Efficient Roller Conveyor Power Calculation: Methods and Models
Roller conveyor systems are a critical component in material handling, providing efficient transportation of goods across various industries. They consist of a series of rollers supported within a frame, powered by motors or gravity to move items along a path. The roller conveyor power calculation is essential to determine the required motor power and ensure the system operates smoothly and efficiently. Roller conveyors are commonly used in industries such as manufacturing, warehousing, distribution, and logistics, where they facilitate the movement of heavy loads, pallets, cartons, and other items. Understanding the roller conveyor power calculation helps in designing reliable and cost-effective conveyor systems tailored to specific operational needs.
What are Roller Conveyor Power Calculation
Why Power Calculation is Essential
Accurate roller conveyor power calculation is fundamental to the design and operation of conveyor systems. Here’s a detailed look at why this process is so crucial:
Ensuring Efficiency and Reliability
A key reason for conducting a roller conveyor power calculation is to ensure the system operates efficiently and reliably. Efficiency in a roller conveyor system means the conveyor uses the least amount of energy necessary to perform its tasks, thereby reducing operational costs and minimizing wear and tear on the system components. By calculating the exact power requirements, engineers can design systems that avoid unnecessary power consumption while maintaining the required performance levels.
Reliability is equally important. A reliable conveyor system consistently performs its intended functions without frequent breakdowns or interruptions. An accurate power calculation ensures that the conveyor is equipped with the right motor and drive components to handle the expected load and operational demands. This reliability translates to higher productivity, less downtime, and lower maintenance costs.
Preventing Overloading and Mechanical Failures
Overloading is a common cause of mechanical failures in conveyor systems. When a conveyor is overloaded, it places undue stress on the rollers, belts, motors, and other components, leading to premature wear and potential breakdowns. Conducting a roller conveyor power calculation helps in understanding the maximum load the system can handle and ensures that the components are selected based on these calculations.
By preventing overloading, the calculation helps extend the lifespan of the conveyor system. It also enhances safety by reducing the risk of failures that could result in accidents or damage to goods being transported. Overloading not only affects the mechanical components but can also lead to increased friction and heat, further accelerating wear and potentially causing thermal damage to the conveyor system.
Optimizing Energy Consumption and Operational Costs
Energy consumption is a significant factor in the operational costs of a conveyor system. An accurately performed roller conveyor power calculation helps optimize the energy usage by ensuring that the conveyor is neither underpowered nor overpowered. An underpowered system may struggle to move loads efficiently, leading to increased energy consumption and potential damage due to stalling. Conversely, an overpowered system wastes energy and may incur higher operational costs due to unnecessary power usage.
Optimizing energy consumption through precise power calculation not only reduces operational costs but also supports sustainability initiatives by lowering the carbon footprint of the conveyor system. Companies can achieve significant cost savings and contribute to environmental conservation by using energy more efficiently.
Detailed Steps in Power Calculation
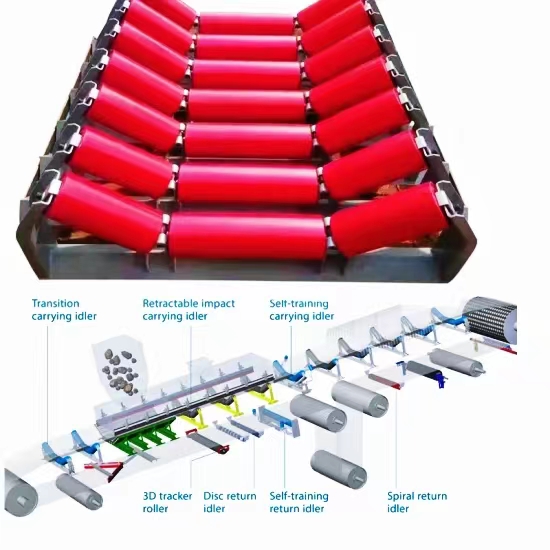
To understand how to perform a roller conveyor power calculation, it’s essential to delve into the specific steps involved in the process. Each step plays a critical role in determining the power requirements accurately.
Step 1: Assessing the Load
The first step in the roller conveyor power calculation is assessing the load that the conveyor will be moving. This involves determining the weight and size of the items being transported. The load assessment includes both the static load (the weight of the items when stationary) and the dynamic load (the additional forces exerted when the items are in motion).
In many cases, it’s also necessary to consider the distribution of the load. For instance, if the conveyor will transport items that are unevenly loaded or have varying weights, this variability must be factored into the calculation. Accurate load assessment ensures that the conveyor system is designed to handle the heaviest and most challenging loads it will encounter.
Step 2: Calculating the Effective Tension
The next step in the roller conveyor power calculation is calculating the effective tension, often referred to as Te. Effective tension is the tension required to overcome the frictional forces, the weight of the conveyor components, and any additional forces such as those caused by inclines or declines in the conveyor path.
The effective tension can be broken down into several components:
- Frictional Tension (Tf): This accounts for the resistance caused by the friction between the conveyor belt and the rollers or the sliding bed. Frictional tension is influenced by factors such as the type of conveyor belt, the material of the rollers, and the condition of the conveyor system.
- Gravity Tension (Tg): If the conveyor has an incline, the gravity tension accounts for the additional force required to lift the load against gravity. Conversely, for a decline, it represents the reduced force needed to lower the load.
- Acceleration Tension (Ta): When starting or stopping the conveyor, additional force is required to accelerate or decelerate the load. This component of the tension is crucial for conveyors that frequently start and stop or operate at varying speeds.
The effective tension is calculated using the following formula:
[ Te = Tf + Tg + Ta ]
Where:
- Te = Effective Tension
- Tf = Frictional Tension
- Tg = Gravity Tension
- Ta = Acceleration Tension
Step 3: Determining Motor Power Requirements
Once the effective tension (Te) has been calculated, the next step is to determine the motor power requirements. The power required to move the load on the conveyor is a function of the effective tension and the speed at which the conveyor operates. The basic formula for calculating the required motor power (P) is:
[ P = \frac{Te \times v}{\eta} ]
Where:
- P = Motor Power (in watts)
- Te = Effective Tension (in newtons)
- v = Conveyor speed (in meters per second)
- η = Efficiency of the motor and drive system (a dimensionless factor, typically ranging from 0.7 to 0.95)
The efficiency factor (η) accounts for losses in the motor and drive system, such as friction in the bearings, inefficiencies in the motor, and other mechanical losses. Selecting a high-efficiency motor and ensuring proper maintenance of the conveyor system can help improve this factor and reduce energy consumption.
In addition to the basic power calculation, it’s important to consider the starting torque of the motor. Conveyors often require a higher torque to start moving the load from a standstill compared to maintaining motion. The starting torque should be at least 150% to 200% of the running torque to ensure smooth operation.
Step 4: Selecting the Appropriate Motor and Drive Components
After calculating the required motor power, the next step in the roller conveyor power calculation is selecting the appropriate motor and drive components. This involves choosing a motor that can provide the required power and torque, as well as selecting compatible drive components such as gearboxes, chains, belts, and pulleys.
