Essential Guide to Rolls of Rubber Belting
Rolls of rubber belting are essential components in various industrial applications. These rolls are made from durable rubber compounds designed to withstand harsh conditions and heavy usage.FR Rubber Belt, in particular, offers fire-resistant properties, providing added safety in environments with potential heat or spark risks. Rolls of rubber belting are commonly used in conveyor systems to transport materials efficiently and safely. They offer excellent resistance to abrasion, chemicals, and extreme temperatures, making them ideal for use in mining, manufacturing, and logistics industries. Additionally, rolls of rubber belting can be customized to meet specific requirements, ensuring optimal performance and longevity. Whether you need to replace old belts or install new systems, rolls of rubber belting provide a reliable solution for maintaining smooth and efficient operations.
Rolls of Rubber Belting
Rubber belting is commonly associated with industrial applications, such as conveyor belts in factories and warehouses. However, this versatile material has found its way into other, more unexpected areas, including fashion. Rolls of rubber belting have been creatively adapted to serve as durable, stylish belts for pants. This section explores this unique use case, highlighting the benefits and offering DIY tips for those interested in creating their own rubber belts for pants.
Rubber Belt for Pants: A Unique Use Case
Rubber belting, traditionally used in heavy-duty machinery, has unique properties that make it suitable for fashion applications. Its durability, flexibility, and distinctive texture provide a fresh alternative to conventional materials like leather or fabric. Fashion designers and DIY enthusiasts alike have begun to experiment with rolls of rubber belting to create belts that are not only functional but also make a bold style statement.
Explanation of How Rubber Belting Can Be Adapted for Fashion
The adaptation of rubber belting for fashion, particularly as belts for pants, involves a creative approach to material use. Rubber belting is cut into strips of appropriate width and length to fit the wearer. These strips are then processed to smooth out any rough edges and to add decorative elements if desired. Buckles and other fastening mechanisms are attached to complete the transformation from industrial material to fashion accessory.
The inherent properties of rubber belting, such as its resistance to wear and tear, make it an excellent choice for belts. Unlike traditional leather belts, rubber belts do not crack or fray easily, maintaining their appearance and functionality over time. Additionally, the flexibility of rubber allows for a comfortable fit, molding to the wearer’s waist without causing discomfort.
Benefits of Using Rubber Belts for Pants
There are several benefits to using rubber belts for pants. First and foremost is durability. Rolls of rubber belting are designed to withstand significant stress and abrasion in industrial settings, so they naturally offer long-lasting performance when repurposed as fashion belts. This means fewer replacements over time, making them a cost-effective choice in the long run.
Another benefit is the unique aesthetic appeal. Rubber belts have a modern, edgy look that can complement various styles, from casual to avant-garde. The texture of rubber adds an interesting visual element that sets these belts apart from their traditional counterparts.
Rubber belts are also highly versatile. They can be easily customized with different colors, patterns, and buckle designs to suit personal tastes. This versatility extends to their functionality as well; rubber belts are often more adjustable than leather belts, providing a better fit for a wider range of body types.
Moreover, rubber belts are eco-friendly. Many rubber belts are made from recycled materials, contributing to sustainability efforts. By repurposing rolls of rubber belting, you are reducing waste and promoting the use of renewable resources.
DIY Tips for Creating Your Own Rubber Belt for Pants
Creating your own rubber belt for pants can be a rewarding project. Here are some DIY tips to help you get started:
- Materials and Tools: Begin by sourcing rolls of rubber belting. These can be purchased from industrial suppliers or salvaged from old machinery. You will also need a sharp utility knife, a metal ruler, a cutting mat, sandpaper, a hole punch, and a belt buckle of your choice.
- Measuring and Cutting: Measure the desired length and width of your belt. Standard belts are typically around 1-2 inches wide, but you can customize this to your preference. Use the metal ruler to ensure straight cuts and the utility knife to slice through the rubber belting on the cutting mat.
- Smoothing the Edges: After cutting, use sandpaper to smooth out the edges of the rubber belt. This step is crucial for comfort and aesthetics, as it prevents rough edges from causing irritation or looking unpolished.
