Roller Bed Conveyor Design and Types
In the vast world of modern manufacturing and logistics, roller bed conveyor systems stand out as indispensable tools for efficient material handling. These systems are designed to transport heavy loads smoothly and with minimal effort, leveraging rollers to reduce friction and enhance the flow of goods through production lines or distribution centers. The design of a roller bed conveyor is critical to its effectiveness, directly impacting the system’s capacity to handle varying weights and sizes of products. By integrating advanced roller bed conveyor design techniques, industries can significantly optimize their operations, improving not only the speed and efficiency of product movement but also ensuring the safety and longevity of the conveyor system itself. This foundational technology supports a wide array of applications, from simple warehouse operations to complex assembly lines, highlighting its pivotal role in the seamless execution of manufacturing and logistic operations worldwide.
Mastering Roller Bed Conveyor Design for Enhanced Efficiency
In the realm of material handling, mastering the essentials of roller bed conveyor design is crucial for engineers and facility managers aiming to enhance operational efficiency. Roller conveyor design PDFs serve as foundational resources, offering detailed insights into the specifications, capabilities, and configurations of various systems. These documents are invaluable for understanding the intricate aspects of roller bed conveyors, including load capacity, roller spacing, and belt material options. They provide a solid theoretical background that aids in the practical application and customization of conveyor systems to meet specific operational needs.
Furthermore, the exploration of small roller bed conveyor design opens up possibilities for optimizing material handling in compact spaces and specialized applications. Small roller bed conveyors are designed with efficiency and flexibility in mind, catering to environments where space is at a premium or where specific handling requirements necessitate customized solutions. These conveyors often incorporate adjustable roller spacing and variable speed options, allowing for the precise control of material flow and accommodating a wide range of product sizes and shapes.
Integrating the principles of roller bed conveyor design into the planning and implementation of conveyor systems ensures that each component is perfectly suited to its intended application. Whether dealing with high-volume distribution centers, manufacturing plants, or specialized packaging facilities, understanding the essentials of roller bed conveyor design is key to developing efficient, reliable, and adaptable material handling solutions. This approach not only improves operational throughput but also enhances safety and reduces maintenance requirements, contributing to a more productive and cost-effective operation.
Advanced Calculations and Types of Rollers in Roller Bed Conveyor Design
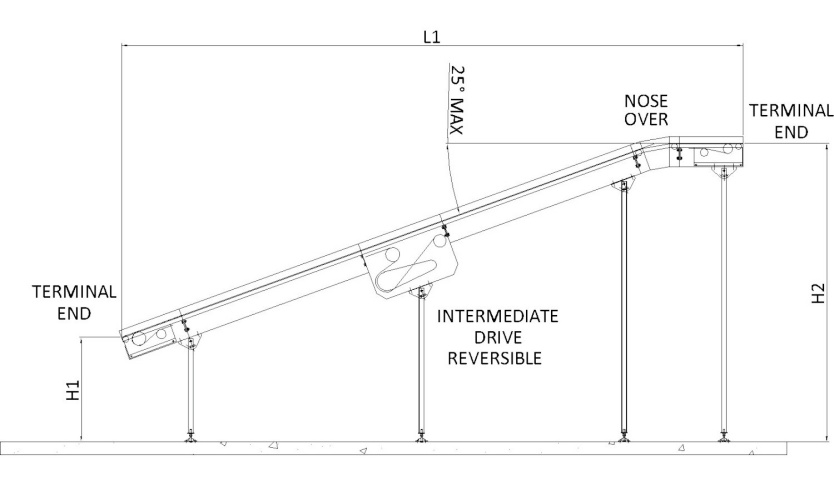
Delving deeper into the technical aspects of roller bed conveyor design, advanced calculations play a pivotal role in the precise engineering of these systems. Roller conveyor design calculations available for download are essential tools that enable engineers to tailor conveyor systems to the exact requirements of their operations. These calculations encompass a wide range of parameters, including load capacity, roller diameter, spacing, and speed requirements. By employing these detailed formulas, designers can ensure that their roller bed conveyor systems are optimized for both efficiency and durability, capable of handling the intended loads with minimal wear and tear.
