Selecting Rubber Conveyor Belt Rollers
Rubber conveyor belt rollers play a crucial role in industrial applications by guiding and supporting conveyor belts during material transportation. By providing grip and absorbing impacts, these rollers help reduce belt wear and ensure smooth material flow. Effective rubber conveyor belt rollers are vital in mining, manufacturing, and agriculture, preventing belt misalignment and ensuring uninterrupted operation. Their resilient rubber surface makes them ideal for handling heavy loads and high-impact conditions, safeguarding the belt’s longevity.
Rubber Conveyor Belt Rollers Hardness
The hardness of rubber conveyor belt rollers is a critical factor that affects their performance, durability, and suitability for various applications. Hardness in this context refers to the resistance of the rubber material to indentation and wear, typically measured using the Shore A hardness scale. The Shore A scale ranges from 0 (soft) to 100 (hard), with higher numbers indicating harder materials.
When discussing the hardness of rubber conveyor belt rollers in detail, it’s important to consider how this property influences their performance in various industrial applications. Here’s a more in-depth exploration:
Understanding Hardness in Rubber Conveyor Belt Rollers
Hardness in rubber materials is a measure of how resistant the surface is to deformation. In conveyor belt rollers, this property is critical because it affects how the roller interacts with the conveyor belt and the materials being transported. The hardness of the rubber is measured using the Shore A durometer scale, which ranges from 0 (extremely soft) to 100 (extremely hard). The hardness level determines the roller’s ability to resist wear, absorb shocks, and maintain grip.
Soft Rubber Rollers (Shore A Hardness 50-60)
- Grip and Flexibility: Softer rubber rollers are generally more flexible and provide a higher degree of surface grip. This makes them ideal for conveying delicate items that require gentle handling, such as fragile goods, food products, or electronics. The flexibility of the rubber allows it to conform slightly to the shape of the belt and the items, reducing the risk of slipping and ensuring smooth transport.
- Shock Absorption: The softer material acts as a cushion, absorbing vibrations and impacts. This property is particularly useful in applications where the conveyor system is subject to frequent starts and stops, or where the items being transported are sensitive to shock.
- Noise Reduction: Softer rollers tend to operate more quietly, making them suitable for environments where noise reduction is important, such as in factories or warehouses where workers are present.
Hard Rubber Rollers (Shore A Hardness 70-90)
- Wear Resistance: Harder rubber rollers are more durable and resistant to wear and tear, making them suitable for heavy-duty applications where the conveyor system handles abrasive or heavy materials. These rollers are less likely to deform under load, which ensures they maintain their shape and functionality over time.
- Load Capacity: With higher hardness, the rollers can support heavier loads without compromising their structural integrity. This makes them ideal for industries like mining, construction, or logistics, where conveyors are used to move bulk materials or heavy products.
- Heat and Chemical Resistance: Harder rubber materials are often more resistant to heat and chemicals, which is beneficial in environments where the conveyor is exposed to harsh conditions, such as high temperatures or corrosive substances.
Balancing Hardness with Other Properties
- Rolling Resistance: While harder rollers offer greater durability, they can also increase rolling resistance, which may require more power to drive the belt conveyor system. This trade-off must be considered when designing or selecting a conveyor system.
- Maintenance and Longevity: Harder rollers generally require less frequent maintenance due to their resistance to wear. However, if the hardness is too high for a given application, it can lead to increased wear on the conveyor belt itself, potentially leading to higher overall maintenance costs.
- Cost Considerations: Softer rollers may need to be replaced more often due to faster wear, but they might be less expensive initially. In contrast, harder rollers, while more expensive, might offer a better long-term investment due to their durability.
Application-Specific Selection
The choice of roller hardness should be tailored to the specific needs of the application. For example:
- Food Processing: Softer rollers might be chosen for conveyors transporting food items, where maintaining product integrity is crucial.
- Mining and Quarrying: Harder rollers would be preferable due to the abrasive nature of the materials being conveyed.
- Automotive Industry: A balance between hardness and flexibility might be required to handle a variety of components without damaging them.
In conclusion, the hardness of rubber conveyor belt rollers is a crucial factor that impacts their performance, durability, and suitability for specific applications. The correct hardness selection ensures the optimal balance between grip, flexibility, shock absorption, wear resistance, and load capacity, leading to efficient and cost-effective conveyor system operation.

Dimensions and Specifications of Rubber Conveyor Belt Rollers
The dimensions and specifications of rubber conveyor belt rollers can vary widely depending on the application, industry, and specific conveyor system design. However, some general parameters and specifications are commonly considered when designing or selecting rubber conveyor belt rollers. Here’s a detailed breakdown:
1. Dimensions
- Roller Diameter: The diameter of the roller is a critical dimension that affects the overall performance of the conveyor system. Common roller diameters range from 50 mm to 219 mm, but they can be larger or smaller depending on the application. The diameter influences the belt’s tension and the roller’s ability to support the load.
- Roller Length: The length of the roller is typically designed to match the width of the conveyor belt. Standard roller lengths vary, with common widths ranging from 300 mm to 2400 mm. Custom lengths can be manufactured to fit specific conveyor designs.
- Shaft Diameter: The shaft diameter is another important dimension, affecting the roller’s load-bearing capacity and rotational stability. Shaft diameters typically range from 20 mm to 50 mm or more, depending on the load requirements.
