Durable Rubber Conveyor Belt for Heavy Duty Applications
Rubber conveyor belts are crucial components in various industries, known for their durability, flexibility, and capacity to handle heavy loads and demanding environments. These belts provide an efficient and reliable means of transporting materials over long distances, making them indispensable in sectors like mining, agriculture, manufacturing, logistics, and recycling. They help streamline operations, ensuring smoother, faster, and safer material handling.
The versatility of rubber conveyor belts stems from the wide range of materials and designs available. While general-purpose belts serve less demanding environments, heavy-duty versions are specially engineered for industries such as mining and construction, where harsh conditions require enhanced strength and resilience. Additionally, specialty belts offer tailored features like heat resistance, fire resistance, and oil resistance, addressing the unique needs of specific applications. Whether for simple material transport or complex industrial tasks, there is a rubber conveyor belt designed to meet the specific requirements of every project.
What is a Rubber Conveyor Belt?
A rubber conveyor belt is a type of industrial conveyor belt made from rubber or rubber-based materials that are designed to move materials from one place to another in various industries. These belts are made to withstand wear, weather, and the stress of heavy loads while offering a smooth and continuous transportation solution. The structure typically consists of a flexible rubber outer layer, often reinforced with fabric or steel cords for added strength and durability, with some belts incorporating additional layers for specific purposes, such as heat or oil resistance. For example, a steel cord rubber conveyor belt is often used for heavy-duty applications where high strength is required.
The primary purpose of a rubber conveyor belt is to facilitate the efficient movement of goods and materials in automated systems. Conveyor belts are used to transport everything from raw materials to finished products, making them essential for the smooth operation of many production lines, mining operations, and other industrial processes. The choice of conveyor belt material plays a crucial role in determining the efficiency and durability of these systems. Rubber conveyor belts are favored for their ability to handle heavy loads, their resilience to wear and tear, and their ability to operate in various environmental conditions. In some cases, the cheapest rubber conveyor belt might be used for lighter applications or where cost efficiency is a priority, while more specialized belts, like the plain flat rubber conveyor belt, are used for specific functions such as flat, low-friction surfaces.
Common Industries That Use Rubber Conveyor Belts
Rubber conveyor belts are integral to a wide variety of industries due to their durability and adaptability. Some of the most common industries that rely on these conveyor systems include:
- Mining: In mining operations, rubber conveyor belts are used to transport raw materials such as coal, ores, minerals, and sand from the extraction site to processing facilities. Due to the heavy, abrasive nature of the materials being moved, mining belts are often heavy-duty and designed to handle high-impact and wear-resistant demands. These might include rubber conveyor belt specifications for extreme conditions and durability.
- Agriculture: In agriculture, rubber conveyor belts are used to move harvested crops, seeds, or fertilizers through processing plants or to storage areas. These belts must be durable and flexible, able to transport various types of agricultural products without damage. The use of black rubber conveyor belt is common in these applications due to its resistance to wear and dirt.
- Manufacturing and Assembly Lines: Rubber conveyor belts are commonly found in manufacturing plants where they are used to move products through different stages of production. Whether it’s automotive assembly, electronics manufacturing, or packaging, these belts provide an efficient means of handling materials on assembly lines, reducing labor costs and increasing production speed.
- Food Processing: Conveyor belt in the food industry are often made from food-grade rubber materials, ensuring that they meet safety standards for transporting raw ingredients or finished food products. These belts are used for everything from washing and sorting fruits and vegetables to transporting packaged foods for distribution.
- Logistics and Warehousing: Rubber conveyor belts are critical for the smooth operation of logistics and warehouse systems. They are used to move packages, boxes, and bulk items from one area of a warehouse to another, improving efficiency and reducing manual labor in sorting and distributing goods. For these purposes, rubber conveyor belt pictures can help illustrate different belt types suited for varying environments.
- Recycling and Waste Management: In recycling plants, rubber conveyor belts are used to transport waste materials such as paper, plastics, and metals to sorting and processing stations. They must be resistant to damage from sharp or heavy objects and capable of withstanding exposure to harsh chemicals and abrasive materials.
- Construction and Cement: In the construction industry, rubber conveyor belts are used to move heavy materials like gravel, sand, cement, and stone. These belts must be capable of carrying large volumes of materials over long distances, often through rugged and challenging environments. Specialized belts, like steel cord rubber conveyor belt, are used in these high-load applications.
Types of Rubber Conveyor Belts
Rubber conveyor belts come in a variety of rubber conveyor belt types, each designed to suit specific operational requirements and environmental conditions. These belts are made with different materials and construction techniques, allowing them to perform optimally under different conditions. The three main types of rubber conveyor belts are general-purpose belts, heavy-duty belts, and specialty belts, each serving distinct purposes across various industries.
General-purpose Rubber Belts
General-purpose rubber conveyor belts are the most common type used in industries where the demands on the belt are moderate. These belts are designed to handle light to medium-duty operations, making them suitable for a wide range of applications such as transportation of packaged goods, light materials, or bulk products in factories, warehouses, and assembly lines.
These belts typically feature a simple rubber construction with one or more layers of fabric (such as polyester or nylon) for reinforcement. The rubber compound used in general-purpose belts is designed to provide a balance of strength, flexibility, and resistance to wear under normal conditions. While they are not as heavy-duty as other types, they are cost-effective and provide reliable service in environments where extreme conditions (like high temperatures or abrasives) are not a major concern.
