Solutions of Rock Conveyor Belt Systems
A rock conveyor belt is a mechanical system designed to transport rocks and other bulk materials efficiently. It consists of a continuous loop of flexible material, usually reinforced rubber or steel, supported by rollers or pulleys. As the belt moves, it carries materials from one location to another, typically from mining or quarrying sites to processing or storage areas. Conveyor belts are essential for handling large volumes of material quickly and safely, reducing the need for manual labor and minimizing the risk of accidents. They are commonly used in industries such as mining, construction, and aggregates, where the reliable movement of heavy loads is crucial for operational efficiency.
Consumer Needs Analysis of Rock Conveyor Belt
Here’s a structured approach for your Consumer Needs Analysis of rock conveyor belts:
Background of Demand
Growth in Mining, Construction, and Other Related Industries:
- Mining Expansion: Increased extraction activities demand efficient transportation systems for large volumes of mined materials.
- Construction Boom: Rising infrastructure projects require bulk materials like gravel and crushed rock, which drives the need for reliable conveyor systems.
- Other Related Industries: Industries such as aggregate production and recycling also contribute to the growing demand for rock conveyor belts.
Efficiency Needs for Handling Large Quantities of Rock and Ore:
- High Capacity: Conveyors must handle substantial volumes without compromising performance.
- Speed and Throughput: The efficiency of operations is often dependent on the speed at which materials are moved.
- Reliability: Continuous operation without frequent breakdowns is crucial to maintaining productivity.
Challenges Faced by Consumers
Technical Challenges in Efficient Rock Transport:
- Durability of Belts: Conveyor belts must withstand abrasive materials and harsh operating conditions.
- Design and Configuration: Proper design to fit different operational environments and material types is essential for efficiency.
- Load Distribution: Ensuring even distribution of material to prevent overloading and excessive wear.
Maintenance and Operational Costs:
- Maintenance Requirements: Regular maintenance is necessary to avoid unexpected breakdowns and extend the lifespan of the conveyor system.
- Cost of Repairs: Replacement parts and repair services can be expensive, impacting overall operational costs.
- Operational Efficiency: Downtime for repairs or adjustments can disrupt workflow and lead to financial losses.
This analysis should give a comprehensive view of the current demand and challenges in the rock conveyor belt market. Let me know if you need further details or specific data points!

Main Types of Rock Conveyor Belts
Here’s a detailed description of the main types of rock conveyor belts, including their features, pros, and cons:
Belt Conveyors
Features:
- Suitable for Long-Distance Transport: Belt conveyors can efficiently transport materials over long distances, from a few meters to several kilometers.
- High Stability: They provide a stable and smooth transportation of materials, reducing the risk of spillage and damage.
- Versatility: Can handle a wide range of materials, from fine powders to large rocks, with various belt designs and materials.
Pros:
- Cost-Effective for Long Distances: Economical for transporting materials over long distances compared to other conveyor types.
- Low Operating Costs: Typically have lower energy consumption and maintenance costs.
- Continuous Operation: Can operate continuously, which improves efficiency and productivity.
- Customization: Belts can be customized with different widths, materials, and designs to suit specific needs.
Cons:
- Limited Incline Capability: Less effective for steep inclines or vertical transport; generally requires additional equipment for significant elevation changes.
- Spillage Risk: Material spillage can occur if the belt is not properly enclosed or if it is overloaded.
- Initial Investment: Can be expensive to install, especially for very long or complex systems.
Chain Conveyors
Features:
- Suitable for Rough Materials: Designed to handle heavy, abrasive, and bulk materials, including rocks and ore.
- Strong Load-Bearing Capacity: Capable of supporting substantial loads, making them ideal for heavy-duty applications.
- Durability: Constructed to withstand harsh operating conditions and heavy impact.
Pros:
- High Load Capacity: Ideal for transporting large and heavy materials without risk of belt damage.
- Durability and Reliability: Strong and robust, with a long service life under demanding conditions.
- Versatility in Handling Materials: Can handle irregularly shaped and large materials that might damage other types of conveyors.
Cons:
- Higher Maintenance: Requires regular maintenance to ensure the chain remains in good condition and to address wear and tear.
- Higher Initial Cost: Typically more expensive than belt conveyors due to their robust construction and heavy-duty components.
- Noise Levels: Can be noisier during operation, which might be a concern in some environments.
Screw Conveyors
Features:
- Suitable for Vertical or Inclined Transport: Designed to move materials vertically or at steep angles, making them ideal for elevating materials.