2. Material Specifications
- Roller Shell Material: The shell or outer covering of the roller is usually made from rubber, which can vary in hardness depending on the application. The rubber is typically vulcanized onto a steel or aluminum core. Rubber types can include natural rubber, neoprene, nitrile, or polyurethane, depending on the required durability, chemical resistance, and temperature tolerance.
- Shaft Material: The shaft is commonly made of steel (often carbon steel or stainless steel) for strength and durability. In some cases, aluminum or other materials might be used for lighter-duty applications.
3. Rubber Hardness
- Shore A Hardness: The rubber covering of the rollers is often specified by its hardness, measured on the Shore A scale. As previously mentioned, hardness can range from around 50 to 90 Shore A. Softer rollers (around 50-60 Shore A) are used where flexibility and shock absorption are required, while harder rollers (around 70-90 Shore A) are used for durability and wear resistance.
4. Load Capacity
- Static and Dynamic Load Ratings: Rollers are rated for both static and dynamic loads. Static load capacity refers to the maximum weight the roller can support when stationary, while dynamic load capacity refers to the maximum weight it can support while in motion. Load capacities can vary greatly depending on the conveyor roller size and material, ranging from a few kilograms to several tons per roller.
5. Bearing Type
- Bearings: The type of bearings used in the rollers can affect performance, noise levels, and maintenance requirements. Common bearing types include deep groove ball bearings, cylindrical roller bearings, and tapered roller bearings. Sealed or shielded bearings are often used to protect against dust and moisture, extending the roller’s lifespan.
6. Surface Finish
- Smooth vs. Textured Surface: The surface of the roller can be smooth or textured. Smooth surfaces are generally used for general-purpose applications, while textured or grooved surfaces can be used to increase grip or handle specific types of materials, such as wet or sticky items.
7. Environmental Resistance
- Temperature Range: The rubber material used in the rollers needs to withstand the operating temperature of the conveyor system. Typical rubber rollers can operate in temperatures ranging from -20°C to 80°C, but specialized rubbers can handle more extreme temperatures.
- Chemical Resistance: Depending on the environment, rollers may need to resist chemicals, oils, or other corrosive substances. Neoprene or nitrile rubber is often used in such environments due to their resistance to oils and chemicals.
8. Mounting and Alignment
- Mounting Configurations: Rollers can be mounted using various methods, including spring-loaded shafts, fixed shafts, or through bolts. Proper alignment of the rollers is essential to ensure smooth operation and prevent excessive wear on the conveyor belt.
9. Speed and Rotation
- Rotational Speed: The rotational speed of the roller depends on the conveyor system’s speed. This is usually measured in revolutions per minute (RPM). Rollers must be designed to handle the required speed without excessive wear or heat generation.
- Peripheral Speed: The peripheral speed, or the surface speed of the roller, should match the speed of the conveyor belt to ensure smooth and efficient operation.
10. Tolerances
- Dimensional Tolerances: Precision in the dimensions of the rollers, such as diameter and length, is important for ensuring that the conveyor system operates smoothly and efficiently. Tolerances are typically specified to ensure that the rollers fit correctly within the conveyor frame and interact properly with the belt.
The dimensions and specifications of rubber conveyor belt rollers are critical to the design and operation of conveyor systems. By selecting the appropriate roller dimensions, materials, hardness, load capacity, and other specifications, conveyor systems can be optimized for performance, durability, and efficiency in various industrial applications. Customization of these specifications allows the rollers to meet the unique demands of specific industries, whether in food processing, mining, manufacturing, or logistics.
Rubber Conveyor Belt Rollers Price
Rubber conveyor belt rollers are crucial for maintaining smooth operations across industries such as mining, manufacturing, and agriculture. Their price can vary widely, influenced by several factors such as material quality, manufacturing processes, and roller design. Understanding these factors is key to making informed purchasing decisions, ensuring that you select rollers that balance performance with cost-effectiveness.
1. Material Costs
- Rubber Quality: The type and grade of rubber used in rollers directly impact their price. High-quality synthetic rubbers like nitrile or neoprene are more expensive due to their superior resistance to wear, chemicals, and extreme temperatures. Natural rubber may be cheaper but might not offer the same durability.
- Metal Core: Most rollers have a steel or aluminum core, contributing significantly to their overall cost. Steel is stronger and more durable but heavier and more expensive, while aluminum is lightweight and corrosion-resistant but less resilient under heavy loads.
2. Manufacturing Process
- Molding Techniques: The precision molding of rubber over the metal core requires specialized equipment and processes. High-precision molding ensures a uniform rubber layer, leading to improved performance but increasing manufacturing costs.
- Custom Requirements: Some applications require customized rubber conveyor belt rollers for unique belt widths, diameters, or specific industrial conditions. Customization often demands additional labor and material, affecting pricing.
3. Roller Design and Features
- Impact Rollers: These are designed with a reinforced structure to withstand high-impact conditions, especially in loading areas. The additional reinforcement and thicker rubber layer result in higher prices.
- Troughing Rollers: Often arranged in sets to create a trough shape, these rollers guide the belt and protect materials during transport. Troughing rollers may be more expensive due to their specific design requirements.
- Self-aligning Rollers: These rollers correct belt misalignment by automatically adjusting their angle. Their sophisticated design and engineering contribute to a higher price than standard rollers.