- Common Applications:Material handling in warehouses and distribution centers
Transporting non-abrasive materials like grains, plastics, or packaged items
Small manufacturing operations and assembly lines
Heavy duty Rubber Conveyor Belts
Heavy-duty rubber conveyor belts are built to withstand the demanding conditions of industries like mining, construction, and quarrying. These belts are designed to handle large, heavy, and abrasive materials, such as rocks, gravel, sand, ores, and coal. They are constructed with multiple layers of reinforced fabric and steel cords, giving them the strength and durability needed to support heavy loads and resist tearing or damage from sharp objects.
The rubber used in heavy-duty belts is often compounded with additional additives to enhance its resistance to impact, abrasion, and wear. These belts can also be designed to handle extreme conditions, such as exposure to chemicals, high temperatures, or heavy impacts. Heavy-duty rubber conveyor belts are also available in specialized designs, such as corrugated or sidewall belts, which allow for the transportation of materials at steeper angles or in confined spaces.
- Common Applications:Mining and aggregate operations for transporting ores, coal, and other minerals
Construction sites for transporting sand, gravel, and building materials
Waste management and recycling for heavy and bulk materials
Specialty Rubber Conveyor Belts
Specialty rubber conveyor belts are designed for applications that require specific performance characteristics beyond what general-purpose and heavy-duty belts can provide. These belts are customized to meet the unique needs of various industries where conditions such as high temperatures, chemical exposure, or fire hazards are prevalent. Specialty rubber belts can be tailored with various compounds and treatments to make them resistant to specific conditions.
- Fire-resistant belts: These belts are made from fire-resistant rubber compounds to prevent fires from spreading along the conveyor system. They are commonly used in industries like coal handling, cement manufacturing, and chemical processing, where there is a risk of fire due to flammable materials.
- Heat-resistant belts: These are designed to handle high temperatures without deteriorating. They are commonly used in industries such as steel mills, foundries, and power plants, where materials like molten metal, hot ash, or cement clinker need to be transported.
- Oil-resistant belts: These belts are specially treated to resist damage from exposure to oils, greases, and other petroleum-based products. They are essential in industries like automotive manufacturing, chemical processing, and food production, where oil spillage or contact with lubricants is common.
- Chemical-resistant belts: For industries dealing with chemicals or hazardous materials, rubber conveyor belts can be customized with compounds that provide resistance to a wide range of acids, alkalis, and solvents. These belts are crucial in chemical processing plants, pharmaceutical manufacturing, and wastewater treatment facilities.
- Food-grade belts: In the food processing industry, rubber conveyor belts can be manufactured from FDA-approved materials that are safe for food contact. These belts are designed to meet strict hygiene standards and prevent contamination during the transportation of food products.
- Antistatic belts: Used in industries where static electricity poses a risk, such as electronics manufacturing, antistatic rubber belts are designed to safely dissipate static charges and reduce the risk of sparks, which could damage sensitive equipment or cause explosions in hazardous environments.
Common Applications:
- Fire-resistant belts: Coal mines, power plants, and cement manufacturing
- Heat-resistant belts: Steel mills, foundries, and asphalt plants
- Oil-resistant belts: Automotive factories, chemical plants, and food processing
- Chemical-resistant belts: Chemical manufacturing, water treatment plants, and pharmaceutical industries
- Food-grade belts: Food processing plants, packaging lines, and beverage industries
- Antistatic belts: Electronics manufacturing, clean rooms, and explosive environments
Materials Used in Rubber Conveyor Belt
The composition of materials used in rubber conveyor belt material is critical in determining their durability, flexibility, strength, and overall performance in various industrial applications. These belts are constructed using a combination of rubber, fabric, and steel cord, each contributing to specific aspects of the belt’s functionality. The type and quality of materials selected depend on the intended application, the load it must carry, and the environmental conditions it will be exposed to.
Composition of Materials
- Rubber: The rubber compound forms the outer surface of the conveyor belt and is responsible for its resistance to wear, abrasion, impact, and environmental factors such as heat, chemicals, and oils. The quality and type of rubber used in the construction of the belt are paramount in determining its performance in specific industrial applications.
- Fabric: Fabric, typically made from polyester, nylon, or other synthetic materials, is used as reinforcement within the belt to provide strength, flexibility, and elasticity. The fabric layers, also known as plies, help the belt maintain its shape under tension and ensure it can support heavy loads without excessive stretching or deformation.
- Steel Cord: Steel cord is often used in high-strength rubber conveyor belts, particularly in heavy-duty applications. Steel cords provide the belt with additional tensile strength, allowing it to carry extremely heavy loads and withstand high-impact environments. This improves the conveyor belt tensile strength, ensuring better performance in demanding applications. Steel-reinforced belts are commonly used in industries such as mining, quarrying, and bulk material handling.
Types of Rubber
Rubber conveyor belts can be made from various types of rubber, each offering specific characteristics that make them suitable for different applications. The two primary categories of rubber used are natural rubber and synthetic rubber. Each type of rubber has unique properties that enhance the performance of the belt in certain conditions.
Natural Rubber (NR):
- Characteristics: Natural rubber, derived from latex, is known for its excellent elasticity, high tensile strength, and superior resistance to wear and tear. It has a high rebound resilience and can endure significant levels of stretching and deformation without permanent damage. Natural rubber conveyor belt are commonly used in a variety of applications due to these properties.
- Applications: Natural rubber is commonly used in general-purpose conveyor belts that operate in environments where flexibility, durability, and wear resistance are essential. It is often used in light to medium-duty operations such as packaging, food handling, and material handling in controlled environments. These applications typically require a quality rubber conveyor belt for optimal performance.