In addition to these calculations, the selection of the appropriate types of rollers is fundamental to the performance and longevity of conveyor systems. Below is a detailed examination of the various types of rollers used in conveyor belts, highlighting their specific applications and benefits:
Each type of roller offers distinct advantages, making them suitable for specific tasks within a roller bed conveyor system. Steel rollers, for instance, are the go-to choice for heavy-duty applications where strength and durability are paramount. Gravity rollers, on the other hand, are ideal for lighter loads and can significantly reduce energy consumption by utilizing the force of gravity for movement. Tapered rollers are specifically designed for curved sections, ensuring smooth transitions and maintaining the orientation of the conveyed items.
Understanding these advanced calculations and the characteristics of different roller types is essential for the effective design and implementation of roller bed conveyor systems. By leveraging this knowledge, engineers can create highly efficient, durable, and tailored conveyor solutions that meet the unique demands of their operations, thereby enhancing productivity and operational efficiency.
Purpose of Roller Bed Conveyors
Efficient Material Movement
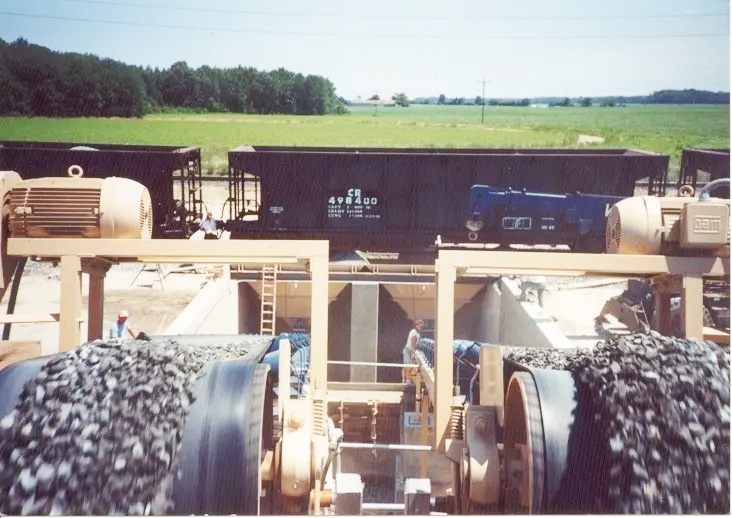
- Transport of Heavy Loads:
- Roller bed conveyors are specifically designed to transport heavier loads compared to other conveyor types. The rollers reduce friction, allowing for smoother movement of large and bulky items, which might be too heavy or irregularly shaped for other conveyor systems.
- Reduction of Belt Friction:
- By using rollers to support the belt, roller bed conveyors significantly reduce the friction between the belt and the conveyor frame. This not only facilitates the movement of heavy loads but also extends the lifespan of the conveyor belt by minimizing wear and tear.
- Handling Irregular Items:
- The design of roller bed conveyors makes them ideal for handling items with irregular bottoms or those that are too small to be supported on roller conveyors. The belt over the rollers provides a continuous surface, ensuring stability and consistent movement of varied products.
Versatility in Applications
- Assembly Lines:
- Roller bed conveyors are commonly used in assembly line operations where products need to be transported between different stages of assembly. Their ability to handle various load sizes and types makes them versatile for different manufacturing processes.
- Inspection and Sorting:
- In inspection and sorting applications, roller bed conveyors provide a stable platform for detailed examination of products. This is crucial in quality control processes where products are checked for defects or sorted based on specific criteria.
- Packaging and Shipping:
- These conveyors are also used extensively in packaging and shipping operations. They facilitate the efficient movement of packed goods from the production area to the storage or shipping area, ensuring timely and organized dispatch of products.
Enhanced Operational Efficiency
- Continuous Flow:
- Roller bed conveyors support a continuous flow of materials, which is essential for maintaining high productivity levels in various industrial processes. The reduction in manual handling and intervention leads to smoother operations and fewer disruptions.
- Energy Efficiency:
- The reduced friction in roller bed conveyors not only protects the conveyor components but also contributes to energy savings. Less power is required to move the belt and the load, making these conveyors an energy-efficient choice for heavy-duty applications.