4. Production Volume and Supply Chain
- Bulk Manufacturing: Large-scale production can significantly reduce the per-unit price, making it more economical for buyers purchasing in bulk.
- Logistics Costs: Shipping and handling can substantially affect the final price, especially for international orders or heavy-duty rollers requiring special freight services.
5. Market Demand and Brand Reputation
- Industry Demand: Prices may fluctuate based on industry demand, as mining, agriculture, and logistics companies expand their operations. High demand for quality rubber conveyor belt rollers can drive up prices.
- Brand Premium: Established brands with a proven reputation for quality may charge a premium for their rollers due to reliability and warranty coverage.
The price of rubber conveyor belt rollers is shaped by material quality, manufacturing processes, and specific design features. Understanding these factors can help businesses make informed decisions, ensuring that the selected rollers provide the required performance and longevity while fitting within budget constraints. Balancing initial costs with long-term durability will ultimately yield the best value for any industrial application.

Benefits of Used Rubber Conveyor Belt Rollers
In industrial settings like mining, manufacturing, and agriculture, rubber conveyor belt rollers are indispensable for maintaining efficient material transport systems. Used rubber conveyor belt rollers provide a cost-effective alternative to new ones, offering substantial savings while delivering reliable performance. Here’s a detailed look into their benefits:
1. Cost Savings
- Reduced Initial Investment: Used rollers are typically sold at a fraction of the cost of new rollers. This makes them an excellent option for businesses seeking to minimize equipment expenses.
- Lower Replacement Costs: When replacing worn or damaged rollers, purchasing used ones can significantly reduce the financial burden, enabling frequent replacements without high expenditure.
2. Immediate Availability
- Readily Available Stock: New rollers often require lead time for manufacturing and delivery. In contrast, used rollers are often readily available from suppliers specializing in secondhand conveyor equipment.
- Avoiding Downtime: Quick access to used rollers reduces machinery downtime, allowing businesses to keep their conveyor systems operational and productive.
3. Proven Durability
- Industry-Tested: Many used rollers come from decommissioned conveyor systems where they have already demonstrated their performance and durability. These rollers can continue to operate effectively, especially in non-critical applications.
- Pre-Verified Quality: Reputable suppliers of used rubber conveyor belt rollers thoroughly inspect, refurbish, and verify the quality of their products, ensuring buyers receive reliable components.
4. Environmental Benefits
- Sustainability: By purchasing used rollers, companies contribute to a circular economy by reducing the demand for new manufacturing and extending the life of existing components. This approach reduces waste and conserves natural resources.
- Lower Carbon Footprint: The production of new rollers involves energy-intensive processes that contribute to environmental degradation. Choosing used rollers helps minimize the carbon footprint associated with new manufacturing.
5. Availability of Diverse Options
- Range of Sizes: Suppliers of used conveyor belt rollers typically offer a wide range of sizes to suit various conveyor belt widths and system configurations.
- Varied Designs: Whether a system requires impact, troughing, or tracking rollers, many different types are available, often sourced from discontinued systems with high-quality components.
6. Customization Potential
- Reengineering: In some cases, used rollers can be reconditioned or modified to fit specific system requirements. Refurbished rollers can undergo additional customization, such as changing rubber coatings or core designs.
- Upcycling Opportunities: Creative repurposing or upcycling of used rollers provides additional utility in non-traditional applications, such as DIY projects, industrial furniture, or low-cost systems.
7. Budget Flexibility
- Balanced Inventory Management: By opting for used rollers, businesses can better allocate their budgets towards other vital operations or equipment while still maintaining efficient conveyor systems.
- Trial Implementations: Used rubber conveyor belt rollers allow companies to implement trial conveyor setups at a lower cost, helping assess system feasibility before investing in new infrastructure.
Used rubber conveyor belt rollers offer numerous advantages, from significant cost savings to immediate availability, while also providing environmental and logistical benefits. By choosing quality pre-owned rollers from reputable suppliers, businesses can maintain efficient, reliable, and sustainable conveyor systems without compromising performance. Whether for replacement, expansion, or experimental conveyor configurations, used rollers represent an effective solution that aligns with both operational and environmental goals.
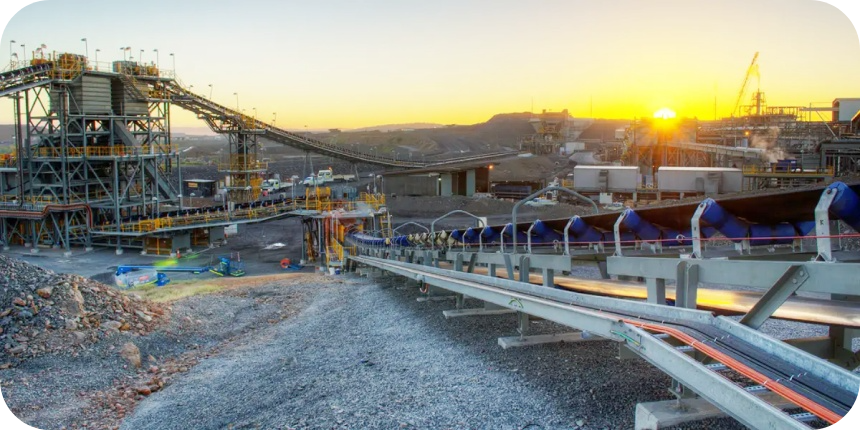
Finding Rubber Conveyor Belt Rollers for Sale
Locating reliable rubber conveyor belt rollers for sale is crucial for businesses looking to maintain efficient production systems. This involves understanding where to source these rollers, identifying trusted suppliers, and evaluating key factors before purchasing. Here’s a detailed guide:
1. Identifying Reputable Suppliers
- Authorized Distributors: Start by seeking out authorized distributors or agents who have a direct relationship with manufacturers. They offer authentic products and can assist with installation advice, after-sales service, and warranties.
