Rubber Belt Conveyor System | Industry Applications
Rubber belt conveyor systems have revolutionized the way industries handle materials, offering a seamless and efficient method for moving goods across facilities. These systems, characterized by a looped belt made of durable rubber, are pivotal in various sectors, including manufacturing, mining, and packaging. The inception of conveyor systems dates back to the late 19th century, but it was the introduction of rubber belts that marked a significant leap in their evolution. This innovation provided unmatched durability and flexibility, allowing for the transportation of a wide range of materials over long distances. The rubber belt conveyor system quickly became a staple in industrial operations, heralding a new era of productivity and operational efficiency. Its adaptability and robustness have made it an indispensable tool in the modern industrial landscape.Rubber belt conveyor systems are indispensable in various industries due to their ability to handle different types of materials efficiently and reliably. The choice of rubber material ensures resistance to wear, tear, and environmental conditions.
What Is The Rubber Belt Conveyor System?
A rubber belt conveyor system is a transportation mechanism designed to move materials from one location to another efficiently and continuously. It is widely used in various industries, including mining, manufacturing, agriculture, and logistics, to transport bulk materials or packaged goods.
Components of a Rubber Belt Conveyor System
Rubber Belt: The core component of the system, typically made from layers of rubber and fabric to provide flexibility, strength, and durability.
Pulleys: These are used to support and guide the belt. Key types include:
- Drive Pulley: Powers the conveyor.
- Tail Pulley: Returns the belt to the drive pulley.
Idlers: Support the belt and load, ensuring smooth movement.
Motor: Provides the necessary power to move the belt.
Frame: The structure that supports the entire system.
Belt Cleaner: Maintains the belt by removing any residue, ensuring efficiency and longevity.
How It Works
The rubber belt conveyor system operates by using a continuous loop of rubber belt that rotates around two or more pulleys. The belt is driven by a motor, usually connected to the drive pulley. The material to be transported is placed on the belt, which moves it from the loading point to the unloading point. The speed and direction of the belt can be adjusted according to the specific requirements of the operation.
Advantages of Rubber Belt Conveyor Systems
- Durability: Rubber belts are resistant to wear and tear, making them suitable for handling abrasive materials.
- Flexibility: Can be used for both horizontal and inclined transportation.
- Efficiency: Capable of moving large volumes of materials quickly and continuously.
- Versatility: Suitable for a wide range of materials, including granular, lumpy, or packaged goods.
- Low Maintenance: Requires minimal maintenance compared to other types of conveyors.
Rubber belt conveyor systems are indispensable in various industries due to their ability to handle different types of materials efficiently and reliably. Their robust construction, flexibility, and low maintenance requirements make them a preferred choice for many material handling applications.
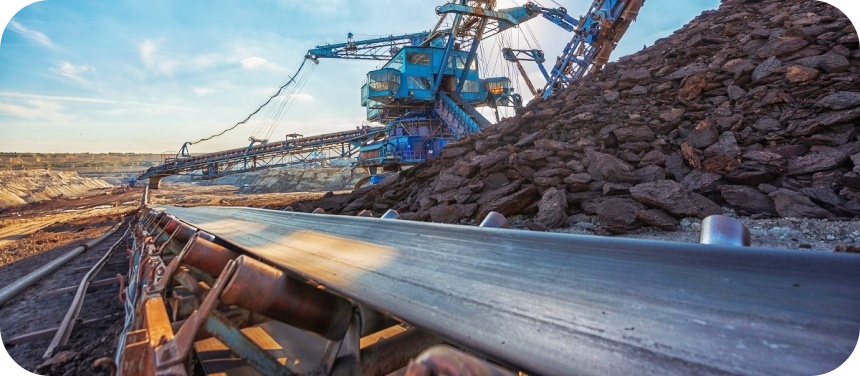
Components and Functions of a Rubber Belt Conveyor System
A rubber belt conveyor system is a sophisticated assembly of various components, each playing a crucial role in its operation. Understanding these components and their functions is essential for optimizing the system’s efficiency and longevity.