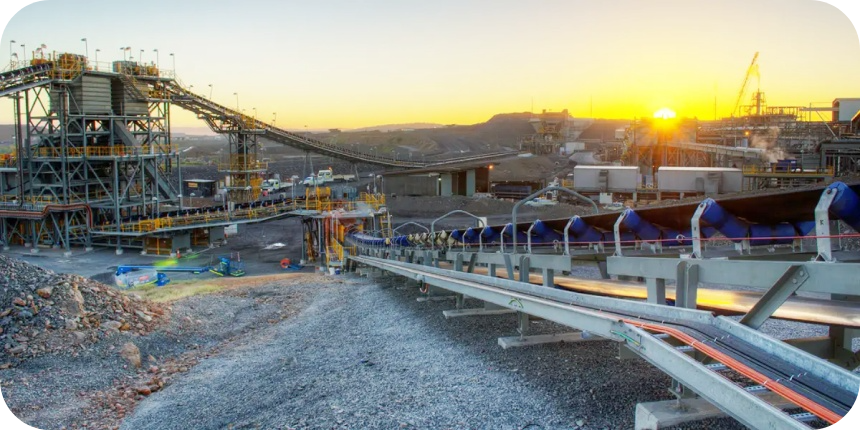
Enhancing Efficiency with Gravity Roller Conveyors in Roller Bed Conveyor Design
Integrating gravity roller conveyors into roller bed conveyor design is a strategic approach to enhance operational efficiency and sustainability. The principles of gravity roller conveyor design leverage the natural force of gravity to facilitate the movement of goods, minimizing the need for external power sources. This energy-efficient operation is not only cost-effective but also reduces the environmental footprint of material handling processes. Here are 10 advantages of incorporating gravity roller conveyors into roller bed conveyor design:
- Energy Efficiency: Gravity roller conveyors require no electricity for movement, significantly reducing energy consumption and operational costs.
- Low Maintenance: With fewer moving parts than motorized conveyors, gravity roller systems are less prone to breakdowns, resulting in lower maintenance requirements.
- Ease of Installation: These conveyors can be easily installed and integrated into existing conveyor systems, offering flexibility in setup and layout design.
- Scalability: Gravity roller conveyors can be expanded or reconfigured as operational needs change, making them a versatile solution for growing businesses.
- Simplicity: The simple design of gravity roller conveyors makes them easy to operate and maintain, reducing the need for specialized training.
- Noise Reduction: Operating without motors or electronic components, gravity roller conveyors produce less noise, contributing to a quieter work environment.
- Durability: Designed for longevity, gravity roller conveyors are built to withstand the rigors of daily use, even in high-volume settings.
- Safety: The passive movement mechanism of gravity conveyors minimizes the risk of injury, enhancing workplace safety.
- Versatility: Capable of handling a wide range of product sizes and weights, gravity roller conveyors are suitable for various industries and applications.
- Environmental Impact: By reducing energy consumption, gravity roller conveyors offer a more sustainable option for material handling, aligning with eco-friendly business practices.
Incorporating gravity roller conveyors into the design of roller bed conveyor systems not only improves energy efficiency but also offers numerous operational benefits. From reducing operational costs to enhancing safety and flexibility, gravity roller conveyors represent a smart investment for businesses looking to optimize their material handling processes. As part of a comprehensive roller bed conveyor design strategy, these systems play a crucial role in achieving efficient, sustainable, and cost-effective operations.
Selection and Manufacturing of Conveyor Rollers in Roller Bed Conveyor Design
The selection and manufacturing of conveyor rollers are critical components in the overall success of roller bed conveyor design. These elements directly influence the efficiency, durability, and reliability of the conveyor system. Here we present 8 guidelines on choosing the right conveyor roller manufacturer and an overview of the roller manufacturing process, highlighting its 10 impacts on conveyor efficiency and durability.
Choosing the Right Conveyor Roller Manufacturer
- Experience and Reputation: Look for manufacturers with a proven track record and strong reputation in the industry for quality and reliability.
- Product Quality: Ensure the manufacturer adheres to high-quality standards in their products, using durable materials and precise engineering.
- Customization Capabilities: Choose a manufacturer that offers customization options to tailor rollers to specific needs of your roller bed conveyor design.
- Technical Support: Select manufacturers that provide excellent technical support and customer service, offering guidance from design to implementation.
- Lead Times: Consider the manufacturer’s ability to meet your timelines, ensuring they can deliver products within your project schedule.
- Cost-Effectiveness: Evaluate the cost relative to the quality and durability of the rollers, seeking the best value for your investment.
- Innovative Solutions: Look for manufacturers that invest in research and development to offer innovative solutions that enhance conveyor efficiency and functionality.
- After-Sales Service: Ensure the manufacturer offers reliable after-sales service, including maintenance and replacement parts.