- Specialty Retailers: Some retailers specialize in industrial equipment and can provide a wide selection of rubber conveyor belt rollers. These retailers often have specialized staff who can help find the right fit.
- Manufacturers Direct: Contacting manufacturers directly can sometimes yield good deals, especially if they offer refurbished or surplus products. Some manufacturers also have second-hand divisions that sell quality rollers at discounted prices.
2. Exploring Online Marketplaces
- Industry-Specific Platforms: Websites focused on industrial equipment offer a comprehensive range of rubber conveyor belt rollers. Look for platforms that vet their suppliers or provide reviews to ensure reliability.
- General Marketplaces: Popular e-commerce websites often feature a diverse selection, but due diligence is needed. Review the seller’s ratings, customer feedback, and business certifications to gauge trustworthiness.
3. Local and Global Suppliers
- Local Sourcing: Buying locally ensures faster delivery and may come with more personalized service, including installation support. Local vendors are also easier to vet through direct visits and customer references.
- Global Sourcing: For specific or hard-to-find rollers, international suppliers may offer better availability and pricing. However, consider shipping costs, delivery timeframes, and import regulations.
4. Industrial Auctions and Liquidation Sales
- Auctions: Industrial auctions are great venues to find rubber conveyor belt rollers for sale at competitive prices. These may include surplus equipment or unused inventory from businesses that are downsizing or liquidating.
- Liquidation Sales: Companies going out of business often sell their machinery and components. Such sales offer substantial discounts, but the equipment should be inspected before purchase to ensure functionality.
5. Networking and Industry Referrals
- Professional Networks: Reach out to industry peers or professional networks for referrals. Often, trusted recommendations come from those who have dealt with reputable suppliers.
- Trade Shows: Industry trade shows provide an excellent opportunity to meet suppliers in person, inspect their products directly, and negotiate favorable deals.
6. Evaluating Supplier Credentials and Quality
- Certifications and Standards: Check if the supplier holds certifications that reflect adherence to quality standards, such as ISO 9001. This can be indicative of a commitment to quality manufacturing.
- Customer Support and After-Sales Service: A reputable supplier provides technical assistance, responsive customer service, and post-sale support for repairs or replacements.
- Warranty: Ensure the supplier offers reasonable warranties on their rollers, as this indicates confidence in their product’s durability.
7. Testing and Verification
- Sample Testing: Some suppliers offer samples for testing to verify compatibility with existing conveyor systems.
- Inspection Reports: Suppliers should be able to provide inspection reports or other documentation that vouch for the quality of their rollers.
8. Negotiating Price and Delivery Terms
- Bulk Purchases: If buying in bulk, negotiate discounts to bring down the per-unit cost.
- Flexible Delivery: Ensure the supplier can accommodate delivery schedules that match your production needs to avoid unnecessary delays.
Finding the right rubber conveyor belt rollers for sale requires a strategic approach. Whether sourcing locally or globally, through auctions or online platforms, it’s crucial to work with reputable suppliers offering quality products and strong after-sales support. By carefully vetting suppliers and negotiating favorable terms, businesses can ensure they get the best rollers that fit both their operational needs and budget constraints.
Choosing Heavy Duty Rubber Conveyor Belt Rollers
When it comes to ensuring seamless operations in demanding industrial settings, heavy-duty rubber conveyor belt rollers play a vital role. Their resilience, durability, and smooth functioning are essential for industries like mining, manufacturing, agriculture, and logistics. Here’s a comprehensive guide on choosing these rollers and understanding their features:
1. Heavy Duty Rubber Conveyor Belt Rollers
Heavy-duty rubber conveyor belt rollers are designed to handle extreme loads, adverse environmental conditions, and extended usage. They feature robust materials and innovative engineering to provide continuous service in challenging environments.
- Material: The rollers often incorporate high-quality rubber and steel or aluminum cores, providing resistance to corrosion, abrasion, and impact.
- Structure: Internal bearings and shaft seals are designed for smooth rotation, reducing friction and wear over time.
- Weight Capacity: These rollers have a higher load-bearing capacity compared to standard rollers, which makes them ideal for industries that transport heavy and abrasive materials.
2. Assessing Your Application’s Requirements
Before selecting heavy-duty rubber conveyor belt rollers, assess the specific needs of your industrial application.
- Load Capacity: Ensure the roller can withstand the weight and bulk density of the materials to be conveyed.
- Operating Environment: Consider factors like temperature, humidity, chemical exposure, and dust levels in the working environment.
- Speed Requirements: The rollers must be compatible with the conveyor’s operating speed without compromising stability.
3. Core Features of Heavy Duty Rollers
When choosing heavy-duty rubber conveyor belt rollers, prioritize these essential features:
- Sealing Systems: Multi-labyrinth sealing systems prevent contaminants like dust and water from infiltrating, ensuring longer bearing life.