- Advantages: High tear resistance, good flexibility, and superior grip. It is also cost-effective for applications where extreme chemical or heat resistance is not required.
- Limitations: Poor resistance to oil, grease, and certain chemicals; not suitable for high-temperature environments.
Synthetic Rubber:
Synthetic rubbers are manufactured through chemical processes and offer a range of specific benefits that natural rubber may not provide. The most common types of synthetic rubber used in conveyor belts include neoprene, EPDM, and nitrile rubber, each with distinct advantages depending on the environmental factors they must withstand.
Neoprene (Polychloroprene):
- Characteristics: Neoprene is a versatile synthetic rubber known for its excellent resistance to oils, fuels, and other chemicals. It also provides good flexibility and impact resistance, making it suitable for applications that require exposure to harsh conditions.
- Applications: Neoprene is often used in environments where the conveyor belt will be exposed to oils, chemicals, or temperatures ranging from -40°C to 120°C. It is commonly found in automotive, industrial, and manufacturing applications where oil resistance is crucial.
- Advantages: Excellent resistance to oils, greases, and weathering; good abrasion resistance.
- Limitations: Not as heat-resistant as other rubbers like EPDM or silicone.
EPDM (Ethylene Propylene Diene Monomer):
- Characteristics: EPDM is a synthetic rubber with exceptional resistance to heat, ozone, and weathering. It also has good electrical insulating properties, which makes it suitable for certain specialized applications. EPDM belts can withstand temperatures up to 150°C (300°F), making them ideal for high-temperature environments.
- Applications: EPDM is used in environments where high heat resistance is required, such as in power plants, steel mills, and foundries. It is also used in applications where exposure to UV light and weathering is common, such as outdoor material handling.
- Advantages: Superior heat resistance, excellent ozone and UV resistance, and good aging properties.
- Limitations: Poor resistance to oils, fats, and fuels.
Nitrile Rubber (NBR):
- Characteristics: Nitrile rubber is a synthetic rubber with excellent resistance to oil, fuel, and other hydrocarbons. It also has good abrasion resistance, making it suitable for use in applications where petroleum-based products are present.
- Applications: Nitrile rubber conveyor belts are widely used in industries that handle oils, fats, and petroleum products, such as automotive, food processing, and chemical manufacturing.
- Advantages: Outstanding resistance to oils, greases, and fuels; high tensile strength.
- Limitations: Poor resistance to heat and ozone, less flexibility compared to natural rubber.
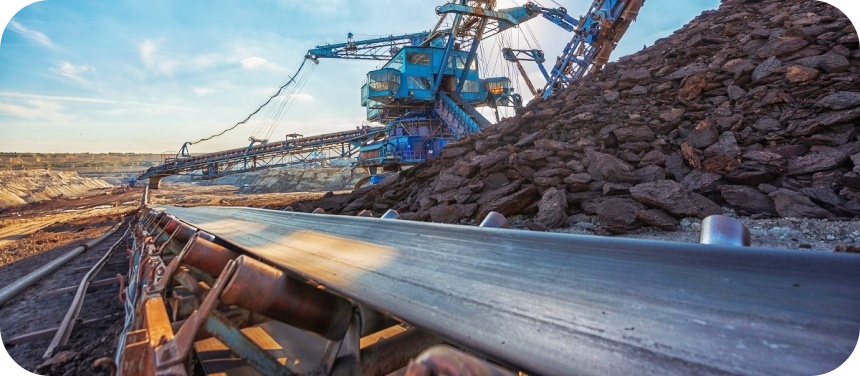
The Role of Each Material in Determining the Belt’s Durability, Flexibility, and Strength
Each material used in the construction of a rubber conveyor belt plays a crucial role in determining its overall performance, particularly in terms of durability, flexibility, and strength:
- Rubber (Outer Layer): The rubber compound is the primary material in contact with the transported materials, and its properties determine how well the belt can handle wear, impacts, and environmental conditions. The choice of rubber directly influences the belt’s resistance to abrasion, tearing, oil, chemicals, heat, and UV exposure. A high-quality rubber compound ensures that the belt can withstand the demanding conditions of its operating environment.
- Fabric (Reinforcement Layer): The fabric reinforcement, which can consist of materials like polyester, nylon, or aramid, provides the necessary strength to the belt while maintaining flexibility. The number of plies (layers of fabric) in the belt determines its load-carrying capacity and how much the belt can stretch under tension. Fabric reinforcement is essential for preventing belt elongation and ensuring that the belt maintains its shape and efficiency over time.
- Steel Cord (Reinforcement for Heavy-duty Belts): Steel cord belt are used in heavy-duty applications where high tensile strength is required. The steel cords provide the belt with the strength necessary to carry heavy loads and withstand high-impact operations. Steel cords also improve the belt’s dimensional stability, reducing elongation and the need for frequent adjustments.
Features of a Good Rubber Conveyor Belt
A high-quality rubber conveyor belt is crucial for efficient, long-lasting operation in various industries. When selecting a conveyor belt, it is important to consider several key features that influence the belt’s performance, durability, and adaptability to different applications. These features ensure that the belt can handle heavy loads, resist environmental stresses, and operate reliably under challenging conditions.
Strength, Flexibility, and Resistance to Wear
- Strength: The strength of a rubber conveyor belt is one of its most important features, as it determines the amount of weight and pressure the belt can withstand. A strong conveyor belt will not only support the load being carried but also resist deformation, stretching, and breaking under tension. The strength of the belt is largely influenced by its construction, particularly the fabric reinforcement and, for heavy-duty applications, steel cord. High-strength belts are essential for industries like mining, steel manufacturing, and material handling, where heavy and often abrasive materials need to be transported over long distances.
