The Essential Guide to Rubber Coated Steel Rollers
Rubber coated steel rollers are pivotal components in a myriad of industrial settings, offering unmatched durability and versatility. These rollers, encased in a rubber layer, are integral to machinery used in manufacturing, packaging, and material handling, among other sectors. Their significance lies in their ability to reduce noise, absorb shocks, and provide traction, which facilitates smoother operations and enhances product quality. This blog post aims to serve as a comprehensive guide on rubber coated steel rollers, delving into the various types available, their specific applications, and practical advice on where to source them. Whether you’re involved in the procurement, maintenance, or operation of industrial machinery, understanding the nuances of these rollers can significantly impact your operations’ efficiency and cost-effectiveness.
To Understand Rubber Coated Steel Rollers
In the realm of industrial machinery, the significance of components that offer both durability and precision cannot be overstated. Among these, rubber coated steel rollers stand out for their unique combination of strength and flexibility. This section delves into what these rollers are, how they are made, and the myriad advantages they bring to industrial applications.
Definition and Description
At their core, rubber coated steel rollers are precisely what their name suggests: robust steel cylinders enveloped in a protective rubber coating. This fusion harnesses the structural integrity of steel with the elastic properties of rubber, creating a versatile tool for countless industrial processes. The rubber not only shields the steel from environmental threats but also adds a layer of functionality, whether it’s reducing noise, increasing grip, or mitigating vibration.
The Manufacturing Process of Rubber Coated Steel Rollers
The creation of rubber coated steel rollers is a meticulous process that involves several critical steps:
- Steel Core Preparation: The journey begins with shaping the steel core to the exact specifications needed for its intended use.
- Surface Treatment: To ensure a flawless bond between steel and rubber, the core’s surface is thoroughly cleaned and treated.
- Primer Application: A specialized primer is applied to the prepared surface to further enhance the rubber’s adhesion.
- Rubber Material Selection: Selecting the right rubber material is crucial, as different applications require different rubber properties.
- Rubber Application: The chosen rubber is then applied to the core using one of several techniques, tailored to the roller’s final use.
- Curing: The rubber-coated core is cured under controlled heat and pressure, solidifying the bond and setting the rubber’s final properties.
- Finishing Touches: The last step involves fine-tuning the roller’s dimensions and surface finish to meet the precise requirements of its application.
9 Advantages of Using Rubber Coated Steel Rollers in Industrial Applications
Rubber coated steel rollers offer a plethora of benefits that make them indispensable in many sectors:
- Durability: Their robust construction ensures a long service life even under harsh conditions.
- Shock Absorption: The rubber coating effectively absorbs impact, protecting both the machinery and the materials being processed.
- Noise Reduction: These rollers operate quietly, contributing to a more pleasant workplace environment.
- Improved Traction: The rubber surface prevents slippage, ensuring smooth and efficient material handling.
- Corrosion Resistance: The rubber protects the steel core from corrosive substances, prolonging the roller’s lifespan.
- Customizability: They can be tailored to specific needs, offering solutions for a wide range of industrial challenges.
- Reduced Maintenance Costs: Their resilience leads to fewer breakdowns and lower repair costs.
- Versatility: Suitable for various applications, rubber coated steel rollers are a versatile tool in the industrial arsenal.
- Improved Product Quality: They enhance the quality of the end product by providing uniform pressure and reducing material damage.
Rubber coated steel rollers embody the perfect blend of strength and adaptability, making them a cornerstone of modern industrial machinery. Their comprehensive benefits underscore the importance of selecting the right roller for your specific needs, ensuring efficiency, durability, and quality in your operations.
Types of Rubber Coated Steel Rollers
The diversity of rubber coated steel rollers in the industrial world is vast, with each type designed to meet specific operational demands. From the resilience required in heavy-duty applications to the precision needed in delicate manufacturing processes, the choice of rubber coating can significantly influence a roller’s performance. This section provides a detailed exploration of the various rubber coatings available, their comparative advantages in different settings, and the specialized coatings engineered for unique industrial challenges.
Overview of Different Types of Rubber Coatings Used on Steel Rollers
Rubber coated steel rollers are not a one-size-fits-all solution. The type of rubber used for coating can vary widely, each with its unique properties and applications:
- Natural Rubber: Preferred for its flexibility and durability, making it suitable for a broad range of general applications.