- Compact Design: Generally more compact than other conveyor types, suitable for installations with limited space.
- Effective for Fine Materials: Good for transporting powders, granules, and small bulk materials.
Pros:
- Efficient Vertical Transport: Excellent for moving materials upwards or at steep inclines where other conveyors might not be suitable.
- Compact and Space-Saving: Ideal for tight spaces or when a compact solution is needed.
- Versatility: Can handle a variety of materials, including those with varying flow characteristics.
Cons:
- Limited Capacity: Not ideal for transporting very large or heavy materials; capacity is generally lower compared to belt or chain conveyors.
- Potential for Material Degradation: May cause degradation or compaction of certain materials during transport.
- Maintenance Requirements: Requires regular maintenance to prevent issues with the screw and bearings, especially when handling abrasive materials.
Each type of conveyor belt has its own strengths and weaknesses, making them suitable for different applications. Choosing the right conveyor belt depends on factors such as the type of material being transported, the distance, the required incline, and budget constraints.

Choosing the Right Rock Conveyor Belt
Material Selection
When selecting a rock conveyor belt, the choice of material is crucial as it impacts the belt’s performance, longevity, and suitability for specific applications. Here’s a comparison of the most common types of belts:
- Rubber Belts:
- Description: Rubber conveyor belts are made from natural or synthetic rubber and are commonly used in various industries.
- Advantages:
- Flexibility: Rubber belts are flexible and can handle irregularly shaped materials.
- Resistance: They offer good resistance to abrasion, impact, and wear, making them suitable for heavy and abrasive materials.
- Cost-Effective: Generally more affordable than steel belts.
- Disadvantages:
- Temperature Sensitivity: Rubber belts may degrade under extreme temperatures or harsh environmental conditions.
- Lower Load Capacity: Less suitable for extremely heavy loads compared to steel belts.
- Steel Belts:
- Description: Steel conveyor belts are made of steel cords or mesh, offering high strength and durability.
- Advantages:
- High Strength: Capable of supporting heavy loads and withstanding extreme conditions.
- Durability: Extremely durable and resistant to wear, making them ideal for heavy-duty applications.
- Temperature Tolerance: Better suited for high-temperature environments.
- Disadvantages:
- Higher Cost: Generally more expensive than rubber or fabric belts.
- Flexibility: Less flexible, which can be a limitation for certain applications.
- Maintenance: Requires more maintenance and can be harder to repair.
- Fabric Belts:
- Description: Fabric conveyor belts are made from layers of fabric (e.g., polyester, nylon) and are used in various industrial applications.
- Advantages:
- Cost-Effective: Generally cheaper than rubber or steel belts.
- Flexibility: Highly flexible and suitable for applications where flexibility is important.
- Lightweight: Easier to handle and install.
- Disadvantages:
- Lower Durability: Not as durable as steel belts and less resistant to wear and tear.
- Limited Load Capacity: Suitable for lighter loads and not ideal for heavy or abrasive materials.
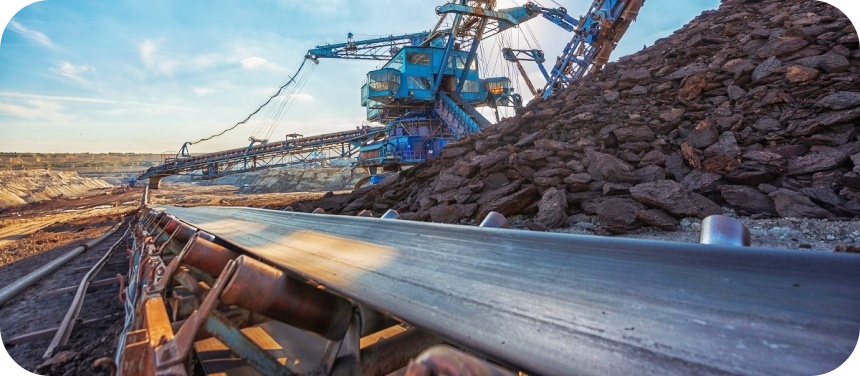
Transport Capacity
The transport capacity of a conveyor belt is influenced by factors such as belt width and conveyor speed:
- Belt Width:
- Impact on Capacity: Wider belts can transport more material at once, increasing the overall capacity of the conveyor system. However, wider belts may also require more space and might be more expensive.
- Selection Considerations: Choose a belt width that matches the volume and size of the material being transported, ensuring that the conveyor can handle the required load without overloading.