When selecting a motor, it’s important to consider factors such as:
- Motor Type: Different types of motors, such as AC motors, DC motors, and servo motors, have varying characteristics. The choice of motor depends on factors such as the desired speed control, torque characteristics, and cost.
- Power Rating: Ensure that the motor’s power rating matches or exceeds the calculated power requirement. It’s advisable to select a motor with a slightly higher power rating to provide a safety margin and account for any unforeseen increases in load or friction.
- Speed Control: Some conveyor systems require precise speed control to match the pace of other equipment in the production line. In such cases, motors with variable frequency drives (VFDs) or servo motors may be appropriate.
Drive components should be selected based on the calculated torque and the operational conditions of the conveyor system. Gearboxes should be chosen to provide the necessary reduction ratio and torque multiplication, while belts and chains should be rated for the expected loads and operating conditions.
Key Components in Roller Conveyor Power Calculation
Understanding the roller conveyor power calculation requires a thorough examination of the key components involved in the design and operation of roller conveyor systems. Each component plays a vital role in determining the overall power requirements and efficiency of the system.
Roller Conveyor Design Elements
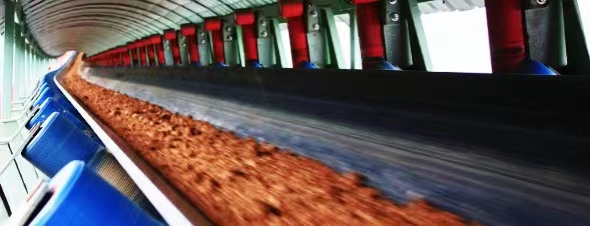
Description of Key Components
Rollers
Rollers are the central component of a roller conveyor system. They are cylindrical components that rotate to move the items placed on them. Rollers can be made from various materials, including steel, aluminum, and plastic, each chosen based on the application requirements such as load capacity, environmental conditions, and the type of goods being conveyed.
- Steel Rollers: Known for their durability and strength, steel rollers are suitable for heavy-duty applications where high loads are transported. They offer excellent wear resistance but can be susceptible to rust if not properly coated or maintained.
- Aluminum Rollers: Lighter than steel, aluminum rollers are often used in applications where weight is a concern. They offer good corrosion resistance and are suitable for transporting lighter loads.
- Plastic Rollers: Typically used in applications where corrosion resistance and lightweight properties are essential. Plastic conveyor rollers are ideal for food processing, pharmaceuticals, and other industries where hygiene is critical.
The diameter and length of the rollers are critical factors in the roller conveyor power calculation. Larger diameter rollers can handle higher loads and provide smoother motion, but they require more power to operate.
Drive Mechanisms
The drive mechanism is responsible for powering the rollers and ensuring the conveyor moves the items along the desired path. Various drive mechanisms can be used, including chain drives, belt drives, and direct drives.
- Chain Drives: Chain-driven rollers are connected by chains that transfer power from a motor to the rollers. This type of drive is robust and suitable for heavy loads. However, it requires regular maintenance to ensure the chains are properly lubricated and tensioned.
- Belt Drives: In a belt-driven conveyor, a belt wraps around the rollers and is driven by a motor. Belt drives provide smooth and quiet operation, making them suitable for lighter loads and applications where noise reduction is important.
- Direct Drives: Direct drive systems use motors directly connected to the rollers, eliminating the need for intermediary components like chains or belts. This setup offers high efficiency and low maintenance, making it ideal for precise applications.
The choice of drive mechanism significantly impacts the power calculation. Chain drives, for example, may introduce more friction and require additional power compared to belt or direct drives.
Frames
The frame of a roller conveyor system provides structural support and alignment for the rollers and drive mechanisms. Frames are typically made from steel, aluminum, or stainless steel roller, depending on the application and environmental conditions.
- Steel Frames: Offer high strength and durability, making them suitable for heavy-duty applications. However, they can be prone to corrosion if not properly coated.
- Aluminum Frames: Lightweight and corrosion-resistant, aluminum frames are ideal for applications where weight and corrosion are concerns.
- Stainless Steel Frames: Provide excellent corrosion resistance and are used in environments where hygiene and cleanliness are critical, such as food processing and pharmaceuticals.
The frame’s design and material influence the overall weight and rigidity of the conveyor system, which in turn affects the power required to move the system and the load.
Motors
The motor is the powerhouse of the conveyor system, providing the necessary energy to drive the rollers and move the load. Several factors need to be considered when selecting a motor for a roller conveyor, including power rating, speed, torque, and efficiency.
- Power Rating: The motor’s power rating must match or exceed the calculated power requirements to ensure the system operates effectively. Underpowered motors can lead to inefficiencies and potential mechanical failures.
- Speed: The motor speed should align with the desired conveyor speed. Variable speed motors or those with adjustable speed controls are often preferred for applications requiring flexibility in conveyor speed.
- Torque: Sufficient torque is necessary to start the conveyor and move the load, especially in systems with high starting inertia or frequent start-stop cycles.
- Efficiency: High-efficiency motors reduce energy consumption and operational costs. Motors with a high efficiency rating are particularly beneficial in systems that run continuously or under heavy loads.
The selection of the motor is directly influenced by the power calculation, ensuring that the motor can handle the expected load and operating conditions without excessive energy consumption or wear.
Importance of Each Component in Power Calculation
Each of the key components described above plays a crucial role in the roller conveyor power calculation. Let’s explore how each component impacts the overall power requirements and efficiency of the conveyor system.
Rollers and Their Impact
The size, material, and configuration of the rollers significantly affect the power calculation. Larger rollers, while capable of handling higher loads, require more power to rotate due to increased inertia. The material of the rollers influences the friction coefficient between the rollers and the items being conveyed, which in turn affects the power needed to overcome this friction.
In systems with multiple rollers, the spacing and alignment of the rollers can also impact the power requirements. Proper alignment and spacing ensure smooth movement of items, reducing unnecessary friction and power consumption.
Drive Mechanisms and Their Impact
The choice of drive mechanism—whether chain, belt, or direct drive—directly influences the efficiency and power requirements of the conveyor system. Chain drives, for example, introduce additional friction due to the interaction between the chain and the sprockets, requiring more power to maintain smooth operation. Belt drives, while offering quieter and smoother operation, may also have frictional losses that need to be considered in the power calculation.
Direct drives are often the most efficient, as they eliminate intermediary components and directly transfer power from the motor to the rollers. However, the selection of the drive mechanism should consider the specific application requirements, including load capacity, operational environment, and maintenance considerations.
Frames and Their Impact
The frame’s material and design impact the overall weight and rigidity of the conveyor system. A heavier frame adds to the total weight that the motor needs to move, increasing the power requirements. Conversely, a lighter frame reduces the load on the motor but may compromise structural integrity if not designed correctly.
The rigidity of the frame ensures proper alignment of the rollers and drive mechanisms, reducing potential sources of friction and misalignment that can increase power consumption. Therefore, the frame’s design and conveyor belt material selection are integral to an accurate power calculation.
