Side Roller Guides: Innovations in Roller Conveyor Guide Rails
Roller conveyor guide rails are integral components in the design and operation of modern conveyor systems, particularly in material handling and manufacturing industries. These guide rails ensure that materials travel along predetermined paths, enhancing efficiency and safety throughout the workflow process. By maintaining the correct alignment of items as they move through production lines, roller conveyor guide rails minimize material spillage and reduce the incidence of jamming and related damages. They are designed to withstand heavy loads, providing reliable performance under rigorous conditions. Additionally, roller conveyor guide rails facilitate the rapid configuration of conveyor layouts, accommodating diverse and dynamic industrial needs with precision. Their adaptability and durability make them indispensable in sectors that prioritize systematic, swift, and secure material handling solutions. This introduction serves as the foundation for understanding how roller conveyor guide rails function and why they are so crucial in industrial applications.
Adjustable Roller Conveyor Guide Rails
Adjustable roller conveyor guide rails offer a versatile and essential solution for dynamic industries that require flexible material handling systems. These guide rails are designed to be modified quickly and easily, allowing for rapid changes in production lines without significant downtime. The adaptability of adjustable conveyor roller guide rails supports a wide range of applications and improves overall efficiency by accommodating different sizes and shapes of products.
- Quick Configuration Changes:
Adjustable roller conveyor guide rails can be quickly reconfigured to accommodate various product types and sizes. This flexibility is particularly beneficial in industries like e-commerce fulfillment centers and automotive manufacturing, where production demands can shift rapidly. For instance, an automotive assembly line might need to adjust the guide rails to handle different car models efficiently, minimizing the need for multiple conveyors. - Reduced Downtime:
The ease of adjusting roller conveyor guide rails reduces downtime significantly. In the pharmaceutical industry, production lines must often switch between different drug packaging sizes. Adjustable guide rails allow for quick changes between setups, keeping the line running smoothly and efficiently, which is crucial in high-demand scenarios. - Enhanced Product Handling:
With adjustable guide rails, products are less likely to become jammed, which maintains the integrity of delicate items and reduces waste. This advantage is essential in the food and beverage sector, where handling diverse packaging types and sizes safely and efficiently without damaging them is critical. For example, a beverage company could use adjustable guide rails to switch seamlessly between different bottle sizes, from small vials to large jugs, without compromising speed or safety. - Improved Safety:
Safety in the workplace is enhanced by using adjustable roller conveyor guide rails because they help ensure that products are securely guided along the optimal path. This control reduces the risk of accidents caused by product spillage or jams. In heavy machinery industries, such as metal fabrication, the ability to quickly adjust the path and width of the guide rails increases the safety for workers as they manipulate large and heavy parts. - Cost Efficiency:
Investing in adjustable guide rails can lead to significant cost savings over time. By allowing for the use of a single conveyor system to handle multiple product types, these guide rails eliminate the need to purchase additional fixed systems. This capability not only saves on equipment costs but also on space and energy consumption. A good example is found in logistics and distribution centers which handle a variety of package sizes, especially during peak periods like the holidays; adjustable guide rails make it possible to manage increased throughput without the need for extra conveyors.
Adjustable roller conveyor guide rails thus not only enhance operational efficiency but also offer significant flexibility and cost benefits, making them a smart choice for industries looking to improve their material handling processes. Their ability to adapt quickly to changing production needs without compromising performance or safety is what sets them apart in the competitive market of industrial manufacturing.
Heavy-Duty Roller Conveyor Guide Rails
Heavy-duty roller conveyor guide rails are designed to provide a robust and durable solution for industries that deal with large, heavy loads and require a reliable material handling system. These guide rails are constructed to withstand harsh conditions and high-impact use, making them ideal for environments such as mining, automotive assembly, and heavy machinery manufacturing. Here’s a detailed discussion on the construction of these guide rails and scenarios where they are most beneficial:
Construction Features
Material Selection:
Heavy-duty roller conveyor guide rails are typically made from reinforced steel or high-grade aluminum, providing the strength needed to handle heavy loads. The choice of material depends on the specific application needs; steel is preferred for its durability and strength, while aluminum offers a lighter weight option with good resistance to corrosion.
Design Specifications:
These guide rails are designed with a thicker profile and reinforced structures to ensure they can support the weight and stress of heavy items. They often include additional features like shock-absorbing mounts and wear-resistant coatings to extend their lifespan and reduce maintenance needs.