- Flexibility: Flexibility is critical in ensuring that the conveyor belt can operate smoothly around pulleys and through complex configurations. A flexible belt is easier to install and maintain, and it can adjust to changes in the load or speed without risk of damage. Flexibility is influenced by the type of rubber used (such as natural or synthetic rubber) and the reinforcement materials within the belt. Conveyor belts designed for heavy-duty operations or specific purposes may be less flexible to maximize strength but still need a certain degree of elasticity to allow for smooth movement and handling.
- Resistance to Wear: The ability of a rubber conveyor belt to resist wear and tear is vital for its longevity. Conveyor belts operate under constant friction, so the outer layer of the belt must be resistant to abrasion and impact. The rubber compound used must be able to handle repetitive contact with rough materials without degrading or losing its integrity. High-wear-resistant belts are crucial in industries such as mining, quarrying, and bulk handling, where the materials being conveyed can be particularly abrasive.
Durability Against Extreme Temperatures, Chemicals, and Abrasion
- Resistance to Extreme Temperatures: Conveyor belts may be exposed to a wide range of temperatures depending on the environment in which they are used. Some industries require belts to withstand extreme heat, such as in steel mills, cement plants, or power stations, where the belt must operate at temperatures of up to 200°C or more. On the other hand, belts used in cold storage facilities or food processing plants may need to handle sub-zero temperatures. To ensure durability in extreme conditions, heat-resistant and cold-resistant rubber compounds are often used. Materials like EPDM, silicone, or certain synthetic rubbers can withstand higher or lower temperature ranges, maintaining the integrity of the belt and minimizing the risk of failure due to heat or cold-induced brittleness.
- Chemical Resistance: In industries where belts are exposed to chemicals, oils, or other corrosive substances, having a belt that resists chemical degradation is essential. Rubber belts with good chemical resistance are made from specialized synthetic rubbers like nitrile (for oils), neoprene (for chemicals), or fluorocarbon rubbers, which can endure exposure to harsh chemicals without breaking down. A conveyor belt’s ability to resist chemicals will directly impact its service life and prevent safety hazards, particularly in the petrochemical, food processing, and pharmaceutical industries.
- Resistance to Abrasion: Abrasion resistance is crucial in applications where the conveyed materials are abrasive or sharp. The belt must be able to endure constant friction without significant wear or damage to the surface. Abrasive materials like sand, gravel, coal, or cement can quickly degrade a belt that isn’t sufficiently resistant to abrasion. Conveyor belts used in mining, cement manufacturing, and other heavy-duty industries are often made with specialized rubber compounds or reinforced with materials like ceramic or polyurethane to improve abrasion resistance. This feature ensures that the belt can endure long-term use without compromising its efficiency or safety.
Customization Options
One of the key advantages of rubber conveyor belts is their ability to be customized to meet specific operational needs. Custom features can be added to enhance the belt’s performance and ensure it is optimized for the intended application.
- Cleating: Cleats are raised patterns or features attached to the surface of the conveyor belt. They help to keep materials in place, prevent slippage, and enable the belt to carry materials at an incline. Cleats are particularly useful in inclined conveyors, where materials might slide or roll off without a proper surface feature. The height, spacing, and material of the cleats can be customized depending on the material being conveyed and the angle of the conveyor. Rubber cleats are commonly used in food processing, agriculture, and mining, where materials need to be conveyed on steep inclines.
- V-Guides: V-guides are strips of rubber or other materials that are attached to the underside of the conveyor belt to help it stay aligned and maintain its proper tracking as it moves along the conveyor system. V-guides are particularly helpful in systems where the belt is subject to lateral movement or misalignment, as they help guide the belt along its track, reducing wear and improving efficiency. V-guides can be added in a variety of sizes and configurations to suit specific belt widths and the type of conveyor system in use.
- Special Coatings: Conveyor belts can also be customized with special coatings to improve their performance in specific environments. Coatings such as flame retardants, oil-resistant coatings, or non-stick coatings are often applied to the surface of the belt to enhance its ability to perform in challenging conditions. For example, in food-grade applications, non-stick coatings can help prevent materials from sticking to the belt, ensuring smooth operation and easy cleaning. In environments where fire safety is a concern, flame-resistant coatings are applied to reduce the risk of fire hazards. Coatings can also provide additional resistance to wear, chemicals, or UV damage, further extending the service life of the conveyor belt.
How to Choose the Best Rubber Conveyor Belt
Selecting the right rubber conveyor belt for your operation is critical for optimizing efficiency, reducing maintenance costs, and ensuring the safety and reliability of your system. The best rubber conveyor belt for your application will depend on a variety of factors, including load capacity, temperature resistance, environmental conditions, and expected conveyor belt life. A proper selection process can prevent premature belt failure, minimize downtime, and improve overall productivity. Below, we explore the key factors to consider when choosing the best rubber conveyor belt for your needs.
Load Capacity
The load capacity of a rubber conveyor belt refers to the maximum weight the belt can safely transport at any given time. Choosing a belt with the appropriate load capacity is essential to prevent overloading, which could cause the belt to stretch, warp, or even break. Overloading can lead to increased wear and tear, higher maintenance costs, and a shorter service life for the conveyor system.
