Industry Rock Quarry Conveyor Belt System
Understanding the critical role of conveyor belt systems in rock quarries is essential for optimizing material handling efficiency. This guide explores various aspects of rock quarry conveyor belts, including types, rentals, sales, and specific applications. The rock quarry conveyor belt is a vital component in transporting materials efficiently and safely across different areas within a quarry. Rock quarry conveyor belt are designed to reduce downtime and increase efficiency in transporting bulk materials. Offer excellent rip, tear, and impact resistance.By exploring the features and benefits of different types of rock quarry conveyor belts, this guide aims to provide comprehensive insights into their usage and advantages in the quarrying industry.
Rock Quarry Conveyor Belt System
A rock quarry conveyor belt system is an essential part of a quarry’s operations, used to transport materials efficiently and effectively. Here’s an overview of the components and workings of such a system:
Components of a Rock Quarry Conveyor Belt System
- Conveyor Belts:
- Material: Made from materials such as rubber, textile, or steel cords, depending on the type and amount of material being transported.
- Design: Can be flat, troughed, or cleated to prevent materials from slipping, especially on inclines.
- Pulleys:
- Drive Pulley: Powered by a motor to move the belt.
- Idler Pulley: Supports the belt and materials, ensuring smooth movement.
- Motors and Drives:
- Electric Motors: Provide the necessary power to move the conveyor belts.
- Gearboxes and Drives: Control the speed and direction of the belts.
- Rollers and Idlers:
- Carrying Rollers: Support the loaded belt.
- Return Rollers: Support the empty belt on its return trip.
- Impact Idlers: Placed at loading points to absorb the impact of heavy materials.
- Belt Cleaners:
- Primary and Secondary Cleaners: Remove material that sticks to the belt to prevent buildup and ensure smooth operation.
- Hoppers and Chutes:
- Hoppers: Used for loading materials onto the conveyor belt.
- Chutes: Guide the materials as they are discharged from the belt.
- Safety Devices:
- Emergency Stop Switches: Allow the conveyor to be stopped immediately in case of an emergency.
- Safety Guards: Protect workers from moving parts of the conveyor system.
- Control Systems:
- Programmable Logic Controllers (PLCs): Automate the operation of the conveyor system.
- Sensors: Monitor belt speed, alignment, and load.
Working of a Rock Quarry Conveyor Belt System
- Material Loading:
- Raw materials are loaded onto the conveyor belt from a hopper or directly from an excavator.
- Material Transport:
- The conveyor belt moves the materials from the loading point to the processing area. The belt’s speed and direction are controlled by motors and drives.
- Rollers and idlers support the belt and ensure smooth movement.
- Material Processing:
- As materials are transported, they may pass through crushers, screens, and other processing equipment.
- Material Discharge:
- Processed materials are discharged from the conveyor belt into storage piles, bins, or directly into trucks for transport.
- Maintenance and Safety:
- Regular maintenance is performed to ensure the system operates efficiently and safely.
- Safety devices and control systems are in place to protect workers and prevent accidents.
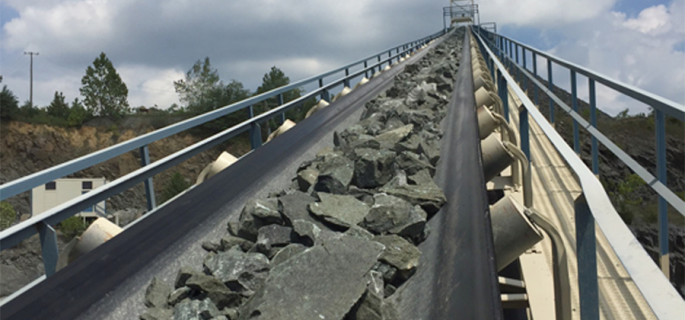
Types of Rock Quarry Conveyor Belt
Rock quarry conveyor belts come in various types, each designed to suit specific applications and materials. Here are some common types of conveyor belts used in rock quarries:
Each type of conveyor belt is selected based on the specific needs of the quarry operation, including the type of material being transported, the distance and incline of the conveying route, and environmental conditions.