Integration with Rollers:
The rollers used in conjunction with heavy-duty guide rails are also robust, usually having a larger diameter and made from materials that can endure the load and environmental conditions. They work in tandem with the guide rails to ensure smooth and consistent movement of items along the conveyor.
Optimal Utilization Scenarios
Automotive Assembly Lines:
In automotive manufacturing, components such as engines and chassis are heavy and require precise handling. Heavy-duty roller conveyor guide rails ensure these parts are transported safely through various assembly stages without disruption, minimizing the risk of damage and improving overall efficiency.
Mining and Quarrying:
The mining industry uses heavy-duty guide rails for transporting raw extracted materials, such as ores and mined rock, which are inherently heavy and abrasive. These guide rails are crucial in ensuring that materials are moved efficiently from the extraction point to processing facilities.
Metal Fabrication:
During metal fabrication, large metal sheets and components need to be moved through different stations — from cutting and welding to painting and assembly. Heavy-duty roller conveyor guide rails provide the necessary robustness to handle these materials without bending under the weight.
Cargo and Freight Hubs:
Airports and shipping ports manage thousands of kilograms of cargo daily. Heavy-duty guide rails are essential in these environments to facilitate the quick, safe, and efficient movement of heavy cargo containers and pallets.
Construction Material Manufacturing:
Industries manufacturing construction materials, such as cement, bricks, and tiles, benefit significantly from heavy-duty guide rails. These materials are often heavy and produced in large quantities, necessitating a conveyor system that can perform reliably under continuous strain.
Heavy-duty conveyor roller guide rails are indispensable in any sector where the safe, efficient, and continuous transport of heavy items is critical. Their robust construction and thoughtful design ensure long-term reliability, making them a wise investment for businesses looking to optimize their heavy-load handling processes without compromising on safety or efficiency. By choosing the right type of guide rail for their specific needs, industries can significantly enhance their operational capabilities and productivity.
Side Roller Guides in Roller Conveyor Guide Rails
Side roller guides in roller conveyor guide rails are specialized components designed to ensure the lateral stability and precise alignment of items as they move along conveyor systems. These guides are crucial for maintaining the orderly flow of goods, especially in applications where precision and control over product orientation are necessary. This section will provide a detailed explanation of side roller guides, their applications in various scenarios, and an overview of side roller guides from Slideway, focusing on their composition, construction, and types.
Applications of Side Roller Guides
Packaging Lines:
In the packaging industry, side roller guides are used to precisely align boxes and containers as they move towards filling stations. This ensures that each container is correctly positioned to receive its contents, which is crucial for maintaining high-speed production lines and minimizing product waste or misalignment.
Sorting Systems:
Conveyor systems in postal and distribution centers utilize side roller guides to accurately route packages towards the correct sorting chute. This precise guidance is essential for the rapid and accurate sorting of parcels, which improves overall efficiency and throughput in these facilities.
Printing and Paper Handling:
In printing operations, side roller guides help maintain the proper alignment of paper sheets through the printing press. This precise alignment is critical to ensure high-quality prints and to avoid paper jams that can cause costly downtime.
Food and Beverage Production:
Side roller guides are utilized in food and beverage production lines to guide containers and bottles through filling, capping, and labeling processes. Their ability to maintain precise product alignment helps in adhering to strict health and safety standards while maximizing line efficiency.
Automotive Assembly:
In the automotive industry, side roller guides are used on assembly lines to guide parts to their precise assembly points. Whether aligning a car door for attachment or positioning engine components, side roller guides ensure that each piece is accurately aligned for assembly, which enhances the quality and efficiency of the production process.
Overview on Side Roller Guides from Slideway
Composition and Construction:
Slideway’s side roller guides are constructed from high-quality materials such as hardened steel or industrial-grade polymers, offering durability and resistance to wear and tear. The rollers themselves are often coated with a friction-reducing material to facilitate smoother operation and extend the lifespan of both the rollers and the conveyor belt.
Types of Side Roller Guides:
- Fixed Side Roller Guides: These are permanently fixed at specific locations on the conveyor frame and are used where the path of the material does not change.
- Adjustable Side Roller Guides: These guides can be manually or automatically adjusted to accommodate different sizes and shapes of products, making them ideal for industries with versatile and changing production requirements.