When selecting a belt, consider both the weight of the materials you will be conveying and the operating conditions of the system, including belt speed and incline. For heavy-duty applications, such as in mining, construction, or quarrying, a heavy-duty conveyor belt made with steel cord reinforcement may be necessary to handle the high tension and weight loads. On the other hand, light-duty applications, such as in packaging or food processing, may require a lighter, more flexible rubber belt.
To accurately determine the required load capacity, you should assess the total weight of the conveyed material and the maximum load it will experience during operation, factoring in variables such as load surges or peak throughput.
Temperature Resistance
Conveyor belts are often exposed to a wide range of temperatures depending on the materials being transported and the working environment. Whether you need a belt that can withstand extreme heat, sub-zero temperatures, or rapid temperature fluctuations, selecting the right rubber compound is crucial for performance and longevity.
- Heat Resistance: Conveyor belts used in high-temperature environments, such as cement plants, steel mills, or coal handling facilities, require heat-resistant rubber compounds. These compounds are designed to resist degradation and maintain flexibility even at temperatures that exceed normal limits. Heat-resistant belts are typically made from synthetic rubbers like EPDM (ethylene propylene diene monomer) or silicone, which can tolerate heat without hardening or cracking.
- Cold Resistance: On the flip side, belts used in cold storage or environments with freezing temperatures need to be made from rubber compounds that retain their flexibility and strength at lower temperatures. Natural rubber or specially formulated synthetic rubbers like nitrile are often used in applications where the belt will be exposed to cold conditions.
- Temperature Fluctuations: In many industrial applications, conveyor belts are subjected to temperature cycles, where they alternate between extreme hot and cold environments. For such applications, it’s essential to select a belt that can withstand these fluctuations without becoming brittle or deforming. Specially engineered belts with heat-resistant and cold-resistant properties offer the best performance in such environments.
Cost Considerations
When selecting a rubber conveyor belt, cost is a critical factor that must be carefully balanced with performance, durability, and operational needs. While the initial rubber conveyor belt price may vary based on material composition, reinforcement, and specialized features, the total cost of ownership includes factors like maintenance, lifespan, and downtime. A rubber conveyor belt for sale may offer attractive prices, but it’s important to assess whether it aligns with your specific application requirements to ensure it provides long-term value.
Opting for a good price and quality rubber conveyor belt can help reduce overall expenditures without compromising performance. However, focusing solely on the upfront cost may lead to higher maintenance or replacement expenses in the future. A rubber conveyor belt cost that reflects a higher-quality material may result in fewer repairs, longer lifespan, and more efficient operations, thus offering a better return on investment over time.
By factoring in both the purchase price and the potential operational savings, companies can make an informed decision that balances cost and performance effectively.
Environmental Conditions
Environmental factors such as moisture, exposure to chemicals, UV rays, and abrasive materials can all impact the durability and performance of a rubber conveyor belt. When selecting a belt, consider the specific conditions in which it will operate to ensure it can withstand external stresses without failure.
- Moisture and Water Resistance: In industries like agriculture, food processing, or wastewater treatment, conveyor belts are often exposed to high humidity or direct contact with water. In such cases, polyurethane-coated belts or belts made with neoprene rubber are excellent choices because of their superior resistance to moisture absorption. The conveyor belt made of these materials offers enhanced durability, making them ideal for environments where moisture resistance is critical. Moisture resistance is particularly important to prevent the belt from becoming slippery, losing strength, or developing mold.
- Chemical Resistance: If your conveyor system handles chemicals, oils, or other corrosive substances, selecting a rubber belt that can resist degradation from chemical exposure is essential. Rubber compounds like nitrile (oil-resistant), neoprene, and viton offer excellent resistance to a wide range of chemicals, oils, and fats. Chemical-resistant belts are often used in industries such as petrochemical, pharmaceutical, and food processing, where contamination or degradation could lead to costly downtime or safety hazards.
- UV Resistance: Conveyor belts used outdoors or in applications where they are exposed to sunlight must be resistant to UV rays. UV radiation can cause rubber to degrade over time, leading to cracking, hardening, and reduced performance. Special rubber compounds like urethane or belts with UV-resistant coatings can provide longer-lasting protection against UV damage.
- Abrasion Resistance: In industries where the conveyed materials are highly abrasive, such as mining, recycling, or sand and gravel operations, abrasion resistance is a crucial factor to consider. The rubber used in these belts must be tough enough to resist the wear caused by constant friction and contact with rough, sharp materials. Belts with reinforced covers or abrasion-resistant compounds such as carboxylated nitrile rubber or polyurethane are ideal for such applications.
Belt Life and Maintenance Considerations
One of the most significant factors to consider when selecting a rubber conveyor belt is its expected lifespan. The longer a belt lasts, the fewer replacements or repairs will be necessary, reducing maintenance costs and downtime. Several factors contribute to the belt’s lifespan:
- Material Durability: The quality of the rubber and the reinforcement materials used (e.g., fabric, steel cord) plays a major role in determining the belt’s longevity. Stronger, more resilient materials are less likely to wear out or stretch under stress, providing a longer service life.
- Maintenance and Inspection: Even the best rubber conveyor belts require regular maintenance and inspection to ensure they continue to perform optimally. Factors like proper belt alignment, tension adjustments, and regular cleaning can help extend the life of the belt. Some manufacturers offer belts with built-in features for easier maintenance, such as easy-to-repair fasteners or self-cleaning surfaces.
- Environmental Considerations: The operating environment also affects the life expectancy of a belt. Harsh conditions such as extreme temperatures, chemical exposure, and heavy abrasives can shorten the life of the belt. Therefore, choosing a belt with appropriate resistance to these conditions will ensure that it performs for the longest possible time before requiring replacement.