Roller Manufacturing Process and Its Impact
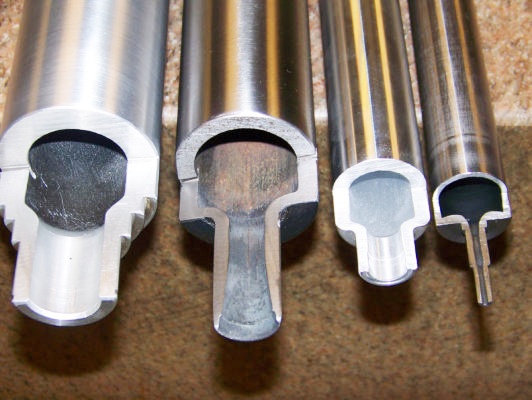
The manufacturing process of conveyor rollers plays a pivotal role in determining the overall efficiency and longevity of a roller bed conveyor system. Here are 10 impacts of this process:
- Material Selection: High-quality materials ensure the durability and wear resistance of rollers, directly impacting the conveyor’s lifespan.
- Precision Engineering: Precise dimensions and tolerances improve roller performance and reduce the risk of malfunctions, enhancing system reliability.
- Surface Treatment: Treatments like galvanizing or coating protect rollers from corrosion and abrasion, extending their service life.
- Bearing Quality: High-grade bearings reduce friction and noise, contributing to smoother operation and lower maintenance needs.
- Balancing: Properly balanced rollers ensure uniform distribution of loads, preventing uneven wear and extending conveyor belt life.
- Quality Control: Rigorous quality control measures throughout the manufacturing process guarantee the consistency and reliability of the final product.
- Innovative Designs: Adoption of innovative roller designs can significantly reduce energy consumption and increase efficiency.
- Eco-Friendly Manufacturing: Environmentally sustainable manufacturing processes minimize the ecological footprint of producing conveyor rollers.
- Customization: Custom-manufactured rollers tailored to specific operational requirements can optimize performance and efficiency.
- Testing and Validation: Comprehensive testing ensures rollers meet stringent performance standards, ready for the demands of operational environments.
Incorporating these considerations into the selection and manufacturing of conveyor rollers ensures that the roller bed conveyor design not only meets the current needs of material handling operations but also adapts to future challenges, optimizing both efficiency and durability.
Application Scope of Roller Conveyors in Roller Bed Conveyor Design
The versatility and efficiency of roller bed conveyor design have led to its widespread application across a multitude of industries. Each sector leverages these systems to meet unique logistical and manufacturing needs, showcasing the adaptability of roller conveyors. Below, we explore six case studies that highlight the extensive application scope of roller conveyors, followed by a comparative analysis of flat belt conveyors versus roller conveyors in various operational settings.
Case Studies Across Industries
- E-Commerce Fulfillment Centers: In the fast-paced world of e-commerce, roller conveyors streamline the sorting, packaging, and shipping processes. They facilitate rapid movement and sorting of packages, directly impacting delivery times.
- Automotive Manufacturing: Roller conveyors are integral in assembly lines, where they transport parts and assemblies between workstations with precision and efficiency, contributing to the streamlined production of vehicles.
- Food and Beverage Industry: Utilizing stainless steel and plastic roller conveyors for hygiene and easy cleaning, these systems move products through processing and packaging with minimal contact, ensuring food safety standards are met.
- Pharmaceuticals: In the highly regulated pharmaceutical industry, roller conveyors handle sensitive products through production lines, where contamination control and precision are paramount.
- Logistics and Distribution: Roller conveyors facilitate the movement of goods in warehouses and distribution centers, optimizing space usage and improving inventory management through automated sorting and stacking.
- Agriculture and Farming Equipment: Durable, heavy-duty roller conveyors are used to move large and heavy agricultural products or equipment, showcasing the system’s capability to handle varied weights and sizes.