- Bearing Housing: Precision-engineered bearing housings ensure stable bearing positioning, reducing noise and minimizing vibration.
- Shell Thickness: A thicker roller shell offers better impact resistance, crucial in high-load applications like mining.
- Dynamic Balancing: Properly balanced rollers prevent belt misalignment and minimize wear on the belt.
4. Material Quality and Compatibility
Heavy-duty rollers should be compatible with the type of conveyor belt and the materials being transported:
- Rubber Quality: Select rollers with high-grade rubber that resists wear, heat, and corrosion. Different types of rubber compounds can be used to meet specific requirements.
- Metal Cores: Steel or aluminum cores add structural stability, ensuring long-term durability.
5. Manufacturing Standards and Certification
Ensure that the rollers conform to recognized industry standards:
- ISO Certification: Compliance with ISO 9001 and other relevant standards indicates adherence to quality management practices.
- Testing Protocols: Look for manufacturers that conduct rigorous quality testing, including load capacity tests, abrasion resistance, and dimensional accuracy.
6. Suitability for Different Environments
Choose rollers tailored for specific environments:
- Mining and Quarrying: Heavy-duty rollers with extra-thick shells and reinforced bearings are suitable for conveying ores, rocks, and minerals.
- Manufacturing and Packaging: Rollers with high load capacities and precise balancing minimize noise and ensure smooth transport of finished goods.
- Agriculture: Rubber rollers with high abrasion resistance are needed for conveying grains, fertilizers, and agricultural byproducts.
7. Maintenance and Service Life
Heavy-duty rollers should offer extended service life with minimal maintenance:
- Lubrication Systems: Some rollers feature self-lubricating bearings, reducing the need for frequent greasing.
- Replacement Parts: Opt for rollers with readily available replacement parts, ensuring fast repairs when necessary.
8. Vendor Selection and Support
Choose a supplier with a solid reputation for delivering quality products and customer service:
- Technical Assistance: A supplier should offer support in selecting the appropriate rollers, installation guidance, and troubleshooting.
- Warranty: Ensure the rollers come with a warranty that covers manufacturing defects or premature wear.
Selecting the right heavy-duty rubber conveyor belt rollers is crucial for optimizing conveyor performance and minimizing downtime. Consider load capacity, operating environment, sealing systems, and material quality to find the most suitable rollers for your application. Partner with reputable suppliers who offer strong technical support and quality assurance, and you’ll ensure your conveyor system operates reliably even under the most demanding conditions.
Replacing Rubber Conveyor Belt Rollers
Replacing rubber conveyor belt rollers is a crucial maintenance task that ensures the efficient operation and longevity of a conveyor system. Here’s a detailed guide on the process:
1. Safety Precautions
- Power Off the Conveyor: Before starting the replacement process, ensure that the conveyor system is completely powered off and locked out to prevent accidental startup. This is essential to avoid any risk of injury.
- Wear Appropriate PPE: Personal protective equipment (PPE) such as gloves, safety glasses, and steel-toed boots should be worn to protect against potential hazards during the replacement process.
- Inspect the Area: Ensure the workspace is clean and free of any debris that could cause accidents. Also, make sure you have all the necessary tools and replacement parts ready.
2. Identify the Rollers to Be Replaced
- Inspect Rollers: Perform a thorough inspection of the conveyor system to identify which rollers need to be replaced. Look for signs of wear such as cracking, flattening, excessive noise, or reduced performance.
- Check Alignment and Bearings: While inspecting the rollers, also check for misalignment and bearing issues, as these can cause premature wear on the rollers and belt.
3. Removing the Old Rollers
- Release Tension on the Conveyor Belt: Loosen the tension on the conveyor belt to create slack, making it easier to remove the rollers. This can usually be done by adjusting the tensioning device or using a belt tension release tool.
- Remove Mounting Hardware: Depending on the roller design, remove the mounting hardware (such as bolts, brackets, or clips) that secure the roller in place. Keep these components in a safe place if they will be reused.
- Extract the Roller: Carefully slide the roller out of its position. Depending on the roller’s weight and size, you might need assistance or use lifting equipment.
4. Installing the New Rollers
- Select the Correct Roller: Ensure that the replacement roller matches the specifications of the old roller, including diameter, length, shaft size, and bearing type.
- Insert the New Roller: Slide the new roller into position, ensuring it is properly aligned with the conveyor belt and other rollers. Alignment is critical to prevent belt tracking issues and uneven wear.
- Secure the Roller: Reattach the mounting hardware to secure the roller in place. Ensure all bolts and clips are tightened to the manufacturer’s specifications to prevent loosening during operation.
5. Re-Tension the Conveyor Belt
- Adjust Belt Tension: After the new rollers are installed, re-tension the conveyor belt to the appropriate level. The belt should be tight enough to avoid slipping but not so tight that it causes excessive wear on the rollers or bearings.
- Check Belt Alignment: Ensure the belt is properly aligned over the rollers. Misalignment can cause the belt to drift to one side, leading to uneven wear and potential damage.
6. Final Inspection and Testing
- Inspect the Installation: Double-check that all rollers are securely installed and that the belt tension and alignment are correct. Also, ensure that all tools and materials are cleared from the conveyor area.
- Power On and Test: Once everything is in place, power on the conveyor system and observe its operation. Listen for any unusual noises and watch for smooth belt movement over the rollers.