Motors and Their Impact
The motor is the final component that drives the system, and its selection is critical to achieving the desired performance and efficiency. The power rating of the motor must be based on the effective tension and speed calculated during the power calculation process. An undersized motor may struggle to move the load, leading to inefficiencies and potential mechanical failures. On the other hand, an oversized motor consumes more energy than necessary, increasing operational costs.
Variable speed motors offer flexibility, allowing the conveyor speed to be adjusted according to the load and operational requirements. This flexibility can optimize energy consumption and improve the overall efficiency of the system. High-efficiency motors reduce energy losses and operational costs, making them a preferred choice for continuous or heavy-duty operations.
Integrating Components into the Power Calculation
To perform an accurate roller conveyor power calculation, it is essential to consider the interplay between the different components. The following steps outline how to integrate these components into the calculation process:
Step 1: Assessing the Load
As mentioned earlier, the first step involves assessing the load that the conveyor will handle. This includes determining the weight, size, and distribution of the items being conveyed. Accurate load assessment ensures that the rollers and drive mechanisms are designed to handle the expected load without overloading.
Step 2: Calculating Effective Tension
The effective tension (Te) is calculated by considering the frictional, gravitational, and acceleration components. This calculation requires detailed information about the rollers, including their size, material, and configuration, as well as the drive mechanism and frame design.
Step 3: Determining Motor Power Requirements
The motor power requirements are determined based on the effective tension and the conveyor speed. This step involves selecting a motor with the appropriate power rating, speed, and torque to ensure the system operates efficiently and reliably.
Step 4: Selecting Drive Components
Based on the power calculation, the appropriate drive components—chains, belts, or direct drives—are selected. This selection considers the efficiency, maintenance requirements, and operational conditions of the conveyor system.
Step 5: Verifying and Optimizing the Design
The final step involves verifying the power calculation and optimizing the design to ensure all components work together harmoniously. This step includes checking the alignment of the rollers, ensuring proper tensioning of the drive mechanisms, and selecting a motor with a suitable efficiency rating.
Roller Conveyor Power Calculation Methods
Understanding the different methods for calculating power requirements for roller conveyors is crucial for designing efficient and reliable systems. The roller conveyor power calculation can be performed manually or using automated tools, each with its own set of advantages and procedures. This section provides a detailed look at both methods to help you choose the best approach for your needs.
Manual Calculation Methods
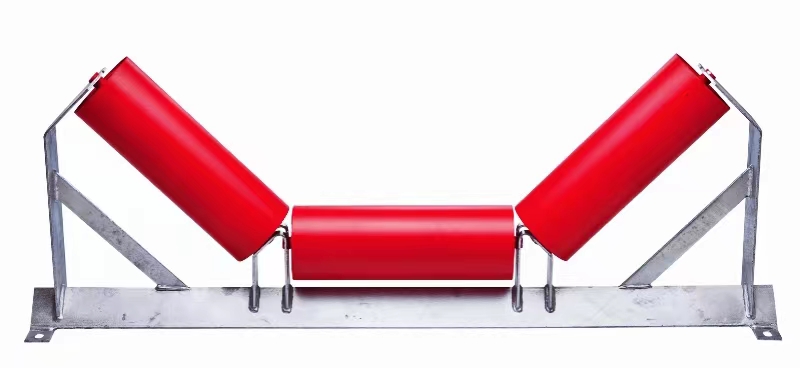
Manual calculation methods for roller conveyor power calculation involve a step-by-step approach to determine the power requirements based on the specific parameters of your conveyor system. Calculate the required linear force for your payload by considering the starting acceleration, conveyor incline, and using manual methods for roller conveyor power calculation. Here’s a detailed guide to manually calculating roller conveyor power requirements.
Step-by-Step Guide to Manually Calculating Roller Conveyor Power Requirements
Determine the Total Load
- Calculate the total weight of the items being conveyed.
- Include the weight of the conveyor belt and any additional components.
Calculate the Effective Tension (Te)
- Effective tension is the sum of the forces required to overcome friction, gravity, and acceleration. Frictional Tension (Tf)
[ Tf = \mu \times W ]
Where: - (\mu) = Coefficient of friction
- (W) = Total weight of the load Gravity Tension (Tg)
- For inclined conveyors, calculate the tension required to lift the load.
[ Tg = W \times \sin(\theta) ]
Where: - ( \theta ) = Angle of inclination Acceleration Tension (Ta)
- Calculate the tension needed to accelerate the load.
[ Ta = \frac{W \times a}{g} ]
Where: - (a) = Acceleration
- (g) = Acceleration due to gravity (9.81 m/s²) Combine these tensions to find the effective tension:
[ Te = Tf + Tg + Ta ]
Determine the Conveyor Speed (v)
- Measure the speed at which the conveyor will operate (in meters per second or feet per minute).
Calculate the Required Motor Power (P)
- Use the effective tension and conveyor speed to determine the motor power.
[ P = \frac{Te \times v}{\eta} ]
Where: - (\eta) = Efficiency of the motor and drive system
Convert to Appropriate Units
- Convert the power from watts to horsepower (if necessary).
[ \text{Power (HP)} = \frac{P \text{ (watts)}}{745.7} ]
Consider Safety Factors
- Apply safety factors to account for unexpected loads or operational conditions. Typically, a safety factor of 1.5 to 2 is used.
Example Formulas and Calculations
Let’s consider an example to illustrate the manual calculation process:
Example:
- Total weight (W) = 1000 kg
- Coefficient of friction ((\mu)) = 0.05
- Angle of inclination ((\theta)) = 10 degrees
- Acceleration (a) = 0.2 m/s²
- Conveyor speed (v) = 1 m/s
- Motor and drive efficiency ((\eta)) = 0.9
Step 1: Determine Frictional Tension (Tf)
[ Tf = \mu \times W = 0.05 \times 1000 \text{ kg} = 50 \text{ N} ]
Step 2: Determine Gravity Tension (Tg)
[ Tg = W \times \sin(\theta) = 1000 \times \sin(10^\circ) \approx 174.5 \text{ N} ]
Step 3: Determine Acceleration Tension (Ta)
[ Ta = \frac{W \times a}{g} = \frac{1000 \times 0.2}{9.81} \approx 20.4 \text{ N} ]
Step 4: Calculate Effective Tension (Te)
[ Te = Tf + Tg + Ta = 50 + 174.5 + 20.4 \approx 245 \text{ N} ]
Step 5: Calculate Required Motor Power (P)
[ P = \frac{Te \times v}{\eta} = \frac{245 \times 1}{0.9} \approx 272.2 \text{ watts} ]
Step 6: Convert to Horsepower
[ \text{Power (HP)} = \frac{272.2}{745.7} \approx 0.37 \text{ HP} ]
Step 7: Apply Safety Factor
Assuming a safety factor of 1.5:
[ \text{Required Power (HP)} = 0.37 \times 1.5 \approx 0.56 \text{ HP} ]
This example demonstrates the process of manually calculating the power requirements for a roller conveyor system. The steps involve determining the various tensions, calculating the motor power, and applying safety factors to ensure reliable operation.