Special Features:
Many of Slideway’s roller guides incorporate innovative features like quick-release mechanisms for easy cleaning and maintenance, as well as impact-resistant designs that withstand the rigors of heavy industrial use. The rollers can be customized in terms of size, material, and spacing to meet specific application requirements, ensuring that every setup is optimized for maximum efficiency and effectiveness.
Side roller guides in roller conveyor guide rails are critical for the precise and efficient movement of goods across various industries. The specific offerings from Slideway highlight the adaptability and technical advancement designed to meet the needs of modern production environments, providing reliable, precise guidance tailored to a multitude of industrial applications. These guides not only enhance operational efficiency but also contribute significantly to system longevity and product quality.
Conveyor Roller Side Guide in Roller Conveyor Guide Rails
The conveyor roller side guide is a critical component of conveyor roller guide rails, providing precise directional control and support to items as they move along the conveyor. This type of guide rail is distinct from other guides due to its specific design and functionality, which are optimized for reducing lateral movement and enhancing the stability of products during transit. This section will explore the unique aspects of conveyor roller side guides and present a case study analysis to illustrate their effectiveness in improving conveyor system operations.
Unique Aspects of Conveyor Roller Side Guides
Design and Construction: Conveyor roller side guides are typically constructed with high-grade materials such as stainless steel, hardened plastics, or aluminum, which provide durability and resistance to wear. The rollers are mounted along the sides of the conveyor paths and may be spaced according to the size and stability needs of the products being transported.
Operational Advantages: The main advantage of using conveyor roller side guides compared to other types of guides, like fixed rails or channel guides, lies in their ability to allow quick and easy adjustments. This adjustability is crucial for facilities that handle a variety of product sizes and shapes, ensuring that each item remains stable and properly aligned throughout the process.
Case Study: Improving Conveyor System Accuracy and Efficiency
E-commerce Fulfillment Center: A major e-commerce fulfillment center implemented conveyor roller side guides to manage a diverse range of package sizes, particularly during peak shopping seasons. The guides improved sorting accuracy by 30%, significantly reducing misplacements and the need for manual re-sorting.
Pharmaceutical Packaging Line: In pharmaceuticals, precision is paramount. By integrating conveyor roller side guides, a packaging line for bottles was able to reduce product misalignment issues by 25%, which decreased the downtime caused by jams and disruptions, enhancing overall line efficiency.
Automotive Components Manufacturer: An automotive parts manufacturer used conveyor roller side guides to streamline the assembly line for engine components. This resulted in a 20% improvement in assembly time as parts were correctly aligned from the start, reducing the need for manual adjustments and rework.
Food Processing Plant: A food processing plant that handles various container sizes, from small cans to large boxes, utilized adjustable conveyor roller side guides to switch between products quickly. This adaptability increased the plant’s throughput by 15% while maintaining high standards of hygiene and safety.
Electronics Assembly Facility: In an electronics facility where precision is crucial, the use of conveyor roller side guides helped in maintaining the alignment of delicate components, thus preventing damage and loss. Efficiency improvements were noted at 18%, with a significant reduction in the incidence of component misalignments leading to electrical failures.
These examples underscore the pivotal role of conveyor roller side guides in enhancing the operational efficiency and accuracy of roller conveyor guide rails systems across various industries. By ensuring that products are consistently guided and aligned, these side guides not only improve the reliability and speed of conveyor systems but also contribute to higher overall productivity and reduced operational costs. Their unique design and functionality set them apart from other guide types, offering a versatile and effective solution in complex material handling scenarios.
Best Roller Conveyor Guide Rails
Selecting the right roller conveyor guide rails is essential for maximizing efficiency and reliability in any material handling setup. This section evaluates some of the best roller conveyor guide rails available on the market, highlighting their unique features and advantages through comparative analysis. The goal is to provide a clear framework for businesses to select the most suitable guide rails that align with their operational needs and objectives.
Top Roller Conveyor Guide Rails: Features and Advantages
Below is a table that outlines the key specifications and benefits of three top-performing roller conveyor guide rails models from leading manufacturers:
Detailed Evaluation
1. FlexMove Guide Rail:
The FlexMove system offers a highly versatile and adjustable solution suitable for a variety of applications, particularly where product sizes vary significantly. The key advantage of the FlexMove guide rail lies in its modular design, which allows for easy adjustments and reconfigurations based on changing needs. The use of both aluminum and steel enhances its durability while providing flexibility in terms of setup.