- Fine-Tuning: If necessary, make fine adjustments to the belt tension or roller alignment to ensure optimal performance.
7. Documentation and Maintenance Records
- Record the Replacement: Document the roller replacement in the conveyor system’s maintenance log, including details such as the date of replacement, the type of rollers used, and any issues encountered.
- Schedule Regular Inspections: To prevent future issues, schedule regular inspections and maintenance for the conveyor system, including checking the rollers for signs of wear.
Replacing rubber conveyor belt rollers is a straightforward process when done with care and attention to detail. Proper replacement ensures that the conveyor system continues to operate efficiently and reduces the risk of downtime due to roller failure. Regular maintenance and timely replacement of worn components are key to extending the life of the conveyor system and optimizing its performance.

Rubber Conveyor Belt Rollers for Bulk Handling
Rubber conveyor belt rollers for bulk handling are specifically designed to support the transport of large quantities of materials, such as minerals, grains, coal, sand, and other bulk items, through conveyor systems. These rollers play a crucial role in ensuring the efficient and smooth operation of the conveyor, particularly in heavy-duty and harsh environments. Here’s a detailed overview:
Design and Construction
- Robust Build: Rubber rollers used in bulk handling are typically built with a heavy-duty construction to withstand the high demands of bulk material transportation. The core is often made of steel or aluminum to provide strength, while the rubber covering offers durability and protection against wear.
- Thick Rubber Coating: The rubber coating on these rollers is usually thicker than on standard conveyor rollers, providing enhanced impact resistance and cushioning for the conveyor belt. This is particularly important in bulk handling, where the materials can be heavy, abrasive, and unevenly distributed.
- Corrosion Resistance: Since bulk handling often occurs in outdoor or harsh environments, the rollers are designed to resist corrosion. The rubber itself, as well as any metal components, may be treated or coated to prevent rust and degradation from moisture, chemicals, and other environmental factors.
Load Capacity and Durability
- High Load Capacity: Bulk handling requires rollers that can support significant weight. These rollers are engineered to handle heavy loads without deforming or failing. They are designed to distribute the weight of the bulk material evenly across the conveyor system, reducing the risk of belt damage and prolonging the system’s lifespan.
- Wear Resistance: The rubber material used in these rollers is selected for its high wear resistance. This is essential for handling abrasive materials like coal, ore, or gravel, which can quickly wear down less durable rollers.
Roller Types and Applications
- Carrying Rollers: These are the primary rollers that support the conveyor belt and the load it carries. In bulk handling, carrying rollers are spaced closely together to provide consistent support, preventing the belt from sagging under heavy loads.
- Impact Rollers: Positioned at loading points where the bulk material is dropped onto the conveyor belt, impact rollers are designed to absorb the shock and reduce damage to the belt. These rollers often have a thicker, more resilient rubber coating to handle the high impact forces.
- Return Rollers: These rollers support the return side of the conveyor belt, which carries no load. While less critical than carrying rollers, they are still important for maintaining belt tension and alignment.
Specialized Features
- Self-Cleaning Rollers: In bulk handling applications where materials can stick to the rollers or belt (e.g., wet sand or clay), self-cleaning rollers are often used. These rollers are designed with ridges or grooves that help shed material, preventing buildup that can lead to belt misalignment or increased wear.
- Rubber Disc Rollers: Sometimes used in bulk handling, these rollers feature rubber discs mounted along the roller’s length. The discs help to clean the belt and are particularly useful in applications where debris or fine particles are a concern.
Performance in Harsh Conditions
- Temperature Resistance: Bulk handling operations can occur in extreme temperatures, from freezing conditions in mining operations to high heat in industrial settings. The rubber used in these rollers is often formulated to withstand such temperature extremes without losing its flexibility or durability.
- Vibration and Shock Absorption: In bulk handling, the conveyor system is often subjected to significant vibrations and shocks, particularly during loading and unloading. Rubber rollers are ideal for absorbing these forces, protecting both the conveyor system and the material being transported.
Rubber conveyor belt rollers designed for bulk handling are essential components of heavy-duty conveyor systems. Their design prioritizes durability, load-bearing capacity, and resistance to wear and environmental factors. These rollers ensure that bulk materials are transported efficiently and safely, minimizing downtime and maintenance costs in industrial operations. Whether in mining, agriculture, or construction, choosing the right rollers is critical to optimizing the performance and longevity of conveyor systems used for bulk handling.
Maintenance Tips for Rubber Conveyor Belt Rollers
Proper maintenance of rubber conveyor belt rollers is crucial for maximizing the efficiency and longevity of your conveyor system. Neglecting regular maintenance can lead to costly downtime, premature equipment failure, and reduced productivity. Below, you’ll find essential maintenance tips that can help keep your rubber conveyor belt rollers in optimal working condition.
Establishing a Maintenance Schedule
Creating a comprehensive and regular maintenance schedule is the first step to ensuring your rollers remain in top condition:
- Routine Inspections: Perform regular visual inspections to check for visible wear, cracks, or misalignment of rollers.
- Frequency: Schedule inspections according to your conveyor system’s operational demands. For heavy-duty applications, monthly or even weekly checks might be necessary.
- Record Keeping: Document maintenance activities and findings to track trends in wear and identify recurring issues.