- Rubber Belt: The heart of the system, the rubber belt, is designed for durability and flexibility. It serves as the carrying medium for materials from one point to another. The choice of rubber material ensures resistance to wear, tear, and environmental conditions, making it suitable for a wide range of applications.
- Pulleys: Pulleys are critical in directing the movement of the rubber belt. The drive pulley, powered by the motor, imparts motion to the belt, while the tail pulley provides tension and guidance, ensuring the belt operates smoothly. Pulleys are strategically placed to support and redirect the belt’s path.
- Motors: The motor is the driving force behind the rubber belt conveyor system. It powers the drive pulley, which in turn moves the belt. The motor’s specifications, including power and speed, are selected based on the system’s load requirements and operational needs.
- Idlers: Idlers support the rubber belt and materials being conveyed. They are spaced along the conveyor’s length and can be adjusted to control the belt’s shape and tension. Idlers reduce friction and wear on the belt, contributing to the system’s overall efficiency.
- Conveyor Frame: The frame provides structural support for the rubber belt conveyor system, holding the pulleys, motor, and idlers in place. It is designed to withstand the load of the materials being transported, as well as the stress exerted by the moving belt.
- Control Systems: Control systems regulate the operation of the rubber belt conveyor system. They can adjust the speed, monitor the load, and provide safety features like emergency stops. Control systems ensure the conveyor operates within its designed parameters, enhancing safety and efficiency.
Each component of a rubber belt conveyor system is integral to its function, working in harmony to transport materials efficiently. Understanding these components helps in maintaining the system effectively, ensuring a long and productive service life.
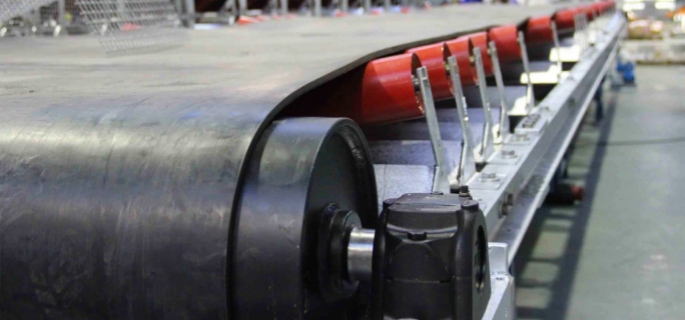
Types of Rubber Belt Conveyor Systems
The versatility of rubber belt conveyor systems is evident in the variety of types available, each designed to meet specific industrial needs. Below is a table that explores the different types of rubber belt conveyors, highlighting their advantages and specific applications:
Each type of rubber belt conveyor system is engineered to fulfill specific operational requirements, enhancing efficiency and productivity in various industrial settings.
Heavy Rubber Belt Conveyor System
A heavy rubber belt conveyor system is designed to handle substantial loads and operate in demanding industrial environments. These systems are robust and engineered to transport large, bulky, or abrasive materials efficiently and reliably, making them essential for heavy-duty applications.
Components of a Heavy Rubber Belt Conveyor System
Heavy-Duty Rubber Belt: Composed of multiple layers of reinforced rubber to withstand heavy loads and abrasive materials.
Heavy-Duty Pulleys: Engineered to support significant weight and tension. Key types include:
- Drive Pulley: Provides the necessary power to move the belt.
- Tail Pulley: Returns the belt to the drive pulley.
Reinforced Idlers: Support the belt and heavy loads, ensuring smooth operation.
High-Power Motor: Delivers the torque needed to move heavy materials.
Sturdy Frame: Constructed from high-strength materials to support the entire system and withstand heavy loads.
Belt Cleaner: Maintains the belt by removing residue and debris, ensuring optimal performance.
Looking for durable conveyor belts? Contact us for more information.
Applications of Heavy Rubber Belt Conveyor Systems
Mining and Quarrying
- Application: Transporting heavy materials such as ores, coal, and aggregates.
