Roller Steel Industrial Engineering: Types and Uses
In the realm of industrial engineering, the use of roller steel is pivotal, serving as the backbone for numerous manufacturing and processing operations. Rollers, particularly those crafted from steel, are indispensable due to their durability, strength, and ability to withstand high-pressure environments. These components play a crucial role in facilitating the smooth and efficient movement of materials across various stages of production. From conveyor systems in assembly lines to heavy-duty applications in metalworking and material handling, the integration of roller steel industrial engineering solutions ensures operational efficiency and productivity. The importance of steel rollers extends beyond mere functionality; they are also vital in maintaining the quality and integrity of products during manufacturing, making them an essential element in the industrial sector.
Types of Rollers in Mechanical Engineering in Roller Steel Industrial Engineering
In the field of roller steel industrial engineering, various types of rollers are pivotal in mechanical engineering, each serving distinct functions across diverse applications. Below is a detailed overview of common rollers, including Conveyor Rollers, Heavy Duty Rollers, and three other prevalent types, showcasing their unique roles and applications in industrial settings.
Each type of roller in roller steel industrial engineering plays a vital role in the efficiency and effectiveness of mechanical systems. Their applications span across various sectors, demonstrating the versatility and importance of rollers in industrial and manufacturing processes.
The Steel Rolling Process in Roller Steel Industrial Engineering
The steel rolling process is a cornerstone in roller steel industrial engineering, representing a fundamental technique in metal manufacturing. This process transforms steel into various shapes and sizes through mechanical deformation, where the metal is passed through one or more pairs of rollers to achieve the desired thickness and shape. Here, we delve into the intricacies of the steel rolling mill process, detailing the hot rolling process step by step, and exploring the five types of rolling mills and their specific applications.

Hot Rolling Process Step by Step:
- Heating: The steel is heated to a temperature that makes it pliable, usually above its recrystallization temperature.
- Descale: Before entering the rolling mill, the heated billets are descaled using high-pressure water jets to remove surface oxides.
- Roughing: The initial rolling stage where the steel is passed through several roughing stands to reduce its thickness.
- Intermediate and Finishing Rolling: The steel goes through intermediate stands for further reduction and then to the finishing stands to achieve the final dimensions and surface finish.
- Cooling: After rolling, the steel is cooled down to room temperature through controlled cooling methods.
- Coiling: Finally, the rolled steel is coiled for easier handling and transportation.
Types of Rolling Mills in Roller Steel Industrial Engineering:
The steel rolling process in roller steel industrial engineering is a sophisticated and highly controlled operation, crucial for producing steel products with precise dimensions and mechanical properties. Understanding the nuances of this process and the capabilities of different types of rolling mills is essential for engineers and professionals in the metal manufacturing industry.
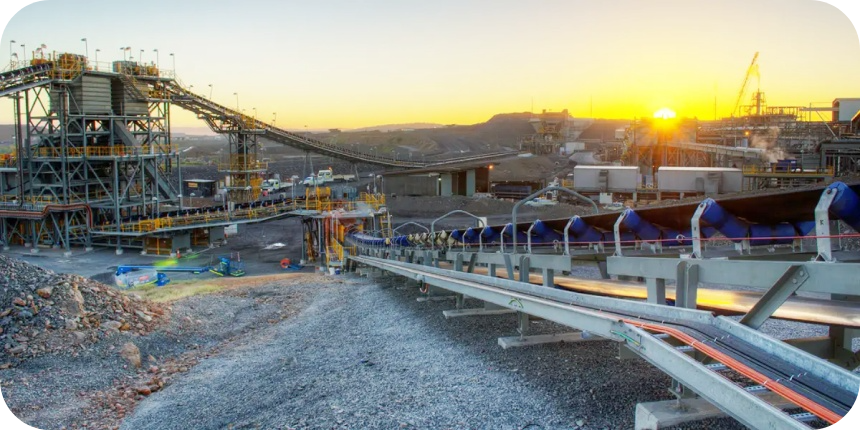
Advantages of the Rolling Process in Roller Steel Industrial Engineering
The rolling process, a pivotal technique in roller steel industrial engineering, offers numerous advantages that significantly enhance manufacturing efficiency, productivity, and the quality of the final steel products. This section delves into the key benefits of this process, highlighting how it stands as a cornerstone in the metalworking industry.

- Efficiency and Productivity: The rolling process is renowned for its ability to produce large volumes of metal products in a relatively short amount of time. This high throughput is crucial in meeting the demands of various industries, from construction to automotive manufacturing, ensuring a steady supply of essential steel components.
- Material Properties: Rolling significantly improves the mechanical properties of steel, including its strength, ductility, and toughness. The process aligns the grain structure of the metal, enhancing its ability to withstand external stresses and strains, which is vital for structural applications.