Lubrication and Bearings
Bearings are integral to the smooth operation of rubber conveyor belt rollers, and proper lubrication is vital for their performance.
- Grease Type: Use the manufacturer’s recommended grease type to avoid chemical incompatibility and ensure efficient lubrication.
- Lubrication Frequency: Regularly lubricate roller bearings as per the maintenance schedule. For sealed bearings, confirm if they are pre-lubricated and don’t require additional grease.
- Bearing Replacement: Replace bearings immediately if they produce unusual noises or vibrations, as these indicate internal damage.
Alignment and Tracking
Roller misalignment can cause belt tracking issues and excessive wear on both the rollers and conveyor belt.
- Check Alignment: Periodically verify that each roller is properly aligned and horizontally level within the conveyor framework.
- Adjust Tracking: Adjust the tracking devices or tensioners to keep the conveyor belt centered on the rollers.
- Retighten Fasteners: Ensure that all roller mounting brackets and fasteners are securely tightened.
Cleaning and Debris Removal
Accumulated debris on rollers can affect performance, leading to belt slippage and wear.
- Regular Cleaning: Regularly clean the rollers to remove dirt, dust, and debris that could impair their function.
- Scraper Installation: Consider installing belt scrapers or cleaners to prevent material buildup on rollers.
- Belt Washing Systems: In environments with sticky materials, use washing systems to maintain a clean belt and reduce contamination.
Roller Surface Wear and Replacement
Roller surface wear is inevitable, but monitoring wear patterns and replacing rollers in time can prevent significant conveyor downtime.
- Wear Monitoring: Keep an eye on the roller surface for signs of wear, such as flattening, cracks, or rubber detachment.
- Replace Timely: Replace rollers showing excessive wear before they become a liability and cause belt damage or misalignment.
- Use Quality Rollers: Investing in high-quality rubber conveyor belt rollers reduces premature wear and ensures consistent performance.
Impact Zones and High-Load Areas
Areas with high impact or load, such as loading or transfer points, require extra attention.
- Impact Rollers: Use impact rollers with reinforced rubber shells to absorb the force at loading points.
- Frame Reinforcement: Check for conveyor frame reinforcement at high-load areas to prevent damage or frame distortion.
- Support Structure: Ensure the support structure can handle the maximum load without excessive deflection.
Monitoring Noise and Vibrations
Unusual noises or excessive vibrations from rubber conveyor belt rollers can indicate mechanical issues that need immediate attention.
- Noise Levels: Listen for abnormal sounds during conveyor operation, such as squeaking, grinding, or knocking.
- Vibration Analysis: Use vibration analysis tools to detect early signs of roller imbalance or bearing failure.
- Immediate Response: Address noise or vibration issues promptly to avoid severe mechanical failure.
Regular Staff Training
Well-trained staff can play a significant role in maintaining the efficiency of rubber conveyor belt rollers.
- Training Programs: Implement training programs for maintenance teams to ensure they understand best practices for roller care.
- Problem Identification: Train staff to identify potential issues quickly and take appropriate action.
- Technical Expertise: Encourage technical proficiency by providing guides, manuals, or direct manufacturer support.
Adhering to a strict maintenance schedule and following the outlined tips will ensure that your rubber conveyor belt rollers continue operating efficiently for a long time. By keeping the bearings lubricated, the rollers aligned, and the conveyor system clean, you’ll minimize downtime and maximize productivity. Investing time and resources in roller maintenance pays off through reduced replacement costs and increased equipment longevity, helping your conveyor system run smoothly and efficiently.
Investing in Quality Rubber Conveyor Belt Rollers
When it comes to maximizing productivity and minimizing operational disruptions in any industry reliant on conveyor systems, the importance of investing in high-quality rubber conveyor belt rollers cannot be overstated. These components play a pivotal role in ensuring the efficient, reliable, and safe transportation of materials, ultimately impacting the bottom line of any business.
Why Quality Matters
- Durability and Longevity: High-quality rubber conveyor belt rollers are built with robust materials that withstand wear and tear over prolonged periods. Investing in durable rollers reduces the frequency of replacements, thereby lowering maintenance costs and extending the lifespan of the entire conveyor system.
- Enhanced Safety: Poor-quality rollers can cause uneven belt movement or unexpected breakdowns, leading to safety hazards for workers. Quality rollers, on the other hand, are less prone to malfunctions and thus contribute to a safer working environment.
- Operational Efficiency: Reliable rollers ensure consistent belt movement, reducing the likelihood of material spillage or downtime due to mechanical issues. This leads to higher throughput and optimized production rates, directly influencing the overall efficiency of the operation.
- Reduced Energy Consumption: Efficient rubber conveyor belt rollers reduce friction and rolling resistance, allowing the conveyor belt to move smoothly. This efficiency translates into lower energy consumption and reduced operating costs over time.
Key Factors to Consider
- Material Quality: Look for rollers made from high-grade rubber and steel materials that can handle the specific conditions of your application, whether it be high temperature, heavy impact, or corrosive environments.
- Load Capacity: Ensure the rollers are capable of handling the maximum load weight without flexing or bending, as this can cause belt misalignment and premature roller wear.
- Type and Size: Choose the appropriate type and size of rollers based on belt width, load weight, and operational speed. This alignment ensures uniform load distribution and minimizes wear.
- Seal Protection: Properly sealed bearings prevent the ingress of dust, moisture, and chemicals, extending the bearing life and reducing maintenance needs.