Automated Calculation Tools
Automated calculation tools provide a convenient and efficient way to perform roller conveyor power calculation. These tools are designed to simplify the calculation process, reduce the risk of errors, and provide more accurate results.
Overview of Available Tools and Software for Power Calculation
Several software tools and online calculators are available to assist with the power calculation for roller conveyors. These tools often come with user-friendly interfaces and advanced features to streamline the calculation process. Some of the most popular tools include:
Excel Spreadsheets
- Customizable spreadsheets with built-in formulas for power calculation.
- Users can input their specific parameters, and the spreadsheet performs the necessary calculations.
- Excel spreadsheets are widely used due to their flexibility and accessibility.
Online Calculators
- Web-based calculators that allow users to input their conveyor specifications and receive instant power calculation results.
- These calculators are often provided by conveyor manufacturers and industry websites.
- They are convenient for quick calculations without the need for specialized software.
Specialized Software
- Dedicated software programs designed for conveyor system design and power calculation.
- These programs offer advanced features, including 3D modeling, simulation, and detailed reporting.
- Examples include software from companies like Rulmeca, FlexSim, and Dorner.
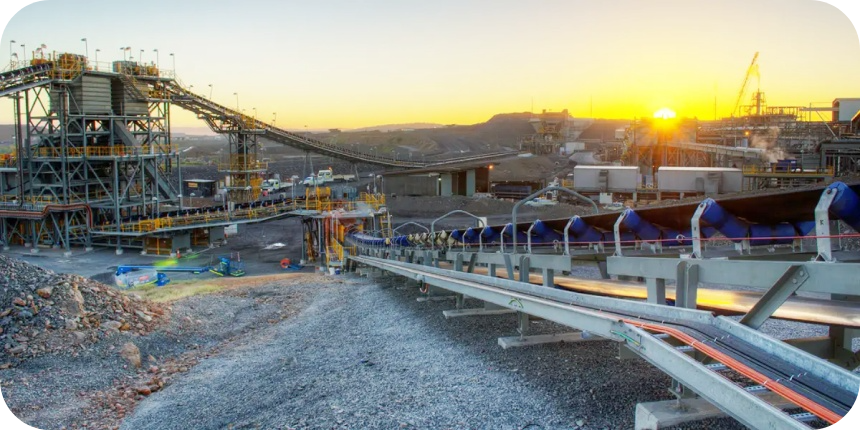
Benefits of Using Tools Like Excel and Online Calculators
Using automated tools for roller conveyor power calculation offers several benefits:
Accuracy
- Automated tools reduce the risk of human error in calculations.
- They use precise formulas and algorithms to ensure accurate results.
Efficiency
- Automated tools save time by performing complex calculations quickly.
- They eliminate the need for manual calculations, allowing engineers to focus on other tasks.
User-Friendly Interfaces
- Most tools come with intuitive interfaces that make it easy to input data and interpret results.
- Users can quickly learn to use these tools without extensive training.
Flexibility
- Tools like Excel spreadsheets can be customized to meet specific requirements.
- Users can modify formulas and add additional parameters as needed.
Consistency
- Automated tools ensure consistent calculations across different projects.
- They provide standardized results that can be easily compared and analyzed.
Accessibility
- Online calculators are accessible from anywhere with an internet connection.
- Excel spreadsheets and software programs can be used on various devices, including laptops and tablets.
Advanced Features
- Specialized software offers advanced features such as 3D modeling, simulation, and detailed reporting.
- These features help engineers visualize and optimize their conveyor systems.
Cost-Effectiveness
- Many online calculators and Excel templates are available for free or at a low cost.
- Specialized software, while sometimes more expensive, offers a high return on investment through improved efficiency and accuracy.
Integrating Automated Tools into the Calculation Process
To effectively use automated tools for roller conveyor power calculation, follow these steps:
Select the Appropriate Tool
- Choose the tool that best fits your needs based on the complexity of your conveyor system and the level of detail required.
Input Accurate Data
- Ensure that all input parameters are accurate and reflect the actual specifications of your conveyor system.
- Common parameters include load weight, conveyor speed, angle of inclination, and drive efficiency.
Review Calculation Results
- Carefully review the results provided by the tool to ensure they make sense and align with your expectations.
- Cross-check the results with manual calculations if necessary to verify accuracy.
Utilize Advanced Features
- Take advantage of advanced features such as 3D modeling and simulation to visualize the conveyor system and identify potential issues.
- Use detailed reports to document the calculation process and results for future reference.
Iterate and Optimize
- Use the tool to explore different scenarios and optimize the design of your conveyor system.
- Adjust parameters and re-calculate as needed to find the most efficient and cost-effective solution.
Detailed Roller Conveyor Power Calculation Steps
Accurate roller conveyor power calculation involves a series of detailed steps that ensure the conveyor system operates efficiently and reliably. This section breaks down these steps, providing a comprehensive guide to determining load and force, calculating effective tension, and determining motor power requirements.
Determining Load and Force
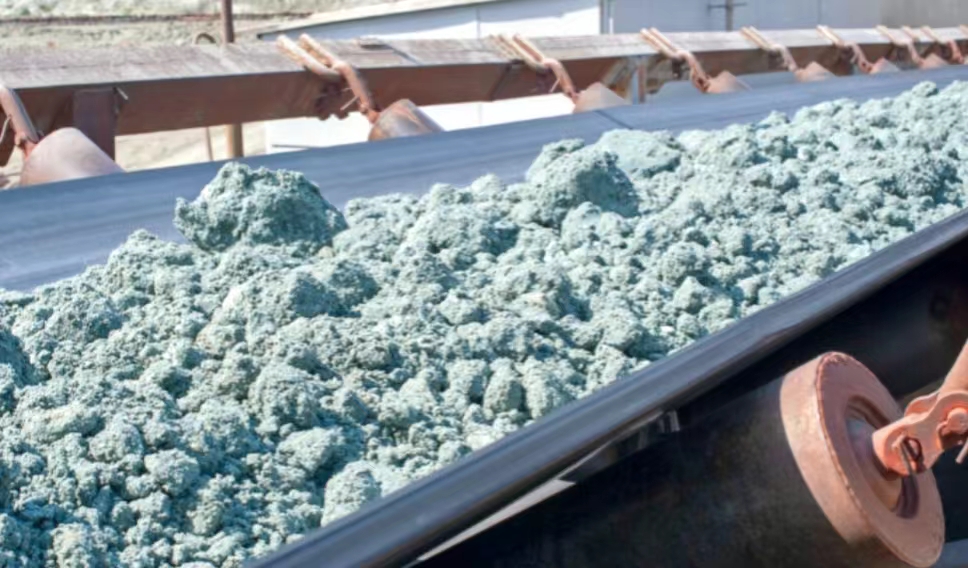
Methods to Calculate Load Based on Conveyor Specifications
The first step in the roller conveyor motor power calculation is determining the load that the conveyor will carry. This involves understanding the weight and distribution of the items being transported, which impacts the overall power requirements.