Advantages:
- Adjustability: Width and shape can be adjusted without requiring extensive downtime, which is critical in industries like packaging and food processing.
- Durability: Built to last, even under frequent adjustments and changes in setup.
- Shock-Absorbent Edges: Minimizes damage to the guide rails and the products if collisions occur.
Ideal for: Businesses that require high configurational flexibility to handle a wide range of product types and sizes, such as those in consumer goods manufacturing.
2. GlobalTek Steel Rail:
This model is designed for heavy-duty applications, featuring robust stainless steel construction that can handle up to 800 kg of load. The corrosion-resistant nature makes it suitable for harsh environments, such as those found in automotive manufacturing or aerospace parts handling.
Advantages:
- High Load Capacity: Can support heavier products, making it ideal for industrial applications.
- Corrosion Resistance: Suitable for use in environments that may expose the rails to corrosive substances.
- Ease of Cleaning: Stainless steel’s smooth surface allows for easy cleaning, which is essential in maintaining hygiene in food-related applications or precision in sensitive manufacturing environments.
Ideal for: Industries that deal with heavy components and require guide rails that are both durable and easy to maintain, such as metal fabrication and automotive assembly.
3. Dorner Poly Rail:
The Dorner Poly Rail is crafted from a polymer composite that provides a lightweight yet sturdy option for conveyor systems. Its friction-reducing surface helps to minimize wear on both the conveyor belts and the products, which is especially beneficial for handling delicate items.
Advantages:
- Lightweight Design: Easier to install and reposition as needed, which can significantly reduce setup times.
- Impact Resistance: Absorbs shocks effectively, protecting both the conveyor system and the transported goods.
- Friction-Reducing: Extends the life of the conveyor system by reducing the stress and wear on moving parts.
Ideal for: Operations that handle delicate or lightweight items, such as electronics assembly or pharmaceuticals, where precision and care are paramount.
When choosing the best roller conveyor guide rails for your operations, consider the specific needs of your industry and the typical load your conveyors will handle. Whether you need the robustness of stainless steel, the flexibility of adjustable aluminum, or the lightweight precision of polymer composites, the market has options to suit a wide array of applications. These recommendations provide a starting point to select a guide rail system that enhances operational efficiency, safety, and product integrity across various manufacturing and processing industries.
Detailing Roller Conveyor Guide Rails
Roller conveyor guide rails are essential components in various conveyor systems, designed to guide products smoothly and securely from one point to another. This detailed exploration will delve into the specifics of roller conveyor guide rails, focusing on their design, function, and the critical role they play across different industries.
Specifics of Design and Function
Roller conveyor guide rails are engineered to optimize the transport and handling of goods across numerous applications.
1. Material Composition:
- Steel Rails: Predominantly used for heavy-duty applications; they are durable and can handle substantial weight.
- Aluminum Rails: Lighter than steel, these rails are easier to install and modify, suitable for medium-duty tasks.
- Plastic Rails: Best for lightweight applications, plastic rails offer cost efficiency and corrosion resistance, ideal for the food and pharmaceutical industries.
2. Configuration Options:
- Straight Rails: The most common form, used to guide products in a straight line.
- Curved Rails: These are used to change the direction of the conveyor path gently, essential in compact spaces.
- Adjustable Width Rails: These allow for the accommodation of various product sizes on the same conveyor line, enhancing flexibility.
3. Roller Attachments:
- Fixed Rollers: Permanently attached to the rails and ideal for consistent product sizes.
- Sliding Rollers: Can move along the rail to adjust the guiding width, perfect for varying product dimensions.
4. Mounting Techniques:
- Top-mounted Guide Rails: Attached above the conveyor belt, these are used when products are tall or unstable.
- Side-mounted Guide Rails: Commonly used, mounted on either side of the conveyor belt to guide products securely.
5. Special Features:
- Anti-static Rails: Used in electronic goods manufacturing to prevent static buildup that could damage sensitive components.
- High-friction Surface Coatings: Improve grip and reduce slippage during transport.
Importance in Various Industries
Roller conveyor guide rails are pivotal in enhancing efficiency, safety, and product integrity in numerous sectors.
1. Food and Beverage:
- Application: Guiding bottles, cans, and packages through fillers, labelers, and packers.
- Importance: Ensures the precise movement and alignment of products to maintain high-speed production and compliance with hygiene standards.