The Role of Proper Belt Selection in Improving Efficiency and Reducing Downtime
Choosing the right rubber conveyor belt for your system is not just about selecting a product that meets the technical specifications; it is also about ensuring optimal efficiency and reliability. When a belt is properly matched to its operating conditions and load requirements, it will perform at its best, minimizing the risk of failure, reducing the need for frequent repairs, and extending its useful life.
Proper belt selection leads to smoother operations with fewer interruptions, which ultimately results in lower maintenance costs, reduced downtime, and improved productivity. Conversely, selecting the wrong belt can lead to premature wear, frequent breakdowns, and increased operational costs.
For example, a high-performance belt that is correctly matched to the load capacity and environmental conditions of the system will reduce the risk of stretching, misalignment, or rupture. In turn, this leads to fewer maintenance interventions, greater operational efficiency, and reduced downtime, contributing to overall cost savings.
Rubber Conveyor Belt Manufacturers: Gram
At Gram, we pride ourselves on being a leader in the rubber conveyor belt manufacturers industry with over 30 years of experience. We specialize in providing high-quality rubber conveyor belts, rollers, and related components, all designed to meet the demanding needs of industries like mining, construction, and manufacturing.
Our Global Presence and Commitment to Excellence
With branches in top cities across China, including Shanghai, Beijing, Guangzhou, and Shenzhen, we’ve established a widespread presence that allows us to serve our customers efficiently—both locally and internationally. As one of the leading rubber conveyor belt manufacturers in China, we are well-positioned to compete with rubber conveyor belt manufacturers in India. Our strategic advantage lies in offering superior quality and cost-effective products, thanks to our advanced manufacturing processes and extensive industry experience. This enables us to deliver competitive solutions that outperform those from manufacturers in India and other regions. Our global reach ensures that wherever you are, we’re ready to support you with fast, reliable service. We are also a prominent player in the rubber conveyor belts market, ensuring we meet the needs of diverse industries worldwide.
Innovative Technology and Expertise
At Gram, we believe that innovation is key to driving the future of conveyor systems. Our dedicated research and development team has developed cutting-edge technologies to enhance the performance of our products. From high-tension resistant conveyor belts designed for heavy-load applications to automated monitoring systems for real-time diagnostics, we continually push the boundaries to make your operations more efficient and cost-effective.
We’re also committed to using energy-efficient drive mechanisms and wear-resistant materials, which significantly reduce operational costs and extend the lifespan of your equipment. As a rubber conveyor belt factory that focuses on technological advancements, we provide solutions that offer both durability and efficiency, making us a preferred rubber conveyor belt supplier in the industry.
Quality You Can Rely On
Quality is at the core of everything we do. Our manufacturing processes meet the highest international standards, including ISO 9001, ISO 14001, and ISO 45001 certifications. We’re proud to offer CE marking, MSHA approvals, and CEMA compliance, ensuring our products perform reliably in even the toughest environments. When you choose Gram, you’re choosing a company that has built its reputation on delivering products that last. Whether you need a rubber conveyor belt distributor to supply your materials or a reliable partner for custom needs, we are equipped to support all your requirements.
What Sets Us Apart?
Experience and Expertise: With over 30 years of experience, we understand the complexities of various industries and tailor our products to meet your specific needs.
Comprehensive Product Range: We offer an extensive selection of rubber conveyor belts, including high-tension belts, wear-resistant options, and custom-designed solutions, ensuring we have the right product for every application. As a rubber conveyor belt supplier, we provide diverse options to cater to different operational needs.
Innovative Solutions: From advanced sealing technology to automated monitoring systems, we bring innovative solutions that enhance the efficiency and safety of your conveyor systems.
- Global Support: With a presence in major cities across China and beyond, we offer local support with a global reach, making sure you get the service you need, wherever you are. As a reliable rubber conveyor belt distributor, we ensure timely and efficient deliveries.
- Certifications and Compliance: Our commitment to quality is backed by certifications like ISO, CE, and MSHA, ensuring that our products meet the highest standards of safety and performance.
What to Look for When Choosing a Rubber Conveyor Belt Manufacturer
When selecting a manufacturer for rubber conveyor belts, consider the following factors to ensure you’re making the best choice:
- Certifications and Compliance: Look for rubber conveyor belt manufacturers with ISO certifications and other industry-specific approvals to ensure product quality and reliability.
- Industry Experience: A manufacturer with extensive experience, like Gram, is more likely to offer reliable, high-performance products that meet your operational needs.
- Customization Options: Choose a manufacturer that offers tailored solutions to address specific requirements, such as high-tension belts or custom conveyor components. For instance, we also offer a rubber conveyor belt jointing solution to help with belt installation and maintenance.
- Global Reach and Support: Ensure the manufacturer has a strong global presence and can provide responsive support for maintenance, repairs, and product inquiries.
- Warranty and After-Sales Support: A manufacturer with a robust warranty and after-sales support system ensures that you’re covered if any issues arise with the product.
- Product Range and Quality: A diverse product range, including various rubber conveyor belts and components, allows you to choose the best option for your specific needs, whether for heavy-duty, high-temperature, or food-grade applications.
Rubber Conveyor Belt Pricing and Availability
When purchasing a rubber conveyor belt, several factors influence both the price and availability of the product. Understanding these factors will help you make an informed decision and ensure that you get the best value for your investment. Let’s dive into the key aspects that affect pricing and availability, and explore considerations for purchasing the right belt for your needs.