- Nitrile Rubber (NBR): Its oil and solvent resistance make it ideal for industries where chemical exposure is a concern.
- Neoprene: This versatile rubber offers balanced chemical stability and flexibility, perfect for environments with fluctuating temperatures.
- Silicone Rubber: The go-to choice for high-temperature applications, silicone withstands conditions that would degrade other materials.
- Polyurethane: Known for its exceptional tear and abrasion resistance, polyurethane is favored for heavy-duty applications.
- Ethylene Propylene Diene Monomer (EPDM): Its resistance to UV, ozone, and weathering makes EPDM ideal for outdoor use.
- Butyl Rubber: Chosen for its low gas permeability and high chemical resistance, butyl rubber is used in specialized chemical processing.
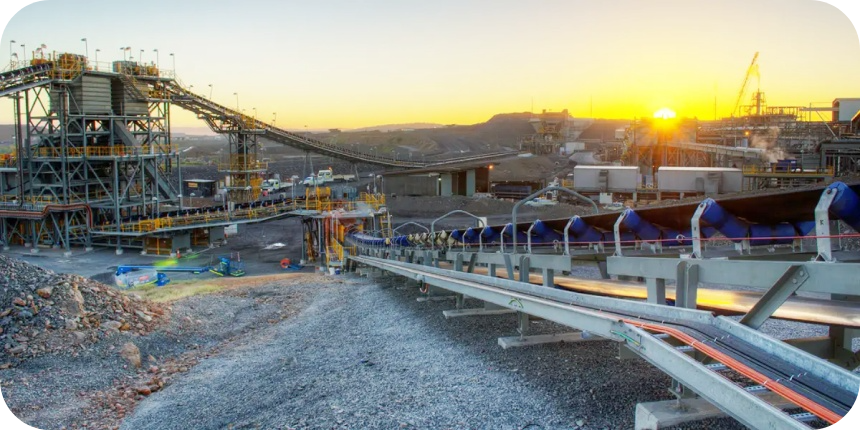
Comparison Between Heavy-Duty and Standard Rubber Coated Steel Rollers
The distinction between heavy-duty and standard rubber coated steel rollers lies in their construction and intended use. Heavy-duty rollers are built to endure more extreme conditions, featuring thicker and more resilient rubber coatings capable of handling higher loads and more abrasive conditions. Standard rollers, while still robust, are designed for less intensive applications, offering a cost-effective solution without the need for the enhanced specifications of heavy-duty versions.
Specialized Rubber Coatings for Specific Industrial Needs
The industrial landscape presents a myriad of challenges, each requiring a tailored approach to material handling and processing:
- High Temperature Resistance: Silicone rubber coatings excel in environments with extreme heat.
- Chemical Resistance: Viton and butyl rubber are selected for their ability to withstand harsh chemicals.
- Food Grade Coatings: Silicone and EPDM coatings meet FDA standards for direct contact with food products.
- Oil and Solvent Resistance: Nitrile rubber is the preferred choice in industries where oil and solvent exposure is frequent.
- Electrical Insulation: EPDM and silicone provide safety in applications requiring electrical insulation.
- Static Dissipation: Special coatings are available to prevent static build-up in sensitive environments.
- Abrasion Resistance: Polyurethane and natural rubber offer superior durability in abrasive conditions.
- UV and Ozone Resistance: EPDM coatings are designed to resist degradation from UV light and ozone, making them suitable for outdoor applications.
Selecting the right type of rubber coated steel roller is crucial for optimizing performance and extending the lifespan of both the rollers and the machinery they support. By understanding the specific properties and advantages of each rubber type, industries can make informed decisions that enhance efficiency, safety, and product quality.
Applications of Rubber Coated Steel Rollers
The versatility and adaptability of rubber coated steel rollers make them an invaluable asset across a broad spectrum of industries. From enhancing operational efficiency to ensuring the quality of the end product, these rollers play pivotal roles in various sectors. This section delves into the widespread applications of rubber coated steel rollers, showcasing their importance and utility in different industrial landscapes.