- Benefits: High durability and load capacity, essential for handling abrasive and heavy materials.
Construction
- Application: Moving construction materials like sand, gravel, cement, and debris.
- Benefits: Robust construction capable of withstanding harsh environments and heavy usage.
Bulk Material Handling
- Application: Conveying large volumes of bulk materials in ports, power plants, and industrial facilities.
- Benefits: Efficient and continuous operation, reducing manual handling and increasing throughput.
Recycling and Waste Management
- Application: Transporting heavy recyclable materials and waste products.
- Benefits: Enhanced durability and resistance to wear and tear, improving operational efficiency.
Steel and Metal Processing
- Application: Handling heavy steel products, scrap metal, and raw materials.
- Benefits: Ability to manage high temperatures and abrasive conditions, ensuring longevity and reliability.
Advantages of Heavy Rubber Belt Conveyor Systems
- High Load Capacity: Designed to transport large and heavy materials, essential for demanding industrial applications.
- Durability: Resistant to wear, tear, and abrasion, ensuring long-term operation in harsh environments.
- Efficiency: Capable of moving large volumes of materials continuously, optimizing productivity.
- Versatility: Suitable for a wide range of heavy-duty applications across various industries.
- Safety: Reduces the need for manual handling of heavy materials, enhancing workplace safety and reducing the risk of injuries.
Key Considerations for Selecting a Heavy Rubber Belt Conveyor System
Material Characteristics: Consider the type, size, and abrasiveness of the materials to be transported.
Load Requirements: Ensure the system can handle the maximum expected load.
Environmental Conditions: Choose materials and components that can withstand the specific conditions, such as extreme temperatures or exposure to chemicals.
Maintenance Needs: Select a system that offers easy maintenance and minimal downtime.
Customization: Look for customizable options to meet specific application requirements.
Heavy rubber belt conveyor systems are vital for industries that require the transportation of large, bulky, or abrasive materials. Their robust design, high load capacity, and durability make them suitable for demanding applications in mining, construction, bulk material handling, recycling, and steel processing. Investing in a high-quality heavy rubber belt conveyor system can significantly enhance operational efficiency, safety, and productivity in industrial environments.
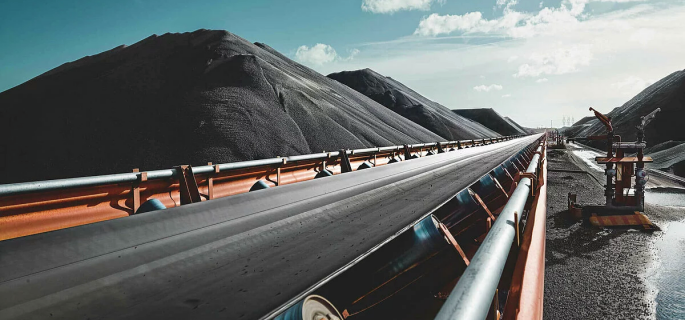
Design and Manufacturing of Rubber Belt Conveyor Systems
The creation of a rubber belt conveyor system is a meticulous process that involves detailed design and precise manufacturing techniques. This process ensures that the conveyor system meets the specific needs of various industries, from mining to food processing.
- Initial Design Phase: The journey of a rubber belt conveyor system begins with the initial design phase, where engineers assess the requirements, including the type of materials to be transported, the distance, the load capacity, and the environmental conditions. This phase determines the specifications for the rubber belt, the motor, the frame, and other components.
- Material Selection: Selecting the right materials for the rubber belt is crucial. The choice depends on the application, with factors such as temperature resistance, chemical exposure, and wear resistance being considered. Materials range from natural rubber to synthetic compounds like neoprene or silicone.
- Calendering Process: In this stage, the selected rubber material is processed through a series of rollers in the calendering machine. This process ensures the rubber reaches the desired thickness and width, forming a uniform sheet that will become the conveyor belt’s surface.