- Adding Holes: Use a hole punch to create evenly spaced holes along one end of the belt. These holes will allow you to adjust the belt to fit your waist. Ensure the holes are appropriately sized for the buckle prong.
- Attaching the Buckle: Secure the buckle to the opposite end of the belt. Depending on the type of buckle, you may need to fold the rubber belt back on itself and secure it with rivets or screws. Make sure the buckle is firmly attached to withstand daily use.
- Customization: Personalize your belt by adding decorative elements. This can include painting, stamping patterns, or attaching embellishments such as studs or rhinestones. Customization allows you to create a belt that reflects your unique style.
- Finishing Touches: Inspect your finished belt for any rough spots or imperfections. Make any necessary adjustments to ensure the belt is both comfortable and visually appealing.
Characteristics of Rolls of Rubber Belting
Rolls of Rubber Belting
Rolls of rubber belting are a fundamental component in numerous industrial applications, providing durability, flexibility, and strength. They are essential in conveying systems across various industries, including mining, manufacturing, and logistics. EP Rubber Belt, known for its enhanced tensile strength and superior resistance to wear, is a popular choice for demanding applications. The primary attributes of rubber belting materials, including EP Rubber Belt, play a crucial role in their effectiveness and longevity. EP Rubber Belt, specifically, offers excellent performance under heavy loads and high-stress conditions, making it ideal for use in high-demand environments. These qualities ensure that rubber belting, including EP Rubber Belt, can withstand the rigors of continuous operation and maintain long-term reliability.
Materials Used in Rubber Belting
Rubber belting is typically manufactured from a range of rubber compounds, each chosen for specific characteristics that enhance performance under different operational conditions. The most common materials used in rolls of rubber belting include:
- Natural Rubber (NR): Known for its excellent elasticity and resilience, natural rubber offers superior flexibility and impact resistance. It is ideal for applications where dynamic stress and high wear are concerns.
- Styrene-Butadiene Rubber (SBR): SBR is widely used due to its balanced properties, including good abrasion resistance and cost-effectiveness. It performs well in general-purpose applications, where moderate mechanical stress and abrasion occur.
- Neoprene (CR): Neoprene is valued for its chemical stability, resistance to oils, and temperature tolerance. It is often used in environments where exposure to oils, solvents, and varying temperatures is expected.
- Nitrile Rubber (NBR): NBR offers excellent resistance to oils, fuels, and other chemicals, making it suitable for industrial settings where these substances are prevalent. It also provides good abrasion and tear resistance.
- Ethylene Propylene Diene Monomer (EPDM): EPDM is notable for its resistance to weathering, ozone, and UV radiation. It is commonly used in outdoor applications where exposure to environmental elements is a concern.
- Polyurethane (PU): Polyurethane belts are known for their exceptional wear resistance and strength. They are ideal for heavy-duty applications where high mechanical stress and continuous operation are required.
Properties Making Rubber Belting Suitable for Industrial Use
The selection of rubber compounds for belting material is driven by the need for specific properties that ensure optimal performance in industrial applications. Some of the critical properties include:
- Abrasion Resistance: Rubber belting must withstand constant friction and wear from moving parts and conveyed materials. High abrasion resistance extends the lifespan of the belts.
- Flexibility: Flexibility allows the belting to adapt to various conveyor configurations and operational stresses without cracking or breaking.
- Tensile Strength: High tensile strength ensures that the belting can endure significant stretching and pulling forces without deforming or snapping.
- Chemical Resistance: Industrial environments often expose belts to oils, solvents, and other chemicals. Chemical-resistant rubber compounds prevent degradation and maintain performance.
- Temperature Resistance: Depending on the application, belting may need to function in extreme temperatures. Rubber compounds that can tolerate high and low temperatures ensure reliability under diverse conditions.
- Impact Resistance: In industries like mining, where heavy materials are conveyed, impact resistance is crucial to prevent damage from sudden shocks and loads.
Comparison of Different Rubber Compounds Used in Belting
Each rubber compound used in rolls of rubber belting offers distinct advantages and potential drawbacks, depending on the specific requirements of the application.
- Natural Rubber (NR):
- Advantages: Excellent elasticity, high tensile strength, and superior flexibility.