Factors That Affect the Price of Rubber Conveyor Belts
- Material Type: The composition of the rubber conveyor belt is one of the most significant determinants of its price. Different types of rubber offer varying levels of durability, flexibility, and resistance, which all contribute to cost variations. For example:Natural rubber is often less expensive but may not be suitable for heavy-duty or high-temperature environments.
Synthetic rubbers such as EPDM (ethylene propylene diene monomer), neoprene, or nitrile are typically more expensive due to their enhanced durability, chemical resistance, and versatility.
Reinforced belts, which include layers of fabric or steel cords, also increase the cost but are necessary for applications involving heavy loads, high tension, or abrasive materials.
Belt Width and Length: The dimensions of the conveyor belt also directly affect pricing. Wider belts, often used in large-scale industrial operations or mining, require more raw material, increasing both the manufacturing time and material costs. Longer belts, especially in applications with extended conveyor systems, also contribute to higher prices. Customization of these dimensions, particularly if the belt needs to fit a specific system or operate in specialized environments, will increase the cost compared to standard sizes.
Customization: Many industries require conveyor belts with special modifications to suit unique operational needs. Customizations can include:
Cleating (the addition of raised profiles or patterns to the belt surface to prevent material slippage),
V-guides (used for tracking to keep the belt aligned),
Coatings (such as fire-resistant, oil-resistant, or chemical-resistant coatings).
Specialized edge treatments or belt reinforcements for high-impact environments.
These custom features often add to the cost because they require specialized manufacturing processes and may involve higher-end materials or more labor-intensive production. - Grade of Belt and Durability Requirements: Conveyor belts designed to handle extreme conditions, such as high heat, abrasion, or chemical exposure, generally come with a higher price tag. For example:Heat-resistant belts and fire-resistant belts require specialized materials and construction to withstand extreme temperatures, which adds to the cost.
Belts intended for highly abrasive environments, like mining or construction, require more durable and wear-resistant materials, increasing their price.
Volume of Purchase: The quantity of belts ordered can impact the pricing. Bulk orders often come with discounts, as manufacturers can reduce costs through economies of scale. However, ordering in smaller quantities or requesting highly specialized custom belts could increase unit costs due to lower production volumes.
Availability Across Different Regions and Shipping Considerations
- Regional Availability: Availability of rubber conveyor belts can vary depending on geographic location, as manufacturers may have different supply chains or warehouses in different regions. In some cases, specific types of conveyor belts may only be available in certain areas or require long lead times if the manufacturer needs to source materials or components from overseas.
Local suppliers might offer quicker delivery times and lower shipping costs, particularly for standard or commonly used belts that don’t require specialized modifications.
International suppliers or manufacturers, such as Gram, with global reach can offer access to a broader range of products, but international shipping times and import duties may increase both the cost and wait time. - Shipping and Logistics Considerations: Shipping considerations also play an important role in the final price of the conveyor belt. The weight, size, and volume of the belt can impact shipping costs, especially for large or heavy-duty belts. In addition, shipping options can vary:
Standard shipping typically takes longer and may be more affordable, but if you need the belt urgently, expedited shipping could significantly increase costs.
Freight charges for large or bulk orders can add up, especially if the belt needs to be transported over long distances or across borders.
Working with a supplier that has global shipping capabilities or strategically located warehouses can reduce shipping time and cost. For example, Gram has a widespread presence with multiple branches across key regions, ensuring faster delivery and better availability of products to customers in different locations. - Stock Availability and Lead Time: Some manufacturers may have belts in stock, while others may require custom manufacturing based on order specifics. In the case of customized belts or specialty products (such as heat-resistant or oil-resistant belts), lead times could be longer, sometimes requiring weeks or even months for production and delivery.
For urgent needs, it’s important to consult with the manufacturer about stock availability and estimated lead times to ensure the belts arrive on time and meet operational requirements. - After-Sales Service and Support: Pricing should also factor in the availability of after-sales support, such as installation assistance, warranty options, and maintenance services. Reliable customer service is key to ensuring that the product performs as expected and that any issues can be addressed quickly. At Gram, we provide comprehensive support through our dedicated teams, ensuring that customers receive both the product and the services necessary to maintain optimal performance.
Rubber Conveyor Belt HS Code
The HS code (Harmonized System Code) plays a critical role in international trade, as it is a standardized numerical method used to classify products for customs purposes. In the context of rubber conveyor belts, the HS code is used to define and categorize these products for import and export, ensuring they are correctly processed by customs authorities. Here’s an in-depth look at the HS code for rubber conveyor belts, and how it affects pricing, import/export processes, and customs regulations.
What is an HS Code?
The HS code is a 6-digit numerical code that identifies goods traded internationally. It is part of the Harmonized System, which is maintained by the World Customs Organization (WCO). The system is used by over 200 countries and economies worldwide, helping standardize product classifications across borders.
For rubber conveyor belts, the HS code helps categorize them under a specific category related to rubber and its products. While there might be slight variations in how different countries break down the code further (with additional digits for more specific classifications), the basic 6-digit code is universally recognized.
Importance of the HS Code for Rubber Conveyor Belts in International Trade
How HS Codes Affect Pricing
- Tariffs and Customs Duties: The HS code determines the tariff classification of rubber conveyor belts when they cross borders. Different HS codes can attract different levels of customs duties depending on the importing country’s trade policies. For example, a rubber conveyor belt might be subject to a higher duty rate if it falls under a category that’s heavily taxed, or it might qualify for a lower rate if it’s classified under a trade agreement or preferential tariff.