Applications of Rubber Coated Steel Rollers
- Printing and Packaging: Rubber coated steel rollers are indispensable in the printing industry, ensuring even ink distribution for high-quality prints. In packaging, they facilitate the smooth and precise movement of materials, crucial for the protection and presentation of goods.
- Conveyor Systems and Material Handling: These rollers are the backbone of conveyor systems, providing the necessary traction to move goods efficiently through warehouses, distribution centers, and production lines, minimizing slippage and enhancing productivity.
- Manufacturing Processes: In metal fabrication, rubber coated steel rollers assist in the precise bending and shaping of metal sheets. The paper production industry relies on them for the smooth transportation of paper and the even application of coatings.
- Textile Industry: They guide fabric through machines for finishing processes, ensuring uniform treatment and protecting delicate materials from damage, crucial for maintaining fabric quality.
- Food Processing: Food-grade rubber coatings on steel rollers ensure safe product movement through processing stages, adhering to hygiene standards while facilitating easy cleaning and maintenance.
- Agriculture: Utilized in machinery for crop processing and packaging, these rollers withstand outdoor conditions and rigorous use, demonstrating their durability and reliability in agricultural applications.
- Pharmaceuticals: In the pharmaceutical sector, rubber coated steel rollers are essential for the coating of pills and the handling of sensitive products, where contamination prevention and precision are paramount.
- Automotive Manufacturing: These rollers support the assembly and production of automotive parts, where they contribute to precision handling and coating applications, ensuring the high quality of automotive components.
- Logistics and Sorting: In logistics centers, these rollers are used in sorting systems to efficiently move and sort packages, enhancing the speed and accuracy of order fulfillment.
- Laminating Processes: Rubber coated rollers are key in laminating machines, applying even pressure for the bonding of laminates to substrates, crucial for quality control in the production of laminated products.
- Chemical Processing: In industries dealing with chemicals, specially formulated rubber coatings provide resistance to corrosive substances, ensuring the longevity and safety of processing equipment.
- Mining and Quarrying: Durable rubber coatings are used in the harsh environments of mining and quarrying, where they help convey raw materials without slipping, even in dusty, wet, or abrasive conditions.
Case Studies or Examples in Action
- Automotive Assembly Line Enhancement: An automotive manufacturer integrated custom rubber coated steel rollers in their assembly line, resulting in a smoother workflow and reduced damage to sensitive automotive parts, showcasing the rollers’ impact on efficiency and product integrity.
- Food Processing Plant Upgrade: By incorporating FDA-approved rubber coated steel rollers, a food processing plant not only met stringent hygiene standards but also saw a reduction in maintenance downtime, highlighting the rollers’ contribution to operational excellence.
- Textile Industry Innovation: A textile company utilized specialized rubber coated steel rollers to handle delicate fabrics, leading to a marked improvement in fabric quality and a reduction in waste, demonstrating the rollers’ role in enhancing product quality.
- Chemical Processing Facility Improvement: A chemical processing plant faced challenges with their conveyor systems in corrosive environments. After switching to rubber coated steel rollers designed with chemical-resistant coatings, the plant saw a significant decrease in equipment degradation rates. This adaptation not only extended the lifespan of their conveyor systems but also maintained a safer working environment, emphasizing the rollers’ ability to withstand aggressive substances.
- Mining Operation Efficiency: In a rugged mining operation, the introduction of heavy-duty rubber coated steel rollers equipped to handle abrasive materials and heavy loads led to a noticeable increase in material handling efficiency. These rollers reduced downtime caused by equipment failures and maintenance, showcasing their durability and reliability in one of the harshest industrial environments.
- Paper Production Optimization: A leading paper manufacturing company implemented specially designed rubber coated steel rollers to improve the handling of paper during the production process. This change resulted in a smoother paper feed, reduced tearing and wastage, and an overall increase in production speed and quality. The rollers’ precise engineering ensured uniform pressure and tension, critical for high-quality paper production.
- Airport Baggage Handling System Upgrade: An international airport upgraded its baggage handling systems with advanced rubber coated steel rollers, significantly improving the reliability and speed of baggage processing. This upgrade enhanced passenger satisfaction by reducing waiting times and minimizing the risk of baggage damage, demonstrating the rollers’ impact on service quality in the transportation sector.