- Versatility: Roller steel industrial engineering through the rolling process allows for the production of steel in a wide range of shapes and sizes, from thin sheets to large beams. This versatility ensures that steel can be tailored to meet the specific requirements of different applications.
- Cost-Effectiveness: Compared to other forming processes, rolling is more cost-effective, especially for high-volume production. The efficiency of the process reduces labor costs and energy consumption, contributing to lower overall manufacturing expenses.
- Uniformity and Consistency: The controlled conditions of the rolling process ensure that each product has uniform dimensions and consistent quality. This predictability is crucial for industries where precision and reliability are paramount.
- Scalability: The rolling process is easily scalable, accommodating small batch productions to large-scale operations without significant changes in setup. This flexibility allows manufacturers to adjust their output based on market demands.
- Energy Efficiency: Rolling is relatively energy-efficient compared to other metalworking processes, such as forging or casting. The process utilizes the initial heat from the molten steel, reducing the need for additional heating and thus conserving energy.
- Recyclability: The rolling process supports the use of recycled steel, contributing to sustainable manufacturing practices. This not only reduces the demand for raw materials but also minimizes the environmental impact of steel production.
The advantages of the rolling process in roller steel industrial engineering are manifold, encompassing efficiency, productivity, material property enhancements, and more. These benefits underscore the critical role of rolling in the modern industrial landscape, providing a foundation for the development and production of high-quality steel products.
Rolling Manufacturing Process in Roller Steel Industrial Engineering
The rolling manufacturing process is a cornerstone in roller steel industrial engineering, involving the deformation of metal by passing it between rollers to reduce its thickness and make it uniform. This section provides a detailed examination of the rolling manufacturing process, offering insights into the technical aspects, methodologies, and the various types of rolling processes employed in the industry.
Detailed Examination of the Rolling Manufacturing Process:
The rolling process begins with heating the steel to a high temperature, making it pliable and ready for deformation. This is followed by the primary rolling stage, where the hot steel passes through a series of rollers, reducing its thickness with each pass. The material may undergo several stages, including roughing, intermediate rolling, and finishing, to achieve the desired shape and properties. Cooling and post-processing treatments such as annealing or tempering may follow to enhance the material’s mechanical properties.
Types of Rolling Processes in Roller Steel Industrial Engineering:
The rolling manufacturing process in roller steel industrial engineering is diverse, with each type of rolling process tailored to specific applications and material requirements. Understanding these processes and their applications is crucial for engineers and professionals in the field, ensuring the optimal selection of techniques for the production of high-quality steel products.
Applications and Innovations in Roller Steel Engineering in Roller Steel Industrial Engineering
The field of roller steel industrial engineering encompasses a wide range of applications and has been the focus of numerous innovations, particularly in the areas of conveyor roller steel and heavy-duty roller steel engineering. This section explores the diverse applications of roller steel in industrial settings through case studies and examples, and delves into the latest advancements and future trends in heavy-duty roller steel engineering.
Conveyor Roller Steel in Industrial Applications:

Conveyor roller steel plays a pivotal role in various industries by facilitating the efficient movement of goods and materials. Here are eight case studies highlighting its diverse applications:
- Automotive Assembly Lines: Conveyor rollers made of steel are integral in moving parts and assemblies through different stages of vehicle production, from body welding to final assembly.
- Food and Beverage Processing: Stainless steel rollers are used in processing lines for their resistance to corrosion and ease of cleaning, ensuring hygiene standards are met.
- Airport Baggage Handling Systems: Durable steel rollers ensure the smooth and reliable transport of luggage between check-in, security, and aircraft loading areas.
- Mining Operations: Heavy-duty steel rollers are employed in conveyor systems for transporting mined materials over long distances in harsh environments.
- E-commerce Fulfillment Centers: Conveyor systems equipped with steel rollers enable the rapid sorting and dispatching of packages, catering to high-volume online shopping demands.
- Pharmaceutical Manufacturing: Precision-engineered steel rollers are used in cleanroom environments for the production and packaging of pharmaceuticals.
- Paper and Pulp Industries: Steel rollers are involved in the processing, drying, and rolling of paper products, where strength and precision are crucial.
- Recycling Facilities: Robust steel rollers are essential in conveyor systems for sorting and processing recyclable materials, withstanding heavy loads and abrasive conditions.
Innovations in Heavy Duty Roller Steel Engineering:

The field of heavy-duty roller steel engineering is witnessing significant advancements, driven by the need for higher efficiency, durability, and sustainability. Some of the latest innovations and future trends include:
- Smart Roller Technologies: Integration of sensors and IoT devices into roller systems for real-time monitoring of performance, wear, and tear, enabling predictive maintenance and reducing downtime.