- Manufacturer Reputation: Working with reputable suppliers ensures that you receive reliable products backed by warranties and customer support, safeguarding your investment.
The Long-Term Impact of Quality
- Return on Investment (ROI): Though the initial cost may be higher, investing in quality rubber conveyor belt rollers yields significant returns over time through reduced maintenance costs, fewer replacements, and minimized downtime.
- Sustainability: Long-lasting rollers contribute to sustainability by reducing waste from frequent replacements and promoting efficient resource utilization.
- Business Growth: A reliable conveyor system driven by high-quality rollers supports uninterrupted production, enabling businesses to meet growing demand and expand their market share.
- Competitive Edge: Quality rollers keep production running smoothly, ensuring timely delivery of goods and building a reputation for reliability in the industry.
Investing in quality rubber conveyor belt rollers is a strategic decision that directly affects operational efficiency, safety, and profitability. They minimize downtime, reduce maintenance expenses, and provide consistent performance, which is crucial for high-demand industrial environments. By understanding the factors influencing roller quality and making informed choices based on your operational needs, you ensure that your conveyor system remains an asset, not a liability. Ultimately, this investment secures the productivity and competitiveness of your business for the long term.
Get a personalized conveyor roller quote by completing this form.
FAQs about Rubber Conveyor Belt Rollers
A belt conveyor typically uses several types of rollers that play crucial roles in the system. The primary rollers include:
Carrying Rollers: Positioned along the length of the conveyor to support the belt and material being transported.
Return Rollers: Support the belt on its return journey, keeping it aligned and tensioned.
Impact Rollers: Placed under loading zones to absorb the impact and reduce belt damage when heavy material falls onto the conveyor.
Guide Rollers: Assist in aligning the belt to prevent misalignment and potential material spillage.
Snub Rollers: Increase the contact area between the drive pulley and belt for better traction and tension control.
These rollers are crucial to ensuring smooth belt movement, reducing belt wear, and improving the overall efficiency of the conveyor system.
Rubber rollers have versatile applications in various industries due to their ability to grip, provide traction, and resist wear:
Conveyor Systems: As rubber conveyor belt rollers, they guide and support the belt to transport materials in mining, agriculture, manufacturing, and food processing.
Printing: Rubber rollers help apply ink evenly on printing plates, ensuring consistent prints.
Laminating: They press materials together during lamination, ensuring strong adhesion.
Textile Production: Rubber rollers help manage fabric tension and guide textile material through processing stages.
Industrial Manufacturing: Used in various machinery, they provide grip, alignment, and precision in material processing and handling.
Rubber rollers’ adaptability to specific conditions makes them indispensable in processes where high traction and controlled movement are necessary.
The primary purposes of rollers in a conveyor system are:
Supporting the Belt: Rollers ensure the belt maintains its shape while carrying heavy loads, preventing sagging and uneven wear.
Reducing Friction: Rollers allow smooth movement of the belt, reducing energy consumption and wear on the belt and machinery.
Maintaining Alignment: Guide and tracking rollers help keep the belt aligned, preventing it from veering off and causing material spillage or damage.
Absorbing Impact: Impact rollers absorb the force of falling material at loading points, protecting the belt from damage.
Increasing Drive Efficiency: Snub rollers and bend pulleys enhance the belt’s contact with drive pulleys for better traction and tension control.
Tracking or guide rollers are specially designed to keep the conveyor belt aligned during operation. They typically include:
Training Rollers: These are angled to adjust themselves automatically when the belt starts to misalign, guiding the belt back to its proper path.
Guide Rollers: Positioned along the belt edges, guide rollers prevent the belt from moving off-center or spilling material.
Steering Rollers: Often part of the drive system, steering rollers can be adjusted manually or mechanically to change the belt’s direction.
A roller conveyor and a belt conveyor are both used for material handling, but they operate differently. A roller conveyor uses a series of rotating cylinders (rollers) to move items along. These conveyors are typically used for heavy or bulky items, as the rollers can support large weights. They rely on either gravity or a powered mechanism to keep the items moving. On the other hand, a belt conveyor uses a continuous loop of material, usually made of rubber or fabric, to transport items. Belt conveyors are ideal for moving smaller or more delicate items, providing a smooth, controlled flow. While roller conveyors are better suited for rigid objects like boxes or pallets, belt conveyors are preferred for handling smaller, lighter items or materials with irregular shapes. Each system has its own advantages depending on the type of material being transported and the specific requirements of the task.
Last Updated on September 10, 2024 by Jordan Smith
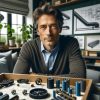
Jordan Smith, a seasoned professional with over 20 years of experience in the conveyor system industry. Jordan’s expertise lies in providing comprehensive solutions for conveyor rollers, belts, and accessories, catering to a wide range of industrial needs. From initial design and configuration to installation and meticulous troubleshooting, Jordan is adept at handling all aspects of conveyor system management. Whether you’re looking to upgrade your production line with efficient conveyor belts, require custom conveyor rollers for specific operations, or need expert advice on selecting the right conveyor accessories for your facility, Jordan is your reliable consultant. For any inquiries or assistance with conveyor system optimization, Jordan is available to share his wealth of knowledge and experience. Feel free to reach out at any time for professional guidance on all matters related to conveyor rollers, belts, and accessories.