- Conveyor Speed:
- Impact on Capacity: Faster conveyor speeds increase the rate at which material is moved but may impact the quality and safety of material handling. It’s essential to balance speed with the desired throughput and ensure that the speed does not lead to excessive wear or spillage.
- Selection Considerations: Determine the optimal speed for your application based on the material’s characteristics and the required delivery rate.
Durability and Maintenance
Evaluating durability and maintenance requirements is crucial to ensure the long-term efficiency and cost-effectiveness of the conveyor belt:
- Considerations for Lifetime:
- Material Impact: The choice of material (rubber, steel, fabric) affects the belt’s lifespan. Steel belts generally last longer but at a higher cost. Rubber belts are more susceptible to wear but are more affordable.
- Operating Conditions: Extreme conditions such as high temperatures, corrosive environments, or heavy impact can shorten the belt’s lifespan. Choose a belt designed to withstand these conditions.
- Maintenance Frequency:
- Routine Maintenance: Regular inspections and maintenance are essential to prolong the belt’s life and prevent unexpected failures. This includes checking for wear and tear, cleaning, and adjusting tension.
- Repair and Replacement: Plan for periodic replacements and repairs to avoid downtime and ensure smooth operation. Steel belts may require more specialized maintenance compared to rubber or fabric belts.
Environmental Factors
Considering environmental factors can help in selecting a conveyor belt that meets sustainability and efficiency goals:
- Energy Efficiency:
- Importance: An energy-efficient conveyor system can significantly reduce operational costs and environmental impact. Energy-efficient belts and drive systems consume less power and reduce energy expenditure.
- Selection Tips: Look for belts designed to minimize friction and energy loss. Advanced technologies such as variable speed drives can further enhance energy efficiency.
- Emission Reduction:
- Impact: Conveyor systems can contribute to emissions if not properly managed. Selecting belts and components that reduce dust and emissions can help in adhering to environmental regulations.
- Selection Tips: Consider using enclosed or covered belts to prevent dust emissions and enhance air quality. Choose materials and designs that comply with environmental standards and regulations.
By carefully considering these factors, you can select a rock conveyor belt that best suits your operational needs, ensuring optimal performance, durability, and cost-efficiency.

Rock Conveyor Belt Practical Application Cases
Mining Industry
Effectiveness and Improvements in Practical Applications:
- Material Handling Efficiency:
- Long-Distance Transport: In mining operations, conveyor belts are crucial for moving ore and waste materials from the mining site to processing plants or stockpiles. Belt conveyors can handle large volumes over long distances, reducing the need for trucks and improving overall efficiency.
- Reduced Labor Costs: Automating material transport with conveyor systems reduces labor requirements and associated costs. This leads to more consistent and predictable material handling.
- Improvements in Technology:
- Enhanced Durability: Modern conveyor belts are designed to withstand the harsh conditions of mining environments, including heavy impacts, abrasive materials, and extreme temperatures. Advances in materials and design have improved the durability and lifespan of these systems.
- Automation and Monitoring: Advanced conveyor systems now include sensors and automation technology that monitor belt performance, detect potential issues, and optimize operation. This enhances safety and reduces maintenance costs by allowing for predictive maintenance.
- Safety and Environmental Benefits:
- Reduced Dust Emissions: Enclosed and covered conveyor systems help minimize dust emissions, improving air quality and reducing environmental impact.
- Improved Safety: Conveyor systems reduce the need for manual handling and transportation of heavy loads, decreasing the risk of injuries associated with manual labor.
Construction Industry
Role and Advantages of Rock Conveyor Belts:
- Efficient Material Transport:
- Short to Medium Distances: In construction projects, conveyor belts are used to transport materials such as sand, gravel, and concrete across short to medium distances, often on-site. This speeds up construction processes and improves site productivity.
- Handling Bulk Materials: Conveyor belts facilitate the efficient handling of bulk materials, which is essential for large-scale construction projects like roadworks, building foundations, and aggregate processing.
- Advantages:
- Cost-Effectiveness: Conveyor belts reduce the need for heavy machinery and manual labor, leading to cost savings on equipment and labor.
- Flexibility: Modular and portable conveyor systems can be easily set up and reconfigured on construction sites to adapt to changing project requirements and layouts.
- Reduced Environmental Impact: Using conveyor belts for material transport reduces the need for trucks, which decreases fuel consumption and lowers greenhouse gas emissions.
Other Industries
Relevant Applications and Specific Use Cases:
- Agriculture:
- Grain Handling: Conveyor belts are widely used in the agricultural industry to transport grains from harvesters to storage bins or processing facilities. They handle bulk materials efficiently and reduce the risk of grain damage during transport.