- Drawbacks: Limited chemical and heat resistance, not suitable for environments with oils and solvents.
- Styrene-Butadiene Rubber (SBR):
- Advantages: Good abrasion resistance, cost-effective, and balanced mechanical properties.
- Drawbacks: Moderate resistance to chemicals and weathering compared to other compounds.
- Neoprene (CR):
- Advantages: Resistant to oils, chemicals, and temperature variations; good mechanical properties.
- Drawbacks: Higher cost compared to SBR and natural rubber, and can be less flexible.
- Nitrile Rubber (NBR):
- Advantages: Excellent oil and chemical resistance, good abrasion and tear resistance.
- Drawbacks: Limited flexibility at low temperatures, can be more expensive than SBR and NR.
- Ethylene Propylene Diene Monomer (EPDM):
- Advantages: Superior resistance to weathering, ozone, and UV radiation; good heat resistance.
- Drawbacks: Not resistant to oils and fuels, can be less durable in abrasive environments.
- Polyurethane (PU):
- Advantages: Exceptional wear resistance, high tensile strength, and durability.
- Drawbacks: Typically more expensive, can be less flexible than rubber compounds.
Practical Applications of Rolls of Rubber Belting
In industrial settings, the specific rubber compound chosen for belting can significantly impact the efficiency and durability of the conveying system. For example:
- Mining Industry: Requires belting with high abrasion and impact resistance, often using NR or PU for durability.
- Manufacturing: Needs versatile belting that can handle diverse materials and conditions, making SBR and Neoprene popular choices.
- Food Processing: Utilizes belting materials that meet hygienic standards and resist oils and chemicals, where NBR and Neoprene are commonly used.
- Outdoor Conveying Systems: EPDM is preferred for its weather resistance and longevity in harsh environmental conditions.
How about Rolls of Rubber Belting
In the industrial world, rubber belting is a crucial material used in various applications, particularly in conveyor systems. However, the life cycle of these belts doesn’t necessarily end when they are no longer suitable for their original purpose. Rolls of rubber belting, especially used conveyor belt rubber, can be repurposed and sold, providing a cost-effective and environmentally friendly alternative for numerous applications. This section delves into the market for used conveyor belt rubber, essential considerations when purchasing, and recommended suppliers and marketplaces.
Used Conveyor Belt Rubber for Sale
The market for used conveyor belt rubber is diverse and growing, driven by the increasing awareness of sustainability and cost efficiency. These belts, once retired from their primary roles in industries such as mining, manufacturing, and logistics, find new life in various secondary applications. Buyers can acquire rolls of rubber belting at a fraction of the cost of new belts, making it an attractive option for businesses and individuals alike.
Overview of the Market for Used Conveyor Belt Rubber
The market for used conveyor belt rubber encompasses a wide range of industries. Agricultural sectors, for example, use these belts for fencing, livestock mats, and ground cover. Construction companies repurpose them for truck bed liners, mud flaps, and even temporary roadways. In the world of DIY enthusiasts, used conveyor belt rubber is prized for projects like horse stall mats, garden beds, and unique furniture pieces.
The demand for used conveyor belt rubber is not just about cost savings; it also supports sustainable practices. By repurposing these belts, businesses reduce waste and contribute to the circular economy. This trend aligns with the growing consumer and corporate emphasis on environmentally responsible practices, driving the market forward.
Factors to Consider When Purchasing Used Conveyor Belts
When considering the purchase of used conveyor belt rubber, several factors need to be evaluated to ensure the material meets your needs. Here are some critical aspects to keep in mind:
- Condition: Assess the condition of the belts. While used, the belts should still be in good structural condition without excessive wear, tears, or damage that could affect their new intended use. Inspect for cracks, holes, and the integrity of the rubber surface.
- Dimensions: Ensure the belts are available in the dimensions required for your specific application. Rolls of rubber belting come in various widths and thicknesses, so precise measurements are crucial to avoid wastage or the need for additional modifications.
- Material Composition: Different conveyor belts are made from various rubber compounds, each suited for different environments. For example, NN Rubber Belt is known for its excellent resistance to abrasion and high tensile strength, making it ideal for handling heavy loads in demanding applications. Determine the type of rubber and its properties, such as resistance to heat, oil, chemicals, or abrasion, depending on your application needs.