- Reinforcement Layer Addition: To enhance the durability and strength of the conveyor belt, reinforcement layers, often made of fabric or metal, are added. This step is crucial for heavy-duty applications where the belt must withstand high tensions and loads.
- Vulcanizing Process: The vulcanization process is where the rubber belt truly comes to life. Under high pressure and temperature, the rubber is cured, and the various layers are bonded together. This process gives the conveyor belt its final properties, such as elasticity and strength.
- Quality Control: After vulcanization, the belt undergoes rigorous conveyor belt testing to ensure it meets all specifications and quality standards. The quality tests may include tensile strength, elongation, abrasion resistance, and other relevant parameters.
- Customization: Manufacturers play a vital role in customizing the conveyor system to meet specific industry needs. This can involve adjusting the belt’s width, thickness, surface texture, and even the type of splice used to join the belt ends.
- Assembly and Installation: The final step involves assembling the conveyor system, including the installation of the rubber belt, pulleys, motors, and control systems. Manufacturers often provide support during installation to ensure the system operates as intended.
The design and manufacturing of a rubber belt conveyor system are complex processes that require expertise and precision. Manufacturers are key in ensuring that each conveyor system is tailored to meet the unique demands of different industrial applications, ensuring efficiency and reliability in material handling.
Applications of Rubber Belt Conveyor Systems
Diverse Applications
Rubber belt conveyor systems are integral to numerous industries, facilitating the efficient and safe transport of materials. Their versatility and durability make them suitable for a wide range of applications:
- Mining: In the mining industry, rubber belt conveyors are used to transport ore and minerals from the mining site to processing facilities, handling heavy loads and rough conditions.
- Agriculture: Conveyors are used in agriculture for moving grain, seeds, and other products, helping in the sorting, cleaning, and distribution processes.
- Manufacturing: Manufacturing plants utilize these systems for the assembly line, moving parts and finished products through various stages of production.
- Packaging: In packaging facilities, rubber belt conveyors streamline the process of moving products into packaging stations and final dispatch.
- Food Processing: These systems are designed with food-grade materials to transport ingredients, processed food, and packaged items within food processing plants.
- Pharmaceuticals: Conveyors in the pharmaceutical industry are used for the careful handling of sensitive medical products and materials through production lines.
- Recycling: Rubber belt conveyors play a crucial role in recycling plants, sorting and transporting recyclable materials efficiently.
- Airports: Baggage handling systems at airports rely on these conveyors for the swift and secure movement of luggage.
- Retail: In large distribution centers, conveyors are used to move goods from storage to shipping areas, optimizing logistics and inventory management.
- Construction: Conveyors are used on construction sites to move materials across different levels, aiding in the efficient management of resources.
Case Studies
- Mining Success: A mining company implemented a rubber belt conveyor system to transport coal over 2 kilometers from the mine to the processing plant, resulting in a 20% increase in production efficiency.
- Agricultural Efficiency: A large farm introduced conveyors for grain handling, significantly reducing the time and labor required to move produce from storage to market.
- Manufacturing Innovation: An automotive manufacturer integrated a series of rubber belt conveyors into their assembly line, cutting down vehicle assembly time by 30%.
- Packaging Revolution: A packaging facility adopted a high-speed rubber belt conveyor system, doubling their packaging capacity and reducing manual labor.
- Food Processing Upgrade: A food processing plant replaced their old conveyor system with a state-of-the-art rubber belt conveyor, enhancing hygiene and processing speed.
- Recycling Impact: A recycling center installed a specialized rubber belt conveyor system for sorting recyclables, improving sorting efficiency by 25% and reducing contamination.
These applications and case studies showcase the broad utility and significant impact of rubber belt conveyor systems across various sectors, highlighting their role in enhancing productivity and operational efficiency.