Static Load Calculation:
- The static load is the weight of the items when they are stationary on the conveyor.
- Calculate the total weight by summing up the weight of individual items.
Dynamic Load Calculation:
- Dynamic load includes additional forces when items are in motion.
- Factors such as acceleration and deceleration must be considered.
Load Distribution:
- Assess how the load is distributed across the conveyor.
- Uneven load distribution can lead to increased power requirements.
Examples of Load Distribution and Its Impact on Power Requirements
Uniform Load Distribution:
- Items are evenly spaced and of equal weight.
- Results in consistent power requirements.
Concentrated Load:
- Heavier items are placed in specific areas.
- Requires additional power to move concentrated weights.
Variable Load Distribution:
- Items of varying weights and sizes.
- Power calculation must account for the heaviest item.
Intermittent Load:
- Load appears in intervals (e.g., batches).
- Requires motor power to handle peak loads.
Continuous Load:
- Steady flow of items.
- Easier to calculate as load is consistent.
Inclined Load:
- Items are transported on an inclined plane.
- Additional power needed to overcome gravitational forces.
Calculating Effective Tension
Explanation of Effective Tension (Te) and Its Role in Power Calculation
Effective tension (Te) is the total force required to move the load on the conveyor. It includes the forces needed to overcome friction, gravity, and acceleration. Understanding Te is crucial for accurate roller conveyor power calculation.
Frictional Tension (Tf):
- The force needed to overcome friction between the conveyor belt and rollers.
- Formula: ( Tf = \mu \times W )
- Where (\mu) is the coefficient of friction and (W) is the total weight.
Gravity Tension (Tg):
- The force needed to lift or lower the load against gravity.
- Formula: ( Tg = W \times \sin(\theta) )
- Where (\theta) is the angle of inclination.
Acceleration Tension (Ta):
- The force needed to accelerate the load.
- Formula: ( Ta = \frac{W \times a}{g} )
- Where (a) is the acceleration and (g) is the acceleration due to gravity.
Detailed Formulas and Calculation Examples
Example Calculation:
Given Data:
- Total weight (W): 500 kg
- Coefficient of friction ((\mu)): 0.04
- Angle of inclination ((\theta)): 15 degrees
- Acceleration (a): 0.5 m/s²
Calculate Frictional Tension (Tf):
- ( Tf = \mu \times W = 0.04 \times 500 = 20 \text{ N} )
Calculate Gravity Tension (Tg):
- ( Tg = W \times \sin(\theta) = 500 \times \sin(15^\circ) \approx 129.9 \text{ N} )
Calculate Acceleration Tension (Ta):
- ( Ta = \frac{W \times a}{g} = \frac{500 \times 0.5}{9.81} \approx 25.5 \text{ N} )
Calculate Effective Tension (Te):
- ( Te = Tf + Tg + Ta = 20 + 129.9 + 25.5 \approx 175.4 \text{ N} )
Motor Power Calculation
Steps to Calculate the Required Motor Power
The final step in the roller conveyor power calculation is determining the motor power required to drive the conveyor. This involves using the effective tension and conveyor speed to calculate the power.
Determine Conveyor Speed (v):
- Measure the speed at which the conveyor operates (e.g., meters per second).
Calculate Motor Power (P):
- Use the effective tension and speed to calculate power.
- Formula: ( P = \frac{Te \times v}{\eta} )
- Where (\eta) is the efficiency of the motor and drive system.
Convert to Horsepower (HP) if Necessary:
- Formula: ( \text{Power (HP)} = \frac{P \text{ (watts)}}{745.7} )
Apply Safety Factors:
- Typically, a safety factor of 1.5 to 2 is used to ensure reliability.
Examples Using Different Types of Motors and Configurations
Standard AC Motor:
- Given Data:
- Effective tension (Te): 175.4 N
- Conveyor speed (v): 2 m/s
- Efficiency ((\eta)): 0.9
- Calculate Power (P):
- ( P = \frac{Te \times v}{\eta} = \frac{175.4 \times 2}{0.9} \approx 389.8 \text{ watts} )
- Convert to HP:
- ( \text{Power (HP)} = \frac{389.8}{745.7} \approx 0.52 \text{ HP} )
- Apply Safety Factor:
- ( \text{Required Power (HP)} = 0.52 \times 1.5 \approx 0.78 \text{ HP} )
Variable Frequency Drive (VFD) Motor:
- Given Data:
- Effective tension (Te): 250 N
- Conveyor speed (v): 1.5 m/s
- Efficiency ((\eta)): 0.85
- Calculate Power (P):
- ( P = \frac{Te \times v}{\eta} = \frac{250 \times 1.5}{0.85} \approx 441.2 \text{ watts} )
- Convert to HP:
- ( \text{Power (HP)} = \frac{441.2}{745.7} \approx 0.59 \text{ HP} )
- Apply Safety Factor:
- ( \text{Required Power (HP)} = 0.59 \times 1.5 \approx 0.88 \text{ HP} )
Servo Motor:
- Given Data:
- Effective tension (Te): 100 N
- Conveyor speed (v): 1 m/s
- Efficiency ((\eta)): 0.95
- Calculate Power (P):
- ( P = \frac{Te \times v}{\eta} = \frac{100 \times 1}{0.95} \approx 105.3 \text{ watts} )
- Convert to HP:
- ( \text{Power (HP)} = \frac{105.3}{745.7} \approx 0.14 \text{ HP} )
- Apply Safety Factor:
- ( \text{Required Power (HP)} = 0.14 \times 1.5 \approx 0.21 \text{ HP} )
DC Motor:
- Given Data:
- Effective tension (Te): 300 N
- Conveyor speed (v): 0.8 m/s
- Efficiency ((\eta)): 0.8
- Calculate Power (P):
- ( P = \frac{Te \times v}{\eta} = \frac{300 \times 0.8}{0.8} = 300 \text{ watts} )
- Convert to HP:
- ( \text{Power (HP)} = \frac{300}{745.7} \approx 0.4 \text{ HP} )
- Apply Safety Factor:
- ( \text{Required Power (HP)} = 0.4 \times 1.5 = 0.6 \text{ HP} )
Hydraulic Motor:
- Given Data:
- Effective tension (Te): 150 N
- Conveyor speed (v): 0.5 m/s
- Efficiency ((\eta)): 0.75
- Calculate Power (P):
- ( P = \frac{Te \times v}{\eta} = \frac{150 \times 0.5}{0.75} \approx 100 \text{ watts} )
- Convert to HP:
- ( \text{Power (HP)} = \frac{100}{745.7
} \approx 0.13 \text{ HP} )
- Apply Safety Factor:
- ( \text{Required Power (HP)} = 0.13 \times 1.5 \approx 0.2 \text{ HP} )
Geared Motor:
- Given Data:
- Effective tension (Te): 400 N
- Conveyor speed (v): 1.2 m/s
- Efficiency ((\eta)): 0.85
- Calculate Power (P):
- ( P = \frac{Te \times v}{\eta} = \frac{400 \times 1.2}{0.85} \approx 564.7 \text{ watts} )