Applications of Rock Quarry Conveyor Belt
Rock quarry conveyor belts are used in various stages of quarry operations to ensure efficient material handling and processing. Here are some specific applications of rock quarry conveyor belts:
Primary Crushing and Transport
- Application: Transporting large rocks from the quarry face to primary crushers.
- Description: Large dump trucks or loaders transport raw material from the quarry face and deposit it into hoppers, which feed onto primary conveyor belts. These belts then transport the material to the primary crusher for initial size reduction.
Secondary and Tertiary Crushing
- Application: Moving material between crushing stages.
- Description: After primary crushing, conveyor belts transport the material to secondary and tertiary crushers for further size reduction. This helps in achieving the desired material size and shape.
Screening and Sorting
- Application: Transporting materials to screening equipment.
- Description: Conveyor belts move crushed material to screening stations where it is sorted by size. Screens separate the material into different grades, and conveyors transport each grade to the appropriate location.
Stockpiling
- Application: Creating storage piles of processed materials.
- Description: Conveyor belts transport sorted and processed materials to stockpile areas. This allows for efficient storage and easy access when the material is needed for further processing or transport.
Loading and Unloading
- Application: Loading materials onto transport vehicles or into storage silos.
- Description: Conveyor belts are used to load trucks, railcars, or ships with processed materials for transport. They can also feed materials into storage silos or bins for later use.
Reclaiming
- Application: Retrieving materials from stockpiles for further processing or shipping.
- Description: Conveyor systems with reclaimers are used to retrieve stored materials and transport them to processing plants or directly to loading stations for shipping.
Waste Management
- Application: Transporting waste and byproducts away from the processing areas.
- Description: Conveyor belts are used to move waste material and byproducts to designated disposal areas, ensuring the main operation areas remain clean and efficient.
Environmental Management
- Application: Minimizing dust and spillage during material transport.
- Description: Enclosed conveyor belts or those equipped with dust control systems help to reduce the environmental impact by minimizing dust and material spillage during transport.
Example Workflow in a Rock Quarry
- Extraction:
- Raw material is extracted using blasting, drilling, or digging.
- Primary Crushing:
- Large rocks are transported by conveyor belts to primary crushers for initial processing.
- Secondary Crushing and Screening:
- Material is conveyed to secondary and tertiary crushers and then to screening plants.
- Stockpiling:
- Processed material is transported to stockpile areas for storage.
- Loading and Transport:
- Material is loaded onto trucks, railcars, or ships via conveyor belts for delivery to customers.
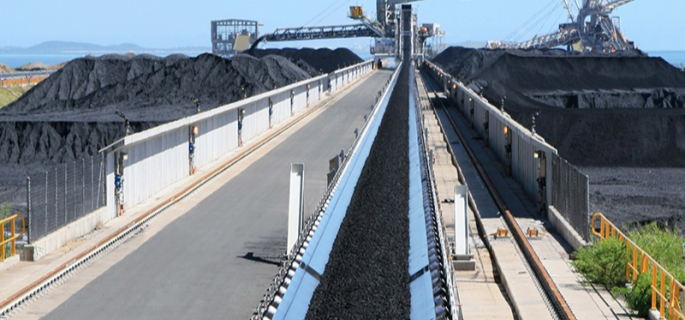
Gravel Rock Quarry Conveyor Belt Systems
Introduction to Gravel Conveyors
Gravel conveyors play a crucial role in rock quarries by facilitating the efficient movement of materials. A rock quarry conveyor belt is essential for optimizing material handling, reducing manual labor, and increasing productivity. Key features of these conveyor belts include durability, high load capacity, and adaptability to different terrains and materials, ensuring they can handle the demanding conditions of a quarry environment.
Types of Gravel Conveyors
Gravel conveyors come in various types to suit different needs. Standard conveyor belts are versatile and suitable for most gravel transport tasks, while heavy-duty conveyor belts are designed for large volumes and heavier loads. Both types ensure efficient material transport within the quarry.
Applications in Rock Quarries
A rock quarry conveyor belt is used for several key applications within a quarry:
- Transporting gravel from extraction points to processing areas.
- Loading gravel onto trucks or other transport vehicles.
- Unloading gravel at different points within the quarry for processing or storage.