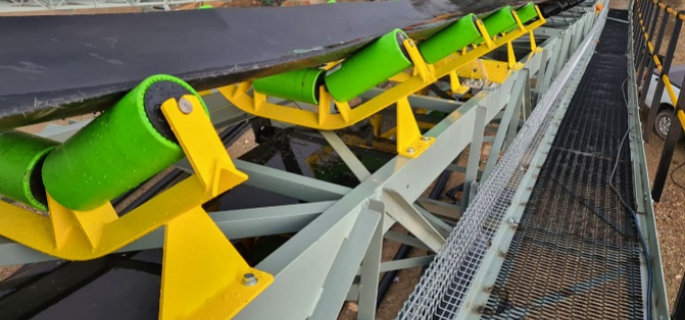
Rubber Belt Conveyor System for Industry Applications
A rubber belt conveyor system is a crucial component in various industrial processes, providing efficient and continuous material handling solutions. These systems are designed to move bulk materials, packages, and products within a facility or from one location to another, optimizing workflow and productivity.
Advantages of Rubber Belt Conveyor Systems in Industry Applications
- Durability: Rubber belts are resistant to wear, chemicals, and extreme temperatures, ensuring longevity in harsh industrial environments.
- Flexibility: Can be customized to suit various industrial applications, including horizontal, inclined, and vertical conveying.
- Capacity: Capable of handling large volumes of materials, making them suitable for high-demand industrial operations.
- Efficiency: Continuous operation reduces downtime and increases throughput, optimizing overall production efficiency.
- Safety: Reduced manual handling and ergonomic design improve workplace safety and reduce the risk of injuries.
Rubber belt conveyor systems are indispensable in industrial applications due to their versatility, durability, and efficiency. They play a vital role in optimizing material handling processes across various industries, contributing to increased productivity, cost savings, and operational excellence. Investing in a reliable rubber belt conveyor system can significantly enhance the efficiency and profitability of industrial operations.
Find the perfect conveyor belt solution – get in touch today.
Custom Rubber Belt Conveyor System
A custom rubber belt conveyor system is tailored to meet the specific needs and requirements of an industry or application. By designing a conveyor system that addresses unique operational demands, businesses can achieve enhanced efficiency, productivity, and reliability.
Key Features of a Custom Rubber Belt Conveyor System
- Tailored Design: Customized dimensions, configurations, and components to fit specific operational spaces and requirements.
- Material Selection: Choice of rubber belt materials to suit different applications, such as high heat resistance, abrasion resistance, or chemical resistance.
- Load Capacity: Designed to handle specific load requirements, whether light, medium, or heavy-duty.
- Speed and Control: Adjustable speed settings and control systems to match the pace of production or material handling needs.
- Safety Features: Inclusion of safety guards, emergency stop buttons, and sensors to ensure safe operation.
- Integration: Capability to integrate with existing systems and processes for seamless operation.
Benefits of Custom Rubber Belt Conveyor Systems
- Optimized Performance: Customized solutions ensure optimal performance for specific tasks, enhancing overall efficiency.
- Flexibility: Ability to adapt to various layouts and operational changes, providing long-term usability and scalability.
- Cost Efficiency: Reduces unnecessary features and components, focusing on what is essential for the application, potentially lowering costs.
- Enhanced Durability: Use of high-quality, application-specific materials to ensure longevity and minimal downtime.
- Improved Safety: Custom safety features reduce the risk of accidents and improve workplace safety.
Designing a Custom Rubber Belt Conveyor System
- Assessment: Conduct a thorough assessment of the operational needs, including material characteristics, load capacities, and workflow.
- Planning: Collaborate with conveyor system designers to plan the layout and specifications.
- Material Selection: Choose the appropriate rubber belt materials and other components based on the specific application requirements.
- Prototyping: Develop prototypes to test and refine the design.
- Installation and Integration: Install the custom system and integrate it with existing processes and machinery.
- Testing and Training: Conduct comprehensive testing to ensure performance and safety. Provide training for operators to maximize the system’s benefits.