- Convert to HP:
- ( \text{Power (HP)} = \frac{564.7}{745.7} \approx 0.76 \text{ HP} )
- Apply Safety Factor:
- ( \text{Required Power (HP)} = 0.76 \times 1.5 \approx 1.14 \text{ HP} )
Induction Motor:
- Given Data:
- Effective tension (Te): 200 N
- Conveyor speed (v): 1.0 m/s
- Efficiency ((\eta)): 0.9
- Calculate Power (P):
- ( P = \frac{Te \times v}{\eta} = \frac{200 \times 1.0}{0.9} \approx 222.2 \text{ watts} )
- Convert to HP:
- ( \text{Power (HP)} = \frac{222.2}{745.7} \approx 0.3 \text{ HP} )
- Apply Safety Factor:
- ( \text{Required Power (HP)} = 0.3 \times 1.5 = 0.45 \text{ HP} )
Stepper Motor:
- Given Data:
- Effective tension (Te): 50 N
- Conveyor speed (v): 0.4 m/s
- Efficiency ((\eta)): 0.8
- Calculate Power (P):
- ( P = \frac{Te \times v}{\eta} = \frac{50 \times 0.4}{0.8} = 25 \text{ watts} )
- Convert to HP:
- ( \text{Power (HP)} = \frac{25}{745.7} \approx 0.03 \text{ HP} )
- Apply Safety Factor:
- ( \text{Required Power (HP)} = 0.03 \times 1.5 = 0.045 \text{ HP} )
Servo Motor with Gearbox:
- Given Data:
- Effective tension (Te): 80 N
- Conveyor speed (v): 1.5 m/s
- Efficiency ((\eta)): 0.95
- Calculate Power (P):
- ( P = \frac{Te \times v}{\eta} = \frac{80 \times 1.5}{0.95} \approx 126.3 \text{ watts} )
- Convert to HP:
- ( \text{Power (HP)} = \frac{126.3}{745.7} \approx 0.17 \text{ HP} )
- Apply Safety Factor:
- ( \text{Required Power (HP)} = 0.17 \times 1.5 \approx 0.26 \text{ HP} )
Synchronous Motor:
- Given Data:
- Effective tension (Te): 120 N
- Conveyor speed (v): 0.7 m/s
- Efficiency ((\eta)): 0.85
- Calculate Power (P):
- ( P = \frac{Te \times v}{\eta} = \frac{120 \times 0.7}{0.85} \approx 98.8 \text{ watts} )
- Convert to HP:
- ( \text{Power (HP)} = \frac{98.8}{745.7} \approx 0.13 \text{ HP} )
- Apply Safety Factor:
- ( \text{Required Power (HP)} = 0.13 \times 1.5 \approx 0.2 \text{ HP} )
Advanced Roller Conveyor Power Calculation Considerations
When delving into the intricacies of the roller conveyor power calculation, it’s essential to consider various advanced factors that influence the overall efficiency and reliability of the conveyor system. This section explores special considerations for chain-driven systems, compares roller and belt conveyor power calculations, and provides example formulas and best practices.
Chain Driven Roller Conveyor Design Calculation
Special Considerations for Chain-Driven Systems
Chain-driven roller conveyors are robust and suitable for heavy-duty applications. However, they come with unique challenges that must be addressed during the power calculation process. Key considerations include:
Chain Tension:
- Chain tension impacts the efficiency and longevity of the conveyor. Proper tensioning is crucial to prevent slippage and ensure smooth operation.
- Over-tensioning can cause excessive wear on the chain and sprockets, while under-tensioning can lead to chain derailment.
Friction and Wear:
- Chain-driven systems experience higher friction due to the interaction between the chain and sprockets.
- Regular lubrication and maintenance are necessary to minimize wear and extend the system’s lifespan.
Load Distribution:
- Even distribution of load across the rollers is vital to prevent uneven wear and reduce the power required to move the load.
- The design should ensure that the load is evenly distributed to avoid overloading specific rollers or chain links.
Calculation Examples and Best Practices
Example Calculation for Chain-Driven System:
Given Data:
- Total load weight (W): 1500 kg
- Coefficient of friction ((\mu)): 0.03
- Conveyor speed (v): 1.2 m/s
- Efficiency of chain drive system ((\eta)): 0.85
Calculate Frictional Tension (Tf):
- ( Tf = \mu \times W = 0.03 \times 1500 = 45 \text{ N} )
Calculate Effective Tension (Te):
- Since there’s no incline or acceleration specified, Te is equal to Tf.
- ( Te = Tf = 45 \text{ N} )
Calculate Motor Power (P):
- ( P = \frac{Te \times v}{\eta} = \frac{45 \times 1.2}{0.85} \approx 63.5 \text{ watts} )
Convert to Horsepower (HP):
- ( \text{Power (HP)} = \frac{63.5}{745.7} \approx 0.085 \text{ HP} )
Best Practices:
- Regularly inspect and adjust chain tension.
- Lubricate the chain and sprockets to reduce friction.
- Ensure even load distribution by designing the conveyor layout appropriately.
- Use high-quality chains and sprockets to enhance durability and reduce maintenance needs.
Belt Conveyor Power Calculation
Comparison of Roller Conveyor vs. Belt Conveyor Power Calculations
While the principles behind power calculations for roller and belt conveyors are similar, there are distinct differences due to the nature of the components and the load handling characteristics. The table below highlights these differences:
Example Formulas and Scenarios
Example Calculation for Belt Conveyor System:
Given Data:
- Total load weight (W): 2000 kg
- Coefficient of friction ((\mu)): 0.04
- Conveyor speed (v): 1.0 m/s
- Incline angle ((\theta)): 5 degrees
- Efficiency of belt drive system ((\eta)): 0.9
Calculate Frictional Tension (Tf):
- ( Tf = \mu \times W = 0.04 \times 2000 = 80 \text{ N} )
Calculate Gravity Tension (Tg):
- ( Tg = W \times \sin(\theta) = 2000 \times \sin(5^\circ) \approx 174.5 \text{ N} )
Calculate Effective Tension (Te):
- ( Te = Tf + Tg = 80 + 174.5 = 254.5 \text{ N} )
Calculate Motor Power (P):
- ( P = \frac{Te \times v}{\eta} = \frac{254.5 \times 1.0}{0.9} \approx 282.8 \text{ watts} )
Convert to Horsepower (HP):
- ( \text{Power (HP)} = \frac{282.8}{745.7} \approx 0.38 \text{ HP} )
Scenarios:
Horizontal Belt Conveyor:
- If the conveyor is horizontal, ( Tg ) would be zero, simplifying the calculation to only consider ( Tf ) and ( Ta ) if there’s acceleration.
Inclined Belt Conveyor:
- For inclined conveyors, ( Tg ) must be calculated to account for the additional force required to lift the load.
Variable Speed Conveyor:
- For conveyors with variable speeds, the calculation must consider the highest operational speed to ensure the motor can handle peak loads.