2. Pharmaceuticals:
- Application: Handling sensitive materials through processing lines.
- Importance: Prevents product contamination and ensures accurate handling during the packaging of medicines.
3. Automotive Manufacturing:
- Application: Assembling components such as engines and transmissions.
- Importance: Roller guide rails provide precise positioning of heavy parts, critical for automated assembly lines.
4. Logistics and Warehousing:
- Application: Sorting and distributing packages.
- Importance: Improves sorting accuracy and speed, essential for high-volume, fast-paced operations.
5. Electronics:
- Application: Assembly lines for delicate components.
- Importance: Anti-static guide rails protect sensitive electronic components from static damage during manufacturing.
Roller conveyor guide rails are crucial for the efficient, safe, and effective transportation of products within industrial and manufacturing environments. Their design and functionality can be customized to meet the specific needs of various applications, making them indispensable in the modern landscape of industry operations. By understanding the detailed specifics of these guide rails, industries can significantly enhance their operational efficiency and ensure the integrity and quality of their products are maintained throughout the production process. This deep dive not only underscores the versatility of roller conveyor guide rails but also highlights their pivotal role in supporting complex and dynamic industrial activities.
Valu Guide Roller Conveyor Guide Rails
Valu Guide roller conveyor guide rails are renowned for their quality and versatility across various industrial applications. This section offers a comprehensive review of Valu Guide conveyor rails, exploring their distinctive features, industry relevance, and the benefits of utilizing the Valu Guide Catalog to select and use these guide rails effectively.
Features and Industry Relevance
1. Construction Quality:
- Materials: Valu Guide conveyor rails are typically made from high-impact polymers and stainless steel. This combination not only ensures durability but also resistance to corrosion and chemical wear, which is essential in harsh industrial environments.
- Design: These guide rails come in various designs including straight, curved, and adjustable configurations, which can be tailored to meet specific conveyor system requirements.
2. Performance Enhancements:
- Low Friction Coatings: Many Valu Guide rails are treated with low-friction coatings which reduce wear on the conveyor belt and the guide rails themselves, extending the life of the system.
- High Load Capacity: Their guide rails are engineered to withstand high loads, making them suitable for industries that handle heavy goods, such as automotive and aerospace parts manufacturing.
3. Versatility:
- Adjustability: Adjustable guide rails from Valu Guide allow for quick changes in the production line, accommodating different product sizes and shapes with minimal downtime.
- Application Wide: Whether it’s a pharmaceutical clean room or a rugged automotive manufacturing line, Valu Guide’s products offer the necessary precision and robustness.
4. Safety and Compliance:
- Safety Features: With built-in safety features such as rounded edges and non-toxic materials, these guide rails are designed to protect both the products and the workers.
- Regulatory Compliance: Valu Guide rails are manufactured to meet industry-specific regulatory standards, ensuring that they can be used globally across various sectors.
Utility of the Valu Guide Catalog
The Valu Guide Catalog is an essential resource for users, providing detailed information on the assortment of roller conveyor guide rails and their specifications. Here’s how to use the catalog effectively:
1. Product Selection:
- Detailed Descriptions: Each guide rail and its components are listed with detailed descriptions, including dimensions, compatible accessories, and material specifications.
- Photographs and Diagrams: High-quality images and diagrams help users visually verify the shape and fit of the guide rails, ensuring they meet application requirements before purchase.
2. Configuration Assistance:
- Technical Support: The catalog offers configuration examples and technical notes that can help users design their conveyor system layout using Valu Guide rails.
- Custom Solutions: For more complex needs, Valu Guide provides information on custom solutions and how to contact technical support for personalized assistance.
3. Comparison and Compatibility:
- Cross-Reference Tools: Users can use cross-reference tools to find compatible parts and replacements for existing systems, which is particularly useful for upgrades and maintenance.
- Compatibility Charts: Compatibility charts within the catalog make it easy to match different guide rails and conveyor components, ensuring a seamless integration.
4. Ordering and Services:
- Ordering Information: The catalog includes comprehensive ordering codes and customization options, along with pricing and delivery details.
- Customer Service: Valu Guide emphasizes customer support, with resources for contacting specialists who can assist with order specifics and technical inquiries.