A custom rubber belt conveyor system is an excellent investment for industries with specific material handling needs. By tailoring the design, materials, and features to match unique operational demands, businesses can achieve significant improvements in efficiency, productivity, and safety. Whether in automotive manufacturing, food processing, pharmaceuticals, e-commerce, or agriculture, a custom conveyor system provides the flexibility and performance necessary to excel in today’s competitive market.
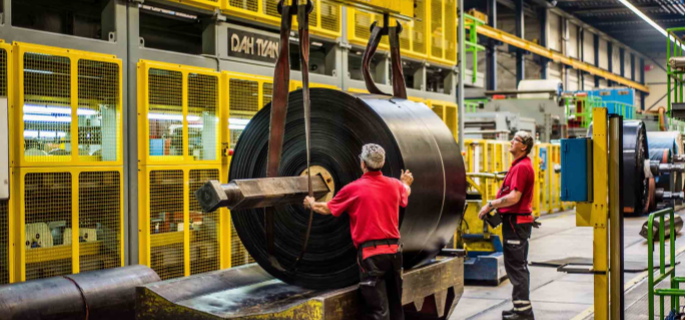
Choosing the Right Rubber Belt Conveyor System
Factors to Consider
Selecting the appropriate rubber belt conveyor system is crucial for ensuring operational efficiency and longevity. Here are eight key factors to consider:
- Material Handling Requirements: Understand the types of materials the conveyor will transport. Consider their weight, size, shape, and abrasiveness to determine the suitable belt type and strength.
- Environment: The operating environment significantly impacts the choice of conveyor. Factors such as temperature, humidity, exposure to chemicals, and outdoor or indoor use dictate the material and design of the conveyor system.
- Load Capacity: Assess the maximum load the conveyor needs to handle. This includes both the weight and volume of materials per time unit, ensuring the system’s components can withstand the operational demands.
- Conveyor Length and Speed: The required length and speed of the conveyor influence the motor’s power and the belt’s durability. Longer systems with higher speeds require more robust materials and components.
- Incline or Decline Angles: If the conveyor needs to move materials up or down, the incline or decline angle affects the belt’s design, such as the inclusion of cleats or sidewalls to prevent slippage.
- Integration with Existing Systems: The new conveyor should seamlessly integrate with existing material handling systems. Compatibility in terms of speed, control systems, and material flow is essential.
- Safety Features: Safety is paramount. Features like emergency stops, guards, and warning signals are critical, especially in environments with high human interaction.
- Maintenance and Durability: Consider the ease of maintenance and the durability of the conveyor system. Durable materials and accessible components reduce downtime and extend the system’s lifespan.
Importance of Selecting the Right Type
The importance of selecting the right type of belt material and design cannot be overstated, as it directly impacts the conveyor’s performance and reliability:
- Material Compatibility: The belt material should be compatible with the materials being conveyed to prevent damage to both the product and the conveyor.
- Abrasion Resistance: For handling abrasive materials, the belt should have high abrasion resistance to prolong its service life.
- Chemical Resistance: In environments where chemicals are present, the belt material must resist degradation to maintain its integrity.
- Temperature Tolerance: The belt should withstand the operating temperatures, whether they are high due to the materials being moved or low due to environmental conditions.
- Strength and Flexibility: The belt must be strong enough to handle the load and flexible enough to navigate the conveyor’s path, especially around curves and inclines.
- Hygiene Requirements: For food processing applications, the belt material must meet hygiene standards and be easy to clean.
- Impact Resistance: The ability to absorb impacts from materials being loaded onto the conveyor is crucial to prevent damage.
- Electrical Properties: In certain applications, the belt may need to be antistatic or conductive to prevent the buildup of static electricity.
- Customization Options: The ability to customize the belt, such as the inclusion of cleats, sidewalls, or specific coatings, can be crucial for certain applications.
Choosing the right rubber belt conveyor system involves a thorough assessment of these factors and an understanding of how they impact the system’s performance in specific applications.