Get a quote for high-quality conveyor rollers today!
Tools and Resources for Roller Conveyor Power Calculation
For anyone involved in the design and implementation of conveyor systems, having access to the right tools and resources for motor power calculation for roller conveyor download is crucial. This section highlights some of the most useful downloadable resources, software tools, online calculators, and reference materials available to aid in the power calculation process.
Downloadable Resources
Links to PDF Guides and Downloadable Excel Sheets for Power Calculation
PDF Guides:
- “Roller Conveyor Design Guide”: This comprehensive guide provides detailed instructions on designing roller conveyors, including power calculation methods. It covers topics such as load assessment, tension calculations, and motor selection.
- Download Roller Conveyor Design Guide
- “Conveyor Power Calculation PDF”: A step-by-step guide specifically focused on power calculation. It includes formulas, example calculations, and tips for optimizing conveyor performance.
- Download Conveyor Power Calculation PDF
Excel Sheets:
- “Power Calculation Excel Template”: An Excel spreadsheet template designed to simplify the power calculation process. Users can input their conveyor specifications, and the sheet automatically calculates the required motor power.
- Download Power Calculation Excel Template
- “Conveyor Load Calculation Excel”: This Excel tool helps users calculate the load and distribution across the conveyor system, providing a solid foundation for subsequent power calculations.
- Download Conveyor Load Calculation Excel
Overview of Useful Software and Online Calculators
Software Tools:
- FlexSim Conveyor Simulation Software: FlexSim offers advanced simulation capabilities, allowing users to model conveyor systems and calculate power requirements dynamically. It includes features for visualizing load distribution, tension, and motor performance.
- FlexSim Conveyor Simulation Software
- Rulmeca Bulk Handling Power Calculation Program: This software assists with calculating conveyor belt pull and power requirements for bulk handling applications. It includes tools for both CEMA 7 and CEMA 4 standards.
- Rulmeca Power Calculation Program
Online Calculators:
- Dorner Conveyor Power Calculator: Dorner’s online tool allows users to quickly calculate the power requirements for their conveyor systems. Input parameters include load weight, conveyor speed, and incline angle.
- Dorner Conveyor Power Calculator
- EICAC Conveyor Power and Torque Calculator: This calculator helps users determine the force, torque, and power needed to move a load on a conveyor, accommodating both horizontal and inclined configurations.
- EICAC Conveyor Power and Torque Calculator
Reference Materials
Recommended Reading and Resources for Further Learning
Books:
- “Belt Conveyors for Bulk Materials” by CEMA: This book is a comprehensive resource on conveyor design and power calculation, including detailed chapters on tension calculations and motor selection.
- Buy on Amazon
- “Handbook of Conveyor and Elevator Belting” by Goodyear: A detailed guide covering various aspects of conveyor systems, including power calculation methods and best practices for efficient operation.
- Buy on Amazon
Technical Articles and Manuals:
- “Optimizing Conveyor System Performance”: This article discusses strategies for improving conveyor efficiency, including detailed sections on power calculation and energy-saving techniques.
- Read Article
- “Conveyor Belt Calculations”: An in-depth manual that explains the mathematical foundations of conveyor power calculations, including practical examples and case studies.
- Read Manual
Links to Technical Articles, Manuals, and Industry Standards
Industry Standards:
- CEMA Standards: The Conveyor Equipment Manufacturers Association (CEMA) sets standards for conveyor design and operation. Their publications provide essential guidelines for power calculations and system design.
- CEMA Standards
- ISO 5048: This international standard outlines the calculation methods for belt conveyor power requirements. It is a crucial resource for ensuring compliance with global engineering practices.
- ISO 5048 Standard
Technical Manuals:
- “SKF Conveyor Solutions”: SKF offers a range of technical manuals and whitepapers focused on conveyor design and power calculation, providing valuable insights and best practices.
- SKF Conveyor Solutions
- “SEW Eurodrive Conveyor Technology”: SEW Eurodrive’s manuals cover various aspects of conveyor technology, including detailed power calculation methods and motor selection guidelines.
- SEW Eurodrive Conveyor Technology
Utilizing Tools and Resources Effectively
To maximize the benefits of these tools and resources, it’s essential to follow best practices:
Stay Updated with Latest Standards:
- Regularly check for updates to industry standards and guidelines to ensure your calculations and designs are compliant with the latest engineering practices.
Cross-Reference Multiple Resources:
- Use a combination of software tools, online calculators, and downloadable templates to cross-verify your power calculations. This approach helps identify any discrepancies and ensures accuracy.
Leverage Advanced Software Features:
- Take advantage of advanced features in simulation software like FlexSim to model complex conveyor systems and optimize performance. Features such as 3D visualization and dynamic simulation can provide deeper insights into system behavior.
Engage with Professional Communities:
- Join professional organizations such as CEMA or participate in online forums and discussion groups. Engaging with peers and industry experts can provide valuable advice and solutions to specific challenges you may encounter.
Document and Review Calculations:
- Maintain detailed records of your power calculations, including all assumptions, input parameters, and results. Regularly review these documents to identify areas for improvement and ensure consistent application of best practices.
Practical Application and Examples
Understanding the theoretical aspects of roller conveyor power calculation is crucial, but seeing how these calculations are applied in real-world scenarios is equally important. This section provides practical applications and examples, focusing on case studies and troubleshooting and optimization strategies.
Case Studies
Real-World Examples of Power Calculation in Roller Conveyor Systems
Case Study 1: Toyota Manufacturing Plant
Background: Toyota’s automotive manufacturing plant required a new conveyor system to transport heavy car parts across the assembly line. The challenge was to ensure the system could handle varying loads and operate efficiently under continuous use.
Power Calculation: Engineers from Toyota conducted a detailed power calculation considering the weight of the car parts, conveyor speed, and the friction coefficient of the rollers. They used a combination of manual calculations and specialized software to determine the required motor power.
Outcome: The chosen motor and drive components were able to handle the load efficiently, reducing downtime and improving production rates. The system operated smoothly, demonstrating the effectiveness of accurate power calculations.
Case Study 2: Nestlé Food Processing Facility
Background: Nestlé’s food processing facility needed a conveyor system to move packaged goods through various processing stages. The primary concern was maintaining hygiene standards while ensuring the conveyor could handle the load and speed requirements.
Power Calculation: The team used an online calculator and downloadable Excel templates to calculate the power requirements, considering factors such as load weight, conveyor speed, and incline. Stainless steel rollers were selected to meet hygiene standards.
Outcome: The new conveyor system met all operational requirements, running efficiently without any mechanical issues. Regular maintenance and hygiene checks were implemented, further enhancing system performance.
Case Study 3: Amazon E-commerce Distribution Center
Background: Amazon’s e-commerce distribution center needed a flexible conveyor system to handle varying package sizes and weights. The system required frequent start-stop operations, making accurate power calculations essential to prevent overloading.
Power Calculation: Engineers used simulation software to model the conveyor system and perform power calculations. They accounted for peak loads and variable speeds, ensuring the motor could handle the operational demands.