- Source: Consider the origin of the used belts. Belts from heavy industries like mining may have been exposed to harsh conditions, potentially affecting their durability. Conversely, belts from lighter applications may have less wear and tear.
- Price: Compare prices among different suppliers. While cost savings are a significant benefit of used belts, ensure that the price reflects the belt’s condition and remaining lifespan. Extremely low prices may indicate poor quality or heavily worn belts.
- Environmental Impact: Purchasing used conveyor belt rubber contributes to sustainability efforts by reducing waste and the demand for new materials. Consider suppliers who prioritize environmentally friendly practices and have certifications or endorsements that highlight their commitment to sustainability.
Recommended Suppliers and Marketplaces
Finding reliable suppliers and marketplaces is essential to ensure you receive quality used conveyor belt rubber. Here are some recommended sources:
- Industrial Surplus Suppliers: Many companies specialize in industrial surplus, including used conveyor belts. These suppliers often have extensive inventories and can provide belts in various conditions and sizes. Examples include Surplus Conveyors and Rubber Recycling Company.
- Online Marketplaces: Platforms like eBay, Craigslist, and specialized industrial marketplaces such as Machinio offer used conveyor belts. These platforms allow you to compare prices and conditions across a broad range of sellers, providing more options and competitive pricing.
- Recycling Companies: Some recycling companies focus on repurposing industrial materials, including conveyor belts. These companies often ensure that the belts are in good condition and may even offer refurbishment services. Recycled Rubber Products and Sustainable Rubber Solutions are notable examples.
- Direct from Industry: Contacting industries directly, such as mining companies, manufacturing plants, or logistics firms, can sometimes yield excellent deals on used conveyor belts. These companies periodically replace their belts and may sell their used stock at competitive prices.
- Local Suppliers: Local suppliers and dealers often have used conveyor belts available. Visiting these suppliers allows for direct inspection of the belts and immediate purchase without the need for shipping. It also supports local businesses and reduces the environmental impact associated with transportation.
- Trade Shows and Industrial Expos: Attending trade shows and industrial expos can provide opportunities to connect with suppliers of used conveyor belts. These events often feature companies showcasing their surplus materials, offering a chance to negotiate deals and learn more about the product directly from the source.
- Online Auctions: Participating in online industrial auctions can be a way to purchase used conveyor belts at lower prices. Websites like Auction Nation and GovPlanet frequently list industrial equipment, including conveyor belts, where you can bid on items.
- Networking: Building a network within the industry can also lead to opportunities to purchase used conveyor belts. Joining industry groups, attending meetings, and connecting with professionals in related fields can provide insights and leads on available materials.
Finding Rolls of Rubber Belting Near Me
Locating Suppliers for Rolls of Rubber Belting
When searching for rolls of rubber belting, identifying local suppliers can significantly impact both cost and convenience. Whether you’re in need of small quantities for a specific project or large volumes for ongoing industrial applications, sourcing rubber belting nearby offers numerous advantages. Here are some practical tips for locating local suppliers of rubber belting:
- Utilize Online Directories and Search Engines: Start by using online business directories and search engines to find suppliers in your area. Keywords like “rubber belting supplier” or “industrial belting” combined with your location can yield valuable results. Websites such as Google Maps, Yelp, and industry-specific directories can provide listings of nearby suppliers.
- Check Industry Associations and Trade Organizations: Many industry associations and trade organizations have directories of member companies, including suppliers of rubber belting. These directories often include detailed information about each member, such as contact details, product offerings, and areas of expertise. Organizations like the Rubber Manufacturers Association (RMA) or the Conveyor Equipment Manufacturers Association (CEMA) can be valuable resources.
- Visit Trade Shows and Industry Events: Trade shows and industry events are excellent opportunities to meet suppliers face-to-face, view product samples, and discuss your specific needs. These events often attract a wide range of exhibitors, providing a comprehensive overview of available products and services.
- Network with Industry Peers: Reach out to colleagues, industry peers, and business networks to get recommendations for local suppliers. Word-of-mouth referrals can provide insights into the reliability and quality of suppliers based on first-hand experiences.