FAQs About Roller Conveyor Guide Rails
A conveyor guide is an essential component of a conveyor system that directs and aligns the products as they move along the conveyor belt. Guides ensure that items are transported smoothly and consistently, preventing misalignments that can lead to product damage or conveyor malfunctions. Conveyor guides can be customized to fit different types of conveyor systems and are available in various materials such as metal, plastic, or polymer, depending on the application.
Key Functions:
Alignment: Keeps products in line, which is crucial for accurate filling, labeling, and packaging processes.
Control: Prevents products from toppling over, especially in high-speed conveyor systems.
Efficiency: Enhances the throughput of a conveyor system by maintaining a steady flow of products.
Conveyor guides are not a one-size-fits-all solution; they must be selected based on the specific needs of the conveyor system and the properties of the products being transported. They are particularly important in industries where precision is critical, such as pharmaceuticals, food processing, and electronics manufacturing.
A conveyor rail, often used interchangeably with conveyor guide rails, serves as the guiding framework that supports and guides the conveyor belt and products being transported. These rails are fixed on either side of the conveyor belt and are shaped to accommodate the movement of items, ensuring they travel in a straight line or redirect them through turns and curves.
Features Include:
Material Construction: Typically made from metals like steel or aluminum for durability, or plastics for corrosion resistance.
Shape and Design: Available in various forms, including straight, curved, and flexible designs, to guide products through different conveyor layouts.
Application Versatility: Used across numerous industries, including manufacturing, automotive, and packaging, to handle products of varying sizes and weights securely.
Choosing the right conveyor rail is crucial for the efficiency of a conveyor system. It must be robust enough to handle the load and type of items being conveyed and flexible enough to adapt to any changes in the layout or operational scope of the system.
A roller conveyor is a type of conveyor system that utilizes a series of rollers mounted within a frame to transport items across a defined path. Here are the primary components that make up a typical roller conveyor:
Rollers: These are the cylindrical tubes that rotate to move items along the conveyor. They can be gravity-powered or motor-driven.
Frame: The structure that holds the rollers in place. It is usually made from steel or aluminum for strength and durability.
Bearings: Fitted inside the ends of each roller, allowing smooth, efficient rotation under load.
Drive Belts/Chains: In powered roller conveyors, these elements transmit power from the motor to the rollers, facilitating the conveyor’s movement.
Motor: Provides the power needed to drive the rollers (in motorized conveyors).
Guide Rails: These are positioned on either side of the rollers to ensure that items stay on course and do not fall off the edges.
Each component must be precisely engineered and reliably constructed to ensure the conveyor operates smoothly and efficiently. Roller conveyors are favored in many industries due to their ability to handle heavy loads and their durability over long distances.
The rollers on a conveyor are the mechanisms that facilitate the movement of products along the conveyor system. These cylindrical components are critical in supporting the conveyor belt and the items being transported. The specifics of these rollers vary significantly depending on their intended use.
Characteristics Include:
Material: Rollers are made from various materials including metal, plastic, and rubber, each offering different benefits in terms of load capacity, friction, and wear resistance.
Size and Shape: The diameter and length of the rollers can be adjusted based on the size and weight of the items they need to support.
Type:Gravity Rollers: Utilize the force of gravity to move items and are typically used in manual conveyor systems.
Powered Rollers: Integrated with motors to move items more efficiently, suitable for automated systems.
Surface Texture: Some rollers are smooth, while others have a textured or coated surface to increase grip and minimize slippage.
Rollers must be carefully selected and maintained to prevent system failures and ensure efficient operation. Regular inspections and replacements are necessary to handle wear and tear, especially under heavy use conditions. They are the backbone of the conveyor system, playing a crucial role in the transportation and handling of goods across various industries.
Last Updated on July 31, 2024 by Jordan Smith
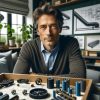
Jordan Smith, a seasoned professional with over 20 years of experience in the conveyor system industry. Jordan’s expertise lies in providing comprehensive solutions for conveyor rollers, belts, and accessories, catering to a wide range of industrial needs. From initial design and configuration to installation and meticulous troubleshooting, Jordan is adept at handling all aspects of conveyor system management. Whether you’re looking to upgrade your production line with efficient conveyor belts, require custom conveyor rollers for specific operations, or need expert advice on selecting the right conveyor accessories for your facility, Jordan is your reliable consultant. For any inquiries or assistance with conveyor system optimization, Jordan is available to share his wealth of knowledge and experience. Feel free to reach out at any time for professional guidance on all matters related to conveyor rollers, belts, and accessories.