Outcome: The conveyor system operated efficiently, reducing energy consumption and handling high volumes of packages without issues. The flexibility of the system allowed for easy adjustments based on package size and weight.
Lessons Learned and Best Practices from Industry Applications
- Thorough Load Assessment: Accurate load assessment is critical for effective power calculation. Understanding the weight and distribution of items being conveyed helps in selecting the appropriate motor and drive components.
- Use of Advanced Tools: Leveraging specialized software and online calculators enhances the accuracy of power calculations, providing detailed insights into system performance.
- Regular Maintenance: Regular maintenance of the conveyor system, including lubrication and tension adjustments, ensures smooth operation and extends the lifespan of components.
- Customization: Customizing conveyor components based on specific application needs, such as material type and load distribution, optimizes performance and efficiency.
- Collaboration with Experts: Working with industry experts and manufacturers can provide valuable guidance and ensure compliance with best practices and standards.
Troubleshooting and Optimization
Common Issues and Solutions in Roller Conveyor Power Calculation
Inaccurate Load Measurements:
- Issue: Incorrect load measurements can lead to inadequate power calculations, resulting in underpowered or overpowered systems.
- Solution: Ensure precise measurement of load weight and distribution. Use calibrated scales and regularly verify measurements.
Incorrect Friction Coefficients:
- Issue: Using incorrect friction coefficients can affect the accuracy of power calculations.
- Solution: Select appropriate friction coefficients based on material and environmental conditions. Consult manufacturer specifications for accurate values.
Underestimating Peak Loads:
- Issue: Failing to account for peak loads can lead to system overload and potential failures.
- Solution: Factor in peak loads and apply safety margins to ensure the motor can handle maximum operational demands.
Improper Tensioning:
- Issue: Incorrect tensioning of chains or belts can cause slippage and inefficient operation.
- Solution: Regularly inspect and adjust tension to ensure optimal performance. Use automatic tensioning devices if possible.
Inadequate Motor Selection:
- Issue: Selecting a motor with insufficient power or incorrect specifications can lead to operational inefficiencies.
- Solution: Carefully match motor specifications to calculated power requirements. Consider motor efficiency and torque characteristics.
Environmental Factors:
- Issue: Environmental conditions such as temperature and humidity can impact conveyor performance.
- Solution: Select materials and components suitable for the operational environment. Implement protective measures to mitigate environmental effects.
Lack of Regular Maintenance:
- Issue: Neglecting regular maintenance can lead to increased wear and unexpected failures.
- Solution: Establish a routine maintenance schedule, including lubrication, cleaning, and component inspections.
Insufficient Safety Margins:
- Issue: Failing to apply adequate safety margins can result in system failures under unexpected conditions.
- Solution: Always include safety margins in power calculations to account for unforeseen loads and operational variations.
Inconsistent Speed Control:
- Issue: Variable speeds without proper control can cause inefficiencies and wear.
- Solution: Use variable frequency drives (VFDs) to maintain consistent and controlled speeds, optimizing energy consumption.
Tips for Optimizing Conveyor Performance and Reducing Energy Consumption
Use High-Efficiency Motors:
- Select motors with high efficiency ratings to reduce energy consumption and operational costs.
Optimize Conveyor Speed:
- Adjust conveyor speed to match operational requirements, avoiding excessive speeds that increase wear and energy use.
Implement Variable Frequency Drives (VFDs):
- Use VFDs to control motor speed dynamically, optimizing performance based on load and operational needs.
Regularly Inspect and Maintain Components:
- Conduct routine inspections and maintenance to ensure all components operate smoothly and efficiently.
Utilize Advanced Control Systems:
- Implement advanced control systems for precise monitoring and adjustment of conveyor operations.
Enhance Load Distribution:
- Ensure even load distribution across the conveyor to reduce stress on individual components and improve efficiency.
Minimize Friction:
- Use low-friction materials and lubricants to reduce resistance and power requirements.
Optimize Layout and Design:
- Design the conveyor layout to minimize inclines and sharp turns, reducing the power needed to move the load.
Incorporate Energy-Saving Features:
- Implement energy-saving features such as automatic shut-off during idle periods and regenerative braking systems.
Contact us now for premium conveyor roller solutions.
FAQs about Roller Conveyor Power Calculation
To calculate the power of a belt conveyor, follow these steps:
Determine the Conveyor Belt Speed: Measure the belt speed in meters per second (m/s).
Calculate the Load: Identify the load weight on the conveyor in kilograms (kg).
Calculate the Belt Tension: Use the formula T = F * v, where T is the belt tension, F is the force exerted by the load, and v is the belt speed.
Determine the Power Requirement: Power (P) is calculated by the formula P = T * v / η, where η is the efficiency of the conveyor system. This gives the power in kilowatts (kW).
Calculating the horsepower (HP) of a conveyor involves:
Identify the Load Weight: Measure the weight of the load in pounds (lbs).
Calculate the Total Belt Tension (T1): This includes the effective tension required to move the load and the additional tension due to the belt.
Determine the Conveyor Speed: Measure the speed in feet per minute (fpm).
Apply the Horsepower Formula: HP = (T1 * belt speed) / 33,000. The factor 33,000 converts the product of tension and speed to horsepower.
For chain conveyor motor power calculation:
Determine the Total Load: Sum the weights of the load and the chain.
Calculate the Required Torque: Torque (T) is the product of the force exerted by the load and the radius of the sprocket (T = F * r).
Identify the Speed of the Chain: Measure in meters per second (m/s).
Use the Power Formula: Motor Power (P) = T * chain speed. Convert this to kW using the appropriate conversion factor and consider the efficiency of the motor.
To calculate the load capacity of a conveyor:
Determine the Conveyor Type and Dimensions: Identify the type (belt, roller, chain) and measure its width, length, and incline.
Identify the Material Load: Know the type and weight of materials being conveyed.
Calculate the Load Weight per Unit Length: Divide the total load weight by the length of the conveyor.
Consider the Conveyor Structure: Ensure the conveyor frame and components can support the calculated load weight.
Apply Safety Factors: Use safety factors to account for unexpected overloads and ensure reliable operation.
Last Updated on August 9, 2024 by Jordan Smith
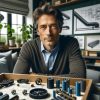
Jordan Smith, a seasoned professional with over 20 years of experience in the conveyor system industry. Jordan’s expertise lies in providing comprehensive solutions for conveyor rollers, belts, and accessories, catering to a wide range of industrial needs. From initial design and configuration to installation and meticulous troubleshooting, Jordan is adept at handling all aspects of conveyor system management. Whether you’re looking to upgrade your production line with efficient conveyor belts, require custom conveyor rollers for specific operations, or need expert advice on selecting the right conveyor accessories for your facility, Jordan is your reliable consultant. For any inquiries or assistance with conveyor system optimization, Jordan is available to share his wealth of knowledge and experience. Feel free to reach out at any time for professional guidance on all matters related to conveyor rollers, belts, and accessories.