Flat Belt Conveyors vs. Roller Conveyors
Flat Belt Conveyors:
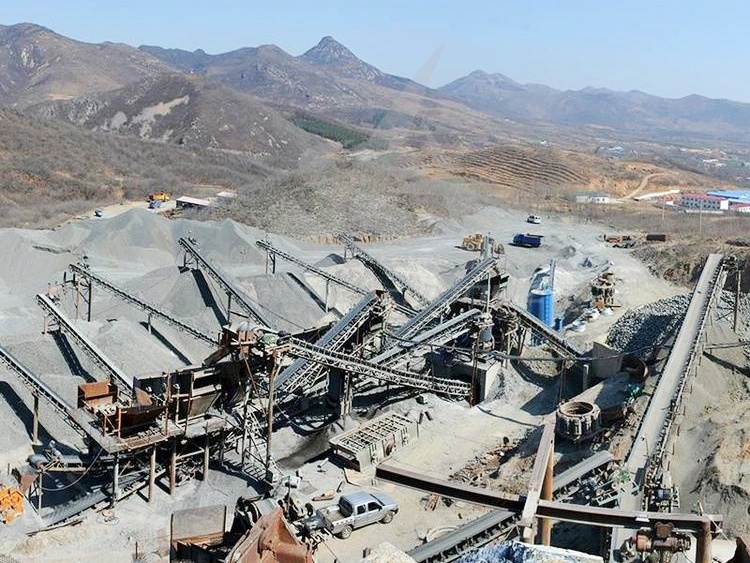
- Pros: Provide a continuous flat surface for products, ideal for delicate items or those requiring stable support. They can move items of varied sizes efficiently and are typically quieter than roller conveyors.
- Cons: Higher maintenance requirements due to wear and tear on the belt. Less effective in gravity-driven applications due to the need for power at all times.
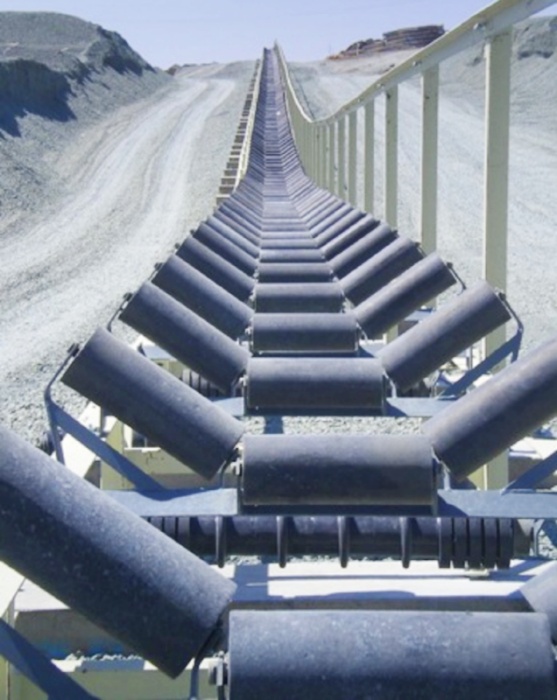
- Pros: Highly efficient for items with rigid bottoms, allowing for accumulation and automated sorting. Gravity roller conveyors reduce power requirements, lowering operational costs. Roller conveyors are also more adaptable to irregularly shaped items.
- Cons: May not be suitable for items that require a flat surface for stability during transport. Noise levels can be higher compared to flat belt conveyors.
In various operational settings, the choice between flat belt conveyors and roller conveyors in roller bed conveyor design depends on the specific requirements of the application, including the nature of the items being transported, the desired speed and efficiency of the system, and the operational costs associated with maintenance and power consumption. Roller conveyors offer unparalleled versatility and efficiency in many scenarios, making them a cornerstone of modern material handling and manufacturing processes.
The Role of Rollers in Belt Conveyor Systems in Roller Bed Conveyor Design
The incorporation of rollers in belt conveyor systems is a fundamental aspect of roller bed conveyor design, significantly contributing to their overall functionality and efficiency. Rollers play a myriad of crucial roles within these systems, each enhancing the conveyor’s operation and the handling of materials. Here are ten key contributions of rollers to the efficiency and functionality of belt conveyor systems:
- Reducing Friction: Rollers decrease the friction between the conveyor belt and the surface it moves over, which reduces wear on the belt and energy consumption, leading to longer belt life and lower operational costs.
- Supporting the Belt: They provide essential support to the conveyor belt, ensuring it remains in a stable and flat position, which is crucial for the smooth transportation of materials.
- Facilitating Movement: The rotation of rollers allows for the effortless movement of goods along the conveyor, enhancing the speed and efficiency of material handling.
- Handling Heavy Loads: Heavy-duty rollers are designed to support and transport large and heavy items, expanding the capability of conveyor systems to handle a wide range of product weights.
- Improving Conveyor Belt Alignment: Rollers play a critical role in maintaining the alignment of the conveyor belt, preventing it from drifting off course and reducing the risk of damage or spillage.
- Enabling Accumulation: Certain types of rollers, such as zero-pressure accumulation rollers, allow products to accumulate on the conveyor without touching, preventing damage to sensitive items.