For example, in a large-scale quarry, a conveyor belt can move up to 1000 tons of gravel per hour, streamlining the workflow and significantly reducing manual handling.
Maintenance Tips
Proper maintenance of a rock quarry conveyor belt is essential to ensure its longevity and efficiency. Regular inspection is necessary to identify and address issues such as belt wear, misalignment, or damaged rollers. Routine upkeep, such as lubrication and tension adjustment, helps maintain optimal performance. Common issues like belt slippage or material spillage should be addressed promptly to avoid operational disruptions.
By following these maintenance tips and conducting periodic inspections, quarry operators can ensure their rock quarry conveyor belt remains in excellent working condition, minimizing downtime and maximizing productivity.
Portable Aggregate Rock Quarry Conveyor Belt Systems
Benefits of Portable Aggregate Conveyors
Portable aggregate rock quarry conveyor belts offer significant mobility and flexibility, making them ideal for various quarrying needs. Their ease of installation and relocation allows for quick adjustments on-site, enhancing operational efficiency. For example, a portable conveyor can be moved to different locations within the quarry as extraction sites change, reducing downtime and labor costs.
Features of Portable Conveyors
Portable rock quarry conveyor belts are designed with lightweight and durable construction, ensuring they can withstand harsh quarry environments. They often come with adjustable heights and lengths, making them versatile for different applications. For instance, a conveyor with adjustable height can facilitate the loading of aggregate onto trucks of varying sizes.
Applications in Rock Quarries
Portable rock quarry conveyor belts are crucial for temporary projects and site adjustments. They are particularly useful in scenarios where portability is essential, such as when new excavation sites are frequently established. In a large quarry, a portable conveyor can handle the movement of 500 tons of aggregate daily, significantly improving workflow efficiency.
Selecting the Right Portable Conveyor
Choosing the right portable rock quarry conveyor belt involves considering project-specific criteria such as duration, material type, and required capacity. Balancing cost and functionality is key. For example, a quarry operation requiring the transport of 300 tons of sand per day might opt for a medium-capacity portable conveyor that offers both efficiency and cost-effectiveness.
By understanding the benefits, features, applications, and selection criteria of portable aggregate rock quarry conveyor belts, quarry operators can enhance their material handling processes, ensuring a more productive and efficient operation.
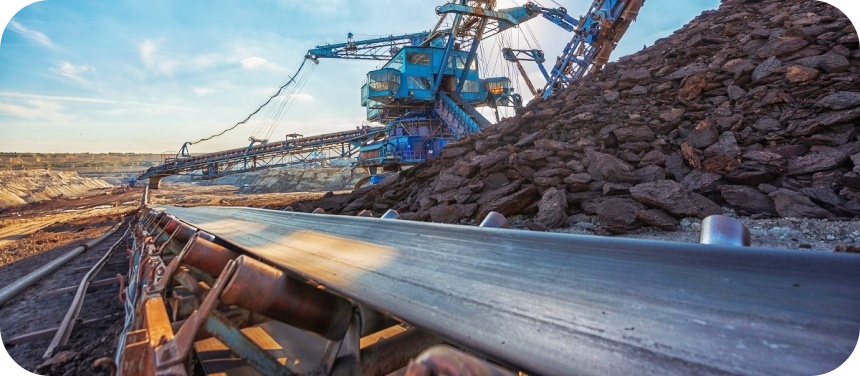
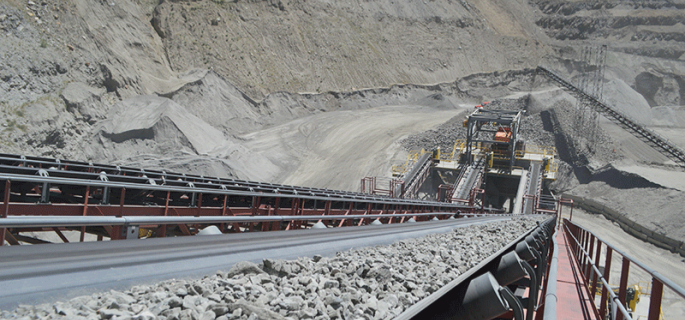
Purchasing Rock Quarry Conveyor Belt Systems
Purchasing Considerations
When considering the purchase of a rock quarry conveyor belt, it is important to weigh the pros and cons of new versus used belts. New conveyor belts ensure reliability and a longer lifespan but come at a higher cost. Used conveyor belts offer cost savings but may require more maintenance. Key factors in the decision include budget, project scale, and expected usage. For example, a large-scale quarry project may justify the investment in new belts due to their durability and lower long-term maintenance costs.