- Advanced Materials: Development of new steel alloys and coatings that enhance the wear resistance, load-bearing capacity, and lifespan of heavy-duty rollers, even in extreme conditions.
- Eco-friendly Designs: Focus on sustainability by designing rollers that are energy-efficient, require less maintenance, and are made from recyclable materials, reducing the environmental footprint of industrial operations.
- Customization and Modularity: Advances in manufacturing technologies, such as 3D printing, allow for the customization of roller components for specific applications, improving performance and adaptability.
- Automation and Robotics: Incorporation of automated systems and robotics in roller steel engineering to enhance precision, efficiency, and safety in industrial processes.
Contact us now for premium conveyor roller solutions.
The applications and innovations in roller steel industrial engineering demonstrate the field’s dynamic nature and its critical role in supporting and advancing industrial operations. As technology evolves, so too will the capabilities and applications of roller steel in industrial engineering, promising even greater efficiency, reliability, and innovation in the future.
FAQs about Roller Steel Industrial Engineering
In a steel mill, rollers play a crucial role in the manufacturing process of steel products. These cylindrical components are primarily used in rolling mills, where they apply force to steel billets or slabs, causing the metal to deform and elongate. This deformation process reduces the thickness of the steel while increasing its length and width to produce sheets, plates, bars, and other shapes. Rollers in steel mills are designed to withstand extreme temperatures and pressures, ensuring they can efficiently process the steel while maintaining precise dimensions and surface finishes of the final products. The rollers’ ability to consistently produce steel with specific characteristics is vital for various applications, from construction materials to automotive parts, highlighting their indispensable role in the steel manufacturing industry.
Industrial rollers are utilized in a wide array of applications across numerous sectors, including manufacturing, packaging, printing, and material handling, to name a few. Their primary function is to facilitate the movement, processing, and transformation of materials and products through different stages of production and logistics. For instance, in conveyor systems, rollers enable the smooth and efficient transport of goods across facilities. In printing and textile industries, they assist in the application of inks, coatings, and the smoothing of fabrics. Industrial rollers also play a role in shaping and bending materials, as seen in metalworking and plastic manufacturing. The versatility and efficiency of industrial rollers make them essential components in optimizing production workflows, enhancing product quality, and increasing operational efficiency across various industrial landscapes.
In mechanical engineering, rollers are cylindrical components that facilitate the movement, alteration, or processing of materials and mechanical parts. They are engineered to rotate around their axis and can be found in machinery and equipment across a broad spectrum of industries. Rollers in mechanical engineering are designed to perform tasks such as supporting, moving, compressing, or shaping materials. Their applications range from simple tasks like guiding a belt in a conveyor system to more complex functions like reducing the thickness of metal sheets in rolling mills. The design, material, and surface finish of rollers can vary significantly, depending on their specific application, to ensure optimal performance, durability, and efficiency in their designated roles within mechanical systems.
The choice of steel for rollers depends on their specific application and the environmental conditions they will be exposed to. Common types of steel used for rollers include carbon steel, alloy steel, stainless steel, and tool steel. Carbon steel is widely used for its good balance of strength, ductility, and cost-effectiveness, making it suitable for general-purpose rollers in conveyor systems and other applications. Alloy steel, which contains additional elements like chromium, molybdenum, and nickel, offers enhanced strength and resistance to wear and heat, making it ideal for rollers in high-stress environments such as rolling mills. Stainless steel is preferred for rollers in applications requiring corrosion resistance, such as in food processing or chemical industries. Tool steel, known for its hardness and resistance to abrasion, is used for rollers that need to withstand high pressures and wear, such as in metal forming and cutting machinery. The selection of steel type is critical to ensure the rollers can meet the mechanical and environmental demands of their application, ensuring longevity and reliability in operation.
Last Updated on June 21, 2024 by Jordan Smith
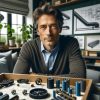
Jordan Smith, a seasoned professional with over 20 years of experience in the conveyor system industry. Jordan’s expertise lies in providing comprehensive solutions for conveyor rollers, belts, and accessories, catering to a wide range of industrial needs. From initial design and configuration to installation and meticulous troubleshooting, Jordan is adept at handling all aspects of conveyor system management. Whether you’re looking to upgrade your production line with efficient conveyor belts, require custom conveyor rollers for specific operations, or need expert advice on selecting the right conveyor accessories for your facility, Jordan is your reliable consultant. For any inquiries or assistance with conveyor system optimization, Jordan is available to share his wealth of knowledge and experience. Feel free to reach out at any time for professional guidance on all matters related to conveyor rollers, belts, and accessories.