- Pharmaceutical Packaging Line Enhancement: A pharmaceutical company revamped its packaging line with FDA-approved rubber coated steel rollers, ensuring the gentle handling of delicate medicine packages. This enhancement not only complied with stringent regulatory standards but also optimized the packaging process, reducing material waste and maintaining the integrity of pharmaceutical products.
The applications of rubber coated steel rollers are as diverse as the industries they serve. Their ability to be customized for specific needs—whether it’s for handling delicate materials, enduring harsh environments, or meeting hygiene standards—underscores their significance in industrial operations. Through strategic implementation, these rollers continue to drive advancements in efficiency, safety, and product quality across various sectors.
How to Choose the Right Rubber Coated Steel Rollers
Selecting the right rubber coated steel rollers is crucial for optimizing industrial operations and ensuring longevity and efficiency in machinery. The choice of rollers must be informed by a comprehensive understanding of the application requirements and the specific properties of different rubber coatings. This section outlines key factors to consider when selecting rubber coated steel rollers for industrial applications and provides a guide to the properties of various rubber roller coatings.
Factors to Consider When Selecting Rubber Coated Steel Rollers
- Load Capacity: The ability of the roller to support the weight of the materials it will be handling is paramount. Choosing a roller with an appropriate load capacity ensures durability and prevents deformation under weight.
- Environmental Conditions: The operational environment’s temperature range, potential exposure to chemicals, and presence of moisture or abrasive materials can significantly affect the choice of roller. Selecting a rubber coating that can withstand these conditions is essential for maintaining roller integrity.
- Speed and Friction Requirements: The operational speed of the rollers and the required friction level to prevent slippage while ensuring smooth material handling must be considered. Different rubber materials offer varying degrees of friction and are suited to different speeds of operation.
- Abrasion Resistance: In applications where the roller will be subject to wear from rough materials, choosing a rubber material with high abrasion resistance is crucial to extend the roller’s service life.
- Chemical Resistance: For environments exposed to chemicals, oils, or solvents, selecting a rubber coating that can resist these substances without degrading is necessary.
- Temperature Resistance: Applications involving extreme temperatures require rollers with rubber coatings that can maintain their properties without softening or becoming brittle.
- Compliance with Regulations: Especially in food processing, pharmaceuticals, and other sensitive applications, ensuring that the rubber material complies with relevant safety and hygiene standards is essential.
- Ease of Maintenance: Consideration should be given to how easily the rollers can be cleaned, repaired, or replaced, affecting downtime and operational efficiency.
Guide to Rubber Roller Coatings and Their Properties
- Neoprene: Offers a good balance of chemical stability, flexibility, and weather resistance, making it suitable for moderate environments.
- Silicone: Excellent for high-temperature applications, silicone maintains its properties across a wide temperature range and is resistant to aging, sunlight, and moisture.
- Urethane: Known for its exceptional abrasion resistance and load-bearing capacity, urethane is ideal for heavy-duty applications where durability is a priority.
- Natural Rubber: Provides excellent elasticity and shock absorption, making it ideal for applications requiring a high grip.
- Nitrile Rubber (NBR): Offers superior resistance to oil, making it suitable for use in automotive and industrial applications where oil exposure is likely.
- Ethylene Propylene Diene Monomer (EPDM): Exhibits outstanding resistance to weathering, ozone, and UV, making it ideal for outdoor applications.
- Butyl Rubber: Has a low permeability to gases and excellent resistance to chemicals, heat, and aging, suitable for chemical processing environments.
Selecting the right rubber coated steel rollers involves a careful analysis of the operational requirements and environmental conditions. By understanding the unique properties of different rubber coatings, industries can make informed decisions that enhance the performance and longevity of their machinery, ultimately contributing to operational efficiency and product quality.
Top-quality conveyor rollers for all your industrial needs.
Maintenance and Repair of Rubber Coated Steel Rollers
Ensuring the longevity and optimal performance of rubber coated steel rollers is pivotal in maintaining the efficiency of industrial operations. This section is dedicated to guiding you through the essential maintenance practices, repair strategies, and how to find expert services for your rubber coated steel rollers. By adhering to these guidelines, you can safeguard the functionality and durability of these crucial components.