- Feed Production: In animal feed production, conveyor systems move raw ingredients through various stages of processing and packaging, improving production efficiency and consistency.
- Recycling Industry:
- Sorting and Processing: Conveyor belts are essential in recycling facilities for sorting and processing recyclable materials. They enable the separation of different materials (e.g., paper, plastics, metals) and transport them to appropriate processing areas.
- Efficiency in Sorting: Automated conveyor systems equipped with sensors and sorting mechanisms enhance the efficiency and accuracy of material separation, increasing overall recycling rates.
- Food and Beverage Industry:
- Processing and Packaging: Conveyor belts are used in food processing plants to transport ingredients, processed foods, and packaged products through various stages of production. They ensure smooth and continuous operation, reduce manual handling, and maintain hygiene standards.
- Quality Control: Conveyor systems with integrated quality control mechanisms help detect and remove defective products, ensuring high-quality standards in food production.
- Pharmaceutical Industry:
- Medication Handling: In pharmaceutical manufacturing, conveyor belts transport raw materials, intermediate products, and finished medications through different stages of production, packaging, and distribution. They help maintain precise control over the production process and ensure regulatory compliance.
- Cleanroom Applications: Specialized conveyor systems are designed for use in cleanroom environments, where maintaining contamination control is critical. These systems are constructed from materials that can be easily sanitized and meet strict cleanliness standards.
Each industry benefits from the use of rock conveyor belts by improving efficiency, reducing labor costs, and enhancing safety and environmental performance. The choice of conveyor system and design is tailored to meet the specific needs and challenges of each application.
Maintenance Rock Conveyor Belt
Proper maintenance of rock conveyor belts is essential for ensuring their reliability, efficiency, and longevity. Regular maintenance helps prevent unexpected breakdowns, reduces downtime, and extends the lifespan of the conveyor system. Here’s a comprehensive guide to maintaining rock conveyor belts:
Routine Inspections
- Visual Inspections:
- Frequency: Conduct regular visual inspections at least once a week or according to the manufacturer’s recommendations.
- What to Check: Look for signs of wear, damage, misalignment, and any unusual noises or vibrations. Inspect the condition of the belt, pulleys, rollers, and other components.
- Operational Checks:
- Performance Monitoring: Check for issues such as belt tracking problems, slippage, and uneven loading. Ensure that the conveyor operates smoothly and efficiently.
- Speed and Tension: Verify that the conveyor belt speed and tension are within the recommended parameters.
Belt Maintenance
- Cleaning:
- Regular Cleaning: Clean the belt regularly to remove debris, dust, and material build-up. Accumulated material can cause slippage, reduce efficiency, and lead to premature wear.
- Cleaning Methods: Use appropriate cleaning tools and methods, such as brushes or compressed air, that do not damage the belt. Avoid using harsh chemicals unless specified by the manufacturer.
- Inspection for Wear and Damage:
- Surface Inspection: Check the belt surface for cracks, tears, and abrasion. Replace any damaged sections promptly to prevent further damage.
- Edge and Joint Inspection: Examine the edges and joints of the belt for signs of wear or separation. Ensure that splice joints are secure and properly aligned.
- Belt Tension and Tracking:
- Adjust Tension: Ensure that the belt tension is correctly set to avoid excessive wear or slippage. Follow the manufacturer’s guidelines for adjusting tension.
- Track Alignment: Regularly check and adjust the alignment of the belt to prevent tracking issues and uneven wear.
Component Maintenance
- Pulley and Roller Maintenance:
- Inspection: Inspect pulleys and rollers for wear, damage, and proper alignment. Ensure that they are functioning correctly and are free of obstructions.
- Lubrication: Apply lubrication to bearings and other moving parts as per the manufacturer’s recommendations. Avoid over-lubrication, which can attract dirt and debris.
- Drive System Maintenance:
- Check Drives and Motors: Inspect the drive system, including motors, gearboxes, and belts, for wear and proper operation. Look for signs of vibration, noise, or overheating.
- Lubricate and Adjust: Regularly lubricate moving parts and adjust tension on drive belts or chains as needed.
Safety Checks
- Guarding and Safety Devices:
- Inspect Safety Guards: Ensure that all safety guards and covers are in place and functioning correctly to prevent accidents and injuries.
- Check Emergency Stops: Verify that emergency stop buttons and safety systems are operational and easily accessible.
- Training and Procedures:
- Staff Training: Train personnel on proper maintenance procedures and safety protocols. Ensure that they are aware of how to recognize potential issues and perform basic maintenance tasks.