- Contact Local Chambers of Commerce: Local chambers of commerce often maintain directories of businesses in the area, including suppliers of industrial materials. These directories can be a helpful starting point for identifying potential suppliers.
Importance of Local Sourcing for Reducing Transportation Costs
Sourcing rolls of rubber belting locally can offer significant cost-saving benefits, particularly in terms of transportation. Here’s why local sourcing is essential:
- Reduced Transportation Costs: One of the most obvious advantages of local sourcing is the reduction in transportation costs. Shipping heavy rolls of rubber belting over long distances can be expensive. By sourcing locally, you can minimize or eliminate these shipping costs, leading to substantial savings.
- Faster Delivery Times: Local suppliers can often provide faster delivery times compared to those located further away. This can be particularly beneficial in urgent situations where immediate access to materials is critical.
- Lower Environmental Impact: Reducing the distance that goods need to travel decreases the carbon footprint associated with transportation. Local sourcing supports sustainability initiatives by lowering emissions and conserving energy.
- Enhanced Supplier Relationships: Working with local suppliers can foster stronger relationships and better communication. Proximity allows for more frequent visits, easier coordination, and a deeper understanding of your needs.
Evaluating Nearby Suppliers for Quality and Reliability
Once you’ve identified potential local suppliers for rolls of rubber belting, it’s crucial to evaluate their quality and reliability. Here are some key factors to consider:
- Product Quality: Assess the quality of the rubber belting products offered by the supplier. Look for information on the materials used, manufacturing processes, and any quality control measures in place. Request samples if possible to inspect the products firsthand.
- Supplier Reputation: Research the supplier’s reputation in the industry. Look for reviews, testimonials, and case studies from other customers. A supplier with a strong track record of delivering high-quality products and excellent customer service is more likely to meet your needs.
- Certifications and Standards: Check if the supplier adheres to industry standards and holds relevant certifications. Compliance with standards such as ISO 9001 for quality management systems can be an indicator of a reliable supplier.
- Customer Service and Support: Evaluate the level of customer service and support provided by the supplier. Consider factors such as responsiveness, willingness to answer questions, and the availability of technical support. A supplier who is attentive and supportive can help address any issues that arise.
- Pricing and Payment Terms: Compare pricing and payment terms among different suppliers. While cost should not be the only determining factor, it’s important to ensure that the supplier’s pricing is competitive and aligns with your budget. Also, review their payment terms and conditions for any flexibility that may be beneficial to your business.
- Delivery and Logistics: Consider the supplier’s delivery capabilities and logistics. Assess their ability to deliver products on time and handle any special delivery requirements you may have. Reliable logistics are crucial to maintaining smooth operations and minimizing downtime.
- After-Sales Service: After-sales service is an important aspect of supplier evaluation. Check if the supplier offers any warranties, maintenance services, or support for installation and usage. Good after-sales service can add significant value and provide peace of mind.
Advantages of Sourcing Rolls of Rubber Belting Locally
Sourcing rolls of rubber belting from local suppliers offers multiple advantages that go beyond cost savings. Here are some key benefits:
- Customization and Flexibility: Local suppliers may offer more flexibility in terms of customization. They can work closely with you to tailor their products to meet your specific requirements, providing solutions that are perfectly suited to your needs.
- Stronger Community Ties: Supporting local businesses helps strengthen the local economy and community. By choosing local suppliers, you contribute to the growth and sustainability of businesses in your area, fostering a sense of community and mutual support.
- Quick Issue Resolution: Proximity to local suppliers allows for quicker resolution of any issues that may arise. Whether it’s a quality concern, a need for additional products, or a logistical challenge, local suppliers can respond more promptly and effectively.
- Better Communication: Face-to-face meetings and site visits are more feasible with local suppliers. This can enhance communication, leading to better collaboration and understanding. Effective communication is key to ensuring that your needs are met and that any potential problems are addressed swiftly.
The Keys of Rolls of Rubber Belting
Rubber belting plays a critical role in various industrial applications due to its durability, flexibility, and resistance to different environmental factors. Among the different types and thicknesses of rubber belting available, 1/4 inch thick rubber belting stands out for its specific uses and advantages in various industrial scenarios. In this section, we will explore the applications of 1/4 rubber belting, discuss the advantages of this particular thickness, and provide case studies of successful applications.