Tips for Maintaining Rubber Coated Steel Rollers
Maintaining rubber coated steel rollers is not just about preserving their physical condition; it’s about ensuring they continue to perform their function effectively and efficiently. Here are several maintenance tips designed to extend the lifespan of your rollers:
- Regular Cleaning: Dust, debris, and material build-up can significantly impair a roller’s performance. Regular cleaning with suitable agents is crucial.
- Routine Inspections: Conduct periodic checks for any signs of wear, tear, or damage. Early detection can prevent minor issues from escalating.
- Lubricate Bearings: Proper lubrication of bearings is essential to minimize friction and prevent overheating, which can degrade the rubber coating over time.
- Avoid Overloading: Operating within the roller’s load capacity ensures it remains in good condition and performs as expected.
- Temperature Control: Excessive heat or cold can damage the rubber. Maintaining an optimal temperature range during operation is vital.
- Chemical Exposure: Protect the rollers from harsh chemicals that could deteriorate the rubber, affecting its integrity and functionality.
- Proper Storage: When not in use, storing rollers in a controlled environment prevents premature aging of the rubber.
- Use Protective Covers: Protective covers can shield the rollers from potential damage caused by sharp or abrasive materials.
When and How to Repair Rubber Coated Steel Rollers
Effective maintenance and timely repair of rubber coated steel rollers are crucial for sustaining their performance and extending their service life. Recognizing the signs that indicate the need for repair and understanding the repair process are essential for keeping your operations running smoothly.
When to Repair:
- Uneven Wear Patterns: Uneven wear can lead to material handling issues, such as improper feeding or tracking. This is a clear sign that the roller surface needs to be evaluated and possibly repaired.
- Hardening or Softening of the Rubber: Changes in the rubber’s hardness can affect its performance. Exposure to certain chemicals or extreme temperatures can cause the rubber to harden or soften, necessitating repair or recoating.
- Vibration or Noise Increase: An increase in noise or vibration during operation can indicate misalignment, imbalance, or damage to the roller. These symptoms should prompt an immediate inspection.
- Cracking or Splitting: Visible cracks or splits in the rubber coating can compromise the roller’s integrity and functionality, requiring immediate attention.
How to Repair:
- Regrinding: Regrinding the roller’s surface can remove minor imperfections, restore its roundness, and improve its finish, enhancing performance.
- Strip and Recoat: For more severe damage, stripping the old rubber coating and applying a new layer can restore the roller to its original condition. This process allows for the customization of the rubber compound to better suit the application if needed.
- Precision Machining: After recoating, precision machining ensures the roller meets the exact dimensional and tolerance specifications required for the application.
- Alignment and Balancing: Post-repair, it’s crucial to check the alignment and balance of the roller within the machinery. Proper alignment reduces wear and tear, while balancing minimizes vibration, both of which contribute to the roller’s longevity.
- Core Repair or Replacement: Sometimes, the steel core itself may be damaged. Assessing the core for issues like corrosion, deformation, or fatigue is vital. In some cases, repairing the core is possible; however, replacement might be necessary for severe damage.
Understanding when and how to repair rubber coated steel rollers, coupled with proactive maintenance strategies, ensures these critical components continue to function efficiently and reliably. Addressing issues promptly and effectively not only saves time and resources but also maintains the quality and consistency of your production processes.
Finding Rubber Roller Coating and Repair Services Near You
Securing a reliable service provider for your rubber coated steel rollers is essential for ongoing maintenance and emergency repairs. Here’s how to find the best services in your area:
- Specialized Directories: Look for online directories that list industrial repair services. These platforms often provide detailed information about providers’ specialties.
- Manufacturer Recommendations: Contact the manufacturer of your rollers or machinery. They often have a network of recommended service providers or offer repair services themselves.
- Industry Forums and Communities: Online forums and social media groups focused on industrial maintenance can be excellent resources for service provider recommendations.
- Local Industrial Supply Stores: These stores not only supply parts but also have connections with local repair services. They can often recommend providers who specialize in rubber roller repairs.
- Certification Bodies: Providers certified by recognized industrial standards organizations are generally reliable and adhere to high-quality service levels. Look for certifications or memberships in their promotional materials.