Additionally, HS codes may determine whether goods are eligible for exemptions or reduced tariffs in certain countries, depending on international trade agreements like free trade agreements (FTAs). For example, rubber products like conveyor belt might have lower duties in countries that are signatories to agreements that waive tariffs on certain industrial goods. - Customs Valuation: The price you pay for your rubber conveyor belt, along with the HS code, can influence how your product is valued by customs. Customs authorities use the HS code to assess the customs value of a product, which is the price upon which duties and taxes will be calculated. Depending on the classification of your rubber conveyor belt, the customs value may be subject to different rules.
For instance, if a product falls under a category with stricter regulations, additional fees might apply, raising the cost of importing the goods. On the other hand, belts that fall under certain reduced-duty categories can offer cost-saving advantages. - Impact on Lead Time and Costs: Incorrect classification or misidentification of the HS code can lead to delays in clearing customs, resulting in additional shipping costs and longer lead times. Properly identifying the HS code for rubber conveyor belts from the beginning ensures a smoother shipping experience, avoiding costly delays that might otherwise arise from incorrect paperwork or disputes over tariff classifications.
How HS Codes Affect Import/Export Processes and Customs Regulations
Additionally, the HS code will identify whether rubber conveyor belts are subject to import quotas, bans, or special import licenses, depending on the product’s category. Understanding these regulations and using the correct HS code can prevent unnecessary delays and ensure compliance with local laws.
FAQs about Rubber Conveyor Belt
What is the use of rubber conveyor belt?
Rubber conveyor belts are essential in various industries as they are designed to transport materials efficiently over long distances. These belts are commonly used in mining, agriculture, manufacturing, and material handling sectors due to their durability and versatility. Their primary function is to move bulk materials, such as coal, grains, ore, sand, cement, and packaged goods, from one location to another. Rubber conveyor belts are particularly effective because they provide smooth, continuous motion, which helps in reducing manual labor and increasing productivity. The rubber construction offers a high degree of flexibility, resistance to wear, and protection against environmental conditions, making it suitable for both indoor and outdoor applications. Furthermore, rubber conveyor belts can be customized for specific needs, such as heat-resistant, oil-resistant, or fire-resistant versions, depending on the type of materials being transported and the environmental conditions. This makes them indispensable in industries that require a reliable, efficient, and long-lasting transportation solution for bulk materials.
What are the three types of conveyor belts?
Conveyor belts come in a variety of types, each designed for specific operational requirements. The three most common types are general-purpose conveyor belts, heavy-duty conveyor belts, and specialty conveyor belts.
General-purpose conveyor belts: These belts are designed for light to medium-duty applications where the materials being transported are not overly heavy or abrasive. They are commonly used in industries like food processing, pharmaceuticals, and light manufacturing.
Heavy-duty conveyor belts: These are built to handle high-load and abrasive materials, making them ideal for demanding industries such as mining, construction, and bulk material handling. They are typically reinforced with steel cords or fabric to increase their strength and durability.
Specialty conveyor belts: This category includes conveyor belts that are designed to withstand extreme conditions, such as heat-resistant, oil-resistant, fire-resistant, and chemical-resistant belts. These belts are tailored for applications where the environment or materials being transported present special challenges, such as in steel mills, chemical plants, or foundries.
What is the best way to cut a rubber conveyor belt?
Cutting a rubber conveyor belt requires precision and the right tools to ensure a clean cut without damaging the belt or compromising its integrity. The most effective way to cut a rubber conveyor belt is to use a sharp industrial knife or a circular saw with a blade specifically designed for rubber materials. Here are the key steps to safely and efficiently cut a rubber conveyor belt:
Measure and Mark the Cut: Before cutting, carefully measure the length and width of the belt where it needs to be cut. Use chalk or a marker to mark the cutting line clearly.
Secure the Belt: Lay the conveyor belt flat on a solid surface and secure it using clamps or weights to prevent it from moving while cutting.
Cut with Proper Tools: Use a sharp industrial knife for smaller cuts or a circular saw for thicker or tougher belts. If using a saw, ensure it has a fine-toothed blade designed for rubber. Cut in straight lines and avoid any jagged edges.
Finish Edges: After cutting, use a file or grinder to smooth the edges of the rubber belt, preventing any rough spots that might cause damage during installation or operation.
What size belts are there in rubber conveyors?
Rubber conveyor belts come in a variety of sizes, allowing them to be tailored for specific applications. The size of a rubber conveyor belt is generally determined by its width, length, and thickness. These dimensions depend on the capacity, material type, and operating environment of the conveyor system.
Width: Conveyor belts can range in width from as narrow as 18 inches (45 cm) to more than 120 inches (300 cm), with most standard belts typically falling in the range of 24 inches (60 cm) to 72 inches (180 cm). The width of the belt is chosen based on the amount of material it needs to carry at once and the conveyor’s design.
Length: The length of the belt varies significantly depending on the distance the material needs to be transported. Conveyor belts can be as short as 10 feet (3 meters) for small systems or more than 1000 feet (300 meters) in large-scale applications. Custom-length belts can be fabricated to meet specific requirements.
Thickness: The thickness of a rubber conveyor belt can range from 0.5 mm to 50 mm or more, depending on the material being transported and the conditions in which the belt operates. Thicker belts are typically used for heavy-duty applications that involve abrasive materials, while thinner belts may be used for lighter, less abrasive materials.
CONTACT US
Let us help you find a better solution!