Applications of 1/4 Rubber Belting
1/4 inch thick rubber belting, often supplied in rolls of rubber belting, is highly versatile and used in numerous industrial and commercial applications. This specific thickness provides a balance of strength and flexibility, making it suitable for a variety of tasks.
Specific Uses of 1/4 Inch Thick Rubber Belting
1/4 inch rubber belting is commonly used in the following applications:
Conveyor Systems: One of the primary uses of 1/4 inch rubber belting is in conveyor systems. This thickness is ideal for handling medium-weight loads, providing sufficient durability without being excessively heavy. It is used in industries such as packaging, manufacturing, and food processing where reliable material transport is essential.
Protective Coverings: In industrial environments, machinery and surfaces often require protection from wear and tear. Rolls of rubber belting in 1/4 inch thickness are used as protective coverings for equipment, floors, and walls. This application helps in reducing damage and prolonging the lifespan of expensive machinery.
Skirting and Sealing: Rubber belting is also used as skirting material in conveyor systems to prevent spillage and ensure smooth operation. The 1/4 inch thickness provides adequate flexibility to form tight seals while maintaining durability to withstand constant abrasion.
Agricultural Uses: In agriculture, 1/4 inch rubber belting is used for making chute liners, silo liners, and other protective linings. It is resistant to weather conditions and can handle the rough treatment often encountered in farming activities.
Impact and Vibration Dampening: This thickness of rubber belting is excellent for applications requiring impact and vibration dampening. It is used in industrial mats, bumpers, and pads where cushioning is needed to protect equipment and structures.
Automotive Applications: In the automotive industry, 1/4 inch rubber belting is used for making mud flaps, gaskets, and seals. Its resilience and resistance to oil and chemicals make it suitable for these demanding environments.
Advantages of 1/4 Inch Thick Rubber Belting in Different Industrial Scenarios
Using 1/4 inch thick rubber belting offers several advantages across various industrial applications. These advantages include:
Durability: The thickness provides a robust solution that can withstand significant wear and tear. It is less likely to crack or degrade under harsh conditions, making it a long-lasting material choice.
Flexibility: Despite its durability, 1/4 inch rubber belting retains enough flexibility to be used in applications requiring tight seals or cushioning. This balance of strength and flexibility is crucial in many industrial settings.
Resistance to Environmental Factors: Rubber belting is inherently resistant to various environmental factors such as moisture, chemicals, and extreme temperatures. This makes it suitable for outdoor and harsh industrial environments.
Cost-Effectiveness: Investing in rubber belting rolls at this thickness can be cost-effective over time. Its longevity reduces the need for frequent replacements, saving on maintenance and material costs.
Ease of Installation and Maintenance: 1/4 inch rubber belting is relatively easy to handle and install. Its manageable weight and flexibility simplify installation, while its durability ensures minimal maintenance requirements.
Case Studies of Successful Applications
Case Study 1: Food Processing Plant
A food processing plant required a durable conveyor belt system to handle the transportation of various food products. The plant opted for rolls of rubber belting in 1/4 inch thickness due to its suitability for medium-weight loads and resistance to moisture and food-related chemicals. The installation of 1/4 inch rubber belting improved the efficiency and reliability of the conveyor system, reducing downtime and maintenance costs. The belting’s easy-to-clean surface also helped in maintaining hygiene standards, crucial in the food industry.
Case Study 2: Agricultural Equipment Manufacturer
An agricultural equipment manufacturer needed a solution for protecting the interior surfaces of silos and chutes. They chose 1/4 inch rubber belting for its ability to withstand the abrasive nature of grain and other agricultural products. The rubber belting was cut and installed as liners, significantly extending the life of the equipment by preventing wear and tear. This application demonstrated the material’s durability and effectiveness in a demanding agricultural setting.
Case Study 3: Automotive Parts Supplier
An automotive parts supplier was looking for a material to use for mud flaps that could endure the harsh conditions of the road. They selected 1/4 inch rubber belting due to its excellent resistance to oil, chemicals, and physical abrasion. The resulting mud flaps provided superior protection for vehicles, reducing maintenance needs and enhancing vehicle longevity. This application highlighted the material’s resilience and suitability for automotive use.