Preventive and Predictive Maintenance
- Scheduled Maintenance:
- Maintenance Plan: Develop a maintenance schedule based on the manufacturer’s recommendations and the conveyor’s usage. Include routine inspections, cleaning, and component checks in the plan.
- Record Keeping: Maintain detailed records of all maintenance activities, including inspections, repairs, and replacements. This helps track the conveyor’s condition and identify recurring issues.
- Predictive Maintenance:
- Monitoring Systems: Implement monitoring systems that use sensors and data analysis to predict potential failures. This allows for proactive maintenance before issues lead to breakdowns.
- Condition Monitoring: Use techniques such as vibration analysis, thermal imaging, and belt condition monitoring to assess the health of the conveyor system and components.
Repairs and Replacements
- Addressing Issues:
- Prompt Repairs: Address any identified issues promptly to prevent further damage. Repair or replace damaged belts, components, or drive systems as needed.
- Quality Parts: Use high-quality replacement parts that meet the manufacturer’s specifications to ensure compatibility and performance.
- Professional Assistance:
- Expert Help: If major repairs or replacements are needed, consider consulting with or hiring professional technicians who specialize in conveyor systems.
By following these maintenance practices, you can ensure that rock conveyor belts operate efficiently, safely, and with minimal downtime. Regular attention to maintenance not only extends the life of the conveyor system but also enhances overall productivity and reduces long-term costs.

West River Conveyors: Customized Rock Conveyor Belt Solutions
West River Conveyors specializes in enhancing mining operations with their customized rock conveyor belt solutions. Their focus on efficiency and environmental safety through advanced overland conveyor systems ensures that mining activities are not only productive but also sustainable. West River Conveyors offers tailored quotes for custom conveyor systems, allowing clients to specify their unique requirements and receive a solution designed to meet their specific needs.
Your perfect rock conveyor belt is just a form away.
Recommended Products
West River Conveyors provides a range of highly functional products designed to handle various materials effectively.
Radial Stacker Conveyor
- Portable Radial Stacker: Ideal for stockpiling, this conveyor can be easily moved to different locations, offering flexibility and efficiency in handling materials.
- Tracked Radial Stacker: This conveyor provides superior mobility on rough terrain, making it suitable for challenging mining environments.
- Telescoping Radial Stacker: With adjustable length, this stacker allows for precise placement of materials and maximizes stockpiling capacity.
- Fixed Radial Stacker: Designed for permanent installations, it offers robust performance for long-term use in high-capacity operations.
- Electric Radial Stacker: Environmentally friendly and cost-effective, this conveyor is powered by electricity, reducing operational costs and emissions.
Conveyor Structure
West River Conveyors’ structures are designed to meet the rigorous demands of underground and longwall mining operations. These structures are built to withstand harsh conditions and provide reliable support for the rock conveyor belt systems. Specifications include:
- Heavy-Duty Construction: Ensures durability and longevity in underground environments.
- Modular Design: Facilitates easy assembly and maintenance, reducing downtime.
- Corrosion-Resistant Materials: Protects against moisture and chemical exposure common in mining settings.
- High Load Capacity: Supports heavy loads of rock and other materials, ensuring continuous operation.
- Adjustable Components: Allows customization to fit specific operational needs and spatial constraints.
Surface Conveyor Belts
Durable surface conveyor belts from West River Conveyors are designed for above-ground applications, offering robust performance and longevity. These belts are constructed from high-quality materials to withstand wear and tear while maintaining efficiency. Key features include:
- Abrasion Resistance: Extends the belt’s lifespan by preventing damage from sharp and abrasive materials.
- Heat Resistance: Suitable for high-temperature environments, ensuring consistent performance.
- Oil and Chemical Resistance: Ideal for industries where exposure to oils and chemicals is common.
- High Tensile Strength: Provides the necessary strength to transport heavy loads without stretching or breaking.
- Custom Widths and Lengths: Available in various sizes to meet specific operational requirements.
Project Handling
West River Conveyors excels in project handling, offering tailored solutions for a wide range of materials. Their expertise ensures that each project is approached with a customized plan that maximizes efficiency and productivity.
- Sand: Customized rock conveyor belt systems designed to handle sand efficiently, minimizing spillage and ensuring smooth transport.
- Gravel: Durable conveyor systems capable of transporting large volumes of gravel without frequent maintenance.
- Dry Bulk Materials: Solutions tailored to the unique requirements of handling dry bulk materials, ensuring safe and efficient transport.