By implementing these maintenance tips, understanding the repair needs of your rollers, and knowing how to find expert services, you can ensure the continued reliability and efficiency of your rubber coated steel rollers. This proactive approach not only extends the lifespan of the rollers but also supports the smooth operation of your industrial processes.
To Purchase Rubber Coated Steel Rollers
When it comes to integrating or upgrading components within industrial machinery, the procurement of rubber coated steel rollers stands out as a critical decision-making process. The right rollers can significantly enhance operational efficiency, reduce maintenance costs, and improve product quality. This section is dedicated to providing comprehensive advice on finding and selecting the best rubber coated steel rollers for sale, identifying reputable manufacturers, and understanding the importance of custom solutions tailored to unique industrial needs.
Advice on Finding and Selecting Rubber Coated Steel Rollers for Sale
The quest for the perfect rubber coated steel rollers requires a strategic approach, blending thorough research with a keen understanding of your operational needs. This journey towards finding the ideal rollers is not just about purchasing a product; it’s about investing in a component that will significantly influence your operational efficiency and productivity. Here’s how to navigate this process effectively:
- Understand Specific Requirements: Begin with a clear assessment of what you need in terms of load capacity, environmental resilience, and operational speed. This clarity will narrow down your options to those most suited to your application.
- Conduct Comprehensive Research: Dive into the market to explore manufacturers who specialize in rubber coated steel rollers. Look for those with a strong presence in your specific industry sector.
- Check for Quality Assurance: Quality certifications or standards are non-negotiable. They are a testament to a manufacturer’s commitment to quality and reliability.
- Evaluate Material Suitability: The type of rubber coating and its compatibility with your operational environment is crucial. Ensure the materials used can withstand your specific industrial conditions.
- Consider Customization Capabilities: Not all needs can be met with off-the-shelf solutions. Manufacturers who offer customization can tailor rollers to your exact requirements, enhancing their effectiveness.
- Seek Out Technical Support: A manufacturer’s willingness to provide detailed technical support and guidance is indicative of their service quality and customer care.
- Understand Warranty and Service Terms: A comprehensive warranty and clear service terms are indicators of a manufacturer’s confidence in their product and their commitment to customer satisfaction.
- Price Comparison: While the cheapest option isn’t always the best, understanding how pricing reflects quality, service, and longevity can help you make a cost-effective decision.
How to Identify Reputable Industrial Rubber Roller Manufacturers
Finding a manufacturer you can trust is pivotal in ensuring that the rubber coated steel rollers you purchase are of the highest quality and suited to your specific needs. Here’s how to identify those who stand out in the industry:
- Seek Industry Endorsements: Recommendations from within your industry or from trusted business partners can lead you to reputable manufacturers.
- Analyze Customer Feedback: Genuine customer reviews can provide insights into a manufacturer’s reliability, product quality, and customer service.
- Review Their Work History: A portfolio of successful projects similar to your requirements can serve as proof of a manufacturer’s expertise and experience.
- Evaluate Their Communication: Transparency, willingness to engage in detailed discussions, and prompt responses are signs of a manufacturer’s professionalism and customer service quality.
The Importance of Custom Solutions for Unique Industrial Needs
Custom solutions in the realm of rubber coated steel rollers are not merely an option; they are often a necessity for addressing the unique challenges and requirements of various industrial applications. Here’s why tailored solutions are critical:
- Enhanced Compatibility: Custom rollers are designed to fit seamlessly into your existing machinery, ensuring optimal performance and reducing the risk of operational issues.
- Targeted Performance: By tailoring the roller to your specific operational needs, manufacturers can optimize the roller conveyor’s design for improved efficiency and output.
- Innovative Solutions: Collaborating on a custom solution allows for innovative approaches to complex problems, potentially leading to breakthroughs in operational efficiency.
- Long-Term Cost Savings: Although custom solutions might require a higher initial investment, their ability to reduce downtime, maintenance, and replacement costs can lead to significant savings over time.
- Regulatory Compliance: Custom rollers can be designed to meet specific regulatory requirements, ensuring compliance in industries where standards are stringent.