Pricing of Rubber Belt Conveyor Systems
The cost of a rubber belt conveyor system can be influenced by a myriad of factors, making it essential for potential buyers to understand what drives pricing in this market. Additionally, obtaining competitive quotes and choosing the right manufacturer are crucial steps in the procurement process.
Factors Influencing Price
- Material Quality: The type and quality of rubber and other materials used in the conveyor system can significantly affect the price.
- System Size and Length: Larger and longer conveyor systems require more materials and labor, increasing the cost.
- Load Capacity: Conveyor belt systems designed to handle heavier loads need to be more robust, which can drive up the price.
- Design Complexity: Custom features and complex designs that require additional engineering and manufacturing efforts can increase costs.
- Brand Reputation: Established brands with a proven track record may command higher prices due to their reliability and service quality.
- Technological Features: Advanced features like integrated sensors, automation compatibility, and energy-efficient designs can add to the cost.
- Installation and Maintenance: The ease of installation and the level of ongoing maintenance required can influence the overall cost of ownership.
- Market Demand and Raw Material Costs: Fluctuations in market demand and the prices of raw materials can also impact the pricing of conveyor systems.
Getting Competitive Quotes
- Clearly Define Your Needs: Provide detailed specifications of your requirements to ensure accurate and comparable quotes.
- Request Quotes from Multiple Manufacturers: Reach out to several suppliers to compare prices, features, and services.
- Evaluate Total Cost of Ownership: Consider not just the purchase price but also maintenance, operational, and potential downtime costs.
- Check References and Reviews: Look at past projects and customer testimonials to gauge the manufacturer’s reliability and quality of work.
- Negotiate Terms: Don’t hesitate to negotiate on price, warranty terms, and after-sales support services.
- Consider Lead Times: Factor in the delivery and installation times, as these can affect your project timelines.
- Ask About Customization Costs: If your system requires customization, understand how these changes will impact the final price.
Maintenance and Safety of Rubber Belt Conveyor Systems
Proper maintenance and adherence to safety protocols are paramount for the longevity and efficient operation of rubber belt conveyor systems. Here are ten maintenance tips followed by essential safety practices:
Maintenance Tips
- Regular Inspections: Conduct routine inspections of the rubber belt, looking for signs of wear, tears, or misalignment. Early detection of issues can prevent more significant problems.
- Cleanliness: Keep the conveyor belt and components clean from debris and materials that can cause damage or inefficiency.
- Lubrication: Regularly lubricate moving parts like bearings and rollers to reduce friction and wear.
- Tension Adjustment: Ensure the belt is properly tensioned. Over or under-tensioning can lead to inefficiencies and increased wear.
- Alignment Checks: Regularly check and adjust the alignment of the belt and rollers to prevent uneven wear and potential derailment.
- Pulley and Roller Inspection: Inspect pulleys and rollers for wear or damage. Replace any components that are not functioning correctly.
- Electrical System Checks: For motorized systems, regularly inspect electrical connections and controls to ensure they are in good working order.
- Splice Monitoring: Monitor the condition of belt splices and repair or replace them as needed to maintain belt integrity.
- Training and Tracking: Adjust the tracking of the conveyor belt to ensure it runs centrally on the pulleys and rollers.
- Preventive Replacement: Replace parts that are near the end of their service life before they fail to minimize downtime.
Safety Protocols
- Emergency Stops: Ensure that emergency stop buttons are accessible along the length of the conveyor and that they are tested regularly.
- Guarding: Install guards around moving parts to protect workers from pinch points and entanglement hazards.
- Training: Provide comprehensive training for all operators and maintenance personnel on safe operating procedures and emergency responses.
- Signage: Post clear safety signs and warnings around the conveyor system to remind workers of potential hazards.
- Lockout/Tagout Procedures: Implement lockout/tagout procedures for maintenance and repair work to ensure the system is not accidentally powered on.
- Personal Protective Equipment (PPE): Require appropriate PPE, such as gloves, safety glasses, and hard hats, when working near or on the conveyor.
- Regular Safety Audits: Conduct regular safety audits to identify potential hazards and implement corrective actions.