- Facilitating Speed Control: The spacing and type of rollers can be adjusted to control the speed at which items move, allowing for a customizable flow of materials through the system.
- Adapting to Various Environments: Rollers are available in different materials, such as plastic, steel, or coated with rubber, making them suitable for a variety of environmental conditions, including those requiring resistance to corrosion, heat, or impact.
- Reducing Operational Noise: Modern roller designs focus on minimizing noise, contributing to a more pleasant and safer working environment.
- Enhancing Durability and Reliability: The design and material quality of rollers affect the durability and reliability of the conveyor system. High-quality rollers reduce the need for frequent maintenance and replacement, ensuring continuous operation.
Get a quote for high-quality conveyor rollers today!
Rollers are, without a doubt, the backbone of belt conveyor systems in roller bed conveyor design, offering a versatile and efficient means of transporting goods across various industries. Their role extends beyond mere transportation; they enhance the operational efficiency, safety, and reliability of conveyor systems, making them an indispensable component in the material handling sector. By understanding the multifaceted contributions of rollers, designers and operators can optimize their conveyor systems for peak performance and longevity.
FAQs about Roller Bed Conveyor Design
A roller bed conveyor is a type of conveyor system where the surface that supports the belt is made up of rollers rather than a flat pan. The rollers are typically spaced evenly across the width of the conveyor, and the belt sits on top of these cylindrical components as it moves. This design is especially suited for moving heavier loads or items over long distances because the rollers reduce friction and make it easier for the conveyor belt to glide with less resistance and power consumption. Roller bed conveyors are known for their durability and efficiency and are commonly used in a variety of industries such as logistics, manufacturing, and distribution.
The formula for a conveyor roller typically involves determining the roller spacing for the conveyor system. One of the key calculations is the “roller pitch,” which is the center-to-center distance between two rollers. This is crucial because it affects the conveyor’s ability to transport items smoothly. The pitch depends on the size and weight of the items being conveyed. For example, heavier items require rollers that are closer together to support the load adequately. A basic formula used for roller pitch (P) in relation to the load length (L) is P ≤ L/3, ensuring that there are always at least three rollers under the item being conveyed for support.
The structure of a roller conveyor typically consists of a series of rollers mounted within a frame. The key components of a roller conveyor structure include the conveyor frame, rollers, axle centers, and the drive mechanism. The conveyor frame is usually made from formed steel or aluminum that provides the structural support for the rollers. The rollers themselves can be made of metal, plastic, or rubber, each suited for different applications. Axle centers can be fixed or adjustable to change the distance between rollers. The drive mechanism varies depending on whether the conveyor is powered or gravity-fed, with powered conveyors using motors and belts to turn the rollers.
The standard size of a roller conveyor can vary greatly depending on the application and the manufacturer, but some common dimensions include roller diameters of 1.5 inches to 3.5 inches, and widths ranging from 12 inches to 36 inches. The length of a roller conveyor can be anywhere from a few feet to hundreds of feet, tailored to the needs of the specific installation. The size and spacing of rollers are often determined by the size and weight of the items to be transported, as well as the desired speed and efficiency of the system. Custom sizes are also frequently available to accommodate specific requirements of a material handling operation.
The spacing of roller conveyor rollers, also known as “pitch,” typically ranges from 1.5 to 12 inches, depending on the size and weight of the items being conveyed. The standard practice is to space the rollers at a distance equal to or less than one-third of the shortest item length to ensure smooth movement.
The angle of a roller conveyor, also known as the “incline angle,” can vary depending on the application, but typical angles range from 5° to 15°. The angle is chosen based on the gravity needed to move items smoothly without manual assistance.
Last Updated on June 21, 2024 by Jordan Smith
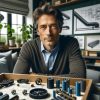
Jordan Smith, a seasoned professional with over 20 years of experience in the conveyor system industry. Jordan’s expertise lies in providing comprehensive solutions for conveyor rollers, belts, and accessories, catering to a wide range of industrial needs. From initial design and configuration to installation and meticulous troubleshooting, Jordan is adept at handling all aspects of conveyor system management. Whether you’re looking to upgrade your production line with efficient conveyor belts, require custom conveyor rollers for specific operations, or need expert advice on selecting the right conveyor accessories for your facility, Jordan is your reliable consultant. For any inquiries or assistance with conveyor system optimization, Jordan is available to share his wealth of knowledge and experience. Feel free to reach out at any time for professional guidance on all matters related to conveyor rollers, belts, and accessories.