Investing time in finding the right rubber coated steel rollers and a reputable manufacturer, especially one that offers custom solutions, is crucial. It ensures that you not only meet your current operational needs but also position yourself for future efficiency and success.
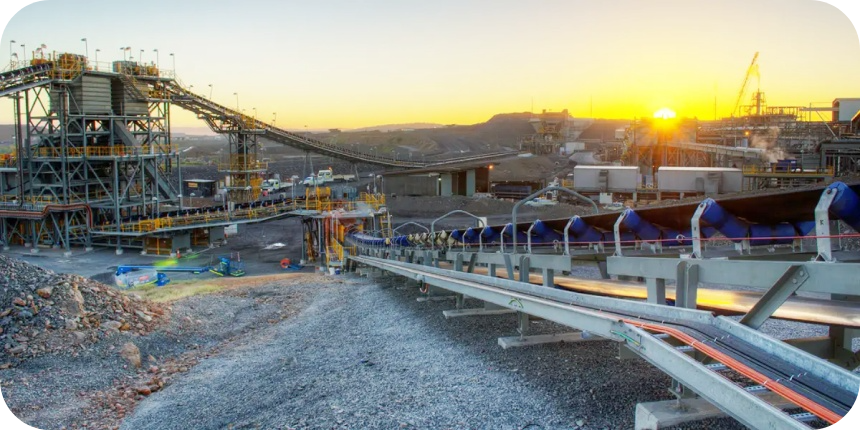
Future Trends in Rubber Coated Steel Rollers
The landscape of industrial manufacturing and machinery is ever-evolving, with rubber coated steel rollers at the forefront of many technological advancements and innovations. As industries continue to develop, the demand for more efficient, durable, and specialized rollers increases. This section explores the future trends in rubber coated steel rollers, highlighting the innovations in rubber coating technologies and how these rollers are adapting to meet the changing needs of various industries.
Innovations and Advancements in Rubber Coating Technologies
- Eco-Friendly Materials: The shift towards sustainability is driving the development of eco-friendly rubber coatings that are less harmful to the environment, without compromising on performance.
- Improved Durability: Advances in material science are leading to the creation of rubber compounds that offer enhanced wear resistance and longevity, reducing the need for frequent replacements.
- Temperature and Chemical Resilience: New formulations are being developed to enhance the resistance of rubber coatings to extreme temperatures and corrosive chemicals, broadening the range of applications for rubber coated steel rollers.
- Self-Healing Rubbers: Research into self-healing materials is paving the way for rubber coatings that can repair minor cuts and abrasions autonomously, significantly extending the life of the rollers.
- Smart Coatings: The integration of sensor technology into rubber coatings is emerging, allowing for real-time monitoring of wear, temperature, and other critical parameters, enabling predictive maintenance and reducing downtime.
- Customization Through 3D Printing: Advances in 3D printing technology are enabling the production of rubber coatings with customized textures, patterns, and properties, tailored to specific operational requirements.
- Nanotechnology: The incorporation of nanomaterials into rubber coatings is enhancing their mechanical properties, such as strength and elasticity, and introducing new functionalities like antimicrobial surfaces.
- Hybrid Materials: The development of hybrid coatings that combine rubber with other materials, such as silicone or polyurethane, is offering improved performance characteristics, including better friction control and vibration damping.
The Evolving Needs of Industries and How Rubber Coated Steel Rollers Are Adapting
- Automation and Robotics: As industries increasingly adopt automation, the demand for rubber coated steel rollers capable of operating with precision and reliability in automated environments is growing. Rollers are being designed to accommodate higher speeds and more complex movements.
- Food and Pharmaceutical Safety: With stricter regulations on materials that come into contact with food and pharmaceuticals, rubber coated steel rollers are being developed with certified safe materials, ensuring compliance and safety.
- High-Speed Manufacturing: The push for faster production lines is driving the need for rollers that can handle higher speeds without degradation, prompting innovations in both rubber materials and roller designs.
- Customization for Niche Applications: The trend towards customization is leading manufacturers to offer highly specialized rollers designed for niche applications, from textile manufacturing to paper printing, each with unique requirements.
- Wear and Maintenance Monitoring: The future of rubber coated steel rollers includes smarter maintenance strategies, with rollers equipped with sensors to predict wear and schedule maintenance, minimizing unexpected breakdowns.