Case Study 4: Industrial Manufacturing Facility
An industrial manufacturing facility required vibration dampening mats for heavy machinery to reduce noise and prevent damage to the floor. Rolls of 1/4 inch rubber belting were used to create custom-sized mats placed under the machinery. These mats effectively absorbed vibrations, leading to a quieter and safer working environment. The durability of the rubber belting ensured that the mats remained functional over long periods, demonstrating the material’s impact resistance and longevity.
Case Study 5: Warehouse Operations
A large warehouse faced issues with product spillage and conveyor system inefficiency. By installing 1/4 inch rubber belting as skirting on their conveyors, they significantly reduced product loss and improved operational efficiency. The flexible yet durable nature of the rubber belting allowed it to form effective seals, preventing materials from falling off the conveyor belts. This application showcased the practical benefits of using rubber belting in logistics and warehousing.
Exploring Used Rubber Belting
Benefits of Using Second-Hand Rubber Belting
When it comes to industrial applications, the use of second-hand rubber belting offers several significant benefits. Rolls of rubber belting are often replaced in various industries long before their functional life ends. This practice opens up opportunities for other businesses to take advantage of quality materials at a fraction of the cost.
- Cost Savings: One of the most compelling reasons to consider used rubber belting is the cost savings. New belting can be expensive, especially for large-scale operations. By opting for second-hand belting, businesses can significantly reduce their expenditure on materials while still maintaining operational efficiency.
- Proven Durability: Used rolls of rubber belting have already been put to the test in real-world conditions. This means their durability and performance have been proven, providing peace of mind that they can handle demanding industrial environments. If the belting is still in good condition after previous use, it is likely to continue performing well.
- Availability: Used rubber belting is often readily available and can be sourced quickly compared to new belts, which may require lead time for production and delivery. This immediate availability can be crucial in situations where a quick replacement is needed to minimize downtime.
- Environmental Benefits: Reusing materials is inherently more sustainable than producing new ones. By opting for second-hand rolls of rubber belting, businesses can reduce their environmental footprint, supporting recycling efforts and minimizing waste. This aligns with global trends toward more sustainable and eco-friendly industrial practices.
Cost-Effectiveness and Environmental Impact
The cost-effectiveness and environmental impact of using used rubber belting are intertwined, offering dual benefits that can enhance both the financial and ecological performance of a business.
- Lower Purchase Costs: As mentioned, the primary financial advantage of used belting is the lower purchase cost. This can free up budgetary resources for other critical areas, such as maintenance, upgrades, or expansion. Additionally, lower material costs can improve the overall profitability of operations.
- Reduced Disposal Costs: By reusing rolls of rubber belting, businesses can also save on disposal costs. Disposing of industrial belting can be costly and environmentally taxing. Reusing these materials mitigates these costs and the associated environmental impact.
- Energy Savings: Manufacturing new rubber belting consumes significant energy resources. By reusing existing materials, the energy demand associated with production is reduced, leading to lower overall energy consumption and a smaller carbon footprint.
- Waste Reduction: Utilizing second-hand belting helps divert materials from landfills, contributing to waste reduction. This practice supports broader environmental goals and regulatory compliance related to waste management and sustainability.
Where to Find Quality Used Rubber Belting
Finding quality used rolls of rubber belting requires knowing where to look and what to consider during the purchasing process. Here are some tips to help you source reliable second-hand rubber belting:
- Specialized Suppliers: There are suppliers who specialize in used industrial materials, including rubber belting. These suppliers often have a wide selection of belts in various conditions and can provide detailed information about the history and performance of the belting.
- Industrial Auctions: Industrial auctions can be a great place to find used rubber belting. Companies that are closing down or upgrading their equipment often sell their used materials at these auctions. Participating in these events can yield high-quality belting at competitive prices.
- Online Marketplaces: Websites like eBay, Craigslist, and industry-specific platforms can offer a range of used belting options. These platforms allow you to compare prices, conditions, and sellers’ reputations, helping you make an informed purchase.