- Clear Work Areas: Keep the areas around the conveyor clear of debris and obstructions that could pose tripping hazards.
- Safe Material Handling: Train workers on safe material handling practices to prevent overloading and uneven loading of the conveyor.
- Incident Reporting: Encourage prompt reporting of any safety incidents or near-misses to address potential hazards before they result in injury.
Adhering to these maintenance and safety guidelines ensures that rubber belt conveyor systems operate efficiently and safely, protecting both the equipment and the workers who operate them.
FAQs about Rubber Belt Conveyor System
Rubber conveyor belts are versatile components used in a wide range of industries for the transportation and handling of materials. These belts are particularly valued for their durability, flexibility, and the ability to transport various types of materials — from large, bulky items to fine particles. Industries such as mining, agriculture, manufacturing, and packaging rely heavily on rubber conveyor belts to move raw materials or finished products through production lines or within storage and distribution facilities. In mining, for example, rubber conveyor belts are used to transport ore from the mine to processing areas. In agriculture, they might be used to move grain from storage silos to delivery trucks. The adaptability of rubber conveyor belts to different environmental conditions and their capability to handle a range of materials make them indispensable in modern industrial operations.
The manufacturing process of rubber conveyor belts involves several key steps, starting with the creation of the belt material itself. The process typically begins with the mixing of raw materials, including rubber, carbon black, and various chemicals, to create a compound with the desired properties. This compound is then formed into sheets through a process called calendering, where it is passed through rollers to achieve the correct thickness and width. The next step involves the addition of reinforcement materials, such as fabric or steel cords, to provide the belt with the necessary strength and durability. This reinforced sheet is then cut to the desired size and shape. The final step in the manufacturing process is vulcanization, where the belt is subjected to heat and pressure to cure the rubber, bonding the layers together and giving the belt its final strength and resilience.
A rubber conveyor belt system is composed of several key components that work together to transport materials efficiently. The most visible part is the belt itself, made of rubber or a rubber composite, which moves over a series of rollers. These rollers include the drive roller, which propels the belt forward, and the idler rollers, which support the belt along its length. The system also includes a frame that holds these rollers in place and provides structural support. Additionally, there are pulleys at either end of the conveyor — the head pulley at the discharge end and the tail pulley at the loading end. The belt is tensioned between these pulleys to prevent slippage. Other components can include cleaning devices to remove debris from the belt, sensors and controls for operation, and safety features like emergency stops and guards.
The principle of belt conveyor systems is based on the continuous movement of a flexible belt over a series of rollers to transport materials from one point to another. The system is powered by a motor, which drives a pulley at one end of the conveyor. This pulley, known as the drive pulley, imparts motion to the belt. As the belt moves, it carries materials placed upon it from the loading point to the discharge point. The belt’s movement is supported by idler rollers that reduce friction and wear, allowing the belt to move smoothly. The efficiency of a conveyor belt system lies in its simplicity and the ability to move large volumes of material over long distances with minimal effort. The design of the system can be adapted to move materials horizontally, inclined, or even vertically, making it a versatile solution for material handling in various industrial applications.
Last Updated on June 25, 2024 by Jordan Smith
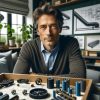
Jordan Smith, a seasoned professional with over 20 years of experience in the conveyor system industry. Jordan’s expertise lies in providing comprehensive solutions for conveyor rollers, belts, and accessories, catering to a wide range of industrial needs. From initial design and configuration to installation and meticulous troubleshooting, Jordan is adept at handling all aspects of conveyor system management. Whether you’re looking to upgrade your production line with efficient conveyor belts, require custom conveyor rollers for specific operations, or need expert advice on selecting the right conveyor accessories for your facility, Jordan is your reliable consultant. For any inquiries or assistance with conveyor system optimization, Jordan is available to share his wealth of knowledge and experience. Feel free to reach out at any time for professional guidance on all matters related to conveyor rollers, belts, and accessories.