Types of Rock Conveyor Belts Available
Rock quarry conveyor belts come in various types to suit different needs:
- Heavy-duty belts for transporting large rocks and handling high-impact loads.
- Specialized belts designed for specific rock types, such as abrasive or sharp-edged materials.
Selecting the right type ensures efficient material handling and prolongs the belt’s life. For instance, heavy-duty belts are ideal for quarries dealing with large, heavy rocks, ensuring they can handle the intense demands without frequent replacements.
Finding Reliable Suppliers
Selecting a trustworthy supplier for your rock quarry conveyor belt is crucial. Look for vendors with positive reviews, a proven track record, and comprehensive warranties. Quality assurance is essential, as a reliable belt reduces downtime and maintenance costs. For example, a supplier offering a one-year warranty and free installation support demonstrates confidence in their product and commitment to customer satisfaction.
Installation and Setup
Proper installation and setup of a rock quarry conveyor belt are vital for optimal performance. Follow these steps:
- Site Preparation: Ensure the installation area is clear and stable.
- Assembly: Assemble the conveyor components according to the manufacturer’s guidelines.
- Alignment: Properly align the belt to prevent tracking issues.
- Testing: Conduct initial tests to ensure smooth operation.
Ensuring optimal performance from the start minimizes operational disruptions and extends the conveyor belt’s lifespan. For example, a quarry installing a new conveyor system can expect up to a 20% increase in efficiency with proper setup and regular maintenance checks.
By carefully considering these aspects, quarry operators can make informed decisions when purchasing rock quarry conveyor belts, ensuring they select the best systems for their specific needs and operational goals.
Used Rock Quarry Conveyor Belt
Using used rock quarry conveyor belts can be a cost-effective solution for material handling in quarry operations. Here are some considerations and applications for using second-hand conveyor belts in a rock quarry:
Advantages of Using Used Conveyor Belts
- Cost Savings:
- Used conveyor belts are significantly cheaper than new ones, reducing capital expenditure.
- Availability:
- Second-hand belts can be readily available and quickly deployed, minimizing downtime.
- Environmental Impact:
- Reusing conveyor belts reduces waste and supports recycling efforts, contributing to sustainability.
Considerations When Using Used Conveyor Belts
- Condition:
- Inspect the belts thoroughly for wear, tears, and overall integrity to ensure they are suitable for use.
- Check for damage to the reinforcing fabric or steel cords, and ensure that the belt’s surface is in good condition.
- Specifications:
- Verify that the used belts meet the specifications required for your quarry operations, such as conveyor belt tensile strength, width, and length.
- Compatibility:
- Ensure that the used belts are compatible with your existing conveyor system, including pulleys, rollers, and motors.
- Maintenance History:
- Obtain maintenance records to understand the belt’s history and any previous repairs or issues.
- Safety:
- Ensure that the used belts comply with safety standards and regulations to protect workers and equipment.
Sources for Used Conveyor Belts
- Quarry and Mining Equipment Dealers:
- Dealers often sell used conveyor belts as part of their inventory of second-hand equipment.
- Online Marketplaces:
- Websites such as eBay, Alibaba, and specialized industrial equipment marketplaces list used conveyor belts for sale.
- Industrial Auctions:
- Attend industrial auctions where used quarry equipment, including conveyor belts, is sold.
- Local Quarries and Mines:
- Contact local quarries and mines that might have surplus or decommissioned conveyor belts available for sale.
Example Process for Sourcing and Installing Used Conveyor Belts
- Identify Needs:
- Determine the specifications and quantity of conveyor belts required for your operation.
- Source Suppliers:
- Research and contact suppliers who offer used conveyor belts that match your specifications.