- Networking: Industrial networks and professional associations can be valuable resources for finding used rubber belting. Networking with other professionals in your industry can lead to recommendations and contacts who have surplus belting available.
- Local Businesses: Sometimes local businesses that use rubber belting in their operations may have surplus stock or retired belts they are willing to sell. Reaching out to these businesses directly can uncover opportunities to purchase used belting nearby.
- Inspection and Evaluation: Before purchasing used belting, it is crucial to inspect and evaluate the materials thoroughly. Look for signs of wear and tear, such as cracks, fraying, or thinning, which could affect performance. Ensure the belting meets your specifications and operational requirements.
- Reputable Dealers: When purchasing used rolls of rubber belting, it’s important to deal with reputable suppliers who can provide assurance of quality and reliability. Check reviews, ask for references, and ensure the supplier has a track record of delivering good-quality used materials.
FAQS about Rolls of Rubber Belting
Conveyor belts are typically made from a variety of rubber compounds, each designed to meet specific application requirements. The most common types of rubber used in conveyor belts include natural rubber, SBR (styrene-butadiene rubber), neoprene, nitrile, and EPDM (ethylene propylene diene monomer). Natural rubber offers excellent flexibility and abrasion resistance, making it suitable for general-purpose applications. SBR is known for its durability and cost-effectiveness, while neoprene provides good chemical and heat resistance. Nitrile rubber is ideal for applications involving oils and fats due to its oil-resistant properties. EPDM rubber is used in environments with high temperatures and exposure to weather elements, as it offers excellent heat and weather resistance. Each type of rubber provides specific benefits, allowing conveyor belts to perform effectively in various industrial conditions.
The best way to cut rubber belting depends on the thickness and type of the belt. For thin rubber belts, a sharp utility knife or a pair of heavy-duty scissors can be used. It is essential to ensure a straight and clean cut to maintain the integrity of the belt. For thicker or reinforced rubber belts, a specialized cutting tool, such as a belt cutter or a band saw, may be required. When using a band saw, it is crucial to use a blade designed for cutting rubber to avoid damaging the belt. Safety precautions, such as wearing protective gloves and goggles, should be taken to prevent injuries during the cutting process. Ensuring the cut edges are smooth and free from frays is essential for the belt’s longevity and performance.
Rubber belting is a type of material made from rubber compounds and often reinforced with fabric or steel cords to enhance its strength and durability. It is commonly used in conveyor systems to transport materials from one point to another. Rubber belts come in various thicknesses, widths, and lengths, depending on the specific application requirements. The rubber compounds used in belting are designed to withstand wear, abrasion, and extreme temperatures, making them suitable for heavy-duty applications. Rubber belting is known for its flexibility, high tensile strength, and resistance to various environmental factors, making it an essential component in many industrial operations.
Rubber belting is a versatile material widely used in various industrial applications. It is primarily used for conveying materials in different sectors, such as mining, agriculture, manufacturing, and logistics. In mining, rubber belting is crucial for transporting ores and minerals efficiently. In agriculture, it helps in moving bulk materials like grain, seeds, and fertilizers. Manufacturing industries utilize rubber belting to handle products on assembly lines, ensuring smooth and continuous production processes. Logistics and warehousing sectors depend on rubber belting for efficient sorting and distribution of goods. Additionally, rubber belting finds use in power transmission applications, providing reliable and durable performance in machinery and equipment.
Last Updated on December 5, 2024 by Jordan Smith
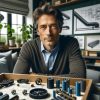
Jordan Smith, a seasoned professional with over 20 years of experience in the conveyor system industry. Jordan’s expertise lies in providing comprehensive solutions for conveyor rollers, belts, and accessories, catering to a wide range of industrial needs. From initial design and configuration to installation and meticulous troubleshooting, Jordan is adept at handling all aspects of conveyor system management. Whether you’re looking to upgrade your production line with efficient conveyor belts, require custom conveyor rollers for specific operations, or need expert advice on selecting the right conveyor accessories for your facility, Jordan is your reliable consultant. For any inquiries or assistance with conveyor system optimization, Jordan is available to share his wealth of knowledge and experience. Feel free to reach out at any time for professional guidance on all matters related to conveyor rollers, belts, and accessories.