and the operating environment, alongside implementing self-aligning return idlers, can significantly improve the performance and reliability of conveyor systems.
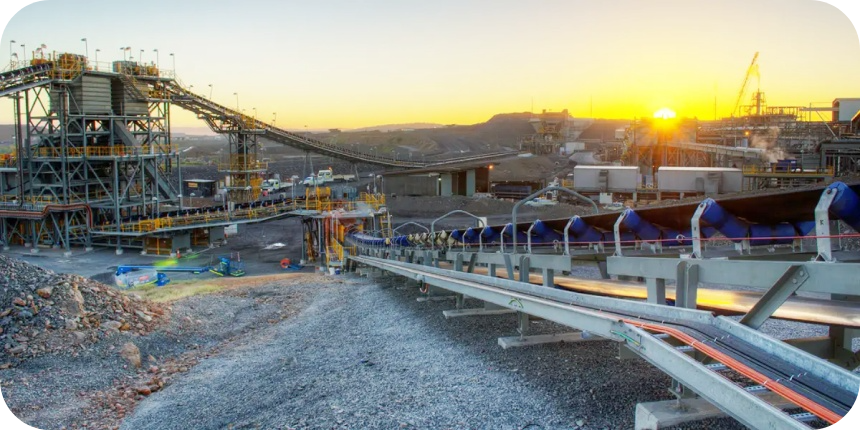
Pricing and Availability of Return Idler Rollers
The cost and availability of return idler rollers are crucial considerations for maintenance managers and procurement officers in industries relying on conveyor systems. Understanding the pricing dynamics and where to source these components can significantly impact operational budgets and maintenance schedules. This section provides an overview of the factors influencing return idler roller pricing and offers guidance on where to find these essential components for sale and replacement.
Overview of Return Idler Roller Pricing and Factors That Affect Cost
Factors Influencing Pricing:
- Material Quality: High-quality materials such as premium steel or specialized plastics can increase the price due to their durability and performance characteristics.
- Design Complexity: Advanced features, such as self-aligning capabilities or integrated sensors for monitoring, can add to the cost.
- Brand Reputation: Rollers from well-established manufacturers with a proven track record of reliability and performance may command higher prices.
- Load Capacity: Rollers designed to support heavier loads typically require more robust materials and construction, influencing the price.
- Customization: Custom specifications for length, diameter, or material to meet specific conveyor system requirements can increase the cost compared to standard models.
Finding Return Idler Rollers for Sale and Parts for Replacement:
- Manufacturer Direct: Purchasing directly from the manufacturer often provides access to the latest models, technical support, and potential discounts on bulk orders.
- Industrial Supply Companies: These companies offer a wide range of conveyor components, including return idler rollers from various manufacturers, providing options to compare prices and features.
- Online Marketplaces: Platforms like Alibaba, Amazon Business, and others can be sources for return idler rollers, offering competitive pricing and reviews for informed decision-making.
- Local Distributors: Partnering with local distributors can offer the advantage of quick delivery times and the opportunity for hands-on inspection before purchase.
- Specialty Conveyor System Suppliers: Suppliers specializing in conveyor systems often have comprehensive parts inventories, including return idler rollers, and can offer expert advice on the best options for specific applications.
When considering the purchase of return idler rollers, it’s essential to balance cost with the quality and specific needs of your conveyor system. Opting for the lowest price might not always yield the best value over the long term, especially if it compromises the system’s efficiency or increases downtime due to maintenance issues. Researching and comparing options from various sources can help ensure that you find the best return idler rollers for your system’s requirements and budget.
Innovations and Trends in Return Idler Roller Design
The landscape of return idler roller design is continually evolving, with innovations aimed at enhancing conveyor system efficiency, reducing environmental impact, and improving monitoring and maintenance processes. These advancements are pivotal in meeting the demands of modern industries for more sustainable, efficient, and intelligent material handling solutions. This section explores recent trends and innovations in return idler technology, focusing on energy-saving designs, smart monitoring systems, and the use of sustainable materials.
Recent Advancements in Return Idler Technology
Energy-Saving Designs:
- Low-Friction Bearings: Incorporation of advanced, low-friction bearings reduces the energy required to operate the conveyor, leading to significant power savings.
- Lightweight Materials: The use of lightweight composite materials for roller construction decreases the overall system weight, reducing energy consumption.
- High-Efficiency Roller Shapes: Aerodynamic roller designs minimize air resistance during operation, further cutting down on energy use.
- Energy-Generating Rollers: Some return idler rollers are designed to capture and convert the kinetic energy from the moving conveyor belt into electrical energy, which can be fed back into the grid or used to power auxiliary systems.
- Solar-Powered Sensors: Integration of solar-powered sensors for monitoring roller performance and health, eliminating the need for external power sources.