- Inspect Belts:
- Conduct a thorough inspection of the belts for wear and damage, and verify their suitability for your needs.
- Negotiate Purchase:
- Negotiate terms and prices with the supplier to get the best deal.
- Transport and Install:
- Arrange for transportation of the belts to your quarry site and install them with the assistance of experienced technicians.
- Regular Maintenance:
- Implement a maintenance schedule to monitor the condition of the used belts and address any issues promptly.
By carefully selecting and maintaining used conveyor belts, quarry operators can achieve significant cost savings while maintaining efficient material handling operations.
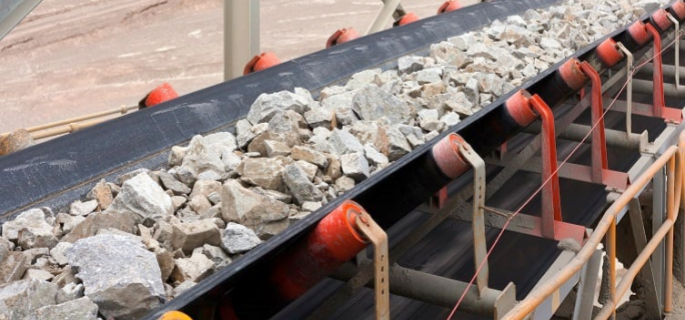
Rock Quarry Conveyor Belt Rental Options
Overview of Rental Options
Rental options for rock quarry conveyor belts are crucial for short-term projects or temporary needs. Renting allows for flexibility and cost savings compared to purchasing. For example, a quarry needing a conveyor belt for a three-month project can save significantly on capital expenditure by renting rather than buying a new system. Renting also allows companies to access the latest conveyor technology without the long-term commitment.
Types of Rental Conveyors
Portable and stationary conveyor belts are the primary types of rental options available. Portable conveyors are ideal for projects that require frequent relocation, while stationary conveyors are suitable for longer-term use in fixed locations.
Specialized conveyors cater to different materials, such as sand, gravel, or aggregate, ensuring efficient handling and transport.
Selecting the Right Conveyor for Your Needs
When selecting a rock quarry conveyor belt, consider project duration, material type, and volume. For instance, a six-month project handling heavy rocks would benefit from a stationary conveyor with a high load capacity. Determine the appropriate conveyor length and capacity based on the volume of material to be transported daily. For example, if transporting 500 tons of gravel daily, choose a conveyor with a suitable capacity to handle the load efficiently.
Rental Process
The process of renting a rock quarry conveyor belt involves several steps:
- Identify your project requirements and duration.
- Contact rental companies to inquire about availability and options.
- Review rental terms and conditions, including pricing and maintenance responsibilities.
- Arrange for delivery and installation of the conveyor belt.
For a successful rental experience, ensure clear communication with the rental company and schedule regular maintenance checks to avoid downtime. For example, a quarry project in Arizona renting a portable conveyor belt for three months should establish a maintenance schedule to inspect the belt every two weeks, ensuring smooth operation throughout the project duration.
Rock Quarry Conveyor Belt for Gravel Conveyor Rental
Advantages of Renting Gravel Conveyors
Renting gravel conveyors for rock quarry conveyor belt systems offers significant cost-effectiveness for short-term needs. It provides flexibility in equipment selection, allowing companies to choose the best fit for specific project requirements without a long-term commitment. For example, a quarry that needs a conveyor for a three-month project can avoid the high upfront costs of purchasing by opting for rental, thus freeing up capital for other essential expenditures.
Rental Options and Packages
Various types of gravel conveyors are available for rent to suit different needs:
Rental packages can be customized to fit project requirements, offering options such as daily, weekly, or monthly rates, and including additional services like maintenance and support.
Process of Renting a Gravel Conveyor
Renting a rock quarry conveyor belt for gravel involves several steps:
- Finding Rental Services: Research and contact reputable rental companies that specialize in rock quarry conveyor belt systems.
- Documentation and Agreements: Review and sign rental agreements, ensuring all terms and conditions are clear, including rental duration, costs, and responsibilities for maintenance and repairs.
For instance, a quarry needing a gravel conveyor for a six-month project would contact multiple rental services, compare quotes, and finalize the agreement with the best terms.