- Renewable Energy Sector: As the renewable energy sector expands, the demand for specialized rubber coated steel rollers in the production of solar panels and wind turbines is increasing, driving innovations tailored to these applications.
The future of rubber coated steel rollers is marked by continuous innovation, with advancements in materials science and manufacturing technologies leading the way. These developments are not only enhancing the performance and durability of the rollers but also enabling them to meet the increasingly specialized and stringent requirements of modern industries. As these trends continue to evolve, rubber coated steel rollers will remain an essential component in the machinery that powers the world’s industries, adapting to meet the challenges of tomorrow.
FAQs about Rubber Coated Steel Rollers
Rubber rollers are versatile components used in a wide array of industries and applications due to their excellent grip, flexibility, and ability to conform to different surfaces. They play a crucial role in material handling, acting as components in conveyor systems to move goods efficiently through production lines. In the printing industry, rubber rollers are indispensable for transferring ink uniformly across printing surfaces, ensuring high-quality print outputs. Additionally, they are used in the textile industry to guide fabric through various processing stages, in packaging machinery to handle and package goods without damage, and in the agricultural sector within equipment for processing crops. The specific application of a rubber roller is determined by its material composition, hardness, and design, all of which are tailored to meet the unique demands of the task at hand, ranging from delicate handling in the pharmaceutical industry to heavy-duty use in mining and construction.
A rubber roller is often referred to by several names, reflecting its diverse applications across different industries. Commonly, it is known as an “elastomeric roller” due to the elastic nature of the rubber coating. In specific contexts, such as in printing or textile manufacturing, it might be called an “ink roller” or “fabric roller,” respectively, denoting its primary function in those settings. The term “urethane roller” is used when the roller is coated with a polyurethane layer, highlighting the type of rubber material used. Regardless of the nomenclature, the fundamental characteristics and functions of these rollers remain consistent, focusing on their ability to apply pressure, provide traction, and ensure the smooth transfer of materials or fluids across surfaces.
An EPDM roller refers to a rubber roller coated with Ethylene Propylene Diene Monomer, a type of synthetic rubber known for its outstanding resistance to heat, weathering, and chemicals. EPDM rollers are particularly valued in applications requiring long-term durability and stability in challenging environmental conditions. Due to EPDM’s excellent resistance to UV rays, ozone, and varying temperatures, these rollers are commonly used in outdoor machinery, automotive applications, and in the chemical processing industry where exposure to harsh elements is frequent. The material’s flexibility and resilience also make EPDM rollers suitable for use in water treatment facilities and in the food processing industry, where they come into contact with water and various cleaning agents.
The hardness of rubber rollers, typically measured on the Shore A scale, can vary significantly depending on their intended use, ranging from very soft (around 20 Shore A) to very hard (up to 100 Shore A). Soft rollers are used in applications requiring high levels of grip and elasticity, such as in the printing industry, where they must conform to the surface of the paper or fabric without causing damage. Medium hardness rollers (around 40-70 Shore A) are versatile and used in a variety of material handling and manufacturing processes, offering a balance between grip and durability. Hard rollers (above 70 Shore A) are suited for applications requiring high levels of precision and minimal deformation, such as in film and foil processing. The specific hardness chosen for a roller is a critical factor that influences its performance, wear resistance, and the quality of the output in its respective application.
Last Updated on July 11, 2024 by Jordan Smith
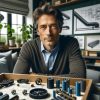
Jordan Smith, a seasoned professional with over 20 years of experience in the conveyor system industry. Jordan’s expertise lies in providing comprehensive solutions for conveyor rollers, belts, and accessories, catering to a wide range of industrial needs. From initial design and configuration to installation and meticulous troubleshooting, Jordan is adept at handling all aspects of conveyor system management. Whether you’re looking to upgrade your production line with efficient conveyor belts, require custom conveyor rollers for specific operations, or need expert advice on selecting the right conveyor accessories for your facility, Jordan is your reliable consultant. For any inquiries or assistance with conveyor system optimization, Jordan is available to share his wealth of knowledge and experience. Feel free to reach out at any time for professional guidance on all matters related to conveyor rollers, belts, and accessories.