- Coal: Robust systems designed to handle the heavy and abrasive nature of coal, providing reliable performance in challenging environments.
- Aggregates: Custom conveyor solutions for aggregates, including systems designed for precise sorting and transport.
West River Conveyors also offers comprehensive replacement part services to ensure minimal downtime and continuous operation. Their inventory includes a wide range of parts compatible with their conveyor systems, ensuring that any necessary repairs can be made quickly and efficiently.
Customization and Accessories
West River Conveyors prides itself on offering custom-designed systems tailored to specific operational needs. Their packages typically include system design, conveyor drive components, and various accessories to enhance performance and extend the service life of the rock conveyor belt systems.
Customization Options
- System Design: Tailored to fit the exact specifications of the client’s operation, ensuring optimal performance and efficiency.
- Conveyor Drive Components: High-quality components designed to provide reliable and efficient power transmission.
- Material Handling Solutions: Custom solutions for handling specific materials, ensuring the conveyor system meets all operational requirements.
Accessories to Improve Performance
- Belt Cleaners: Ensure the conveyor belt remains clean, reducing maintenance and prolonging the life of the system.
- Skirting Systems: Prevent spillage and protect the conveyor belt from damage, enhancing operational efficiency.
- Impact Beds: Absorb the impact of falling materials, protecting the conveyor belt and reducing wear.
- Dust Suppression Systems: Minimize dust generation, improving air quality and safety in the work environment.
- Alignment Systems: Ensure the conveyor belt stays aligned, preventing downtime and increasing the longevity of the system.
West River Conveyors’ commitment to customization and comprehensive solutions makes them a leader in the rock conveyor belt industry, providing clients with reliable, efficient, and durable conveyor systems tailored to their specific needs.
Rock Systems: Heavy-Duty Rock Conveyor Belt Systems
Categories of Conveyors
Rock Systems offers a diverse range of rock conveyor belt systems designed to meet the varying needs of different industries. Their product line includes everything from Radial Stackers to Container Loading Conveyors, each tailored to specific applications to ensure optimal performance and efficiency.
- Radial Stackers: These conveyors are designed for high-capacity stockpiling, capable of moving large quantities of material efficiently. They are commonly used in aggregate, mining, and recycling industries to create large, organized piles of materials.
- Overland Conveyors: Ranging from 30″ to 42″ in width, these conveyors are designed for long-distance material transport. Overland conveyors can span several miles, significantly reducing the need for truck haulage and associated costs.
- Transfer Conveyors: Field transfer conveyors are crucial for moving materials between different points within a site. These conveyors are versatile and can be configured for various operational needs, making them essential for continuous production processes.
- Portable Conveyors: Ideal for temporary operations, portable conveyors are easy to set up and move. They provide flexibility for projects requiring frequent relocation or adjustments in the conveyor setup.
- Container Loading Conveyors: Designed to streamline the loading and unloading process, these conveyors are perfect for efficiently transferring bulk materials into or out of shipping containers, reducing manual labor and speeding up operations.
Overview
Rock Systems’ heavy-duty rock conveyor belt systems are engineered for the economical transportation of materials over both short and long distances. These systems are built to handle the rigorous demands of transporting heavy and abrasive materials such as rock, sand, gravel, and dirt.
Key Features and Applications:
- Durability: Built with high-quality materials to withstand harsh operating conditions and minimize maintenance needs.
- Flexibility: Adaptable to various environments and operational requirements, from stationary setups to mobile applications.
- Efficiency: Designed to optimize material handling processes, reducing operational costs and increasing throughput.
- Loading/Unloading Capabilities: Ideal for facilitating the efficient loading and unloading of materials, minimizing downtime and labor costs.
- Stockpiling Capabilities: Enhance storage and inventory management with conveyors that can create organized stockpiles, making it easier to manage large volumes of materials.
Inventory and Specific Offerings
Rock Systems boasts an extensive inventory of rock conveyor belt systems available for sale, rent, or lease, providing flexible options to meet the needs of different projects and budgets. Their detailed inventory includes conveyors tailored for various applications, from portable units to stationary installations.
- Portable Radial Stackers: Available in multiple configurations to suit different project needs, these stackers are ideal for creating stockpiles in temporary or permanent sites. Their portability ensures they can be moved and reconfigured as required.
- Stationary Overland Conveyors: Perfect for long-term installations, these conveyors provide a reliable solution for transporting materials over long distances. They are designed to be durable and efficient, minimizing the need for frequent maintenance.