Tips for a Successful Rental
To ensure a successful rock quarry conveyor belt rental experience:
- Proper Usage: Train staff on the correct operation of the conveyor to prevent misuse and damage.
- Maintenance: Schedule regular maintenance checks to keep the conveyor in optimal condition.
- Avoid Pitfalls: Be aware of common issues like overloading the conveyor or improper alignment, which can lead to breakdowns and project delays.
For example, a quarry in California renting a conveyor belt for a gravel project should establish a weekly maintenance routine and ensure operators are well-trained to minimize the risk of operational disruptions. By following these tips, quarries can maximize the efficiency and lifespan of their rented rock quarry conveyor belt systems.
Sand Conveyor Rental for Rock Quarry Conveyor Belt Systems
Importance of Sand Conveyors in Rock Quarries
Sand conveyors play a vital role in rock quarry conveyor belt systems, specifically designed to handle sand efficiently within quarry operations. These conveyors facilitate the smooth transport of sand from extraction sites to processing areas, significantly reducing manual labor and improving operational efficiency. For instance, in a large quarry, sand conveyors can move up to 800 tons of sand per day, streamlining the workflow.
Types of Sand Conveyors for Rent
Different types of sand conveyors are available for rent, tailored to various needs:
Renting Process and Considerations
Renting a sand conveyor for a rock quarry conveyor belt involves several steps:
- Evaluating Sand Handling Needs: Assess the volume and type of sand to be transported to determine the right conveyor type.
- Securing a Rental Agreement: Contact rental companies, compare quotes, and finalize the rental agreement. Ensure that the agreement covers all aspects, including rental duration, cost, and maintenance responsibilities.
For example, a quarry needing a portable sand conveyor for a three-month project should evaluate daily sand volume and select a conveyor that can handle the load efficiently.
Maximizing Rental Efficiency
To maximize the efficiency of a rented sand conveyor for a rock quarry conveyor belt system, follow these best practices:
- Proper Usage: Train staff on correct conveyor operation to avoid misuse and ensure safety.
- Regular Maintenance: Schedule maintenance checks to prevent equipment breakdowns and extend the conveyor’s lifespan.
- Avoiding Downtime: Address common issues such as belt misalignment or overloading promptly to minimize disruptions.
For example, a quarry in Texas renting a sand conveyor should establish a weekly maintenance routine and ensure operators are trained to detect and resolve common issues quickly. By following these practices, quarries can ensure efficient and reliable operation of their rented rock quarry conveyor belt systems for sand handling.
Speak with our team about custom conveyor belt options.
FAQs about Rock Quarry Conveyor Belt
The world’s largest rock quarry conveyor belt is located in the Western Sahara, stretching over 61 miles (100 kilometers). This extensive system transports phosphate rock from the Bou Craa mine to the coastal town of El Aaiún. The rock quarry conveyor belt’s impressive length and capacity significantly enhance the efficiency of mining operations, allowing for the continuous transport of large quantities of phosphate. The belt’s visibility from space underscores its immense scale and crucial role in the regional mining industry.
The longest rock quarry conveyor belt used in mining spans 31 kilometers (19 miles) in Western Australia. This single conveyor system moves bauxite from the Mount Saddleback mine to the Worsley Alumina refinery, demonstrating the effectiveness of long-distance conveyor technology in the mining sector. The rock quarry conveyor belt reduces the reliance on truck transport, thereby minimizing environmental impact and operational costs. Such systems highlight the advancements in conveyor technology, enabling the efficient handling of vast amounts of material over extended distances.
A rock quarry conveyor belt is designed for transporting bulk materials such as rocks and gravel within quarry environments. It typically consists of a continuous loop of rubber or synthetic material that moves over rollers to convey materials efficiently. In contrast, a slat conveyor features interlocking slats or plates, often made of metal or plastic, which provide a solid moving surface. Slat conveyors are ideal for handling heavy, sharp, or abrasive items that could damage a standard belt. They are commonly used in manufacturing and assembly lines, while rock quarry conveyor belts are specialized for bulk material handling in quarries and mining operations.