Smart Monitoring Systems:
- Real-Time Condition Monitoring: Sensors embedded in return idler rollers provide real-time data on performance, wear, and operational conditions, facilitating proactive maintenance.
- Temperature and Vibration Analysis: Advanced sensors can detect overheating and abnormal vibrations, indicating potential failures before they occur.
- Wireless Communication: Wireless technology allows for the remote monitoring of return idler rollers, enabling maintenance teams to access data from anywhere.
- Predictive Maintenance Algorithms: Utilizing data collected from sensors, predictive algorithms can forecast roller lifespan and maintenance needs, optimizing maintenance schedules.
- RFID Tagging: Incorporating RFID tags in return idler rollers for easy identification, tracking, and inventory management.
Sustainable and Eco-Friendly Materials in Production
Sustainable Materials:
- Recycled Steel: Many return idler rollers are now made from recycled steel, reducing the demand for virgin materials and lowering the carbon footprint.
- Biodegradable Lubricants: The use of biodegradable lubricants for bearings and moving parts minimizes environmental contamination.
- Composite Materials: Composites made from recycled plastics and other sustainable materials offer durability while being environmentally friendly.
- Renewable Energy Manufacturing: Production facilities powered by renewable energy sources, such as solar or wind, contribute to the sustainability of return idler rollers.
- Eco-Friendly Packaging: Reducing plastic use and opting for recyclable or biodegradable packaging materials for shipping and handling.
These innovations and trends in return idler roller design reflect the industry’s commitment to improving efficiency, embracing smart technology, and reducing environmental impact. As these advancements continue to evolve, conveyor systems worldwide stand to benefit from increased operational efficiency, reduced maintenance costs, and a smaller environmental footprint.
FAQs About Return Idler Roller
A return idler is a specific type of roller used in conveyor systems, positioned on the underside of the conveyor belt to support the return path of the belt. This component plays a crucial role in ensuring the smooth operation and longevity of the conveyor system. Return idlers are designed to help maintain the structural integrity of the conveyor belt, preventing sagging and ensuring it remains centered and aligned. They come in various designs to accommodate different types of conveyor systems and operational requirements, including flat, rubber disc, and self-aligning idlers. The choice of return idler depends on factors such as the material being conveyed, the environment in which the conveyor operates, and the specific needs of the material handling process.
Idler rollers are cylindrical rods that form an essential part of a conveyor system. Their primary function is to support the conveyor belt and the material being transported along the length of the system. Idler rollers are strategically placed to distribute the weight of the load evenly, reducing friction and wear on the belt, which in turn minimizes operational costs and maintenance needs. They also play a significant role in controlling the movement of the conveyor belt, ensuring it runs smoothly and stays aligned. Different types of idler rollers, including carrying idlers, return idlers, impact idlers, and guide rollers, are used throughout the conveyor system to fulfill various roles, from supporting weight to absorbing impact at loading points.
A return roller is another term for a return idler, specifically referring to the rollers that support the return side of the conveyor belt. After the conveyor belt has transported materials to their destination, it must return to the starting point to continue the cycle; the return rollers ensure that this return path is supported and maintained. These rollers help to keep the belt clean by preventing sagging, which can lead to material buildup on the underside of the belt. Return rollers are available in different materials and designs, including plain steel, rubber-coated, and those equipped with cleaning devices, to suit various operational environments and requirements.
While the terms “roller” and “idler” are often used interchangeably in the context of conveyor systems, they refer to components that, though similar, have distinct roles. A roller is a broad term that describes any cylindrical bar that rolls and is used to facilitate movement. In conveyor systems, rollers are part of the mechanism that moves the conveyor belt or the materials being transported. An idler, on the other hand, specifically refers to rollers that are used to support the conveyor belt itself. Idlers do not directly move materials but are crucial for the smooth and efficient operation of the conveyor system. They are categorized based on their location and function within the system, such as carrying idlers, return idlers, and impact idlers.
Last Updated on July 4, 2024 by Jordan Smith
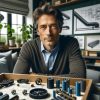
Jordan Smith, a seasoned professional with over 20 years of experience in the conveyor system industry. Jordan’s expertise lies in providing comprehensive solutions for conveyor rollers, belts, and accessories, catering to a wide range of industrial needs. From initial design and configuration to installation and meticulous troubleshooting, Jordan is adept at handling all aspects of conveyor system management. Whether you’re looking to upgrade your production line with efficient conveyor belts, require custom conveyor rollers for specific operations, or need expert advice on selecting the right conveyor accessories for your facility, Jordan is your reliable consultant. For any inquiries or assistance with conveyor system optimization, Jordan is available to share his wealth of knowledge and experience. Feel free to reach out at any time for professional guidance on all matters related to conveyor rollers, belts, and accessories.