- Field Transfer Conveyors: Versatile and essential for any material handling operation, these conveyors facilitate the smooth transfer of materials between different processing stages or storage areas within a site.
- Heavy-Duty Container Loading Conveyors: Engineered to handle the demands of bulk material loading and unloading, these conveyors streamline the process, reducing manual labor and speeding up operations.
- Custom Conveyor Systems: Rock Systems can design and build custom conveyor systems tailored to specific operational needs, ensuring optimal performance and efficiency for unique project requirements.
Rock Systems’ comprehensive range of heavy-duty rock conveyor belt systems is designed to meet the diverse needs of various industries. Their products are built for durability, flexibility, and efficiency, ensuring that they can handle the rigorous demands of transporting heavy and abrasive materials over short and long distances. With an extensive inventory available for sale, rent, or lease, and the ability to provide custom solutions, Rock Systems is a reliable partner for any material handling needs. Their focus on quality and innovation ensures that their rock conveyor belt systems are among the best in the industry, providing reliable performance and enhancing productivity for their clients. Whether you need a portable solution for a temporary project or a robust, stationary conveyor for a long-term installation, Rock Systems has the expertise and products to meet your requirements.
Bando: Advanced Rock Conveyor Belt Systems
Features
Bando’s advanced rock conveyor belt systems are engineered to handle the most demanding industrial environments, providing superior performance and durability. These belts are designed with specific features that make them ideal for high-impact and abrasive conditions.
Impact Resistance: Bando’s rock conveyor belts are built to withstand significant impacts from heavy and sharp materials. This makes them highly durable and less prone to damage, ensuring a longer service life even in harsh conditions.
- Heavy-Duty Mining Operations: Designed to handle the extreme impact of large rocks and debris common in mining.
- Quarrying: Suitable for the heavy impact of transporting large stones and aggregates.
- Construction Sites: Effective in handling the rigorous impact from construction debris and heavy materials.
- Recycling Facilities: Can manage the impact from various waste materials, including metals and concrete.
- Logging Operations: Durable enough to handle the impact from transporting large logs and timber.
Cut and Abrasion Resistance: These belts are engineered to resist cuts and abrasion, extending their lifespan by protecting against sharp materials and continuous wear.
- Sharp Rock Transport: Effective in environments where sharp rocks are regularly transported, preventing belt damage.
- Scrap Metal Handling: Ideal for recycling plants handling sharp metal scraps.
- Sand and Gravel Operations: Resistant to the abrasive nature of sand and gravel, minimizing wear.
- Industrial Manufacturing: Suitable for transporting abrasive industrial materials without excessive wear.
- Glass Recycling: Capable of handling sharp glass pieces without sustaining significant damage.
Bite Resistance: Bando’s rock conveyor belts are designed to minimize surface damage at loading points, which is crucial for maintaining belt integrity and performance.
- Coal Handling: Effective in preventing damage from sharp coal edges during loading.
- Aggregate Transport: Reduces surface damage when loading large, irregularly shaped aggregates.
- Cement Plants: Maintains belt integrity under the harsh conditions of cement loading.
- Metal Mining: Resists damage from heavy metal ores during the loading process.
- Construction Material Handling: Prevents surface damage from heavy and sharp construction materials during loading.
Applications and Types of Belts
Bando’s rock conveyor belts are ideal for applications that involve high impact and wear, often requiring frequent replacement due to the demanding nature of the materials being transported. Their belts are categorized based on construction and intended use.
Monoply Belts: These belts feature a single-ply construction, making them suitable for less harsh applications. They offer a cost-effective solution for operations where the material transported is not excessively abrasive or heavy.
- Food Processing: Ideal for transporting food products with minimal impact and abrasion.
- Packaging: Suitable for handling packaged goods in manufacturing and logistics.
- Light Manufacturing: Effective in transporting non-abrasive industrial materials.
- Textile Industry: Suitable for handling textile products without causing damage.
- Pharmaceuticals: Ideal for transporting delicate pharmaceutical products in clean environments.
Large Block Belts: Featuring dual-ply construction, these belts are designed for higher impact resistance and are well-suited for transporting large or sharp materials. Their robust design ensures longevity and reliability in tough conditions.
- Mining Operations: Essential for transporting large rocks and ores in mining environments.
- Quarries: Ideal for moving large stones and aggregates, offering high resistance to impact and abrasion.
- Heavy Construction: Suitable for transporting heavy and sharp construction materials such as concrete blocks and steel beams.
- Steel Mills: Effective in handling sharp and heavy steel products.