The heavy-duty rubber rock quarry conveyor belt is the most commonly used type in mining operations. These belts are engineered to withstand the demanding conditions of mining environments, including the transport of heavy, abrasive materials such as ore, rocks, and gravel. Their robust construction ensures excellent impact resistance and durability, making them suitable for continuous operation under harsh conditions. Heavy-duty rubber conveyor belts’ ability to handle large volumes of material efficiently makes them a preferred choice in the mining industry, contributing to improved operational productivity and reduced downtime.
An auger and a conveyor belt are both used to transport materials, but they function differently and are suited for distinct applications. An auger, also known as a screw conveyor, uses a helical screw blade that rotates within a tube to move granular or semi-solid materials like grain, sand, or mining waste. It is ideal for confined spaces and vertical or inclined transport. Conversely, a conveyor belt consists of a continuous loop of material that moves over rollers and pulleys to transport bulk materials like ore, coal, and aggregates over long distances and flat or gently inclined surfaces. Conveyor belts are preferred in heavy industries such as mining and quarrying for their high capacity, efficiency, and ability to cover extensive horizontal and inclined distances.
The largest conveyor belt company is Continental AG, a German multinational corporation known for its extensive range of conveyor belt solutions. Continental’s products are renowned for their durability, efficiency, and innovation, catering to various industries including mining, heavy industry, and bulk material handling. Their conveyor belts are designed to withstand harsh conditions and high loads, making them ideal for use in demanding environments such as quarries and mining operations. With a global presence and a strong focus on research and development, Continental continues to lead the market, offering cutting-edge technologies that enhance productivity and safety in heavy industrial applications.
A mining conveyor belt works by transporting raw materials such as ore, coal, and overburden from one point to another, often from the mining site to a processing plant or stockpile. The system consists of a continuous loop of belt material that moves over a series of rollers and pulleys driven by electric motors. These belts are engineered to withstand heavy loads, abrasive materials, and harsh environmental conditions. Sensors and automation systems often monitor the belt’s operation, ensuring efficient material flow and preventing issues like spillage or belt misalignment. The use of conveyor belts in mining significantly enhances operational efficiency by reducing manual handling, speeding up material transport, and enabling continuous, automated processes.
The world’s largest conveyor belt is located in the Western Sahara, specifically in the Bou Craa phosphate mines. This belt system, spanning over 100 kilometers, transports phosphate rock from the mining site to the coastal town of El Aaiún, where it is then shipped for processing. The conveyor belt system is a crucial infrastructure for the mining operation, significantly reducing the need for truck transportation and enabling efficient, continuous movement of large volumes of material. This vast conveyor system highlights the scale and complexity of modern mining operations, demonstrating the essential role of advanced conveyor technology in heavy industry.
The three main types of conveyors used in heavy industries like mining and quarrying are belt conveyors, chain conveyors, and roller conveyors. Belt conveyors are the most common, featuring a continuous belt loop that transports materials over long distances and varied terrains, ideal for bulk materials like ore and coal. Chain conveyors use a series of interlinked chains to move materials, offering robust performance for heavy loads and abrasive conditions, often used for transporting bulk materials in mining and industrial settings. Roller conveyors consist of a series of rollers that allow materials to be moved manually or by gravity, suitable for handling heavy loads and used extensively in material handling and packaging processes. Each type offers unique advantages depending on the application and material characteristics.
Last Updated on August 15, 2024 by Jordan Smith
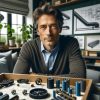
Jordan Smith, a seasoned professional with over 20 years of experience in the conveyor system industry. Jordan’s expertise lies in providing comprehensive solutions for conveyor rollers, belts, and accessories, catering to a wide range of industrial needs. From initial design and configuration to installation and meticulous troubleshooting, Jordan is adept at handling all aspects of conveyor system management. Whether you’re looking to upgrade your production line with efficient conveyor belts, require custom conveyor rollers for specific operations, or need expert advice on selecting the right conveyor accessories for your facility, Jordan is your reliable consultant. For any inquiries or assistance with conveyor system optimization, Jordan is available to share his wealth of knowledge and experience. Feel free to reach out at any time for professional guidance on all matters related to conveyor rollers, belts, and accessories.