- Waste Management: Robust enough to handle large and sharp waste materials in recycling facilities.
Bando’s advanced rock conveyor belt systems are a testament to their commitment to quality and innovation in material handling solutions. With features like impact resistance, cut and abrasion resistance, and bite resistance, these belts are engineered to meet the rigorous demands of industries that handle heavy, sharp, and abrasive materials.
Their monoply belts offer a cost-effective solution for less harsh environments, providing reliable performance where heavy-duty belts are not necessary. On the other hand, the large block belts are designed for the toughest applications, ensuring durability and longevity even under extreme conditions.
Whether it’s mining, quarrying, construction, or industrial manufacturing, Bando’s rock conveyor belt systems provide the durability and reliability needed to keep operations running smoothly and efficiently. Their ability to minimize surface damage at loading points, resist cuts and abrasion, and withstand heavy impacts makes them an ideal choice for any industry dealing with demanding material handling challenges.
FAQs About Rock Conveyor Belt
The strongest conveyor belts are typically made from high-tensile strength materials, such as steel-reinforced rubber or synthetic fibers like Kevlar. These materials are designed to withstand extreme loads and harsh conditions, making them ideal for demanding applications in industries such as mining, quarrying, and heavy-duty manufacturing. Steel-reinforced belts, for example, can handle the heaviest loads and the most abrasive materials without tearing or stretching. Kevlar-reinforced belts are known for their excellent resistance to impact and wear, making them suitable for high-impact environments. The choice of the strongest conveyor belt depends on the specific requirements of the application, including the type of material being transported, the distance of conveyance, and the environmental conditions.
A conveyor belt is commonly referred to as a “belt conveyor.” It is a key component of a conveyor system, which is used to transport materials from one location to another efficiently. Belt conveyors consist of a continuous loop of material (the belt) that moves around a series of pulleys, driven by motors. The belt itself can be made from various materials, including rubber, PVC, fabric, or metal, depending on the application. Belt conveyors are widely used in various industries, including manufacturing, mining, logistics, and food processing, due to their ability to move materials quickly and efficiently over both short and long distances.
There are several types of belt conveyors, each designed for specific applications and material handling needs:
Flat Belt Conveyors: The most common type, used for transporting items on a flat surface. Ideal for light to medium loads.
Modular Belt Conveyors: Made of interlocking plastic pieces, suitable for transporting goods around curves and for applications requiring frequent cleaning.
Cleated Belt Conveyors: Feature raised sections (cleats) that help transport materials up inclines and prevent items from sliding backward.
Incline/Decline Belt Conveyors: Designed to move materials between different elevations, useful in multi-level warehouses or production lines.
Sidewall Belt Conveyors: Have corrugated sidewalls to contain materials and are used for transporting loose bulk materials like grains or coal.
Steel Belt Conveyors: Made from stainless or carbon steel, ideal for transporting hot, sharp, or heavy materials in harsh environments.
The main difference between a belt conveyor and a slat conveyor lies in their design and applications.
Belt Conveyor: This system uses a continuous belt made of materials like rubber, fabric, or metal to transport items. It is versatile, suitable for a wide range of materials, and ideal for both short and long-distance transportation. Belt conveyors are commonly used in industries like mining, manufacturing, and logistics due to their efficiency and ability to handle various loads.
Slat Conveyor: This system uses a series of slats or plates, usually made of metal or plastic, linked together to form a continuous chain. The slats provide a stable surface, making them ideal for transporting heavy, bulky items or products that need to remain in a fixed position during transportation. Slat conveyors are often used in assembly lines, automotive manufacturing, and packaging applications. They are more durable than belt conveyors but can be less flexible in terms of the types of materials they can handle.
Last Updated on July 30, 2024 by Jordan Smith
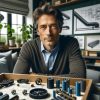
Jordan Smith, a seasoned professional with over 20 years of experience in the conveyor system industry. Jordan’s expertise lies in providing comprehensive solutions for conveyor rollers, belts, and accessories, catering to a wide range of industrial needs. From initial design and configuration to installation and meticulous troubleshooting, Jordan is adept at handling all aspects of conveyor system management. Whether you’re looking to upgrade your production line with efficient conveyor belts, require custom conveyor rollers for specific operations, or need expert advice on selecting the right conveyor accessories for your facility, Jordan is your reliable consultant. For any inquiries or assistance with conveyor system optimization, Jordan is available to share his wealth of knowledge and experience. Feel free to reach out at any time for professional guidance on all matters related to conveyor rollers, belts, and accessories.